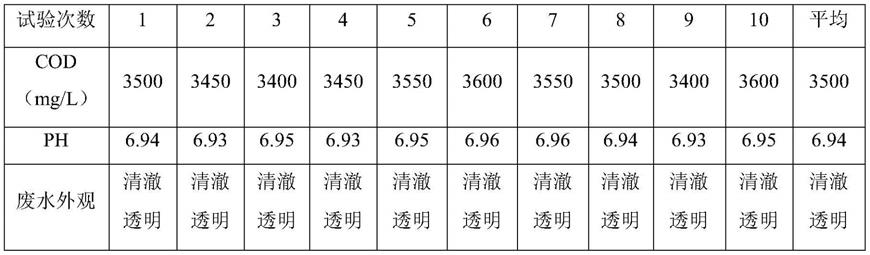
1.本发明涉及化工废水处理领域,具体而言,涉及一种甲基丙烯酸甲酯装置废水处理的方法。
背景技术:2.丙酮氰醇法(ach法)生产甲基丙烯酸甲酯,其装置中的尾气鼓风机、精制分层器、蒸汽喷射泵等设备在正常运行过程中产生废水,该废水cod值高、酸性强,通过化学分析,废水中主要含有甲醇、丙酮和甲基丙烯酸甲酯等有机物,cod值主要由这些有机物贡献,只有脱除废水中的有机物才能降低废水cod值。废水中含有的甲基丙烯酸甲酯在常压受热条件下温度达到60℃开始聚合,由于废水组成复杂且显强酸性,常用的甲基丙烯酸甲酯阻聚剂在废水加热过程中无法起到良好的阻聚效果。如果废水中甲基丙烯酸甲酯出现聚合现象,会导致废水浑浊且有聚合物,无法进行生化处理。
3.以国内某厂甲基丙烯酸甲酯装置为例,配套生化处理装置要求废水可生化处理满足三个条件:
4.(1)废水清澈无悬浮物;
5.(2)cod值低于20000mg/l;
6.(3)ph中性或弱酸性。
7.该装置废水cod高达238000mg/l,ph值2.38显强酸性,无法直接进行生化处理。目前主要以天然气为燃料燃烧处理该部分废水,废水燃烧过程中产生废气,废水处理成本高且不环保。
技术实现要素:8.本发明的主要目的在于提供一种甲基丙烯酸甲酯装置废水处理的方法,以解决现有技术中废水处理后的难以满足生化处理要求的问题。
9.为了实现上述目的,根据本发明的一个方面,提供了一种甲基丙烯酸甲酯装置废水处理的方法,该方法包括:采用多种萃取剂将甲基丙烯酸甲酯从废水中萃取出来,得到第一萃余相;将第一萃余相的ph值调节至中性,得到第二萃余相;对第二萃余相进行精馏,得到处理后废水。
10.进一步地,多种萃取剂包括正己烷、环己烷和辛醇。
11.进一步地,正己烷、环己烷和辛醇的质量比为95~97:3.0~2.0:2.0~1.0。
12.进一步地,多种萃取剂的总质量与废水的质量之比为1:9~1:11。
13.进一步地,萃取的温度为293k~300k。
14.进一步地,在搅拌的条件下进行萃取,搅拌的速度为30r/min~50r/min,搅拌的时间控制在10min~20min。
15.进一步地,搅拌后静置25min~35min,得到第一萃余相。
16.进一步地,采用碱将萃余相的ph值调节至6.0~8.0。
17.进一步地,在低于0.1mpa的压力下,对第二萃余相进行精馏。
18.进一步地,采用精馏塔对第二萃余相进行精馏,并将精馏塔的塔釜温度控制在99~101℃之间,塔顶温度控制在55~56℃,回流比控制在3:1~5:1之间。
19.应用本发明的技术方案,通过采用多种萃取剂形成的萃取剂组合对废水中的易聚物
---
甲基丙烯酸甲酯进行萃取去除,使得萃余相在后续的精馏过程中不会出现聚合的情况,然后调节ph值再通过一步常压精馏法使处理后的废水满足生化处理要求。该方法一方面解决了现有技术中废水有机物脱除过程中甲基丙烯酸甲酯受热会聚合的问题,另一方面使得处理后的废水cod值低于15000mg/l且ph值接近中性,从而满足生化处理要求。
具体实施方式
20.需要说明的是,在不冲突的情况下,本技术中的实施例及实施例中的特征可以相互组合。下面将结合实施例来详细说明本发明。
21.本发明中的甲基丙烯酸甲酯装置废水是指丙酮氰醇法(ach法)生产甲基丙烯酸甲酯装置(包括装置尾气鼓风机、精制分层器、蒸汽喷射泵等设备)在正常运行过程中产生高cod值的废水。
