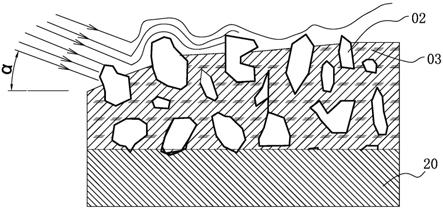
[0001]
本实用新型属于桨叶耐磨层成型方法技术领域,具体的说是在具耐磨层的强混机桨叶。
背景技术:[0002]
在桨叶10容易受到磨损的部位通过焊接、涂层的方式形成一个耐磨层00,用于提高桨叶的耐磨性能,这是行业常用方法,参考图1和图2。
[0003]
例如,中国专利cn201120502286.5中公开了一种高速混合设备的桨叶,包括桨叶本体,桨叶本体的一端为自由端,另一端与桨轴相连,桨轴上设有用于与主轴相连的连接端,所述自由端表面及桨叶本体的上下侧面堆焊有碳化钨耐磨层。桨叶转动时,最容易受到磨损的部位为桨叶本体的上下侧面和自由端的表面,在易磨损的部位设置碳化钨耐磨层,所述碳化钨耐磨层的厚度为1mm至4mm;碳化钨耐磨层沿桨叶长度方向延伸20-60mm。上述参数可保证桨叶在耐磨的同时,可以使整体制造成本较低。
[0004]
事实上,碳化钨的熔点:2800-3000℃左右;颗粒度:60-100目(0.15-0.25mm);硬度 hv1700-2200,耐磨性能仅次于金刚石,是耐磨材料中的上乘佳品。
[0005]
上述的技术方案中提到了设置碳化钨耐磨层,是单一成分(碳化钨)的耐磨层,且需要高温才能完成熔融堆焊。该技术中利用了碳化钨的高硬度、高耐磨性的特显,这是其优势所在。但是,单一成分的碳化钨耐磨层与桨叶母材的结合强度较低,即可焊接性能较差,这对于强混机的使用环境中的强冲击下保持耐磨性是非常不利的,这种强烈冲击甚至可能造成熔覆层的整体脱落,即存在碳化钨耐磨层整体脱落的可能。因此,作为强混机中使用的桨叶,这种碳化钨耐磨层与桨叶母材的脱离是非常危险的。
[0006]
同时,常规由于碳化钨的熔点在2800-3000℃左右,在将碳化钨堆焊在母材表面时,碳化钨中的c原子在高温作用下回产生固态迁移扩散,这对于碳化钨的耐磨性能具有直接的影响。
[0007]
所以,单纯的在桨叶表面焊接碳化钨形成耐磨层,是存在缺陷的。即,上述的碳化钨耐磨层的耐磨原理是,利用碳化钨的耐磨性能对抗物料的磨损,但是引入了焊接性能差、耐磨层容易整体脱落的缺陷。
[0008]
如何解决这种问题,为了解决碳化钨耐磨层与桨叶母材之间存在的脱落问题,下面技术提供了一种思路:
[0009]
cn201110087226.6公开了一种船舶螺旋桨桨叶的修复方法,对于磨损的桨叶,可将桨叶导边磨损处用气焊堆焊起来,要求所用的焊丝材质与螺旋桨的材质一样,然后打磨堆焊处的表面。具体过程为:
[0010]
1)在螺旋桨桨叶本体导边的磨损部位,用电焊的方法将其堆焊起来形成一个堆焊区,而后使用手提磨削机及手工修整将其修复至恢复桨叶本体的原有形状;
[0011]
2)对缺损的桨叶本体,按缺损处的形状事先铸造略大一点的与螺旋桨材质一样的铸件,然后用手工的方法配作出其形状大小及厚度,其中边缘的焊缝处应加工适当的焊接
倒角;然后用氧
--
乙炔手工焊焊接起来,最后用手工进行打磨和修整至与原桨叶本体一致的形状。
[0012]
即,理论上,通过将桨叶材质和待修复部位设置为同样的材质,可以有效的避免。但是,碳化钨材质的桨叶,碳化钨的脆性会对桨叶的韧性产生不利影响。且采用碳化钨作为整体的桨叶材料,考虑到其抗冲击性、韧性和成本、尤其是其冲击韧性与抗弯强度远比高速钢差,不适合作为抗冲击的桨叶使用,使得其仅仅存在于理论上的可能,所以现有的强混机桨叶技术领域中,并没有出现以单一成分的碳化钨作为桨叶母材的先例。
