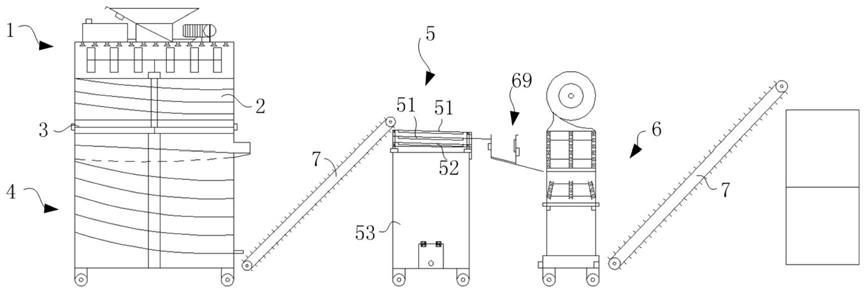
1.本实用新型涉及造粒设备技术领域,具体涉及一种造粒设备。
背景技术:2.造粒设备是一种可将物料造成特定形状的成型设备,可将物料制备成颗粒状结构,如在对重金属污染的土壤进行修复时,可向土壤中添加改良材料使重金属向低溶解、被固定、低毒形态转化,达到降低污染土壤重金属有效性和环境风险的方法。但是土壤钝化材料大多为粉末状的固体颗粒,在进行农业生产过程中,其很难像施加肥料一样加入土壤中,因为可能部分钝化材料为质地较轻,如改性后的粉煤灰等,在自然风下,会形成粉尘,无法均匀有效地添加到土壤中,从而无法对重金属污染的土壤进行稳定化修复,而通过造粒设备将土壤钝化材料制备成颗粒状结构时,便于对土壤进行修复操作。
3.而如何提供一种结构简单、占用空间小且能够获得均匀粒径的颗粒物料的造粒设备,是本领域技术人员所需要解决的技术问题。
技术实现要素:4.本实用新型的目的是提供一种造粒设备,结构简单、占用空间小且能够获得均匀粒径的颗粒物料。
5.为解决上述技术问题,本实用新型提供一种造粒设备,其包括由上至下依次设置的混合装置、推送装置、成型装置和干燥装置;所述混合装置包括混合箱以及设于所述混合箱内的搅拌部,所述混合箱设有加料口;所述成型装置包括驱动部、成型板和刮刀,所述成型板设有成型孔,所述驱动部能够驱动所述刮刀沿成型板的端面移动;所述推送装置能够将经过所述混合装置混合后的物料推动至所述成型装置,并将所述物料挤压至所述成型孔内,所述刮刀能够沿所述成型板的端面移动并切割穿过所述成型孔的所述物料,以获得物料颗粒;所述干燥装置位于所述成型装置的下方,所述物料颗粒能够下落至所述干燥装置,所述干燥装置包括用于对所述物料颗粒进行干燥的干燥部。
6.通过该造粒设备对物料进行造粒的过程中,混合装置自动对物料进行搅拌混合,然后推送装置自动将混合后的物料推送至成型装置即可成型物料颗粒,通过干燥部对物料颗粒进行干燥,结构简单且自动化程度高,无需人工操作,有效降低成本,并且混合装置、推送装置、成型装置和干燥装置均是由上至下依次设置的,能够有效减小整体占用空间,便于现场布置。
7.优选地,所述混合装置还包括液料箱、计量泵和管路,所述管路连通于所述液料箱和所述混合箱之间并设有喷嘴,所述计量泵用于控制所述管路的流量;所述加料口还设有斜板和斜板电机,所述斜板电机能够驱动所述斜板移动以调节所述加料口的开度。
8.优选地,所述成型板沿预设方向设有至少两排成型孔;所述驱动部包括驱动件和驱动杆,所述刮刀与所述驱动杆连接,所述驱动件能够通过所述驱动杆驱动所述刮刀沿所述成型板的端面向预设方向移动。
9.优选地,所述驱动件为电机,所述驱动部的数量为两组,且两组所述驱动部的电机的驱动方向相反,且两组所述驱动部的驱动杆分别与预设方向平行设置。
10.优选地,所述成型板和所述驱动部可拆卸连接。
11.优选地,所述干燥装置包括收集板和输送槽,所述收集板位于所述成型装置的下方,所述收集板的上端面设有倾斜面,落入所述收集板的所述物料颗粒能够在重力的作用下沿所述倾斜面滑动至所述输送槽,所述输送槽包括多条并列设置的滑道,所述物料颗粒能够沿所述滑道滑动。
12.优选地,各所述输送槽呈螺旋形结构布置,并且所述滑道的宽度由上至下逐渐减小,所述物料颗粒能够在自身重力的作用下沿所述滑道滑动。
13.优选地,还包括与所述干燥装置连接的振筛装置,所述振筛装置包括两层筛网和位于所述筛网下方的集料板,位于上层的所述筛网的孔径大于位于下层的所述筛网的孔径。
