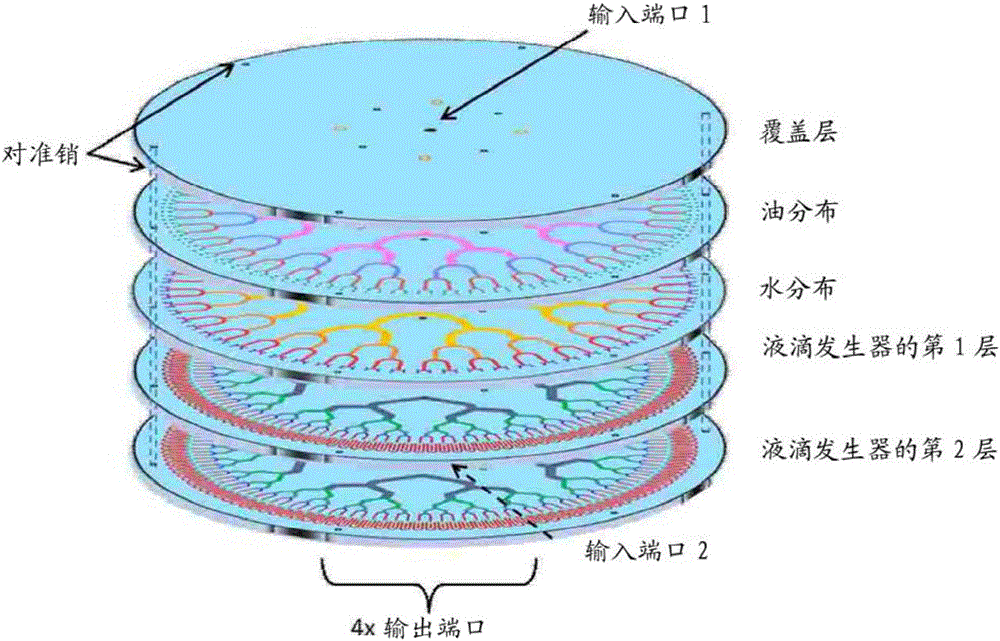
本申请要求2013年11月11日提交的美国临时申请No.61/902,600的权益,将其全部通过参考引入。
技术领域:
本发明涉及用于制造(生产)单分散的乳液的器件和方法以及连续后处理技术。
背景技术:
:微流控学已获得越来越多的关注,具有被应用于例如芯片实验室、燃料电池、诊断系统、微反应器、材料的合成和许多其它的领域中的潜力。微流控学还提供用于制造对于例如药物递送和生活消费品的行业有意义的均匀地尺寸化的乳液和胶囊的潜力。高度单分散的乳液的产生对于例如药物、化妆品、腐蚀性化学品和精细化学品的公司以及食品工业可为非常重要的。技术实现要素:用于微流控系统的并行化(平行化,paralellization)的多层微流控器件可包括包含多个通道以控制流体的流动的分布网络,所述分布网络形成于至少两个板或基材层中以形成通过各层中的通孔在所述层之间对准(align)的流体通道的分形(fractal)图案。流体通道的分形图案可同时运行。并行化容许使用者同时运行多个微流控系统,其可以大的量制造微流控乳液。所述器件可包括从所述器件的表面能到达的输入端。所述通道可在由聚合物塑料材料例如聚(甲基丙烯酸甲酯)、不锈钢、陶瓷、或玻璃或其组合制成的基材或板上。所述通道可以基于遵循方程p×m×2n的任意数的图案布置,其中p为代表瓣(petal)的数量的整数,m为代表相同的产生层的数量的整数且n为代表分形支化水平的数量的整数。所述分布网络可连接形成乳液产生层的板或基材的堆。所述分布网络可包括至少两个分布层,各分布层包括流体通道的分形图案和将它们与乳液产生层的堆互连的通孔。所述器件可包括至少一个入口或输入端以及至少1个出口或输出端以容许不混溶的液体的可达性和液滴的离开。在一些实施方式中,所述器件可包括每种不混溶的流体的至少一个入口或输入端。形成乳液的方法可包括使流体通过包括至少两个层的多层器件,其中所述两个层通过通孔连接,其中各层包括分形图案,和其中各层包括分配所述乳液的与所述器件的通道连接以控制流体到出口的流动的分布网络。所述乳液可为单分散的或多分散的。用于后处理乳液的方法可包括将流体供应到具有弯曲表面的处理区使得所述流体形成没有侧面边缘的均匀的且连续的层。所述处理区可包括具有弯曲表面的管。替代地,所述处理区可包括类似于球形喷泉(ball-fountain)的开放的圆形表面。所述方法可包括将乳液输出端排列在具有弯曲表面的管周围或在所述开放的圆形表面周围。所述方法可包括:对所述弯曲表面进行热处理以形成适合用于药物、涂料或其它应用的晶体和另外的单分散的颗粒,或对所述弯曲表面进行UV处理以形成晶体和另外的单分散的颗粒。在一个方面,多层微流控器件可包括与所述器件的通道连接以控制流体的流动的分布网络,所述分布网络包括至少两个板或基材层,各层包括和雕刻(蚀刻)有通过孔在所述板或基材层之间对准的通道的图案以容许不混溶的液体的组合和均匀的液滴的形成。在所述多层器件中,流体可在所述器件中从一个层流动到另一层。在一些实施方式中,所述器件可包括从所述器件的表面能到达的轴对称的输入端。如果包含较多的液体,则所述输入端可从一个位置开始然后被引导至中部用于初始分布。各层的厚度可小于1mm或更多,而所述通道可形成于可由聚合物材料例如聚(甲基丙烯酸甲酯)或任何另外的材料例如金属例如不锈钢、硅、玻璃或陶瓷或以上中的任意的组合制成的基材或板上。在一些实施方式中,所述板上的雕刻的图案可导致范围从至少2个通道起的低或高数量的通道和更多遵循该方程至少p×m×2n的微流控液滴发生器(MFDG),其中p为代表(下面说明的)瓣的数量的整数,m为代表相同的产生层的数量的整数且n为代表分形支化水平的数量的整数,且因此p×2n为每个层的发生器的数量。例如,所述器件可包括至少128个通道、至少256个通道、至少512个通道、或至少1024个通道。所述器件可包括分布由正被使用的工艺的化学所要求的任意数量的不混溶的流体的多个层。各层可对应于单独的流体。在一些实施方式中,所述器件可进一步包括水分布层。所述器件可包括油分布层。所述器件可包括覆盖层。在另一方面,用于处理乳液的系统可包括封闭的弯曲表面或开放的圆形表面以及至少一个输出端,所述输出端将所述乳液作为层供应在所述封闭的弯曲表面的表面上。所述系统可包括至少四个供应乳液的输出端。所述输出端可包括排列在所述封闭的弯曲表面周围的多个输出端。所述乳液可将所述封闭的弯曲表面的横截面的整个周边润湿以消除对于(with)干的对应物的侧面边缘。以这种方式处理容许通过可操控由所述并行化的系统产生的容量的产物的发展的后处理系统以大的量操控微流控乳液。在一些实施方式中,所述系统可连接到包括至少两个层的多层微流控器件,其中所述两个层通过通孔连接,其中各层包括分形图案,和其中各层包括与所述器件的通道连接以控制流体的流动的分布网络。各层可包括分布通道和通孔。在另一方面,用于制备乳液的方法可包括使用多层微流控器件,所述多层微流控器件包括至少两个层,其中所述两个层通过通孔连接,其中各层包括分形图案,和其中各层包括所述器件的分布网络和多个通道以控制流体的流动。至少一个层可包括刚性材料。在一些实施方式中,所述乳液可为单分散的。所述乳液的制造速率可为至少300mL/h。在另一方面,用于处理乳液的方法可包括将流体从混合器或乳液源供应到具有弯曲表面的处理区,使得所述流体形成没有从润湿的表面到干燥表面的过渡的侧面边缘的层。所述处理区可包括具有弯曲表面的管或开放的圆形表面。所述流体可接触所述表面的壁以形成薄膜。所述流体可将所述弯曲表面的整个周边润湿。所述表面可聚集和均匀地分布乳液供应的输出端,使得它可被连续地且均匀地处理。该过程的实例可包括热处理或UV曝光处理。在一个实施方式中,圆柱体可让其壁均匀地涂覆有向下滑动并且容许后处理的流动着的乳液的薄层。在另一实施方式中,开放的圆形表面可让其表面均匀地涂覆有流动着的乳液的薄层。在一些实施方式中,所述开放的圆形表面可为开放的球。在一些另外的实施方式中,所述开放的圆形表面可为圆形的柱。在一些实施方式中,所述方法可使用至少四个输出端以将流体从混合器供应到处理区。所述方法可包括将乳液输出端排列在具有弯曲表面的管周围。在一些实施方式中,所述方法可包括加热所述弯曲表面。所述方法可包括加热没有边缘的流体的层。所述方法可包括使处理区暴露于紫外光。在一个方面,多层微流控器件可包括连接乳液产生层的堆的分布网络,其中所述分布网络可包括至少两个分布层,各分布层包括流体通道的分形图案和将它们与乳液产生层的堆互连的通孔。所述产生层的数量可为整数,例如,1、2、3、4、5、6、7、8、9、或10个、更多。所述乳液产生层可通过微流控液滴发生器的极阵列(环形阵列,polararray)形成。所述乳液产生层可包括至少128个发生器、或至少256个发生器、或至少512个发生器、或至少1024个发生器。各发生器可为以上描述的通道。根据瓣的数量和每瓣的发生器的数量,所述器件的另外的构造可具有不同数量的发生器。由以下描述、附图和权利要求书,其它方面、实施方式和特征将是明晰的。附图说明图1A显示以聚(甲基丙烯酸甲酯)("PMMA")制作的具有256个通道的微流控芯片,其包括2个堆叠的各自128个通道的层。图1B显示器件的侧面图像。图2显示形成用于两种流体的器件的层的实例设计,其具有两个用于油和水供应的分布网络和两个液滴产生层。图3显示组装的堆。图4显示盖层或顶部层。图5显示连续相分布网络和分布网络。图6显示分散相分布网络和分布网络。图7显示发生器的第一层、或底部层。图8显示发生器的中间层。例如,它可为第二层、第三层、第四层等。图9显示形成器件的不同的层。图10显示液相如何从输入端通过分布层流动到发生器的示意图。图11显示当产生层中的发生器同时工作时它们看起来如何的特写图像。图12显示关于所测试的不同的多层微流控器件的尺寸和变异系数的结果。图12A为描绘在不同的分散相流动速率下的液滴尺寸的图。图12B为描绘作为每个产生层的流动速率的函数的变异系数的图。图13A显示用于微流控液滴发生器的大规模并行化的实验装置的实例,其中所述装置包括其中可处理输出乳液的后处理台。为了容易的可视化,图13B和13D显示经染色的油包水乳液的实例的图像。图13C为描绘有效直径分布的图。图14显示说明瓣如何在芯片内充当独立的单位的瓣构造。图15显示描绘当关闭不同数量的瓣时对乳液的分散性的影响的图。图16和图17显示用于微流控液滴发生器的大规模并行化的实验装置的实例,其中所述装置包括其中可处理输出乳液的后处理台。