[0013]
事实上,本实用新型依然是沿用在高强度钢表面覆耐磨层的技术路线,提供一种更高耐磨性的桨叶及其制造工艺。
[0014]
基于此,作为常规钢材质的桨叶,本实用新型人未检索到采用将碳化钨颗粒与镍基耐磨合金混合耐磨材料辅以粉末等离子弧堆焊工艺方法用于增强桨叶表面耐磨性能的相关技术,以及文献。
技术实现要素:[0015]
为了解决现有技术的不足,本实用新型提供一种桨叶,用于解决现有技术中在钢母材的桨叶表面焊接单一成分的碳化钨形成的耐磨层容易自钢母材脱落的问题,以及进一步地提高新技术中耐磨层的耐磨性能和抗冲击性能。
[0016]
本实用新型解决其技术问题所采用的技术方案为:
[0017]
一种强混机桨叶,该桨叶包括位于内部的钢质母材,以及位于母材表层的耐磨层,其特征在于,所述耐磨层是在桨叶表面用粉末等离子弧熔覆工艺将镍基耐磨合金熔融并加入碳化钨硬质合金颗粒进行逐层堆焊形成的,且耐磨层在显微状态下:
[0018]
所述碳化钨硬质合金颗粒在耐磨层中均匀分布,无沉底现象;
[0019]
所述耐磨层高倍金相照片显示堆焊层中硬质相有碳化钨硬质合金颗粒、cr7c3颗粒、nib 颗粒,三种颗粒硬质相面积占比60-70%;
[0020]
所述耐磨层与母材的结合部位测试稀释率为3%-5%。
[0021]
进一步地,碳化钨硬质合金颗粒显微硬度平均值hv=1982,cr7c3颗粒显微硬度平均值 hv=1326,nib颗粒显微硬度平均值hv=1153,
[0022]
进一步地,堆焊工艺中所述碳化钨硬质合金颗粒与镍基耐磨合金用料重量比为40-60%。
[0023]
进一步地,所述桨叶的迎料面部位耐磨层厚度为6mm,其余部位为4mm。
[0024]
进一步地,所述堆焊单层厚度为2mm。
[0025]
本实用新型的有益效果是:
[0026]
1、首次将(wc+ni60)混合耐磨材料粉末等离子弧堆焊工艺方法用于桨叶的国产化制造,该中桨叶尤其能够满足强混机的使用要求。
[0027]
2、本实用新型中的桨叶采用粉末等离子弧熔覆工艺制造属于绿色增材制造范畴,初始制造时就埋下了再制造的基因,可以重复的进行覆材再制造,母材坯体可以重复使用3-4次,第二、三、四次再制造成本只有初始制造的1/4。
附图说明
[0028]
图1为桨叶和桨叶轴的安装示意图。
[0029]
图2为桨叶与耐磨层的位置关系(纵切面)。
[0030]
图3为桨叶与耐磨层的位置关系(横面)。
[0031]
图4为现有技术中wc硬质合金颗粒在堆焊熔覆过程中出现的沉底现象示意图。
[0032]
图5为wc硬质合金颗粒填充镶嵌在熔融的镍基耐磨合金内的耐磨机理。
[0033]
图6为粉末等离子弧堆焊原理示意图。
[0034]
图7为喷嘴的尺寸图。
[0035]
图8为氩弧焊与等离子电弧形态对比图。
[0036]
图9为氩弧焊与等离子电弧温度场示意图。
[0037]
图10为耐磨层的金相显微照片(1000μm单位)。
[0038]
图11为耐磨层的金相显微照片(100μm单位)。
[0039]
图中:
[0040]
00耐磨层,01碳化钨硬质合金颗粒,02熔合线,021脱碳层,03熔覆金属,04迎料面, 05 cr7c3和nib颗粒,
[0041]
10桨叶,
[0042]
20母材,
[0043]
图5中,31为钨极,32为合金粉末,33为喷嘴。
具体实施方式
[0044]
