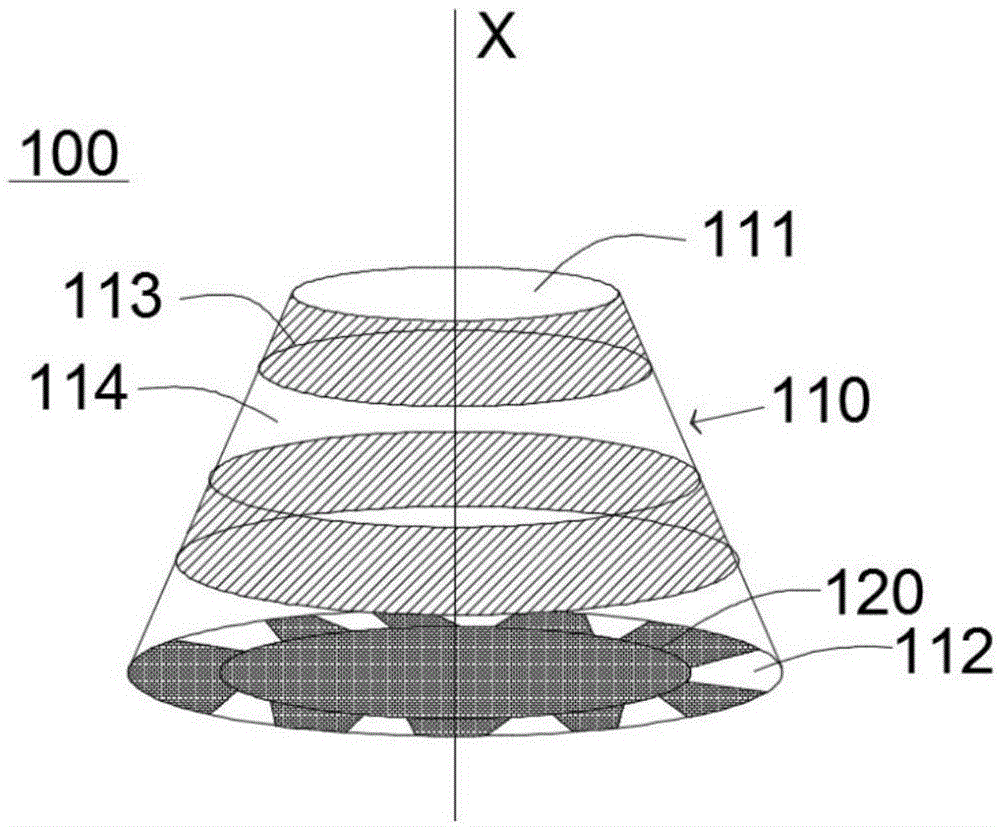
本发明涉及一种挤出机用混炼构件,特别地,涉及一种无螺杆挤出机混炼构件。
背景技术:
:随着高分子材料的发展,合成出一种新型高分子材料越来越困难。因此目前高分子材料的主要研究方向是对已知高分子材料进行各种改性,而目前最常用的改性手段是共混改性。共混改性是指将两种或两种以上的高分子材料一同混炼,通过加入不同的改性剂以及原料之间不同的比例来制备出具有一定特定性质的新型复合高分子材料。而制备这种高分子复合材料所用到的最常用的设备就是挤出机。挤出机通常是将两种或两种以上的物质通过混炼以达到均匀混合或相对均匀混合的目的。常用的挤出机通常有单螺杆挤出机、双螺杆挤出机以及多螺杆挤出机等。挤出机的螺杆通常有着传输和混炼的双重作用,通过螺杆的转动,可以向前输送物质,不仅如此还可以对挤出机套筒中的熔融组分形成一定的剪切搅拌作用,已达到混炼均匀的目的。但是由于螺杆的存在,螺杆之间的磨损以及螺杆与套筒之间的磨损是不可避免的,因此此类挤出机通常在使用一段时间后需要进行对螺杆的保养过程。这一过程通常需要拆卸螺杆。拆卸过程将耗费大量时间成本。不仅如此,螺杆的制造材料和制造工艺也相当复杂,因此这将增大螺杆型挤出机的制造成本。技术实现要素:为了克服上述现有技术中的不足之处,本发明的目的在于提供一种无螺杆混炼构件以及包括该混炼构件的挤出机。根据本发明的一方面,提供一种具有不同粘附力的高分子混炼构件,所述高分子混炼构件包括:主体,具有圆台形状的内腔,主体在主体的圆台的横截面积最小的第一端部处具有作为进料口的敞开的第一开口并且在主体的圆台的横截面积最大的第二端部处具有敞开的第二开口;以及挡板,在第二开口处位于内腔中,并且与主体的内表面以等间距间隔开,以作为出料口,其中,主体具有在与圆台的轴方向垂直的方向上交替布置在主体的内表面上的极性区和非极性区。根据本发明的示例实施例,第一端部处的圆台的横截面与第二端部处的圆台的横截面的直径比可以为1:2.5-1:10。根据本发明的示例实施例,第一端部处的圆台的横截面的直径与从第一端部到第二端部的最小距离的比可以为1:10-1:15。根据本发明的示例实施例,极性区可以包括羟基,非极性区可以包括不小于10个碳的长直链烷烃。根据本发明的示例实施例,极性区和非极性区在圆台的轴方向上的宽度可以相同。根据本发明的示例实施例,主体可以包括铁和铝中的一种。根据本发明的另一方面,提供一种挤出机,所述挤出机包括:如上所述的高分子混炼构件;装料部,用于将物料加入到高分子混炼构件;以及出料部,用于成型地排出高分子混炼构件中的物料,其中,高分子混炼构件可转动地与装料部和出料部连接。根据本发明的示例实施例,所述装料部可以包括与混炼构件的进料口连通的加热圆筒以及位于加热圆筒内部的输料螺杆。根据本发明的示例实施例,所述出料部可以与混炼构件的出料口连通。根据本发明的又一方面,提供一种挤出高分子的方法,所述方法包括:将物料加入到混炼构件内;以及使混炼构件转动,以使物料混合,其中,混炼构件包括:主体,具有圆台形状的内腔,主体在主体的圆台的横截面积最小的第一端部处具有作为进料口的敞开的第一开口并且在主体的圆台的横截面积最大的第二端部处具有敞开的第二开口;以及挡板,在第二开口处位于内腔中,并且与主体的内表面以等间距间隔开,以作为出料口,其中,主体具有在与圆台的轴方向垂直的方向上交替布置在主体的内表面上的极性区和非极性区。根据本发明的示例实施例,第一端部处的圆台的横截面与第二端部处的圆台的横截面的直径比可以为1:2.5-1:10。根据本发明的示例实施例,第一端部处的圆台的横截面的直径与从第一端部到第二端部的最小距离的比可以为1:10-1:15。