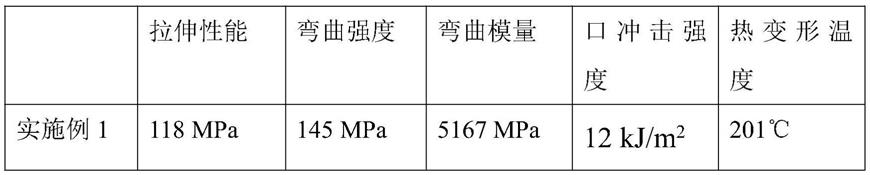
1.本发明属于汽车用塑料制备技术领域,具体涉及一种汽车用高性能复合材料。
背景技术:2.聚丙烯作为汽车用塑料,聚丙烯是结晶性的高聚物,具有良好的耐溶剂性,流动性高、电绝缘性和耐化学腐蚀性,但其有如下缺陷限制了其应用:1)分子链节上侧甲基的规则排列使聚丙烯材料具有较高的结晶度,在通常的加工条件下,由熔体自然冷却的均相结晶主要为α晶型,球晶颗粒较大,受到冲击时易成为应力集中点,使材料低温下易脆断,抗冲能力差;2)聚丙烯是一种非极性聚合物,其染色性、粘接性、抗静电性以及与无机填料的相容性都较差;3)聚丙烯的结晶行为使材料的加工成型收缩率大,制品的尺寸稳定性较低;4)聚丙烯分子中的叔碳原子和甲基上带有活泼氢,易在紫外线和氧气的作用下发生氧化降解反应,不利于零件的长期使用。
3.聚硅氧烷具有优异的润滑性能,可降低材料的摩擦因数,从而提高材料的耐刮擦性能,但是聚硅氧烷与聚丙烯的相容性较差,添加聚硅氧烷可能会造成聚丙烯复合材料出现相分离,进而降低聚丙烯复合材料的其力学性能。
4.聚苯醚是一种性能优异的非结晶工程塑料,具有优异的力学性能,成炭率高,耐热性好、吸水性低、尺寸稳定性好和密度小等优点,但其分子结构中的苯环导致了分子链刚性大,熔融流动性差,而且玻璃化温度在热塑性塑料中最高,加工时需要加热到300℃,因此极大地限制了其的应用。
5.再考虑到极性非结晶的聚苯醚和非极性结晶的聚丙烯相容性较差,并且熔体粘度相差较大,若相容剂选择不当,会造成分散相的分布不规则,易产生分离现象,导致力学性能等下降。所以将聚苯醚、聚丙烯、聚硅氧烷形成优势互补仍值得研究。
6.专利申请号cn201711402116.8公开了一种汽车内饰材料及其制备方法,尤其是一种高质感汽车内饰材料及其制备方法。本发明的材料包括以下重量份数的组分:聚丙烯40
‑
70份,柔软剂1
‑
10份,补强剂10
‑
25份,促进剂2
‑
5份,高弹体5
‑
20份,矿物粉5
‑
25份,功能助剂1
‑
3份,该发明通过强剪切、超高速拉伸方法实现取向成纤,大幅提高了原有聚丙烯材料强度、刚性、韧性和耐热性,同时获得了高品质外观制品,再通过高剪切分散实现了高弹体在体系中的良好分散,获得了表面柔软触感、低光泽度,消除制品硬塑感,提升汽车塑料内饰视觉档次和手感舒适度,有利于营造出最舒适的车内空间,但该文献并未解决聚苯醚和聚丙烯相容性较差、熔体粘度相差较大的问题。
技术实现要素:7.本发明针对现有技术的不足,提出了一种汽车用高性能复合材料。
8.具体是通过以下技术方案来实现的:
9.一种汽车用高性能复合材料,是采用电纺丝法在基体表面上形成抗老化膜,基体由以下重量百分数计的组分组成:聚苯醚20
‑
25%、改性聚硅氧烷5
‑
10%,表面活性剂0.1
‑
0.3%,相容剂0.5
‑
0.8%,余量为聚丙烯。
10.所述电纺丝法具体为:将基体依次置于质量浓度为1
‑
2%的壳聚糖溶液浸泡5
‑
10min,然后将基体置于静电纺丝仪接收板上,将电纺丝液液注入注射器,电纺丝溶液在静电力的作用下从针尖喷出,通过水凝胶粘附所纺的抗老化膜,然后置于质量浓度为3
‑
7%的氯化钙溶液中浸泡3
‑
10min,然后置于真空冷冻干燥机中冻干即得汽车用高性能复合材料。
11.所述电纺丝法的工作条件为:电压10
‑
20kv,推进速度3
‑
8ml/min,距离15
‑
20cm,温度<30℃,湿度<45%。
