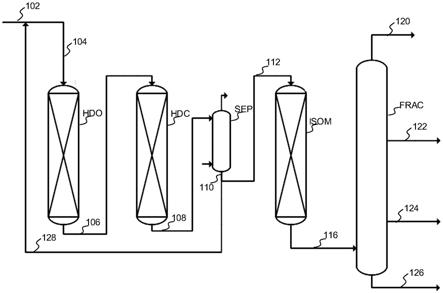
联合生产航空燃料和柴油的方法
1.迄今为止,加氢处理中含氧化合物(如可再生能源)的转化一直集中在制造柴油上,因为链烷烃对应于生物材料的典型脂肪酸,如植物油和动物脂肪(c14、c16和c18),通常沸点为250℃至320℃,与沸点为150℃至380℃的典型柴油产品充分相对应。喷气燃料产品的沸点范围为120℃至300℃,这意味着需要将一定量的来自可再生原料的链烷烃重质部分转化为较轻质的材料,以仅生产喷气燃料。本公开涉及通过选择性地将重质材料转化为较轻质的材料而具有高收率的满足典型的产品要求的液体运输燃料、特别是可再生柴油和可再生喷气燃料的混合物的方法。
2.在设计用于制造柴油的单元中对可再生原料进行加氢处理期间,经常还会产生一定量的喷气燃料。但是,人们希望将沸点主要在柴油范围内的可再生原料的中间产物灵活且良好受控地转化为喷气燃料产品,这需要大量转化。
3.控制源自经加氢处理的酯和脂肪酸的喷气燃料的质量的标准是astm d7566,a2.1,其中特别规定了沸点曲线和组成。这些特性中的大多数都可以通过加氢处理和分馏而容易实现。但是,要特别注意满足最高
‑
40℃的凝固点(fp)要求,以及最多0.5wt/wt%的总芳烃含量。此外,该标准通过要求t
10
(即低于该温度,10%发生沸腾)低于205℃而要求一定量的低沸点产品。根据astm d86,最终沸点(fbp)规定为300℃,这意味着所有沸点高于300℃的材料都必须转化为较轻质的组分,以落入喷气燃料范围。
4.现在,根据本公开,提出以两阶段构造进行柴油和喷气燃料的联合生产,其中在第一阶段对进料进行加氢脱氧和加氢裂化,并且在除去酸性气体之后对产物进行异构化以及可能的加氢脱芳烃,最后进行分馏。通过这种方法,可以在第一阶段用较便宜的贱金属催化剂进行加氢裂化,而在选择的贵金属催化剂上可以进行异构化,从而导致特定的凝固点降低。如果芳烃的量太高,则可以优化异构化条件以同时除去芳烃,或者为此目的可以提供特定的加氢脱芳烃催化剂。
5.在下文中,术语阶段用于该方法的一个工段,其中不执行任何分离。
6.在下文中,缩写ppm
v
用于表示每百万份的体积份数,例如摩尔气体浓度。
7.在下文中,缩写ppm
molar
用于表示每百万份的原子份数。
8.在下文中,缩写wt/wt%用于表示重量百分比。
9.在下文中,缩写vol/vol%用于表示气体的体积百分比。
10.在下文中,术语可再生原料或烃用于表示源自生物来源或废物再循环的原料或烃。化石来源的再循环废物,例如塑料,也应解释为可再生的。
11.在下文中,术语加氢脱氧用于表示在氢存在下通过形成水从含氧化合物中除去氧,以及在氢存在下通过形成碳氧化物而从含氧化合物中除去氧。
12.在下文中,术语分子筛的拓扑结构以"atlas of zeolite framework types,"sixth revised edition,elsevier,2007中描述的含义使用,并且据此使用三字母的骨架类型编码。
13.本公开的一个广泛方面涉及一种由为含氧化合物原料的原料生产适合用作喷气燃料的烃馏分的方法,该方法包括以下步骤:将原料与一定量的液体稀释剂混合,以形成混