本实施例致力于强混机中使用的抗冲击桨叶的制造国产化,介绍一种桨叶耐磨层堆焊方法,该方法尤其是针对桨叶迎料面耐磨性能的研究,该桨叶迎料面耐磨制造解决方案的主要思路是:粉末等离子弧熔覆工艺+镍基耐磨合金+wc硬质合金颗粒(碳化钨硬质合金颗粒)。即,以粉末等离子弧熔覆工艺在桨叶的表面进行逐层堆焊,并将wc硬质合金颗粒填充镶嵌在熔融的镍基耐磨合金内,并尽可能的保证wc硬质合金颗粒在镍基耐磨合金中均匀的布置。
[0045]
现实中,wc硬质合金颗粒在堆焊过程中,在镍基耐磨合金中是非均匀的存在的,并非是理想的均匀存在,且焊接带来的高温会造成wc硬质合金颗粒内c原子(碳原子)的固态迁移。因此,本实施例在实施的过程中,存在的技术难点有二,其一,如何保证wc硬质合金颗粒弥散均匀分布,其二,如何避免高温堆焊对wc硬质合金颗粒带来的破坏,并尽量将破坏最小化。
[0046]
wc硬质合金颗粒:即,碳化钨硬质合金颗粒,其具有如下特点,熔点:2800-3000℃左右;颗粒度:60-100目(0.15-0.25mm);硬度hv1700-2200,耐磨性能仅次于金刚石,是耐磨材料中的上乘佳品。
[0047]
由于碳化钨硬质合金颗粒比重是普通碳钢的近一倍,所以在堆焊熔覆过程中总是有沉底现象(参考图4),大量的碳化钨硬质合金颗粒01沉积在熔合线02附近,这种非均匀的沉降对熔覆层与母材20的结合是非常不利的,可能造成熔覆层的整体脱落。同时,从耐磨角度出发,也希望碳化钨硬质合金颗粒在熔覆层厚度方向均匀分布,但是,现实中做到这一点是有难度的,这也是必须要面对的一个难题。
[0048]
关于碳化钨硬质合金颗粒01被破坏的机理:粉末等离子弧熔覆过程中,碳化钨硬质合金颗粒不可避免的会受损伤,尤其是碳化钨硬质合金颗粒的突出的尖角被熔化了,虽然硬质合金颗粒的其他形状平缓部分在高温熔池中并不熔化,但是,在高温作用下,碳化钨硬质合金颗粒的表面c原子(碳原子)存在固态迁移扩散现象。这种c原子固态迁移是不利因素,危害如下:
[0049]
其一,碳化钨硬质合金颗粒表面脱碳会导致耐磨层的耐磨性下降。
[0050]
其二,c原子的固态迁移扩散到基体金属(镍基耐磨合金)中,会造成堆焊单层的脆化,极易断裂、剥落,为不利因素。
[0051]
经过研究分析,这种固态迁移扩散现象完全杜绝是不可能的。能做的只是尽量减少硬质合金颗粒表面c原子的固态迁移,让碳化钨硬质合金颗粒的耐磨性能最大限度发挥出来,这需要对工艺进行修改。
[0052]
镍基耐磨合金:熔点低(1000℃左右)易熔化,与wc硬质合金颗粒融和性好,对碳不敏感,且可以固溶wc硬质合金颗粒中迁移扩散出来的c原子,这是选择镍基耐磨合金的原因。
[0053]
碳化钨硬质合金颗粒01起到抗磨损的骨架作用,是抗磨损主力军,参考图5,图5中箭头模拟的是强混机中物料对桨叶的冲击方向;镍基耐磨合金作为基体金属也是一种耐磨合金,同时充当“粘接剂”,即,把wc硬质合金颗粒黏合镶嵌固定在熔覆金属03(熔融的镍基耐磨合金)中;二者相互依存,是“唇齿”关系。耐磨性优劣取决于wc颗粒分布、面积占比;数量越多,分布均匀,则耐磨性越高。
[0054]
镍基耐磨合金与碳化钨硬质合金颗粒结合的磨损理论:
[0055]
例如,sio2、ai2o3作为一种常规磨料,硬度一般用莫氏硬度来表示,没有与wc硬质合金颗粒对比的相同单位,不能直接对比。不过在长期的生产实践中有经验认识,sio2、ai2o3硬度略低于wc硬质合金颗粒,ha/hm值在k2位置偏右一点,理论推断,wc硬质合金颗粒处于低磨损区。
[0056]