22.如背景技术所提到的,现有的甲基丙烯酸甲酯装置废水中因含有高浓度的甲基丙烯酸甲酯,在现有方法中容易导致聚合而使得处理后废水难以满足生化处理的要求。为改善这一状况,在本技术一种典型的实施方式中,提供了一种甲基丙烯酸甲酯装置废水处理的方法,该方法包括:采用多种萃取剂将甲基丙烯酸甲酯从废水中萃取出来,得到第一萃余相;将第一萃余相的ph值调节至中性,得到第二萃余相;对第二萃余相进行精馏,得到处理后废水。
23.该方法通过采用多种萃取剂形成的萃取剂组合对废水中的易聚物
---
甲基丙烯酸甲酯进行萃取去除,使得萃余相在后续的精馏过程中不会出现聚合的情况,然后调节ph值再通过一步常压精馏法使处理后的废水满足生化处理要求。该方法一方面解决了现有技术中废水有机物脱除过程中甲基丙烯酸甲酯受热会聚合的问题,另一方面使得处理后的废水cod值低于15000mg/l且ph值接近中性,从而满足生化处理要求。
24.本技术的上述废水处理的方法,从废水中易聚合的有机物甲基丙烯酸甲酯出发,通过采用萃取的方式将其分离出来,一方面解决了废水中有机物聚合而导致无法生化处理的问题,另一方面还回收了甲基丙烯酸甲酯,提高了产品收率。而对甲基丙烯酸甲酯进行萃取的萃取剂,可根据如下原则进行选择:1)萃取容量大,即单位浓度的萃取剂对被萃取物质有较大的萃取能力;2)选择性高,即对分离的有关物质有较大的分离系数;3)化学稳定性好,即不易水解、加热不易分解、能耐酸、碱、盐、氧化剂或还原剂的作用;4)水溶性小油溶性大,与水相易分层,不生成第三相,不发生乳化现象;5)易于反萃,即改变萃取条件时,能够容易地使被萃取物质从有机相转入到水相。
25.在本技术一种优选的实施例中,上述多种萃取剂包括正己烷、环己烷和辛醇。
26.选择了上述合适的萃取剂进行组合时,具体组合的比例可以根据萃取效果来进行优化调整。在本技术一种优选的实施例中,控制正己烷、环己烷和辛醇的质量比为95~97:3.0~2.0:2.0~1.0。在该比例下,对甲基丙烯酸甲酯的萃取效率更高。
27.在另一种优选的实施例中,多种萃取剂的总质量与废水的质量之比为1:9~1:11。
控制萃取剂的总质量与废水的质量在1:10左右,对废水中甲基丙烯酸甲酯的萃取效率更高。
28.上述萃取在常温下进行即可。在一种优选的实施例中,上述萃取的温度为293k~300k。在该优选的温度范围内进行萃取,萃取效率更高。
29.在上述萃取条件下,为了进一步提高对废水中的甲基丙烯酸甲酯的萃取率,在一种优选的实施例中,在搅拌的条件下进行萃取,搅拌的速度为30r/min~50r/min,搅拌的时间控制在10min~20min。搅拌促进萃取剂与被萃取物的接触时间和接触面积,从而提高萃取率。
30.在上述搅拌后,静置一定时间使得水相与有机相有效分离,优选搅拌后静置25min~35min分离有机相,得到第一萃余相。
31.上述在得到第一萃余相后先调节ph值为中性再进行废水中的甲醇、丙醇的精馏,一方面由于生化处理要求废水接近中性,另一方面先调节为中性也可以防止酸性的萃余相对精馏设备造成腐蚀及环境破坏。具体调节ph的方式不限,优选地,采用碱将萃余相的ph值调节至6.0~8.0。
32.将调节到中性后的第二萃余相在常压下进行精馏即可。优选地,在低于0.1mpa的压力下,对第二萃余相进行精馏。
33.为了进一步提高甲醇和丙酮的精馏效率,在一种优选的实施例中,采用精馏塔对第二萃余相进行精馏,并将精馏塔的塔釜温度控制在99~101℃之间,塔顶温度控制在55~56℃,回流比控制在3:1~5:1之间。