14.优选地,还包括分装装置,所述分装装置包括支架以及设于所述支架的转轴、剪切部、动作部和缝合部;所述转轴可转动地连接于所述支架,且所述转轴的外壁缠绕有袋卷;所述动作部的顶端能够穿入所述袋卷的开口端,并带动所述开口端向下移动;所述剪切部位于所述动作部的上方,用于剪切所述袋卷,以形成包装袋;所述缝合部位于所述动作部的下方,所述缝合部能够缝合所述包装袋的开口。
15.优选地,还包括进料部,所述进料部的下料口位于所述剪切部和所述动作部之间,所述进料部用于向所述包装袋的顶端开口内加入物料;所述进料部包括上挡料板、下挡料板和驱动件,所述上挡料板和所述下挡料板之间围合形成存料区,所述驱动件能够分别驱动所述上挡料板和下挡料板移动,以启闭所述存料区。
16.优选地,所述进料部包括上挡料板、下挡料板和驱动件,所述上挡料板和所述下挡料板之间围合形成存料区,所述驱动件能够分别驱动所述上挡料板和下挡料板移动,以启闭所述存料区;所述存料区的底部设有称重单元;和/或,所述下挡料板还设有位置传感器
附图说明
17.图1是本实用新型实施例所提供的造粒设备的结构示意图;
18.图2是混合装置、成型装置和干燥装置的结构示意图;
19.图3是成型装置的结构示意图;
20.图4是干燥装置的俯视图;
21.图5是分装装置的结构示意图;
22.图6是图5中动作部的结构示意图;
23.图7是图6中各导杆的结构示意图。
24.附图1
‑
7中,附图标记说明如下:
[0025]1‑
混合装置,11
‑
混合箱,12
‑
搅拌部,13
‑
加料口,131
‑
斜板,132
‑
斜板电机,14
‑
液料箱,15
‑
计量泵,16
‑
喷嘴;
[0026]2‑
螺旋推送杆;
[0027]3‑
成型装置,31
‑
驱动件,32
‑
驱动杆,33
‑
成型板,34
‑
成型孔,35
‑
刮刀,36
‑
激光感应器;
[0028]4‑
干燥装置,41
‑
干燥部,42
‑
收集板,43
‑
输送槽,44
‑
滑道,441
‑
滑道出口;
[0029]5‑
振筛装置,51
‑
筛网,52
‑
集料板,53
‑
回收箱;
[0030]6‑
分装装置,61
‑
支架,62
‑
转轴,63
‑
剪切部,64
‑
动作部,641
‑
伸缩组件,6411
‑
伸缩杆,642
‑
驱动轮,643
‑
导向件,644
‑
导杆,645
‑
驱动电机,646
‑
传动杆,647
‑
传动齿轮,648
‑
传动轴,65
‑
缝合部,66
‑
袋卷,661
‑
开口端,67
‑
托盘,68
‑
导向部,69
‑
进料部,691
‑
上挡料板,692
‑
存料区,693
‑
下挡料板,694
‑
驱动件,695
‑
称重单元,696
‑
位置传感器;
[0031]7‑
输送部。
具体实施方式
[0032]
为了使本领域的技术人员更好地理解本实用新型的技术方案,下面结合附图和具体实施例对本实用新型作进一步的详细说明。
[0033]
本实用新型实施例提供了一种造粒设备,如图1所示,该造粒设备包括由上至下依次设置的混合装置1、推送装置、成型装置3和干燥装置4,其中,混合装置1包括混合箱11以及设于混合箱11内的搅拌部12,混合箱11设有加料口13,搅拌部12能够对加入至混合箱11内的物料进行搅拌混合,推送装置用于将搅拌混合后的物料推送至成型装置3内,该成型装置3能够使混合后的物料成型颗粒状,然后由干燥装置4对颗粒物料进行干燥以使其形状稳定。
[0034]
其中,物料包括固体物料和液体物料,其中固体物料可以是粉末状物料也可以是颗粒状物料均可,液体物料可以是药剂,用于与固体物料混合作用,或者该液体物料也可以是仅用于辅助固定物料成型的液体,在此不做具体限制。
[0035]