图18显示在PMMA上切削的微流控通道的SEM照片。图19显示甘氨酸球形晶体附聚物的结晶化。图19A为甘氨酸球形晶体附聚物的SEM图像。图19B为描绘由液滴的快速收缩、成核、球晶生长、和陈化组成的结晶化顺序的示意图。图19C为甘氨酸晶体附聚物的SEM图像。图19D为甘氨酸球形晶体附聚物的光学图像。图20显示分布网络的实例。图20A是环形的分布网络。图20B是与树状结构组合的环形的分布网络。图20C是分形树状分布网络。在插图中,蓝色表示水相的进料路线,而橙色表示油相的路径。对于图20C,水相和油相具有相同的路径但在不同的层中且排列以形成瓣。图21显示在开放的圆形表面中的后处理的示意图。图22显示在开放的圆形表面中的UV后处理的示意图。图23显示具有6个瓣的器件的实例,其中每个瓣具有八个发生器。具体实施方式在过去二十几年中的基于液滴的微流控学的发展已经为在若干研究领域中的快速和连续的进步提供机会。在精细化学、药物发现、和生物学中的应用已得益于它们的整个系统向纳升到飞升尺寸液滴的微型化。由于该尺寸减小,给定系统的表面积对体积比变得更大,且表面相关的物理学支配体积现象。该技术已容许新的方法来实现在宏观尺度上是不可能的实验。参见,A.B.Theberge,F.Courtois,Y.Schaerli,M.Fischlechner,C.Abell,F.Hollfelder和W.T.S.Huck,Small,2010,49,5846-5868,其全部通过参考引入。例如,液滴中的快速热传递容许在颗粒的合成中的以及对芯片温度循环的精确温度控制。参见E.Chan,A.Alivisatos和R.Mathies,J.Am.Chem.Soc.,2005,127,13854-13861,S.Xu,Z.Nie,M.Seo,P.Lewis,E.Kumacheva,H.A.Stone,P.Garstecki,D.B.Weibel,I.Gitlin和G.M.Whitesides,Angew.Chem.,2005,117,734-738,以及Y.Schaerli,R.C.Wootton,T.Robinson,V.Stein,C.Dunsby,M.A.A.Neil,P.M.W.French,A.J.deMello,C.Abell和F.Hollfelder,Anal.Chem.,2009,81,302-306,其各自全部通过参考引入。可在液滴的尺度上控制的其它反应参数包括:试剂的量、混合速率(通过分散或者通过微流控混合器辅助)、停留时间、和与后处理步骤有关的另外的参数(例如UV曝光时间、结晶化温度等)。参见D.J.Han,J.H.Jung,J.S.Choi,Y.T.Kim和T.S.Seo,LabChip,2013,13,4006-4010,G.T.N.Khalid,M.A.Neves,T.Kuroiwa,M.Nakajima,K.Uemura,S.Ichikawa和I.Kobayashi,Adv.DrugDeliveryRev.,2013,65,1626-1663,以及E.Chan,A.Alivisatos和R.Mathies,J.Am.Chem.Soc.,2005,127,13854-13861,其各自全部通过参考引入。试剂的内在的低消耗和对于液滴环境条件的增强的控制保持使得实现化学和生物实验室的高通量筛选的希望。例如,基于液滴的微流控学已被用于分子分析方面的研究、以及其中可以较小的量消耗有价值的试剂的单细胞研究。参见J.Hong,J.B.Edel和A.J.deMello,DrugDiscoveryToday,2009,14,134-146;S.-Y.Teh,R.Lin,L.-H.Hung和A.P.Lee,LabChip,2008,8,198;以及M.T.Guo,A.Rotem,J.A.Heyman和D.A.Weitz,LabChip,2012,12,2146-2155,其各自全部通过参考引入。由于反应被限制在微小的量,因此当关注安全性时,还可以低的风险操控反应性试剂和产物。由于液滴微流控学所提供的所有益处,在各种领域中复杂反应动力学的研究和经设计的颗粒的合成已经是可行的。通过该技术设计和合成的颗粒的实例包括:聚合物颗粒,17,18微胶囊,纳米颗粒,量子点,光子晶体等。参见M.Seo,Z.Nie,S.Xu,M.Mok,P.C.Lewis,R.Graham和E.Kumacheva,Langmuir,2005,21,11614-11622;J.I.Park,A.Saffari,S.Kumar,A.Günther和E.Kumacheva,Annu.Rev.Mater.Res.,2010,40,415-443;R.K.Shah,H.C.Shum,A.C.Rowat,D.Lee,J.Agresti,A.S.Utada,L.-Y.Chu,J.-W.Kim,A.Fernandez-Nieves,C.J.Martinez和D.A.Weitz,Mater.Today,2008,11,18-27;W.J.Duncanson,T.Lin,A.R.Abate,S.Seiffert,R.K.Shah和D.A.Weitz,LabChip,2012,12,2135-2145;K.-S.Huang,K.Lu,C.-S.Yeh,S.-R.Chung,C.-H.Lin,C.-H.Yang和Y.-S.Dong,J.ControlledRelease,2009,137,15-19;C.H.Yang,K.S.Huang,Y.S.Lin,K.Lu,C.C.Tzeng,E.C.Wang,C.H.Lin,W.Y.Hsu和J.Y.Chang,LabChip,2009,9,961-965;S.A.Khan和S.Duraiswamy,LabChip,2012,12,1807-1812;S.Duraiswamy和S.A.Khan,Small,2009,5,2828-2834;A.M.Nightingale和J.C.deMello,ChemPhysChem,2009,10,2612-2614;以及Y.Zhao,X.Zhao,J.Hu,M.Xu,W.Zhao,L.Sun,C.Zhu,H.Xu和Z.Gu,Adv.Mater.,2008,21,569-572,其各自全部通过参考引入。为了产生这些微反应器,使用微流控液滴发生器(MFDG)。不同类型的MFDG和它们的特性总结在别处。参见例如,C.-X.Zhao,Adv.DrugDeliveryRev.,2013,65,1420-1446;R.K.Shah,H.C.Shum,A.C.Rowat,D.Lee,J.Agresti,A.S.Utada,L.-Y.Chu,J.-W.Kim,A.Fernandez-Nieves,C.J.Martinez和D.A.Weitz,Mater.Today,2008,11,18-27;J.-T.Wang,J.Wang和J.-J.Han,Small,2011,7,1728-1754;以及G.T.I.Kobayashi和M.Nakajima,Microfluid.Nanofluid.,2012,13,151-178,其各自全部通过参考引入。典型的MFDG是将两种不混溶的流体一起带到一个位置的一组微通道。在该节点(junction)中,两种液体的粘性力和界面张力之间的相互作用导致液滴形成。这些器件的产物的分布可通过它们的变异系数(Cv)度量,变异系数(Cv)定义为样品的标准偏差和平均直径之间的比率。当所述分布足够窄(Cv≤5%)时,所述乳液被称为单分散的。参见A.Jillavenkatesa,S.J.Dapkunas和L.-S.H.Lum,ParticleSzieCharacterization,Washington,2001,其全部通过参考引入。尽管已经展示了在液滴微流控学方面的许多进步,但是与这些研究有关的低容量生产能力已经阻碍了它们在工业中的采用。单个MFDG的典型的制造速率为大约1-10mL/h的液滴,而工业应用经常要求高出若干数量级的制造速率。参见T.Nisisako,T.Ando和T.Hatsuzawa,LabChip,2012,12,3426-3435,其全部通过参考引入。该缺点已使得液滴微流控学技术仅对于高附加值的工业例如药物、食品、精细化学、和化妆品是有吸引力的。