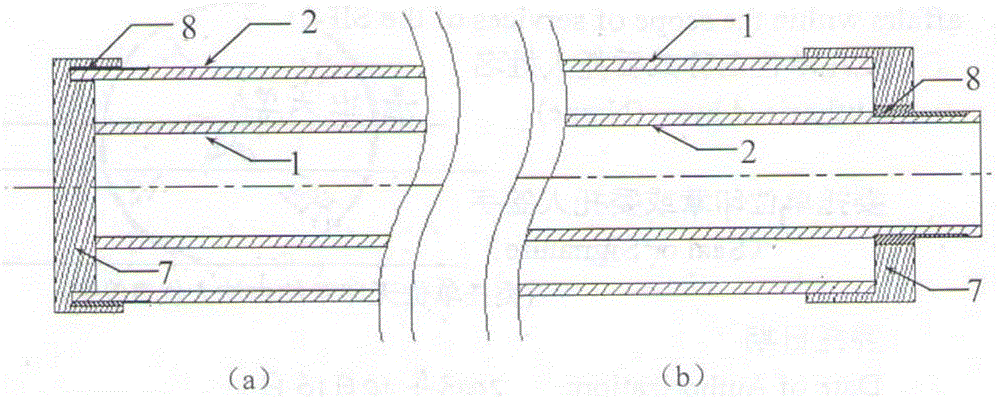
本发明属于强化传热技术领域,特别涉及一种具有固定汽化核心多孔壁面的换热管及其制备方法。
背景技术:世界能源紧张问题日益突出,以节约能源与减少材料消耗为主要目的的,开发高效紧凑式换热器是传热界的重要研究课题。蒸发器广泛应用于制冷空调领域、ORC(中文)循环领域、以及能源存储等领域,其换热结果直接影响整个机组的换热性能。因此,沸腾传热强化技术在强化传热领域中占有非常重要的地位。在制冷空调、ORC循环等领域,蒸发器常常采用卧式管壳式结构,无论是水平管内沸腾还是管外沸腾,其沸腾过程形成的汽体往往使得真实的沸腾换热面显著减小。水平管内沸腾过程随着沸腾进行,由于存在气液密度差,几乎上半个水平管的换热面积均被汽相所覆盖,不仅造成换热面积骤然下降,同时增大了换热管干烧、烧毁的危险。同样,水平管外沸腾过程中,沸腾管底部较长时间的被气泡覆盖,形成较大气膜热阻,长期局部过热,很容易造成设备的老化与损坏。多孔金属结构具有大量的微细毛孔结构,能使液体在微结构内部毛细泵里的作用下进行快速铺展;同时多孔金属结构应用于沸腾过程,具有密集的汽化核心。事实上,多孔表面换热管由于沸腾温差低、换热系数高、临界热流密度高和康够能力强等优势,早就受到广泛关注。自从20世纪70年代初美国联合碳化公司开发出烧结型多孔表面管后,此种多孔换热管就得到了长足的发展。最受青睐的当属烧结性表面多孔管,其传热系数可比普通光管传热系数至少提高10倍,而且其有效温差仅为普通光管的1/7‐1/8,普通光管经烧结制成多孔表面管后可以有效提高光管的扛结垢性能。因此将多孔换热管应用于水平沸腾传热过程中,不仅可以利用毛细结构输运液体到干壁区,壁面干烧导致的毁坏,同时具有较高密度的汽化核心,也显著提高了其传热性能。事实上,多孔结构表面密集的核化中心,还会引起相邻多个汽化核心气泡之间具有相互作用,气泡之间的相互抑制或融合,气泡被抑制延长气泡脱离时间或在传热表面形成一空气热阻层,都会恶化其传热性能。多孔亲水性表面可将沸腾临界热通量提高至原来的1.5‐1.6倍,而疏水的多孔金属反而大大降低了沸腾临界热流密度,其根部原因就是汽化核心处过于密集,致使在多孔结构内部形成了类似于膜沸腾的气泡层。综上所述,针对出镜率较高的卧式沸腾换热管,利用表面烧结毛细结构结合人为控制其核化中心,即可有效提高其传热性能的同时避免其干烧、提高其安全系数。本发明提出一种具有固定汽化核心的多孔壁面换热管,其是利用精确加工的烧结模板结合金属微纳颗粒,在普通换热管内外烧结而成的具有固定沸腾汽化核心的多孔壁面换热管,其多孔结构能够有效控制汽化核心的同时,可避免水平管内形成大面积气膜以致干烧的现象。
