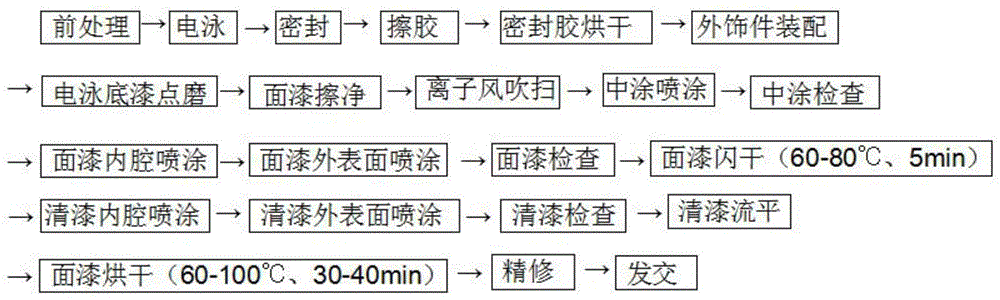
本发明属于涂料领域,尤其涉及一种中涂漆及其制备方法、应用。
背景技术:
:当前,环保、轻量化、新能源化、智能化等新的行业趋势发展引发了汽车行业新一轮的技术变革,对包括涂料在内的整个供应链亦提出了新的要求和挑战。近年来随着环保要求逐渐加强以及国家环保法规的不断出台,低voc排放的水性涂料已经成为了未来汽车涂料的发展趋势,同时简化涂装工艺以减少涂装过程的能源消耗、成本也成为了各方关注的重点。现在,作为汽车业界内接受的环保型涂装工序缩短施工方式,已有省去中涂烘烤的水性3c1b涂装工艺(如附图2所示),并且在多个工厂和车型实例中得到了应用。但是现有的3c1b涂装工艺均为高温烘烤型工艺,依然存在能源消耗大这一缺点。同时高温烘烤决定车身与外饰件如保险杠必须分开涂装,这也大大的增加了涂装成本。因此,需要开发一种汽车用水性涂料组合物,要求能够适用于当前汽车界偏爱的施工工艺,并实现汽车车身及外饰件的一体化喷涂。技术实现要素:本发明所要解决的技术问题是克服以上
背景技术:
中提到的不足和缺陷,提供一种用于汽车的中涂漆及其制备方法、应用。为解决上述技术问题,本发明提出的技术方案为:一种用于汽车的中涂漆,包括a组分和b组分,所述a组分包括以下重量份的原料:所述b组分为固化剂,所述a组分和b组分的重量比为(6-10):1。上述中涂漆中,优选的,所述水性聚氨酯分散体包括聚醚型水性聚氨酯分散体、聚碳酸酯型水性聚氨酯分散体和聚酯型水性聚氨酯分散体中的一种或多种。更优选的,所述水性聚氨酯分散体包括聚碳酸酯型水性聚氨酯分散体或聚酯型水性聚氨酯分散体。进一步优选的,所述水性聚氨酯分散体为带羟基的聚碳酸酯型水性聚氨酯,且所述带羟基的聚碳酸酯型水性聚氨酯的胺酯键大于8%。上述水性聚氨酯分散体的存在,可以使中涂漆具有强的内聚力,可以降低与面漆的相互作用,从而与配方中的聚酯树脂、丙烯酸改性聚氨酯协同实现湿碰湿涂装,可以为中涂漆提供优异的附着力、耐石击性能、耐磨性和耐化学品及耐油性等性能。上述中涂漆中,优选的,所述聚酯树脂(含羟基的聚酯树脂)主要由多元酸与多元醇聚合而成,所述多元酸为具有长链的二聚酸,且所述聚酯树脂的分子量多分散系数为20-40,酸值小于1mgkoh/g。采用长链的二聚酸作为二元酸结构,使树脂具有较好的触变性的同时,疏水性好,再通过分子结构设计(主要是通过控制多元酸、多元醇链上官能团的种类、数量以及活性,从而使聚合反应有选择的进行),使树脂分子量分布宽,酸值低,能为中涂漆提供良好的耐水性、柔韧性及耐石击性能等性能,同时还能够很好的适应于湿碰湿工艺。上述中涂漆中,优选的,所述丙烯酸改性聚氨酯(自交联型水性丙烯酸改性聚氨酯乳液)为脂肪族氨基甲酸酯聚丙烯酸酯混合物。上述脂肪族氨基甲酸酯聚丙烯酸酯混合物特有的网络结构有利于中涂漆在工件表面的涂覆成膜,同时该树脂还能限制湿膜状态下中涂层与面漆层中的分子结构运动,保证中涂、面漆湿碰湿状态下的表面效果。上述中涂漆中,优选的,所述丙烯酸乳液为核壳结构的功能性水性丙烯酸乳液,主要由水性丙烯酸树脂、水和中和剂n、n-二甲基乙醇胺物理混合组成,且控制水性丙烯酸树脂的质量浓度为29-31%,n、n-二甲基乙醇胺的用量以控制体系的ph值为5.5-7.0为准。