合原料;引导所述混合原料在加氢处理条件下与在加氢脱氧中具有催化活性的材料接触,以提供经加氢脱氧的中间产物;引导至少一定量的所述经加氢脱氧的中间产物在加氢裂化条件下与在加氢裂化中具有催化活性的材料接触,以提供经加氢裂化的中间产物;将所述经加氢裂化的中间产物分离成至少两个馏分,包括蒸汽馏分和液体馏分;任选地提供至少一定量的所述经加氢裂化的液体产物作为所述液体稀释剂;引导至少一定量的所述经加氢裂化的液体产物在异构化条件下与在异构化中具有催化活性的材料接触,以提供经异构化的中间产物;以及使所述经异构化的中间产物分馏,以提供至少所述适合用作喷气燃料的烃馏分,其具有的相关益处在于,所述方法非常适合于将高沸点的可再生原料高效地转化为较低沸点的产物,例如非化石煤油。除了所述适合用作喷气燃料的烃之外,还可以生产柴油和其他烃。
14.在另一个实施方案中,所述适合用作喷气燃料的烃馏分的最终沸点根据astm d86为小于300℃,其具有的相关益处在于,所述方法的产物满足可再生喷气燃料规范astm d7566的沸点规范。
15.在另一个实施方案中,任选地通过添加包含一种或多种含硫化合物例如二甲基二硫化物或化石燃料的料流,使相对于被引导以与在加氢脱氧中具有催化活性的材料接触的混合原料的气相中分子氢的体积,硫化氢的总体积为至少50ppm
v
、100ppm
v
或200ppm
v
,其具有的相关益处在于,所述方法可以用低成本的在加氢脱氧中具有催化活性的材料来高效运行,所述材料包含硫化贱金属。
16.在另一个实施方案中,所述原料包含至少50wt/wt%的甘油三酯或脂肪酸,其具有的相关益处在于,这样的原料高度适合于提供具有优异性能的喷气燃料。
17.在另一个实施方案中,加氢脱氧条件包括温度区间为250
‑
400℃,压力区间为30
‑
150bar和液时空速(lhsv)区间为0.1
‑
2;并且其中在加氢脱氧中具有催化活性的材料包括负载在载体上的一种或多种硫化的选自镍、钴、钼或钨镍、钼或钨的金属,所述载体包括一种或多种耐热(refractory)氧化物,例如氧化铝、二氧化硅或二氧化钛,其具有的相关益处在于,所述工艺条件非常适合以成本有效的方式从可再生原料去除杂原子,尤其是氧。
18.在另一个实施方案中,加氢裂化条件包括温度区间为250
‑
425℃,压力区间为30
‑
150bar以及液时空速(lhsv)区间为0.5
‑
4,任选地与通过用冷的氢、进料或产物的骤冷进行的中间冷却一起,并且其中在加氢裂化中具有催化活性的材料包括:(a)选自铂、钯、镍、钴、钨和钼的一种或多种活性金属;(b)酸性载体,其选自显示高裂化活性并具有例如mfi、bea和fau的拓扑结构的分子筛和无定形酸性氧化物,例如二氧化硅
‑
氧化铝;和(c)耐热载体,例如氧化铝、二氧化硅或二氧化钛,或其组合,其具有的相关益处在于,所述工艺条件高度适合于降低产物的沸点以匹配煤油的沸点范围。
19.在另一个实施方案中,与所述经加氢脱氧的中间产物相比,所述经加氢裂化的中间产物中沸点高于300℃的材料的量减少了至少20wt/wt%、50wt/wt%或80wt/wt%或更多,其具有的相关益处在于,由于高的工艺严苛性,高转化率使沸点高于300℃的产物最小化。
20.在另一个实施方案中,引导至少一定量的所述经异构化的中间产物在加氢脱芳烃条件下与在加氢脱芳烃中具有催化活性的材料接触,以提供包含少于1wt/wt%、0.5wt/wt%或0.1wt/wt%的经加氢脱芳烃的产物,所述值是基于芳烃分子总质量相对于料流中所