34.下面将结合具体的实施例来进一步说明本技术的有益效果。
35.实施例1
36.取国内某厂甲基丙烯酸甲酯装置废水。
37.萃取剂制备:其组分包括:正己烷、环己烷、辛醇。各组份质量配比为:正己烷:环己烷:辛醇=96:2.5:1.5。将正己烷、环己烷和辛醇按照比例混合,搅拌均匀后,制得萃取剂。
38.萃取工艺为:萃取剂和废水的萃取质量为1:10,萃取温度为298k,搅拌速度为40r/min,搅拌时间为15min,静置时间为30min,然后萃取分离甲基丙烯酸甲酯,得到萃余相。
39.向萃余相中加碱(氢氧化钠)调ph值至7.0。
40.精馏工艺为:精馏塔填料总高度为40cm(20块塔板),其中精馏段高度为12cm(6块塔板),提馏段高度为28cm(14块塔板),塔釜温度100℃,塔顶温度56℃,回流比4:1,操作压力为常压。
41.连续取样10次精馏后的塔釜废水,观察其外观及分析废水cod值和ph值,结果见表1。
42.43.表1中数据显示,处理后的废水连续取样10次,cod平均值为3500,ph平均值为6.94,废水外观清澈透明,满足装置生化处理要求。
44.实施例2
45.取国内某厂甲基丙烯酸甲酯装置废水。
46.萃取剂制备:其组分包括:正己烷、环己烷、辛醇。各组份质量配比为:正己烷:环己烷:辛醇=95:3:2。将正己烷、环己烷和辛醇按照比例混合,搅拌均匀后,制得萃取剂。
47.萃取工艺为,萃取剂和废水的萃取质量为1:10,萃取温度为298k,搅拌速度为40r/min,搅拌时间为15min,静置时间为30min。
48.萃余相加碱(氢氧化钠)调ph值至7.0。
49.精馏工艺为,精馏塔填料总高度为40cm(20块塔板),其中精馏段高度为12cm(6块塔板),提馏段高度为28cm(14块塔板),塔釜温度100℃,塔顶温度56℃,回流比4:1,操作压力为常压。
50.连续取样10次精馏后的塔釜废水,观察其外观及分析废水cod值和ph值,结果见表2。
[0051][0052]
表2中数据显示,处理后的废水连续取样10次,cod平均值为4550,ph平均值为6.89,废水外观微浑且有少量悬浮物,基本满足装置生化处理要求。
[0053]
实施例3
[0054]
取国内某厂甲基丙烯酸甲酯装置废水。
[0055]
萃取剂制备:其组分包括:正己烷、环己烷、辛醇。各组份质量配比为:正己烷:环己烷:辛醇=97:2:1。将正己烷、环己烷和辛醇按照比例混合,搅拌均匀后,制得萃取剂。
[0056]
萃取工艺为,萃取剂和废水的萃取质量为1:10,萃取温度为298k,搅拌速度为40r/min,搅拌时间为15min,静置时间为30min。
[0057]
萃余相加碱(氢氧化钠)调ph值至7.0。
[0058]
精馏工艺为,精馏塔填料总高度为40cm(20块塔板),其中精馏段高度为12cm(6块塔板),提馏段高度为28cm(14块塔板),塔釜温度100℃,塔顶温度56℃,回流比4:1,操作压力为常压。
[0059]
连续取样10次精馏后的塔釜废水,观察其外观及分析废水cod值和ph值,结果见表3。
[0060]
表3废水cod、ph及外观
[0061][0062]
表3中数据显示,处理后的废水连续取样10次,cod平均值为5300,ph平均值为6.91,满足生化处理要求,但是废水外观微浑有悬浮物,废水有悬浮物会影响废水的生化处理效果。
[0063]
实施例4