具体的,成型装置3包括驱动部、成型板33和刮刀35,其中,成型板33设有成型孔34,刮刀35能够在驱动部的驱动作用下沿成型板33的下端面移动,推送装置能够将经过混合装置1混合后的物料推送至成型装置3,并将混合后的物料挤压至成型板33,物料在挤压力的作用下能够进入成型孔34内,并由成型孔34穿过成型板33以形成与成型孔34的形状相适配的条状物料,然后刮刀35可沿成型板33的端面移动,并从成型板33的下端面将条状物料切断,以获得物料颗粒,干燥装置4位于成型装置3的下方,物料颗粒在被刮刀35割断后会在重力的作用下自动下落至干燥装置4内,干燥装置4的干燥部41能够对物料颗粒进行干燥,使其状态稳定,以避免后期颗粒物料彼此之间发生粘连或变形的情况。
[0036]
通过该造粒设备对物料进行造粒的过程中,混合装置1自动对物料进行搅拌混合,然后推送装置自动将混合后的物料推送至成型装置3即可成型物料颗粒,通过干燥部41对物料颗粒进行干燥,结构简单且自动化程度高,无需人工操作,有效降低成本,并且混合装置1、推送装置、成型装置3和干燥装置4均是由上至下依次设置的,能够有效减小整体占用空间,便于现场布置。
[0037]
具体的,本实施例中,对于推送装置不做限制,其主要是将混合后的物料推送至成型装置3即可,该推送装置可设置为螺旋推送杆2,该螺旋推送杆2位于混合装置1的下方,混合装置1的底部设有开关阀,当混合装置1内的物料混合均匀后,开关阀开启,物料从上方落入螺旋推送杆2,螺旋推送杆2可通过螺旋挤压力将混合后的物料推送至成型装置3,结构较为简单。
[0038]
如图2所示,混合装置1还包括液料箱14、计量泵15和管路,其中,液料箱14用于放
置液体物料,管路连通于液料箱14和混合箱11之间,该管路设有多个喷嘴16,计量泵15用于控制管路内的液体物料的流量,从而能够精准地控制从喷嘴16喷入混合箱11内的液体物料的加入量,加料口13还设有斜板131和斜板电机132,其中,斜板电机132能够驱动斜板131移动以调节加料口13的开度,从而调节固体物料的加入量,从而保证混合物料的成分的精确性、均匀性和一致性。也就是说,固体物料从加料口13加入,液体药剂从喷嘴16喷入,各加入量均可得到精准控制,然后通过搅拌部12进行搅拌混合。
[0039]
并且,当对不同配比或不同成分的物料进行造粒时,可先将液料箱14内放置清洗水,通过计量泵15控制加大管路内的清洗水的流量,从而实现对液料箱14、管路以及混合箱11的清洗,并且由于清洗水会在自身重力作用下向下流动至成型装置3和干燥装置4内,以完成清洗,在此过程中,无需人工进行清洗操作,自动化程度高、使用方便。
[0040]
如图3所示,成型板33沿预设方向设有至少两排成型孔34,驱动部包括驱动件和驱动杆32,其中,驱动杆32与刮刀35固定,驱动件能够驱动驱动杆32沿成型板33的端面向预设方向移动,从而带动刮刀35沿成型板33的端面向预设方向移动,以对穿过成型孔34的条状物料进行切割。具体的,驱动孔呈至少两排布置,刮刀35在移动的过程中,能够同时切割一排成型孔34处的物料,如此设置能够提高物料切割效率。具体的,成型孔34的排数以及各排成型孔34设有的成型孔34数量均不作限制,同时,对于刮刀35的数量也不做限制,如图3所示,可以是刮刀35的数量与成型孔34的排数相同,并且各刮刀35沿预设方向并列布置,如此设置,每个刮刀35在驱动部的作用下仅需切割一排成型孔34处的物料即可完成此次切割,如此能够保证同一批切割的物料颗粒的尺寸相同,且切割效率较高。
[0041]