上述丙烯酸乳液能够改善中涂漆的施工性,使中涂漆具有良好的流平和流挂性能,同时还能够调节中涂漆的施工稳定性。上述中涂漆中,优选的,钛白粉选用结构稳定,光学活性小,耐候性优异的钛白粉,优选为金红石型钛白粉,更优选美国杜邦公司的r-960钛白粉。分散助剂的作用促进涂料在磨浆过程中颜料的分散,选用适合于含有粘结剂以及可用于研磨无粘结剂的颜料浓缩浆的分散助剂,更优选比克公司的byk2012。润湿流平剂能够有效降低涂料的表面张力,优选有机硅烷类基材润湿剂,进一步优选tegotwin4100。消泡剂的作用是消除涂料在磨浆和配漆过程中产生的气泡,同时还要保证不影响涂层的层间附着力,消泡剂为非有机硅类消泡剂,优选byk011。有机胺为中和剂作为涂料ph调节剂使用,优选沸点不高于150℃的有机胺中和剂,更优选n,n-二甲基乙醇胺。成膜助剂选用具有亲水亲油平衡能够对不同树脂发挥不同成膜效果的醇醚类成膜助剂,优选二丙二醇甲醚。相容剂能够改善涂料组分的相容性,所用溶剂采用醇醚类中的一种或多种,优选丙二醇丁醚和丙二醇甲醚醋酸酯。中涂漆中所用的水优选为去离子水,由于自来水中的钙镁等多价离子的存在会影响水性树脂的稳定性,导致最终涂料的稳定性变差。上述中涂漆中,优选的,所述b组分包括水性异氰酸酯固化剂(如科思创2655,401-60,万华aquolin268等)或水性封闭异氰酸酯(bayhydurbl5335等)中的一种或两种。作为一个总的技术构思,本发明还提供一种上述的用于汽车的中涂漆的制备方法,所述中涂漆的a组分包括以下步骤:(1)在搅拌条件下(200-400转/分钟)向5-8重量份丙烯酸树脂中加入15-25重量份钛白粉、0.5-0.9重量份分散助剂、0.01-0.03重量份润湿流平剂、0.05-0.1重量份消泡剂、0.1-0.2重量份有机胺、1-2重量份相容剂和3-5重量份去离子水,加完后继续搅拌(400-600转/分钟条件下搅拌30min),然后研磨至细度小于10μm得到预混料;(2)在搅拌条件下(200-400转/分钟)向步骤(1)得到的预混料中加入10-20重量份水性聚氨酯分散体、12-23重量份聚酯树脂、5-15重量份丙烯酸改性聚氨酯、2-8重量份丙烯酸乳液、0.04-0.17重量份润湿流平剂、0.15-0.4重量份消泡剂、1-3重量份成膜助剂、0.3-0.6重量份有机胺、2-6重量份相容剂和1-3重量份去离子水,调粘至80-90s(25℃,福特4#杯),200目滤布过滤,即得到所述中涂漆的a组分。作为一个总的技术构思,本发明还提供一种上述用于汽车的中涂漆的应用,将所述中涂漆用于汽车车身的一体化涂装工艺,所述涂装工艺为3c1b涂装工艺,包括以下步骤:(1)车身前处理、电泳底漆处理、pvc车底喷涂及焊缝密封处理;(2)装配与车身颜色要求一致的外饰件(预涂底漆);(3)电泳底漆点磨,再喷涂中涂漆,流平2-5min后在中涂漆上喷涂面漆,流平2-5min后于60-80℃闪干2-5min;再在面漆上喷涂清漆,流平3-8min后烘烤;(4)烘干漆膜,烘烤温度为60-100℃,保温时间为30-40min。上述应用中,所述车身前处理依次包括以下步骤:预脱脂、脱脂、一次水洗、二次水洗、表调、磷化、一次水洗、二次水洗、纯水洗、新鲜纯水洗、沥液;所述电泳底漆处理依次包括以下步骤:电泳涂装、超滤液uf冲洗、纯水冲洗、沥液、电泳烘干、电泳点磨;电泳烘干时,烘干温度为160-180℃,保温时间20min左右,所述pvc车底喷涂及焊缝密封处理后于140-150℃保温20min后进入下道工序。