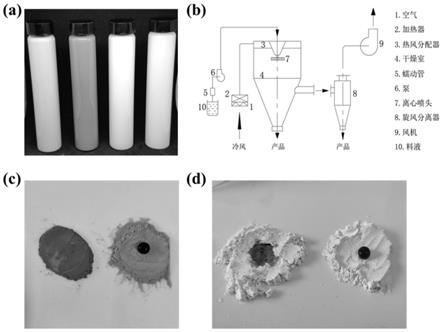
1.本发明属于功能涂层材料制备技术领域,具体涉及一种负载超疏水颗粒的多孔粉体及其制备方法和应用。
背景技术:2.超疏水表面是指在表面微纳米结构和低表面能物质共同作用下,水滴可以在微动力作用下滚落的固体表面,具备三防(防水、防油、防尘)、抗露、减阻、耐蚀等优异的综合性能,可广泛应用于织物的三防、空调的抗露防霜、建筑材料的抗菌防霉、油水分离、抗生物黏附界面和集水体系等工业领域。但是,在磨损、冲击等机械外力和结露、结霜等外界环境作用下,构成超疏水表面最关键的微结构和低表面能物质易破坏,从而造成超疏水性降低或失效,露霜难脱附。实现超疏水表面长效服役,已是材料科学等领域国际前沿研究课题。
3.研究表明,构建类似于荷叶表面的多级粗糙结构或内外结构与组成一致的自相似结构,能提升超疏水表面稳定性,但构建工艺一般较为复杂。与传统的多级粗糙结构和自相似结构超疏水材料相比,有机超疏水涂层具有更好的稳定性。2013年,美国rust
‑
oleum公司和ultratech公司基于柔性有机底漆和超疏水纳米颗粒面漆的底面两层法,先后成功推出neverwet与ultra
‑
ever dry超疏水涂料产品,分别面向民用和工业用。2015年,伦敦大学学院lu等在《science》上证实,以商用万能胶为底漆,超双疏纳米颗粒悬浮液为面漆制备的涂层,手指擦拭、砂纸磨损和刀片刮擦时都表现了良好的机械稳定性。受此启发,本课题组通过树脂交联、颗粒掺杂等手段增加底漆强度和附着力,进一步提升了涂层的稳定性。随后,为了增强超疏水面漆强度,研究人员通过在纳米颗粒中加入少量有机粘合剂,或是直接合成基于有机硅、含氟树脂和纳米颗粒的新型纯有机或有机无机杂化涂料,一步涂覆即获得了具有自相似结构的耐久涂层材料,即底面合一法。例如,《nature materials》2018年曾以封面论文形式报道,将环氧树脂、含氟聚合物、全氟聚醚和ptfe颗粒复合,制备的纯有机超疏水涂层较为柔韧且磨损时材料能逐层去除,所以经30次胶带剥离和磨轮200g负载100转磨损后仍具有超疏水性,同时还可经受高压水流冲击和持续王水腐蚀。但深入研究表明,底面两层法中树脂底漆仅能对超疏水颗粒底部起粘合作用,表层颗粒仍然易损伤;底面合一法中常用的有机硅或含氟树脂很难与超疏水颗粒相容或键合,导致微结构疏松、机械性能差,常规外力时涂层就需不断剥离来保持超疏水性,苛刻外力时涂层使用寿命则非常有限。
4.受荷叶等生物体在受损区域通过蜡质再生重构超疏水性的启发,同行们发明了多种微结构和低表面能物质自修复技术,用于提高超疏水涂层稳定性。微结构修复主要是在温度、湿度、光照、浸泡等刺激下,利用高分子聚合物变形、流动、降解来实现,工艺较为复杂,难度大。利用涂层本体内存储的低表面能有机物自发迁移进行自修复是最常用的方法。其中一种是在外力、光照、酸碱度等刺激下,涂层损伤区储存有低表面能物质的微胶囊破裂使该区域修复。但由于自修复会逐渐损耗低表面能物质,所以再生次数有限。另一种方法则是涂层内含有未反应有机硅或含氟有机物分子,在自由能、熵变和浓度梯度驱使下自发扩散迁移至损伤区,再生成氢键、离子键等动力键来进行修复。由于无物质消耗,涂层寿命在
常规外力作用时普遍较长。例如,密歇根大学tuteja课题组利用玻璃点低于室温的含氟聚氨酯弹性体(fpu)和含氟聚倍半硅氧烷(f
‑
poss)共混制备的涂层,在弹性磨轮250g负载磨损期间,借助间歇加热使f
‑
poss分子迁移不断自修复,即使5000转后仍可保持超疏水性。但需要指出,基于有机涂层材料的自修复技术不但需要一定条件刺激,室温耗时较长,而且外力作用时也难免损耗严重。如上述最优配比的fpu/f
‑
poss涂层(厚度100μm)在磨耗仪250g负载100r后失重高达32%。如何构筑机械性能优异、结合牢固、能快速自修复的超疏水涂层,已成为该类超疏水材料研究的难点。
5.较为理想的机械稳定超疏水涂层,内部应具有结合紧密的自相似结构,底层应与基体结合牢固,并结合瞬时原位的自修复功能,使表面具备稳定的微纳结构。同时,要使其能够在海工、采油、热交换、飞行器、低温工程等领域,涂层还需要具有优异的防腐、防垢、防冰、防污、减阻等性能。
6.申请人之前提出了一种高耐磨常温固化底面合一超疏水涂层及其制备方法(对比文件cn110003735a),主要是先在乙醇溶液中进行硅藻土颗粒和纳米颗粒级配并改性,再旋蒸并冷冻干燥制备超疏水级配颗粒粉体,最后再与低表面能的氟碳树脂及其固化剂一起加入酯、酮、苯和醚等挥发性稀释剂中,涂覆成膜固化后获得具有一定耐磨性的超疏水涂层。但是,该涂层仍为多孔结构,机械外力作用时掉粉严重,环境稳定性也很差,仍然难以进行规模化使用。
7.与完全改性的超疏水颗粒相比,半改性或低改性程度的多孔微米颗粒具有更大的比表面积和富余的活性基团,能够与粘接剂之间形成化学键合,获得优异机械性能的超疏水涂层;同时结合负载的纳米颗粒释放,在涂层被破坏时,可以瞬时原位地修复表面被破坏的结构和化学性质,有几乎能满足抵抗外力破坏所需的所有性能,如极佳的耐候性、高硬度、耐磨性、耐水性等,更加适用于制备长效超疏水涂层。目前,尚未有公开资料报道相关涂层。实际上,只有机械稳定、环境稳定的长效超疏水涂层才能使其真正实现广泛应用,而这目前是此类技术最核心、也最难解决的问题。
