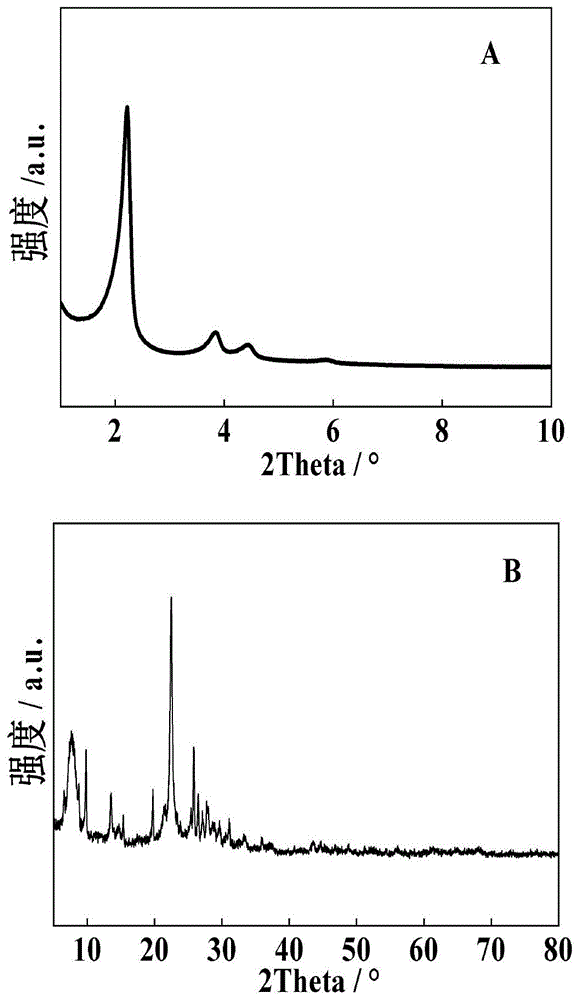
本发明属于固体多相催化
技术领域:
,尤其涉及一类含有贵金属和酸中心两种活性位的担载型贵金属双功能固体催化剂。
背景技术:
:双功能催化剂是一类具有两种不同活性中心,能够同时催化两类不同反应的催化剂。金属或金属硫化物活性中心催化加氢/脱氢反应,而酸中心则催化异构化、芳构化、环化以及裂化等反应。对于担载型的加氢催化剂,提高载体或催化剂酸性也有利于提高催化剂催化某些反应的活性。例如对担载型贵金属或硫化物加氢脱硫(hds)催化剂,提高载体的酸性有利于提高催化剂的活性。需要指出的是,在这些双功能催化剂上,金属活性中心都担载在酸性载体上,直接与酸中心接触。提高载体酸性虽然能够改善催化剂加氢或加氢性能,但同时也会加剧裂化、结焦等副反应,影响产品质量、液收以及催化剂寿命。当金属活性中心直接与酸中心接触时,在酸中心上生成的焦炭或大分子有机化合物会覆盖金属活性中心,导致催化剂快速失活。对于一些以具有很高活性的贵金属作为活性组分的催化剂(如重整催化剂)来说,这一问题尤为突出。贵金属催化剂一般具有高活性易中毒等特点。为了得到最佳性能,工业催化剂往往需要金属活性组分非均匀地分布在载体中。贵金属活性组分在催化剂中主要有蛋壳型、蛋白型、蛋黄型和均匀分布等四种形式。在蛋壳型催化剂中,贵金属组分主要分布在催化剂外表面,对于受内扩散控制的快速反应有良好的性能。蛋壳型催化剂还对连串反应中的中间体有良好的选择性。当反应受动力学控制时,应以均匀分布为宜。若反应物中含有能使催化剂中毒的组分,并且载体能够吸附该毒物,则蛋黄型或蛋白型分布可能有助于提高金属组分抗中毒性能。但是这些非均匀分布尺度一般都为毫米级,并且酸中心也直接和金属组分相接触。技术实现要素:本发明的目的是提供一种非均匀分布的双功能催化剂,该催化剂纳米尺度金属中心与酸中心相分离。具体说来,是以一种包覆型介微孔材料作载体,其中载体内核为酸性的沸石材料,沸石表面包覆了一层介孔孔道由沸石内核向外生长的不具有酸性的mcm-41介孔相,而贵金属pd纳米粒子完全分布在载体表面,不与酸中心接触。一种非均匀分布双功能pd催化剂,载体的内核为酸性的沸石材料,沸石表面包覆mcm-41介孔相,贵金属pd纳米粒子分布在mcm-41介孔相的外表面。pd活性组分特指金属pd,而不是钯的化合物。其组成为pd的质量含量不大于10%。其中,质量含量应当理解为pd的质量占催化剂总质量的含量比例。该催化剂制备方法如下:(1)用水热合成法制备mcm-41包覆沸石复合分子筛;(2)采用nh4no3交换的方法脱除分子筛中钠离子得到氢型复合分子筛;(3)硅烷化处理步骤(2)制得的氢型复合分子筛;(4)在步骤(3)制得的氢型复合分子筛上浸渍pd,制得前驱体;(5)氢气气氛下还原步骤(4)制得的前驱体,得到非均匀分布双功能pd催化剂。而且,步骤(1)的具体步骤是:称取一定量的沸石分散在适量的去离子水中,然后加入适量十六烷基三甲基溴化铵的水溶液,在一定温度下搅拌一定时间,形成混合物a;然后将适量的na2sio3·5h2o溶于一定量的去离子水中,加入h2so4溶液调节ph值至10~12,形成溶液b;将a溶液和b溶液混合后再加入适量去离子水形成溶胶,将所得溶胶在室温下剧烈搅拌一定时间后,装入水热釜中,于120℃下进行水热合成反应12~72h,所得固体经分离,冲洗和干燥后,于540℃焙烧4h,制得复合分子筛。而且,步骤(2)的具体步骤是:称取步骤(1)制得的复合分子筛置于1mol/l的nh4no3溶液中,其中筛水比为1g/10ml溶液,于70℃搅拌交换2h,真空抽滤,然后重新加入nh4no3溶液进行第二次交换,第二次交换完成后,真空抽滤、洗涤,然后将干燥后的nh4型分子筛样品在马弗炉中于500℃焙烧3h,得到氢型复合分子筛。