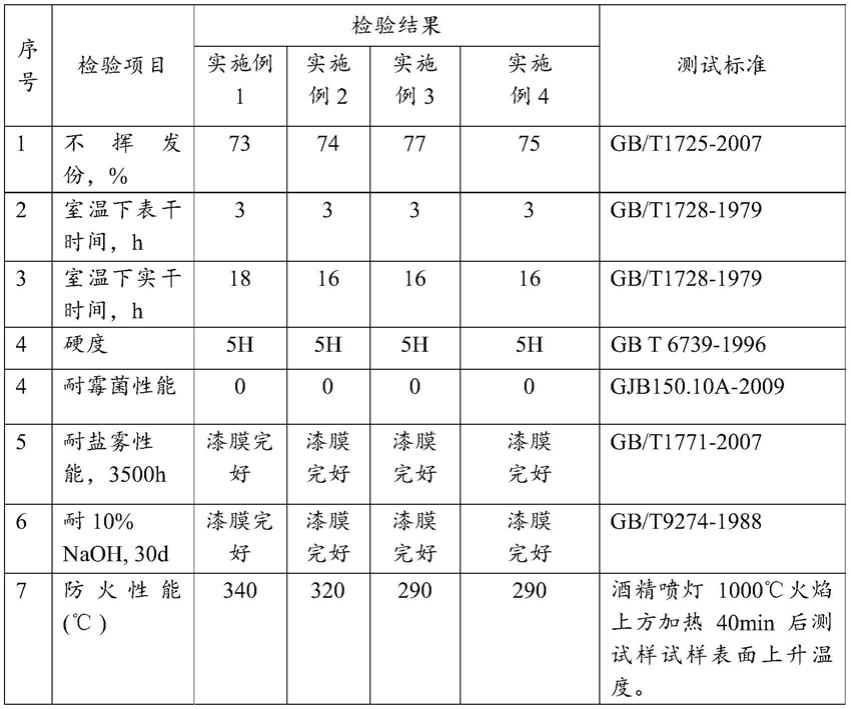
1.本发明涉及涂料制备技术领域,具体涉及一种氟碳涂料及其制备方法和应用。
背景技术:2.船舶水线以下的部分长期浸泡在海水中,不仅受到海水本身的腐蚀,还受到各种粘附于材料表面的海洋生物的腐蚀。而没有浸泡于海水中的船体,潮湿的内舱、露天甲板等区域也长期处于海洋大气腐蚀环境下。因此船舶的金属组件部分均会由于长期不同程度地受到海水腐蚀、海洋大气腐蚀及微生物腐蚀而逐渐失效。海洋环境下的腐蚀对海洋经济效益以及海上军事安全带来很大的负面影响。
3.而目前报道的海洋环境杀菌防腐涂层大多为常规溶剂型涂层或者水性低voc(volatile organic compounds,挥发性有机化合物)涂层,水性涂层虽然相比于常规溶剂型涂层voc排放量明显减少,但存在易缩孔,对施工环境条件要求更高,一般需高温烘烤干燥成膜的缺点。常规溶剂型涂料则主要以高分子量树脂、填料与溶剂组成,通常固含量低,使用的有机溶剂较多,在施工时,涂膜中挥发的有机物含量高,安全环保性较低,对人体和环境造成危害。基于以上现状,亟需开发高固体含量的溶剂型杀菌海洋防腐涂料。
4.在高固体份溶剂型涂料中,有机溶剂的使用量减少,要保证合理的施工粘度则必须采用比常规树脂分子量更小的低分子量低粘度树脂为原料。树脂分子量越小、分子链中参与交联的活性基团数量也会减少,必然导致基体树脂的总体聚合度降低,其网状交联程度较常规涂层有所下降,这必然会影响涂层的力学性能以及抗介质渗透性,因此需要进一步采用特殊功能型添加剂以提高涂料的力学性能和耐腐蚀性能。
技术实现要素:5.本发明的目的在于克服上述技术不足,提供一种氟碳涂料及其制备方法和应用,解决现有技术中涂料因获得高固体含量的需求而采用低分子量树脂导致的力学性能和耐腐蚀性能较差的技术问题。
6.为达到上述技术目的,本发明的技术方案提供一种氟碳涂料及其制备方法和应用。
7.本发明提出一种氟碳涂料,由组分a和组分b按照质量比10:(0.8
‑
1)混合制得;所述组分a,按照重量份数计算,包括氟碳树脂60
‑
65份、改性晶须氧化锌5
‑
10份、改性二氧化硅5
‑
10份、钼酸锌0.3
‑
0.5份、硼酸锌4
‑
8份、硫酸锌0.3
‑
0.5份、分散剂0.5
‑
1.8份、流平剂0.2
‑
0.5份、消泡剂0.1
‑
0.3份和溶剂12
‑
14份;所述组分b为脂肪族多异氰酸酯;所述改性晶须氧化锌由晶须氧化锌通过偶联剂改性制得;所述改性二氧化硅由二氧化硅通过硅烷偶联剂改性制得。
8.进一步地,所述改性晶须氧化锌或者所述改性二氧化硅由以下步骤制得:
9.按照乙醇和水的体积比(10
‑
11):1配置成混合溶剂,之后按照晶须氧化锌或者二氧化硅与所述混合溶剂的质量比1:(30
‑
35)进行混合得到混合溶液;
10.将所述混合溶液与硅烷偶联剂按照质量比1:(12
‑
13)混合,之后调节ph值至3.5
‑
4.5,之后静置密封,之后在60
‑
70℃下反应得到所述改性晶须氧化锌或者所述改性二氧化硅。
11.进一步地,所述晶须氧化锌的直径为0.5
‑
5μm,长度为10
‑
50μm。
12.进一步地,所述二氧化硅的平均粒径为30
‑
35nm。
13.进一步地,所述硅烷偶联剂为kh550和kh570中的一种或者两种。
14.进一步地,所述分散剂为basf4401或byk161中的一种或者两种。
15.进一步地,所述氟碳树脂为hlr
‑
6和hlr
‑
670的混合氟碳树脂,所述hlr
‑