具体的,本实施例中,对于驱动件的具体结构并不做限制,如图3所示,驱动件为电机,驱动杆32包括齿条结构,电机能够通过齿轮与齿条结构配合,以带动驱动杆32移动,或者,还可将驱动杆32设置为包括丝杆结构,电机通过螺母与丝杆配合,以带动丝杆沿预设方向移动。具体的,驱动部的数量为两个,两个驱动部的驱动杆32平行设置,并且这两个驱动部的驱动方向相反,如图3所示,两个驱动杆32能够在各自配合的电机的驱动作用下分别沿相反的两个方向移动,这两个驱动杆32都与上述预设方向平行设置,从而带动刮刀35沿成型板33的端面往复运动,以对物料进行切割,如此设置,两个电机可选用单向电机,当然也可以通过一个双向电机实现刮刀35的往复运动,而两个单向电机的设置能够降低对电机的要求,两个单向电机间歇式工作,能够延长单个电机的使用寿命、增强设备的可靠性。或者,本实施例中,还可以将驱动件设置为气缸、液压缸等均可。
[0042]
成型板33和驱动部可拆卸连接,如此一来,当需要的物料颗粒的粒径不同或者形状不同时,可更换设有对应成型孔34的成型板33即可,驱动部和刮刀35无需更换,灵活性好。
[0043]
该成型装置3还包括激光感应器36,该激光感应器36设于成型板33的下端面,用于监测条状物料的长度,以便于刮刀35切割后的物料颗粒的尺寸一致,或者,还可以是驱动部根据设定时间间隔对物料进行切割均可,在此不做具体限制。
[0044]
如图2和图4所示,干燥装置4包括收集板42和输送槽43,其中,收集板42位于成型装置3的下方,收集板42的上端面设有倾斜面,物料颗粒在落入收集板42后,能够在自身的重力作用下沿倾斜面移动至输送槽43,该输送槽43包括多条并列设置的滑道44,颗粒物料能够沿倾斜面移动至各滑道44内,并沿各滑道44滑动以实现输送,由于各滑道44并排设置,
因此,当颗粒物料在进入输送槽43时,能够分别进入各滑道44内,避免物料颗粒在沿输送槽43滑动的过程中发生多数颗粒粘连的情况。
[0045]
如图2和图4所示,输送槽43呈螺旋形结构布置,并且滑道44的宽度也是由上至下逐渐变窄的,各滑道44的顶端与收集板42连接,物料颗粒能够在自身的重力作用下由倾斜面滑动至滑道44的顶端,并沿各滑道44由上至下做螺旋形滑动,由于螺旋形滑动,坡度较缓,能够防止同一滑道44内各物料颗粒之间的相互挤压,滑道44的侧壁能够与各物料颗粒之间产生相互作用,通过各物料颗粒之间的摩擦力以及滑道44侧壁与物料颗粒之间的摩擦力,能够使得物料颗粒的棱角被打磨,使其在沿滑道44滑动至底端时,棱角基本磨平,形成球形或椭球型结构,如此相较于设有棱角的物料颗粒来说,便于后期使用。由于滑道44的宽度逐渐变窄,物料颗粒在沿滑道44滑动的过程中,能够加强滑道44的侧壁对物料颗粒的作用,从而有利于对物料颗粒的棱角的打磨。
[0046]
并且,物料颗粒在沿滑道44滑动的过程中,干燥部41能够对物料颗粒进行干燥,因此坡度较缓的螺旋形滑道44能够增加干燥部41的作用时间,保证干燥效果,使得物料颗粒在滑落至滑道44的底部时,能够形成稳定的物料颗粒。具体的,干燥部41可以是热风机,用于向干燥装置4内吹热风,以使得物料颗粒干燥,或者,该干燥部41还可以是设于滑道44侧壁的加热装置,如滑道44的侧壁、底壁等内部设置有加热丝,通过加热丝加热使得物料颗粒干燥均可,在此不做具体限制。
[0047]
