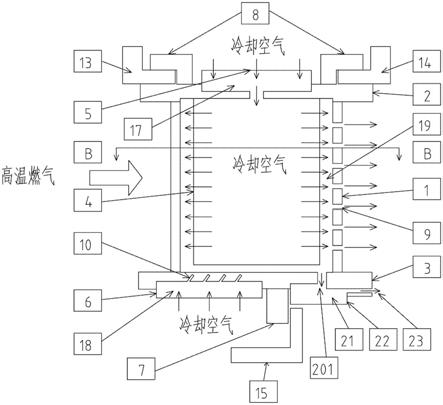
1.本实用新型涉及燃气轮机设计的技术领域,尤其涉及一种燃气轮机的涡轮静子叶片及采用其的燃气轮机。
背景技术:2.随着燃气轮机设计技术水平的提高,燃气轮机涡轮进口燃气温度不断提高,涡轮部件所面临的热负荷极高,早已超过高温材料能够承受的极限。为了保证涡轮叶片安全可靠工作,需要对其进行复杂的冷却设计,以使叶片本体的温度和应力分布保持在合理的水平。
3.为满足日渐提高的环保要求,燃气轮机燃烧系统普遍采用了dln低氮燃烧技术,这种技术使得燃气轮机进口温度剖面更加扁平——即减小了燃机进口温度峰值,但增大了端壁区域的温度水平。因此,在低氮燃烧的燃气轮机透平中,端壁设计难度进一步加大,涡轮静子叶片端壁尾缘区域冷却布置困难,极容易出现裂纹、高温氧化、甚至烧蚀等失效现象。
技术实现要素:4.有鉴于此,本实用新型的主要目的在于提供一种燃气轮机的涡轮静子叶片及采用其的燃气轮机,以期至少部分地解决上述提及的技术问题中的至少之一。
5.为了实现上述目的,本实用新型的技术方案为:
6.作为本实用新型的一个方面,提供一种燃气轮机的涡轮静子叶片,包括叶片叶身、位于叶片叶身两端的端壁;所述叶片叶身的外表面由吸力面和压力面构成,吸力面和压力面交界区域分别为叶片前缘和叶片尾缘;叶片尾缘对应的端壁部位定义为端壁尾缘;
7.其中,端壁尾缘设置有端壁尾缘空腔,所述端壁尾缘空腔在对应端壁尾缘区域设置至少一个冷气通孔。
8.作为本实用新型的另一个方面,还提供一种燃气轮机,采用了如上所述的涡轮静子叶片。
9.基于上述技术方案可知,本实用新型相对于现有技术至少具有如下有益效果的其中之一或其中一部分:
10.(1)本实用新型在端壁尾缘区域设置端壁尾缘空腔,在不增加冷却空气量的情况下,降低涡轮静子叶片端壁尾缘区域的温度和应力水平;
11.(2)本实用新型的端壁尾缘空腔的进气设置方式多种,冷却气获取方式灵活,易于实现和应用;
12.(3)端壁尾缘空腔内设置蛇形通道,形成多个连续冷却通道的对流冷却,可进一步降低该端壁尾缘区域的温度、温度梯度以及应力水平;
13.(4)端壁尾缘空腔内布置冷却强化结构,如各种形状的凸起、扰流柱等,更进一步起到增强冷却的效果。
附图说明
14.图1是对比例1的燃气轮机的涡轮静子叶片示意图;
15.图2是图1的a
‑
a向剖面示意图;
16.图3是本实用新型实施例1的燃气轮机的涡轮静子叶片示意图;
17.图4是图3的b
‑
b向剖面示意图;
18.图5是本实用新型实施例2的燃气轮机的涡轮静子叶片示意图;
19.图6是图5的c
‑
c向剖面示意图;
20.图7是本实用新型实施例3的燃气轮机的涡轮静子叶片示意图;
21.图8是图7的d
‑
d向剖面示意图。
22.上述附图中,附图标记含义如下:
[0023]1‑
叶片叶身;2
‑
上端壁;3
‑
下端壁;4
‑
冲击衬套;5
‑
第一冲击冷却盖板;6
‑
第二冲击冷却盖板;7
‑
下端壁导轨;8
‑
上端壁导轨;9
‑
第一冷气喷射孔;10
‑
第二冷气喷射孔;11
‑
叶片前缘;12
‑
叶片尾缘;13
‑
第一挂钩;14
‑
第二挂钩;15
‑
支撑环;16
‑
端壁尾缘高温区;17
‑
上端壁冲击腔;18
‑
下端壁冲击腔;19
‑
叶片内部冲击腔;201、202、203
‑
下端壁尾缘空腔入口;21
‑
下端壁尾缘空腔;22
‑
下端壁尾缘空腔盖板;23
‑
下端壁尾缘空腔通孔;24
‑
隔板;25
‑
第一冷却通道;26
‑
第二冷却通道;27
‑
第三冷却通道。
具体实施方式
[0024]
本实用新型在不增加总冷却空气量的情况下,对涡轮静子叶片尾缘端壁区域冷却进行设计,以降低涡轮静子叶片端壁尾缘区域的温度和应力水平。
[0025]
为使本实用新型的目的、技术方案和优点更加清楚明白,以下结合具体实施例,并参照附图,对本实用新型作进一步的详细说明。
[0026]
