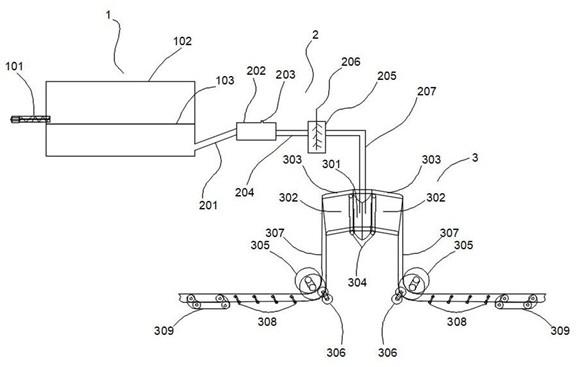
1.本发明涉及一种载板玻璃成型生产成型装置及其方法,属于玻璃制造成型装置技术领域。
背景技术:2.载板玻璃是一种表面及其平整的薄玻璃片,为oled高清显示面板制造的上游关键材料,应用于柔性oled面板制作,在面板制程中起承载作用。随着经济的发展,人民生活水平的提高,载板玻璃符合新型显示发展趋势,市场前景广阔。oled高清显示想较于其他显示行业工艺更复杂,对载板玻璃的品质要求更高,这就对载板玻璃的生产制造工艺提出更高的要求。载板玻璃相较于其他显示用玻璃基板对原材料的混合配比、混合料的熔化温度、玻璃液的品质、载板成型工艺提出更高的要求。较高玻璃液品质要求,就需要较高原材料的规格;较高的熔化温度,就需要较高耐受温度的耐火材料;较高玻璃液温度,就增加了料道贵金属的损失量;较高品质载板玻璃,就需要较高成型规格。载板玻璃产线建设成本较高于其他显示用玻璃基板。
3.现有的载板玻璃的生产工艺是原材料(石英砂、氧化铝、碳酸钙等)经过混合、熔化、调质、成型等工艺制成载板玻璃。载板玻璃混合料大多以天然气燃料,以纯氧为助燃剂,电助熔为主要热能来源,料道采用电能保温。载板玻璃相较于其他显示用玻璃基板生产需要更多的燃料和电能消耗,需要更高的生产成本投入。载板玻璃中的气泡、结石、析晶等内含物,成型过程中的应力、垂度是制约载板玻璃生产制造过程中良率的关键因素。直接决定了公司的产能效益。因此,怎样改进载板玻璃的生产成型装置和方法能够解决上述问题成为目前的迫切需求。
技术实现要素:4.针对现有技术的不足,本发明的目的在于提供一种载板玻璃成型生产成型装置及其方法,解决了现有技术中出现的问题。
5.本发明所述的一种载板玻璃成型生产成型装置,包括配合料熔融部件、玻璃液澄清均化部件和玻璃成型部件,所述的配合料熔融部件包括熔融炉,所述混合料在熔融炉中熔融成玻璃液,所述玻璃液澄清均化部件包括玻璃液澄清仓和玻璃液均化装置,所述玻璃液经玻璃液澄清仓和玻璃液均化装置进行澄清和均化后输送至玻璃成型部件中进行成型,所述玻璃成型部件包括玻璃液注入槽,所述玻璃液注入槽的外部设有溢流成型装置,溢流成型装置的外部玻璃牵引部件,所述玻璃液注满玻璃液注入槽后流向溢流成型装置和玻璃牵引部件后形成载板玻璃。
6.进一步的,熔融炉的外部设有螺旋加料装置,所述配合料通过螺旋加料装置输送至熔融炉中。
7.进一步的,熔融炉和玻璃液澄清仓之间连接有提升料道,玻璃液澄清仓和玻璃液均化装置之间连接有冷却料道,所述玻璃液澄清仓的上方设有排气口,玻璃液均化装置内
设有搅拌杆。
8.进一步的,玻璃液均化装置和玻璃液注入槽之间连接有成型供给料管,所述成型供给料管的出料口位于玻璃液注入槽中心位置。
9.进一步的,玻璃液注入槽为u型槽,所述溢流成型装置为成型翼板,成型翼板位于u型槽外部的左右两侧,u型槽和成型翼板两端设置有溢流挡砖,控制玻璃液的流向,所述成型翼板的下缘设有加热装置。
10.进一步的,玻璃牵引部件包括牵引大滚轮和牵引小滚轮,所述牵引大滚轮和牵引小滚轮相配合进行夹持牵引,引导载板玻璃成型。
11.进一步的,玻璃牵引部件的下方设有主动导向装置,所述主动导向装置用于引导载板玻璃前移,主动导向装置的末端设有输送装置。