参见C.Haber,LabChip,2006,6,1118-1121,G.M.Whitesides,Nature,2006,442,368-373,G.Muschiolik,Curr.Opin.ColloidInterfaceSci.,2007,12,213-220,以及O.Skurtys和J.M.Aguilera,FoodBiophysics,2007,3,1-15,其各自全部通过参考引入。用于增加液滴的总产量和基于液滴的微流控应用的可能的解决方案是并行化,其由将具有共享的输入端的同时工作的单独的MFDG数量提高(number-up)组成。目前在工业中,存在若干种乳液形式的液滴产生方法。参见M.F.Edwards,N.Harnby和A.W.Nienow,MixingintheProcessIndustries,Butterworth-Heinemann,2ndedn.1992,以及P.Walstra,Chem.Eng.Sci.,1993,48,333-349,其各自全部通过参考引入。常规的乳化技术在容器中使用两种不混溶的相的连续的高剪切混合以导致乳液的间歇制造。这些方法的实例为:高速掺合机、胶体磨机、高压均化器、和超声均化器。参见D.J.McClements,FoodEmulsions:Principles,Practice,andTechniques,CRCPressLLC,1999,以及S.M.Joscelyne和G.J.Membr.Sci.,2000,169,107-117,其各自全部通过参考引入。它们典型地以宽的尺寸分布(Cv~30%)和大约100-20,000L/h的制造速率制造在0.1-100μm直径范围内的液滴。膜乳化是第二种类型的乳化技术,其中分散相被压力驱动通过控制尺寸的多孔膜进入连续相中。参见R.A.Williams,S.J.Peng,D.A.Wheeler,N.C.Morley,D.Taylor,M.Whalley和D.W.Houldsworth,Chem.Eng.Res.Des.,1998,76,902-910,以及T.Nakashima,M.Shimizu和M.Kukizaki,Adv.DrugDeliveryRev.,2000,45,47-56,其各自全部通过参考引入。液滴的尺寸和尺寸分布强烈地依赖于膜的孔尺寸。典型地,液滴尺寸范围在0.1到10μm直径之间,变异系数为10-20%且制造速率为15-300L/h。类似的方法是所谓的微通道乳化,其利用具有微制作的通道或狭缝的基材代替膜中的孔。参见I.Kobayashi,Y.Wada,K.Uemura和M.Nakajima,Microfluid.Nanofluid.,2010,8,255-262,I.Kobayashi,M.A.Neves,Y.Wada,K.Uemura和M.Nakajima,GreenProcessesSynth.,2012,1,353-362,其各自全部通过参考引入。该技术容许窄得多的尺寸分布(Cv<5%),但处于较低的制造容量。这样的一个实例是Kobayashi等的工作,报道了1.4L/h的制造速率。在绝缘体晶片上的硅上深反应离子蚀刻微洞。然后将微制作的结构放置在两个加压的腔室之间并且与膜乳化的情况相比,分散相通过微洞流动到连续相中。表1.微流控乳液发生器技术的总结*参见T.Nisisako,T.Ando和T.Hatsuzawa,LabChip,2012,12,3426-3435(“Nisisako”);W.Li,J.Greener,D.Voicu和E.Kumacheva,LabChip,2009,9,2715(“Li”);M.B.Romanowsky,A.R.Abate,A.Rotem,C.Holtze和D.A.Weitz,LabChip,2012,12,802(“Romanowsky”);M.Muluneh和D.Issadore,LabChip,2013,13,4750-4754(“Muluneh”);G.Tetradis-Meris,D.Rossetti,C.PulidodeTorres,R.Cao,G.Lian和R.Janes,Ind.Eng.Chem.Res.,2009,48,8881-8889(“Tetradis-Meris”);Y.Zeng,R.Novak,J.Shuga,M.T.Smith和R.A.Mathies,Anal.Chem.,2010,82,3183-3190,(“Zeng”);J.Guzowski,P.M.Korczyk,S.Jakiela和P.Garstecki,LabChip,2011,11,3593-3595(“Guzowski”);R.Dangla,S.C.Kayi和C.N.Baroud,Proc.Natl.Acad.Sci.U.S.A.,2013,110,853-858(“Dangla-PNAS”);R.Dangla和C.N.Baroud,ProductionofMonodisperseBulkEmulsionsinaBeakerUsingaNovelMicrofluidicDevice,Freiburg,2013,pp.83-85(“Dangla-Freiburg”),其各自全部通过参考引入。微流控乳液发生器技术的总结参见表1。Dangla等最近介绍了用于产生单分散的乳液的微通道乳化系统的另一变型。在该工作中,液滴形成通过微通道中的受限梯度调解。这些通道在一个末端具有锥形的壁以产生具有小的倾斜角的液滴产生喷嘴。在该系统中,液滴形成是相对慢的,因为它不依赖于流体流动,而是依赖于这些喷嘴的几何结构(受限)。尽管256个喷嘴被并行化,但是最大制造速率为约~3.6mL/h。尽管这些方法的一些制造单分散的液滴,但是它们不能充分地引入液滴微流控的优点的全部。平行MFDG乳化器件在所有时候(即在微通道内部)保持对液滴的控制并且保持由单个MFDG系统所给予的其它优点。由于平行系统将若干个MFDG连接在器件中,因此在相邻的器件之间发生复杂的流体机械耦合。串扰和许多其它因素可使系统失去平衡并且产生多分散的产物。这些变动来源的一些包括:依赖于通道包含的液滴的数量的液压阻力变动,液滴形成中固有的压力变动(在液滴夹断(pinchoff)期间的压力变化)、通道之间的制作差异、泵送中的不规则性、非均匀的装载(负载)、气泡和在特殊通道中俘获的碎屑等。参见W.Li,J.Greener,D.Voicu和E.Kumacheva,LabChip,2009,9,2715;P.Parthiban和S.A.Khan,Biomicrofluidics,2013,7,044123;P.Parthiban和S.A.Khan,LabChip,2012,12,582-588;C.N.Baroud,F.Gallaire和R.Dangla,LabChip,2010,10,2032-2045;G.Tetradis-Meris,D.Rossetti,C.PulidodeTorres,R.Cao,G.Lian和R.Janes,Ind.Eng.Chem.Res.,2009,48,8881-8889;以及T.Ward,M.Faivre,M.Abkarian和H.A.Stone,Electrophoresis,2005,26,3716-3724,其各自全部通过参考引入。以微流控芯片展示出单分散的O/W乳液(Cv=2.2%)的高容量制造的平行MFDG乳化器件由Nisisako等提出。参见T.Nisisako,T.Ando和T.Hatsuzawa,LabChip,2012,12,3426-3435,其全部通过参考引入。对于在一起工作的144个MFDG的阵列,该系统以180mL/h的最大流动速率制造乳液。所述芯片是在合成二氧化硅玻璃上使用光刻法和深反应离子蚀刻制造的。该制作过程制造仅一个发生器层且需要使用由不锈钢块机械加工出的在外部制作的液压歧管。尽管环形的歧管代表用于使平行MFDG去耦(decouple)的解决方案,但是它限制可扩展性(scalability)的程度。要求N+1个圆柱形块的组件能够连接N个共轴的环形的通道,由此将该系统限制到相对低数量的仅对一个发生器层进行进料的环形的通道。而且,该环形的分布网络被横向进料且由于管道和各环形的通道之间的非对称连接,存在跨越器件的流动变动(即存在更接近于接头的MFDG)。软光刻法也已被用于使用聚二甲基硅氧烷(PDMS)制作平行MFDG乳化器件。参见X.-H.Ji,N.-G.Zhang,W.Cheng,F.Guo,W.Liu,S.-S.Guo,Z.-K.He和X.