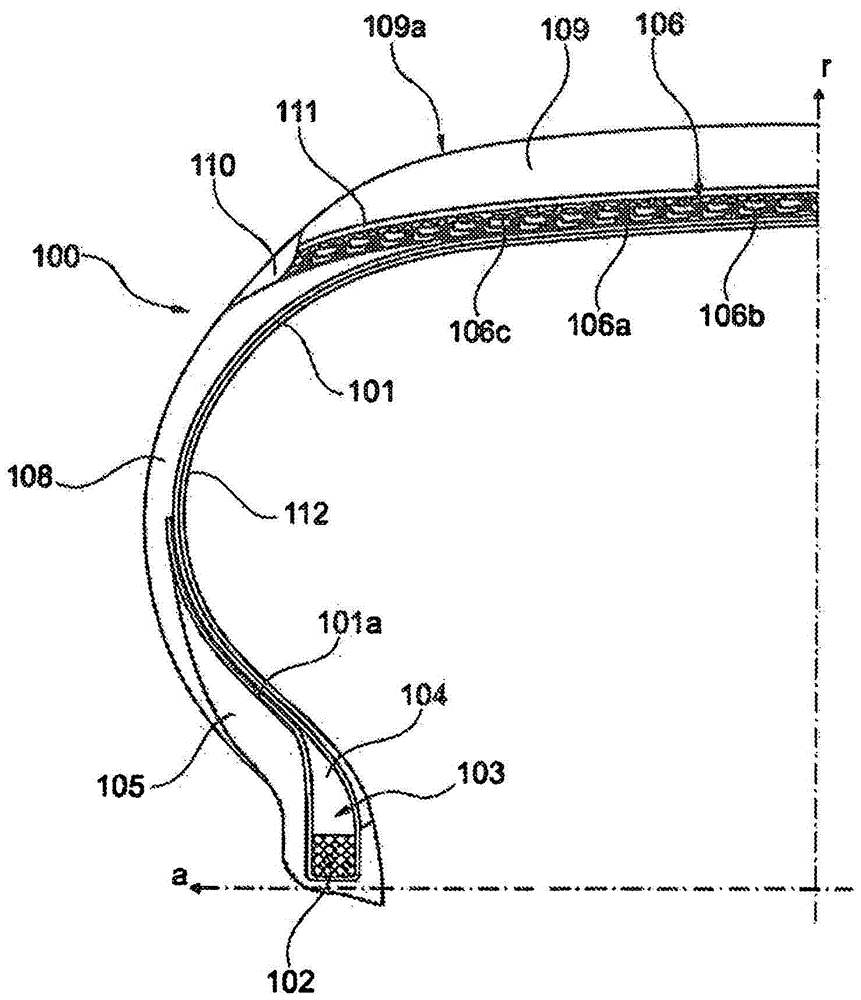
本发明涉及车轮的轮胎。更特别地,本发明涉及轮胎,其包含至少一个结构元件,该结构元件通过交联包含碳纳米管的可交联的弹性体组合物而获得,该碳纳米管用基本上没有co、ni和mo的铁氧化物和/或铝氧化物基催化剂来获得。现有技术在橡胶工业中,特别是在轮胎生产中,通常使用弹性体组合物,在该弹性体组合物中增强填料已经引入到弹性体聚合物基料中,以改进所获得的交联产物的特性、特别是力学性能。归因于其高增强效率,炭黑是特别有用的增强填料。尽管如此,炭黑代表不可再生原材料,其主要来源于化石燃料的部分燃烧过程,该化石燃料主要是石脑油或石油、甲烷气和其他烃的其他衍生物。另外,炭黑可以是一种环境问题,因为其如果没有正确处置则是潜在的污染物。目前用来生产轮胎的结构元件(特别是外部元件如胎面和胎侧)的许多弹性体组合物是通过引入二氧化硅基增强填料来制造的。该二氧化硅基增强填料允许在低滚动阻力、在潮湿或积雪表面上行进、耐磨性方面获得各种优点。在现今的轮胎中,用二氧化硅基增强填料部分地取代炭黑已经在装备有这样的轮胎的车辆上产生了静电聚集现象,因为与炭黑相反,二氧化硅基增强填料不是导电性的,并且因此不能将通过车轮滚动以及随后的车辆移动产生的静电释放到地上。出于克服该缺点的目的,轮胎制造商已经制造了包含导电条的轮胎,该导电条用包含炭黑或其他导电材料的混合物制造,浸入在胎面结构和/或胎侧中,为了获得车辆的合适接地的目的。这样的轮胎的实施方案描述在相同申请人的ep658452中。这样的导电条的制造包括几个缺点。从生产观点来说,获得这样的条需要使用另外的途径以及在将要形成轮胎胎面的混合物的挤出中使用更复杂的装置。在本领域中,已经提出了用混合有碳纳米管的混合物来制造整个胎面,以恢复轮胎正确的导电性。这样的轮胎和/或用于含有碳纳米管的轮胎部件的混合物的实施方案描述在ep2338697、de10/2007/056689和wo03/060002中。该碳纳米管通过如下方式来制备:使含碳(典型地为甲烷、乙烯或者乙炔)的气态化合物在高温(约700℃)下通过基于金属纳米颗粒的催化剂。通常所用的催化剂基于负载在sio2、al2o3或mgo上的fe-ni、fe-co或fe-mo,并且通常用浸渍、共沉淀和溶胶-凝胶技术来制备。在浸渍技术中,载体是预成形的,而在共沉淀和溶胶-凝胶技术中,载体和催化剂二者都是从其组分的可溶性盐(如硝酸盐和/或碳酸盐)开始,借助于加入合适的碱性物质来引起它们的共沉淀而形成的。在溶胶-凝胶技术中,凝胶的形成通常借助于加入凝胶化有机物质来进行。用于合成碳纳米管的制备催化剂的实例描述在avdeeva,l.b.等,“iron-containingcatalystsofmethanedecomposition:accumulationoffilamentouscarbon”,appliedcatalysisa:general228,53-63(2002),reshetenko,t.v.等,“coprecipitatediron-containingcatalysts(fe-al2o3,fe-co-al2o3,fe-ni-al2o3)formethanedecompositionatmoderatetemperatures:partii.evolutionofthecatalystsinreaction”,appliedcatalysisa:general270,87-99(2004),kukovecz,a.等,“catalyticsynthesisofcarbonnanotubesoverco,feandnicontainingconventionalandsol-gelsilica-aluminas”,physicalchemistrychemicalphysics2,3071-3076(2000)和专利申请wo2007/93337、wo2007/33438和ep2213369中。用前述催化剂制备碳纳米管的实例也描述在专利和专利申请如ep1797950、ep2223743、us7923615、us8398949、us2001/0014307和wo2013/105779中。本发明的概述用根据传统技术所制造的催化剂制造的纳米管具有若干缺点。主要缺点在于在碳纳米管结构中存在高催化剂残留物,通常高于10重量%,而且高于20重量%,相对于该碳纳米管结构的总重量。这种高催化剂残留物的存在需要使用通常用于降低残留物的量的净化技术,这使得将碳纳米管用于轮胎工业中是经济上不便的。另一缺点在于在残留物中存在高百分比的用于制造该催化剂的污染金属,特别是ni、co和mo。污染金属以及特别是ni、co和mo的存在使得将用传统技术制造的纳米管用于轮胎工业中是不可取的。本申请人已经面临这样的问题,制造包含克服前述缺点的碳纳米管的轮胎。本申请人还面临这样的问题,制造具有降低的催化剂残留物含量的碳纳米管,并且避免使用特别是污染金属如ni、co和mo。本申请人已经发现该问题通过使用基本上缺乏这样的污染金属的催化剂,通过仅使用分散在al2o3中的fe能够被解决,然而验证了使用传统制备技术所获得的催化剂所提供的碳纳米管仍然需要净化以降低催化剂残留物的量。本申请人还面临着这样的问题,制造特别是在碳/催化残留物比方面有效的铁氧化物和/或铝氧化物基催化剂。