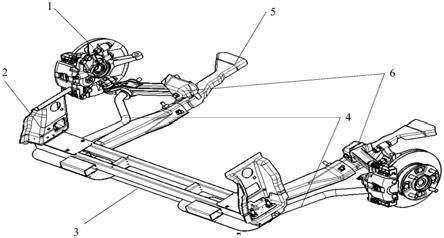
[0001]
本实用新型涉及汽车技术领域,尤其涉及一种新型副车架前横梁结构。
背景技术:[0002]
目前微型乘用车底盘受成本和空间影响,下摆臂和副车架采用传统布置形式比较困难,会造成前舱空间拥挤,各部件之间的间隙偏小。稳定杆也因空间问题,导致外径尺寸受到限制,走向变得复杂,工艺更加复杂。
[0003]
目前汽车底盘前横梁总成仅提供车身侧向刚度,和为冷凝器提供下部固定点。参照图1图2,盒式结构前横梁时先用的结构,其生产需要大量的模具,开发成本高,开发中期遇到问题,设计变更周期长,成本高。
技术实现要素:[0004]
基于背景技术存在的技术问题,本实用新型提出了一种新型副车架前横梁结构。
[0005]
本实用新型提出的一种新型副车架前横梁结构,前横梁总成采用框架结构,其包括:两根横杆、至少一根纵杆、第一加强板和第二加强板;
[0006]
两根横杆相互平行,纵杆连接在两根横杆之间并垂直于横杆设置;
[0007]
第一加强板和第二加强板分别设置在横杆两端,且第一加强板上设有分别用于连接车身和安装稳定杆的第一车身连接结构和第一稳定杆安装结构;第二加强板上设有分别用于连接车身和安装稳定杆的第二车身连接结构和第二稳定杆安装结构。
[0008]
优化的,第一车身连接结构、第一稳定杆安装结构、第二车身连接结构和第二稳定杆安装结构均为通孔结构。
[0009]
优化的,前横梁总成通过安装架与车身连接,第一车身连接结构和第二车身连接结构处分别连接有安装架,安装架与稳定杆位于前横梁总成相对的两侧。
[0010]
优化的,两根横杆均采用方管,第一加强板和第二加强板均贴合横杆设置。
[0011]
优化的,稳定杆远离前横梁总成的一端插入下摆臂。
[0012]
优化的,稳定杆与下摆臂之间填充有衬套,且衬套两端设有垫片。
[0013]
优化的,垫片与稳定杆螺纹连接。
[0014]
优化的,稳定杆端部设有第一凸台和第二凸台,第一凸台与稳定杆本体连接,第二凸台与第一凸台连接,第一凸台和第二凸台与稳定杆本体同轴设置,且稳定杆本体的截面直径、第一凸台的截面直径和第二凸台的截面直径依次减小;衬套套设在第一凸台上,衬套两端的垫片分别位于第一凸台两端的台阶位置。
[0015]
优化的,衬套由沿着第一凸台径向分布的第一部分和第二部分拼接组成。
[0016]
优化的,下摆臂采用两点式安装结构。
[0017]
本实用新型提出的一种新型副车架前横梁结构,将前横梁总成优化为框架结构,并通过加强板进行加强,使得前横梁的结构简单,工艺实现容易,开发、模具、零部件单件成本低。本实用新型中,前横梁总成和下摆臂的实现了轻量化设计,稳定杆的尺寸不受限制,
布置走向简单,工艺实现容易。本实用新型中,稳定杆的设置,不仅可以增加全车的侧倾刚度,同时也承受纵向拉压力,效率更高。
[0018]
本实用新型中,通过加强板将前横梁总成进行加强,稳定杆安装于前横梁总成上,稳定杆两纵臂穿过两点式下摆臂的中间,通过垫片及衬套和两点式下摆臂连接,以此实现制动时通过稳定杆和前横梁总成承受两点式下摆臂所无法承受的纵向力。
附图说明
[0019]
图1为传统盒式前横梁总成结构图;
[0020]
图2为图1的另一角度试图;
[0021]
图3为本实用新型提出的框架式前横梁总成结构图;
[0022]
图4为图3中横杆与纵杆形成的框架结构图;
[0023]
图5为制动时悬架系统受力结构示意图;
[0024]
图6为稳定杆与与下摆臂连接示意图;
[0025]
图7为图5的另一视图。
[0026]
图示:制动器总成1、安装架2、前横梁总成3、第一车身连接结构31、第一稳定杆安装结构32、第一加强板33、横杆34、纵杆35、第二加强板36;
[0027]