[0064]
取国内某厂甲基丙烯酸甲酯装置废水。
[0065]
萃取剂制备:其组分包括:正己烷、环己烷、辛醇。各组份质量配比为:正己烷:环己烷:辛醇=95:3:2。将正己烷、环己烷和辛醇按照比例混合,搅拌均匀后,制得萃取剂。
[0066]
萃取工艺为,萃取剂和废水的萃取质量为1:9,萃取温度为300k,搅拌速度为30r/min,搅拌时间为20min,静置时间为35min。
[0067]
萃余相加碱(氢氧化钠)调ph值至7.0。
[0068]
精馏工艺为,精馏塔填料总高度为40cm(20块塔板),其中精馏段高度为12cm(6块塔板),提馏段高度为28cm(14块塔板),塔釜温度101℃,塔顶温度56℃,回流比5:1,操作压力为常压。
[0069]
连续取样10次精馏后的塔釜废水,观察其外观及分析废水cod值和ph值,结果见表4:
[0070][0071]
实施例5
[0072]
取国内某厂甲基丙烯酸甲酯装置废水。
[0073]
萃取剂制备:其组分包括:正己烷、环己烷、辛醇。各组份质量配比为:正己烷:环己烷:辛醇=95:3:2。将正己烷、环己烷和辛醇按照比例混合,搅拌均匀后,制得萃取剂。
[0074]
萃取工艺为,萃取剂和废水的萃取质量为1:9,萃取温度为293k,搅拌速度为30r/min,搅拌时间为20min,静置时间为25min。
[0075]
萃余相加碱(氢氧化钠)调ph值至8.0。
[0076]
精馏工艺为,精馏塔填料总高度为40cm(20块塔板),其中精馏段高度为12cm(6块
塔板),提馏段高度为28cm(14块塔板),塔釜温度99℃,塔顶温度55℃,回流比3:1,操作压力为常压。
[0077]
连续取样10次精馏后的塔釜废水,观察其外观及分析废水cod值和ph值,结果见表5。
[0078][0079]
实施例6
[0080]
取国内某厂甲基丙烯酸甲酯装置废水。
[0081]
萃取剂制备:其组分包括:正己烷、环己烷、辛醇。各组份质量配比为:正己烷:环己烷:辛醇=94:3:3。将正己烷、环己烷和辛醇按照比例混合,搅拌均匀后,制得萃取剂。
[0082]
萃取工艺为,萃取剂和废水的萃取质量为1:9,萃取温度为293k,搅拌速度为30r/min,搅拌时间为20min,静置时间为25min。
[0083]
萃余相加碱(氢氧化钠)调ph值至8.0。
[0084]
精馏工艺为,精馏塔填料总高度为40cm(20块塔板),其中精馏段高度为12cm(6块塔板),提馏段高度为28cm(14块塔板),塔釜温度99℃,塔顶温度55℃,回流比3:1,操作压力为常压。
[0085]
连续取样10次精馏后的塔釜废水,观察其外观及分析废水cod值和ph值,结果见表6。
[0086][0087]
实施例7
[0088]
取国内某厂甲基丙烯酸甲酯装置废水。
[0089]
萃取剂制备:其组分包括:正辛烷、环己烷、辛醇。各组份质量配比为:正辛烷:环己烷:辛醇=95:3:2。将正己烷、环己烷和辛醇按照比例混合,搅拌均匀后,制得萃取剂。
[0090]
萃取工艺为,萃取剂和废水的萃取质量为1:9,萃取温度为293k,搅拌速度为30r/min,搅拌时间为20min,静置时间为25min。
[0091]
萃余相加碱(氢氧化钠)调ph值至8.0。
[0092]
精馏工艺为,精馏塔填料总高度为40cm(20块塔板),其中精馏段高度为12cm(6块塔板),提馏段高度为28cm(14块塔板),塔釜温度99℃,塔顶温度55℃,回流比3:1,操作压力为常压。