在大量不成功的尝试之后,本申请人已经发现通过在合适的实验条件下工作,能够制造如下这样的铁氧化物和/或铝氧化物基催化剂,其基本上没有污染金属,其允许获得相对于该碳纳米管结构的总重量催化剂残留物的百分比低于10重量%、优选低于5重量%、更优选低于3重量%且甚至更优选低于2重量%的碳纳米管。特别地,本申请人已经发现这样的结果通过如下方式制备催化剂而获得:首先在试剂浓度和其相对添加时间的合适的条件下工作,并且合适地控制该混合物的ph,以便获得含有铁和/或铝氢氧化物的无机凝胶的生成,和随后在空气或氮气气氛下在合适的温度条件下干燥并煅烧这种凝胶。本申请人还已经令人惊讶地发现通过将用这种催化剂获得的碳纳米管用在制造轮胎用的弹性体组合物中,除了克服本领域已知的且以上所描述的缺点之外,还获得了改进的力学性能,特别是更大的且改进的拉伸强度和极限伸长率的值,以及因此改进的轮胎的抗冲击和抗撕裂性,其是用于生产轮胎的外部元件(如胎侧和胎面)的混合物中特别期望的特性。因此在第一方面,本发明涉及车轮的轮胎,其包含至少一个结构元件,该结构元件包含通过交联包含碳纳米管的可交联的弹性体组合物而获得的交联的弹性体材料,其中所述碳纳米管用基本上没有co、ni和mo的铁氧化物和/或铝氧化物基催化剂来获得。特别地,所述轮胎包含至少一个胎体结构,该胎体结构具有与各自的增强环形结构相连的相对的横向边缘,在相对于所述胎体结构的径向外部位置施加的带束层结构,在相对于所述胎体结构的径向外部位置施加的胎面带(treadband),和在相对于所述胎体结构的相对侧上横向施加的一对胎侧。有利地,所述结构元件选自胎面带、胎侧、胎侧插入件、相对于所述胎面带径向内部的弹性体材料层如内层和迷你胎侧、胎圈结构以及织物和金属的橡胶涂层。在第二方面,本发明涉及一种生产基本上没有co、ni和mo的铁氧化物和/或铝氧化物基催化剂的方法,包括以下步骤:·制备包含fe3+可溶性盐和al3+可溶性盐的水溶液(i),其中fe3+的摩尔浓度为0.3-1.5m,和al3+的摩尔浓度为0.8-2.4m,·制备包含氢氧化铵的水溶液(ii),其中nh3摩尔浓度为1.8-18m,·将溶液(ii)以如下这样的方式加入到溶液(i)中:加入1.3×10-4-4.5×10-1摩尔/总铁和/或铝摩尔/分钟的量的nh3,直到ph为6-8,在此ph下发生该溶液的凝胶化,·将该凝胶在35℃-100℃的温度下干燥,以及·将所获得的固体在250℃-750℃的温度下在空气或氮气气氛下煅烧。在本说明书和以下的权利要求中,关于表述“铁氧化物和/或铝氧化物基”,其旨在表示铁氧化物、铝氧化物和/或混合的铁和铝氧化物的混合物。特别地,用本发明的方法获得的催化剂包含铁氧化物、铝氧化物和/或混合的铁和铝氧化物的混合物,其选自赤铁矿(fe2o3)、磁铁矿(fe3o4)、方铁矿(feo)、铁尖晶石(feal2o4)、其他混合的铁和铝氧化物(fe(1+x)al(2-x)o4)(其中x是0.0-2.0的小数)和氧化铝(al2o3)。该组分的精确组成和结晶度取决于所选择的起始试剂和所使用的操作条件,特别是煅烧的那些。另外,本发明的第三方面涉及一种制备碳纳米管的方法,包括以下步骤:·将在多孔材料上的催化剂装入反应室中,·使所述反应室的温度达到反应温度,和·在该反应室中流通(fluxing)一种或多种气态烃的气态流,其特征在于所述催化剂是用本发明的制备方法所获得的基本上没有co、ni和mo的铁氧化物和/或铝氧化物基催化剂。关于用本发明方法所制造的催化剂中存在的co、ni和mo的含量使用表述“基本上没有”旨在表示低于0.1ppm、优选低于0.01ppm、更优选低于0.001ppm的量。有利地,用本发明方法所制造的催化剂中存在的co、ni和mo的含量低于这样的金属的测定限(lod)。根据本发明的车轮的轮胎包含结构元件,该结构元件通过交联包含用本发明方法所获得的碳纳米管的可交联的弹性体组合物来制造。制备碳纳米管的方法通常包括在置于反应炉中的反应器内的达到反应温度的催化剂上的碳源(典型地为气态的如甲烷和/或乙烷和/或乙烯和/或乙炔)的通道。在该升温步骤期间,可使通常包含惰性气体如氮气和/或氩气的气态流流动以消除通常大气中天然存在的氧。优选地,这样的气态流用含有0.4-1个大气压的惰性气体、0-0.4个大气压的烃和0-0.4个大气压的氢的混合物(总是使总压力等于约1个大气压)在等于约1个大气压的压力下流动。在该纳米管形成期间,该气态碳源优选与惰性气体、以及通常与充当催化剂的还原剂的氢混合,并且能够有利于选择性并有利于延长催化剂本身的寿命。该气态流可然后由二元或三元混合物构成,其总压力通常等于约1个大气压。通常,该混合物可含有0.4-0.9个大气压的惰性气体、0.1-0.6个大气压的烃和0-0.5个大气压的氢(总是使总压力等于约1个大气压)。更特别地,在使用三元气态混合物(即包含碳源、惰性气体和氢)的情况下,碳源的分压在0.1-0.5个大气压、优选0.2-0.4个大气压的区间,惰性气体的分压在0.3-0.8个大气压、优选0.4-0.6个大气压的区间,和氢气的分压在0.1-0.6个大气压、优选0.2-0.5个大气压的区间。将催化剂置于装备有充当气体分布器的多孔隔膜的反应器(优选圆柱体)中。反应温度可首先通过在惰性气体流中加热该催化剂、并且然后进料三元或二元气态混合物,或者通过在室温下进料三元或二元气态混合物、并且然后逐渐升温直到反应温度来达到。该反应温度为550-750℃、优选600-700℃且更优选约650℃。