粉末等离子弧熔覆工艺:等离子弧能量集中(105-106w/cm2)、温度高(18000-24000℃)、高温停留时间短,对于母材和碳化钨硬质合金颗粒的影响小,是高能束其中的一种(其他两种是激光、电子束);节能节材,绿色低碳,属于环境友好型的熔覆工艺。
[0057]
氩弧焊与等离子电弧形态对比图参考图8。
[0058]
为了解决这些技术上的难点做了如下工作:
[0059]
总的原则是首先要调试出一种适合wc硬质合金颗粒进行堆焊的电弧,在此基础上摸索可行的工艺参数。此堆焊用的电弧不同于普通焊接,普通焊接电弧能量高、密度大、热量集中、加热范围小、穿透力强,可以穿透10mm厚的钢板,很显然不适合此堆焊工艺。
[0060]
从宏观上看,与焊接电弧相比较,堆焊电弧要柔性一些,电弧温度低一些,要规避高的电弧能量密度,也要规避强的穿透力(见图9)。过高的能量密度会造成wc硬质合金颗粒严重烧损而失去耐磨性,过强的穿透力会造成很高的稀释率耐磨性下降,这些都是wc硬质合金颗粒堆焊要避免的。国内目前还没有成熟的整套粉末等离子弧堆焊装备,也没有可以实用的工艺参数借鉴参考,针对wc硬质合金颗粒的堆焊技术难度高于通常的铁基、镍基、钴基合金粉末堆焊,要求的工艺条件更为苛刻,既要保障低稀释率,又要保障wc硬质合金颗粒尽可能少的烧损,最大限度把wc硬质合金颗粒优良的耐磨性发挥出来。
是合适的。
[0070]
三、焊枪
[0071]
焊枪的核心部件是喷嘴,喷嘴的核心是三个尺寸,压缩孔的孔道直径h、孔道长度l、压缩角度β(参考图7)。
[0072]
其中,孔道直径h小电弧压缩强,孔道长度l大电弧压缩加强,压缩角度β小电弧压缩强,反之则弱。本项目选择h=6mm孔径的喷嘴有三个考虑,一是倾向于获得一种柔性等离子弧,把焊接电弧的温度场拉低拉宽,电弧温度不要太高,有效加热面积大一点,有利于减少 wc烧损;二是获得一个大一点的熔池,减少送粉过程中合金粉末的损耗;特别是wc硬质合金颗粒,wc硬质合金颗粒比重大,形状不规则,多棱角,输送不顺畅,不可能都落在理论设计的落点上,10%-20%的wc硬质合金颗粒落到熔池之外损失掉了,熔池大可以减少损耗;镍基粉末和wc硬质合金颗粒价格都很昂贵,有效利用资源是必须考虑的重要问题;第三点是调整%落点到熔池的边缘区域,离电弧中心高温区远一点,有利于减少%烧损。孔径7mm时,压缩效果很弱,基本上可以定义为弱等离子,不可用;可用的孔径范围在5-6mm之间,没有多大的调整余地,5mm孔径粉末利用率会低一点,wc硬质合金颗粒烧损会多一点,于是选定喷嘴直径6mm。
[0073]
这样设备的硬件指标就确定下来,电源频率10k、空载电压90v、喷嘴尺寸h=6,l=6,β=60
°
,参考图7。80安培电流在试板上熔焊,熔池直径7mm左右,熔深0.5-1.0mm,电弧稳定、熔池平静,符合上述六点表述的要求。
[0074]
四、堆焊工艺参数
[0075]
工艺参数的选择要服务于减少wc硬质合金颗粒烧损这个主题。总的原则是快速、薄焊层、多层焊。堆焊速度快,熔池高温停留时间短,可以减少wc硬质合金颗粒烧损;氩弧焊、药芯焊丝电弧焊都曾有过wc硬质合金颗粒堆焊的案例,它们的电弧温度比等离子低很多,wc硬质合金颗粒都有不同程度的烧损,所以笔者认为熔池停留时间对wc硬质合金颗粒烧损有更大的影响,工艺参数应该偏重于在快速上下功夫;wc硬质合金颗粒比重大,进入熔池后向底部沉降是一个必然的趋势,薄焊层只是减缓这种趋势,并不能从根本上消除,堆焊层越厚沉降越严重。
[0076]
强混机桨叶堆焊层示意图,参考图2。