12.所述电纺丝液是先将纳米tio2溶于15wt%的乙醇溶液,制得纳米二氧化钛含量为1
‑
5%的分散液,再将纳米tio2分散液与wpu乳液混合按质量比1:1超声分散45
‑
60min。
13.所述改性聚硅氧烷,其制备方法为:采用乙醇溶解亚磷酸酯粉体,制得亚磷酸酯溶液,然后在亚磷酸酯溶液中加入聚硅氧烷和蒸馏水,使得体系固含量为50%,在100
‑
108℃的条件下反应30
‑
45min后,冷却至常温,过滤,于120
‑
137℃条件下真空干燥。
14.所述亚磷酸酯的用量是亚磷酸酯与聚硅氧烷的摩尔比为(0.1
‑
0.2):100。
15.所述表面活性剂为聚山梨酯。
16.所述相容剂为马来酸酐接枝聚丙烯和乙烯丙烯酸共聚物按质量比1:(0.4
‑
0.7)。
17.所述基体的制备方法为,包括如下步骤:
18.1)将聚苯醚溶于氯苯中搅拌至溶解,制得聚苯醚的氯苯溶液;
19.2)将改性聚硅氧烷充分溶于氯苯中,制得聚硅氧烷的氯苯溶液,然后加入硫酸、1/3表面活性剂,在108
‑
115℃条件下缓慢加入聚苯醚溶液,保温反应2
‑
3h后,过滤除去不溶物,用甲醇进行沉淀,抽滤、洗涤后,得到固形物;
20.3)将步骤2)所得固形物、聚丙烯、相容剂、剩余表面活性剂进行共混挤出造粒,挤出温度为250
‑
275℃。
21.所述硫酸,其浓度为0.2mol/l,用量为改性聚硅氧烷质量的1
‑
2%。
22.本发明的汽车用高性能复合材料用于制作汽车内饰零件。
23.有益效果:
24.本发明的复合材料具有如下优异的性能:
25.1)力学性能好;
26.本发明采用亚磷酸酯与聚硅氧烷进行反应,实现了亚磷酸酯对聚硅氧烷的修饰,利用聚硅氧烷的氨基能够与亚磷酸酯上的磷酰氯进行反应,将抗氧化剂良好的固化于复合材料中。
27.本发明引入聚硅氧烷结构,极大改善了以聚丙烯为主要原料制备的复合材料的耐刮擦性能,而采用亚磷酸酯对聚硅氧烷进行改性,对聚硅氧烷起到了扩链效果,进而改善了其与聚丙烯分子链间物理缠结和分子间的作用力。同时,本发明利用聚硅氧烷能够与聚苯醚进行交联反应生成共聚物,进而避免了聚硅氧烷、聚苯醚分别与聚丙烯相容性差的问题。
28.本发明在步骤2)中加入表面活性剂,利用聚山梨酯能够有助于增溶,进而保证聚苯醚、聚硅氧烷的良好反应,降低了反应温度,缩短了反应时间,提高了反应效率。
29.本发明在步骤3)中加入表面活性剂,利用聚山梨酯能够降低界面张力,进而加强了聚苯醚、聚硅氧烷与聚丙烯的良好结合。
30.2)耐热性能优;通过引入以si
‑
o
‑
si为主链的聚硅氧烷以及优异性能的聚苯醚,提
高了材料的高温性能、热氧化稳定性。
31.3)抗老化性能优;
32.本发明选择采用亚磷酸酯修饰聚硅氧烷,极大改善了材料的抗氧化性能;再结合在电纺丝法将二氧化钛与基材进行粘结,达到了抗氧化抗紫外线的效果,极大提高了复合材料的抗老化性能;采用壳聚糖与wpu形成较高的粘粘,再通过浸泡于氯化钙中,使得抗老化剂膜与基体紧密结合。
33.4)能够用于制作汽车内饰零件;
34.首先,本发明在共混挤出过程中加入表面活性剂具有改善熔体流动性的效果,满足了汽车内饰材料对高流动性的要求;其次,本发明中加入聚苯醚,能够保证尺寸的稳定性,防止翘曲变形的发生。
具体实施方式
35.下面对本发明的具体实施方式作进一步详细的说明,但本发明并不局限于这些实施方式,任何在本实施例基本精神上的改进或代替,仍属于本发明权利要求所要求保护的范围。
36.实施例1