根据本发明的示例实施例,极性区可以包括羟基,非极性区可以包括不小于10个碳的长直链烷烃。根据本发明的示例实施例,极性区和非极性区在圆台的轴方向上的宽度可以相同。根据本发明的示例实施例,在将物料加入到混炼构件内中,可以通过装料部将物料加入到混炼构件内。根据本发明的示例实施例,所述装料部可以包括与混炼构件的进料口连通的加热圆筒以及位于加热圆筒上部,用于加料的加料口和位于加热圆筒内部的输料螺杆。根据本发明的示例实施例,可以以式1的角速度来使混炼构件绕圆台的轴转动,式1:其中,在式1中,ω表示混炼构件转动的角速度,g表示重力加速度,d表示第一端部处的圆台的横截面的直径。根据本发明的示例实施例,所述方法还可以包括:成型地排出混炼构件中的物料。根据本发明的示例实施例,可以通过排出部成型地排出混炼构件中的物料。根据本发明的示例实施例,主体可以包括铁和铝中的一种。根据本发明的具有不同粘附力的高分子混炼构件和包括其的挤出机具有如下技术效果中的至少一个:1)本发明用具有极性区和非极性区的混炼构件代替现有的挤出机中的螺杆构造,从而避免了对螺杆的更换与保养,降低了时间成本;2)本发明的混炼构件的结构简单,降低了制造成本;3)本发明提出的新的挤出机用混炼构件为该领域提供新的思路。附图说明为了更清楚地说明本发明实施例或现有技术中的技术方案,下面将对实施例或现有技术描述中所需要使用的附图作简单地介绍。图1是示出了根据本发明的示例实施例的高分子混炼构件的透视图;图2是示出了图1中示出的高分子混炼构件的主体的展开的图;图3是示出了根据本发明的示例实施例的挤出机的平面示意图。具体实施方式对所公开的实施例的上述说明,使本领域专业技术人员能够实现或使用本发明。对这些实施例的多种修改对本领域的专业技术人员来说将是显而易见的,本文中所定义的一般原理可以在不脱离本发明的精神或范围的情况下,在其它实施例中实现。因此,本发明将不会被限制于本文所示的这些实施例,而是要符合与本文所公开的原理和新颖特点相一致的最宽的范围。在下文中将参照图1和图2来详细描述根据本发明的示例实施例的高分子混炼构件。图1是示出了根据本发明的示例实施例的高分子混炼构件的透视图。图2是示出了图1中示出的高分子混炼构件的主体的展开的图。参照图1和图2,具有不同粘附力的高分子混炼构件100可以包括主体110和挡板120。主体110可以具有圆台形形状的中空内腔,并且主体110的上端部和下端部可以是敞开的,具体地,主体110在主体110的圆台的横截面积最小的第一端部处具有敞开的第一开口111,其可以作为高分子混炼构件100的进料口;主体110在主体110的圆台的横截面积最大的第二端部处具有敞开的第二开口112,其可以作为高分子混炼构件100的出料口。也就是说,主体110可以是由板体围成的且上下端部是敞开的一体结构的形式。在本发明的示例实施例中,主体110可以由铁或铝形成,从结构强度的角度选择,优选铁作为主体110的材质;然而,本发明不限于此。此外,主体110还可以具有在与圆台的轴方向x垂直的方向上交替地布置在主体110的内表面上的极性区113和非极性区114。此外,极性区113和非极性区114在圆台的轴方向上的宽度可以相同。这里,圆台的轴方向x可以指圆台的高度方向。在主体110的内表面上沿与圆台的轴方向x垂直的方向交替布置有极性区113与非极性区114,其主要的工作原理在于:主体110在转动的情况下,当熔融态的非极性高分子(例如,聚丙烯)在经由主体110的内腔流经非极性区114时,由于两者极性相同,因此对非极性高分子具有较高的粘附力,此时非极性高分子与主体110的内表面上的非极性区114接触的界面处流速较低,非极性高分子的内部速度梯度分布较大;当非极性高分子流经极性区113时,对非极性高分子所受粘附力较低,界面流速较快,对非极性高分子的内部速度梯度影响较低,因此,当非极性高分子周期性地流经交替布置在主体110的内表面上的极性区113和非极性区114后,主体110内部的速度梯度发生周期性变化,这种变化可以有效地提高混炼效率。