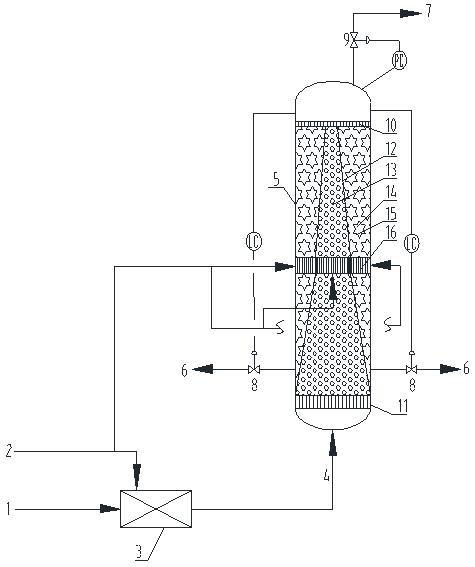
1.本发明属于化工及石油化工领域,具体为一种加氢反应器及加氢方法。
背景技术:2.加氢反应是氢与化合物相互作用的反应过程,通常是在催化剂存在下进行的。加氢过程已是化学工业和石油炼制工业中最重要的反应过程之一。加氢反应是可逆、放热和分子数减少的反应,低温、高压有利于化学平衡向加氢反应方向移动。加氢过程所需的温度决定于所用催化剂的活性,活性高者温度可较低。对于在反应温度条件下平衡常数较小的加氢反应,为了提高平衡转化率,反应过程需要在高压下进行,并且也有利于提高反应速度。另外采用过量的氢,不仅可加快反应速度和提高被加氢物质的转化率,而且有利于导出反应热。过量的氢可循环使用。
3.加氢反应器分为多种类型,如固定床加氢反应器、悬浮床加氢反应器、沸腾床加氢反应器等,其中以固定床加氢反应器的应用最为广泛。其中上流式固定床反应器能够处理多种类型的油品,在油品加氢过程中显示出了独特的优势,如劣质油品渣油、煤液化油中由于杂质含量高,容易造成加氢催化剂中毒或者催化剂孔道堵塞而快速失活,并且杂质可能堵塞床层使压降快速升高导致反应器工况变差,甚至无法正常操作,若采用上流式加氢反应过程使气液并流向上运动造成催化剂床层的膨胀,可以增加床层的空隙率,避免催化剂床层的堵塞。而在加氢工艺中,液相加氢工艺过程相比于传统的固定床气/液/固三相加氢工艺而言,具有加氢反应速率快、反应效率高、能耗低、投资少等诸多优势,得到广泛认可和应用,因此,上流式液相加氢反应过程综合了上流式加氢反应器和液相加氢反应工艺过程二者的优势,应用于加氢过程已经显示出了一定的优势。但是,常规的上流式液相加氢反应器及反应工艺中仍然存在如下问题:(1)反应物料与催化剂的接触更加充分,反应速率快,反应效率高,但仍然存在停留短达不到反应要求的深度,而反应停留时间长副反应或裂解及催化剂结焦严重的问题;(2)尤其是在末期反应温度高的区间段内,由于物料和催化剂接触较为充分,使得副反应或裂解反应较为严重,已经远远超过了正反应,导致反应末期发生了大量不希望发生的反应,降低了收率和生产效率;(3)反应过程中随着物料在加氢反应器内的流动和氢气的消耗,氢气在油品中的溶解分散状态已经逐渐发生了变化,导致油品分子周围溶解的氢气气泡已经发生了反应,那些没有发生反应的气泡逐渐聚结为大气泡,使油品在加氢反应过程中不能持续的提供氢气,也会增加副反应或裂解反应;(4)在反应末期,有些加氢反应存在产物或产物中的某一种或几种组份对正反应的抑制作用,使得很难达到要求的加氢反应深度。因此,对于常规的上流式液相加氢反应过程来说,采用有效的手段,如开发新的加氢方法及反应器形式,改善加氢反应速率和反应深度,同时抑制高温段副反应或裂解反应,具有重要意义。
4.cn202063881u公开了一种液相加氢反应器,反应器顶部封头内设置混合器,混合器有混合油进料口和氢气入口,溶氢混合物出口和气体出口,混合物溶氢混合物出口插到反应器液相中。该专利的目的是通过混氢器在反应器内的结构,来增加气液相接触面积,使
氢气溶解在混合油中,来提高加氢反应效率。
5.cn105713659a提出了一张烃类连续液相加氢工艺方法,是烃类原料和氢气经气液混合器充分混合形成溶解氢气饱和的液相物流,在包含至少的两级催化剂的反应器中,从上往下先后与各级催化剂下部的氢气分配器中注入氢气,产物从反应器引出后续处理。该方法的目的是在催化剂床层减即使补充新鲜氢气,同样是用来提高反应效率。