如图1所示,该造粒设备还包括与干燥装置4连接的振筛装置5,干燥装置4内的物料在沿滑道44滑动的过程中被干燥后成型稳定,然后由滑道出口441经过输送部7进入振筛装置5进行筛分。具体的,该振筛装置5包括两层筛网51和一层集料板52,其中,两层筛网51位于集料板52的上方,并且位于上方的筛网51的孔径要大于位于下方的筛网51的孔径,如此设置,物料在进入振筛装置5后,较大颗粒的物料将会被上层筛网51过滤,并留在上层筛网51,而较小颗粒的物料将会经过第二层筛网51并下落至集料板52,而留在第二层筛网51的物料颗粒的大小则满足要求,保证各物料颗粒的均匀性和一致性,可进入下一步分装操作。具体的,可将该第二层筛网51倾斜设置,其朝向分装装置6的一侧位置要低于朝向干燥装置4的一侧,以便于物料颗粒在自身重力的作用下移动至分装装置6。
[0048]
振筛装置5还包括回收箱53,该回收箱53设于集料板52的下方,最上层的筛网51内的物料颗粒以及集料板52收集的物料颗粒均可输送至该回收箱53统一回收处理。
[0049]
如图1所示,该造粒设备还包括分装装置6,该分装装置6设于振筛装置5之后,可将粒径符合要求的物料颗粒分装入包装袋内,具体的,如图5所示,该分装装置6包括支架61以及设于该支架61的转轴62、剪切部63、动作部64和缝合部65,其中,转轴62可转动地连接于支架61,并且该转轴62的外壁缠绕有袋卷66,动作部64的顶端能够穿入该袋卷66的开口端661,并带动开口端661向下移动,剪切部63位于动作部64的上方,用于沿横向剪切袋卷66,以形成独立的包装袋,该缝合部65位于动作部64的下方,缝合部65能够沿横向缝合包装袋的开口(具体包括上开口和下开口)。
[0050]
详细的讲,在通过该分装装置6对物料进行分装时,动作部64的顶端能够穿入袋卷66的开口端661,并带动该开口端661向下移动,此时,袋卷66作用于转轴62使其相对于支架61转动,当开口端661向下移动至预设距离后,剪切部63从上方将袋卷66剪开,即可形成一个独立的包装袋,该包装袋套设于动作部64外,缝合部65可从底端对该包装袋的下开口进
行缝合,此时,该包装袋的底端缝合、动作部64位于其内部并将其撑开,包装袋的上开口处于打开状态,可从上方向其内部加入物料,物料加入完成后,动作部64继续动作并带动包装袋向下移动,直至动作部64与包装袋脱离,此时,可通过缝合部65对包装袋的顶端进行缝合,以完成该一个包装袋的物料分装操作,然后即可进入下一个包装袋的物料的分装操作即可。
[0051]
通过该分装装置6可将袋卷66自动裁剪成独立的包装袋,并在物料装入包装袋后,可对各包装袋进行缝合,自动化程度高,无需人工对包装袋进行操作,省时省力且效率较高,由于是自动化操作,因此,可保证各包装袋的大小一致,产品一致性好。同时还能够避免在对物料进行分装操作的过程中,产生粉尘污染对工作人员造成的健康隐患,提高安全性。
[0052]
在上述实施例中,如图5所示,该分装装置6还包括托盘67,该托盘67设于缝合部65的下方,当缝合部65将包装袋的下开口缝合后,动作部64可继续作用于包装袋使其向下移动至包装袋的底部与托盘67抵接,此时,向包装袋内加入物料时,托盘67能够对该包装袋提供支撑,从而减小对动作部64与包装袋之间的作用力的要求。
[0053]
动作部64包括伸缩组件641,该伸缩组件641包括两条相互交叉设置的伸缩杆6411,每根伸缩杆6411的两端分别设有驱动轮642,驱动轮642能够贴合于包装袋的内壁,并且驱动轮642能够通过转动能够带动包装袋向下移动,当然,本实施例中,对于该动作部64的具体结构并不做限制,如还可以是动作部64还设有移动件,该移动件能够沿竖直方向移动,并带动包装袋向下移动即可,而通过驱动轮642的转动带动包装袋移动时,该驱动轮642是与包装袋的内壁贴合的,而中部位置是通过伸缩杆6411支撑的,能够将包装袋撑开的同时,不会影响向包装袋内装入物料。并且,伸缩杆6411还能够通过伸缩调节其长度,从而调节包装袋的开口,适用于不同尺寸规格的包装袋,灵活性好。