技术实现要素:8.解决的技术问题:针对现有方法制备超疏水涂层时普遍存在的大量使用有机溶剂、工艺繁琐、配方适用性差、机械性能不佳、环境稳定性差等问题,本发明提供了一种负载超疏水颗粒的多孔粉体及其制备方法和应用,通过配方和工艺的选择与控制,解决了传统方法中成膜物难以和超疏水颗粒键合、涂层难以自修复、长效性不好等关键问题,显著提升了涂层的机械性能和环境稳定性,并显示出优异的防腐性、防湿热和节能降耗性能,适合大规模制备生产,实现超疏水涂层技术的真正且广泛的应用。
9.技术方案:一种负载超疏水颗粒的多孔粉体的制备方法,步骤如下:按质量份,(1)将1
‑
12份纳米溶胶、2
‑
10份氨水和1
‑
2份水性疏水处理剂分散于60
‑
100份去离子水中,连续搅拌12
‑
48h,制得改性纳米颗粒悬浮液,并通过喷雾干燥法获得超疏水改性纳米颗粒粉体;所述纳米溶胶为粒径1
‑
200nm的氧化铝、二氧化钛和二氧化硅纳米溶胶中的至少一种,固含15wt.%
‑
30wt.%,ph值8
‑
9;所述水性疏水处理剂为水性全氟烷基硅氧烷和水性丙基辛基硅氧烷低聚物中的一种,或是烷基硅氧烷和阳离子或非离子型全氟丙烯酸类表面活性剂混合形成的乳化液,烷基硅氧烷与表面活性剂混合质量比例为(1
‑
3):1;(2)将1
‑
18份多孔微
米陶瓷粉体、0.1
‑
0.5份水性硅烷偶联剂加入60
‑
100份去离子水中或将1
‑
18份多孔微米陶瓷粉体、2
‑
10份氨水、0.4
‑
1份水性疏水处理剂、0.1
‑
0.5份水性硅烷偶联剂加入60
‑
100份去离子水中,连续搅拌12
‑
48h,再加入1
‑
5份步骤(1)所述的超疏水改性纳米颗粒粉体,再连续搅拌12
‑
48h,制得负载超疏水颗粒的多孔颗粒悬浮液,经过滤干燥或喷雾干燥法获得负载超疏水颗粒的多孔粉体;所述多孔微米陶瓷粉体为粒径1
‑
75μm的硅藻土、二氧化硅、氧化铝、氧化锆或以此为原料高温烧结制备的多孔陶瓷颗粒中的至少一种。
10.上述改性纳米颗粒悬浮液也可以是含有聚四氟乙烯、聚苯乙烯、聚丙烯或高密度聚乙烯纳米颗粒乳液中的一种,其固含为30wt.%,ph值8
‑
9。
11.上述过滤干燥是在0.02mpa真空度条件下抽滤分离或在6000rpm转速下离心分离多孔颗粒悬浮液,将过滤出的浆料在80
‑
120℃下干燥1
‑
2h;所述喷雾干燥法是在入口温度160
‑
220℃、喷雾空气压0.3mpa、水分蒸发量1
‑
200l/h条件下喷雾干燥1
‑
2h。
12.上述水性全氟烷基硅氧烷为赢创dynasylan f8815,所述水性丙基辛基硅氧烷低聚物为赢创protectosil ws 670,烷基硅氧烷可以是十三氟三甲氧基硅烷、异丁基三甲氧基硅烷或丙基三甲氧基硅烷中的任一种。
13.上述多孔微米陶瓷粉体形状为片状、柱状、圆盘状或球状,孔径为20nm
‑
2μm,比表面积为40
‑
200m2/g,孔体积为0.08
‑
1.2cm3/g。
14.上述方法制得的负载超疏水颗粒的多孔粉体,粒径1
‑
75μm,比表面积为10
‑
80m2/g,孔体积为0.02
‑
0.6cm3/g,干燥后的粉体具有亲水性,150
‑
250℃加热1
‑
2h后,呈现超疏水性。
15.上述负载超疏水颗粒的多孔粉体在制备涂料或涂层中的应用。
16.应用的制备步骤为:按质量份,(1)油性或水性涂料:将0.1
‑
10份负载超疏水颗粒的多孔粉体机械搅拌分散于10
‑
30份挥发性有机溶剂或去离子水中,当制备水性涂料时也可直接使用1
‑
40负载超疏水颗粒的多孔颗粒悬浮液,随后加入2
‑
10份成膜物、1
‑
4份固化剂、0.05
‑
0.4份丙烯酸酯共聚体作为分散剂、0.1
‑
0.5份附着力促进剂、0.1
‑
0.5份硅烷偶联剂、0.1
‑
0.5份丙二醇甲醚醋酸酯作为稳定剂,机械搅拌10min后即可获得超疏水涂料;通过喷涂、浸涂、滚涂或刷涂方法,涂覆于清洁后的任意基底表面后,置于150
‑
250℃烘箱中加热烘干1
‑
2h,即可获得超疏水涂层;所述挥发性有机溶剂为酮类、醇类、酯类、氟碳类和醚类中的至少一种;所述成膜物为低表面能的氟碳树脂、有机硅及其改性树脂或非疏水性的丙烯酸树脂、环氧树脂、聚氨酯树脂、陶瓷粘结剂、水性丙烯酸树脂、水性环氧树脂或水性聚氨酯树脂中的至少一种;所述附着力促进剂为氨基硅氧烷、烷基硅氧烷或甲硅氧基共聚树脂中的至少一种;所述丙烯酸酯共聚体为聚丙烯酸酯、烷基丙烯酸酯共聚物和丙烯酸酯
‑
丙烯酸共聚物中的至少一种;所述硅烷偶联剂一端为氨基,另一端为乙氧基或甲氧基;固化剂为异氰酸酯类、脂肪族胺类、芳族胺类和酰胺基胺类中的至少一种;(2)粉末涂料:将0.1
‑
10份负载超疏水颗粒的多孔粉体、2
‑
8份粘结剂粉末,放入球磨机中球磨,装入模具中加热熔融,冷却后使用多功能粉碎机粉碎5
‑
10min后,得到尺寸15
‑
48μm的超疏水粉末涂料;将制备的粉料静电喷涂至金属基底上,放置烘箱内150
‑
250℃高温固化10
‑