-Z.Zhao,J.Mater.Chem.,2011,21,13380-13387,以及M.B.Romanowsky,A.R.Abate,A.Rotem,C.Holtze和D.A.Weitz,LabChip,2012,12,802,其各自全部通过参考引入。该制作技术还要求使用洁净室设备以产生高长径比的主模,因此它的成本仍是高的。使用该制作方法,Li等制作了用于以50g/h的制造速率进行聚合物颗粒的UV合成的多模态微流控器件。参见W.Li,J.Greener,D.Voicu和E.Kumacheva,LabChip,2009,9,2715,其全部通过参考引入。在该工作中,16个通道的八个单独的模块各自平行地运行。这些模块是需要大量的外部接头和管道的独立的芯片,这限制更高规模的并行化。通常,先前的并行化研究主要努力钻研仅用于阵列扩展的第二维度。然而,如果期望真的并行化,则也必须研究三维扩展。已以PDMS展示了三维并行化,然而仅展示了三层的堆形式的15个MFDG,且由于它们的制作过程,出于以下原因,按比例增加MFDG的数量是有挑战性的:堆叠层之间的互连通孔是用打孔器手工制作的(即易于出错的过程),且橡胶状材料例如PDMS中的可再现的对准是难以实现的。存在其它类型的处理在过去已被并行化的气-液微反应器的技术。例如,使用硅展示了在三角形通道中产生气-液分段流动的多层分布器件。N.deMas,A.Günther,T.Kraus,M.A.Schmidt和K.F.Jensen,Ind.Eng.Chem.Res.,2005,44,8997-9013,其全部通过参考引入。类似地,具有模块化流动分布58的气-液系统的制造容量对于以Taylor流动制度运行且产生具有在1.5-4.5μL范围内的体积的液体段的器件已实现高达9L/h的流动速率。微流控液滴发生器(“MFDG”)可用作具有受控的尺寸和内部组成的单分散的单乳液和混合乳液的制造器件。乳液滴可用作通用模板来设计多种具有一定性质的颗粒。然而,对于在工业中的实际应用,MFDG受其生产能力限制。微流控液滴发生器的典型产量为大约10g/h或小于100kg/年,而工业要求典型地为大约若干吨一年。许多公司一直存在开发可将乳液的总产量增加到工业相关规模的微流控解决方案的兴趣。为了具有大规模制造,通过MFDG的平行的数量提高的设计来增加生产能力而不增加液压泵和专门的设备的数量是重要的。本文中公开具有低至~6%的变异系数的可堆叠的微流控乳液发生器的设计、制作和表征。用于单乳液的大规模制造的多层微流控并行化芯片可包括用于大规模并行化的另一维度和分布网络在所述芯片内的充分(完全)集成,其可固有地扩展到甚至更高的容量。该器件显示在文献中对于具有液-液液滴发生器的同时运行的微流控器件所报道的最高的生产能力。在包含以圆形阵列组织的四个各自具有128个发生器的产生层的器件中可产生分散相的高达1L/h的制造速率。这些特别的器件的分散性的最小值出现在每层120mL/h。这些层可经由通孔互连且用设计的分形分布网络进行进料。可在聚(甲基丙烯酸甲酯)(PMMA)片材上铣削(mill)出所提出的层并且可将堆热压缩结合以产生具有高密度的发生器和集成的分布网络的多层器件。堆叠多层的效果显示,与向所述堆添加更多的层相比,制作精度对乳液的分散性具有更大的影响。通过堆叠流体分布层和液滴产生层,多层微流控器件同时运行平行的微流控液滴产生单元。形成堆的不同的层可利用通孔和机械压缩彼此对准。这些层可通过在基材上雕刻微流控通道而形成。所述器件可包括负责将流体均匀地进料到每个平行的液滴产生单元的集成的分布网络。构成所述分布网络的通道可使用分形图案布置,所述分形图案继而可以按称作瓣的功能性子单元组织。制作过程可在任何高精度CNC铣床中容易地实施且不需要使用洁净室设备。该过程是低成本的且使得实现多层微流控器件的快速成型(原型制造,prototyping)。该制作方法的另一优点是与弹性体例如PDMS相比,聚(甲基丙烯酸甲酯)(PMMA)的更大的刚性。这些芯片的刚性壁使微通道的液压容(hydrauliccapacitance)最小化且改善对于流动变化的瞬态响应。该器件可经受高达7.5巴的压力。还使用金属销和通孔精确地实现可再现的对准(<5μm)。在一些实施方式中,分布网络可充分地集成在所述微流控芯片内。在一些另外的实施方式中,不同的类型的分布网络可用在并行化器件中;可为呈共轴的环形的构造的树状、梯状、或二者的组合。分形树状分布网络可使耦合最小化。MFDG的组可以按内在地独立的组(瓣)组织,且相邻的MFDG在最低的分等级的水平(即MFDG节点)处断开。对于器件公开在不同的总的流速下向堆添加额外的乳液产生层对液滴尺寸分布的影响。分散性未显示出与堆中的层的数量(例如1-4个产生层)的增加的直接关联。然而,由于使两个相都通过相同的分布网络和连接的通孔,因此当堆叠更多的层时,对于更大的流动速率,预期歧管阻力的增加。树状分布网络的优点是如下事实:层中的所有单独的MFDG从流体输入端起接收相同的压力降,因此跨越器件,产生条件是均匀的。使用较薄的材料片或较大直径的通孔可使产生层之间的压力降的差异最小化。在这些器件中,铣削过程的制作可变性可最大地贡献于液滴尺寸分布的分散性且更精确的图案化技术可显著地改善乳液分散性。集中的树状分形分布网络对于改善液滴产生过程显示出最好的结果,因为其构造促进两相的均匀的装载和没有气泡的稳态性能。此外,器件的剩余部分的MFDG的组的去耦通过如下展示:将它们以瓣状结构布置。当使一个或多个构成瓣失活时,测试具有256个通道和四个瓣的双层并行化芯片。运行部分(分区,section)的变异系数和液滴尺寸保持当MFDG以相当的流动速率运行时的类似的值。提出颗粒结晶化作为可得益于这些平行的MFDG器件的药物应用。由通过这些微流控器件产生的乳液,可成功地制造甘氨酸球形附聚物。该实例显示,通过提供处于升/小时的生产能力(其为最终按比例放大过程中的关键要求)的受控制的微流控乳化,所述器件可大大促进例如活性药物成分(“API”)的方法向工业上相关的制造规模的转化。该乳液发生器连同高生产能力膜蒸发的直接组合可转化成工业应用。多层微流控器件可配备MFDG的高容量并行化。参见例如T.Nisisakoetal.,LabonaChip,pp.3426-3435,2012年6月,其全部通过参考引入。然而,Nisisako仅制造了一个层且需要使用在外部制作的分布网络,这限制可扩展性的程度和MFDG的流动分布,这归因于管道和各环形的通道之间的非对称连接。分布网络可包括在分布层中且通过将所述层彼此连接的通孔雕刻的一组分布通道。使用不同的方法,分布网络可集成在设计台(designstage)内部且与芯片整体地制作。另外,可使用薄层(1mm)保持系统紧凑且可在单层上制造分布网络线路以保持流动跨越盘的均匀分布。分布网络集成在芯片内部且其中轴对称输入端位于盘的中心可产生液相的均匀装载且可避免在进料线路中俘获气泡。通过减少不同的通道中的流动变动,该优点对芯片的稳定性做贡献。轴对称输入端可为从所述器件的表面能到达的。利用该方法,多层微流控器件可包括至少两个层,其中至少一个层包括刚性聚合物,其中所述两个层通过通孔连接,其中各层包括分形图案,和其中各层包括与所述器件的通道连接以控制流体的流动的分布网络。所述两个层可为平行的。可设计和制作多层微流控器件用于单分散的单乳液的大规模制造,从而以对于单芯片所报道的最高速率(300mL/h)制造液滴。液滴的尺寸可取决于通道的尺寸、流动速率和液体的性质。例如,使用水和十二烷,可获得l75μm的平均直径(Cv=0.12)。在另一实例中,可获得225μm的平均液滴直径和(Cv=0.09)。图1A显示具有256个通道的微流控芯片(110mm直径),其包括2个堆叠的各自128个通道的层,以聚(甲基丙烯酸甲酯)(PMMA)制作,其中分布网络和分布网络也集成在器件上。图1B显示形成用于2种流体的器件的层的实例设计,所述器件具有用于供应的油和水的2个分布网络以及2个液滴产生层。可使用将分布网络集成在芯片内的低成本过程配备256个交叉节点(cross-junction)微流控液滴发生器(MFDG)的并行化并且将其布置在两个层中。该设计和制作方法是灵活的,容许制造具有定制的平均直径的乳液的系统和比其它方法大的生产能力。所述通道可具有不同的几何结构,且所述几何结构可影响液滴形成。宽且薄的(浅的,shallow)长方形的通道横截面几何结构(例如,长方形的285×61μm)相对于其它几何结构(即更窄的长方形的和梯形的几何结构)是优选的,因为随着改变水/油流动速率比,它显示出最低的在液滴尺寸方面的可变性。