37.一种汽车用高性能复合材料,是采用电纺丝法在基体表面上形成抗老化膜,具体是:将基体依次置于质量浓度为1%的壳聚糖溶液浸泡5min,然后将基体置于静电纺丝仪接收板上,将电纺丝液液注入注射器,电纺丝溶液在静电力的作用下从针尖喷出,通过水凝胶粘附所纺的抗老化膜,然后置于质量浓度为3%的氯化钙溶液中浸泡3min,然后置于真空冷冻干燥机中冻干即得汽车用高性能复合材料;所述电纺丝法的工作条件为:电压10kv,推进速度3ml/min,距离15cm,温度<30℃,湿度<45%;
38.所述电纺丝液是先将纳米tio2溶于15wt%的乙醇溶液,制得纳米二氧化钛含量为1%的分散液,再将纳米tio2分散液与wpu乳液混合按质量比1:1超声分散45min;
39.所述基体由以下重量百分数计的组分组成:聚苯醚20%、改性聚硅氧烷5%,表面活性剂0.1%,相容剂0.5%,余量为聚丙烯;
40.所述改性聚硅氧烷,其制备方法为:采用乙醇溶解亚磷酸酯粉体,制得亚磷酸酯溶液,然后按照亚磷酸酯:聚硅氧烷=0.1:100的摩尔比在亚磷酸酯溶液中加入聚硅氧烷和蒸馏水,使得体系固含量为50%,在100℃的条件下反应30min后,冷却至常温,过滤,于120℃条件下真空干燥;
41.所述表面活性剂为聚山梨酯;
42.所述相容剂为马来酸酐接枝聚丙烯和乙烯丙烯酸共聚物按质量比1:0.4;
43.所述基体的制备方法为,包括如下步骤:
44.1)将聚苯醚溶于氯苯中搅拌至溶解,制得质量浓度为5%聚苯醚的氯苯溶液;
45.2)将改性聚硅氧烷充分溶于氯苯中,制得质量浓度为5%改性聚硅氧烷的氯苯溶液,然后加入硫酸、1/3表面活性剂,在108℃条件下缓慢加入聚苯醚溶液,保温反应2h后,过滤除去不溶物,用甲醇进行沉淀,抽滤、洗涤后,得到固形物;所述硫酸,其浓度为0.2mol/l,用量为改性聚硅氧烷质量的1%;
46.3)将步骤2)所得固形物、聚丙烯、相容剂、剩余表面活性剂进行共混挤出造粒,挤
出温度为250℃。
47.实施例2
48.一种汽车用高性能复合材料,是采用电纺丝法在基体表面上形成抗老化膜,具体是:将基体依次置于质量浓度为2%的壳聚糖溶液浸泡10min,然后将基体置于静电纺丝仪接收板上,将电纺丝液液注入注射器,电纺丝溶液在静电力的作用下从针尖喷出,通过水凝胶粘附所纺的抗老化膜,然后置于质量浓度为7%的氯化钙溶液中浸泡10min,然后置于真空冷冻干燥机中冻干即得汽车用高性能复合材料;所述电纺丝法的工作条件为:电压20kv,推进速度8ml/min,距离20cm,温度<30℃,湿度<45%;
49.所述电纺丝液是先将纳米tio2溶于15wt%的乙醇溶液,制得纳米二氧化钛含量为5%的分散液,再将纳米tio2分散液与wpu乳液混合按质量比1:1超声分散60min;
50.所述基体由以下重量百分数计的组分组成:聚苯醚25%、改性聚硅氧烷10%,表面活性剂0.3%,相容剂0.8%,余量为聚丙烯;
51.所述改性聚硅氧烷,其制备方法为:采用乙醇溶解亚磷酸酯粉体,制得亚磷酸酯溶液,然后按照亚磷酸酯:聚硅氧烷=0.2:100的摩尔比在亚磷酸酯溶液中加入聚硅氧烷和蒸馏水,使得体系固含量为50%,在108℃的条件下反应45min后,冷却至常温,过滤,于137℃条件下真空干燥;
52.所述表面活性剂为聚山梨酯;
53.所述相容剂为马来酸酐接枝聚丙烯和乙烯丙烯酸共聚物按质量比1:0.7;
54.所述基体的制备方法为,包括如下步骤:
55.1)将聚苯醚溶于氯苯中搅拌至溶解,制得质量浓度为5%聚苯醚的氯苯溶液;