6.cn200810117101.1提出了一种上流式反应器及其应用,上流式反应器包括位于反应器底部的初始分布器和初始分布器上方的中间分布器,初始分布器由一个锥形折流板和一个位于其上方的筛板组成;中间分布器由开孔筛板和筛板板串结构组成,该发明所提供的上流式反应器的目的是实现气体均匀分布,从而提高催化剂的利用率。cn201110353672.7提出了一种上流式反应器气液分布器及应用,包括分布盘塔板和帽罩式集气分配器组成,该发明目的是使气相的均匀分布,提高气液两相的传质效率。cn201510697566.9提出了一种上流式分配器和上流式反应器,该发明的目的是该通过本技术方案,流体通过上流式分配器后能够均匀地分配和均匀混合。
7.综上所述,现有技术中的的上流式加氢反应器及液相加氢反应器,一般是通过溶氢方法或溶氢组件来进行溶氢,通过补充氢的方法来提高反应效率,没有解决上流式液相加氢反应器存在反应前期和中期的催化活性高,末期反应速率低、副反应及裂解反应严重的问题,也没有解决反应产物对于反应原料的抑制等问题。
技术实现要素:8.针对现有技术的不足,本发明提供一种加氢反应器及加氢方法,通过在上流式加氢反应器内设置锥形结构的内筒,能够有效控制加氢反应在不同温度段内物料与不同活性催化剂的接触时间,实现低、中温段的快速反应、抑制高温段副反应的目的,提高加氢反应速率和反应深度。
9.本发明的加氢反应器,包含内筒和反应器外壳,内筒为锥形,内筒和反应器外壳之间构成横截面积由上而下逐渐减小的环形空间;内筒顶部和底部敞口,底部边缘与反应器内壁密闭连接;所述的内筒装填加氢催化剂i,环形空间装填加氢催化剂ii,加氢催化剂i的活性高于加氢催化剂ii的活性;反应器中部水平设置补氢组件,补氢组件贯穿环形空间和内筒所在横截面,补氢组件连通外部氢气;反应器原料入口与内筒底部连通,反应器产物出口与环形空间下部连通;物料在内筒的流动方式为由下而上;物料在环形空间的流动方式为由上而下。
10.本发明的加氢反应器,所述的内筒顶部平面直径与反应器的直径之比为1:1.05~1:50,优选1:1.5~1:5。
11.本发明的加氢反应器,所述的补氢组件包括与外部氢气连通的管线及具有氢气分布或气液混合功能的组件。所述的具有气体分布功能的组件,如分布管、分布板等,也可以是具有气液混合功能的设备,如填装有螺旋板片、波纹板片、旋转叶片、平叶片、弯曲叶片或多孔板片等中的任意一种静态混合器,或微孔板纳/微米氢分散组件、陶瓷膜纳/微米氢分散组件等。所述的内筒部分的补氢组件和环形空间部分的补氢组件分别连通外部氢气管线。
12.本发明的加氢反应器,所述的补氢组件优选为陶瓷膜纳/微米分散组件,该组件为
一体式管壳结构,一般包含多根垂直于反应器横截面的方向的陶瓷膜膜管和壳体,膜管两端固定在管板上,壳体固定在反应器内表面;内筒部分的陶瓷膜纳/微米分散组件,膜管与内筒向上流动的物料连通,膜管外侧的空腔与外部氢气管线连通;环形空间部分的陶瓷膜纳/微米分散组件,膜管与外部氢气管线连通,膜管外侧的空腔与环形空间向下流动的物料连通;陶瓷膜纳/微米氢分散组件能够形成的纳/微米气泡氢的尺寸一般为10~1000nm,优选为50~500nm。
13.本发明的加氢反应器,内筒部分的陶瓷膜纳/微米分散组件,位于内筒的陶瓷膜纳/微米氢分散组件的主要是补氢和再次溶氢的作用,内筒下部的物料进入膜管管内,氢气经外部氢气管线进入膜管管外,氢气经管外渗透扩散至管内并与内筒物料混合溶解为含有氢气的物料自膜管流出,增强低、中温段的加氢反应过程推动力,以维持较高的反应速率;环形空间的陶瓷膜纳/微米氢分散组件的主要作用是补氢和汽提作用,环形空间上部向下流动的物料进入膜管管外,氢气经外部氢气管线进入膜管管内,氢气经管外渗透扩散至管外的过程中,与管外物料混合溶解为含有氢气的物料的同时,通过氢气的外扩散对物料进行汽提作用,既可以为反应末期补充氢气,抑制末期高温段催化剂表面结焦,同时又能够将表面结焦前驱体及抑制反应器生成气及时的汽提分离出来,改善加强反应深度。
