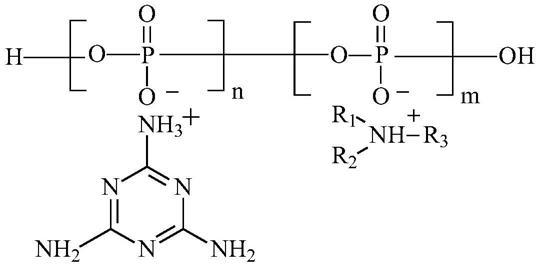
1.本发明涉及一种功能性聚酰胺组合物及其制备方法,尤其涉及一种耐冷冻液耐析出阻燃生物基聚酰胺组合物及其制备方法,属于工程塑料技术领域。
背景技术:2.二乙基次膦酸铝协效mpp(三聚氰胺聚磷酸盐)阻燃pa66材料,属于无卤阻燃工程塑料,因其不含卤族元素在燃烧过程中不会产生二噁英等有害物质、且复合材料有着良好的综合机械性能,被广泛的应用在新能源汽车电池包模块、电子电器设备等领域。
3.当前新能源汽车发展迅猛,对电池包模块阻燃材料的要求也越来越严格,会要求阻燃材料有一定的耐冷冻液性能。但是传统的二乙基次膦酸铝协效mpp阻燃聚酰胺很难被应用于冷却液环境中,这是因为mpp多呈酸性与塑料基体的相容性较差很容易在高温高湿环境下析出从而影响整体材料性能;且mpp整体呈酸性,在冷却液介质中析出之后会使冷却液的整体ph值下降,造成冷却液呈酸性从而腐蚀材料的情况;且应用在pa66体系中,需要添加较多含量的阻燃剂才可达到对应的阻燃要求。
4.当前对于改性mpp的研究多在于提升mpp的热稳定性能,多是采用金属离子等用于mpp进行杂化改性以此提升mpp的初始热分解温度。均未涉及到改良mpp的耐析出性能及复合阻燃体系的耐冷冻液性能。
技术实现要素:5.本发明的目的是为了提供一种耐冷冻液耐析出阻燃生物基聚酰胺组合物及其制备方法,以解决现有技术的上述技术问题。
6.本发明的目的是通过以下技术方案来实现的。
7.一种耐冷冻液耐析出阻燃生物基聚酰胺组合物,由以下重量份数计的原料制备而成:
8.生物基聚酰胺:30-90份;
9.填充物:10-40份;
10.阻燃剂二乙基次膦酸铝:0.01-30份;
11.阻燃剂改性mpp:0.01-10份;
12.抗氧剂:0.01~2份;
13.协效剂:0.01~2份;
14.色母粒:0.01~2份。
15.所述的生物基聚酰胺包括:pa56、pa1010、pa11、pa46、pa410等生物基类聚酰胺材料。
16.所述的填充物为玻璃纤维。
17.所述的阻燃剂改性mpp(三聚氰胺聚磷酸盐)为自主合成,是mpp和有机胺混合均匀后进行升温处理,然后在压力为0-0.6mpa、温度为80-180℃的条件下反应2-8h,最后在压力
为-0.01~-0.09mpa或惰性气体保护下、温度为80~180℃的条件下反应2~6h得到改性mpp。最终制得产品的结构式为:
[0018][0019]
式中,m和n为聚合度,m≥1,n≥1。其中,有机胺包括:乙二胺、二乙烯三胺、三乙烯四胺、乙醇胺、二乙醇胺、三乙醇胺、c1~c8的脂肪胺、苯胺或杂环胺。
[0020]
所述的抗氧剂为铜盐类抗氧剂包括:tph318和tph3386。
[0021]
所述的协效剂为锡酸锌。
[0022]
上述耐析出聚酰胺复合材料的制备方法,其步骤为:
[0023]
(1)按重量份数,将生物基聚酰胺30~90份、填充物10~40份、阻燃剂二乙基次膦酸铝0.01~30份、阻燃剂改性mpp 0.01~10份,抗氧剂0.01-2份,协效剂0.01-2份及色母粒0.1~2份一起加入到高速混料机中混合均匀后,再加入到双螺杆挤出机中,经双螺杆挤出机熔融、挤出、冷却、切粒制备成耐析出聚酰胺复合材料。
[0024]
所述的双螺杆挤出机的i~x区加工温度依次为120℃,200℃,250℃,265℃,265℃,265℃,265℃,265℃,265℃,265℃。主螺杆转速为450~500r/min,水槽温度23℃~50℃。
[0025]
本发明制备的耐冷冻液耐析出阻燃生物基聚酰胺组合物,合成使用的阻燃剂相对于传统阻燃剂的相容性更好,有利于防止阻燃剂析出;合成使用的阻燃剂相对于传统阻燃剂酸性较弱,可以提高复合材料的耐水解性能;本发明制备的耐冷冻液耐析出阻燃生物基聚酰胺组合物所选用的树脂基体为生物基聚酰胺阻燃效率更高。
附图说明
[0026]
图1为样板经历高温高湿实验后析出示意图。
[0027]
(右为配方1#,左为配方4#)
具体实施方式
[0028]
下面结合附图与具体实施例进一步阐述本发明的技术特点。
[0029]
首先对所用的mpp进行合成改性,其制备方法为:首先将有机胺与三聚氰胺聚磷酸盐(mpp)混合均匀后进行升温处理使得有机胺均匀浸润到mpp的分子之间,然后在压力为0~0.6mpa、温度为80~180℃的条件下反应2~8h(使有机胺小分子熔化与mpp反应),最后在压力为-0.01~-0.09mpa或惰性气体保护下、温度为80~180℃的条件下反应2~6h得到有机胺改性三聚氰胺聚磷酸盐。反应化学式如下:
[0030][0031][0032]
其中,x,y≥1。
[0033]
从化学式可以看出改性后的mpp所带h+离子要少于改性前的mpp,用表面羟基数(羟基呈酸性)及测定阻燃剂与水的混合液ph值,可以验证合成成功且h+离子数量大幅减少。
[0034]
①
表面羟基数测定:称量2g产物放置在200ml的烧杯中,之后向烧杯内添加25ml的无水乙醇和75ml20wt%的nacl溶液并且搅拌均匀,之后用0.1moll-1
的hcl向烧杯中滴定并且不断搅拌直至ph=4.0,再向烧杯中滴加0.1moll-1
的naoh溶液调整ph至9.0,保证溶液ph在20s内不变。按照下列方程计算每平方纳米样品表面积上所含有羟基的个数。
[0035]
n=cvna×
10-3
/sm
[0036]
其中:c为naoh的浓度(0.1moll-1
),v为调整ph从4到9时所消耗的naoh的体积(ml),na为阿伏伽德罗常数,s为测试样的比表面积(nm2g-1
),m为所测样的质量(g)。
[0037]
根据上述公式计算可得,在引入有机胺之前mpp的表面羟基数目为每平方纳米7.06个,引入有机胺反应获得的改性mpp的表面羟基数目下降到每平方纳米1.45个。这证明了材料表面的羟基数目明显减少,提高了阻燃剂的疏水性,也更进一步证明了获得了目标产物。
[0038]
②
阻燃剂ph测定:称量50g的mpp和改性mpp于200ml去离子水中,搅拌均匀,静置10min后,测混合液ph值,可得改性mpp的混合液ph为6,未改性的mpp混合液ph为5,也证明了h+被有效去除。
[0039]
得到目标阻燃剂后对配方进行设计,对配方体系的综合效果进行评价。
[0040]
表1 实验配方(质量分数,%)
[0041]
[0042][0043]
对配方进行造粒所测试常规性能如下表
[0044]
泡水ph为将50g塑料粒子至于200ml去离子水中,沸水水浴3h后冷却至常温,测试混合液的ph值;耐析出性能是将样板放置于85℃85rh的环境中500h,到达时间节点之后取出样板放置到室温状态后观察样板表观的析出状态。
[0045]
表2 各配方基础性能
[0046][0047]
对比配方1#、2#、3#可知随着二乙基次膦酸铝和未改性mpp用量增加,阻燃性能有所提升,但是对材料基础性能影响较大;对比配方1#、2#、3#和配方4#、5#、6#可知,当阻燃剂用量一致的情况下,改性过的mpp体系整体的材料性能要优于未改性mpp,且整体阻燃性能要优于未改性的mpp;比配方1#、2#、3#和配方4#、5#、6#可知,改性之后的mpp体系整体的ph值相对于改性前略有升高,即整体酸性减弱,这对于注塑过程中的模具保护及耐冷冻液实验过程中的冷却液可电解成分稳定有着积极作用;对比配方4#、5#、6#和配方7#、8#、9#、10#可知,生物基聚酰胺pa56相对于传统pa66,在要求阻燃等级相同的情况下,所用的阻燃剂含
量相对较少,对于力学性能保持及耐析出效果均更加有利;
[0048]
最后对配方体系耐冷冻液性能进行对比,具体方法为将各配方体系的iso哑铃型拉伸样条均匀浸泡于冷却液(乙二醇与水比例为1:1)中,对反应液及样条进行密封,控制反应液温度为90℃,分别于反应时间200h,400h和600h对样品进行取样测试,探究材料力学性能保持率,具体实验数据如下
[0049]
表3 各配方耐冷却液性能汇总
[0050][0051]
对比配方1#、2#、3#和配方4#、5#、6#可知,改性后的mpp体系在冷冻液中高温浸泡后的材料力学性能保持率更好,这是因为改性后的mpp体系酸性较弱,在冷冻液实验中可电离出的h+数量大幅减少,使得样条受到酸性的腐蚀较小,所以有着更好的力学性能保持率;配方4#、5#、6#和配方7#、8#、9#、10#可知,树脂pa56复合体系相对于树脂pa66复合体系耐冷却液性能保持率基本相当,且pa56体系整体所需的阻燃剂含量较少,对于阻燃剂的均匀分散是更有利的。
[0052]
本发明制备的耐冷冻液耐析出阻燃生物基聚酰胺组合物,合成使用的阻燃剂相对于传统阻燃剂的相容性更好,有利于防止阻燃剂析出;合成使用的阻燃剂相对于传统阻燃剂酸性较弱,可以提高复合材料的耐水解性能;本发明制备的耐冷冻液耐析出阻燃生物基聚酰胺组合物所选用的树脂基体为生物基聚酰胺阻燃效率更高。