6和所述hlr
‑
670的质量比为1:(1
‑
3)。
16.进一步地,所述脂肪族多异氰酸酯为bayern3390或者basonat hi
‑
190中的一种或两种;当所述脂肪族多异氰酸酯为bayern3390和basonat hi
‑
190的混合物时,所述bayern3390与所述basonat hi
‑
190的质量比为1:(1
‑
1.2)。
17.此外,本发明还提出一种上述氟碳涂料的制备方法,包括步骤:将组分a和组分b按照配比混合,之后按照速度500r/min
‑
800r/min搅拌得到所述氟碳涂料。
18.进一步地,本发明还提出一种上述氟碳涂料或者上述制备方法制得的氟碳涂料在制作海洋舰船表面涂层中的应用。
19.与现有技术相比,本发明的有益效果包括:
20.使用了高硬度的无机氧化物填料晶须氧化锌和纳米二氧化硅,并且晶须氧化锌和纳米二氧化硅都由硅烷偶联剂进行了修饰,通过偶联作用在涂料中形成微观无机物增强网络,制得涂层时,通过无机填料本身的高硬度特征以增强涂层硬度的同时,其表面修饰的硅烷偶联剂分子其有机链段与涂层之间的有机链段形成范德华/氢键力等键合作用,从而显著增加涂料中无机组分与有机组分之间的链接强度,也解决了低分子量氟碳树脂较常规高分子量树脂交联度降低的问题,进一步增强其力学性能;涂料中添加的硫酸锌、钼酸锌以及硼酸锌可从两方面的作用途径增强涂层的防腐功能:一方面这三种添加剂均含有锌离子,提供了较强的杀菌功能,可抑制活体微生物的粘附以及由此引发的微生物腐蚀;另一方面这几种锌盐属于无机类缓蚀剂物质,具有很好的协同缓蚀效果。制得涂层后,若有介质渗透到涂层或者涂层和基体之间的界面,锌盐可溶解于介质中,阳离子部分即锌离子通过生成氢氧化锌、碱式碳酸锌等产物覆盖于金属表面阳极区而形成保护膜;阴离子中的钼酸根以及硼酸根可在金属表面发生吸附、沉积、或通过自身的氧化性来改变金属表面膜的性质,从而起到抑制金属活性溶解,促进金属钝化的作用,以上缓蚀剂物质的缓蚀作用可显著增强基体(被涂覆金属物)抗腐蚀能力、延长其使用寿命,从而在各组分的配合下可确保涂料的力学性能的同时提高其抗腐蚀性能,硬度高达5h,还具有较好的耐盐雾性能和耐氢氧化钠性能,耐盐雾性能高达3500h,耐10%氢氧化钠可达30天。
21.另外,缓蚀剂中的硼酸锌以及晶须氧化锌都具有阻燃的作用,添加至涂料中赋予了涂料防火功能,从而使涂层具有多功能性。
具体实施方式
22.本具体实施方式提供了一种氟碳涂料,由组分a和组分b按照质量比10:(0.8
‑
1)混合制得;所述组分a,按照重量份数计算,包括氟碳树脂60
‑
65份、改性晶须氧化锌5
‑
10份、改
性二氧化硅5
‑
10份、钼酸锌0.3
‑
0.5份、硼酸锌4
‑
8份、硫酸锌0.3
‑
0.5份、分散剂0.5
‑
1.8份、流平剂0.2
‑
0.5份、消泡剂0.1
‑
0.3份和溶剂12
‑
14份;所述组分b为脂肪族多异氰酸酯;所述改性晶须氧化锌由晶须氧化锌通过偶联剂改性制得;所述改性二氧化硅由二氧化硅通过硅烷偶联剂改性制得。
23.进一步地,本具体实施方式中所述改性晶须氧化锌或者所述改性二氧化硅由以下步骤制得:
24.按照乙醇和水的体积比(10
‑
11):1配置成混合溶剂,之后按照晶须氧化锌或者二氧化硅与所述混合溶剂的质量比1:(30
‑
35)进行混合得到混合溶液,将混合溶液磁力搅拌20
‑
30min,超声分散30
‑
40min;其中所述晶须氧化锌的直径为0.5
‑
5μm,长度为10
‑
