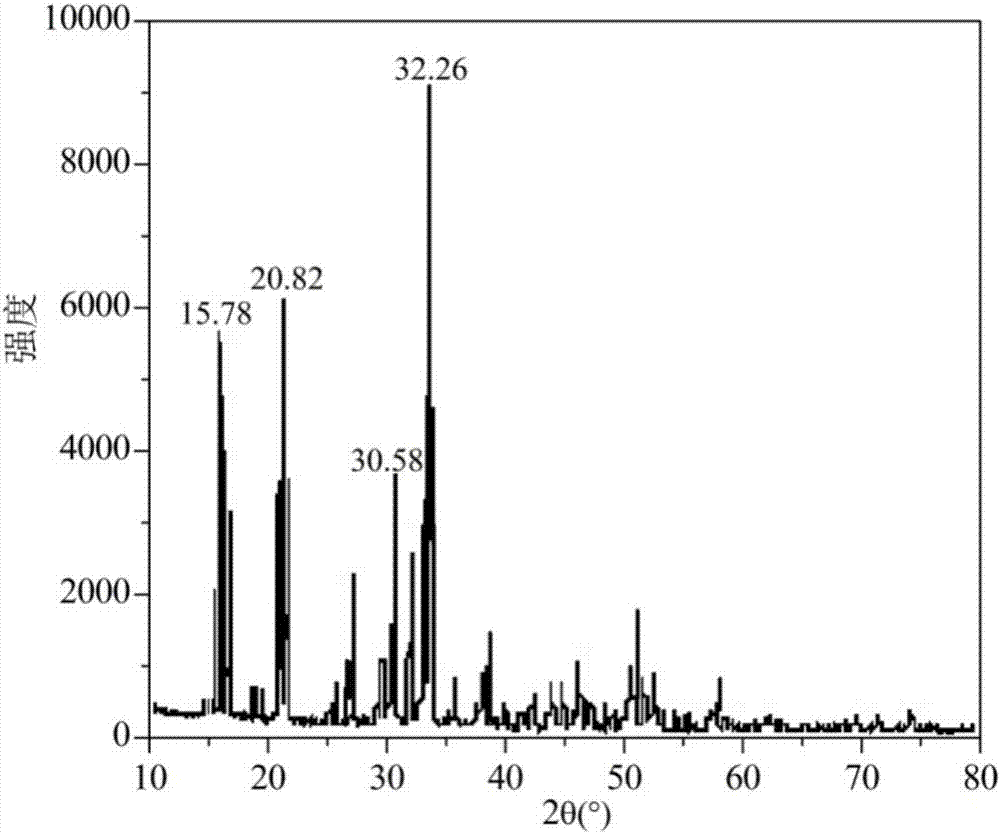
本发明涉及一种氨氮污染物的处理方法,尤其涉及一种循环利用磷酸铵镁处理氨氮污染物的方法,属于污水处理
技术领域:
。
背景技术:
:油品中的氮在原油一次加工和二次加工过程转化迁移到水相,形成大量的高氨氮污水(酸性水),高氨氮污水经汽提装置脱氨处理转化成一般含氮的汽提净化水,汽提净化水部分作为注水回用到电脱盐装置,然后排放到污水处理场,部分直接排放到污水处理场。源头污水中的氮排放分析表明,汽提净化水是污水处理场总氮负荷最大贡献源。常规污水处理工艺脱氮能力分析表明,现有的石油炼制污水处理工艺很难实现总氮含量的深度达标,需要消减的总氮处理负荷。一般采用沉淀法脱除氮污染物物化。其中,磷酸铵镁(MAP)化学沉淀法脱出废水中的氨氮反应机理:NH4+与PO43-和Mg2+生成难溶的复盐MgNH4PO4(MAP鸟粪石,25℃溶解度积常数ksp=2.5×10-13)。MAP的沉淀生成反应很快,不需要诱发。但是,磷酸铵镁沉淀法的药剂消耗量大、成本高是限制该技术推广应用的关键因素。因此,提供一种可以成本低廉的磷酸铵镁(MAP)化学沉淀法脱出废水中的氨氮污染物成为了本领域技术解决的问题。技术实现要素:为了解决上述技术问题,本发明的目的在于提供一种成本低廉的循环利用磷酸铵镁处理氨氮污染物的方法。为了实现上述技术目的,本发明提供了一种循环利用磷酸铵镁处理氨氮污染物的方法,该方法包括以下步骤:步骤一:调节待处理水的pH为8-8.5,加入氯化镁和磷酸氢二钠,20℃-40℃(优选为30℃)下搅拌,静置,得到磷酸铵镁沉淀和脱除氨氮的液体,以脱除待处理水中的氨氮污染物;步骤二:将脱除氨氮的液体进行离心,得到磷酸铵镁固体,对得到的磷酸铵镁固体进行加热烘干,加入氢氧化钠溶液,进行热解反应,得到氨气、氯化镁和磷酸二氢钠,氨气冷凝为氨水,氯化镁和磷酸二氢钠重复进行步骤一,完成通过循环利用磷酸铵镁处理氨氮污染物的方法。在上述方法中,优选地,在步骤一中,调节待处理水的pH为8.12。在上述方法中,优选地,在步骤一中,氯化镁中的n(Mg2+):磷酸氢二钠中的n(PO43-):待处理水中的n(NH4+)=1:1:1。在上述方法中,优选地,在步骤一中,搅拌的步骤包括:以150r/min-300r/min(更优选为300r/min)的速度搅拌5min-10min(更优选为5min),再以150r/min的速度搅拌5min-10min(更优选为5min)。在上述方法中,优选地,在步骤二中,磷酸铵镁固体与氢氧化钠溶液中氢氧化钠的物质的量比为1:0.9。在上述方法中,优选地,在步骤一中,静置的时间为20min-40min;更优选地,静置的时间为15min。在上述方法中,优选地,在步骤二中,将脱除氨氮的液体离心15min;更优选地,离心力为1000g-3000g。在上述方法中,优选地,在步骤二中,加热烘干的温度为80℃-95℃;更优选地,加热烘干的温度为80℃。在上述方法中,优选地,在步骤二中,热解反应的温度为110℃-140℃;更优选地,热解反应的温度为110℃。在上述方法中,优选地,在步骤二中,所述氢氧化钠溶液的质量浓度为4%。根据本发明的具体实施方式,在处理汽提净化水时,经过一级换热的净化水可以作为上述热解步骤的热能。在上述方法中,优选地,该方法中磷酸铵镁固体循环利用的次数为5次。根据本发明的具体方式,循环时,由于每一个周期都会产生药剂的损失,为满足n(NH4+):n(PO43-):n(Mg2+)=1:1:1的配比,第一周期后的每个周期都需要补充沉淀剂(氯化镁和磷酸氢二钠);同时,为了保证n(MAP):n(NaOH)的比例为1:0.9,循环时,需要补充氢氧化钠溶液。