电泳底漆打磨时,采用人工进行电泳底漆点磨,打磨室内风速要求0.2-0.3m/s,室内照明强度600lx,打磨砂纸粒度为400-600#,打磨过程确保不出现打磨露底及明显可见的打磨痕;采用湿发打磨时要求所用水为去离子水,并确保工件在进入下一道工序时表面干燥;采用粘性无尘擦拭布除去工件表面的浮尘。上述应用中,优选的,所述面漆包括c组分和d组分,所述c组分包括以下重量份的原料:所述d组分为固化剂,所述c组分和d组分的重量比为(5-8):1。上述面漆中,优选的,所述d组分包括水性异氰酸酯固化剂(如科思创2655,401-60,万华aquolin268等)或水性封闭异氰酸酯(bayhydurbl5335等)中的一种或两种。上述面漆中,优选的,所述聚酯树脂(含羟基的聚酯树脂)主要由多元酸与多元醇聚合而成,所述多元酸为具有长链的二聚酸,且所述聚酯树脂的分子量多分散系数为20-40,酸值小于1。采用长链的二聚酸作为二元酸结构,使树脂具有较好的触变性的同时,疏水性好,再通过分子结构设计(主要是通过控制多元酸、多元醇链上官能团的种类、数量以及活性,从而使聚合反应有选择的进行),使树脂分子量分布宽,酸值低,能为面漆提供良好的耐水性、柔韧性等性能,同时还能够很好的适应于湿碰湿工艺,另外还能够有效的改善涂料中铝粉的排列。上述面漆中,优选的,所述丙烯酸改性聚氨酯(自交联型水性丙烯酸改性聚氨酯乳液)为脂肪族氨基甲酸酯聚丙烯酸酯混合物。上述脂肪族氨基甲酸酯聚丙烯酸酯混合物特有的网络结构有利于降低面漆中的分子运动能力,满足湿碰湿的喷涂需求,同时其还能改善铝粉定向,为涂膜提供干燥快、硬度发展快、耐久耐候性好、流动平整良好、稳定性好、耐刮性好等性能。上述面漆中,优选的,所述丙烯酸乳液为核壳结构的功能性水性丙烯酸乳液,主要由水性丙烯酸树脂、水和中和剂n、n-二甲基乙醇胺物理混合组成,且控制水性丙烯酸树脂的质量浓度为29-31%,n、n-二甲基乙醇胺的用量以控制体系的ph值为5.5-7.0为准。用中和剂中和乳液可使乳液粘度明显上升,且具有剪切变稀效果,但是当乳液ph稳定在8.0-9.0以后,乳液粘度变化不大,此时,加入醇醚类相容剂后会出现明显的触变性。利用这一特性,一方面可以用于水性铝粉漆中提供优异的铝粉定向,另一方面可以提高涂料的稳定性和施工性。上述面漆中,分散助剂、相容剂、润湿剂、消泡剂、有机胺、去离子水的种类及作用均与中涂漆的相似,此处不再赘述。上述面漆的c组分的制备方法包括以下步骤:(1)在搅拌条件下(200-400转/分钟)向5-12重量份丙烯酸树脂中加入5-8重量份颜料、0.01-1.2重量份分散助剂、0.01-0.02重量份润湿流平剂、0.05-0.08重量份消泡剂、0.1-0.15重量份有机胺、1-1.5重量份相容剂和4-6重量份去离子水,加完后继续搅拌(400-600转/分钟条件下搅拌30min),然后研磨至细度小于10μm得到预混料;(2)在搅拌条件下(200-400转/分钟)向步骤(1)得到的预混料中加入40-60重量份丙烯酸乳液、30-50重量份聚酯树脂、8-12重量份丙烯酸改性聚氨酯、0.04-0.06重量份润湿流平剂、0.05-0.12重量份消泡剂、0.2-0.45重量份有机胺、9-12.5重量份相容剂和4-7重量份去离子水,调粘至80-90s(25℃,福特4#杯),200目滤布过滤,即得到所述面漆的c组分。