有烃计算的,其中分馏的是所述经加氢脱芳烃的产物,而不是所述经异构化的中间产物,具有的相关益处在于,所述方法的产物满足喷气燃料规范astm d7566。所述在加氢脱芳烃条件下在加氢脱芳烃中具有催化活性的材料可以是在有利于加氢脱芳烃的适度温度下运行的加氢裂化中具有催化活性的材料或在异构化中具有催化活性的材料。加氢脱芳烃条件优选包括至少50%或80%的芳烃转化率。
21.在另一个实施方案中,加氢脱芳烃条件包括温度区间为200
‑
350℃,压力区间为30
‑
150bar以及液时空速(lhsv)区间为0.5
‑
8,其中所述在加氢脱芳烃中具有催化活性的材料包含活性金属,其选自铂、钯、镍、钴、钨和钼,优选一种或多种单质贵金属,例如铂或钯;以及耐热载体,优选无定形二氧化硅
‑
氧化铝、氧化铝、二氧化硅或二氧化钛,或其组合,具有的相关益处在于,所述工艺条件适合用于芳烃的加氢。
22.在另一个实施方案中,引导包含至少90%vol氢的富氢料流以与在加氢脱芳烃中具有催化活性的材料接触,具有的相关益处在于,将整个过程所需的高纯度氢引导至加氢脱芳烃步骤,从而有助于平衡向远离芳烃的方向移动。
23.在另一个实施方案中,异构化条件包括温度区间为250
‑
400℃,压力区间为30
‑
150bar以及液时空速(lhsv)区间为0.5
‑
8;其中在异构化中具有催化活性的材料包括活性金属,其选自铂、钯、镍、钴、钨和钼,优选一种或多种单质贵金属,例如铂或钯;酸性载体优选分子筛,更优选具有选自mor、fer、mre、mww、ael、ton和mtt的拓扑结构;以及无定形耐热载体,所述无定形耐热载体包含选自氧化铝、二氧化硅和二氧化钛或其组合的一种或多种氧化物,具有的相关益处在于,这些条件和材料对于调节产物的冷流性能而言是成本有效和选择性方法。
24.本公开的另一方面涉及一种用于由为可再生原料或含氧化合物原料的原料生产烃馏分的工艺设备,所述工艺设备包括加氢脱氧工段、加氢裂化工段、异构化工段、分离工段和分馏工段,所述工艺设备被配置用于将原料和液体稀释剂引导至加氢脱氧工段,以提供经加氢脱氧的中间产物;被配置用于引导至少一定量的所述经加氢脱氧的中间产物在加氢裂化条件下与在加氢裂化中具有催化活性的材料接触,以提供经加氢裂化的中间产物;被配置用于将所述经加氢裂化的中间产物分离成蒸气馏分和液体馏分;被配置用于引导至少一定量的所述经加氢裂化的液体产物在异构化条件下与在异构化中具有催化活性的材料接触,以提供经异构化的中间产物;以及被配置用于分馏所述经异构化的中间产物以提供至少适合用作喷气燃料的烃,具有的相关益处在于,这样的工艺设备适于进行所公开的方法,以成本有效和选择性地生产喷气燃料。
25.在另一个实施方案中,该工艺设备还包括配置用于提供一定量的所述经加氢裂化的液体产物作为液体稀释剂的再循环连接,具有的相关益处在于,在不添加稀释剂例如化石原料的情况下,控制加氢脱氧反应器中的温度。
26.本公开中描述的方法接收可再生原料和/或含氧化合物原料,其包含选自甘油三酯、脂肪酸、树脂酸、酮、醛、醇、酚和芳族羧酸的一种或多种含氧化合物,其中所述含氧化合物源自一种或多种生物来源、气化过程、热解过程、fischer
‑
tropsch合成、基于甲醇的合成或其他合成工艺,特别是获自可再生来源的原材料,例如源自植物、藻类、动物、鱼类、植物油炼制、生活废物、用过的食用油、塑料废物、橡胶废物或工业有机废物,如妥尔油或黑液。这些原料中的一些可能含有芳烃;特别是通过热解或其他工艺由例如木质素和木材得到的