该趋势存在于在不同的总的流动速率下进行的研究中,使得薄的长方形的几何结构最适合用于并行化。在高的总流速(即300μl/分钟)下,毛细管数较大,该行为比在低的流速(即30μl/分钟)下更明显。该行为可归因于发生器中的侧壁的降低的影响。图2显示形成用于2种流体的器件的层的实例设计,所述器件具有用于供应的油和水的2个分布网络以及2个液滴产生层,包括五个层的堆。底部层各自包含128个MFDG,其用通孔连接。油相添加在顶部,而水相从底部输入。二者都被集中以提供均匀的分布。可引入更多的层以堆叠更大数量的微流控液滴发生器,提供高程度的设计灵活性。系统可具有分形的图案的任意倍数的量的MFDG。例如,它可具有128、256、512、或1024个MFDG、或128个MFDG的任意倍数。底部层各自可包含128个通道的阵列,其通过通孔互连。在堆叠的MFDG层的顶部上,可覆盖另外两层的分形分布网络(每个相一个)。通过集成这些网络和连接MFDG的通孔,可配备分布网络在芯片内的三维并行化和集成。MFDG的实例已被报道。参见例如E.Chanetal.,JAmChernSoc,vol.127,no.40,pp.13854-13861,2005,其全部通过参考引入。当用于制备微流控器件时,材料的实例为聚(甲基丙烯酸甲酯)(PMMA)、环状烯烃共聚物(COC)、环状烯烃聚合物(COP)、聚碳酸酯(PC)、聚对苯二甲酸乙二醇酯(PET)、聚二甲基硅氧烷(PDMS)、玻璃或硅。在一些实施方式中,刚性成分可具有对于系统的堆对准、瞬态响应和稳定性的优点。PMMA刚度为大约1.8-3.2GPa,而COC为(2.6-3.2GPa),玻璃为(50-90GPa)且硅为(130-185GPa),因此由它们制成的器件与由其杨氏模量为大约几百千帕的橡胶状材料(即PDMS杨氏模量为360-870KPa)制成的器件相比在经历弹性变形之前可抵抗更大的力/压力。参见表2。表2.材料和杨氏模量刚性材料杨氏模量聚(甲基丙烯酸甲酯)(PMMA)1.8-3.2GPa环状烯烃共聚物(COC)2.6-3.2GPa环状烯烃聚合物(COP)1.7-3.0GPa聚碳酸酯(PC)2.0-2.4GPa聚对苯二甲酸乙二醇酯(PET)2.8-3.1GPa偏离化学计量的硫醇-烯(OSTE)0.25-2.0GPa玻璃50-90GPa硅130-185GPa例如,可使用软光刻法来制作高生产能力聚二甲基硅氧烷(PDMS)芯片。参见例如M.B.Romanowskyetal.,LabonaChip,vol.12,no.4,p.802,2012;W.Li,etal.,LabonaChip,vol.9,no.18,p.2715,2009,其各自全部通过参考引入。该制作技术要求使用洁净室设备来产生高的长径比的主模且因此制作成本增加。与在其中可使用销和通孔来对准(<5μm)的刚性材料例如PMMA中相比,在橡胶状材料例如PDMS中的可再现对准可更难以实现。PMMA的较大的刚度还使液压容最小化且改善瞬态响应。PMMA、COC、玻璃或硅相对于PDMS的另一重要优点是它们对于化学品的低的吸附和吸收以及它们的低的气体渗透性。可使用PMMA-SU8基材来产生高生产能力微流控器件。参见例如G.Tetradis-Merisetal.,Ind.Eng.Chern.Res.,vol.48,no.19,pp.8881-8889,Oct.2009,其全部通过参考引入。Tetradis-Meris还报道了关于从分布网络到并行化的器件网络中的液体分布,梯型布局相对于树型布置是优选的。出处同上。然而,对于如下的多层微流控器件,该结果是相反的:所述多层微流控器件包括至少两个层,其中至少一个层包括刚性聚合物,其中所述两个层通过通孔连接,其中各层包括分形图案,和其中各层包括与所述器件的通道连接以控制流体的流动的分布网络。分形图案包括具有建立于其自身上的特定类型的结构的分形几何结构。分形图案可包括若干代的逐渐增加或减小的等级。所述分形图案的密度随着各重复水平而增加。多层微流控器件可具有拥有高的密度的分形图案。所述分形图案可包括至少128个通道、至少256个通道、至少512个通道、或至少1024个通道。图3显示组装的堆。图4显示盖层或顶部层。该层封闭连续相分布网络的通道。图5显示连续相分布网络。在该图中,各通道逐渐地再分成两个通道;分形的分布网络具有在中心的单个入口。连续的液体从堆的顶部且从中心进料到盘的边缘。图6显示分散相分布网络。在该图中,各通道逐渐地再分成两个通道;分形的分布网络具有在中心的单个入口。待分散的液体从堆的底部且从中心进料到盘的边缘。图7显示发生器的第一层、或底部层。该底部层包括128个发生器。通道的宽度从250μm(对于青色交叉物)到2mm(蓝灰色)改变。由于通道的尺寸,可装配128个微流控液滴发生器。利用更窄的通道,可用分布网络装配或供应任何可被分形的数量。例如,所述数量可为p×m×2n,其中p为代表瓣的数量的整数,m为代表相同的产生层的数量的整数且n为代表以极阵列布置的分形支化发生器的水平的数量的整数。图8显示发生器的第二层。该层可与发生器的第一层相同。该层对于各液滴发生器具有两个连接通孔(例如:500μm直径)以将它们与另外的层连通,使分布网络集成。可多次制作该层以将发生器的数量按比例增加。图9显示形成器件的不同的层且描述如何形成堆。底部层为发生器的第一层且堆的顶部为盖层。堆叠的盘可具有110mm的直径。所述器件可包括任意两种将它们自己贡献于液滴形成的不混溶的流体。一种流体可为“分散相”,即转变成液滴的流体。例如,水、或水溶液(在水中的甘氨酸)可用作流体。另外的流体可为“连续相”,其为剪切或切割液滴并且运送液滴的相。例如,可使用具有表面活性剂的矿物油或十二烷作为流体。在一个实例中,所述器件可包括水分布层。在另一实例中,所述器件可包括油分布层。所述器件可包括覆盖层。各层的厚度可小于几毫米,例如小于1mm。发生器的阵列的堆叠可集成在单个芯片中。三维微流控器件可包括连接乳液产生层的堆的分布网络。所述分布网络可包括至少两个分布层,每一个至少包括流体通道的分形图案和将它们与其它堆层彼此互连的通孔。所述产生层的数量可为任意整数,优选1-100,优选1-50,优选1-25,且优选1-10。所述产生层可通过微流控液滴发生器的极阵列形成。用于制备乳液的方法包括使用包括至少两个层的多层微流控器件,其中至少一个层包括刚性聚合物,其中所述两个层通过通孔连接,其中各层包括分形图案,和其中各层包括与所述器件的通道连接以控制流体的流动的分布网络。乳液可为单分散的。乳液的制造速率可为至少300mL/h。瓣组织流动聚焦并行化的MFDG可包括~250μm宽×~100μm深的十字形收缩部(constriction),其与下游的更宽且更深的通道(400μm宽×300μm深)连接(图18)。先前模拟了宽且薄的长方形的几何结构(参见D.Conchouso,E.Rawashdeh,D.Castro,A.Arevalo和I.G.Foulds,OptimizedChannelGeometryofaFlow-FocusingDropletGeneratorforParallelization,Rotterdam,2013,其全部通过参考引入)且其证明与具有等效的水力直径的其它几何结构相比对流动变化较不敏感,因此使得其适合用于平行系统。MFDG的大规模并行化可包括堆叠方程p×m×2n的层,其中p为代表瓣的数量的整数,m为代表相同的产生层的数量的整数且n为代表以极阵列布置的分形支化发生器的水平的数量的整数。器件可包括一个、两个、或四个、更多各自包含128个MFDG的产生层。通过使用具有更高的特征分辨率的制作工艺例如光刻法或者通过增加器件的总面积,每层更大数量的MFDG是可能的。使用用于并行化的第三维度带来相对于二维扩展的重要优点。多层器件的各层可具有依赖于通道的尺寸的任意厚度。所述层可具有为了有效的分布网络和紧凑的系统设计而采用期望尺寸的通道所需要的最小厚度以用于MFDG的高密度包装。并行化芯片可由四个基础层:盖层、油分布网络、水分布网络、和液滴产生层构成。可向堆引入额外的液滴产生层用于MFDG的进一步按比例增加(图14)。不同的层可全部通过与器件一起制作的通孔彼此连接且容许分布网络在芯片内的集成。测试了对于分布层的若干设计:树状分形分布网络、环形的分布网络、和两者的组合。仅第一种证明是可靠的结构且对于该并行化芯片提供最好的结果。