本发明中的中涂漆与面漆在应用于一体化涂装后,中涂漆与面漆对整个复合涂膜性能的体现上具有协同作用。中涂漆作为电泳与面漆之间的一道涂层,具有提高面漆与电泳层之间的附着,同时还有助于提高遮盖,有利于面漆颜色效果的体现。同时复合涂膜的理化性能也是通过中涂漆与面漆的协同完成的,任何一个涂层的性能达不到要求都会影响整个复合涂膜的性能。只有中涂漆与面漆之间能够达到良好的协同作用,才能保证复合涂膜即能够对被涂工件起到良好的防护,同时还能够起到优良的装饰作用。本发明中,中涂漆与面漆具有一些共同的作用如:附着、耐石击、耐磨等性能,能够对被涂覆工件起到防护作用,这就决定了在其配方中可能出现相同成分的主体树脂,基于上述相同的组分,中涂漆与面漆相互配合良好,其二者配套使用,才能满足本发明中的3c1b涂装工艺需求,满足湿碰湿施工工艺、低温(60-100℃)烘烤固化工艺的需求。本发明中的中涂漆及面漆均为双组份涂料,所使用的固化剂在60-80℃条件下即可释放出的异氰酸酯(-nco)基团与水性树脂分子链上羟基、羧基、氨基等基团反应形成交联结构从而完成涂料中聚氨酯、丙烯酸树脂及聚酯等的完全聚合。上述固化剂与其他成分共同作用,可以使本发明中的中涂漆、面漆满足湿碰湿施工工艺、低温(60-100℃)烘烤固化工艺的需求。与现有技术相比,本发明的优点在于:1、本发明中的中涂漆具有能够满足湿碰湿施工工艺、涂膜能够在低温(60-100℃)下烘烤固化的特点。在具有良好的施工性能及涂膜外观的同时还具备优异的附着力、耐石击性、耐磨性和耐化学品性等理化性能。2、本发明中的面漆能够满足湿碰湿的施工工艺,涂膜固化温度低(60-100℃)。同时具有优异的铝粉定向性能,色浆在其中的展色性良好,能够满足各种复杂颜色的效果展现。同时该面漆还具备有优异的耐石击、耐水和耐化学品等理化性能。3、本发明中的中涂漆和面漆应用于一体化涂装工艺后,中涂漆和面漆之间相互协同作用,满足湿碰湿施工工艺、低温(60-100℃)烘烤固化工艺的需求,不仅能大大减少涂装过程中能源的消耗,还能实现汽车车身与外饰件的一体化喷涂,解决了汽车车身与外饰件对色难的问题。附图说明为了更清楚地说明本发明实施例或现有技术中的技术方案,下面将对实施例或现有技术描述中所需要使用的附图作简单地介绍,显而易见地,下面描述中的附图是本发明的一些实施例,对于本领域普通技术人员来讲,在不付出创造性劳动的前提下,还可以根据这些附图获得其他的附图。图1为本发明低温一体化涂装工艺流程图。图2为现有3c1b汽车车身涂装工艺流程图。具体实施方式为了便于理解本发明,下文将结合说明书附图和较佳的实施例对本发明作更全面、细致地描述,但本发明的保护范围并不限于以下具体的实施例。除非另有定义,下文中所使用的所有专业术语与本领域技术人员通常理解的含义相同。本文中所使用的专业术语只是为了描述具体实施例的目的,并不是旨在限制本发明的保护范围。除非另有特别说明,本发明中用到的各种原材料、试剂、仪器和设备等均可通过市场购买得到或者可通过现有方法制备得到。实施例1:一种用于汽车的中涂漆,包括a组分和b组分(固化剂)。