20min后,冷却至室温即可获得超疏水涂层;所述粘接剂粉末为聚酯树脂粉末、环氧树脂粉末、聚氨酯树脂粉末和氟碳树脂粉末中的至少一种,所述球磨是将混合后的粉末放入球磨罐中,随后加入粒径为1
‑
1.4mm的氧化锆球磨珠,保持球磨机转速为30
‑
300r/min,球磨4
‑
12h;(3)电泳涂料:将2
‑
10份电泳
漆用去离子水稀释5
‑
10倍后,0.05
‑
0.4份丙烯酸酯共聚体作为分散剂,将0.1
‑
10份负载超疏水颗粒的多孔粉体加入上述溶液中,机械搅拌30min后,在30
‑
40v直流电压条件下进行电泳沉积10
‑
30min,然后置于150
‑
250℃烘箱中加热烘干1
‑
2h,即可获得超疏水涂层;所述电泳漆为环氧电泳漆、丙烯酸电泳漆和聚氨酯电泳漆中的至少一种;为所述丙烯酸酯共聚体为聚丙烯酸酯、烷基丙烯酸酯共聚物和丙烯酸酯
‑
丙烯酸共聚物中的至少一种。
17.有益效果:(1)刚制备出的负载超疏水颗粒的多孔粉体呈亲水性,具有非常好的普适性,可以作为功能填料加入各类成膜物中,包括无溶剂、油性或水性树脂、粉末涂料、电泳涂料等,再经过高温固化后,亲水组分分解,使涂层具有超疏水性。(2)负载超疏水颗粒的多孔粉体采用半改性或原始的多孔微米颗粒作为载体,一方面负载超疏水纳米颗粒,赋予涂层优异的超疏水性;另一方面与各类成膜物之间形成键合,显著提高了涂层的机械性能,包括涂层的弹性模量、强度、硬度、附着力和耐磨性等相较于单纯的无此负载颗粒组成的涂层均提高一倍左右;应用负载超疏水颗粒的多孔粉体制备的超疏水涂层的切向附着力和法向附着力相较于粘接剂和常用超疏水涂层均可提高了50%以上;按照iso 2409标准进行划格附着力试验,附着力达到了标准中的0级;相较于所使用的粘接剂和常用的超疏水涂层拉伸强度提高了55
‑
100%,延伸率相较于常用的超疏水涂层提高了约66.7%;耐久性相较于现有技术制备的超疏水涂层如商用的ultra
‑
ever dry涂层和neverwet涂层提高了10倍以上,可以经受住各种苛刻环境。(3)涂层被破坏时,多孔粉体内负载的超疏水纳米颗粒会立即释放出来,修复损伤区域,使涂层维持超疏水性。即涂层修复是原位、智能且即时地进行,完全不同于传统的自修复涂层,后者均需要一定时间的加热、浸泡等方法进行刺激。(4)与对比文件cn106478051相比,本专利应用目标不同,对比文件是通过负载气凝胶降低硅藻土保温材料导热系数,疏水改性降低吸水率,从而用于外墙a级保温。本发明制备的粉体主要用于超疏水涂料配制,提升涂层疏水性、防腐性、防水、防蒸汽等。本发明无需长时间陈化,负载比例可通过颗粒添加量精确控制;对比文件将陈化后的混合物用乙醇、有机硅烷进行表面改性,有机硅烷用量大,烷烃溶剂正己烷进行溶剂交换,再用烷烃溶剂清洗1
‑
5次。本发明在水中进行表面改性,改性剂添加比例可精确控制,才能对包括硅藻土等多孔陶瓷颗粒进行不充分或半改性,使其表面还有羟基,能与涂料中成膜物键合,同时,还能实现对纳米颗粒的充分改性,使其获得强疏水性。对比文件接触角最高120.7度,本发明粉体包含用含氟硅烷改性,疏水疏油性更强,并采用喷雾干燥制粉,更为方便,对比文件采用多级温度梯度干燥。与本课题组之前提出了一种高耐磨常温固化底面合一超疏水涂层及其制备方法(对比文件cn110003735a)相比,本发明更具备普适性,能广泛应用于如多孔硅藻土、二氧化硅、氧化铝、氧化锆或以此为原料高温烧结制备的多孔陶瓷颗粒的负载,且所使用成膜物可以为各类树脂,不仅可以是低表面能的氟碳或有机硅及其改性树脂,还可以是非疏水性树脂或陶瓷涂料,且可以粉末涂料和电泳涂料形式进行具体的实施应用,本发明改性体系为水性体系更为环保。本发明加入硅藻土等多孔微米颗粒并不是为了级配,而主要是为了利用多孔颗粒丰富的孔道负载并隐藏超疏水纳米颗粒,以便成膜物能与多孔颗粒骨架上参与活性基团进行化学键合,提高涂层强度和致密度,避免传统方法中超疏水纳米颗粒表面活性基团少,无法与树脂结合有效结合,导致涂层疏松多孔、机械性能差、环境稳定性不佳等问题;在高湿、低温、水下或盐雾等苛刻环境中,由于涂层的高致密性和优异机械性能,水汽和其它离子难以渗透,从而保护基体;磨损、刮擦、划刻等机械外力作用条件下,基体成膜物损伤
后,多孔颗粒内负载的超疏水纳米颗粒能实时释放,从而让涂层保持优异超疏水性。(6)应用负载超疏水颗粒的多孔粉体制备的涂层具有良好超疏水性,水滴静态接触角>155
°
,滚动角<10
°
;在1000g载荷条件下使用漆膜磨耗仪磨损2000圈后仍能保持水滴静态接触角>155
°
,滚动角<10
°
;在氙灯老化试验2000h、泡水6个月以及高温(85℃)高湿(99%)试验1000h后仍能保持水滴静态接触角>155
°
,滚动角<10
°
;在金属、塑料等基底表面的附着力良好,划格法测试漆膜附着力均为0级,涂层铅笔硬度可达到6h。(7)涂层还具备多功能性,包括优异的防结露、防结霜和防腐性能等,应用负载超疏水颗粒的多孔粉体制备的超疏水涂层的换热器的融霜性能与传统商业化所使用的亲水类涂层换热器相比,过程更加迅速,霜层成块脱落,且没有水滴残留;融霜能耗更低,在不同工况下,如结露,粉尘沾污,结霜,融霜工况下,效率都更高。相较于市场上的防腐涂层(例如环氧树脂和氟碳树脂涂层)和常用的超疏水涂层如ultra