技术实现要素:本发明的目的在于提出一种具有固定汽化核心的多孔壁面换热管及其制备方法,其特征在于,所述具有固定汽化核心的多孔壁面换热管由普通换热管、多孔结构壁面层以及固定的汽化核心空穴依次结合构成;在换热过程中,多孔壁面换热管中的多孔结构壁面层利用其结构的毛细力,吸引液体至汽相聚集的干烧壁面区,避免换热管的干烧。同时多孔壁面换热管中的汽化核心空穴成为沸腾传热过程中的定位核化中心。一种具有固定汽化核心的多孔壁面换热管的制备方法,其特征在于,利用汽化核心模板管和金属微纳颗粒与普通换热管共烧制得;具体步骤为首先根据普通换热管直径加工汽化核心模板管,设计在汽化核心模板管壁面上汽化核心的分布和尺寸;其次筛选导热性能良好的金属颗粒,并对普通换热管进行表面处理,在汽化核心模板管的汽化核心面上涂覆脱模剂氧化聚乙烯蜡,然后将汽化核心模板管与普通换热管利用封头固定压紧,将汽化核心模板管和金属颗粒一起在惰性气体保护下烧结成型;其烧结温度根据不同金属颗粒的尺寸和材料性质而定。其烧结温度无须达到金属熔融温度,只要金属颗粒熔接即可。烧结时间一般为1‐5h,烧结完毕后,在惰性气体保护下自然冷却,然后脱模获得具有固定汽化核心的多孔壁面换热管;此多孔壁面换热管具有金属烧结的多孔毛细结构,利用毛细力引导液体在壁面流动,吸引液体至汽相聚集的干烧壁面区,避免换热管的干烧;同时多孔壁面换热管中的汽化核心空穴成为沸腾传热过程中的定位核化中心,避免多孔结构汽化核心密度过大引起气泡合并形成气膜热阻的现象。所述加工汽化核心的模板管,其截面形状与普通换热管一致,截面大小根据管外沸腾换热还是管内沸腾换热而定;长度比普通换热管略长;壁面分布有汽化核心突起,用于烧结制备多孔结构中的汽化核心空穴,所述模板管壁面上的汽化核心突起,利用激光溅射或刻蚀进行精密加工;针对不同沸腾工质、传热量与传热面积,对汽化核心空穴尺寸根据下式计算:其中Ropt为最佳汽化核心空穴半径;σ为沸腾液体的表面张力;λl为液体的导热系数;β为光滑金属基体与沸腾液体之间的接触角;Q为传递热量;A为利用系数法估计的多孔结构换热面积;对于工质为水的沸腾过程其最佳微柱结构尺寸在10‐30微米,与水蒸气沸腾气泡尺寸相当。所述汽化核心突起材质为耐高温的金属或陶瓷材料。所述汽化核心突起形状为规则或不规则的球形、微柱、圆台或棱锥形状;其尺度为微米级。所述金属颗粒为铜、铝、镁、钛及其合金材料,其形状为圆形、方形或三角形的空心或者实心颗粒。所述金属颗粒尺度为纳米、微米级别,颗粒尺度越小制备的多孔结构缝隙结构尺寸越小,缝隙大小可根据金属质量、密度与体积的关系采用下式进行估算:其中Agap为多孔传结构壁面层上的缝隙面积;Aporous为多孔结构壁面层的横截面积;V为烧结后多孔结构壁面层体积;Mmetal为烧结金属颗粒总质量;ρmetal为金属颗粒密度;对于普通水工质沸腾,金属颗粒尺寸分布于100纳米到60微米之间;当金属颗粒为规则球形,粒径在60微米时,其形成多孔缝隙尺寸在8‐10微米范围。所述多孔壁面层与普通换热管的相对位置取决于换热过程为管内沸腾还是管外沸腾;若为管内沸腾换热过程,多孔壁面层即烧结与普通换热管内部,模板管直径小于普通换热管直径;若为管外换热过程,多孔壁面层即烧结于普通换热管外,模板管直径大于普通换热管;其多孔壁面层厚度为百微米至毫米量级。