a组分包括以下原料:水性聚氨酯分散体、聚酯树脂、丙烯酸改性聚氨酯、丙烯酸乳液、丙烯酸树脂、钛白粉、分散助剂、润湿流平剂、消泡剂、有机胺、成膜助剂、相容剂、去离子水(各组分的重量份见下表1中的配方1)。表1:实施例1-8与对比例1-2中的中涂漆的a组分的成分配比上表中,tw-008,tw-401,tw201,tw-103均为湖南邦弗特新材料技术有限公司生产的水性树脂产品,其具体指标如下表2所示(下同)。其中,tw-008是脂肪族聚氨酯多元醇树脂,其分子量mn为5000,多分散系数pdi为1.7。tw-401为水性聚酯多元醇树脂,分子量mn为3500,多分散系数pdi为20-40。tw-201为水性丙烯酸乳液,具有核壳机构。tw-103为水性丙烯酸树脂,分子量mn为12000,多分散系数pdi为2.2。表2:表1中相关产品的性能指标外观固含(wt%)粘度(mpa*s)酸值(mgkoh/g)ph值tw-103淡黄色透明溶液30-326000-1200016.5-187.8-8.8tw-201乳白带蓝光溶液29-3110-2006.5-8.05.5-7.0tw-401半透明带蓝光溶液27-301000-50000-17.0-8.0tw-008半透明带蓝光溶液30-3310-3006.7-8.07.0-8.0上述中涂漆的a组分的制备方法,包括以下步骤:(1)将7重量份丙烯酸树脂在200-400转/分钟条件下搅拌,在搅拌条件下加入20重量份钛白粉、0.6重量份分散助剂、0.015重量份润湿流平剂、0.06重量份消泡剂、0.12重量份有机胺、1.3重量份相容剂和4重量份的去离子水,加完后400-600转/分钟条件下搅拌30min,然后,研磨至细度小于10μm;(2)将步骤(1)得到的原料在200-400转/分钟条件下搅拌,在搅拌条件下加入15重量份水性聚氨酯分散体、18重量份聚酯树脂、9重量份丙烯酸改性聚氨酯、5重量份丙烯酸乳液、0.085重量份润湿流平剂、0.24重量份消泡剂、2重量份成膜助剂、0.48重量份有机胺、4.7重量份相容剂,2重量份去离子水,调粘至80-90s(25℃,福特4#杯),200目滤布过滤,制得中涂漆的a组分。一种用于汽车的面漆,包括c组分和d组分(固化剂)。c组分包括以下原料:聚酯树脂、丙烯酸改性聚氨酯、丙烯酸乳液、丙烯酸树脂、颜料、分散助剂、消泡剂、有机胺、相容剂、润湿流平剂、去离子水(各组分的重量份见下表3中的配方1)。表3:实施例1-8与对比例1-2中的面漆的c组分的成分配比上述面漆的制备方法,包括以下步骤:(1)将6重量份丙烯酸树脂tw-103在200-400转/分钟条件下搅拌,在搅拌条件下加入4重量份炭黑、0.01重量份分散助剂、0.04重量份消泡剂、0.18重量份有机胺、1.2重量份相容剂和5重量份的去离子水,加完后400-600转/分钟条件下搅拌30min,然后,研磨至细度小于10μm;(2)将步骤(1)得到的原料在200-400转/分钟条件下搅拌,在搅拌条件下加入45重量份丙烯酸乳液(sx-5803)、38重量份聚酯树脂(tw-401)、10重量份丙烯酸改性聚氨酯(daotanvtw6462/36wa)、1重量份蓝珠光、0.76重量份紫珠光、0.6重量份铝粉、0.05重量份润湿流平剂、0.15重量份消泡剂、0.37重量份有机胺、10.8重量份相容剂,6重量份去离子水,调粘至80-90s(25℃,福特4#杯),200目滤布过滤,制得珠光黑面漆的c组分。