‑
ever dry和neverwet涂层,超疏水涂层不仅其低频阻抗模值提高了数个数量级,并且其防腐时间也提高了十倍以上。且在机械外力作用下仍能长期保持功能性。(8)本发明所述制备方法对基底材质和形状要求低,设备简单、易操作,成本低廉,可大面积施工,能有效提升应用涂层的设备的工作效率,如应用于空调换热器时,起到了显著的节能降耗效果,可广泛应用于5g天线防干扰、金属重防腐、低温防结冰、海洋防污、水面和水下减阻、管道防垢、换热器节能降耗等,获得现有技术难以达到的优异性能。
附图说明
18.图1.负载超疏水颗粒的多孔颗粒悬浮液宏观形貌、喷雾干燥设备原理图和粉体宏观润湿性,其中a为四种负载超疏水颗粒的多孔颗粒悬浮液的宏观形貌,b为喷雾干燥设备原理图,c、d为两种原始多孔颗粒对比通过喷雾干燥后再200℃高温烘后的负载超疏水颗粒的多孔粉体的宏观浸润性;
19.图2.应用负载超疏水颗粒的多孔粉体的涂层(纳米颗粒为氧化铝,微米多孔颗粒为高温烧结的多孔陶瓷颗粒)的宏观形貌和浸润性图,其中a为室温固化的应用负载超疏水颗粒的多孔粉体的涂层宏观浸润性,b为该情况下涂层的接触角,c为高温固化后的应用负载超疏水颗粒的多孔粉体的涂层宏观浸润性,d为该情况下涂层的接触角;
20.图3.应用负载超疏水颗粒的多孔粉体的超疏水涂层(纳米颗粒为二氧化硅,微米颗粒为高温烧结的多孔陶瓷颗粒)的宏观形貌和浸润性,其中a为高温固化后应用负载超疏水颗粒的多孔粉体的超疏水涂层的宏观浸润性,b、c分别为该涂层的接触角与滚动角;
21.图4.负载超疏水颗粒的多孔粉体负载前后的sem图,其中a为原始的高温烧结的多孔陶瓷颗粒,b为其孔洞放大后的形貌,c为制成负载超疏水颗粒的多孔粉体后应用的超疏水涂层表面结构图,d为此时负载超疏水颗粒的多孔粉体的孔洞放大后的形貌。
22.图5.应用负载超疏水颗粒的多孔粉体的超疏水涂层的机械耐久性及磨损后的表面sem图,其中a为涂层的接触角和滚动角随taber磨损周期的变化图,b为涂层在经过1000个磨损周期后的表面形貌图(nem为负载超疏水颗粒的多孔粉体,feve为氟碳树脂,epoxy为环氧树脂,ceramic coating为陶瓷涂料,负载为1kg);
23.图6.应用负载超疏水颗粒的多孔粉体的超疏水涂层表面和截面结构图,其中a为表面形貌,b为截面形貌,插图为颗粒负载在多孔结构中的tem图;
24.图7.应用负载超疏水颗粒的多孔粉体的负载前后地sem图及孔体积变化图,其中a
为多孔陶瓷粉体无负载时的sem图,b为多孔陶瓷粉体负载后的sem图,c为不同负载改性纳米颗粒粉体量的孔体积随孔径变化图;应用负载超疏水颗粒的多孔粉体的超疏水涂层机械性能图;
25.图8应用负载超疏水颗粒的多孔粉体的超疏水涂层微观机械性能,其中a为涂层在微观尺度在10mn载荷下刮擦后的表面形貌,b为涂层在微观尺度受到100mn载荷下刮擦后的表面形貌;
26.图9.应用负载超疏水颗粒的多孔粉体的超疏水涂层的耐磨性,其中a为本课题组之前提出的一种高耐磨常温固化底面合一超疏水涂层(对比文件cn110003735 a)taber磨损后的接触角与滚动角,b为同样试验条件下应用负载超疏水颗粒的多孔粉体的超疏水涂层的耐磨性,c为应用负载超疏水颗粒的多孔粉体的超疏水涂层经受不同苛刻环境的测试包括rca纸带磨损、砂子冲蚀、高压水冲击、高速砂水冲蚀、食盐水浸泡(feve为氟碳树脂,1kg负载);
27.图10.应用负载超疏水颗粒的多孔粉体的超疏水涂层的普适性,其中a为环氧树脂粘接剂制备的超疏水涂层的耐磨性,b为陶瓷涂层粘接剂制备的超疏水涂层的耐磨性,c为丙烯酸树脂粘接剂制备的超疏水涂层的耐磨性(nem@feve,nem@epoxy,nem@ceramica coating和nem@acrylic为不同粘接剂制备的应用负载超疏水颗粒的多孔粉体的超疏水涂层,diatomite@feve,nano
‑
silica@feve,mixed
‑
silica@feve和ultra
‑
ever dry为对比超疏水涂层,feve为氟碳树脂,epoxy为环氧树脂,ceramic coating为陶瓷涂料,acrylic为丙烯酸树脂);
28.图11.应用负载超疏水颗粒的多孔粉体的超疏水涂层、负载超疏水颗粒的多孔粉体及氟碳树脂的ftir红外光谱与超疏水纳米粉体、低改性程度微米多孔粉体及负载超疏水颗粒的多孔粉体的含氟量及羟基含量,其中a为ftir红外光谱图,b为含氟量及羟基含量图;
29.图12.应用负载超疏水颗粒的多孔粉体的超疏水涂层机械性能图,其中a为应力应变曲线,b为应用该负载超疏水颗粒的多孔粉体的超疏水涂层拉伸后的形貌图,c为纳米压痕曲线(nem@feve为应用该负载超疏水颗粒的多孔粉体超疏水涂层,diatomite@feve,nano
‑
silica@feve和mixed
‑
silica@feve为对比超疏水涂层,feve为氟碳树脂);
30.图13.应用负载超疏水颗粒的多孔粉体的超疏水涂层附着力图,其中a为法向附着力图,b为切向附着力图,c划格测试示意图,d超疏水涂层划格测试结果(nem@feve为应用负载超疏水颗粒的多孔粉体的超疏水涂层,diatomite@feve,nano