对于图2和14中描绘的树状分形分布网络,两种液体的输入端口都可在芯片的顶部处和底部上轴对称地放置于堆的中心,以在盘中的所有方向上保持从液体源到MFDG的相同的通道长度。替代地,输入端口可放置在任意位置处且然后导向中间用于初始分布。两种液体都从盘的中心流动到边缘,然后从顶部前进到下部层。如果需要额外的相输入端,则每个输入端必须添加两个额外的层以保持该集中的分布(即一个用于分布且一个从输入端到盘的中心)。平行MFDG的耦合通过分布网络发生且发生在系统的输出端处。设计可包括将MFDG的极阵列以四个组或“瓣”进行组织,所述组或“瓣”可在相同的芯片内作为独立的液滴产生块处理,每一个具有其自己的设计的输出端(图14)。至关紧要地,这些瓣仅在其中耦合和阻抗是最小的最高水平的层次(邻近于输入端口)处彼此连接。由于此,关闭这些部分(瓣)之一对于其它的具有很小影响到没有影响,且因此对于输出产量具有很小影响到没有影响。在图14中显示的器件(其中瓣以红色加亮的盘堆)的情况中,形成2n个MFDG的瓣,各瓣具有32个MFDG/层。图23显示具有6个瓣、其中各瓣具有8个发生器的器件。当使用平行系统工作时的主要关注点是堵塞的潜在可能性,尤其是当对付包含树状分布网络的系统时,因为它们被报道对于无规的阻力变化具有较大的敏感性。在所提出的瓣状结构中,分享公共输出端的MFDG的组在相同的芯片内充当独立的单元。如果一个部分变堵塞且其产物突然变成多分散的,则可通过如下将受影响的瓣关闭:关闭其两个输入端分支或一个输入端分支以及输出端。关闭的瓣的通道阻力变得无穷大且通过调节输入端压力以维持每个MDFG的初始流速,其它产物可仍然保持它们的低的分散性和尺寸。具有该类型的瓣结构的平行系统可然后在具有失活的部分的情况下工作并且避免总的制造停止。图15显示关闭堵塞的部分的影响,与在所有瓣都起作用的情况下的“256-器件I”的产物相比,当将“256-器件I”的瓣的一个、两个或三个完全关闭时,测量由“256-器件I”产生的产物的尺寸分布。结果显示,通过调节到正确的压力,可保持类似的液滴尺寸和分散性,这证明瓣结构的优点。作为具有弱的相互影响的独立的功能单元,瓣可被失活和再活化,如果提供恰当的阀的话。还可实施单独的传感器以监控瓣运行。使用单独的传感器使得实现这样的系统:其中,可关闭器件的部分(或瓣)的一些之一,同时保持其它部分(或瓣)工作,伴随着很小的变化到没有变化。用于检测堵塞的瓣(部分)的可能的方法的一些可为监控器件中所有的瓣的输入端或输出端以查看它们是否全都没有变化地运行。可帮助检测最终产物中的变化且可用作用于关闭瓣的反馈系统的传感器可包括RF结构、电容传感器、图像处理(光学检查)、阻抗测量、流动传感器、pH传感器、光散射传感器(例如激光器)、界面传感器、和粘度传感器。预期在具有不同数量的产生层的器件中看到该行为且该行为不依赖于每层的瓣的数量。值得注意的是,这些瓣仅在其中耦合和阻抗是最小的最高水平的层次(邻近于输入端口)处彼此连接。由于此,关闭这些瓣之一对于其它瓣具有很小影响到没有影响,且因此对于生产量具有很小影响到没有影响。后液滴产生处理通过两个不混溶的相的剪切力进行的乳液的间歇处理已在工业中使用了长的时间。然而,微流控系统相对于其间歇制造对应物提供优点。例如,微流控学方法可控制试剂的精确的量、混合速率、停留时间、环境条件和这些乳液以单液滴的粒度的后处理。这些方法中的一些已被讨论。参见例如G.T.Vladisavljevicetal.,Industriallab-on-a-chip:Design,applicationsandscale-upfordrugdiscoveryanddelivery,AdvancedDrugDeliveryReviews,Jul.2013;C.Holtze,J.Phys.D:Appl.Phys.,vol.46,no.11,p.114008,Feb.2013;C.X.Zhao,Multiphaseflowmicrofluidicsfortheproductionofsingleormultipleemulsionsfordrugdelivery,AdvancedDrugDeliveryReviews,2013;Tetradis-Mairisetal.MethodandapparatusforproducingmicroparticlesWO2010025988A1;Nisisakoetal.Apparatusforproducingmicroliquiddrops,EP2594332A1;Kumachevaetal.Multiplecontinuousmicrofluidicreactorsforthescaledupsynthesisofgelorpolymerparticles,WO2008148200A1;MarkBRomanowskyetal.Scale-upofmicrofluidicdevices,WO2010104597A2,其各自全部通过参考引入。微流控系统可包括通过封闭的弯曲表面例如管、漏斗或圆柱体实施的后液滴产生处理步骤,用于任何种类的颗粒的高容量的连续制造。所述后处理步骤可为可修改液滴的结构和组成的任何过程。例如,该步骤可包括用于加快材料的合成的加热机构、用于使UV敏感性颗粒或其它材料聚合的UV暴露区、等离子体处理、通过不同的气体气氛例如反应性气体、放电、冷冻、或者可将液滴转变成颗粒的任何其它处理。所述后处理步骤可包括形成乳液的连续的流,其可在管或漏斗的封闭的弯曲表面的玻璃壁上滑下(图16、17、21、和22)。图16显示用于微流控液滴发生器的大规模并行化的实验装置。所述发生器的四个输出端可排列在玻璃漏斗或管周围并且它们的通过物料(throughput)在管或漏斗的壁上滑动且润湿柱的横截面的整个周边。漏斗或管可用作用于后处理步骤例如加热步骤的延长的直径(横断面,diameter)。图21显示用于在开放的圆形表面中的后处理的实验装置。图17显示用于微流控液滴发生器的大规模并行化的实验装置。所述发生器的四个输出端可排列在玻璃漏斗或管周围并且它们的通过物料在管或漏斗的壁上滑动且润湿柱的整个周边。漏斗或管可用作用于后处理步骤例如UV暴露的延长的直径。图22显示用于在开放的圆形表面中的UV后处理的实验装置。用于制备乳液的方法可包括将流体从混合器供应到颗粒固定区或处理区,其具有弯曲表面使得所述流体形成没有侧面边缘的层。用于供应流体的方法可包括加热没有边缘的流体的层。所述区可包括具有弯曲表面的管,其中从输出端供应的液体通过管,接触弯曲表面的壁,且可润湿弯曲表面的整个周边。可将颗粒固定区或处理区暴露于紫外光或加热。用于制备乳液的方法可包括将流体从混合器供应到具有弯曲表面的处理区,使得所述流体形成没有侧面边缘的层。用于处理乳液的系统可包括管和至少一个将乳液供应通过所述管的输出端。所述系统可包括至少一个供应流体的输出端;所述系统可包括至少四个供应流体的输出端。输出端可包括排列在封闭的弯曲表面周围的多个输出端。所述流体可润湿所述管的整个周边。所述系统可连接到多层微流控器件。所述系统可加热没有边缘的流体的层。所述后处理步骤可为对于将药物微晶的微流控制造按比例放大到工业相关规模的主要步骤。器件和系统的优点对于这样的多层微流控器件,存在优点:所述多层微流控器件包括至少两个层,其中至少一个层包括刚性材料,其中两个层通过通孔连接,其中各层包括分形图案,和其中各层包括与器件的通道连接以控制流体的流动的分布网络。所述刚性材料可包括聚合物、玻璃、或硅。该器件的优点包括:它可以刚性材料(PMMA)制造。这对制作过程中MDG的适当排列做贡献且促进器件的堆叠。它还降低由于当施加压力变化时器件的低的变形所致的液压容,通过这样做,它可显示出更好的且更快的瞬态响应。也可使用玻璃和/或硅或任何聚合物基材。PMMA、COC、COP、PT、PC、玻璃和/或硅相对于PDMS的另一重要优点是它们对化学品的低的吸附和吸收以及它们的低的气体渗透性。另外,液相的轴对称输入端可被集中且可从盘的顶部和底部表面到达,提供流体到液滴发生器的单独的堆的均匀且直接的分布。这导致液体的清洁的且快速的装载且避免俘获不期望的气泡。所述系统可将分布网络充分地集成在微流控芯片内,因此它只需要两个用于以上讨论的不同的相的入口。与之前提供的任何其它设计相比,这提供在设计方面的更大的灵活性和用于大规模堆叠的3D集成。该器件和系统可向256个通道的器件提供在文献中报道的单器件的最大的生产能力(分散相的流动速率FRdp≌300ml/h)。通过在额外的堆叠层中添加更多的微流控液滴发生器阵列,生产能力可进一步改善。