产物或来自例如煎炸油的废弃产物。根据来源,含氧化合物原料可以占1wt/wt%至40wt/wt%。生物来源通常将占约10wt/wt%,并且衍生产物为1wt/wt%至20wt/wt%或甚至40wt/wt%。
27.为了将可再生原料和/或含氧化合物原料转化为烃运输燃料,将原料与与氢气一起引导,以与在加氢处理(尤其是加氢脱氧)中具有催化活性的材料接触。尤其是在升高的温度下,催化加氢脱氧过程可能具有副反应,例如由原料中的烯烃分子形成重质产物。为了缓和热量的释放,可以添加液态烃,例如液体再循环料流或外部稀释剂进料。如果该工艺设计用于化石原料和可再生原料的联合处理,则使用化石原料作为稀释剂是方便的,因为在化石原料的加工期间释放较少的热量,因为较少的杂原子被释放并且较少的烯烃被饱和。除了调节温度外,再循环物或稀释剂也具有降低烯烃材料聚合的潜能的作用。得到的产物料流将是包含烃(通常为正链烷烃)和酸性气体(例如co、co2、h2o、h2s、nh3)以及轻质烃(尤其是c3和甲烷)的经加氢脱氧的中间产物料流。
28.通常,加氢脱氧包括引导原料与负载在载体上的催化活性材料接触,所述催化活性材料通常包含一种或多种硫化的选自镍、钴、钼或钨的金属,所述载体包含一种或多种耐热氧化物,通常为氧化铝,但也可能是二氧化硅或二氧化钛。载体通常是无定形的。催化活性材料可以包含其他组分,例如硼或磷。条件通常是温度区间为250
‑
400℃,压力区间为30
‑
150bar以及液时空速(lhsv)区间为0.1
‑
2。加氢脱氧通常是放热的,并且在存在大量氧气的情况下,该过程可能涉及中间冷却,例如用冷的氢气、原料或产物进行骤冷。原料可以优选含有一定量的硫以确保金属的硫化,从而保持其活性。如果气相包含少于10、50或100ppm
v
的硫,可以向进料添加硫化物供体,例如二甲基二硫化物(dmds)。
29.对于待用作煤油馏分的经加氢脱氧的中间产物料流,必须调节沸点范围。如果在经加氢脱氧的中间体中存在一定量的重质产物,也可能需要调节沸点。通过引导经加氢脱氧的中间产物与加氢裂化中具有催化活性的材料接触,将长链烷烃加氢裂化为较短的链烷烃,来调节沸点。
30.加氢裂化包括引导经加氢脱氧的中间原料与在加氢裂化中具有催化活性的材料接触。在加氢裂化中具有催化活性的材料通常包含活性金属(在本公开中,其为一种或多种硫化贱金属,例如镍、钴、钨和/或钼)、酸性载体(通常是显示高裂化活性,并具有诸如mfi、bea和fau的拓扑结构的分子筛,但也可以使用无定形酸性氧化物(例如二氧化硅
‑
氧化铝))和耐热载体(例如氧化铝、二氧化硅或二氧化钛,或其组合)。催化活性材料可以包含其他组分,例如硼或磷。优选的加氢裂化催化剂包括分子筛,例如zsm
‑
5,y沸石或β沸石。
31.根据本公开,在加氢裂化中具有催化活性的材料是贱金属,其位于在加氢脱氧中具有催化活性的材料的下游。
32.条件通常是温度区间为250
‑
400℃,压力区间为30
‑
150bar,液时空速(lhsv)区间为0.5
‑
4。由于加氢裂化是放热的,因此该过程可能涉及中间冷却,例如通过用冷的氢气、原料或产物进行骤冷。在加氢裂化中具有催化活性的材料上的活性金属是贱金属,因此通常引导包括气相的经加氢脱氧的中间原料与在加氢裂化中具有催化活性的材料接触,而无需进一步纯化。该混合物的气相应优选含有至少50ppm