本发明的效果和益处是:(1)本发明提出一种固定汽化核心的多孔换热管,其制备方法从技术上,打破了核沸腾传热表面无法控制汽化核心的局面;同时毛细结构降低了水平沸腾过程换热管壁面干烧的风险。(2)此结构换热管对于水平管换热过程,人工控制了整管汽化核心的分布,有效避免水平换热上下不均匀性,降低了换热管内部热应力。(3)固定汽化核心的多孔换热管,加工简单,易于在原有普通换热管、换热器中直接烧结改造,其实际应用成本低、效益高。本发明对正在兴起的多孔换热表面提供了又一新的发展方向和加工工艺,具有深远的学术价值和重大的社会效益。附图说明图1是一种固定汽化核心的多孔壁面换热管的制备原理示意图;其中(a)普通管外沸腾换热管(b)汽化核心模板管与普通换热管同轴固定(c)在普通换热管与模板管之间灌装金属微纳颗粒(d)烧结脱模后获得具有固定汽化核心的多孔沸腾换热管。图2为模板管与换热管封头装配示意图。图3为制备具有固定汽化核心的多孔外沸腾换热管的结构原理示意图。图4为制备具有固定汽化核心的多孔内沸腾换热管的结构原理示意图。图中标号:1—普通换热金属管;2—汽化核心模板管;3—金属微纳颗粒;4—微柱结构;5—汽化核心空穴;7—封头;8—螺纹;9—多孔壁面层具体实施方式本发明提出一种具有固定汽化核心的多孔壁面换热管及其制备方法,所述具有固定汽化核心的多孔壁面换热管由普通换热管、多孔结构壁面层以及固定的汽化核心空穴依次结合构成;以下结合附图对本发明进行说明。图1为一种固定汽化核心的多孔壁面换热管的制备原理示意图,其中(a)普通管外沸腾换热管,(b)在汽化核心模板管的汽化核心面上涂覆脱模剂氧化聚乙烯蜡,然后与普通换热管同轴固定,(c)在普通换热管与模板管之间灌装金属微纳颗粒,(d)烧结脱模后获得具有固定汽化核心的多孔壁面换热管。其制备过程主要分为三个操作步骤:(1)设计并加工制备汽化核心模板管2,并与普通换热管利用封头7固定;(2)筛选金属微纳颗粒3,并将金属颗粒3填充于汽化核心模板管2与普通换热管1环隙空间,制成生胚;(3)将填充压实的生胚置于惰性气体保护的烧结炉中烧结,烧结完成后冷却、脱模获得具有汽化核心空穴5的多孔结构换热管。所述步骤(1)中的汽化核心模板管2,其截面形状与普通换热管1一致,截面大小根据管外沸腾换热还是管内沸腾换热而定;如果沸腾过程为管内沸腾,汽化核心模板管2的直径需小于普通换热管1,若为管外沸腾,汽化核心模板管2直径需大于普通换热管1。汽化核心模板管2长度需比普通换热管1略长,以便结合上下封头7更好的填充金属微纳颗粒3。汽化核心模板管2壁面设计的微柱结构4,用于烧结制备多孔结构中的汽化核心空穴5。其材质主要为金属、陶瓷、玻璃等耐高温材料。所述汽化核心模板管2壁面上的微柱结构4利用激光溅射、刻蚀或烧结等精密加工技术,其尺度为微米级;其形状可为球形、微柱、圆台、棱锥等规则或不规则形状,图1所示微柱结构为球形。