这里,由于熔融态的极性高分子流经主体110的内部的工作原理与熔融态的非极性高分子流经主体110的内部的工作原理基本相同,因此将不对其进行赘述。在传统的挤出机中,通常使用螺杆进行混炼,这势必会额外地增加对螺杆的维护和更换的工艺,从而现有的挤出机的工作效率相对较低。然而,在本发明中,在主体110的内表面上沿与圆台的轴方向x垂直的方向交替布置极性区113与非极性区114来代替现有的挤出机中的螺杆能够在保证混炼效果的同时提高工作效率。高分子混炼构件100的主体110对于高分子的混炼效果的影响主要存在三个影响因素,分别包括:第一端部处的圆台的横截面(即,第一开口111)与第二端部处的圆台的横截面(即,第二开口112)的直径比、第一端部处的圆台的横截面的直径与从第一端部到第二端部的最小距离(也即,圆台的高度)的比以及高分子混炼构件100的极性区113和非极性区114的数量。通过试验可知,当第一端部处的圆台的横截面与第二端部处的圆台的横截面的直径比过大,特别是大于1:2.5时,主体的圆台趋向变为圆柱体,这会不利于物料在高分子混炼构件100中从第一端部(即,进料口)向第二端部(即,出料口)的移动;同样地,当第一端部处的圆台的横截面与第二端部处的圆台的横截面的直径比减小,特别是小于1:10时,主体的圆台趋向变为圆锥体,这会使高分子混炼构件100需要高速转动才能将内部的熔融物料从第一端部输送到第二端部,这种情况不仅会增加能耗,而且还会增大高分子混炼构件的磨损。因此,在本发明的示例实施例中,第一端部处的圆台的横截面与第二端部处的圆台的横截面的直径比可以为1:2.5-1:10,优选地,可以为1:3.5-1:9、1:4.5-1:8、1:5.5-1:7、1:4-1:7、1:5-1:9或1:6-1:8。同样地,通过试验可知,当第一端部处的圆台的横截面的直径与从第一端部到第二端部的最小距离(也即,圆台的高度)的比过大,特别是大于1:10时,主体110的圆台高度过低,使得物料在主体110内部的混炼时间较短,混炼效果不佳;当第一端部处的圆台的横截面的直径与从第一端部到第二端部的最小距离的比过小,特别是大于1:15时,主体110的圆台高度过大,物料在主体110内部的混炼时间较长,容易引起物料在高分子混炼构件100内大量堆积,同样不利于混炼效果。因此,在本发明的示例实施例中,第一端部处的圆台的横截面的直径与从第一端部到第二端部的最小距离的比可以为1:10-1:15,优选地,1:9.5-1:14.5、1:9-1:14、1:8.5-1:13.5、1:8-1:13、1:7.5-1:12.5、1:8-1:12、1:8.5-1:11.5、1:9-1:11、1:12-1:14或1:11-1:13。同样地,高分子混炼构件100的极性区113和非极性区114的数量过多,将增大高分子混炼构件的制造难度,而且由于主体110的内表面上的极性区113和非极性区114间隔较小,不利于内部流速的传输,使得混炼效果变差;如果高分子混炼构件100的极性区113和非极性区114的数量过少,主体110内部的速度梯度变化周期变长,同样也会降低混炼效果。通常极性区113或非极性区114的数量为从第一端部到第二端部的最小距离的五分之一,记为:n=l/5,其中,n为极性区113或非极性区114的数量,l为从第一端部到第二端部的最小距离。此外,在本发明的非限制性示例实施例中,极性区113与非极性区114的数量可以基本相同。