根据本发明的具体实施方式,采用蝶式离心机进行离心操作。本发明的上述循环利用磷酸铵镁处理氨氮污染物的方法分为两步:第一步是沉淀剂的烘干,第二步加碱热解再生。本发明的上述循环利用磷酸铵镁处理氨氮污染物的方法适用于任何污水中氨氮污染物的处理,尤其适用于炼化企业源头污水汽提净化水中氨氮污染物的处理。汽提净化水经过一级换热后的热能属于低品质热能,对于炼厂来说已经没有回收价值,但是可以作为热解再生的热能;净化水二级冷凝采用的是风冷,会产生大量的热风,可以作为磷酸铵镁固体烘干的热源。净化水通过重力由储罐进入到沉淀反应器,控制pH值、温度、反应时间、药剂投加量、搅拌速度等条件,反应完成后排出上清液,底部的MAP浓液排到碟式离心机进行分离。分离出MAP进入到再生反应器,先用热风烘干,再加碱混匀,利用净化水余热进行热解反应。热解气冷凝成氨水,热解固体产物循环利用。本发明的循环利用磷酸铵镁处理氨氮污染物的方法的工艺简单,沉氨效果明显。本发明的循环利用磷酸铵镁处理氨氮污染物的方法成本低,可以减少磷酸铵镁沉淀的处置量。附图说明图1为实施例1的循环利用磷酸铵镁处理氨氮污染物的方法的工艺流程图。图2为实施例1中的磷酸铵镁沉淀的XRD曲线。图3为实施例1的方法中MAP循环次数对氨氮脱除效果的影响曲线。图4为实施例1的方法中循环几次后产物的XRD曲线图。具体实施方式为了对本发明的技术特征、目的和有益效果有更加清楚的理解,现对本发明的技术方案进行以下详细说明,但不能理解为对本发明的可实施范围的限定。实施例1本实施例提供了一种循环利用磷酸铵镁处理汽提净化水中的氨氮污染物的方法,其工艺流程如图1所示,其中,净化水中COD为3615.50mg/L,TN含量为186.53mg/L,其中氨氮含量166.43mg/L,净化水的具体水质分析如表1所示。表1单位数量化学需氧量mg/L3615.50悬浮物mg/L28.10石油类mg/L39.37氨氮mg/L166.43总氮mg/L186.53总磷mg/L2.32硫化物mg/L43.10pH值8.12(7.5-8.9)电导率μs/cm1506总硬度mg/L7.4Cl-mg/L62SO42-203.25mg/L未检出PO43+28mg/L1.32具体包括以下步骤:步骤一:调节净化水的pH为8.12,加入氯化镁和磷酸氢二钠,30℃下以300r/min的速度搅拌5min,再以150r/min的速度搅拌5min,静置20min,离心15min,得到磷酸铵镁(MAP)沉淀和脱除氨氮的液体,脱除待处理水中的氨氮污染物;其中,氯化镁中的n(Mg2+):磷酸氢二钠中的n(PO43-):待处理水中的n(NH4+)=1:1:1;步骤二:将脱除氨氮的液体离心15min,80℃下对得到的磷酸铵镁固体进行加热烘干,加入氢氧化钠溶液,110℃下进行热解,得到氨气、氯化镁和磷酸二氢钠,氨气冷凝为氨水,氯化镁和磷酸二氢钠重复进行步骤一,完成通过循环利用磷酸铵镁处理氨氮污染物的方法;其中,磷酸铵镁固体与氢氧化钠溶液中氢氧化钠的物质的量比为1:0.9。对步骤一得到磷酸铵镁沉淀进行XRD分析,结果如图2所示。由图2可以看出,磷酸铵镁沉淀物在2θ为15.78°,20.82°,30.58°,32.26°等处均出现磷酸铵镁沉淀的典型的特征衍射峰,表明此条件下生成沉淀物主要为磷酸铵镁晶体。当步骤二得到的磷酸铵镁固体循环次数超过五次之后,氨氮的去除效率明显下降,如图3所示。第五次热解的MAP再次吸附时氨氮去除率75.69%,可以满足氮减排目标75.34%。由图4可知,MAP第五次热解产物再次吸附氨氮后,又出现了明显的MAP衍射峰,说明MAP第五次热解产物依然具有良好的脱氨能力。