而且,步骤(3)的具体步骤是:称取氢型复合分子筛置于甲苯中,氢型复合分子筛的质量百分含量为2~3%,然后加入三甲基氯硅烷,三甲基氯硅烷的体积百分含量5%,在100~120℃下搅拌回流2~4h,抽滤,用甲苯洗涤滤饼,室温下干燥得到硅烷化处理的复合分子筛。而且,步骤(4)的具体步骤是:将醋酸钯溶于甲苯中,醋酸钯的质量百分含量为2~2.5%,然后逐滴滴加到的硅烷化处理的复合分子筛,边滴加边搅拌,直至全部浸渍液滴加完毕,室温老化,然后干燥,400℃焙烧4~6h,得到前驱体。而且,步骤(5)的具体步骤是:将制得的前驱体压片成型并破碎,然后将一定量前驱体置于固定床反应器中还原反应,制得非均匀分布双功能pd催化剂。而且,所述的沸石为β沸石或y沸石。本发明催化剂用于加氢脱硫时,使用条件为:在氢气存在的条件下,于固定床反应中使反应原料与催化剂接触发生加氢脱硫反应。反应条件为:反应温度200~400℃,压力1.0~10.0mpa,氢油体积比不超过10000nm3/m3,液时体积空速0.1~100h-1。本发明的优点和有益效果:本发明通过将酸中心和金属中心分离,在酸中心的催化下形成的焦炭和/或大分子有机化合物不会覆盖金属活性中心导致失活;mcm-41介孔相的孔道由沸石向外生长,不会影响反应物和产物的扩散;不具有酸性的mcm-41介孔相会覆盖沸石的外表面酸中心,从而抑制裂化等副反应,提高液收;另外金属中心完全分布在载体孔道外部,不受扩散影响,并且h2s分压较低,提高了催化剂活性和稳定性。催化剂综合性能明显优于mcm-41和沸石作载体的pd催化剂。附图说明图1为mcm-41包覆β沸石复合分子筛的xrd谱图;图2为mcm-41包覆β沸石复合分子筛的透射电镜照片;图3为pd/si-βm催化剂中pd完全分布在载体表面或孔口的透射电镜照片;图4为mcm-41包覆y沸石复合分子筛的xrd谱图;图5为mcm-41包覆y沸石复合分子筛的透射电镜照片;图6为未经硅烷化的mcm-41包覆β沸石复合分子筛作载体的pd催化剂透射电镜照片。具体实施方式以下结合技术方案和附图详细叙述本发明的具体实施方式。实施例1一种非均匀分布双功能pd催化剂,制备步骤如下:(1)mcm-41包覆β沸石复合分子筛的制备取1.2g的hβ沸石分散在10ml去离子水中,超声振荡15min。然后加入模板剂溶液(6.4g的十六烷基三甲基溴化铵溶于30ml去离子水),25℃下搅拌24h,形成混合物a。将16.5g的na2sio3·5h2o溶于80ml去离子水中,加入6mol/l的h2so4溶液调节ph值至11,形成溶液b。将a逐滴加入到溶液b中,滴加完毕后,加入20ml去离子水,将所得溶胶在室温下剧烈搅拌2h后,装入水热釜中,于120℃下进行水热合成反应。反应48h后,取出水热釜并冷却,抽滤洗涤至中性,滤饼经干燥后,于550℃焙烧6h制得复合分子筛。对合成的复合分子筛进行nh4+交换脱除na+:将制得的分子筛样品加入到1mol/l的nh4no3溶液中,其中筛水比为1g/10ml溶液。于70℃搅拌交换2h,真空抽滤,然后重新加入nh4no3溶液进行第二次交换。第二次交换完成后,真空抽滤、洗涤,然后将干燥后的nh4型分子筛样品在马弗炉中于500℃焙烧3h,即得到氢型复合分子筛,记为βm。(2)硅烷化处理步骤(1)制得的复合分子筛称取3g的βm置于150ml甲苯中,然后加入三甲基氯硅烷(体积百分含量5%),在110℃下搅拌回流3h,抽滤。