所述步骤(2)中填充的微纳颗粒3,首先在汽化核心模板管的汽化核心面上涂覆脱模剂氧化聚乙烯蜡,然后选择适合的金属微纳米颗粒3,对其进行筛选,确保颗粒均匀,以保证所需毛细结构不被微小颗粒填埋。将筛选好的微纳颗粒3填充于普通换热管1与汽化核心模板管2之间的环隙空间,并利用封头7填实、压紧,制得烧结生胚。所述金属颗粒可以是铜、铝、镁、钛等金属材料,其形状可以为圆形、方形、三角形、空心或者实心。其尺度为纳米、微米级别,颗粒尺度越小制备的多孔结构缝隙结构尺寸越小,所述步骤(3)中生胚烧结,将制得的生胚置于烧结炉中,持续通入惰性气体烧结。其烧结温度低于微纳金属颗粒3的熔融温度,其烧结温度仅需使得颗粒表面熔接即可。其烧结温度和烧结时间长度与金属颗粒的材质和直径有关。如金属颗粒为20微米的铜颗粒时,在氮气保护下,700°烧结3h即可。图2为汽化核心模板管与换热管封头装配示意图;为了便于金属颗粒3的填充,设计了汽化核心模板管与换热管之间的封头7;其作用不仅能够封堵金属颗粒3,同时还可以固定汽化核心模板管2和换热管1的相对位置,确保同轴。当换热管为管外沸腾管时(如图2中(a)换热管为管外沸腾管所示的结构),汽化核心模板管2的直径大于普通换热管1,此时封头7与外侧的汽化核心模板管2外壁通过螺纹8连接。当换热管为管内沸腾管时(如图2中(b)当换热管为管内沸腾管所示的结构),汽化核心模板管2的直径小于普通换热管1,其封头7与内侧的汽化核心模板管2的外壁通过螺纹8连接,其封头7与管之间无需要求密封,只需阻挡大批颗粒滚出即可。图3为制备具有固定汽化核心的多孔外沸腾换热管的结构原理示意图;如图中所示汽化核心模板管2直径大于普通换热管1,其表面设计的微柱结构4为圆柱形,且相邻两圆周上的微柱结构4是交错分布,金属颗粒3示意填充3层。此图为示意图,其结构与分布的可以如图3所示,但其不局限于此。图4为制备具有固定汽化核心的多孔内沸腾换热管的结构原理示意图;如图中所示汽化核心模板管2直径小于普通换热管1,其表面设计的微柱结构4为三菱锥形,相邻两圆周上的微柱结构4可以交错也可以一致;同样,金属颗粒示意填充3层。此图为示意图,其结构与分布的可以如图4所示,但其不局限于此。实施例1烧结具有固定汽化核心的多孔内沸腾铜换热管选用Φ22mm×100mm紫铜金属管为普通内沸腾换热金属管,首先对其进行酸洗、去离子水表面清洗处理,并惰性气体风干待用。选用Φ16mm×120mm的高熔点玻璃管做内模板管基底,先利用薄膜粘附单层40μm二氧化硅颗粒,并贴附在玻璃管外表面,进行900°氮气保护烧结,制备成汽化核心模板管;并在汽化核心模板管外涂覆脱模剂氧化聚乙烯蜡待用。选用传热性能好的金属Cu/CuO微米颗粒,并筛选出10μm左右尺度的均匀颗粒作为多孔结构烧结颗粒。利用封头结构将模板管与普通换热管装配,并填充Cu/CuO微米颗粒;压实封装后,放置于烧结炉中氮气保护下750°烧结3.5h。然后氮气保护下,在烧结炉中室温冷却,最后将汽化核心模板管脱离,获得及具有毛细结构又具有固定汽化核心的多孔内沸腾铜换热管。