可替代地,在进料气态混合物和碳源之前,催化剂的还原在预备步骤中发生。在这样的情况中,该制备方法包括第一步骤:用包含惰性气体和氢的第一种二元气态混合物进料,和随后的第二步骤:用包含惰性气体和碳源如甲烷和/或乙烷和/或乙烯的第二种二元混合物进料,两个步骤都是在反应温度下进行。同样在这种情况下,反应温度可通过在惰性气体流中加热在反应炉内的反应器中的催化剂,或者通过在室温下进料第一种二元混合物并逐渐升温直到反应温度来事先达到。在使用二元气态混合物(即包含混合物中的碳源或氢与惰性气体)的情况下,碳源或氢的分压在0.1-0.5个大气压、优选0.2-0.4个大气压的区间,而惰性气体的分压在0.5-0.9个大气压、优选0.6-0.8个大气压的区间。在所有情况中,反应温度借助于5-50℃/min、优选5-20℃/min的受控的斜坡(ramps)来达到。优选地,该反应温度通过在惰性气体流中预热在反应炉内的反应器中的催化剂来事先达到。根据本发明的一方面,将用本发明方法所获得的催化剂引入到置于炉中的反应器中,使其在惰性气体流中达到反应温度,在氢和惰性气体二元混合物流中还原,并且然后以惰性气体和碳源的二元混合物进料。根据本发明的另一方面,将用本发明方法所获得的催化剂引入到在室温下的反应器中,并且然后以惰性气体、氢和碳源的三元混合物进料,逐渐将炉温升高到反应温度。根据本发明的进一步的方面,将用本发明方法所获得的催化剂引入到反应炉中,使其在惰性气体流中达到反应温度,并且然后以惰性气体和碳源的二元混合物进料。制备根据本发明的碳纳米管的方法包括使用用本发明方法所制备的催化剂。如上所述,可用于本发明的催化剂通过如下方式来获得:在试剂浓度及其相对添加时间的合适条件下工作,和合适地控制混合物的ph,以便获得含有铁氢氧化物和/或铝氢氧化物的无机凝胶的生成,和随后在空气或氮气气氛下且在合适的温度条件下干燥并煅烧所得凝胶。特别地,包含fe3+可溶性盐和al3+可溶性盐的水溶液(i)包含0.3-1.5m、优选0.5-1.1m的fe3+摩尔浓度,和0.8-2.4m、优选1.2-1.8m的al3+摩尔浓度。在本发明的方法中,可使用任何fe3+可溶性盐,优选硝酸铁、硫酸铁、碳酸铁、乙酸铁、柠檬酸铁、葡萄糖酸铁、草酸铁、草酸铵铁和硫酸三(乙二胺)铁。在水中具有高溶解度的铁盐是优选的,例如硝酸铁和草酸铵铁。铁盐水合物如硝酸铁九水合物和草酸铵铁三水合物是有利地使用的。在本发明的方法中,可使用任何al3+可溶性盐,优选硝酸铝、氯化铝、硫酸铝、碳酸铝、乙酸铝、柠檬酸铝、葡萄糖酸铝和草酸铝。在水中具有高溶解度的铝盐是优选的,例如硝酸铝。铝盐水合物如硝酸铝九水合物是有利地使用的。金属离子fe3+和al3+在水溶液(i)中的总摩尔浓度为1.1m-3.9m、优选2.0m-2.5m且更优选2.2m-2.4m。包含氢氧化铵的水溶液(ii)包含1.8-18m、优选包含10-18m的nh3摩尔浓度。在本发明的方法中,将溶液(ii)加入到溶液(i)以受控方式发生,特别是以使得加入nh3的量为1.3×10-4-4.5×10-1摩尔/总铁和铝摩尔/分钟、优选2.5×10-4-2×10-1摩尔nh3/总铁和铝摩尔/分钟的方式发生。添加包含氢氧化铵的溶液(ii)引起ph升高直到6-8的值,在此ph下发生所得水溶液的凝胶化,并且形成引入所有水性溶剂的单一凝胶化物质。在本发明的方法中,所得凝胶在35℃-100℃、优选55℃-80℃的温度下干燥。该干燥步骤优选在烘箱中进行,在搅拌下维持该物质,以优化溶剂的除去。该干燥步骤优选进行6-12小时的时间段,和在任何情况下直到除去由凝胶引入的水性溶剂并获得固体残留物。干燥后所获得的固体残留物优选轻微研磨,获得4-90μm、优选10-50μm的所得粉末的颗粒尺寸。在本发明的方法中,将该固体残留物在250℃-750℃、优选350℃-650℃、更优选450℃-550℃的温度下,在空气或氮气气氛下煅烧。该煅烧步骤优选进行30分钟至4小时、优选1-2小时的时间段。煅烧后获得的固体残留物优选轻微研磨,获得以平均表面等效球形直径表达的10μm-150μm、优选15μm-120μm且更优选30μm-100μm的所得粉末的颗粒尺寸。用本发明的方法所获得的催化剂表现出0.300-0.900g/cm3、优选0.350-0.850g/cm3且更优选0.450-0.750g/cm3的表观密度。用本发明的方法所获得的催化剂表现出50-500m2/g、优选100-400m2/g且更优选150-300m2/g的表面积。用本发明的方法所获得的催化剂优选包含高于30重量%、更优选等于或高于35重量%且甚至更优选等于或高于45重量%的标称铁含量(将催化剂配制剂标准化为fe+al2o3)。本申请人已经发现通过增加铁在用本发明的方法所获得的催化剂中存在的百分比,能够获得如下这样的碳纳米管:其具有较高的纯度和较低的残留百分比(低于10重量%且甚至更低),避免了进一步净化的需要。本申请人因此发现在进料含碳源的二元或三元混合物之前,用惰性气体和氢的混合物预处理或不预处理用本发明的方法所获得的催化剂不导致在所获得的纳米管的纯度、或者纳米管的沉积速度或者纳米管的生成反应的选择性方面的显著差异。如上所述,根据本发明一方面的车轮的轮胎包含结构元件,该结构元件通过交联包含用本发明方法所获得的碳纳米管的可交联的弹性体组合物来制造。优选地,所述可交联的弹性体组合物包含0.5phr-5phr、更优选1phr-4phr且甚至更优选2phr-3phr的量的所述碳纳米管。