v
的硫。
33.不饱和脂肪酸的加氢脱氧可以副反应产生芳烃。因此,即使对于包含少于1%芳烃的含氧化合物原料,也可能有必要进一步引导经异构化的产物以与加氢脱芳烃中具有催化
活性的材料接触。
34.经加氢裂化的中间产物主要为直链烃,如原料,或者如果原料包含甘油三酯,则为正链烷烃,但是长度可能短于脂肪酸。通常,经加氢裂化的中间产物将主要是不适合用作喷气燃料的直链烷烃,所述直链烷烃具有沸点范围(250℃至320℃)和凝固点(0℃至30℃)。如果不饱和脂肪酸聚合,则在加氢脱氧步骤中还可以形成一些重质组分和芳烃。
35.为了在实践中将经加氢裂化的中间产物用作燃料,必须调节凝固点。通过引导经加氢裂化的中间产物与异构化中具有催化活性的材料接触将正链烷烃异构化为异链烷烃,来调节凝固点。
36.在异构化中具有催化活性的材料通常包含活性金属(根据本公开,其为一种或多种单质贵金属,例如铂和/或钯)、酸性载体(通常是显示高形状选择性,并且具有诸如mor、fer、mre、mww、ael、ton和mtt的拓扑结构的分子筛)和通常为无定形的耐热载体(例如氧化铝、二氧化硅或二氧化钛,或其组合)。催化活性材料可以包含其他组分,例如硼或磷。优选的异构化催化剂包括分子筛,例如eu
‑
2、zsm
‑
48、β沸石以及β沸石和沸石y的组合。
37.通常,异构化包括引导经加氢裂化的中间原料与在异构化中具有催化活性的材料接触。条件通常是温度区间为250
‑
400℃,压力区间为30
‑
150bar,液时空速(lhsv)区间为0.5
‑
8。异构化基本上是热中性的,因此在加氢裂化副反应中仅消耗氢,所以在异构化反应器中仅添加适量的氢气。由于在异构化中具有催化活性的最具选择性的材料上的活性金属是贵金属,因此通常通过气/液分离对经加氢裂化的原料进行纯化,以将潜在的催化剂毒物的含量减少至低水平,例如硫、氮和碳氧化物的含量减少至低于1
‑
10ppm。
38.在某些情况下,在加氢脱芳烃中具有催化活性的材料的存在下进行加氢脱芳烃可能是令人满意的,但是也可能需要有一个单独的反应器或反应器床,该反应器或反应器床具有在加氢脱芳烃中具有催化活性的材料。
39.这种在加氢脱芳烃中具有催化活性的材料通常包含活性金属(优选是硫化贱金属,例如镍、钴、钨和/或钼,但也可能是—在纯化后,通过去除例如硫化氢—贵金属,例如铂和/或钯)和耐热载体(例如无定形的二氧化硅
‑
氧化铝、氧化铝、二氧化硅或二氧化钛,或其组合)。加氢脱芳烃是平衡控制的,其中高温有利于芳烃,因此优选贵金属作为活性金属,因为与贱金属相比,贵金属在较低的温度下具有活性。
40.通常,加氢脱芳烃涉及引导中间产物与在加氢脱芳烃中具有催化活性的材料接触。由于在升高的温度下,芳烃和饱和分子之间的平衡向芳烃方向移动,因此优选适度的温度。条件通常是温度区间为200
‑
350℃,压力区间为30
‑
150bar,液时空速(lhsv)区间为0.5
‑
8。在加氢脱芳烃中具有催化活性的材料上的优选活性金属通常优选为贵金属,因为与相当的贱金属催化剂相比,贵金属催化剂通常在较低的温度下具有活性。根据本公开,通常对异构化的产物进行充分纯化,因为在异构化中具有催化活性的材料中的活性金属是贵金属。也可以使用贱金属催化剂,在这种情况下,与经加氢异构化的中间原料相关的气相优选含有至少50ppm