稳定杆4、第一凸台41、第二凸台42、车架纵梁5、下摆臂6、衬套7、第一部分71、第二部分72、垫片8。
具体实施方式
[0028]
参照图3,本实用新型提出的一种新型副车架前横梁结构,前横梁总成3采用框架结构,其包括:两根横杆34、至少一根纵杆35、第一加强板33和第二加强板36。
[0029]
两根横杆34相互平行,纵杆35连接在两根横杆34之间并垂直于横杆34设置。如此,横杆34和纵杆35配合形成如图4所示框架结构。
[0030]
第一加强板33和第二加强板36分别设置在横杆34两端,且第一加强板33上设有分别用于连接车身和安装稳定杆的第一车身连接结构31和第一稳定杆安装结构32;第二加强板36上设有分别用于连接车身和安装稳定杆的第二车身连接结构和第二稳定杆安装结构。具体的,第一车身连接结构31、第一稳定杆安装结构32、第二车身连接结构和第二稳定杆安装结构均为通孔结构。
[0031]
参照图5,前横梁总成3通过安装架2与车身连接,第一车身连接结构31和第二车身连接结构处分别连接有安装架2,安装架2与稳定杆4位于前横梁总成3相对的两侧。第一车身连接结构31和第一稳定杆安装结构32均为贯穿第一加强板33和横杆34的通孔,第二车身连接结构和第二稳定杆安装结构均为贯穿第二加强板36和横杆34的通孔,以方便安装架2和稳定杆4的安装。
[0032]
本实施方式中,第一加强板33和第二加强板36通过焊接的方式安装在框架结构上。如此,方便了通孔结构与螺栓连接的强度,保证了加强板的安装稳定,有利于防止在高制动减速度时发生撕裂失效。具体的,本实施方式中,两根横杆34均采用方管,第一加强板33和第二加强板36均贴合横杆34设置,以增大加强板与横杆的接触面积,提高稳定性。具体的,纵杆35为与横杆34相同规格的方管。横杆34和纵杆35可采用焊接方式连接。
[0033]
参照图6,图7,本实施方式中,稳定杆4远离前横梁总成3的一端插入下摆臂6。稳定杆4与下摆臂6之间填充有衬套7,且衬套7两端设有垫片8。如此,衬套7避免了稳定杆4与下摆臂6之间的磨损,垫片8有利于稳定杆4与下摆臂6之间相对位置的稳定,避免滑动。
[0034]
具体的,本实施方式中,稳定杆4端部设有第一凸台41和第二凸台42,第一凸台41与稳定杆4本体连接,第二凸台42与第一凸台41连接,第一凸台41和第二凸台42与稳定杆4本体同轴设置,且稳定杆4本体的截面直径、第一凸台41的截面直径和第二凸台42的截面直径依次减小;衬套7套设在第一凸台41上,衬套7两端的垫片8分别位于第一凸台41两端的台阶位置。
[0035]
如此,通过第一凸台41与垫片8配合,限制了衬套7在第一凸台41上的移动自由度。具体的,本实施方式中,衬套7由沿着第一凸台41径向分布的第一部分71和第二部分72拼接组成。衬套7的拼接设置,可以使车轮在受到冲击载荷时,缓冲路面传递到稳定杆4处的振动,同时也可以防止稳定杆4端部受到的过大的截面方向力导致端部剪切失效。本实施方式中,垫片8与稳定杆4螺纹连接。具体还可设置成,衬套7一端的垫片8位于稳定杆4本体与第一凸台41之间通过台阶限位,衬套7另一端的垫片8通过螺母安装在第二凸台42上。两个垫片8的设置,保证了稳定杆和下摆臂在运动的过程中衬套不会脱出。
[0036]
本实施方式中,下摆臂6采用两点式安装结构。如此,通过加强板将前横梁总成进行加强,稳定杆安装于前横梁总成上,稳定杆两纵臂穿过两点式下摆臂的中间,通过垫片及衬套和两点式下摆臂连接,以此实现制动时通过稳定杆和前横梁总成承受两点式下摆臂所无法承受的纵向力。
[0037]
以上所述,仅为本实用新型涉及的较佳的具体实施方式,但本实用新型的保护范围并不局限于此,任何熟悉本技术领域的技术人员在本实用新型揭露的技术范围内,根据本实用新型的技术方案及其实用新型构思加以等同替换或改变,都应涵盖在本实用新型的保护范围之内。