‑
silica@feve和mixed
‑
silica@feve为对比超疏水涂层,feve为氟碳树脂);
31.图14.应用负载超疏水颗粒的多孔粉体的超疏水涂层的防垢性,其中a为水泥浆料在涂层表面凝固后宏观图片,b为涂层表面水泥浆料掉下后的宏观照片;
32.图15.应用负载超疏水颗粒的多孔粉体的超疏水涂层的抗结露性,其中a为体式显微图片,b为宏观照片;
33.图16.应用负载超疏水颗粒的多孔粉体的超疏水涂层的抗结霜性,其中a为体式显微下霜层生长过程,b体式显微镜下霜层融化过程,c为宏观霜层生长过程,d为宏观霜层融化过程;
34.图17.应用负载超疏水颗粒的多孔粉体的超疏水涂层的热水蒸汽滴状冷凝性,其中a为热水蒸汽冷凝试验设置示意图(蒸汽温度:100℃),b为热水蒸汽诱导的随时间变化的
凝结行为的光学照片,c为taber磨损后(磨损周期:200次,负载为1kg)的涂层的接触角及滚动角随热水蒸汽冷凝试验时间的变化,d为经过200次taber磨损(负载为1kg)后,磨损涂层随时间变化的凝结行为的光学照片;
35.图18.应用负载超疏水颗粒的多孔粉体的超疏水涂层的耐中性盐雾效果,其中a为不同涂层经中性盐雾测试后的宏观照片,b为中性盐雾测试后5000h应用负载超疏水颗粒的多孔粉体的超疏水涂层的宏观形貌(
ⅰ‑ⅳ
为不同粘接剂制备的应用负载超疏水颗粒的多孔粉体的超疏水涂层,
ⅴ
和
ⅵ
为氟碳树脂和环氧树脂涂层,
ⅶ‑ⅸ
为对比超疏水涂层);
36.图19.应用负载超疏水颗粒的多孔粉体的超疏水涂层的耐盐水浸泡测试,其中a为不同涂层经盐水浸泡后的低频阻抗模值,b为不同涂层随盐水浸泡时间的低频阻抗模值变化,c为不同涂层随盐水浸泡时间的开路电位变化(nem@feve和nem@epoxy为不同粘接剂制备的应用负载超疏水颗粒的多孔粉体的超疏水涂层,diatomite@feve和ultra
‑
ever dry为对比超疏水涂层,feve为氟碳树脂涂层,epoxy为环氧树脂涂层)。
37.图20.湿喷工艺制备的应用负载超疏水颗粒的多孔粉体制备的防腐疏水涂层的耐盐雾腐蚀前后的宏观形貌图,其中a为初始防腐疏水涂层的宏观形貌,b为5000h后防腐疏水涂层的宏观形貌。
38.图21.应用负载超疏水颗粒的多孔粉体的超疏水涂层的空调换热器性能,其中a为应用负载超疏水颗粒的多孔粉体的超疏水涂层换热器和商用亲水换热器除霜过程照片,b为应用负载超疏水颗粒的多孔粉体的超疏水涂层,纳米颗粒涂层以及亲水涂层换热器融霜能耗随时间的变化,c为多种工况下,应用负载超疏水颗粒的多孔粉体的超疏水涂层相较于商用亲水涂层换热器的效率提高比例,多种工况包括:结露,灰尘沾污,结霜,融霜;d和e为应用负载超疏水颗粒的多孔粉体的超疏水涂层和纳米颗粒涂层换热器在吹尘后的结霜换热量和融霜能耗,f为为吹尘后,应用负载超疏水颗粒的多孔粉体的超疏水涂层和纳米颗粒涂层换热器的效率衰减比例。
具体实施方式
39.实施例1
40.本实施例中无机纳米颗粒为氧化铝,溶剂为水,疏水改性剂为水性丙基辛基硅氧烷低聚物赢创protectosil ws 670,多孔微米颗粒为以氧化铝和二氧化硅为原料高温烧结的多孔陶瓷颗粒,所述制备步骤如下,按质量份:
41.(1)将10份纳米氧化铝溶胶、5份氨水、1.6份水性丙基辛基硅氧烷低聚物protectosil ws670加入到100份去离子水中连续搅拌24h,得到的改性纳米颗粒悬浮液;
42.(2)将步骤(1)制得的纳米颗粒悬浮液在入口温度160
‑
220℃、喷雾空气压0.3mpa、水分蒸发量1
‑
200l/h条件下喷雾干燥1
‑
2h去除去离子水,得到纳米颗粒粉体;
43.(3)将9份高温烧结制成的多孔陶瓷颗粒、0.2份赢创dynasylan hydrosil 1151氨基水性硅氧烷、加入80份去离子水中搅拌12h,再加入步骤(2)制得的改性纳米粉体再连续搅拌12h,制得负载超疏水颗粒的多孔粉体悬浮液,然后在入口温度160
‑
220℃、喷雾空气压0.3mpa、水分蒸发量1
‑
200l/h条件下喷雾干燥1
‑
2h获得最终的负载超疏水颗粒多孔粉体;
44.(4)将6份负载超疏水颗粒的多孔粉体机械搅拌分散于25份水中,随后加入8份水性环氧树脂、0.4份聚丙烯酸酯作为分散剂、0.5份氨基硅氧烷,0.4份丙二醇甲醚醋酸酯作
为稳定剂,搅拌10min后即可获得应用该多孔粉体的涂料;
45.(5)将步骤(4)制得的应用该多孔粉体的涂料涂覆于清洁后的任意基底表面后,置于200℃烘箱中加热烘干1h,即可获得超疏水涂层。
46.图1a中右1为该负载超疏水颗粒的多孔粉体悬浮液白色悬浮液,通过喷雾干燥后的粉体在经过高温烘后,在其表面,被甲基蓝染色的水滴在其表面呈球状,对比原始粉体体现了其改性后获得的优异疏水性能如图1d所示;图2为该涂层室温固化后及高温固化后的润湿性情况,可以看出室温固化时涂层是亲水的,得益于亲水组份在高温下的分解,经过高温固化后涂层获得超疏水性能。涂层表面的水滴接触角大于155
°
,滚动角小于5
°