有利地,所述碳纳米管包含相对于该碳纳米管结构的总重量计等于或高于90重量%、优选等于或高于95重量%、更优选等于或高于97重量%且甚至更优选等于或高于98重量%的碳百分比。在用本发明的方法所获得的纳米管中存在的催化剂的残留百分比相对于该碳纳米管结构的总重量计有利地低于10重量%、优选低于5重量%、更优选低于3重量%且甚至更优选低于2重量%。用于本发明轮胎的纳米管有利地表现出高于10:1、优选高于20:1、更优选高于40:1且甚至更优选高于50:1的碳:残留催化剂(c/r)重量比。优选地,用于本发明范围的可交联的弹性体组合物包含分散在至少一种二烯弹性体聚合物中的碳纳米管。根据一种优选的实施方案,可用于本发明的二烯弹性体聚合物可选自常用于可用硫交联的弹性体材料的那些,其特别适于生产轮胎,即选自具有玻璃化转变温度(tg)通常低于20℃、优选在0℃至110℃的区间的不饱和链的弹性体聚合物或共聚物。这些聚合物或共聚物可以是天然来源的或者它们可借助于一种或多种共轭二烯烃(可能混合有选自单乙烯基芳烃和/或极性共聚单体的至少一种共聚单体)的溶液聚合、乳液聚合或气相中聚合来获得。该共轭二烯烃通常含有4-12、优选4-8个碳原子并且可例如选自:1,3-丁二烯、异戊二烯、2,3-二甲基-1,3-丁二烯、1,3-戊二烯、1,3-己二烯、3-丁基-1,3-辛二烯、2-苯基-1,3-丁二烯或其混合物。1,3-丁二烯和异戊二烯是特别优选的。可以用作共聚单体的单乙烯基芳烃通常含有8-20、优选8-12个碳原子并且可例如选自:苯乙烯;1-乙烯基萘;2-乙烯基萘;各种烷基衍生物,环烷基衍生物,芳基衍生物,苯乙烯的烷基芳基或者芳基烷基衍生物如α-甲基苯乙烯、3-甲基苯乙烯、4-丙基苯乙烯、4-环己基苯乙烯、4-十二烷基苯乙烯、2-乙基-4-苄基苯乙烯、4-对甲苯基苯乙烯、4-(4-苯基丁基)苯乙烯,或其混合物。苯乙烯是特别优选的。可使用的极性共聚单体可选自例如:乙烯基吡啶,乙烯基喹啉,丙烯酸酯和烷基丙烯酸酯、腈或其混合物如丙烯酸甲酯、丙烯酸乙酯、甲基丙烯酸甲酯、甲基丙烯酸乙酯、丙烯腈或其混合物。优选地,可用于本发明的二烯弹性体聚合物可选自例如:顺式-1,4-聚异戊二烯(天然或者合成的、优选天然橡胶),3,4-聚异戊二烯,聚丁二烯(特别是具有高含量的1,4-顺式聚丁二烯),异戊二烯/异丁烯共聚物(可能被卤化),1,3-丁二烯/丙烯腈共聚物,苯乙烯/1,3-丁二烯共聚物,苯乙烯/异戊二烯/1,3-丁二烯共聚物,苯乙烯/1,3-丁二烯/丙烯腈共聚物或其混合物。前述的弹性体组合物可包含一种或多种单烯烃和烯烃共聚单体的至少一种弹性体聚合物或其衍生物。该单烯烃可选自:乙烯和通常含有3-12个碳原子的α-烯烃如丙烯、1-丁烯,1-戊烯、1-己烯、1-辛烯或其混合物。以下是优选的:来自乙烯和α-烯烃(可能有二烯)之间的共聚物;异丁烯均聚物或其与少量二烯的共聚物(可能至少部分被卤化)。可能存在的二烯通常含有4-20个碳原子并且优选选自:1,3-丁二烯、异戊二烯、1,4-己二烯、1,4-环己二烯、5-亚乙基-2-降冰片烯、5-亚甲基-2-降冰片烯,乙烯基降冰片烯或其混合物。在这些之中,以下是特别优选的:乙烯/丙烯(epr)共聚物或者乙烯/丙烯/二烯(epdm)共聚物;聚异丁烯;丁基橡胶;卤化丁基橡胶,特别是氯丁基或溴丁基橡胶;或其混合物。还可使用二烯弹性体聚合物或借助于与合适的封端剂或偶联剂反应来官能化的弹性体聚合物。特别地,借助于在有机金属引发剂(特别是有机锂引发剂)存在下的阴离子聚合所获得的二烯弹性体聚合物可通过使衍生自引发剂的残留的有机金属基团与合适的封端剂或偶联剂如亚胺、碳二酰亚胺、烷基锡卤化物、取代的苯甲酮、烷氧基硅烷或芳氧基硅烷反应来官能化。根据一种优选的实施方案,所述弹性体组合物还包含主要由二氧化硅和/或硅酸盐构成的增强填料。可用于本发明的二氧化硅可通常为热解二氧化硅或者优选沉淀二氧化硅,具有约50m2/g至约500m2/g、优选约70m2/g至约200m2/g的bet表面积(根据标准iso5794/1测量)。可根据本发明使用且可在市场上获得的二氧化硅增强填料的实例是以名称190、210、233、243已知的产品,其可获自ppgindustries(pittsburgh,pa);或者以evonik的名称vn2、vn3已知的产品;或者以rhodia的名称1165mp已知的产品。至少一种另外的增强填料可有利地以通常1phr-70phr、优选约10phr至约60phr的量加入到上述弹性体组合物中。该增强填料可选自常用于交联的产物的那些,特别是用于轮胎的那些,例如炭黑、氧化铝、铝硅酸盐、碳酸钙、高岭土或其混合物。有利地,所述可交联的弹性体组合物包含硫化剂。该可交联的弹性体组合物可根据已知的技术来硫化,特别是用常用于二烯弹性体聚合物的硫基硫化体系来硫化。出于该目的,在该材料中,在一种或多种形变热处理阶段之后,将硫基硫化剂与硫化促进剂一起引入。在最终的处理步骤中,温度通常维持低于120℃且优选低于100℃,以防止任何不期望的预交联现象。优选地,所述硫化剂包含这样的硫基硫化体系,其包含硫或含硫分子(硫给体)以及本领域已知的硫化促进剂和/或硫化活化剂。特别有效的活化剂由锌化合物组成并且特别是zno、znco3、含有8-18个碳原子的饱和或不饱和脂肪酸的锌盐如硬脂酸锌,其优选通过zno和脂肪酸或其混合物在该弹性体组合物中原位形成。