14.本发明的加氢反应器中,顶部为反应器上封头,底部为反应器下封头,原料入口处优选设置物料分布器,用于均匀分布物料进入内筒。
15.本发明的加氢方法,包括如下内容:含有氢气的原料经反应器底部进料口进入“锥形”内筒,与内筒装填的加氢催化剂i进行加氢反应,物料经补氢组件进行补氢和再次溶氢,由内筒顶部流出后经反应器顶部,由上而下进入环形空间,与环形空间内装填的加氢催化剂ii发生进一步加氢反应,物流经补氢组件进行补氢和汽提,最终的反应产物自反应器底部的出料口排出。
16.本发明方法中,根据反应过程需要调节内筒和环形空间的补氢量,内筒补氢量与环形空间的补氢量之比为100:1~1:1,优选1:0.5~1:5。
17.本发明方法中,物料在内筒和环形空间的停留时间比为100:1~1:1,优选30:1~5:1。
18.本发明方法中,所述的反应器顶部有气体空间,反应器顶部封头最高点处设置气体出口,用于连续或间断排放反应过程中汽提出的反应气体。
19.本发明方法中,反应器上部通过液位控制出料,保证加氢反应过程为全液相加氢。
20.本发明方法中,所述内筒的加氢反应条件为:反应温度 60℃~360℃,优选180℃~340℃;反应压力0.5mpa~20.0mpa,优选2.0mpa~6.0mpa;新鲜进料液时体积空速0.5h-1
~10.0h-1
,优选1.0h-1
~6.0h-1
。
21.本发明方法中,所述环形空间的加氢反应条件为:反应温度120~400℃,优选220~380℃;反应压力0.5mpa~20.0mpa,优选2.0mpa~6.0mpa;新鲜进料液时体积空速0.5h-1
~15.0h-1
,优选3.0h-1
~10.0h-1
本发明的加氢反应器,可用于石油化工领域能够与氢气发生加氢反应的多种原料,可以为如原油、汽油、煤油、柴油、渣油、重质油、蜡油、润滑油、脱沥青油、生物柴油、动物油或植物油、煤焦油、蒽油等原油和二次加工油,在加氢过程中发生硫/氮/氧/金属等的加氢转化、烯烃及二烯烃加氢饱和、芳烃部分加氢饱和、加氢裂化等反应;也可以为化工领域能够
发生加氢反应的多种原料,可以为含有炭炭双键、炭炭三键以及有机官能团的原料,如烯烃加氢、炔烃加氢、醛类化合物加氢、酮类化合物加氢、酯类化合物加氢、硝基化合物加氢、腈类化合物加氢等反应。
22.本发明方法中,所述的加氢催化剂i的活性高于加氢催化剂ii的活性,优选加氢催化剂i的活性与加氢催化剂ii的活性之比为1.05:1~10:1。其中所述的活性高低是针对内筒和环形空间发生的化学反应而言的,是以每单位容积(或质量)催化剂在单位时间内转化原料反应物的数量来表示,催化活性的高低可以通过催化剂载体比表面积的大小、表面上活性中心的性质和单位表面积上活性中心的数量等进行选择或制备过程中进行调控。
23.催化剂活性的评价方法如下:在相同的原料组成和反应条件下,同体积催化剂在同一套装置上进行加氢反应,经过相同的停留时间后测定产物组成数据,计算转化率比较大小,作为判断活性高低的依据。