56.2)将改性聚硅氧烷充分溶于氯苯中,制得质量浓度为5%改性聚硅氧烷的氯苯溶液,然后加入硫酸、1/3表面活性剂,在115℃条件下缓慢加入聚苯醚溶液,保温反应3h后,过滤除去不溶物,用甲醇进行沉淀,抽滤、洗涤后,得到固形物;所述硫酸,其浓度为0.2mol/l,用量为改性聚硅氧烷质量的2%;
57.3)将步骤2)所得固形物、聚丙烯、相容剂、剩余表面活性剂进行共混挤出造粒,挤出温度为275℃。
58.实施例3
59.一种汽车用高性能复合材料,是采用电纺丝法在基体表面上形成抗老化膜,具体是:将基体依次置于质量浓度为1.5%的壳聚糖溶液浸泡7min,然后将基体置于静电纺丝仪接收板上,将电纺丝液液注入注射器,电纺丝溶液在静电力的作用下从针尖喷出,通过水凝胶粘附所纺的抗老化膜,然后置于质量浓度为5%的氯化钙溶液中浸泡3
‑
10min,然后置于真空冷冻干燥机中冻干即得汽车用高性能复合材料;所述电纺丝法的工作条件为:电压15kv,推进速度5ml/min,距离17cm,温度<30℃,湿度<45%;
60.所述电纺丝液是先将纳米tio2溶于15wt%的乙醇溶液,制得纳米二氧化钛含量为3%的分散液,再将纳米tio2分散液与wpu乳液混合按质量比1:1超声分散45
‑
60min;
61.所述基体由以下重量百分数计的组分组成:聚苯醚21%、改性聚硅氧烷8%,表面活性剂0.2%,相容剂0.6%,余量为聚丙烯;
62.所述改性聚硅氧烷,其制备方法为:采用乙醇溶解亚磷酸酯粉体,制得亚磷酸酯溶液,然后按照亚磷酸酯:聚硅氧烷=0.15:100的摩尔比在亚磷酸酯溶液中加入聚硅氧烷和
蒸馏水,使得体系固含量为50%,在105℃的条件下反应36min后,冷却至常温,过滤,于135℃条件下真空干燥;
63.所述表面活性剂为聚山梨酯;
64.所述相容剂为马来酸酐接枝聚丙烯和乙烯丙烯酸共聚物按质量比1:0.5;
65.所述基体的制备方法为,包括如下步骤:
66.1)将聚苯醚溶于氯苯中搅拌至溶解,制得质量浓度为5%聚苯醚的氯苯溶液;
67.2)将改性聚硅氧烷充分溶于氯苯中,制得质量浓度为5%改性聚硅氧烷的氯苯溶液,然后加入硫酸、1/3表面活性剂,在108
‑
115℃条件下缓慢加入聚苯醚溶液,保温反应2.5h后,过滤除去不溶物,用甲醇进行沉淀,抽滤、洗涤后,得到固形物;所述硫酸,其浓度为0.2mol/l,用量为改性聚硅氧烷质量的1.5%;
68.3)将步骤2)所得固形物、聚丙烯、相容剂、剩余表面活性剂进行共混挤出造粒,挤出温度为265℃。
69.实施例4
70.一种汽车用高性能复合材料,是采用电纺丝法在基体表面上形成抗老化膜,具体是:将基体依次置于质量浓度为1.1%的壳聚糖溶液浸泡9min,然后将基体置于静电纺丝仪接收板上,将电纺丝液液注入注射器,电纺丝溶液在静电力的作用下从针尖喷出,通过水凝胶粘附所纺的抗老化膜,然后置于质量浓度为4%的氯化钙溶液中浸泡8min,然后置于真空冷冻干燥机中冻干即得汽车用高性能复合材料;所述电纺丝法的工作条件为:电压12kv,推进速度7ml/min,距离19cm,温度<30℃,湿度<45%;
71.所述电纺丝液是先将纳米tio2溶于15wt%的乙醇溶液,制得纳米二氧化钛含量为4%的分散液,再将纳米tio2分散液与wpu乳液混合按质量比1:1超声分散48min;
72.所述基体由以下重量百分数计的组分组成:聚苯醚23%、改性聚硅氧烷6%,表面活性剂0.14%,相容剂0.75%,余量为聚丙烯;
73.所述改性聚硅氧烷,其制备方法为:采用乙醇溶解亚磷酸酯粉体,制得亚磷酸酯溶液,然后按照亚磷酸酯:聚硅氧烷=0.17:100的摩尔比在亚磷酸酯溶液中加入聚硅氧烷和蒸馏水,使得体系固含量为50%,在103℃的条件下反应38min后,冷却至常温,过滤,于123℃条件下真空干燥;