实施例2:一种用于汽车的中涂漆,其成分及制备方法与实施例1相同。一种用于汽车的面漆,面漆分为白面和珠光面两层,白面和珠光面两层面漆的配方中的c组分的配方及各配方的重量份分别如表3中配方2、配方3所示。其制备方法参见实施例1中面漆c组分的制备方法。实施例3:一种用于汽车的中涂漆,其成分及制备方法与实施例1相同,但a组分的成分为表1中的配方2。一种用于汽车的面漆,其成分及制备方法与实施例1相同。实施例4:一种用于汽车的中涂漆,其成分及制备方法与实施例1相同,但a组分的成分为表1中的配方2。一种用于汽车的面漆,其成分及制备方法与实施例2相同。实施例5:一种用于汽车的中涂漆,其成分及制备方法与实施例1相同,但a组分的成分为表1中的配方3。一种用于汽车的面漆,其成分及制备方法与实施例1相同。实施例6:一种用于汽车的中涂漆,其成分及制备方法与实施例1相同,但a组分的成分为表1中的配方3。一种用于汽车的面漆,其成分及制备方法与实施例2相同。实施例7:一种用于汽车的中涂漆,其成分及制备方法与实施例1相同,但a组分的成分为表1中的配方4。一种用于汽车的面漆,其成分及制备方法与实施例1相同。实施例8:一种用于汽车的中涂漆,其成分及制备方法与实施例1相同,但a组分的成分为表1中的配方4。一种用于汽车的面漆,其成分及制备方法与实施例2相同。对比例1:一种用于汽车的中涂漆,其成分及制备方法与实施例1相同,但a组分的成分为表1中的配方5。一种用于汽车的面漆,其成分及制备方法与实施例2相同。对比例2:一种用于汽车的中涂漆,其成分及制备方法与实施例1相同,但a组分的成分为表1中的配方6。一种用于汽车的面漆,其成分及制备方法与实施例2相同。对比例3:将用于汽车的水性中涂漆更换为购自湘江关西的wp-541n白中涂,面漆更换为购自湘江关西的wbc-741n雪貂白(bc1)和冰晶白(bc2),清漆与前面提到的实施例及对比例相同。湘江关西中涂(wp-541n白中涂)及面漆(wbc-741n雪貂白、冰晶白)为现在市场使用的典型3c1b水性汽车涂料。应用实施例:上述用于汽车的中涂漆、面漆的应用,将其用于汽车的3c1b一体化涂装工艺,如图1所示。将实施例1-8以及对比例1-3制备得到的中涂漆、面漆分别与固化剂b组分、d组分加水进行黏度调整后进行喷涂,包括以下步骤:(1)涂装前车身前处理,包括以下步骤:预脱脂→脱脂→一次水洗→二次水洗→表调→磷化→一次水洗→二次水洗→纯水洗→新鲜纯水洗→沥液。(2)电泳底漆处理,包括以下步骤:电泳涂装→超滤液uf冲洗→纯水冲洗→沥液→电泳烘干(烘干温度为160-180℃,保温时间20min左右;强冷后工件温度40℃以下)。(3)pvc车底喷涂及焊缝密封,进行pvc车底喷涂及焊缝密封,140-150℃保温20min后进入下道工序。(4)外饰件装配(预涂底漆),进行保险杠等要求与车身颜色一致的外饰件的装配。(5)电泳底漆打磨及擦净,采用人工进行电泳底漆点磨,打磨室内风速要求0.2-0.3m/s,室内照明强度600lx,打磨砂纸粒度为400-600#,打磨过程确保不出现打磨露底及明显可见的打磨痕;采用湿发打磨时要求所用水为去离子水,并确保工件在进入下一道工序时表面干燥;采用粘性无尘擦拭布除去工件表面的浮尘。