常见地使用的促进剂可选自:二硫代氨基甲酸酯、胍、硫脲、噻唑、亚磺酰胺、秋兰姆、胺、黄原酸盐或其混合物。根据一种优选的实施方案,所述可交联的弹性体组合物包含等于或高于约1phr、优选等于或高于约2phr的量的硫化剂。优选地,硫化剂的量低于或等于约7.5phr、优选低于或等于约7。有利地,硫的量为约2phr至约6.5phr。根据一种优选的实施方案,所述弹性体组合物包含硅烷偶联剂,其能够与作为增强填料存在的二氧化硅和/或硅酸盐相互作用并且在硫化期间将它们结合到二烯弹性体聚合物上。根据一种优选的实施方案,可用于本发明的硅烷偶联剂可选自具有至少一种可水解硅烷基团的那些,其例如可由以下通式(ii)定义:(r)3si-cnh2n-x(ii)其中r基团(可相同或者不同)选自:烷基、烷氧基或芳氧基或卤素原子,条件是r基团的至少之一为烷氧基或芳氧基;n是1-6(包括6)的整数;x是选自以下的基团:亚硝基、巯基、胺、环氧化物、乙烯基、酰亚胺、氯、-(s)mcnh2n-si-(r)3或者-s-cor,其中m和n是1-6(包括6)的整数且r基团如上所定义。在该硅烷偶联剂中,特别优选的那些是双(3-三乙氧基甲硅烷基丙基)四硫化物和双(3-三乙氧基甲硅烷基丙基)二硫化物。所述偶联剂可以原样使用或者作为与惰性填料合适的混合物使用,以便有利于它们引入到弹性体组合物中。根据一种优选的实施方案,所述硅烷偶联剂以0.01phr至约10phr、优选约0.5phr至约5phr的量存在于该弹性体组合物中。所述弹性体组合物可包含其他常用的添加剂,其基于该组合物所预期的具体应用来选择。例如可将以下物质加入到所述材料中:抗氧化剂、抗老化剂、增塑剂、粘合剂、抗臭氧剂、改性树脂或其混合物。特别地,出于改进可加工性的目的,可将增塑剂加入到所述弹性体组合物中。这样的增塑剂通常选自矿物油、植物油、合成油或其混合物,例如芳香油、环烷油、大豆油或其混合物。增塑剂的量通常为0phr至约70phr、优选约5phr至约30phr。该弹性体组合物可通过将该聚合物组分与增强填料和可能存在的其他添加剂根据本领域已知的技术混合在一起来制备。该混合可例如使用“开炼机”型的敞口混合器和/或具有切线转子型和/或具有互锁转子型(intermixtm)的密炼机进行,和/或在ko-kneadertm型和/或双螺杆或多螺杆型的连续混炼机中进行。附图说明以下将参考附图来阐述本说明书,附图仅作为非限定性实例来提供并且其中:图1以半横截面示出了根据本发明第一实施方案的机动车轮的轮胎,图2以半横截面示出了根据本发明第二实施方案的机动车轮的轮胎,图3表示如实施例1中所述获得的催化剂cat-1sg-35-a的衍射光谱,图4表示如实施例1中所述获得的催化剂cat-1sg-35-n2的衍射光谱,和图5表示如实施例2中所述获得的催化剂cat-2sg-35-n2的衍射光谱。本发明的详细描述在图1和2中,“a”表示轴向且“r”表示径向。为了简要起见,图1和2仅仅显示了轮胎的一部分,其余未显示的部分是相同的并且相对于径向“r”对称布置。参见图1,机动车轮的轮胎100包含至少一个胎体结构,该胎体结构包含至少一个具有各自的相对端垫带的胎体层101,该垫带与各自的锚定环形结构102(称作胎圈芯,可能与胎边芯104相连)相接合。包含胎圈芯102和胎边芯104的轮胎区域形成了增强环形结构103(所谓的胎圈),其旨在用于将轮胎锚定到相应的安装轮辋(未示出)上。增强环形结构103和特别是胎边芯104有利地用之前描述的包含纳米管的弹性体组合物来制造,因为这样的元件在轮胎滚动期间的使用条件下特别经受机械应力(由于与车辆轮辋直接接触)。胎体结构通常是径向类型的,即至少一个胎体层101的增强元件位于这样的平面上,其包含轮胎旋转轴并且基本上垂直于轮胎的赤道平面。所述增强元件通常由纺织品帘线如人造丝、尼龙、聚酯(例如聚萘二甲酸乙二醇酯(pen))构成。每个增强环形结构借助于在锚定环形结构102周围的至少一个胎体层101的相对横向边缘的向后弯曲来与胎体结构相连,以便形成所谓的胎体101a的卷起元件,如图1所示。在一种实施方案中,胎体结构和增强环形结构之间的耦合可借助于在相对于第一胎体层的轴向外部位置施加的第二胎体层(图1中未示出)来提供。耐磨条105布置在每个增强环形结构103的外部位置。优选地,每个耐磨条105布置在相对于增强环形结构103的至少轴向外部位置,其至少在胎侧108和相对于增强环形结构103径向下部的部分之间延伸。优选地,布置耐磨条105以沿增强环形结构103的轴向内部和外部以及径向下部区域以一定方式包围该增强环形结构103,以便当轮胎100安装于轮辋上时,置于后者和车轮的轮辋之间。胎体结构与带束层结构106相连,该带束层结构包含一个或多个相对于彼此和相对于该胎体层径向重叠布置的带束层的层106a、106b,其具有典型的金属增强帘线。这种增强帘线可相对于轮胎100的圆周延伸方向具有交叉取向。“圆周”方向旨在表示通常根据轮胎旋转方向来定向的方向。在相对于带束层的层106a、106b径向更向外的位置,可施加至少一个零度增强层106c,通常称作“0°带束层”,其通常引入多个以基本上圆周方向取向的增强帘线(典型地为纺织品帘线),由此相对于轮胎的赤道平面形成了几度的角度(例如约0°-6°的角度),并且覆盖有弹性体材料。在相对于带束层结构106的径向外部位置,施加由弹性体混合物制成的胎面带109。