在本发明的示例实施例中,主体110的内表面上的极性区113可以包括羟基,主体110的内表面上的非极性区114可以包括不小于10个碳的长直链烷烃。在本发明中,主体110的内表面上的极性区113和非极性区114可以是通过对主体110的内表面进行化学修饰而得到。下面将详细地描述对主体110的内表面进行化学修饰以得到极性区113和非极性区114的方法。首先,可以使用例如ph为2的盐酸或硫酸的强酸除去主体110的内金属表面上的氧化膜,并用清水冲洗至ph值为中性。接着,用丙酮清洗除去了氧化膜的金属表面,以除去金属表面可能残存的油脂,并用清水冲洗干净,并晾干。然后,可以在主体110的内金属表面的预定区域上以每平方米15g-20g的不小于10个碳的长直链烷烃类化合物的量来涂覆不小于10个碳的长直链烷烃类化合物,随后晾干,该被涂覆的预定区域即为非极性区114,而未涂覆不小于10个碳的长直链烷烃类化合物的区域即为极性区113,由于金属表面经过处理后可以带有羟基,因此极性区113的极性基团为羟基。在本发明的示例实施例中,不小于10个碳的长直链烷烃类化合物可以是不小于10个碳的长直链烷烃的三甲基硅氧烷,诸如正十二烷基三甲氧基硅烷或正十六烷基三甲氧基硅烷等;然而,本发明不限于此。挡板120可以在主体110的第二端部处位于主体110的内腔中,并且与主体110的内表面以等间距间隔开,从而作为出料口。挡板120可以具有圆形的板构造,当设置在主体110的第二端部处时,挡板120可以与圆台的第二端部处的横截面是同心圆。此外,挡板120可以通过支架经由例如焊接等固定在主体110的第二端部处的内表面上。然而,本发明不限于此,例如,可以通过任何合适的方法将挡板120固定在主体110的第二端部处的内表面上。下面将以示例和对比示例来详细说明本发明的示例实施例的高分子混炼构件100的制造方法以及评价标准。[制造示例]示例1用ph为2的盐酸的强酸除去主体110的内金属表面上的氧化膜,并用清水冲洗至ph值为中性;接着,用丙酮清洗除去了氧化膜的金属表面,以除去金属表面可能残存的油脂,并用清水冲洗干净,并晾干;然后,可以在主体110的内金属表面的预定区域上以每平方米15g正十二烷基三甲氧基硅烷的量来涂覆正十二烷基三甲氧基硅烷,随后晾干,该被涂覆的预定区域即为非极性区114,而未涂覆正十二烷基三甲氧基硅烷的区域即为极性区。其中,第一端部处的圆台的横截面的直径d1=10cm,第二端部处的圆台的横截面的直径d2=50cm,第一端部到第二端部的最小距离为l=100cm。示例2除了第二端部处的圆台的横截面的直径d=80cm,第一端部到第二端部的最小距离为l=120cm之外,以与示例1的方法相同的方法来制造高分子混炼构件。示例3除了第二端部处的圆台的横截面的直径d=25cm,第一端部到第二端部的最小距离为l=150cm之外,以与示例1的方法相同的方法来制造高分子混炼构件。示例4除了第二端部处的圆台的横截面的直径d=100cm,第一端部到第二端部的最小距离为l=130cm之外,以与示例1的方法相同的方法来制造高分子混炼构件。对比示例1除了第二端部处的圆台的横截面的直径d=13cm之外,以与示例1的方法相同的方法来制造高分子混炼构件。对比示例2除了第二端部处的圆台的横截面的直径d=140cm之外,以与示例1的方法相同的方法来制造高分子混炼构件。对比示例3除了第一端部到第二端部的最小距离为l=25cm之外,以与示例1的方法相同的方法来制造高分子混炼构件。对比示例4除了第一端部到第二端部的最小距离为l=190cm之外,以与示例1的方法相同的方法来制造高分子混炼构件。[评价示例]通常情况下,可以通过dsc测定共混物tg的数量来评价两种高分子物料的共混效果,也即,当将两种高分子物料共混时,若检测到一个tg值,则说明共混效果较好;反之,若检测到两个tg值,则说明共混效果较差。