[0093]
连续取样10次精馏后的塔釜废水,观察其外观及分析废水cod值和ph值,结果见表7。
[0094][0095]
实施例8
[0096]
取国内某厂甲基丙烯酸甲酯装置废水。
[0097]
萃取剂制备:其组分包括:正己烷、环己烷、己醇。各组份质量配比为:正己烷:环己烷:己醇=95:3:2。将正己烷、环己烷和辛醇按照比例混合,搅拌均匀后,制得萃取剂。
[0098]
萃取工艺为,萃取剂和废水的萃取质量为1:9,萃取温度为293k,搅拌速度为30r/min,搅拌时间为20min,静置时间为25min。
[0099]
萃余相加碱(氢氧化钠)调ph值至8.0。
[0100]
精馏工艺为,精馏塔填料总高度为40cm(20块塔板),其中精馏段高度为12cm(6块塔板),提馏段高度为28cm(14块塔板),塔釜温度99℃,塔顶温度55℃,回流比3:1,操作压力为常压。
[0101]
连续取样10次精馏后的塔釜废水,观察其外观及分析废水cod值和ph值,结果见表8。
[0102][0103]
实施例9
[0104]
取国内某厂甲基丙烯酸甲酯装置废水。
[0105]
萃取剂制备:其组分包括:正己烷、环己烷、辛醇。各组份质量配比为:正己烷:环己烷:辛醇=95:3:2。将正己烷、环己烷和辛醇按照比例混合,搅拌均匀后,制得萃取剂。
[0106]
萃取工艺为,萃取剂和废水的萃取质量为1:9,萃取温度为293k,搅拌速度为30r/min,搅拌时间为20min,静置时间为25min。
[0107]
萃余相加碱(氢氧化钠)调ph值至8.0。
[0108]
精馏工艺为,精馏塔填料总高度为40cm(20块塔板),其中精馏段高度为12cm(6块塔板),提馏段高度为28cm(14块塔板),塔釜温度95℃,塔顶温度58℃,回流比3:1,操作压力为常压。
[0109]
连续取样10次精馏后的塔釜废水,观察其外观及分析废水cod值和ph值,结果见表9。
[0110][0111]
对比例1
[0112]
将实施例5中的调ph值步骤与萃取步骤顺序调换,即,先调ph值为中性,再进行萃取,结果见表10。
[0113][0114]
从以上的描述中,可以看出,本发明上述的实施例实现了如下技术效果:通过采用多种萃取剂形成的萃取剂组合对废水中的易聚物
---
甲基丙烯酸甲酯进行萃取去除,使得萃余相在后续的精馏过程中不会出现聚合的情况,然后调节ph值再通过一步常压精馏法使处理后的废水满足生化处理要求。该方法一方面解决了现有技术中废水有机物脱除过程中甲基丙烯酸甲酯受热会聚合的问题,另一方面使得处理后的废水cod值低于15000mg/l且ph值接近中性,从而满足生化处理要求。
[0115]
相比现有的处理方法,本技术的甲基丙烯酸甲酯装置废水处理方法具有以下优势:
[0116]
(1)萃取剂易得且经济性较好,同时萃取剂对甲基丙烯酸甲酯具有良好的萃取效果。
[0117]
(2)萃取剂易回收。
[0118]
(3)萃取后的废水不含有甲基丙烯酸甲酯,精馏过程中无聚合物产生。
[0119]
(4)处理后的塔釜废水cod平均值3500mg/l,远低于20000mg/l的要求;
[0120]
(5)处理工艺绿色环保,无废气产生。
[0121]
以上所述仅为本发明的优选实施例而已,并不用于限制本发明,对于本领域的技术人员来说,本发明可以有各种更改和变化。凡在本发明的精神和原则之内,所作的任何修改、等同替换、改进等,均应包含在本发明的保护范围之内。