用甲苯洗涤滤饼,室温下干燥10h,得到硅烷化的βm载体,记作si-βm。(3)在步骤(2)所得材料上浸渍pd,制得前驱体;将0.022g醋酸钯溶于5ml甲苯中,然后逐滴滴加到2g硅烷化的si-βm上,边滴加边搅拌,直至全部浸渍液滴加完毕。室温老化10h,然后在120℃烘箱中干燥12h,在马弗炉中以1℃/min的升温速率升至400℃,焙烧5h,得到催化剂前体。pd的担载量以金属pd计为质量分数0.5%。(4)氢气气氛下还原步骤(3)制得的前驱体,得到非均匀分布双功能pd催化剂。前驱体压片成型并破碎至20~40目,然后将一定量催化剂前驱体置于内径8mm的固定床反应器中,用程序升温还原的方法制备负载型的pd催化剂。具体条件如下:在总压1.0mpa的氢气气氛中以10℃/min的升温速率从室温升到300℃,气体流量为75nml/min,保持1h后自然降温至反应温度,制得非均匀分布双功能pd催化剂,记作pd/si-βm。图1示出了βm分别在小角(图1中的a图)和大角(图1中的b图)范围的xrd谱图。在图1中的a图中,于2θ=2.1°处观察到了归属于mcm-41(100)晶面的特征衍射峰,表明生成了mcm-41介孔相。在大角衍射区(图1中的b图),可以观察到β沸石的特征衍射峰,说明制得的βm分子筛为hβ和mcm-41的混合物。由图2所示的βm的tem照片可以看出,在较低的分辨率下(图2中的a图),只能观察到孔径约为4nm的介孔,看不到β沸石的晶粒。较暗的部分表明β沸石可能被mcm-41包覆起来。在较高的分辨率下(图2中的b图),可以观察到少量暴露的β沸石晶粒,晶粒其余部分被规整的介孔相包覆。所有介孔孔道开口向外,说明介孔空孔道由β沸石晶粒向外生长。在这些晶粒上还可以观察到未生长完全的介孔相。由图3所示电镜照片可以看出,在pd/si-βm催化剂中,pd完全分布在载体表面或孔口。实施例2包覆型y沸石和mcm-41复合材料的制备将4.25g的十六烷基三甲基溴化铵溶于40ml去离子水中,再加入1.2g的hy沸石,在室温(25℃)下搅拌24h,形成混合物a。将16.5g的na2sio3·5h2o溶于80ml去离子水中,加入6mol/l的h2so4溶液调节ph值至11,形成溶液b。将溶液b滴加到混合物a中,所得溶胶在室温下搅拌2h,置于不锈钢釜中在120℃下水热反应48h。所得固体经分离,冲洗,和干燥后,于540℃焙烧4h。所得材料记为ym。图4示出了ym分别在小角(图4中的a图)和大角(图4中的b图)范围的xrd谱图。在图4中的a图中,于2θ=2.1°处观察到了归属于mcm-41(100)晶面的特征衍射峰,表明生成了mcm-41介孔相。在大角衍射区(图4中的b图),可以观察到y沸石的特征衍射峰,说明制得的ym分子筛为y沸石和mcm-41的混合物。由图5中的a图所示的ym的tem照片可以观察到清晰的核/壳结构特征形貌,其壳层厚度大约有20nm。由图5中的b图可以观察所有介孔孔道开口向外,说明介孔空孔道由y沸石晶粒向外生长。对比例1制备负载型pd/mcm-41催化剂首先将1g的pdcl2溶于38ml的hcl溶液中(hcl浓度为0.4mol/l)制备浸渍液。称取1g的mcm-41沸石,将上述浸渍液用去离子水稀释后逐滴滴加到mcm-41载体上。静置8h,于120℃烘箱中干燥12h,再于马弗炉中于400℃焙烧3h,得到氧化态前驱体。pd的担载量以金属pd计为质量分数0.5%。将前驱体压片成型并破碎至20~40目,然后将一定量催化剂前驱体置于内径8mm的固定床反应器中,用程序升温还原的方法制备负载型的pd催化剂。