v
的硫。通常,在低于350℃的温度下运行的加氢裂化或加氢异构化催化剂能够催化适当程度的加氢脱芳烃,例如将10wt/wt%的芳烃减少到低于0.5wt/wt%的芳烃。
41.为了将可再生原料转化为喷气燃料,需要将3或4种催化活性材料组合起来,这自然使工艺布局复杂化,并且必须仔细考虑材料的顺序。另外,再循环可用于三个不同的目的;气体再循坏用于高效利用氢气,在加氢裂化中具有催化活性的材料周围的液体再循环
用于使煤油馏分的收率最大化;在加氢脱氧中具有催化活性的材料周围的液体再循环用于限制由于放热的加氢脱氧反应而引起的温度升高。
42.当使用包含贵金属的催化活性材料进行异构化和加氢脱芳烃时,在此反应之前,去除“酸性气体”,包括硫化氢、二氧化碳和氨气。一定量的加氢裂化中间产物也可以再循环至加氢脱氧反应器的入口。
43.根据当前的公开内容进行操作,并在加氢脱氧和加氢裂化反应器周围进行再循环,具有允许通过多次通过而不是在苛刻条件下获得高的加氢裂化转化率的优点,从而允许在适度的温度下进行完全转化,以及因此允许适度的收率损失,因此保持高的煤油收率,并将对石脑油和更轻质部分的过度裂化最小化。使用异构化催化剂来改善喷气燃料的凝固点,允许增加喷气燃料的蒸馏终点,同时仍能满足凝固点的要求。最后,由于第二阶段将使芳烃饱和,因此第一阶段不需要满足任何芳烃要求,因为这些芳烃将在第二阶段被饱和,这允许第一阶段处理更重质和/或更多的芳烃、环烷烃或不饱和原料以及诸如用过的食用油、热解产物或妥尔油沥青等原料,其含有芳烃或不饱和原料,在典型的加氢处理条件下这些芳烃或不饱和原料可以产生少量的芳烃。
44.根据本公开的一个实施方案对应于一种方法,其中包含一定量的硫的包含含氧化合物和再循环烃的料流被引导至含有催化活性材料的加氢脱氧反应器,所述催化活性材料包含一种或多种贱金属和具有低酸性的耐热载体。这样的材料在加氢脱氧和其他加氢处理反应中具有活性,用于除去杂原子和双键。再循环烃作为热槽起作用,吸收从加氢脱氧反应释放出的反应热,因此在加氢脱氧反应器中保持适度的温度。该步骤提供了包含大量饱和直链烷烃以及一定量的水、co、co2、甲烷、硫化氢和氨的料流。
45.经加氢脱氧的烃料流被引导至加氢裂化反应器,以与包含一种或多种贱金属和具有高酸性的耐热载体的催化活性材料接触。这样的材料在加氢裂化中具有活性,并且该步骤提供了其中较高沸点烃被转化为较低沸点烃的料流。加氢裂化过程的严苛性将决定产物的沸点特征,并且通常运行加氢裂化过程使沸点高于柴油温度范围的馏分完全转化。如果选择加氢裂化以使沸点高于喷气燃料范围的馏分完全转化,则气体和石脑油的收率损失通常将太高。
46.经加氢裂化的料流被引导至分离工段,抽出水、硫化氢和氨,并提供甜烃料流(sweet hydrocarbon stream)。一定量的甜烃料流经再循环成为再循环甜烃,并且一定量作为进料被引导至异构化反应器中,所述异构化反应器含有在异构化中具有催化活性的材料和任选的在加氢脱芳烃中具有催化活性的材料。这两种材料均基于贵金属催化剂,例如铂、钯或其组合;以及酸性载体。对于异构化,酸性载体优选具有形状选择性,以提供选择性异构化,将直链烷烃重排为支链烷烃,并最小化较轻质的烃的生产。对于加氢脱芳烃,酸性载体也有助于反应,此外,由于贵金属的活性高于贱金属的活性,因此反应将在较低的温度下进行。由于芳烃和非芳烃化合物之间的平衡在低温下会朝远离芳烃的方向移动,因此贵金属提供了用较低的温度来匹配平衡的益处。加氢脱芳烃甚至可以经由在异构化中具有催化活性的材料发生,所述材料经常具有一定的加氢脱芳烃活性。