24.本发明方法中,所述的加氢反应器采用的催化剂可以根据反应的需要使用适宜的加氢催化剂,实现不同的加氢目的,如加氢精制催化剂、预加氢精制催化剂、加氢改质催化剂、选择性加氢催化剂、加氢处理催化剂、加氢裂化催化剂、补充加氢催化剂等,各种催化剂可以选择商品催化剂,也可以根据现有技术制备。催化反应可以脱除部分或全部烃类原料中的硫、氮、氧、砷、金属、残碳等杂质,或饱和/部分饱和烯烃、芳烃、二烯烃,或发生烃类分子异构化、烷基化、环化、芳构化、裂化、裂解等反应;催化剂活性组分包括但不局限于贵金属、co、mo、ni、w、mg、zn、稀土元素等一种或多种组合。
25.本发明方法中,所述的环形空间可以装填活性全部或部分低于内筒活性的加氢催化剂,催化剂可以使用市售产品,也可以根据本领域常规知识制备;如加氢脱硫活性高的催化剂可以使用一般以氧化铝或含硅氧化铝为载体,mo、co为加氢活性组分。以催化剂的重量为基准,金属mo含量以氧化物计为6wt%~20wt%,金属co含量以氧化物计为1wt%~12wt%。
26.对于常规的加氢反应过程来说,首先,大多数属于放热反应,即随着反应的进行,温度是逐渐升高的,虽然温度越高,反应速率越快,但是当温度越高时,物料在催化剂表面越容易结焦,而发生裂解反应或者降低催化剂活性,所以随着加氢反应温度的升高,原料跟高效催化剂接触时间应该逐渐缩短,保持较高的反应的同时,减缓或控制催化剂表面结焦; 第二方面,在加氢反应后期,反应温度已经较高,高活性催化剂在较高温度条件下更加容易发生结焦,裂解反应更加严重,所以反应末期应填装适当活性甚至稍低活性的催化剂,尽量控制加氢反应速率,抑制反应后期的高反应速率,而且在反应后期同样需要随着加氢反应温度的升高,原料在催化剂表面停留时间逐渐缩短,来控制催化剂表面发生结焦;第三方面,一些副产物反应气体对加氢反应有一定的抑制作用,这些副产物反应气体无法被及时移出体系,不利于深度加氢反应,所以在反应过程中原位汽提对于实现深度加氢具有重要作用;第四方面,在低、中温阶段,加氢反应速率较高,氢气消耗较快,原料中氢气的溶解分散状态已经逐渐发生了变化,导致油品分子周围溶解的氢气气泡已经发生了反应,那些没有发生反应的气泡逐渐聚结为大气泡,使油品在加氢反应过程中不能持续的提供氢气,而降低反应氢的持续推动力,降低反应速率,因此在反应低、中温阶段需要及时补充高分散状态的溶解氢。
27.本发明通过特殊的加氢反应器结构及加氢反应方法,有效控制加氢反应在不同温度段内物料与不同活性催化剂的接触时间,实现低、中温段的快速反应、抑制高温段副反应
的目的,提高加氢反应速率和反应深度。加氢反应器包含锥形内筒、横截面积由下而上逐渐减小的环形空间、贯穿于内筒和环形空间的补氢组件, 物料在锥形内筒的流动方式为由下而上,利用“锥形”结构由下而上截面积逐渐缩小的特点,实现随着反应温度的升高控制原料跟高活性催化剂的接触时间逐渐缩短,保持较高的反应的同时,减缓或控制催化剂表面结焦,减少副反应;物料在环形空间的流动方式为由上而下,利用环形空间由上而下截面积逐渐缩小的特点,实现反应末期温度较高时控制原料跟稍低活性催化剂的接触时间逐渐缩短,可进一步抑制减缓或控制催化剂表面高温结焦及减少副反应。另外,在“锥形”内筒的低、中温反应阶段采用高活性催化剂,发生快速加氢反应,在反应过程中通过补氢组件补充氢气,达到反应过程中的高消耗氢气时,及时的补充高分散氢气,增加加氢反应过程推动力,进一步提高中、低温加氢反应速率;而环形空间内高温阶段填装稍低活性的催化剂,发生慢速加氢反应,在反应过程中通过补氢组件补充氢气,起到补充氢气和汽提的作用,一方面抑制高温反应阶段催化剂结焦,另一方面汽提出抑制加氢反应的反应气体,达到深度加氢反应。
附图说明
28.图1是本发明的加氢反应器及加氢方法的示意图。