由根据本发明获得的弹性体混合物制成的各自的胎侧108也以轴向外部位置施加到胎体结构的横向表面上,每个从胎面109的横向边缘之一延伸直到各自增强环形结构103。在径向外部位置,胎面带109具有旨在与地面接触的滚动表面109a。圆周花纹沟通常在该表面109a中制造,为了简要起见其在图1中显示为光滑的,圆周花纹沟通过横向切口(图1中未示出)连接以便限定出分布在滚动表面109a上的多个各种形状和尺寸的块。内层111排列在带束层结构106和胎面带109之间。由弹性体材料构成的条110(通常称作“迷你胎侧”)可存在于胎侧108和胎面带109之间的连接区域中,该迷你胎侧通常通过与胎面带109共挤出来获得,并且允许改进胎面带109和胎侧108之间的力学相互作用。优选地,胎侧108的端部直接覆盖胎面带109的横向边缘。胎面带和/或内层和/或迷你胎侧和/或胎侧和/或耐磨条和/或胎体结构和/或带束层结构的橡胶涂料混合物可有利地用前述包含纳米管的弹性体组合物来制造,因为更大的拉伸强度赋予了更大的抗撕裂性,以及因此的胎侧和胎面表面更大的耐受性和持久性,特别是在使用期间曝露于突然的机械应力(归因于例如路面的粗糙度,在停车操纵期间与人行道的冲击等)。另外,前述包含纳米管的弹性体组合物将是导电的,甚至在作为主填料的二氧化硅存在下也是如此,合作以构成轮辋和地面之间的导电路径。在没有内管的轮胎的情况下,橡胶层112(通常称作“内衬”,其为轮胎充气提供必需的不可透过性)也可以相对于胎体层101的径向内部位置提供。自支撑型轮胎100(其的一个实例示于图2中)包括能够在相当大的或者全部的压力损失下支撑车辆负荷的载体结构。特别地,根据本发明所制造的胎侧插入件(113)可与每个胎侧相连。在自支撑型轮胎(100)的每一侧中,胎侧插入件(113)在相关的胎圈结构(103)和相应的胎面带(109)的横向边缘之间径向延伸。每个胎侧插入件(113)可由一个或多个部分制造,并且位于相对于胎体帘布层的轴向内部或者外部位置上。例如,如图2中所示,胎侧插入件(113)位于胎体帘布层(101)和内衬(112)之间。可替代地,如果存在多于一个胎体帘布层,则胎侧插入件(113)可位于两个所述胎体帘布层之间(图2中未示出)。可替代地,胎侧插入件(113)可位于胎体帘布层和胎侧之间(图2中未示出)。该胎侧插入件可有利地用前述包含纳米管的弹性体组合物制成,因为在轮胎泄气的工作条件下,其必须具有良好的抗撕裂扩展性(当存在较高的断裂性能、特别是较高的极限伸长率性能时可获得)。根据一种未示出的实施方案,轮胎可以是用于重型运输车辆如卡车、巴士、拖车、箱式车以及通常用于其中轮胎承受高负荷的车辆的车轮的轮胎。根据另一未示出的实施方案,该轮胎可以是用于两轮车辆如摩托车的轮胎。上述轮胎100的构建可以借助于将各自的半成品在成型鼓(未示出)上通过至少一个组装设备进行组装来驱动。在该成型鼓上,可成型和/或组装旨在形成轮胎的胎体结构的部件的至少一部分。更特别地,调适该成型鼓以首先接收可能的内衬,然后是胎体结构和耐磨条。随后,设备(未示出)在每个端垫带周围同轴接合锚定环形结构之一,将包含带束层结构和胎面带的外部套筒定位在圆柱形胎体套筒的周围同轴居中的位置上,并且根据环形构造借助于胎体结构的径向膨胀来使该胎体套筒成形,以便确定其抵靠外部套筒的径向内表面施加。在成型该胎坯之后,进行模制和硫化处理,目的是借助于弹性体混合物的交联确定轮胎的结构稳定性以及在胎面带上赋予期望的胎面设计和在胎侧处赋予可能的区别图形标志。本文以下将借助于仅作为本发明的非限制性实施例提供的多个制备实施例来进一步说明本发明。实施例1制备cat-1sg-50-n2和cat-1sg-50-a将硝酸铁九水合物(126.66g)和硝酸铝九水合物(128.77g)溶解在140ml水中。将氢氧化铵溶液(约17m)在搅拌下滴下,直到ph约7,在此ph下发生凝胶化。氨的加入以恒定速度进行,并且持续30分钟。将该凝胶在60℃下干燥12小时,然后轻微研磨(平均表面等效球形直径(ds)37.88μm),然后将其分成等重量的2个等份,将一份在氮气流中并将另一份在空气流中在500℃下煅烧90分钟。因此分别获得了17.86g的cat-1sg-50-n2和17.40g的cat-1sg-50-a,具有相对于理论83%的总产率。催化剂二者均具有等于50重量%的标称催化剂含量(配制剂标准化为fe+al2o3)以及煅烧后等于0.412的铁的重量分数。以类似方式进行获得了催化剂cat-1sg-35-n2和cat-1sg-35-a,其中标称催化剂含量(配制剂标准化为fe+al2o3)等于35重量%且煅烧后铁的重量分数等于0.304,以及催化剂cat-1sg-25-n2和cat-1sg-25-a,其中标称催化剂含量(配制剂标准化为fe+al2o3)等于25重量%且煅烧后铁的重量分数等于0.226。下表1报告了所获得的催化剂的一些分析数据。平均表面等效直径从用超声颗粒测量仪cilas1180l进行的测量结果开始来获得。表面积借助于通过使用micromeriticstristarii系列仪器进行bet分析来获得。表观密度根据eniso60:1977规则测量。表1图3和4分别代表催化剂cat-1sg-35-a和cat-1sg-35-n2的衍射光谱,其是通过使用装备有石墨分析仪、辐射源cuk-α和40kv+40ma功率的philipsx'pertmpd仪器来获得。