50μm;所述二氧化硅的平均粒径为30
‑
35nm;
25.将超声分散后的所述混合溶液与硅烷偶联剂按照质量比1:(12
‑
13)混合,之后通过草酸调节ph值至3.5
‑
4.5,之后室温下静置水解1
‑
1.5h,之后密封,之后在60
‑
70℃下磁力搅拌反应90
‑
120min,之后抽滤混合液,无水乙醇洗涤3次,恒温箱中110
‑
120℃维持2
‑
3h烘干,再将产物用研钵研磨,得到所述改性晶须氧化锌或者所述改性二氧化硅。
26.进一步地,本具体实施方式中,所述硅烷偶联剂为kh550和kh570中的一种或者两种;所述分散剂为basf4401或byk161中的一种或者两种;所述流平剂为byk354或byk399的一种或者两者;所述消泡为byk1790或byk8801消泡剂中的一种或者两种;所述氟碳树脂为hlr
‑
6和hlr
‑
670的混合氟碳树脂,所述hlr
‑
6和所述hlr
‑
670的质量比为1:(1
‑
3);所述脂肪族多异氰酸酯为bayern3390或者basonat hi
‑
190中的一种或两种;当所述脂肪族多异氰酸酯为bayern3390和basonat hi
‑
190的混合物时,所述bayern3390与所述basonat hi
‑
190的质量比为1:(1
‑
1.2);所述溶剂为丙二醇甲醚醋酸酯(pma)与乙酸正丁酯(bac)的混合溶剂,pma与bac的质量比1:(0.35
‑
0.55)。
27.本具体实施方式中的氟碳涂料中,首先为实现高固体份配方,基体树脂选用低分子量低粘度高固体份树脂,树脂种类则选择表面能较低的氟碳树脂,相比于其它类型如环氧类、丙烯酸类、聚氨酯类树脂涂料表面粘附性大大减弱,可使细菌粘附性明显下降,进而在具有抑菌、杀菌功能的含锌类化学物作用下能够有效抑菌。另外添加的纳米增强体改性二氧化硅同时还是效果优异的触变剂,解决了高固体份涂料流变性能降低的问题。
28.同时硼酸锌是一种无卤环保阻燃剂防火剂,晶须zno对涂料防火性能也有一定提升,因此通过本技术所设计的配方不仅可以获得高固体份、抗菌、耐蚀等优良特性,同时也大大增强了涂层防火性能,在火灾过程中能有效减缓火势的蔓延,防止底材和背火面迅速升温,可给人们逃离火场、组织救援赢得宝贵的时间。
29.此外,本具体实施方式还包括上述氟碳涂料的制备方法,包括步骤:将组分a和组分b按照配比混合,之后按照速度500r/min
‑
800r/min搅拌20
‑
30min得到所述氟碳涂料。
30.本具体实施方式还包括一种上述氟碳涂料或者上述制备方法制得的氟碳涂料在制作海洋舰船表面涂层中的应用。
31.为了使本发明的目的、技术方案及优点更加清楚明白,以下结合实施例,对本发明进行进一步详细说明。应当理解,此处所描述的具体实施例仅仅用以解释本发明,并不用于限定本发明。
32.实施例1
33.本实施例提出一种氟碳涂料,由组分a和组分b bayern3390按照质量比10:0.8混合,之后投入高速搅拌机中按照速度800r/min,搅拌20min制得;
34.所述组分a,按照重量份数计算,包括hlr
‑
6以及hlr
‑
670树脂各33份,改性晶须氧化锌5份,改性二氧化硅10份,钼酸锌0.3份、硼酸锌4份、硫酸锌0.3份、分散剂byk161 1.1份、流平剂byk399 0.5份、消泡剂byk8801 0.3份、溶剂pma9份,bac 3.5份。
35.所述改性晶须氧化锌或者所述改性二氧化硅由以下步骤制得:
36.按照乙醇和水的体积比10:1配置成混合溶剂,之后按照晶须氧化锌或者二氧化硅与所述混合溶剂的质量比1:30进行混合得到混合溶液,将混合溶液磁力搅拌20min,超声分散30min;其中所述晶须氧化锌的直径为0.5
‑
5μm,长度为10
‑
50μm;所述二氧化硅的平均粒径为30nm;
37.将超声分散后的所述混合溶液与硅烷偶联剂kh550按照质量比1:13混合,之后通过草酸调节ph值至3.5,之后室温下静置水解1h,之后密封,之后在60℃下磁力搅拌反应120min,之后抽滤混合液,无水乙醇洗涤3次,恒温箱中120℃维持2h烘干,再将产物用研钵研磨,得到所述改性晶须氧化锌或者所述改性二氧化硅。
38.实施例2
39.本实施例提出一种氟碳涂料,由组分a和组分b basonat hi
‑
190按照质量比10:0.9混合,之后投入高速搅拌机中按照速度800r/min,搅拌20min制得;
40.所述组分a,按照重量份数计算,包括hlr
‑
6树脂20份、hlr
‑
670树脂45份,改性晶须氧化锌10份,改性二氧化硅5份,钼酸锌0.5份、硼酸锌6份、硫酸锌0.4份、分散剂byk161 0.5份、流平剂byk399 0.5份、消泡剂byk8801 0.1份、溶剂pma8份,bac 4份。
41.所述改性晶须氧化锌或者所述改性二氧化硅由以下步骤制得:
42.按照乙醇和水的体积比11:1配置成混合溶剂,之后按照晶须氧化锌或者二氧化硅与所述混合溶剂的质量比1:35进行混合得到混合溶液,将混合溶液磁力搅拌25min,超声分散35min;其中所述晶须氧化锌的直径为0.5
‑
5μm,长度为10
‑
50μm;所述二氧化硅的平均粒径为35nm;
43.将超声分散后的所述混合溶液与硅烷偶联剂kh550按照质量比1:12混合,之后通过草酸调节ph值至4.0,之后室温下静置水解1.5h,之后密封,之后在70℃下磁力搅拌反应90min,之后抽滤混合液,无水乙醇洗涤3次,恒温箱中110℃维持3h烘干,再将产物用研钵研磨,得到所述改性晶须氧化锌或者所述改性二氧化硅。
44.实施例3
45.本实施例提出一种氟碳涂料,由组分a和组分b按照质量比10:1混合,之后投入高速搅拌机中按照速度600r/min,搅拌25min制得;
46.所述组分a,按照重量份数计算,包括hlr
‑
6树脂15份,hlr
‑
670树脂45份,改性晶须氧化锌8份,改性二氧化硅8份,钼酸锌0.3份,硼酸锌8份,硫酸锌0.4份,basf4401分散剂0.8份,byk354流平剂0.3份,byk1790消泡剂0.2份,溶剂pma10份和溶剂bac 4份;
47.所述组分b由质量比为1:1的bayern3390固化剂和basonat hi
‑
190固化剂组成;
48.所述改性晶须氧化锌或者所述改性二氧化硅由以下步骤制得:
49.按照乙醇和水的体积比11:1配置成混合溶剂,之后按照晶须氧化锌或者二氧化硅与所述混合溶剂的质量比1:32进行混合得到混合溶液,将混合溶液磁力搅拌30min,超声分
散40min;其中所述晶须氧化锌的直径为0.5
‑
5μm,长度为10
‑
50μm;所述二氧化硅的平均粒径为30nm;
50.将超声分散后的所述混合溶液与硅烷偶联剂kh550按照质量比1:12混合,之后通过草酸调节ph值至4.5,之后室温下静置水解1h,之后密封,之后在65℃下磁力搅拌反应120min,之后抽滤混合液,无水乙醇洗涤3次,恒温箱中120℃维持2h烘干,再将产物用研钵研磨,得到所述改性晶须氧化锌或者所述改性二氧化硅。
51.实施例4