74.所述表面活性剂为聚山梨酯;
75.所述相容剂为马来酸酐接枝聚丙烯和乙烯丙烯酸共聚物按质量比1:0.6;
76.所述基体的制备方法为,包括如下步骤:
77.1)将聚苯醚溶于氯苯中搅拌至溶解,制得质量浓度为5%聚苯醚的氯苯溶液;
78.2)将改性聚硅氧烷充分溶于氯苯中,制得质量浓度为5%改性聚硅氧烷的氯苯溶液,然后加入硫酸、1/3表面活性剂,在110℃条件下缓慢加入聚苯醚溶液,保温反应2.2h后,过滤除去不溶物,用甲醇进行沉淀,抽滤、洗涤后,得到固形物;所述硫酸,其浓度为0.2mol/l,用量为改性聚硅氧烷质量的1.7%;
79.3)将步骤2)所得固形物、聚丙烯、相容剂、剩余表面活性剂进行共混挤出造粒,挤出温度为268℃。
80.实施例5
81.一种汽车用高性能复合材料,是采用电纺丝法在基体表面上形成抗老化膜,具体
是:将基体依次置于质量浓度为1%的壳聚糖溶液浸泡6min,然后将基体置于静电纺丝仪接收板上,将电纺丝液液注入注射器,电纺丝溶液在静电力的作用下从针尖喷出,通过水凝胶粘附所纺的抗老化膜,然后置于质量浓度为7%的氯化钙溶液中浸泡5min,然后置于真空冷冻干燥机中冻干即得汽车用高性能复合材料;所述电纺丝法的工作条件为:电压10kv,推进速度8ml/min,距离20cm,温度<30℃,湿度<45%;
82.所述电纺丝液是先将纳米tio2溶于15wt%的乙醇溶液,制得纳米二氧化钛含量为5%的分散液,再将纳米tio2分散液与wpu乳液混合按质量比1:1超声分散45min;
83.所述基体由以下重量百分数计的组分组成:聚苯醚25%、改性聚硅氧烷10%,表面活性剂0.1%,相容剂0.5%,余量为聚丙烯;
84.所述改性聚硅氧烷,其制备方法为:采用乙醇溶解亚磷酸酯粉体,制得亚磷酸酯溶液,然后按照亚磷酸酯:聚硅氧烷=0.1:100的摩尔比在亚磷酸酯溶液中加入聚硅氧烷和蒸馏水,使得体系固含量为50%,在100℃的条件下反应45min后,冷却至常温,过滤,于137℃条件下真空干燥;
85.所述表面活性剂为聚山梨酯;
86.所述相容剂为马来酸酐接枝聚丙烯和乙烯丙烯酸共聚物按质量比1:0.6;
87.所述基体的制备方法为,包括如下步骤:
88.1)将聚苯醚溶于氯苯中搅拌至溶解,制得质量浓度为5%聚苯醚的氯苯溶液;
89.2)将改性聚硅氧烷充分溶于氯苯中,制得质量浓度为5%改性聚硅氧烷的氯苯溶液,然后加入硫酸、1/3表面活性剂,在115℃条件下缓慢加入聚苯醚溶液,保温反应2h后,过滤除去不溶物,用甲醇进行沉淀,抽滤、洗涤后,得到固形物;所述硫酸,其浓度为0.2mol/l,用量为改性聚硅氧烷质量的1%;
90.3)将步骤2)所得固形物、聚丙烯、相容剂、剩余表面活性剂进行共混挤出造粒,挤出温度为270℃。
91.对比例1
92.在实施例1的基础上,与实施例1的区别在于:所述改性聚硅氧烷替换为聚硅氧烷。
93.对比例2
94.在实施例2的基础上,与实施例2的区别在于:所述基材中不含有改性聚硅氧烷,所述基体的制备方法为:将聚苯醚、聚丙烯、相容剂、表面活性剂进行共混挤出造粒,挤出温度为275℃。
95.对比例3
96.在实施例3的基础上,与实施例3的区别在于:所述基材的制备中未使用表面活性剂。
97.对比例4
98.在实施例4的基础上,与实施例4的区别在于:所述相容剂为马来酸酐接枝聚丙烯。
99.对比例5