如所示的,发现对应于氧化铝(峰a)、赤铁矿(峰h1)和磁铁矿(峰m)的相。峰p代表铂(用该材料制造样品架)的峰。实施例2制备cat-2sg-35-n2将草酸铵铁(iii)三水合物(67.66g)和硝酸铝九水合物(119.00g)溶解在150ml水中。将氢氧化铵溶液(约17m)在搅拌下滴下,直到ph约7,在此ph下发生凝胶化。氨的加入以恒定速度进行,并且持续20分钟。将该凝胶置于buchner过滤器上并且用3等份的50ml水仔细洗涤。然后将其在80℃下干燥10小时并且然后轻微研磨(10-100μm)。将由此获得的固体在氮气气氛下在505℃下煅烧2小时,这导致获得22.80g催化剂,具有相对于理论91%的收率。下表2报告了所获得的催化剂的一些分析数据。测量用实施例1中所报告的相同技术和仪器来进行。表2图5代表如实施例1中所述获得的催化剂cat-2sg-35-n2的衍射光谱。图5的衍射光谱揭示由峰h所代表的铁尖晶石相feal2o4的存在。实施例3合成碳纳米管该合成方法由ccvd方法(催化化学气相沉积)组成,ccvd方法特别是在具有石英流化床的间歇反应器中进行,流化床提供有作为分布器起作用的多孔隔膜。纳米管cnt1-sg1将如实施例1中所制备的2g的催化剂cat-1sg-50-n2进料到反应器中并且借助于在氮气气流中15℃/min的加热斜坡将温度升到650℃。然后将该催化剂在分压比为0.3:0.7的氢气/氮气气流中还原约60分钟。随后,以0.2:0.8的分压比进料乙烯/氮气混合物60分钟,在此期间发生碳的沉积。在该实验结束时获得了51g产物。纳米管cnt2-sg1使用2g如实施例1中所制备的催化剂cat-1sg-50-a重复该程序。纳米管cnt3-sg1使用2g如实施例1中所制备的催化剂cat-1sg-35-n2重复该程序。纳米管cnt4-sg1使用2g如实施例1中所制备的催化剂cat-1sg-35-a重复该程序。纳米管cnt5-sg1使用2g如实施例1中所制备的催化剂cat-1sg-25-n2重复该程序。纳米管cnt6-sg1使用2g如实施例1中所制备的催化剂cat-1sg-25-a重复该程序。由此获得的纳米管进行热重分析。下表3示出了以残留%(r)、碳%(c)、碳与铁重量比(c/fe)以及碳与残留物重量比(c/r)来表达的所获得的结果。表3纳米管催化剂r[wt%]c[wt%]c/fec/rcnt1-sg1cat-1sg-50n21.80797.486131.07253.949cnt2-sg1cat-1sg-50a2.29497.155102.89542.352cnt3-sg1cat-1sg-35n24.05394.98177.03723.435cnt4-sg1cat-1sg-35a4.31995.03672.33422.004cnt5-sg1cat-1sg-25n213.59685.27627.7896.272cnt6-sg1cat-1sg-25a14.41484.77126.0575.881由此获得的纳米管如在混合物中原样的方便地使用。可替代地,在使纳米管经历用20%w/w硫酸在95℃下进行的湿净化之后来使用它们,以便进一步降低催化残留物。以这样的方式,在所有情况中获得了高于98%的纯度。实施例4纳米管cnt7-sg2将如实施例2中所制备的2g的催化剂cat-2sg-35-n2进料入反应器。随后进料乙烯/氢气/氮气混合物,其中分压下的比为0.2:0.3:0.5并且借助15℃/min的加热斜坡升温至650℃。该体系在这样的温度下维持60分钟,在此期间发生碳的沉积。在实验结束时获得29g产物。由此获得的纳米管通过使用tdasdtq600型仪器进行热重分析。下表4示出了以残留%(r)、碳%(c)、碳与铁重量比(c/fe)和碳与残留物重量比(c/r)来表达的所获得的结果。表4纳米管催化剂r[wt%]c[wt%]c/fec/rcnt7-sg2cat-2sg-35n26.74393.24245.45713.828实施例5在下表5中所报告的弹性体材料以以下方式制备(各种组分的量以phr表示)。除了硫和促进剂(tbbs)之外的所有组分在密炼机(pominipl1.6型)中混合约5分钟(1a步骤)。一旦温度达到145±5℃,则卸料该弹性体组合物。加入硫和促进剂(tbbs),并且在敞开辊混合器中进行混合(2a步骤)。表5r1:参照物;i1:本发明;i2:本发明·br是具有钕催化剂的聚丁二烯橡胶skd,其具有大于97%顺式丁二烯,·ir是高顺式-1,4-聚异戊二烯合成橡胶ski-3,leerubber,·nc7000是纳米管形式的商业碳,nanocylsa,90(wt)%的纯度(纳米管形式)、5.9%al、0.2%co,·标准纳米管根据专利ep2213369(b1)制备并且用稀硫酸净化和具有95.86(wt)%的纯度(纳米管形式)、0.87(wt)%al,其中ni、mo和co低于可检测的极限,·净化的cnt2_sg1(用稀硫酸净化)具有98.33(wt)%的纯度(纳米管形式)、0.01(wt)%al,其中ni、mo和co低于可检测的极限,·vn3二氧化硅是表面积为180m2/g的沉淀二氧化硅,evonikindustries,德国,·6ppd是抗氧化剂芳族胺n-(1,3-二甲基丁基)-n'-苯基-对亚苯基二胺,lanxessdeutschlandgmbh,德国,·tbbs是n-叔丁基-2-苯并噻唑亚磺酰胺的分散体,lanxessdeutschlandgmbh,德国。