;且涂层表面连续、均匀、完整;且无结瘤、缩孔、起泡、针孔、开裂、剥落、粉化、流挂、露底、夹杂脏物等缺陷。
47.实施例2
48.本实施例中无机纳米颗粒为二氧化硅,挥发性有机溶液为丙二醇甲醚,水性疏水处理剂为水性全氟烷基硅氧烷,多孔微米颗粒为以二氧化硅、氧化铝、氧化锆原料高温烧结制成的多孔陶瓷颗粒,所述制备步骤如下,按质量份:
49.(1)将8份纳米硅溶胶、4份氨水、0.5份水性全氟烷基硅氧烷分散于100份去离子水中,连续搅拌24h,制得改性纳米颗粒悬浮液;
50.(2)将步骤(1)制得的超疏水纳米涂料在入口温度160
‑
220℃、喷雾空气压0.3mpa、水分蒸发量1
‑
200l/h条件下喷雾干燥1
‑
2h去除去离子水获得超疏水改性纳米颗粒粉体;
51.(3)将4份高温烧结制成的多孔陶瓷颗粒、0.2份赢创dynasylan hydrosil 1151氨基水性硅氧烷、加入60份去离子水中搅拌12h,再加入步骤(2)制得的改性纳米粉体再连续搅拌12h,制得负载超疏水颗粒的多孔粉体悬浮液,然后在入口温度160
‑
220℃、喷雾空气压0.3mpa、水分蒸发量1
‑
200l/h条件下喷雾干燥1
‑
2h获得最终的多孔粉体;
52.(4)将5份负载超疏水纳米颗粒的多孔粉体机械搅拌分散于30份丙二醇甲醚中,随后加入10份氟碳树脂、4份脂肪族聚异氰酸酯固化剂、0.25份聚丙烯酸酯作为分散剂、0.25份氨基硅氧烷、0.2份丙二醇甲醚醋酸酯作为稳定剂,搅拌10min后即可获得应用该粉体的超疏水涂料,将氟碳树脂和脂肪族聚异氰酸酯固化剂等量替换为环氧树脂和脂肪族胺类固化剂或陶瓷涂料和脂肪族聚异氰酸酯固化剂,则可得到不同粘结剂下的涂料;
53.(5)将步骤(4)制得的应用该粉体的涂料涂覆于清洁后的任意基底表面后,置于160℃烘箱中加热烘干2h,即可获得超疏水涂层。
54.图1中砖红色的浆料为负载超疏水颗粒的多孔粉体悬浮液的宏观形貌,通过喷雾干燥后的粉体在经过高温烘后,被甲基蓝染色的水滴在其表面呈球状,对比原始粉体体现了其改性后获得的优异疏水性能,图3为应用该负载超疏水颗粒的多孔粉体的超疏水涂层的宏观照片和润湿性,涂层表面的水滴接触角为163.6
°
,滚动角为1.6
°
。图4显示了原始的高温烧结的多孔陶瓷颗粒及制备成负载超疏水纳米颗粒的多孔粉体在涂层中的形貌,可以看出纳米二氧化硅颗粒负载到了多孔陶瓷颗粒的孔洞中,在涂层中负载超疏水纳米颗粒的多孔粉体与粘结剂一起形成了致密的结构。
55.实施例3
56.图5为实施例2中负载超疏水颗粒的多孔粉体制备的超疏水涂层的机械耐磨性及在遭受严苛机械磨损后表面的sem图。得益于负载超疏水颗粒的多孔粉体本身良好的分散
性和与粘结剂的强结合力,以及经过试验优选的高强度高温烧结的多孔陶瓷颗粒的“盔甲”保护作用和在经受严苛机械破坏情况下超疏水纳米颗粒的释放,该超疏水涂层在taber磨损(1kg负载)2000周期后仍能保持优异超疏水性能。
57.实施例4
58.本实施例中无机纳米颗粒为二氧化硅,挥发性有机溶液为乙酸丁酯,水性疏水处理剂为水性全氟烷基硅氧烷,多孔微米颗粒为以硅藻土,所述制备步骤如下,按质量份:
59.(1)将8份链状纳米硅溶胶、2份球状纳米硅溶胶、6份氨水、2份水性全氟烷基硅氧烷分散于100份去离子水中,连续搅拌24h,制得改性纳米颗粒悬浮液;
60.(2)将步骤(1)制得的超疏水纳米涂料在入口温度160
‑
220℃、喷雾空气压0.3mpa、水分蒸发量1
‑
200l/h条件下喷雾干燥1
‑
2h去除去离子水获得超疏水改性纳米颗粒粉体;
61.(3)将16份硅藻土、3份氨水、0.2份水性全氟烷基硅氧烷、0.1份赢创dynasylan hydrosil1151氨基水性硅氧烷、加入60份去离子水中搅拌12h,再加入步骤(2)制得的改性纳米粉体再连续搅拌12h,制得负载超疏水颗粒的多孔粉体悬浮液,然后在入口温度160
‑
220℃、喷雾空气压0.3mpa、水分蒸发量1
‑
200l/h条件下喷雾干燥1
‑
2h获得最终的多孔粉体;
62.(4)将6份负载超疏水纳米颗粒的多孔粉体机械搅拌分散于24份乙酸丁酯中,随后加入8份氟碳树脂、3.2份脂肪族聚异氰酸酯固化剂、0.2份聚丙烯酸酯作为分散剂、0.2份氨基硅氧烷、0.15份丙二醇甲醚醋酸酯作为稳定剂,搅拌10min后即可获得应用该粉体的超疏水涂料,将氟碳树脂和脂肪族聚异氰酸酯固化剂等量替换为环氧树脂和脂肪族胺类固化剂或陶瓷涂料和脂肪族聚异氰酸酯固化剂,则可得到不同粘结剂下的涂料;
63.(5)将步骤(4)制得的应用该粉体的涂料涂覆于清洁后的任意基底表面后,置于180℃烘箱中加热烘干2h,即可获得超疏水涂层。
64.图1a左1为该负载超疏水颗粒的多孔粉体悬浮液,其刚喷雾干燥出来的粉具有亲水性可以分散到各种溶剂中;在高温烘后具有超疏水性,仍可以有效分散到有机溶剂中以形成均匀的涂料。
65.实施例5
66.图6为实施例4中应用负载超疏水颗粒的多孔粉体的超疏水涂层表面和截面结构图从中可以看出超疏水纳米颗粒能够成功的负载到多孔硅藻土的孔隙中。图7为负载前后的多孔硅藻土颗粒的形貌图与不同负载量的情况下硅藻土孔径的变化,纳米颗粒太少则多孔粉体负载所达到的优异效果不突出,纳米颗粒太多则无法被负载其中会降低颗粒与粘结剂的结合力,导致涂层耐久性的下降;本发明经过多次试验通过不同形状的纳米硅溶胶(链状与球形纳米颗粒的配合)来达到所使用的硅藻土的最高负载量30%,实现负载量的精确控制。