12.本发明所述的一种载板玻璃成型生产成型方法,包括以下步骤:s1:在配合料中增加碎玻璃,将混合料输送至熔融炉内,熔融成玻璃液;s2:熔融玻璃液输送至玻璃液澄清仓,经搅拌杆进行材质均化,经料道输送至玻璃液注入槽;s3:熔融玻璃液注满玻璃液注入槽后流向两侧成型翼板,玻璃液下流形成载板玻璃;s4:载板玻璃通过牵引大滚轮和牵引小滚轮提供下拉动力,使载板玻璃由垂直方向,变为水平方向;s5:通过主动导向装置引导载板玻璃向前方行走至输送装置;s6:在输送装置上载板玻璃经过切割、检验,最终形成半成品载板玻璃。
13.进一步的,步骤s1中配合料为碎玻璃、sio2、al2o3、b2o3、mgo和na+k的组合物,其中含量占比为:碎玻璃含量占比为25-40%,sio2占比为40-50% ,al2o3占比为8-13%,b2o3占比为5-9%,cao占比为4-8%,mgo占比为0.6-1.2%,na+k占比为0.08-0.19%,其他占比为0.04-0.09%。
14.进一步的,步骤s3中成型翼板的倾斜度为6-10
°
,步骤s4中牵引大滚轮和牵引小滚轮中温度设计为700-800℃。
15.本发明与现有技术相比,具有如下有益效果:本发明所述的一种载板玻璃成型生产成型装置及其方法,成型装置采用单侧溢流下拉,相较于传统的两侧溢流法,有效避免了溢流下拉法对玻璃板两侧厚度比例难以控制的问题。厚度不均匀使造成载板玻璃应力大的一项w重要因素,载板厚度是调整载板其他品质的基础。通过成型装置的改进可以实现单料道双成型,实现产量两倍的增长,最大限度的节省建设费用,节约能源,方法中通过优化混合料的配比工艺,降低混合料熔化过程温度,降低载板玻璃成产建设成本;进一步降低天然气、电能的消耗,降低载板玻璃生产制造运行成本。优化载板玻璃成型方法,提高载板玻璃板产量,提升产能,增加公司生产效益。解决了现有技术中存在的问题。
附图说明
16.图1为本发明实施例中载板玻璃生产装置的示意图;图2为本发明实施例中翼型成型装置的主示意图;
图3为本发明实施例中成型装置的俯示意图;图4为本发明实施例中夹持牵引装置示意图;图5为本发明实施例中载板玻璃主动导向轮示意图;图6为本发明实施例中翼板实施方案示意图;图中:1、配合料熔融部件;2、玻璃液澄清均化部件;3、玻璃成型部件;101、螺旋加料装置;102、熔融炉;103、玻璃液;201、玻璃液提升料道;202、玻璃液澄清仓;203、排气口;204、冷却料道;205、玻璃液均化装置;206、搅拌杆;207、成型供给料管;301、玻璃液注入槽;302、成型翼板;303、溢流挡砖;304、加热装置;305、牵引大滚轮;306、牵引小滚轮;307、载板玻璃;308、主动导向装置;309、输送装置。
具体实施方式
17.下面结合附图和实施例对本发明作进一步的说明:实施例1:如图1-6所示,本发明所述的一种载板玻璃成型生产成型装置,包括配合料熔融部件1、玻璃液澄清均化部件2和玻璃成型部件3,配合料熔融部件1包括熔融炉102,混合料在熔融炉102中熔融成玻璃液103,玻璃液澄清均化部件2包括玻璃液澄清仓202和玻璃液均化装置205,玻璃液103经玻璃液澄清仓202和玻璃液均化装置205进行澄清和均化后输送至玻璃成型部件3中进行成型,玻璃成型部件3包括玻璃液注入槽301,玻璃液注入槽301的外部设有溢流成型装置,溢流成型装置的外部玻璃牵引部件,玻璃液103注满玻璃液注入槽301后流向溢流成型装置和玻璃牵引部件后形成载板玻璃307。
18.熔融炉102的外部设有螺旋加料装置101,所述配合料通过螺旋加料装置101输送至熔融炉102中。
19.熔融炉102和玻璃液澄清仓202之间连接有提升料道201,玻璃液澄清仓202和玻璃液均化装置205之间连接有冷却料道204,所述玻璃液澄清仓202的上方设有排气口203,玻璃液均化装置205内设有搅拌杆206。