增加数量的输出端(4个或更多个)容许控制单分散的乳液的物流并且引导它们形成薄的乳液层,所述薄的乳液层在大直径的漏斗或管之上滑动以应付高级制造和后处理步骤。后处理步骤包括加热、暴露于紫外光等。实施例制作过程由1mm厚的流延PMMA片即在微流控学中通常使用的便宜材料制成多层并行化芯片。本文中提供的计算机数字控制(CNC)微细铣削和热压粘合构成用于三维微流控器件的快速成型的制作方法。微流控通道的直接微细铣削工艺可在任何高精度CNC机床中容易地实施且不需要洁净室设备。而且,已使用范围从热压粘合、微波粘合、低温超声粘合、和通过表面改性的若干种成功的方法展示了便宜的PMMA粘合。参见X.Zhu,G.Liu,Y.Guo和Y.Tian,Microsyst.Technol.,2006,13,403-407;Y.Sun,Y.C.Kwok和N.-T.Nguyen,J.Micromech.Microeng.,2006,16,1681-1688;M.Rahbar,S.Chhina,D.Sameoto和M.Parameswaran,J.Micromech.Microeng.,2009,20,015026;R.J.Holmes,C.McDonagh,J.McLaughlin,S.Mohr,N.J.Goddard和P.R.Fielden,J.Phys.Chem.Solids,2011,72,626-629;S.W.Li,J.H.Xu,Y.J.Wang,Y.C.Lu和G.S.Luo,J.Micromech.Microeng.,2009,19,015035;以及L.Brown,T.Koerner,J.H.Horton和R.D.Oleschuk,LabChip,2006,6,66,其各自全部通过参考引入。MFDG可包括100μm深的十字形收缩部,其与下游的更宽和更深的通道连接。图18显示使用用于制造快速的原型的标准PCB铣床在PMMA上切削的微流控通道的SEM照片。所述十字形收缩部为1000μm长×260μm宽×100μm深。进料管线和输出端为400μm宽×300μm深。可在1mm厚的流延PMMA片上使用LPKFProtoMat-S103PCB绘图机直接机加工芯片。LPKF系统具有±0.5μm的x-y分辨率且装备有深度限定器,取决于基材平面度,所述深度限定器将跨越芯片的深度变动降低到低于±10μm。还对堆叠层之间的所有互连进行CNC钻孔作为同一工艺的部分。使用AmbiosXP-200台阶仪测量通道的表面粗糙度且在十字形的收缩部处的表面粗糙度为~140nm且在分布通道处的表面粗糙度为~350nm,其与所测量的器件制作误差(表3)相比是可忽略的。表3.测试其各自的制作可变性的器件一旦发生器和分布层被铣削,便可然后将层的堆用肥皂水涂刷、清洗和用销对准用于粘合。为了保证没有从铣削工艺留下的残余物阻塞任何通道,目视检查是必要的。然后将所述层的堆使用对准销组装(以进行≤5μm的精确对准)并且使用装配有环境舱的Instron5900-Series热压粘合。然后将所述层的堆使用提供有环境舱的Instron5900-Series在150℃下在压缩应力(12N/cm2)下热粘合45分钟。然后使温度逐渐降低到低于50℃,同时保持压缩应力恒定另外的15分钟。最后,在并行化盘上粘贴世界到芯片(worldtochip)接口(界面,interface)和管道。芯片到世界(chip-to-world)连接机构可包括在顶部层和底部层中。尽管在粘合之后在微通道中不存在明显的变形,但是应注意,盖层可被挤入通道5-10μm。因此,非常薄且宽的通道可通过该粘合过程阻塞。然而,粘合强度被测试为经得住高的压力(~7.5巴),充分高于在器件的装载顺序中通常使用的压力,以消除俘获的气泡。该过程是低成本的且提供以精确的对准在第三维度中并行化的能力。材料为了成像和液滴表征,使用具有2%(重量/重量)的由70%Span-20和30%Span-80(重量/重量)组成的表面活性剂混合物的癸烷(≥99%)作为连续相(CP)。分散相(DP)为具有红色食物色彩的UltrapureMilliporeMilli-Q去离子水(18.3MΩ)的溶液,所述红色食物色彩被添加以增强对比和促进通过图像处理软件对单乳液的表征。参见A.S.Basu,LabChip,2013,13,1892-1901,其全部通过参考引入。颗粒结晶化也使用具有以上描述的相同的表面活性剂含量的十二烷(≥99%)作为CP且使用在室温(22℃)下饱和的甘氨酸(>99%)溶液作为DP实现。该溶液为大约24.4g的甘氨酸含量/100g的去离子水。参见K.Allen,R.J.Davey,E.Ferrari,C.Towler,G.J.Tiddy,M.O.Jones和R.G.Pritchard,Cryst.GrowthDes.,2002,2,523-527,其全部通过参考引入。所有溶液都在各实验之前使用Cole-Parmer注射器过滤器(0.45μm)进行过滤。实验装置实验装置的示意图提供于图13中。将CP和DP两者都装载到独立的容器中,然后连接到ElveflowOB1压力泵以将流体储蓄器中的压力控制在0-2000毫巴的范围内。使用连接到OB1的流量传感器监控流动速率。为了进行实验,将并行化芯片放置在玻璃漏斗上面,所述玻璃漏斗帮助将输出流引导到白色塑料表面用于成像。该表面作为良好的光扩散体工作以促进均匀的照明条件。使用具有流量传感器的ElveflowOB1压力泵将流体储蓄器中的压力控制在0.03-0.7巴的范围内以填充系统且然后将所述系统带到稳态制造。为了实现高生产能力的油包水乳液,连续相为具有2%的由70%Span20和30%Span80构成的表面活性剂的>99%的十二烷的溶液且水相溶液为染色的水之一以及负载了甘氨酸的水之一。对油包染色的水乳液进行成像,如图19中所示,以研究所述乳液的分散性。使用DMV软件研究所述乳液的分散性。参见例如A.S.Basu,"DropletMorphometryandVelocimetry(DMV):Avideoprocessingsoftwarefortime-resolved,label-freetrackingofdropletparameters,"LabonaChip,2013,其全部通过参考引入。图19显示油包染色的水乳液的实例用于容易的可视化。使用具有MPG65mm微镜头的Canon5D照相机对产物进行成像。在测试期间,对于各数据点拍摄平均100张高品质照片(21Mpx)。然后将这些照片转变成AVI视频文件并且通过液滴形态测量学和测速软件(DMV)进行处理。典型地,由~8000个液滴的样品获得实验的有效液滴直径分布,所述~8000个液滴的样品对于非常大的种群代表在统计学上显著的样品。装载顺序和分布网络构造均匀的液体装载在MFDG的并行化中起到最关键的作用之一。装载问题可包括:在非对称分布网络中跨越芯片的压力梯度、改变流量的俘获的气泡、相之一到另外的相中的回流、依赖于流动着的液体的通道阻力的变化、堵塞的通道、和许多其它的。参见G.T.N.Khalid,M.A.Neves,T.Kuroiwa,M.Nakajima,K.Uemura,S.IchikawaandI.Kobayashi,Adv.DrugDeliveryRev.,2013,65,1626-1663,andC.Holtze,J.Phys.D:Appl.Phys.,2013,46,114008,其各自全部通过参考引入。为了使这些问题最小化,对于该高生产能力微流控芯片测试三种不同的构造:共轴的环形的网络、与树状网络组合的环形的网络、和分形树状分布网络(图20)。所有网络构造都是使用类似的装载条件测试的。首先,将油相和水相以高的压力(例如~1000毫巴)推动以清除所有俘获的气泡和确保对所有微流控通道的完全装载。然后,施加逐渐降低的斜线下降(ramp)(-65毫巴/s)并且将压力平稳地降低到50毫巴。在照相机和流量传感器的帮助下通过小的压力变化(1毫巴)完成最后的适当的调整。由于PMMA的透明性,液滴形成的光学检查是可能的,并且容许我们检测系统中的可能的问题。如果注意到不规则性,则以短的脉冲施加高压力(1-2巴)的清洁循环以清除障碍物。与PDMS和另外的弹性材料相比使用PMMA的优点是它的较大的刚度(杨氏模量2.4-3.3GPa),其对具有良好的动态响应和低的液压容的微流控通道做贡献。可对ElveflowOB1压力泵进行编程以自动地进行整个顺序,包括经常需要1-3次的清洁循环。