29.图2是本发明的陶瓷膜纳/微米氢分散组件的示意图。
30.1为原料油,2为氢气,3为氢油混合器,4为加氢反应器进料,5为加氢反应器,6为反应产物,7为排放气,8为反应产物出料阀,9为排气控制阀,10为催化剂压盖格栅,11为催化剂支撑格栅,12为锥形内筒,13为加氢催化剂i,14为环形空间,15为加氢催化剂ii,16为补氢组件(陶瓷膜纳/微米分散组件),17为与环形空间连通的氢气管线,18为锥形内筒的陶瓷膜管,19为环形空间的陶瓷膜管,20为与锥形内筒连通的氢气管线。
具体实施方式
31.下面结合附图说明和实施例对本发明进行详细说明,但不因此限制本发明。
32.以附图1说明本发明的加氢反应器及加氢方法:原料油1与氢气2经氢油混合器3混合后,作为加氢反应器进料4从加氢反应器5的底部进入加氢反应器5后,首先进入加氢反应器5的锥形内筒12,由下而上依次经过加氢催化剂i进行加氢反应后,进入反应器顶部与内筒连通的区域,在锥形内筒12反应过程中,通过补氢组件(陶瓷膜纳/微米氢分散组件)16进行补氢和再次溶氢;离开锥形内筒12的物料进入环形空间14,由上而下与环形空间的加氢催化剂ii15发生进一步的加氢反应,在反应过程中,通过补氢组件(陶瓷膜纳/微米氢分散组件)16进行补氢和汽提反应气体,防止高温催化剂结焦的同时,将反应产物中的反应气体汽提出来;最终的反应产物6经反应产物出料阀8的控制下离开加氢反应器5;环形空间14汽提出的反应气体在反应器顶部排气控制阀9的作用下作为排放气7排出。其中,补氢组件(陶瓷膜纳/微米分散组件)16为一体式管壳结构,一般包含多根一般包含多根垂直于反应器横截面的方向的陶瓷膜膜管和壳体,膜管两端固定在管板上,壳体固定在反应器内表面;内筒部分的陶瓷膜纳/微米分散组件16,膜管16与内筒向上流动的物料连通,膜管外侧的空腔与外部氢气管线20连通;环形空间部分的陶瓷膜纳/微米分散组件16,膜管19与外部氢气管线17连通,膜管外侧的空腔与环形空间向下流动的
物料连通;在加氢反应过程中,内筒部分的陶瓷膜纳/微米分散组件16,是来自于内筒下部的物料进入膜管管内,氢气经外部氢气管线进入膜管管外,氢气经管外渗透扩散至管内并与内筒物料混合溶解为含有氢气的物料自膜管流出向下流动发生加氢反应;环形空间的陶瓷膜纳/微米分散组件16,是来自于环形空间的物料进入膜管管外,氢气经外部氢气管线17进入膜管19的管内,氢气经管外渗透扩散至管外的过程中,与管外物料混合溶解为含有氢气的物料的同时,通过氢气的外扩散对物料进行汽提作用,既可以为反应末期补充氢气,抑制末期高温段催化剂表面结焦,同时又能够将表面结焦前驱体及抑制反应器生成气及时的汽提分离出来,改善加强反应深度。
33.本发明对比例及实施例中采用的原料油为来自某厂的直馏柴油和催化柴油,具体性质见表1。
34.表1 原料性质对比例1采用常规固定床加氢反应器及加氢方法,氢油混合设备采用静态混合器,型号为:sx-2.3-10.0-500;反应器进料中氢气的给量为原料油(新鲜原料油与循环油之和)质量的0.63%。加氢反应器采用的催化剂为抚顺石油化工研究院的fhuds-5。
35.固定床加氢反应条件如下:反应温度为340~388℃,反应压力为6.5mpag,液时体积空速为3.0h-1,循环比为1.5~2.0。
36.分别以表1中的直馏柴油和催化柴油为原料,经过固定床液相加氢后得到反应产品,反应条件及产品性质见表2和表3。
