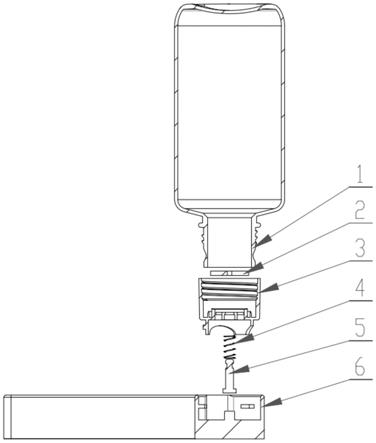
一种光固化3d打印机的自动进料装置
技术领域
[0001]
本发明涉及3d打印领域,尤其涉及的是一种光固化3d打印机的自动进料装置。
背景技术:[0002]
现有技术中,现在市场上常规光固化3d打印机由料槽、构建平台、z轴机构、led光源模块和控制部分组成。打印过程需要将光敏树脂倒入料槽中开始,以便在构建平台和底部之间形成一层树脂。构建平台放置到位后,led发出的uv光线在屏幕的作用下透过料槽,以固化树脂。在这个运行过程中,随着料槽内树脂的消耗,需要人们定时手动添加树脂,以保持料槽中的树脂始终稳定在一个液面高度上,以避免打印过程中出现无料、少料而造成的打印失败,操作非常繁琐,体验较差。
[0003]
同时,目前市场上采用的自动进料,基本上是通过气泵的作用来达到自动进料的目的,这样的缺点是:需要额外的电力成本,造成成本比较高。
[0004]
因此,现有技术存在缺陷,需要改进。
技术实现要素:[0005]
本发明所要解决的技术问题是:提供一种结构简单、无需电机驱动、自动补充树脂材料、节省人力资源的光固化3d打印机的自动进料装置。
[0006]
本发明的技术方案如下:一种光固化3d打印机的自动进料装置,包括料瓶、瓶盖、密封圈、阀杆、伸缩件以及底座,所述瓶盖设置有流道,所述瓶盖套设在料瓶底部,所述流道与料瓶内部连通,所述伸缩件位于阀杆上,所述阀杆顶部与密封圈连接,所述密封圈位于流道上方,所述伸缩件顶部与瓶盖连接;
[0007]
所述底座包括料槽和插槽,所述料槽与插槽之间设置有通槽,所述插槽中设置有凸台,所述阀杆底部位于凸台上方,所述瓶盖位于插槽中,所述流道与插槽连通。
[0008]
采用上述各个技术方案,所述的光固化3d打印机的自动进料装置中,所述瓶盖的底端设置有若干个侧开口,各所述侧开口与流道连通,任一所述侧开口朝向通槽。
[0009]
采用上述各个技术方案,所述的光固化3d打印机的自动进料装置中,所述侧开口的数量为4个,各所述侧开口的大小和高度彼此不同。
[0010]
采用上述各个技术方案,所述的光固化3d打印机的自动进料装置中,所述伸缩件为弹簧,所述弹簧套在阀杆上,所述弹簧底部与阀杆底部连接,所述弹簧顶部与瓶盖连接。
[0011]
采用上述各个技术方案,所述的光固化3d打印机的自动进料装置中,所述料瓶设置有外螺纹,所述瓶盖设置有内螺纹,所述瓶盖与料瓶螺纹连接。
[0012]
采用上述各个技术方案,所述的光固化3d打印机的自动进料装置中,所述料瓶、瓶盖以及阀杆都采用抗腐蚀的塑料或金属制成。
[0013]
采用上述各个技术方案,所述的光固化3d打印机的自动进料装置中,所述弹簧采用不锈钢制成。
[0014]
采用上述各个技术方案,所述的光固化3d打印机的自动进料装置中,所述密封圈
采用硅胶制成。
[0015]
采用上述各个技术方案,本发明有利于环保的定量自动进料,可根据需求流速、液面高度设定瓶盖尺寸大小,瓶盖与插槽的连接处设置有旋转卡合结构,便于快速固定与拆卸,空间利用率高,无需专门定制机台,结构简单,制造成本低,不必电力等能源且清理简单,无需人员操作管理,可应用在各式不同的机台上。
附图说明
[0016]
图1为本发明的爆炸结构示意图;
[0017]
图2为本发明的封液示意图;
[0018]
图3为本发明的通液示意图;
[0019]
图4为本发明的整体立体图。
具体实施方式
[0020]
以下结合附图和具体实施例,对本发明进行详细说明。
[0021]