MAP第六次热解产物,也出现了MAP衍射峰,说明第六次热解MAP中的氨氮没有解析完全,根据峰的强度,残留量比较高。MAP第六次热解产物再次吸附氨氮后,又出现了较强的MAP衍射峰,说明MAP经过六次热解之后还是具有一定的沉氨能力,但是去除效果已经不能满足工艺要求。对本实施例的上述方法的成本进行如下计算:成本主要由固定资产投资成本和运行成本构成,其中运行成本是影响该技术广泛应用的关键制约因素。运行成本主要包括药剂成本和能耗成本等,药剂成本贡献比例最大。本实施例的方法的运行成本主要由搅拌电耗和离心机电耗构成,MAP热解过程已经找到充足的热源,所以该方法的能耗非常低。MAP沉淀法的药剂可以循环使用六个周期,第一个周期投加的是镁盐和磷酸盐生产MAP沉淀;其余五个周期MAP的沉淀物重复利用。六个周期的氨氮去除率为86.30%、84.94%、83.25%、82.36%、78.53%以及75.69%,平均值为81.85%。由于每一个周期都会产生药剂的损失,所以要达到n(NH4+):n(PO43-):n(Mg2+)=1:1:1的配比,第2至5周期都需要补充沉淀剂。第2至5周期每个周期的MAP的回收率定为80%(回收率约等于氨氮的去除率),沉淀剂的补充率约为20%。第一个周期的药剂投加量定为100%,之后的五个周期的药剂投加量都为20%。依据上述分析,可以确定六个周期的药剂的投加量为200%,即原本处理两吨污水的药剂可以处理六吨污水。MAP在回用的时候需要投加氢氧化钠,MAP的回收率为80%,NaOH的投加量为72%[n(MAP):n(NaOH)配比为1:0.9]。污水中的氨氮浓度166.43mg/L,摩尔浓度为11.89mmol/L,则消耗的沉淀剂的量为3.96mmoL/L(11.89mmol/L÷3),NaOH量为7.13mmoL/L(11.89mmol/L×72%×5÷6)。则,MgCl2·6H2O投加量为804.71mg/L,无水Na2HPO4投加量为562.16mg/L,NaOH投加量为285.2mg/L。MAP热解循环沉氨方法主要药剂用量、价格估算见表2。由表2可知,处理一吨污水的药剂成本是3.79元。如果按照污染物浓度计算,处理1kg氨氮的成本是22.78元。如果不对MAP进行热解再生,药剂消耗会增加200%。吨污水成本10元左右。表2名称价格(元/t)用量(kg/t)费用(元)MgCl2·6H2O(工业级)5000.8050.40无水Na2HPO4(工业级)45000.5622.53NaOH(工业级)50000.2850.86合计3.79(10)150(400)万元从经济的角度来说,污水处理量为48.5t/h,药剂处理成本是3.79元/t,如果折合到全厂污水357.06t/h,相当于综合污水处理场每吨污水增加0.51元的处理成本,成本增加不高但是可以有力的保障总氮达标(能耗成本很低,估值每吨新增能耗成本在0.2元以内,但是具体数值不能确定,其对污水处理场的综合能耗贡献低于0.05元,所以未将其纳入成本核算)。从技术的角度来说,上述方法基本在常压条件下进行,主要的反应器是搅拌沉淀装置和加热再生装置,装置都属于常规反应器,易于建设、管理和运行。从环保效益的角度来说,减排氨氮6.46kg/h(浓度×去除率×流量=166.43g/m3×80%×48.5tm3/h),而综合污水处理场的进水氨氮负荷为22.41kg/h,减排了28.83%的总氮处理负荷,污水处理场的进水总氮也由64.30mg/L下降到45.76mg/L,在这样的进水TN负荷条件下,常规的A/O生化脱氮工艺都可以实现总氮15mg/L的深度达标。因此,应用本发明的方法处理石油炼制企业点源高氨氮的污水净化水是可行且高效的。当前第1页1 2 3