47.由于甜烃料流不含有硫化氢或氨,因此在异构化中具有催化活性的材料的贵金属功能和酸功能均不受干扰,并且以高选择性生产了支链烃料流。
48.经异构化的料流被引导至分馏器(在分离器机构中适当除去气相之后),并抽出至
少气体馏分、中间馏分和塔底馏分。
49.根据本公开的布局的一个益处是,与在同一阶段中使用贵金属和贱金属的过程相比,这样的装置的启动是简单的,因为位于分离工段上游的加氢处理/加氢裂化组合阶段可以通过硫化而活化,而位于分离工段下游的异构化工段可以通过还原而活化。
50.该布局使原料转化为柴油、喷气燃料范围或更轻质的产物,因为一些或甚至所有经加氢脱氧的重质烃都可以发生加氢裂化,以产生较轻质的产物。喷气燃料/柴油联合生产或仅柴油生产是可能的,并且沸点的转化主要在仅采用贱金属催化剂的加氢脱氧工段和加氢裂化工段中进行,从而能够在单个工艺位置中添加dmds形式的硫。此外,与加氢裂化条件无关,通过在贵金属催化剂上进行异构化来选择性地进行凝固点的调节。
51.如果希望仅生产柴油而不生产喷气燃料,则不需要加氢裂化。在这种情况下,可以优选绕过加氢裂化反应器或者可替代地,在该反应器之前冷却产物,以使其不具有活性。可以将工艺设备配置为允许这样的具有临时通知的配置,例如通过设置适当的设备和在控制室中进行控制。
52.附图简要说明
53.图1示出了根据本公开的方法的简化图。
54.图2示出了根据现有技术的方法的简化图。
55.图3示出了根据现有技术的方法的简化图。
56.图1是示出根据本公开的布局的简化图,出于简化省略了气态料流的供应和分离的细节。可再生原料(102)与再循环稀释剂料流(128)混合,并作为加氢脱氧进料料流(104)与一定量的富氢料流(未示出)一起被引导至加氢脱氧反应器(hdo),在此其在加氢处理条件下与在加氢反应中具有催化活性的材料接触。这提供了经加氢脱氧的中间产物(106)。经加氢脱氧的中间产物(106)被引导至在加氢裂化条件下运行的加氢裂化反应器(hdc),提供经加氢裂化的中间产物(108)。经加氢裂化的中间产物(108)被引导至分离工段(sep)(出于简化示出为单个单元),将经加氢裂化的中间产物分离为用于再循环的气体料流和液体中间产物料流(110)。液体中间产物料流(110)被分流为再循环稀释剂料流(128)和异构化反应器进料料流(112),异构化反应器进料料流(112)作为进料被引导至异构化反应器(isom),在该反应器中,其在异构化条件下与在异构化中具有催化活性的材料和任选的在加氢脱芳烃条件下与在加氢脱芳烃中具有催化活性的另一材料接触,提供经异构化的产物(116),该经异构化的产物(116)被引导至分馏工段(frac)(出于简化仅示出为单个单元);将经异构化的产物分离为轻质塔顶料流(120)、石脑油产物(122)、喷气燃料产物(124)和塔底柴油馏分(126)。