如图1~4,本实施例提供了一种光固化3d打印机的自动进料装置,包括料瓶1、瓶盖3、密封圈2、阀杆5、伸缩件以及底座6,料瓶1中装打印所需要的树脂材料,瓶盖3设置有流道8,瓶盖3套设在料瓶1底部,流道8与料瓶1内部连通,可以使料瓶1中的树脂材料从瓶盖3的流道8流出。伸缩件位于阀杆5上,为了简化结构,伸缩件采用弹簧4,弹簧4套在阀杆5上。阀杆5顶部与密封圈2连接,密封圈2位于流道8上方,弹簧4顶部与瓶盖3连接,弹簧4底部则与阀杆5底部连接。
[0022]
底座6则包括料槽15和插槽13,料槽15与插槽13之间设置有通槽14,料瓶1中流出的树脂材料经过插槽13、通槽14到达料槽15中,以便于进行3d打印。插槽13中设置有凸台9,阀杆5底部位于凸台9上。如图2,正常状态下,弹簧4将阀杆5往下顶,密封圈2下移,密封圈2将流道8上方堵死,使料瓶1中的树脂材料不能流出。如图3,当阀杆5下压时,弹簧4被压缩,阀杆5往上将密封圈2顶开,瓶盖3的液封面11被打开,使料瓶1中的树脂材料往下流。瓶盖3位于插槽中,流道8与插槽13连通,从而使树脂材料进入料槽15。
[0023]
如图2和图4,瓶盖3的底端设置有若干个侧开口12,各所述侧开口12与流道12连通,任一所述侧开口12朝向通槽14。侧开口12的数量为4个最佳,同时将各所述侧开口12的大小和高度设置的彼此不同。因此,通过转动料瓶1,使不同大小和高度的侧开口12对准通槽14,进而能够控制树脂材料的流速和高度,结构非常简单,容易操作。
[0024]
为了便于快速更换瓶盖3,在料瓶1设置有外螺纹,在瓶盖3设置有内螺纹,瓶盖3与料瓶1螺纹连接,实现快速拆卸装配。同时,瓶盖3的外侧设置l型卡槽7,而插槽13的内侧壁则设置与l型卡槽7适配的环形连接凸块10,通过将瓶盖3下压旋转,将瓶盖3快速固定在插槽13中,拆卸与固定相反,同样可快速拆卸。
[0025]
为了避免在液体长期浸泡的过程中被腐蚀掉,料瓶1、瓶盖3以及阀杆5都采用抗腐蚀的塑料或金属制成,比如塑料采用聚丙烯树脂,金属采用不锈钢,弹簧4也采用不锈钢制成。为了提高密封圈2的密封性能,密封圈2则采用硅胶制成。
[0026]
实施原理过程如下:在使用之前,需要将装满树脂材料的料瓶1与瓶盖3扭紧,此时,在弹簧4的自然伸展力推力下,阀杆5带动密封圈2与瓶盖3的流道12边缘的液封面11贴
合,流道12闭合,液体被密封在料瓶1内无法流出。使用时,需要将瓶盖3朝下,顺着底座6的插槽13用力按下,此时,插槽13中间的凸台9将阀杆5向上顶起,弹簧4收缩,密封圈2随之升起,流道12打开,树脂材料由图示箭头方向流出,最终当液面漫过瓶盖3侧边开口时,树脂材料停止流出,并在树脂材料的消耗过程中,液面下降到瓶盖3的侧开口12以下,树脂材料再次流出,最终使液面保持在一个稳定高度范围内。
[0027]
上述原理利用的是大气压强平衡原理,不需要额外的气动或电动结构,极大的节省成本。瓶盖3底部压强与料槽15液面高度压强相等,瓶内的气体压强加上瓶内到瓶盖3底部光敏树脂的液面压强等于一个大气压(料槽15液面的大气压强)。因此只要液面低于瓶盖3的侧开口12,大气压就会向瓶内补充气体,瓶内气体压强增大,重力就会让瓶中液体向料槽15补充,液面重新高于瓶盖3的侧开口12,压强最终重新达到平衡,液体停止流出。这个过程重复发生使液面始终保持在一个液面高度。
[0028]
采用上述各个技术方案,本发明根据大气压强平衡原理,有利于环保的定量自动进料,可根据需求流速、液面高度设定瓶盖尺寸大小,瓶盖与插槽的连接处设置有旋转卡合结构,便于快速固定与拆卸,空间利用率高,无需专门定制机台,结构简单,制造成本低,不必电力等能源且清理简单,无需人员操作管理,可应用在各式不同的机台上。
[0029]
以上仅为本发明的较佳实施例而已,并不用于限制本发明,凡在本发明的精神和原则之内所作的任何修改、等同替换和改进等,均应包含在本发明的保护范围之内。