纳米管中的金属含量借助于icp/oes(电感耦合等离子体光发射谱)技术,通过使用perkinelmeroptima200dv型仪器来测量。待分析的纳米管样本用浓hno3和h2o2的混合物来矿化。所得澄清溶液在1%超纯hno3中适当稀释,并且进行icp/oes分析。新鲜的混合物进行mdr(移动模口流变仪)测量以便检测其交联动力学。流变分析mdr通过使用mdrmonsanto流变仪来进行。该测试在170℃下以1.66hz(100振荡/分钟)的振荡频率和±0.5°的振幅进行20分钟。测量最小转矩(ml)和最大转矩(mh)值。在100℃下的门尼ml(1+4)粘度根据标准iso289-1:2005,在如上所述获得的非交联的材料上测量。根据标准uni6065的静态力学性能在不同的伸长率(ca05-50%,ca1-100%和ca3-300%)下在上述于170℃下硫化10分钟的弹性体材料样品上测量。动态力学性能e’和tanδ通过使用动态装置instron型号1341以拉伸-压缩模式根据以下方法测量。将具有圆柱形(长度=25mm;直径=14mm)的交联的材料(170℃持续10分钟)的测试片以100hz的频率经历振幅±3.5%(相对于预加负荷下的长度)的动态正弦应力,该测试片在压缩下预加负荷直到相对于初始长度25%的纵向变形并且在整个测试持续时间维持在预定温度(23℃、70℃或100℃)。动态力学性能以动态弹性模量(e’)和tanδ(损耗因子)值的形式表达。tanδ值以动态粘性模量(e”)和动态弹性模量(e’)之间的比来计算。热塑性行为以在基于弹性体组合物的类型及其在轮胎中的应用来选择的两个参照温度下所测量的动态弹性模量值之间的差值△e’来评价。动态力学性能g’和tanδ还通过使用rpaalphatechnologies设备以剪切模式来测量。将交联的弹性体组合物(170℃持续10分钟)的圆盘形样本(体积=5cm3)在70℃、频率10hz、变形0.4%-10%下进行动态弹性剪切模量(g')测量。动态力学性能以动态弹性剪切模量(g’)和tanδ(损耗因子)值的形式来表达。tanδ值以动态粘性剪切模量(g”)和动态弹性剪切模量(g’)之间的比来计算。irhd度形式的硬度(23℃和100℃)根据标准iso48:2007,在刚刚在170℃下交联10分钟后的混合物样品上进行。结果总结在下表6中。表6表6的静态测试中所获得的结果证明与参照物r1相比,本发明i1和i2的混合物(其包含从基本上没有co、ni和mo的铁氧化物和/或铝氧化物基催化剂所获得的纳米管)允许具有更高的伸长率值并且尤其是更高的拉伸强度,这预示改进的耐撕裂性,而没有其他静态、动态或者流变特性的实质变化。为了验证根据本发明的纳米管中可能的fe残留物是否导致混合物的不期望的早期老化现象,本申请人在混合物i1和i2的样品上进行若干次热老化测试,将它们在70℃下在空气下维持7天。这样的测试没有显示出相对于没有纳米管的混合物,该混合物力学性能的实质变化,特别是断裂时的性能。不希望受限于任何解释理论,本申请人相信这归因于这样的事实,根据本发明的纳米管能够不朝向该混合物曝露含铁粒子,相反维持其有效地被限制在纳米管本身的结构内。实施例6下表7中所报告的弹性体材料以以下方式制备(各种组分的量以phr表示)。除了硫和促进剂(tbbs)之外的所有组分在密炼机(pomini型号pl1.6)中混合约5分钟(1a步骤)。一旦温度达到145±5℃,则卸料该弹性体组合物。加入硫和促进剂(tbbs),并且在敞开辊混合器中进行混合(2a步骤)。表7r2:参照物;i3:本发明;i4:本发明·br是具有钕催化剂的聚丁二烯橡胶skd,其具有大于97%顺式丁二烯,·ir是高顺式-1,4-聚异戊二烯合成橡胶ski-3,leerubber,·nc7000是纳米管形式的商业碳,nanocylsa,90(wt)%纯度(纳米管形式)、5.9(wt)%al、0.2(wt)%co,·cnt2-sg1具有91.85(wt)%的纯度(纳米管形式)、2.90(wt)%al,其中ni、mo和co低于可检测水平,·净化的cnt2-sg1是用稀硫酸净化的,并且具有98.33(wt)%的纯度(纳米管形式)、0.01(wt)%al,其中ni、mo和co低于可检测水平,·vn3二氧化硅是表面积为180m2/g的沉淀二氧化硅,evonikindustries,德国,·6ppd是抗氧化剂芳族胺n-(1,3-二甲基丁基)-n'-苯基-对亚苯基二胺,lanxessdeutschlandgmbh,德国,·tbbs是n-叔丁基-2-苯并噻唑亚磺酰胺的分散体,lanxessdeutschlandgmbh,德国。将所述混合物(新鲜的或者在170℃下交联10分钟)进行实施例6中所示的相同测量。体积电阻率根据标准uni4288-72,通过使用西门子的绝缘测量测试仪“normaunilapisox”来测量。结果总结在下表8中。表8同样,表8的静态测试中所获得的结果证实与参照物r相比,混合物i3和i4(其包含利用本发明的方法所获得的纳米管)允许具有更高的伸长率值尤其是更高的拉伸强度,这预示着改进的耐撕裂性,而没有其他静态、动态或者流变特性的实质变化。同时基本上维持了所需的电导率水平,这通过表8中所报告的参照混合物r2和本发明i3和i4的混合物的体积电阻率值来证实,该电导率水平基本上等效于为了获得合适的抗静电效果的电导率水平。当前第1页12