[0054]
进一步的,该动作部64还包括导向件643,伸缩组件641的数量为两组,并且两组伸缩组件641沿该导向件643的轴向间隔布置,导向件643的轴向沿竖直方向设置,该导向件643的设置能够对两组伸缩组件641提供导向,使得各伸缩杆6411的中心位置在同一竖直方向的轴线上,两组伸缩组件641同时作用于包装袋,能够提高动作部64的作用力。并且,两组伸缩组件641沿高度方向间隔设置,位于上方的伸缩组件641的两根伸缩杆6411均处于伸展状态,以将经过的包装袋均匀撑开,位于下方的伸缩组件641可通过一根伸缩杆6411收缩,另一根伸缩杆6411伸展,以将包装袋的开口支撑形成长条形状,然后缝合部65能够沿长条形状缝合,便于缝合操作。
[0055]
更进一步的,两组伸缩组件641之间还连接有四根导杆644,每根伸缩杆6411的端部分别与一根导杆644连接,也就是说,每组伸缩组件641包括两根导杆644,这两根导杆644有四个端部,每个端部分别与一根导杆644对应连接,每根导杆644沿其轴向设有多个上述驱动轮642,如此设置,能够进一步提高驱动轮642的数量,进而提高该动作部64对包装袋的驱动力。
[0056]
如图6和图7所示,每根导杆644还设有驱动电机645、传动杆646、传动齿轮647和传动轴648,其中,传动轴648与驱动轮642同轴传动,传动齿轮647设于传动杆646和传动轴648之间,驱动电机645能够驱动传动杆646转动,该传动杆646的转动能够通过传动齿轮647带动传动轴648转动,进而带动驱动轮642转动,如图7所示,导杆644包括框架结构,其中该框架结构的一个边框能够沿其轴向转动,该边框形成上述传动杆646,驱动电机645可直接驱
动该传动杆646转动也可以通过齿轮传动驱动该传动杆646转动,而该传动杆646的转动可通过传动齿轮647传动带动传动轴648转动。如此设置,可通过一个驱动电机645驱动位于同一个导杆644的所有的驱动轮642转动,可简化整体结构。具体的,传动齿轮647可以是一个齿轮也可以是多个齿轮的齿轮组,在此不做具体限制。
[0057]
如图5所示,该分装装置6还包括导向部68,该导向部68位于转轴62和剪切部63之间,具体的,该导向部68位于袋卷66的开口端661内,以将袋卷66的开口端661撑开,剪切部63设于该导向部68的下方,当剪切部63将袋卷66剪切以形成包装袋后,导向部68始终位于该袋卷66内,如此设置,使得在剪切部63剪切后,该袋卷66的开口端661始终处于撑开的状态,便于动作部64进入袋卷66的开口端661内,并且,导向部68也能够驱动袋卷66的开口端661使其向下移动,直至动作部64进入袋卷66的开口端661内,全程无需人工操作,自动化程度高。
[0058]
在上述实施例中,该分装装置6还包括进料部69和驱动件,该进料部69的下料口位于剪切部63和动作部64之间,该进料部69用于向包装袋的上开口内加入物料,具体的,该进料部69包括上挡料板691和下挡料板693,上挡料板691和下挡料板693均用于阻挡物料,并在二者之间形成存料区692,驱动件能够分别驱动上挡料板691和下挡料板693移动以启闭该存料区692。
[0059]
也就是说,物料在沿进料部69进入包装袋内之前,可预先存储于存料区692,上挡料板691打开时,下挡料板693关闭,此时,物料可进入存料区692内暂存,当无法进入包装袋内,当存料区692内的物料达到一定量后,驱动件驱动上挡料板691关闭,并将下挡料板693开启,此时,外部物料无法进入存料区692内,而存料区692内暂存的一定量的物料可通入包装袋内,然后再通过驱动件驱动下挡料板693关闭,上挡料板691开启,外部物料再进入存料区692内暂存,以为下一个包装袋的装料做准备。