52.本实施例提出一种氟碳涂料,由组分a和组分b按照质量比10:0.9混合,之后投入高速搅拌机中按照速度500r/min,搅拌30min制得;
53.所述组分a,按照重量份数计算,包括hlr
‑
6 20份、hlr
‑
670树脂40份,改性晶须氧化锌8份,改性二氧化硅8份,钼酸锌0.5份,硼酸锌8份,硫酸锌0.4份,basf 4401分散剂1.8份,byk354流平剂0.4份、byk1790消泡剂0.5份、溶剂pma 8份,bac 4.4份。
54.所述组分b由质量比为1:1.2的bayern3390固化剂和basonat hi
‑
190固化剂组成。
55.所述改性晶须氧化锌或者所述改性二氧化硅由以下步骤制得:
56.按照乙醇和水的体积比10:1配置成混合溶剂,之后按照晶须氧化锌或者二氧化硅与所述混合溶剂的质量比1:30进行混合得到混合溶液,将混合溶液磁力搅拌20min,超声分散30min;其中所述晶须氧化锌的直径为0.5
‑
5μm,长度为10
‑
50μm;所述二氧化硅的平均粒径为30nm;
57.将超声分散后的所述混合溶液与硅烷偶联剂kh550按照质量比1:13混合,之后通过草酸调节ph值至3.5,之后室温下静置水解1h,之后密封,之后在60℃下磁力搅拌反应120min,之后抽滤混合液,无水乙醇洗涤3次,恒温箱中120℃维持2h烘干,再将产物用研钵研磨,得到所述改性晶须氧化锌或者所述改性二氧化硅。
58.对比例1
59.本对比例的氟碳涂料与实施例3的区别在于没有添加改性氧化锌晶须、改性二氧化硅、硫酸锌、钼酸锌以及硼酸锌,其他制备方法和组分配方均相同。
60.对比例2
61.本对比例的氟碳涂料与实施例3的区别在于没有添加硫酸锌、钼酸锌以及硼酸锌,其他制备方法和组分配方均相同。
62.对比例3
63.本对比例的氟碳涂料与实施例3的区别在于没有添加改性氧化锌晶须、硫酸锌、钼酸锌以及硼酸锌,其他制备方法和组分配方均相同。
64.对比例4
65.本对比例的氟碳涂料与实施例3的区别在于没有添加改性氧化锌晶须,其他制备方法和组分配方均相同。
66.将实施例1
‑
4、对比例1
‑
4的氟碳涂料及市面上购买的氟碳涂料采用刷涂形式涂覆于a3钢表面得到相应的涂层,将涂层进行各项基本性能测试,所得结果见表1和表2。
67.表1实施例1
‑
4的氟碳涂料制得的涂层的性能测试结果
[0068][0069]
从表1可以看出,实施例1
‑
4制得的涂层固含量均大于70%,属于高固体份涂料,并具有较高的硬度,硬度高达5h,还具有较好的耐盐雾性能和耐氢氧化钠性能,耐盐雾性能高达3500h,耐10%氢氧化钠可达30天,同时还具有优异的耐霉菌性能和防火性能。
[0070]
表2对比例1
‑
4及市售的氟碳涂料制得的涂层的性能测试结果
[0071][0072]
从表2可以看出,对比例1
‑
4及市售氟碳涂料制得的涂层耐盐雾性能、耐碱性能和防火性能明显较差,耐霉菌性能等其他性能也较差。
[0073]
本发明通过特有的配方设计,针对现有技术所生产的溶剂型海洋舰船杀菌防腐涂料固体含量偏低,有机排放物量高,防火效果差等缺点,本发明提供了一种用于海洋舰船的高固体份抗菌耐蚀防火氟碳涂层及其制备方法,制备得到的涂层具有固体份比例高(>70%)、力学性能优异、防细菌粘附、耐腐蚀性能优异的特点并兼具防火功能,具有显著的技术优势。
[0074]
以上所述本发明的具体实施方式,并不构成对本发明保护范围的限定。任何根据本发明的技术构思所做出的各种其他相应的改变与变形,均应包含在本发明权利要求的保护范围内。