[0077]
实焊工艺参数:电流=90a、钨极直径d=3.2mm、内缩量l=6mm、喷嘴到工件高度=8mm、电压=28.5v、离子气q1=3.7l/min、送粉气q2=6l/min、堆焊速度=600mm/min,单层2mm。第二层第三层电流降低至80a,其他不变。
[0078]
wc硬质合金颗粒烧损的评判,在高温熔池中wc硬质合金颗粒突出尖角处熔化掉了,其余平缓表面的c原子向熔池中迁移而形成一个脱碳层(参考图2),这部分的耐磨性急剧下降,烧损程度通常以脱碳层厚度的大小来判断。其次是测试wc硬质合金颗粒的显微硬度,并同出厂原始硬度值相比较。
[0079]
堆焊材料包括:ni60合金粉末(即镍基耐磨合金),粒度60-120目。60%铸造wc(即 wc硬质合金颗粒),粒度60-80目,出厂硬度hv2100。
[0080]
采用上述工艺参数实际施焊,随机选取一个桨叶在耐磨层处取样分析。结果如下:
[0081]
宏观硬度平均值hrc63.7。高倍金相照片显示堆焊层中硬质相有wc颗粒、脱碳层和cr7c3、 nib,wc显微硬度平均值hv=1982,cr7c3显微硬度平均值hv=1326,nib显微硬度平
均值 hv=1153,三种硬质相面积占比60-70%左右,其中,cr7c3和nib颗粒度较小,在图中用05表示,繁星分布的白色细小颗粒是cr7c3和nib,其均匀的分布在熔覆金属03内。wc硬质合金颗粒烧损情况,从图11和图10中可以看出c硬质合金颗粒02的脱碳层021很薄,只有轻微烧损,耐磨性损失很少。
[0082]
从图10至图11中c硬质合金颗粒分布情况,从耐磨层横截面示意图中可以看出c硬质合金颗粒分布是上少下多的趋势,总体看还算均匀,复合要求。
[0083]
熔合线情况:从切开的试样横截面低倍照片上看出,熔合线是一条略带弯曲的曲线,耐磨层与母材结合良好,测试稀释率3-5%。
[0084]
耐磨层的耐磨性取决于硬质相的硬度、分布、数量,硬质相硬度高、分布均匀、数量多则耐磨性优良。高碳高铬耐磨合金硬质相cr7c3硬度同上,面积占比只有25-35%。二者相比,前者硬质相硬度高、数量多、优势明显。
[0085]
迎料面04耐磨层厚度设计为6mm,其余部位4mm,参考图2和图3,硬质合金颗粒40-60%重量比。
[0086]
本桨叶尤其适用于强混机,强混机可以应用于加气砖生产、钢铁行业、玻璃行业、橡胶行业。本技术桨叶采用粉末等离子弧熔覆工艺制造属于绿色制造范畴,初始制造时就埋下了再制造的基因,坯体可以重复使用3-4次,第二、三、四次再制造成本只有初始制造的1/4,对有效利用资源,减少温室气体排放、降低pm2.5浓度。
[0087]
实施例二
[0088]
作为进一步研究和实施例的方向,对wc硬质合金颗进行冷冻(降低c析出)预处理,具体来说,在焊接前,对碳化钨硬质合金颗粒进行液氮冷却预处理,具体来说,使用液氮对碳化钨硬质合金颗粒进行预冷处理,通过控制液氮用量使得碳化钨硬质合金颗粒的温度控制在
ꢀ-
20
°
至0
°
之间,通过预冷处理,将颗粒的温度降低至合理水平,以抵消粉末等离子弧熔覆工艺高温对碳化钨硬质合金颗粒的不利影响,使得在高温作用下,碳化钨硬质合金颗粒的表面碳原子的固态迁移扩散现象得以有效的进一步被遏制。
[0089]
惟以上所述者,仅为本实用新型的具体实施例而已,当不能以此限定本实用新型实施的范围,故其等同组件的置换,或依本实用新型专利保护范围所作的等同变化与修改,皆应仍属本实用新型权利要求书涵盖之范畴。