37.实施例1采用附图1所述的方法,加氢反应器锥形内筒采用的催化剂为抚顺石油化工研究院的fhuds-5,环形空间空间采用的催化剂为fh-40c;加氢反应器进料中含有的氢气为原料油(新鲜原料油与循环油之和)质量的0.31%,加氢反应器锥形内筒中补氢量为原料油(新鲜原料油与循环油之和)质量的0.24%,环形空间中氢气的给量为原料油(新鲜原料油与循环油之和)质量的0.05%。加氢反应器锥形内筒的反应条件如下:反应温度为300~340℃,反应压力为6.0mpag,液时体积空速为5.0h-1
;环形空间的反应条件如下:反应温度为330~358℃,反应压力为5.9mpag,液时体积空速为6.0h-1
。反应器内锥形内筒的顶部平面直径与反应器的直径之比为1:5。
38.以表1中的直馏柴油和催化柴油为原料,经过固定床液相加氢后得到反应产品,反应条件及产品性质见表2和表3。
39.实施例2
采用附图1所述的方法,加氢反应器锥形内筒采用的催化剂为抚顺石油化工研究院的fhuds-2,环形空间采用的催化剂为fh-40c,;加氢反应器进料中含有的氢气为原料油(新鲜原料油与循环油之和)质量的0.26%,加氢反应器锥形内筒中补氢量为原料油(新鲜原料油与循环油之和)质量的0.28%,环形空间空间中氢气的给量为原料油(新鲜原料油与循环油之和)质量的0.06%。加氢反应器锥形内筒的反应条件如下:反应温度为315~352℃,反应压力为6.0mpag,液时体积空速为4.5h-1
;环形空间的反应条件如下:反应温度为340~372℃,反应压力为5.9mpag,液时体积空速为7.5h-1
。反应器内锥形内筒的顶部平面直径与反应器的直径之比为1:3。
40.以表1中的直馏柴油和催化柴油为原料,经过固定床液相加氢后得到反应产品,反应条件及产品性质见表2和表3。
41.实施例3采用附图1所述的方法,加氢反应器锥形内筒采用的催化剂为抚顺石油化工研究院的fhuds-5,环形空间采用的催化剂为fhuds-2;加氢反应器进料中含有的氢气为原料油(新鲜原料油与循环油之和)质量的0.22%,加氢反应器锥形内筒中补氢量为原料油(新鲜原料油与循环油之和)质量的0.31%,环形空间中氢气的给量为原料油(新鲜原料油与循环油之和)质量的0.07%。加氢反应器锥形内筒的反应条件如下:反应温度为318~348℃,反应压力为5.5mpag,液时体积空速为5.0h-1
;环形空间的反应条件如下:反应温度为338~375℃,反应压力为5.4mpag,液时体积空速为9.0h-1
。反应器内锥形内筒的顶部平面直径与反应器的直径之比为1:1.5。
42.表2反应条件及产品性质(直馏柴油原料)表3 反应条件及产品性质(催化柴油原料)由实施例及对比例的加氢反应效果可以看出,采用本发明的加氢反应器及加氢方法,
能够实现低、中温段发生快速反应,抑制高温段的副反应,提高了加氢反应速率和反应深度。这主要是由于本发明方法中,利用反应器内“锥形”结构由下而上截面积逐渐缩小的特点,实现随着反应温度的升高控制原料跟催化剂的接触时间逐渐缩短,在高活性催化剂表明发生较高反应速率的同时,减缓或控制催化剂表面结焦,而物料在环形空间时的流动方式为由上而下,利用环形空间由上而下截面积逐渐缩小的特点,实现反应后期温度较高时,控制原料跟催化剂的接触时间逐渐缩短,且在稍低活性的催化剂表面反应可以进一步抑制减缓或控制催化剂表面高温结焦,同时减少副反应;在锥形内筒反应过程中通过补氢组件补充氢气,达到反应过程中的高消耗氢气时,及时的补充高分散氢气,增加加氢反应过程推动力,进一步提高中、低温加氢反应速率,而环形空间内通过补氢组件补充氢气,起到补充氢气和汽提的作用,汽提出抑制加氢反应的反应气体,达到深度加氢反应。