应用这一简易的判断标准可以评价混炼设备的混炼效果。示例1的评价将质量比为85:15的熔融态的聚丙烯(pp)与低密度聚乙烯(ldpe)加入到示例1的混炼构件100中,然而在200℃下进行混炼,混炼后通过dsc进行测定。测定结果示出在下面的表1中。示例2至示例4以及对比示例1至对比示例4的评价以与评价示例1的方式相同的方式来评价示例2至示例4以及对比示例1至对比示例4。测定结果示出在下面的表1中。表1d1(cm)d2(cm)l(cm)dsc测定值示例110501001示例210801201示例310251501示例4101001301对比示例110131002对比示例2101401002对比示例31050252对比示例410501902从示例1和示例2以及对比示例1和对比示例2可以看出,第一端部处的圆台的横截面的直径d1与第二端部处的圆台的横截面的直径d2的比不在1:2.5-1:10的范围内时,共混效果较差。从示例3和示例4以及对比示例3和对比示例4可以看出,当第一端部处的圆台的横截面的直径d1与第二端部处的圆台的横截面的直径d2的比或是第一端部处的圆台的横截面的直径与从第一端部到第二端部的最小距离的比不在最优范围内,共混效果都会变差。在下文中将参照图3详细地描述根据本发明的示例实施例的包括上述高分子混炼构件100的挤出机。图3是示出了根据本发明的示例实施例的挤出机的平面示意图。参照图3,根据本发明的示例实施例的挤出机10可以包括如上所述的高分子混炼构件100、装料部200和出料部300。这里提及的高分子混炼构件100与上面描述的高分子混炼构件基本相同,因此将不再进行赘述。装料部200可以是用于将待混炼的物料加入到高分子混炼构件100中的装置。例如,装料部200可以包括与高分子混炼构件100的第一端部(即,进料口)连通的加热圆筒220以及位于加热圆筒220上部,用于加料的加料口210和位于加热圆筒210内部的输料螺杆230。然而,本发明不限于此,装料部200可以包括任何合适的部件,只有各部件装配后的装料部200能够使待混炼的物料熔融且将熔融的待混炼的物料输送到高分子混炼构件100的内腔中即可。出料部300可以是用于成型地排出高分子混炼构件100中的熔融的物料的装置。出料部300可以与高分子混炼构件100的出料口连通,以接收熔融的物料,从而将熔融的物料成型地排出,以完成物料的混炼。在本发明的非限制性实施例中,出料部300可以包括现有的挤出机中包含的任何适合的部件,例如传送部件、冷却部件和切割部件等。在此将不对其进行详细赘述。下面将详细描述根据本发明的示例实施例的挤出机10的挤出高分子的方法。根据本发明的挤出高分子的方法包括将物料加入到混炼构件内以及使混炼构件转动以使物料混合。在物料加入到混炼构件内的步骤中,可以通过如上所述的装料部200将待混炼的物料熔融,然后通过输料螺杆230传送至到混炼构件内。这里的混炼构件与如上所述的高分子混炼构件100的构造基本相同,因此将不再进行赘述。在使混炼构件转动的步骤中,可以以下面的式1的速度(例如,角速度)来使混炼构件绕圆台的轴转动。式1:在式1中,ω表示混炼构件转动的角速度,g表示重力加速度,d表示第一端部处的圆台的横截面的直径。此外,根据本发明的示例实施例的挤出高分子的方法还可以包括成型地排出混炼构件中的物料。可以通过如上所述的出料部来成型地排出混炼构件中的物料。综上所述,根据本发明的示例实施例的高分子混炼构件100能够代替现有的挤出机中的螺杆构造,从而避免了对螺杆的更换与保养,降低了时间成本。此外,本发明的混炼构件的结构简单,降低了制造成本。而且本发明的高分子混炼构件100的混炼效果能够达到螺杆型挤出机的混炼效果。当前第1页12