57.图2以类似于图1的详细程度示出了现有技术的示例,出于简化省略了气态料流的供应和分离的细节。将可再生原料(202)与再循环稀释剂料流(228)混合,并作为加氢脱氧进料料流(204)与一定量的富氢料流(未显示)一起被引导至加氢脱氧反应器(hdo),在该反应器中其在加氢处理条件下与在氢化反应中具有催化活性的材料接触。这提供了经加氢脱氧的中间产物(214),其被引导至加氢异构化反应器(isom),在该反应器中其在异构化条件下与在异构化中具有催化活性的材料接触,提供了脱蜡的中间产物(216)。经脱蜡的中间产物(216)被引导至分馏工段(frac)(出于简化示出为单个单元),将经加氢裂化的产物分离为轻质塔顶料流(220)、石脑油料流(222)、喷气燃料产物(224)和塔底柴油馏分,该塔底柴
油馏分被分流为再循环稀释剂料流(228)和柴油产物料流(226)。
58.图3示出了现有技术的另一示例,出于简化省略了气态料流的供应和分离的细节。可再生原料(302)与再循环稀释剂料流(328)混合,并作为加氢脱氧进料料流(304)与一定量的富氢料流(未示出)一起被引导至加氢脱氧反应器(hdo),在该反应器中其在加氢处理条件下与在氢化反应中具有催化活性的材料接触。这提供了经加氢脱氧的中间产物(306),其被引导至分离工段(sep),从中分离出纯化的经加氢脱氧的中间产物(308),该中间产物(308)被分流成再循环稀释剂料流(328)和异构化进料料流(310),异构化进料料流(310)与无硫的氢料流(未示出)混合并被引导至加氢异构化反应器(isom)。在该反应器中,该混合的进料料流在异构化条件下与在异构化中具有催化活性的基于贵金属的材料接触,提供了脱蜡的中间产物(312)。脱蜡的中间产物(312)被引导至分馏工段(frac)(出于简化示出为单个单元),将经加氢裂化的产物分离为轻质塔顶料流(320)、石脑油料流(322)、喷气燃料产物(324)和塔底柴油馏分(326)。
实施例
59.比较了图1和图3所示的工艺布局的性能。
60.表1示出了可再生原料的特性,该可再生原料是动物脂肪和食用油以及加氢处理后的中间产物的组合。中间产物以c16和c18烷烃为主,具有高凝固点(24℃),并含有大于1.5wt/wt%的芳烃。将原料分别按照图1和图3的两种方法进行处理,这种处理的结果示于表2中,其中“实施例1”对应于图1,“实施例2”对应于图2。“净喷气燃料制造量”的值通过下式计算为过程中生产的喷气燃料量减去原料中已经存在的喷气燃料量:净喷气燃料制造量=[总喷气燃料产物]
‑
[进料中存在的原有喷气燃料]。收率在该表中表示为进入该单元的进料的wt/wt%。例如,51wt/wt%的喷气燃料收率表示在该单元中加工的每100千克进料产生51千克的喷气燃料。
[0061]
这两个实施例的结果均显示出具有优异性能:低凝固点(
‑
40℃)和低芳烃含量(<0.5wt/wt%)的喷气燃料的生产。假定喷气燃料和柴油之间的分馏界限点为300℃,根据本公开的实施例1具有51wt/wt%的喷气燃料收率,而实施例2具有43wt/wt%的喷气燃料收率。在喷气燃料价值更高的假设下进行的工艺优化中,这种差异表明显然是实施例1极具吸引力的益处。
[0062]
这两种情况下性能之间的关键差异在于,实施例1的喷气燃料收率为52wt/wt%,而实施例2的收率则低得多,为43wt/wt%。由于转化是在再循环配置中进行的,因此可以选择较温和的反应条件,与单程转化相比,减少了过度转化为石脑油的情况。在喷气燃料价值更高的假设下进行的工艺优化中,得到的差异表明显然是实施例1极具吸引力的益处。
[0063]
表1
[0064]
[0065]