20.玻璃液均化装置205和玻璃液注入槽301之间连接有成型供给料管207,所述成型供给料管207的出料口位于玻璃液注入槽301中心位置。
21.玻璃液注入槽301为u型槽,所述溢流成型装置为成型翼板302,成型翼板302位于u型槽外部的左右两侧,u型槽和成型翼板302两端设置有溢流挡砖303,控制玻璃液103的流向,所述成型翼板302的下缘设有加热装置304。
22.玻璃牵引部件包括牵引大滚轮305和牵引小滚轮306,所述牵引大滚轮305和牵引小滚轮306相配合进行夹持牵引,引导载板玻璃307成型。
23.玻璃牵引部件的下方设有主动导向装置308,主动导向装置308用于引导载板玻璃307前移,主动导向装置308的末端设有输送装置309。
24.本实施例的工作原理为:配合料通过螺旋加料装置101均匀输送至熔融装置102内,配合料在熔融装置102内经过燃气纯氧燃烧、电能提供原料熔化所需要的热能,熔化为玻璃液103。熔融的玻璃液103经提升料道201将玻璃液103输送至玻璃液澄清仓202,玻璃液103在玻璃液澄清仓202内澄清,去除气泡,气泡及挥发物等杂质经排气口203排出。
25.澄清的玻璃液103经冷却料道204对玻璃液103初降温,流向玻璃液均化装置205,
通过搅拌杆206对玻璃液103进行均化搅拌,搅拌杆转速为6-10r/min。
26.均化玻璃液经成型供给料管207调节温度、调节粘度,控制流速,流入玻璃液注入槽301。玻璃液注入槽301为u型槽,供料管出料口在u型槽中心位置,相较于传统的单侧供料模式,更能保证u型槽内的温度均匀,避免了u型槽两端出现温差。
27.玻璃液103流入u型槽,注满u型槽后,溢流向成型装置两侧的成型翼板302,取成型翼板302坡度为6-10
°
。玻璃液103的流速可以通过调节成型供给料管207的温度。u型槽及成型翼板302两端设置有溢流挡砖303,控制玻璃液103的流向。成型翼板302下缘设计两根sic加热装置,维持两侧成型翼板302的温度,保证两侧成型翼板302的玻璃液流速。
28.u型槽注满后,玻璃液103在成型翼板302翼缘处汇聚,依靠玻璃液103本身重力,牵引大滚轮305和牵引小滚轮306夹持载板玻璃,经定型,牵引形成最后的载板玻璃307,牵引装置玻璃板温度设计700-800℃。
29.设计牵引大滚轮305为大滚轮,滚轮表面设计凸点,306为小滚轮,表面设计为平面结构,通过大滚轮和小滚轮夹持牵引,引导载板玻璃307成型。
30.载板玻璃307由主动导向装置308引导载板玻璃307前移,在此区间载板玻璃307逐步降温至40-50℃。
31.载板玻璃307经主动导向装置308输送至传输装置309。载板玻璃307在传输装置309经过切割机切割,设计切割机与载板玻璃307同速。最终载板玻璃307经品质检验,完成包装。
32.实施例2:本发明所述的一种载板玻璃成型生产成型方法,包括以下步骤:s1:在配合料中增加碎玻璃,将混合料输送至熔融炉102内,熔融成玻璃液;s2:熔融玻璃液输送至玻璃液澄清仓202,经搅拌杆进行材质均化,经料道输送至玻璃液注入槽301;s3:熔融玻璃液注满玻璃液注入槽301后流向两侧成型翼板302,玻璃液下流形成载板玻璃307;s4:载板玻璃307通过牵引大滚轮305和牵引小滚轮306提供下拉动力,使载板玻璃307由垂直方向,变为水平方向;s5:通过主动导向装置308引导载板玻璃307向前方行走至输送装置309;s6:在输送装置309上载板玻璃经过切割、检验,最终形成半成品载板玻璃。