100.在实施例4的基础上,与实施例4的区别在于:所述相容剂为乙烯丙烯酸共聚物。
101.对比例6
102.在实施例5的基础上,与实施例5的区别在于:所述基体的制备方法为,包括如下步骤:
103.1)将聚苯醚溶于氯苯中搅拌至溶解,制得质量浓度为5%聚苯醚的氯苯溶液;
104.2)将改性聚硅氧烷充分溶于氯苯中,制得质量浓度为5%改性聚硅氧烷的氯苯溶液,然后加入硫酸、表面活性剂,在115℃条件下缓慢加入聚苯醚溶液,保温反应2h后,过滤除去不溶物,用甲醇进行沉淀,抽滤、洗涤后,得到固形物;所述硫酸,其浓度为0.2mol/l,用量为改性聚硅氧烷质量的1%;
105.3)将步骤2)所得固形物、聚丙烯、相容剂进行共混挤出造粒,挤出温度为270℃。
106.对比例7
107.在实施例5的基础上,与实施例5的区别在于:所述基体的制备方法为,包括如下步骤:
108.1)将聚苯醚溶于氯苯中搅拌至溶解,制得质量浓度为5%聚苯醚的氯苯溶液;
109.2)将改性聚硅氧烷充分溶于氯苯中,制得质量浓度为5%改性聚硅氧烷的氯苯溶液,然后加入硫酸,在115℃条件下缓慢加入聚苯醚溶液,保温反应2h后,过滤除去不溶物,用甲醇进行沉淀,抽滤、洗涤后,得到固形物;所述硫酸,其浓度为0.2mol/l,用量为改性聚硅氧烷质量的1%;
110.3)将步骤2)所得固形物、聚丙烯、相容剂、表面活性剂进行共混挤出造粒,挤出温度为270℃。
111.实验例1
112.拉伸性能按astmd638
‑
2003测试,样条尺寸为165mm
×
13mm
×
3.2mm,拉伸速率5mm/min;弯曲性能按astmd790
‑
2003测试,样条尺寸为127mm
×
12.7mm
×
3.2mm,测试速率2mm/min;悬臂梁缺口冲击强度按astmd256
‑
2006测试,样条尺寸为64mm
×
12.7mm
×
3.2mm,缺口为45
°
v型缺口;热变形温度(hdt)按astmd648
‑
2004测试,样条尺寸127mm
×
12.7mm
×
6.4mm,升温速率2℃/min,1.82mpa;
113.实施例1
‑
5和对比例1
‑
7各组力学性能及耐热性结果如表1所示:
114.表1
115.[0116][0117]
由表可知:实施例1与对比例1对比可看出未利用亚磷酸酯进行修饰,会使得复合材料的力学性能明显下降,可能是因为聚硅氧烷的氨基能够与亚磷酸酯上的磷酰氯进行反应,对聚硅氧烷的结构起到了扩链作用和化学键改变作用。
[0118]
实施例2与对比例2对比可看出未添加改性聚硅氧烷的复合材料,其力学性能和耐热性能均显著下降,这说明改性聚硅氧烷能够加强力学性能,其次改性聚硅氧烷能够改变复合材料的耐热性。
[0119]
实施例3
‑
5以及对比例3
‑
7对比可看出,相容剂和表面活性剂对复合材料的力学性能有显著的影响,其可能影响聚苯醚、聚硅氧烷、聚丙烯分子间的结合性。
[0120]
实验例2
[0121]
用耐刮擦仪按德国大众汽车标准pv3952
‑
2002测试,负荷为10n,划伤速率1000mm/min,用色差仪测定刮擦前后划痕的色差值。
[0122]
实施例2
‑
5和对比例2
‑
7耐刮擦性能如表2所示:
[0123]
表2
[0124]
项目δl项目δl实施例21.23对比例32.27实施例31.08对比例41.32实施例41.16对比例51.78实施例51.11对比例62.31对比例25.74对比例72.22
[0125]
由表2说明:未添加聚硅氧烷会严重影响材料的耐刮擦性能,表面活性剂和相容剂对耐刮擦性能也会有影响。