67.实施例6
68.图8为实施例1中硅藻土颗粒中负载的纳米二氧化硅在微观不同压力下刮擦的sem形貌图,体现了涂层的微观机械性能。负载为10mn时,划擦后sem图像的插图显示硅藻土孔洞中所负载的完整的纳米二氧化硅。硅藻土上仅观察到一点划痕,表明硅藻土具有足够的机械强度以抵抗磨损的能力,硅藻土为纳米二氧化硅提供了“盔甲”保护。当负载增加到100mn时,硅藻土颗粒被破坏,嵌入的纳米二氧化硅从孔隙中逸出并在涂层表面观察到,表
明自适应释放补偿了颗粒的损失,实时修复损伤区域,使涂层维持超疏水性。
69.实施例7
70.本课题组之前提出了一种高耐磨常温固化底面合一超疏水涂层及其制备方法(对比文件cn110003735 a),与之相对比,取本发明实施例4中最终的负载超疏水颗粒的多孔粉体按照对比文件cn110003735 a实施例2的试验条件,按质量份,将4份负载超疏水颗粒的多孔粉体加入到25份丙酮溶液中,加入0.1份丙烯酸酯共聚体,超声分散15min,然后加入10份氟碳树脂,机械搅拌10min,加入0.5份氯化改性聚丙烯,加入0.6份丙二醇甲醚醋酸酯,加入0.2份氢化蓖麻油,加入0.3份二丁基二月桂酸锡,搅拌10min后加入2.5份相同的氟碳树脂固化剂,机械搅拌均匀后获得最终的涂料,将涂料喷涂于玻璃样品表面获得最终的超疏水涂层。图9a为对比文件cn110003735 a实施例2中制备的涂层的耐磨性,图9b为取本发明实施例4中最终的负载超疏水颗粒的多孔粉体制备的涂层的耐磨性,可见相同试验条件下耐磨性有了近5倍的提升,且应用负载超疏水颗粒的多孔粉体制备的超疏水涂层环境稳定性能更优异,致密不掉粉,涂层分别经1kg负载的taber磨损、rca纸带磨损、砂子冲蚀、高压水冲击、高速砂水冲蚀、食盐水浸泡后,均能维持超疏水性。耐久性相较于现有技术制备的超疏水涂层如商用的ultra
‑
ever dry涂层和neverwet涂层提高了10倍以上,可以经受住各种苛刻环境。
71.实施例8
72.图10为实施例4中应用负载超疏水颗粒的多孔粉体制备的智能长效超疏水涂料的普适性,该方法可以适用于各种有机树脂和无机粘接剂,既可以是低表面能的粘结剂也可以是非疏水性粘结剂,均可使超疏水涂层的耐久性显著提高。已报道的超疏水涂层技术,往往是通过优选某一种粘接剂或者特定的粘接剂才能提高涂层的耐久性,本发明的普适性,有效地解决了该限制。
73.实施例9
74.图11为实施例4中应用负载超疏水颗粒的多孔粉体的超疏水涂层、负载超疏水颗粒的多孔粉体及氟碳树脂的ftir红外光谱与实施例4步骤(1)得到的超疏水纳米粉体、实施例4步骤(3)中不添加步骤(1)纳米粉体直接喷雾干燥得到的低改性程度微米多孔粉体及实施例4最终的负载超疏水颗粒的多孔粉体的含氟量及羟基含量。氟碳树脂树脂包覆负载超疏水颗粒的多孔粉体后,
‑
oh和
‑
n=c=o峰消失,而
‑
n
‑
c
‑
峰增强,表明树脂与负载超疏水颗粒的多孔粉体成功结合。通过氟接枝量和羟基残留量可以看出二氧化硅的残留羟基比低改性程度微米多孔粉体低10倍,从而在经过高温烘后达到超疏水性,而低改性程度的微米多孔粉体提供了可与树脂和基底紧密结合的羟基,控制制粉或制浆工艺,使得制备的粉体或浆料中保留部分活性基团,从而具有亲水性,以便提高在成膜物中的分散性。通过精确调控改性程度,从而使最终的负载超疏水颗粒的多孔粉体的含氟量及羟基含量处在最佳范围。图12为应用负载超疏水颗粒的多孔粉体制备的超疏水涂层的机械性能。超疏水涂层相较于所使用的粘接剂和常用的超疏水涂层拉伸强度提高了55
‑
100%,延伸率相较于常用的超疏水涂层提高了约66.7%,在拉伸至屈服强度后,粘接剂依旧附着在多孔粉体表面,呈拉丝状态,为抗拉强度的提高提供了有利作用;除此,超疏水涂层的抗压力学性能相较于常用超疏水涂层也显著提高,包括硬度、杨氏模量等。图13为应用负载超疏水颗粒的多孔粉体制备的的超疏水涂层的附着力。超疏水涂层的切向附着力和法向附着力相较于粘接剂和常用超疏
水涂层均提高了50%以上。按照iso 2409标准进行划格附着力试验,使用的胶带在涂层上的黏附强度不低于(10
±
1)n/25mm,可以发现,涂层无任何脱落,100%附着,达到了标准中的0级。
75.实施例10
76.本实施例中无机纳米颗粒为二氧化钛,挥发性有机溶液为丙酮,疏水改性剂为丙基三甲氧基硅烷和赢创protectosil ws 670,多孔微米颗粒为多孔二氧化硅,所述制备步骤如下,按质量份:
77.(1)将10份纳米二氧化钛溶胶、6份氨水、0.3份丙级三甲氧基硅烷、0.8份赢创protectosil ws 670分散于100份去离子水中,连续搅拌24h,制得改性纳米颗粒悬浮液;
78.(2)将步骤(1)制得的超疏水纳米涂料在6000转离心机离心下,过滤上清液,去除去离子水后在真空干燥箱中干燥1h,获得超疏水改性纳米颗粒粉体;