[0060]
如此设置,能够使得进入每一个包装袋内的物料量均相同,无需人工操作即可完成,省时高效且产品一致性好。并且,当动作部64驱动包装袋向下移动或缝合部65在对包装袋进行缝合的过程中,物料可被准备在存料区692内,省时高效。具体的,对于驱动件的具体结构不做限制,如可将其设置为气缸、液压缸或电机丝杆等均可。并且,驱动件可以设置为一个,通过一个驱动件驱动上挡料板691和下挡料板693的升降,或者还可以将驱动件的数量设置为两个,分别驱动上挡料板691和下挡料板693的升降均可。
[0061]
该存料区692的底部还设有称重单元695,当称重单元695的称重结果表明存料区692内的物料达到预设目标时,上挡料板691封堵存料区692,驱动件可开启下挡料板693。或者,下挡料板693还设有位置传感器696,当存料区692内的物料达到一定高度时,位置传感器696能够获知该物料的高度,下挡料板693可在驱动件的作用下开启即可。或者,本实施例中,还可以是存料区692内设有称重传感器的同时,下挡料板693设置有位置传感器696均可。如此设置,能够保证分装于各包装袋内的物料量一致,精确度高。
[0062]
综上,通过该分装装置6对物料进行分装时,袋卷66的开口端661的导向部68的作用下向下移动,直至动作部64的顶端伸入开口端661内,然后动作部64带动开口端661继续向下移动至预设位置后,动作部64停止动作,位于下方的伸缩组件641的一根伸缩杆6411伸展、另一根伸缩杆6411收缩,使得该开口端661形成长条形状,缝合部65对其进行缝合,然后处于收缩的伸缩杆6411伸展,动作部64继续动作直至缝合后的开口端661与位于下方的托
盘67抵接时,剪切部63从上方将剪裁袋卷66(或者,本实施例中,还可以通过设置激光位置传感器696,监测袋卷66的开口端661的位置,并通过剪切部63对袋卷66进行剪裁操作),使得位于下方的部分形成独立的包装袋,此时,该包装袋的底部缝合,顶部被动作部64的伸缩组件641撑开,在上述形成独立包装袋的过程中,进料部69的存料区692内存储有一定量的物料,然后通过驱动件驱动下挡料板693移动以打开存料区692,使得存料区692内的物料沿包装袋的顶端开口进入包装袋内,然后将位于包装袋顶端开口处的伸缩组件641的一根伸缩杆6411伸展、另一根伸缩杆6411收缩,包装袋的顶部形成长条状,通过缝合部65对其进行缝合即可完成一袋物料的分装。不难理解,当缝合部65在对包装袋的上开口进行缝合操作时,伸缩杆6411仍然对包装袋的上开口提供支撑,因此,缝合位置位于伸缩杆6411的下方。在物料分装完成后,可通过输送部7传送至指定位置即可。
[0063]
通过本实施例所提供的造粒设备,能够将固体物料和药剂在自动混合后通过推送、切割、干燥、筛分、分装,全程无需人工操作,具体可通过单片机设定的程序进行运作,可以通过应用程序和互联网,借助远程终端等对本设备进行监控和管理,符合“智能物联”设计理念,而如何通过程序控制各电气部件的运行,对于本领域技术人员来说,已是熟知的现有技术,为节约篇幅,在此不再赘述。也就是说,整个造粒设备为一条完整的工业生产线,自动化程度高。
[0064]
以上仅是本实用新型的优选实施方式,应当指出,对于本技术领域的普通技术人员来说,在不脱离本实用新型原理的前提下,还可以做出若干改进和润饰,这些改进和润饰也应视为本实用新型的保护范围。