(6)中涂机器人涂装及检查,采用离子化空气进一步除去工件表面浮尘,采用机器人进行中涂漆涂装,中涂漆先加水进行黏度调整,调整黏度管控范围为80-90s(25℃,福特4#杯)。喷漆室内风速为0.3m/s,常温流平2-5min后,进行下一步面漆喷涂,中涂漆层干膜膜厚控制为12-15μm。(7)面漆喷涂及检查,面漆先加水进行黏度调整,调整黏度管控范围为80-90s(25℃,福特4#杯);采用人工进行面漆内的喷涂,机器人进行面漆外表面的喷涂,人工操作区风速0.5m/s,机器人自动操作区风速0.3m/s,室内照明不低于800lx,常温流平3min后于80℃闪干5min,检查合格后进入下道工序,面漆层干膜厚度控制为12-15μm。(8)清漆喷涂及检查,采用手工进行内腔清漆喷涂,机器人进行外表面清漆喷涂,人工操作区风速0.5m/s,机器人自动操作区风速0.3m/s,室内照明不低于800lx,清漆湿膜外观检测合格后流平15min。(9)烘干漆膜,漆膜烘烤温度为80℃,保温30-40min。对实施例1-8与对比例1-3中得到的漆膜进行性能检测,结果如下表4所示。各种性能检测标准如下:1、适应于喷涂的性能:中涂漆、面漆喷涂时分散性好,流平性适中,触变性好,涂层均匀、无明显桔皮、无针眼气泡、无杂质。2、适应于固化烘干的性能:烘烤条件为80±5℃,烘烤时间为30min;经固化后涂层达到完全固化交联,溶剂无残留不回粘。3、储存稳定性:将中涂漆和面漆于40℃下保存5天,用福特4号杯评估保存前后的粘度,评估粘度是否在-15%-15%的范围内。4、漆膜外观:利用doi仪器对涂层表面进行分析,以评估长短波以及doi值。5、硬度:三菱铅笔。6、耐水性:将漆膜样板放置在40℃温水中浸泡10天,观察漆膜外观情况。7、附着力:用附着力划格器在漆膜上划出1mm×1mm大小的100个网格,用附着力胶带粘附在已划网格的涂层上,然后将胶带剥离,观察网格漆膜的脱落情况(0-5级,≤1级合格)。8、冲击强度:使用dupont公司的冲击仪,将1kg冲头经过50cm的高度冲击漆膜评估抗冲击强度(≥30kg*cm合格)。9、耐石击性能:在室温条件下,用500g经过淬火的、有棱角、平均直径为2mm的铁砂,在2bar的压力下对漆膜样板涂层施加冲击。观察涂层中石击点的大小以及剥离面积计算出石击后的平均剥离面积和最大剥离面积来确定耐石击等级(1-5级,≤2合格)。10、耐酸0.1mol/lh2so4,25℃、24h,复合板漆膜无明显变化,色差δe≤1(45°角),无明显失光、起泡、膨胀、脱落。11、耐碱0.1mol/lnaoh,25℃、24h,复合板漆膜无明显变化,色差δe≤1(45°角),无明显失光、起泡、膨胀、脱落。12、耐汽油24h漆膜外观无褶皱、明显软化、起泡、脱落、色差及外观变化。自然晾干24h测试附着力0级或1级,硬度≥hb。室温浸泡无裂纹、起泡、剥落、变色等变化;允许轻微的漆膜软化。13、耐湿热(47±1℃/rh96±2%)≥240h,无明显生锈、气泡、变色、开裂或其他破坏现象。14、活化期测定:在室温条件下,按照既定主固比配制好中涂涂料,用福特4号杯测定初始粘度及每隔一个小时的粘度,每次测量粘度后取样喷板,评估粘度变化、涂料施工性能以及试板外观等变化情况(活化期≥3h合格)。表4:利用实施例1-8及对比例1-3中的中涂漆和面漆得到漆膜的性能测试结果当前第1页1 2 3