79.(3)将8份多孔二氧化硅、0.3份赢创dynasylan hydrosil 1151氨基水性硅氧烷、加入80份去离子水中搅拌12h,再加入步骤(2)制得的改性纳米颗粒粉体再连续搅拌12h,制得负载超疏水颗粒的多孔颗粒悬浮液,然后在在入口温度160
‑
220℃、喷雾空气压0.3mpa、水分蒸发量1
‑
200l/h条件下喷雾干燥1
‑
2h获得最终的多孔粉体;
80.(4)将6份负载超疏水纳米颗粒的多孔粉体机械搅拌分散于30份丙酮中,随后加入12份环氧树脂、2份封闭型聚异氰酸酯固化剂、0.5份聚丙烯酸酯作为分散剂、0.4份氨基硅氧烷、0.3份丙二醇甲醚醋酸酯作为稳定剂,搅拌15min后即可获得应用该粉体的超疏水涂料;
81.(5)将步骤(4)制得的应用负载超疏水颗粒的多孔粉体的涂料涂敷于清洁后的任意基底表面后,置于220℃烘箱中加热烘干2h,即可获得超疏水涂层。
82.图1a左3即为该负载超疏水颗粒的多孔粉体悬浮液,其刚喷雾干燥出来的粉具有亲水性可充分分散到有机溶剂中以形成均匀的涂料。
83.实施例11
84.图14为实施例10中应用负载超疏水颗粒的多孔粉体制备的智能长效超疏水涂料的防垢性,使用的水泥浆料在涂层表面呈球形无法铺展,体现了涂层防垢性能,当倾斜涂层时,随着重力的作用凝固的水泥浆料自然滑落,涂层表面仍然保持初始状态。
85.实施例12
86.图15为实施例10中应用负载超疏水颗粒的多孔粉体制备的超疏水涂层的抗结露性能。露滴凝结时均为球状,且数量较少,覆盖率较低,随着露滴的长大,在重力的作用下,露滴轻易的滚离涂层表面,并带走沿途的露滴,使凝露覆盖率大幅度降低;露出的干燥区域,随着时间的推移,会继续发生结露,滚离,从而达到一个动态的平衡,使涂层表面的露滴覆盖率始终维持在一个较低的水平。
87.实施例13
88.图16为实施例10中应用负载超疏水颗粒的多孔粉体的超疏水涂层的抗结霜性。霜层初始生长速度很慢,直至冷凝20min后,涂层表面才开始出现明显的霜层,结霜行为被明显抑制;融霜时,霜层整层卷起脱落,融霜速度快;融霜后,表面干燥无任何残留。显示出优异的抗结霜性能。
89.实施例14
90.图17为实施例10中的应用负载超疏水颗粒的多孔粉体制备的超疏水涂层的热水蒸汽冷凝性。热水蒸汽液滴冷凝时均为球形,且形成速度很慢,覆盖率较低,随着冷凝液滴的长大,在重力的作用下,液滴轻易地滚离涂层表面,并带走沿途的液滴,随着时间的推移,会继续发生冷凝,滚离,从而达到一个动态的平衡,使涂层表面的液滴覆盖率始终维持在一个较低的水平。在施加负载磨耗后涂层表面在一开始会冷凝大量液滴,但是热水蒸汽液滴冷凝时仍为球形,且随着时间推移,会再次达到一个动态平衡状态,使涂层表面维持低的液滴覆盖率。
91.实施例15
92.图18为实施案例4中应用负载超疏水颗粒的多孔粉体制备的超疏水涂层的耐盐雾腐蚀效果。
‑ⅳ
为不同粘接剂制备的应用负载超疏水颗粒的多孔粉体的超疏水涂层,
ⅴ
和
ⅵ
为氟碳树脂和环氧树脂涂层,
ⅶ‑ⅸ
为对比超疏水涂层;负载超疏水颗粒的多孔粉体制备的超疏水涂层在1000h后表面仍然没有出现任何锈迹,且在各种粘结剂中都体现了优异的耐盐雾腐蚀性。当到达5000h时,涂层滚动角仍小于20
°
,且样品表面无锈迹。
93.实施例16
94.图19为实施案例4中应用负载超疏水颗粒的多孔粉体制备的超疏水涂层的耐盐水浸泡效果。相较于市场上的防腐涂层(例如环氧树脂和氟碳树脂涂层)和常用的超疏水涂层如ultra
‑
ever dry和neverwet涂层,超疏水涂层不仅其低频阻抗模值提高了数个数量级,并且其防腐时间也提高了十倍以上。除此,超疏水涂层的开路电位随着食盐水浸泡的时间延长,始终保持稳定,而其他涂层的开路电位出现了显著的降低。
95.实施例17
96.图20为采用实施案例4中的涂料,将氟碳树脂与其固化剂等量替换为环氧树脂及其固化剂,以湿喷工艺制备的应用负载超疏水颗粒的多孔粉体制备的防腐疏水涂层的耐盐雾前后宏观形貌图,涂层表面由环氧树脂形成致密的结构保护基底,负载超疏水颗粒的多孔粉体均匀分散在涂层中形成对外部盐雾渗入的阻隔,对比单纯的环氧树脂涂层防腐性能提高近百倍,即使在盐雾5000h后样品表面也没有出现锈迹。
97.实施例18
98.图21为实施案例10中应用负载超疏水颗粒的多孔粉体制备的超疏水涂层的换热器的融霜性能;与传统商业化所使用的亲水类涂层换热器相比,应用负载超疏水颗粒的多孔粉体制备的超疏水涂层的换热器的融霜过程更加迅速,霜层成块脱落,且没有水滴残留;与纳米超疏水涂层及商业化亲水涂层相比应用负载超疏水颗粒的多孔粉体制备的超疏水涂层融霜能耗更低,且在不同工况下,如结露,粉尘沾污,结霜,融霜工况下,效率都更高。在吹尘试验种模拟实际工况下污染及砂尘带来的损伤状况,应用负载超疏水颗粒的多孔粉体制备的超疏水涂层的换热器相较于纳米超疏水涂层的换热器结霜换热量更高和融霜能耗更低,吹尘后换热器效率衰减比例更低,显现了应用负载超疏水颗粒的多孔粉体制备的超疏水涂层的突破创新性及长效性。
99.以上所述仅是本发明的优选实施方式,应当指出,对于本技术领域的普通技术人员来说,在不脱离本发明原理的前提下还可以做出若干改进,这些改进也应视为本发明的保护范围。