具体条件如下:在总压1.0mpa的氢气气氛中以10℃/min的升温速率从室温升到300℃,气体流量为75nml/min,保持1h后自然降温至反应温度,制得负载型pd/mcm-41催化剂。对比例2制备负载型pd/β催化剂首先将1g的pdcl2溶于38ml的hcl溶液中(hcl浓度为0.4mol/l)制备浸渍液。称取1g的β沸石,将上述浸渍液用去离子水稀释后逐滴滴加到β沸石载体上。静置8h,于120℃烘箱中干燥12h,再于马弗炉中于400℃焙烧3h,得到氧化态前驱体。pd的担载量以金属pd计为质量分数0.5%。将前驱体压片成型并破碎至20~40目,然后将一定量催化剂前驱体置于内径8mm的固定床反应器中,用程序升温还原的方法制备负载型的pd催化剂。具体条件如下:在总压1.0mpa的氢气气氛中以10℃/min的升温速率从室温升到300℃,气体流量为75nml/min,保持1h后自然降温至反应温度,制得负载型pd/β催化剂。对比例3以未经硅烷化的复合分子筛βm作载体,采用等体积浸渍法制备pd/βm催化剂。首先将1g的pdcl2溶于38ml的hcl溶液中(hcl浓度为0.4mol/l)制备浸渍液。称取1g的βm分子筛,将上述浸渍液用去离子水稀释后逐滴滴加到βm载体上。静置8h,于120℃烘箱中干燥12h,再于马弗炉中于400℃焙烧3h,得到氧化态前驱体。pd的担载量以金属pd计为质量分数0.5%。将前驱体压片成型并破碎至20~40目,然后将一定量催化剂前驱体置于内径8mm的固定床反应器中,用程序升温还原的方法制备负载型的pd催化剂。具体条件如下:在总压1.0mpa的氢气气氛中以10℃/min的升温速率从室温升到300℃,气体流量为75nml/min,保持1h后自然降温至反应温度,制得负载型pd/βm催化剂。由图6所示电镜照片可以看出,在pd/βm催化剂中,pd完全分布在载体介孔孔道内。应用实施例1分别以pd/si-βm、pd/mcm-41、pd/β和pd/βm作催化剂,用质量分数0.8%的二苯并噻吩(dbt)的十氢萘溶液为模拟油品在固定床反应器中进行了加氢脱硫的试验。将床层温度调整至反应温度后(300℃),将氢气压力增加至5.0mpa,然后用高压计量泵向反应器中输送模拟油品,在反应器出口处经气液分离器分离出液体用于产物分析。其他反应条件:催化剂装填量0.05g,重时空速(whsv)为54h-1,h2/油品体积比为1500nm3/m3。原料和产物用agilent6890气相色谱分析,色谱柱为市售hp-1毛细柱,氢火焰检测器。定义脱硫率xhds为:xhds=(c0-cdbt-ci)/c0×100%(1)其中,c0和cdbt分别为原料油品和产品中dbt的含量,ci为产品中dbt的含硫中间体如四氢二苯并噻吩和六氢二苯并噻吩的含量。反应结果列于表1(dbt在不同催化剂上的脱硫率及裂化产物选择性)。由表1可以看出,dbt的脱硫率为pd/si-βm(97.0%)>pd/β(92.9%)>pd/βm(67.2%)>pd/mcm-41(22.3%)。pd/βm的活性略高于pd/β,远高于pd/βm和pd/mcm-41。但是在pd/β裂化产物选择性高达55.4%,而在pd/βm和pd/mcm-41则几乎不会发生裂化副反应。pd/si-βm表现出最佳的加氢脱硫反应性能。表1催化剂实施例1对比例1对比例2对比例3脱硫率(%)97.022.392.967.2裂化产物选择性(%)0055.415.1本发明经过上述的描述,已清楚地公开了本发明催化剂组成和制备条件。但是,本领域内的技术人员十分清楚,对本发明可以进行一些修改和改进。所以,只要不离开本发明的精神,对本发明所进行的任何修改和改进都应在本发明的范围内。当前第1页12