33.本实施例的工作原理为:在载板玻璃307生产过程中配合料制备中增加原料-碎玻璃,以降低原材料的使用量,降低载板玻璃生产运行成本;碎玻璃为生产过程中切边玻璃和缺陷废弃玻璃,经重新粉碎、筛选获得,不增加公司的碎玻璃采购成本;碎玻璃可以降低熔融过程中的天然气和电能的消耗,节省载板玻璃成产运行成本;同时可以加速玻璃的熔制过程,降低玻璃熔制的热量消耗,可以达到废物利用的目的,避免环境污染,降低生产运行成本。
34.载板玻璃板翼型成型装置采用单侧溢流下拉。相较于传统的两侧溢流法,有效避免了溢流下拉法对玻璃板两侧厚度比例难以控制的问题。厚度不均匀使造成载板玻璃应力大的一项重要因素,载板厚度是调整载板其他品质的基础。
35.翼型成型装置可以实现单料道双成型方法,可以实现产量两倍的增长,最大限度
的节省建设费用,节约能源,提升公司的产能,达到效益最大化。
36.如图3所示,成型装置,双侧形成,规格尺寸一致,厚度一致,实现2倍的载板玻璃产出量。厚度不一致,制造不同厚度载板玻璃。
37.如图6所示,成型装置,双侧成型,厚度一致,生产不同规格尺寸的载板玻璃;厚度不一致,生产不同规格尺寸的载板玻璃。实现翼型成型装置实现产品厚度、规格尺寸多样化,实现公司产品的多样化,增强公司核心竞争力。
38.实施例3:在实施例2的基础上,配合料中碎玻璃含量占比为30%,sio2占比为42.02% ,al2o3占比为11.97%,b2o3占比为8.65%,cao占比为6.32%,mgo占比为0.85%,na+k占比为0.12%,其他占比为0.07%。
39.加料量设定为350kg/h,采用天然气纯氧燃烧,电能加热,燃料热量占比40%,需要天然气量为120m
³
/h,电能为350kw/h。
40.实施例4:在实施例2的基础上,配合料中碎玻璃含量占比为40%,sio2占比为34.89% ,al2o3占比为10.12%,b2o3占比为7.12%,cao占比为6.89%,mgo占比为0.75%,na+k占比为0.08%,其他占比为0.15%。
41.加料量设定为350kg/h,采用天然气纯氧燃烧,电能加热,燃料热量占比40%,需要天然气量为115m
³
/h,电能为320kw/h。
42.实施例3和实施例4中碎玻璃30%提升到40%,原材料节省10%,燃气耗量降低5m
³
/h,电能降低30kw/h。通过本方法能够加速玻璃的熔制过程,降低玻璃熔制的热量消耗,可以达到废物利用的目的,避免环境污染,降低生产运行成本。碎玻璃产自生产过程中的切边玻璃以及缺陷废弃玻璃,碎玻璃加工粒度在2~10mm之间。
43.采用以上结合附图描述的本发明的实施例的一种载板玻璃成型生产成型装置及其方法,成型装置采用单侧溢流下拉,相较于传统的两侧溢流法,有效避免了溢流下拉法对玻璃板两侧厚度比例难以控制的问题。厚度不均匀使造成载板玻璃应力大的一项重要因素,载板厚度是调整载板其他品质的基础。通过成型装置的改进可以实现单料道双成型,实现产量两倍的增长,最大限度的节省建设费用,节约能源,方法中通过优化混合料的配比工艺,降低混合料熔化过程温度,降低载板玻璃成产建设成本;进一步降低天然气、电能的消耗,降低载板玻璃生产制造运行成本。优化载板玻璃成型方法,提高载板玻璃板产量,提升产能,增加公司生产效益。解决了现有技术中存在的问题。但本发明不局限于所描述的实施方式,在不脱离本发明的原理和精神的情况下这些对实施方式进行的变化、修改、替换和变形仍落入本发明的保护范围内。