在所有测试的构造中一贯地出现的问题是在MFDG中无规地俘获气泡。在环形的构造的情况下,该问题甚至在若干次高压力清洁循环之后也继续存在,导致不规则的进料和多分散的液滴产生。相反,分形树状网络工作得最好以通过突然的压力变化清洁通道且由于轴对称输入端而显示出流体的均匀装载。该分布网络显示出将MFDG布置成瓣的最好结果,其使得实现关闭芯片的部分而不影响产物,而且其装载响应对芯片的稳定性做贡献且改善产物的分散性。在不同流动条件下的液滴产生进行第一组实验以表征所产生的液滴的尺寸和尺寸分布。对于该部分,使用具有食物色彩的去离子水作为DP。对于包含不同数量的产生层的器件,拍摄所产生的乳液的图像,然后对其进行处理。在保持水/油流动速率比常数1:5的同时,将具有一个(128个MFDG)、两个(256个MFDG)和四个(512个MFDG)产生层的器件在不同的总的流速下进行测试(图12)。对于以固定的总的流动速率和不同的水/油比(1:2、1:5、1:10)运行的具有128和256个MFDG的器件完成的实验未显示出对乳液的尺寸分布的任何显著影响。对于单层,最大生产能力为~300ml/h,对于双层,最大生产能力为~600ml/h,且对于四重层,应预期~1.2L/h的产量。流量传感器能够精确地测量最高达~1L/h。误差棒显示对于~8000个液滴的平均样品尺寸的乳液的标准偏差(图12A)。在所测试的所有器件中,变异系数(图12B)显示类似的U形曲线。在不同的器件之中,双层器件“256-器件I”显示出最小的变异系数(Cv=0.06)。该器件还具有最小的在制作中的标准偏差,这表明在制造可变性和尺寸分布可变性之间的密切关系。在较高数量的产生层下,通过器件的总的流量增加,且因此跨越分布网络的压力降也增加。由于此,需要较高的压力来驱动器件。然而,这看起来对液滴制造不具有影响。由于分散性的变化看起来由制作可变性支配,因此在变异系数和产生层的数量之间未发现直接关联。具有1个、2个和4个层的器件的最大运行压力分别为83、203、和500毫巴。甚至对于高的层计数的器件,驱动压力的该增加也不增加对于分层的担忧。例如,通过从压力测量值进行外推,10层的器件将需要~1.8巴。该估值仍充分低于器件可经得住而没有分层的7.5巴的最大测试压力。使用两个各自具有128个MFDG的器件来研究制作可变性是如何影响产物的分散性的(表3)。“128-器件I”与“128-器件II”(σfab=7.9%)相比具有4.8%的低的制作标准偏差。两个器件都显示出类似的表征曲线;然而,由第二种器件产生的变异系数在各点处增加并且与制作变动变化一致(图12B)。将预期由于制作公差所致的在产物的分散性方面的变化。对于平行器件的按比例放大的情况,已讨论了该问题,因为具有方形横截面的通道中的流体阻力与通道尺寸的四次方成比例。参见G.Tetradis-Meris,D.Rossetti,C.PulidodeTorres,R.Cao,G.Lian和R.Janes,Ind.Eng.Chem.Res.,2009,48,8881-8889,以及H.Bruus,TheoreticalMicrofluidics,OxfordUniversityPress,2007,vol.18,其各自全部通过参考引入。MFDG的通过瓣的去耦当用平行系统进行工作时的主要关注点是堵塞的潜在可能性,尤其是当对付包含树状分布网络的系统时,因为它们被报道对于无规的阻力变化具有较大的敏感性。参见G.Tetradis-Meris,D.Rossetti,C.PulidodeTorres,R.Cao,G.Lian和R.Janes,Ind.Eng.Chem.Res.,2009,48,8881-8889,其全部通过参考引入。在所提出的瓣状结构中,分享公共输出端的MFDG的组在相同的芯片内充当独立的单元。如果一个部分变堵塞且其产物突然变成多分散的,则可通过如下将受影响的瓣关闭:关闭其两个输入端分支或者一个输入端分支以及输出端。关闭的瓣的通道阻力变得无穷大且通过调节输入端压力以维持每个MDFG的初始流速,其它产物可仍然保持它们的低的分散性和尺寸。具有该类型的瓣结构的平行系统可然后在具有失活的部分的情况下工作并且避免总的制造停止。为了研究关闭堵塞的部分的影响,与在所有瓣都起作用的情况下的“256-器件I”的产物相比,当将“256-器件I”的瓣的一个、两个或三个完全关闭时,测量由“256-器件I”产生的产物的尺寸分布。图15显示该比较且表4总结所述实验以及在关闭输出端之后保持每个工作的MFDG的类似的流动速率所需要的压力方面的调节。液滴尺寸的误差是由于作为压力调节以及在整个实验中需要的停止和再装载步骤的结果的在流动速率方面的小的变动。表4.对于“256器件I”在不同的工作容量下的实验的总结(%)PoPwFRo(mL/h)FRw(m/h)FRo/FRw液滴尺寸(μm)100731415563384.6199.9775601311312304.9190.585050137951724.6192.62253712403844.8186.99该研究证明,瓣是具有弱的相互影响的独立的功能单元且它们可被失活和再活化,如果提供恰当的阀的话。预期在具有不同数量的产生层的器件中看到该行为且该行为不依赖于每层的瓣的数量。值得注意的是,这些瓣仅在其中耦合和阻抗是最小的最高水平的层次(邻近于输入端口)处彼此连接。由于此,关闭这些瓣之一对于其它瓣具有很小影响到没有影响,且因此对于生产量具有很小影响到没有影响。球形药物晶体附聚物的制造可使用微流控器件制造药物微晶。将负载了甘氨酸的乳液在加热的玻璃盖玻片上蒸发以产生球形晶体附聚物(图19),其为活性药物微晶的模型(典型)。球形附聚物形式的活性药物成分(“API”)的结晶化和配制对于连续的和可持续的药物制造是关键步骤且在近年来已在科学和工业上被大量地关注。参见例如A.I.Toldyetal.,SphericalCrystallizationofGlycinefromMonodisperseMicrofluidicEmulsions,Cryst.GrowthDes.,2012,12(8),3977-3982;R.A.Leon,W.Y.Wan,A.Z.M.Badruddoza,T.A.Hatton和S.A.Khan,Cryst.GrowthDes.,2013,14,140–146;以及A.Z.MdBadruddoza,A.I.Toldy,T.A.HattonandS.A.Khan,Cryst.GrowthDes.,2013,13,2455–2461,其各自全部通过参考引入。微流控乳液产生与快速的基于薄膜的蒸发结晶化的结合是用于经设计的药物配制物的精确制造的有前景的路线。通过提供处于升/小时的生产能力(其为最终按比例放大过程中的关键要求)的受控制的微流控乳化,所公开的系统大大地促进这样的方法向工业上相关的生产规模的转化。图19A显示在药物工业中作为参考模型使用的甘氨酸球形晶体附聚物的SEM照片。液滴在结晶化过程期间收缩。可通过使用该系统展示甘氨酸晶体附聚物的形成。甘氨酸(>99%)是可从乳液结晶化的氨基酸的实例且通常在药物结晶化中用作模型分子。使用“128-器件I”产生具有150μm的有效直径的负载了甘氨酸的乳液。然后,将~100μL的样品从乳液发生器的输出端引导至加热的显微镜玻璃载玻片(Corning75×50mm)上以形成具有~0.2到0.4mm的估计厚度的甘氨酸的薄膜。将显微镜载玻片放置于TorreyPinesScientificEchoThermTMHS65热板上面并且将设定到90℃的温度以制造甘氨酸晶体附聚物(图19)。结晶化顺序细节提供在A.I.Toldy,A.Z.M.Badruddoza,L.Zheng,T.A.Hatton,R.Gunawan,R.Rajagopalan和S.A.Khan,Cryst.GrowthDes.,2012,12,3977-3982中,其全部通过参考引入。简要地说,它由四个步骤组成,所述四个步骤通过由加热的基材递送到负载了甘氨酸的液滴的外部热引发。首先,液滴直径迅速收缩到大约50%,然后产生局部的成核,随后是从核到液滴边界的快速的辐射状生长,且最后是球形附聚物的陈化(图19B)。使用如下两种方法对所述球形晶体附聚物进行表征:光学显微镜和使用Quanta3DFeg系统的扫描电子显微镜。该方法容许单分散的甘氨酸晶体附聚物的制造且提供用于控制快速的晶体生长的优异方法,因为晶体形成被限制在液滴内。其它实施方式在所附权利要求的范围内。当前第1页1 2 3