作为本实用新型的一个方面,提供一种燃气轮机的涡轮静子叶片,包括叶片叶身、位于叶片叶身两端的端壁;叶片叶身的外表面由吸力面和压力面构成,吸力面和压力面交界区域分别为叶片前缘和叶片尾缘;叶片尾缘对应的端壁部位定义为端壁尾缘;
[0027]
其中,端壁尾缘设置有端壁尾缘空腔,端壁尾缘空腔在对应端壁尾缘区域设置至少一个冷气通孔。
[0028]
在本实用新型的实施例中,冷气通孔的横截面形状包括但并不局限于圆形、椭圆形、方形或者菱形;只要能够实现流通冷却的效果即可。
[0029]
在本实用新型的实施例中,冷气通孔可以但并不局限于通过铸造、电加工或者激光加工的工艺成型。
[0030]
在本实用新型的实施例中,冷气通孔的延伸方向与端壁的壁面平行;冷气通孔包括多个,呈阵列布置。
[0031]
更为具体的,冷气通孔数量、形状、尺寸和布置可以根据实际冷却空气的可用量和端壁尾缘区域的冷却设计需求确定。
[0032]
在本实用新型的实施例中,叶片叶身内部采用空气冷却,端壁尾缘空腔内冷却空气来自于对叶片叶身内部冷却后的空气,定义对叶片叶身内部冷却后的空气为叶片叶身冷却空气乏气;
[0033]
在端壁尾缘上设置端壁尾缘空腔入口,端壁尾缘空腔入口连通端壁尾缘空腔和叶
片叶身内部,叶片叶身冷却空气乏气通过端壁尾缘空腔入口进入端壁尾缘空腔。
[0034]
更为具体的,叶片叶身内部设置冲击衬套,冲击衬套与叶片叶身之间的空间定义为叶片内部冲击腔;冷却空气进入冲击衬套内部后,对叶片叶身进行冲击冷却,冲击冷却后的叶片叶身冷却空气乏气在叶片内部冲击腔内。端壁尾缘空腔入口连通端壁尾缘空腔和叶片内部冲击腔,使叶片内部冲击腔内的叶片叶身冷却空气乏气进入端壁尾缘空腔内。
[0035]
在本实用新型的实施例中,叶片叶身内部可以包括一个或者多个冲击衬套,冲击衬套采用冲击冷却形式。下端壁尾缘空腔内的叶片叶身冷却空气乏气可以来自一个或者多个叶片叶身的冲击衬套。
[0036]
在本实用新型的另一个实施例中,叶片前缘对应的端壁部位定义为端壁前缘;在端壁前缘设置端壁冲击腔;端壁尾缘空腔内冷却空气来自于端壁冲击腔内的端壁冲击冷却空气乏气;
[0037]
在端壁上设置端壁导轨,在端壁导轨上设置第一通孔,端壁冲击冷却空气乏气通过端壁导轨的第一通孔进入端壁尾缘空腔。其中,该第一通孔成为端壁冲击腔上的端壁冲击腔入口的另一设置方式,由此提供了另一种端壁冲击腔的用于冷却的冷却空气来源。
[0038]
在本实用新型的再一个实施例中,在端壁上设置端壁导轨,在端壁导轨上设置第二通孔,压气机排气通过端壁导轨的第二通孔进入端壁尾缘空腔。其中,该第二通孔成为端壁冲击腔上的端壁冲击腔入口的再一设置方式,由此提供了再一种端壁冲击腔的用于冷却的冷却空气来源。
[0039]
在本实用新型的实施例中,端壁尾缘空腔设置于上端壁和/或下端壁。更为具体的,端壁尾缘空腔并不局限于设置于下端壁上,还可以设置于上端壁上以及同时设置于上端壁和下端壁上。
[0040]
在本实用新型的实施例中,端壁尾缘空腔内部设置隔板,使端壁尾缘空腔内部形成蛇形通道。
[0041]
在本实用新型的实施例中,一方面,蛇形通道可以起到提高冷却效果的作用;另一方面,蛇形通道还可以起到限制端壁尾缘空腔内冷却空气的气体流向问题。
[0042]
值得一提的是,蛇形通道的形状、尺寸等可以根据冷却设计需要确定,蛇形通道形状可以为任意多边形,流动面积可以根据实际需要进行变化。
[0043]
在本实用新型的实施例中,端壁尾缘空腔内设置用于强化冷却的凸起和/或扰流柱。
[0044]
在本实用新型的实施例中,端壁尾缘空腔为端壁与端壁尾缘空腔盖板一体铸造成型;或者,端壁尾缘空腔为端壁与端壁尾缘空腔盖板焊接密封成型。
[0045]
在本实用新型的实施例中,涡轮静子叶片的叶片叶身为单个独立铸造结构;或者涡轮静子叶片的叶片叶身为多个间隔设置的一体铸造结构。
[0046]
作为本实用新型的一个方面,还提供一种燃气轮机,采用了如上所述的涡轮静子叶片。
[0047]
下面结合具体实施例和对比例对本实用新型的技术方案作进一步说明,但需要注意的是,下述的实施例仅用于说明本实用新型的技术方案,但本实用新型并不限于此。
[0048]
对比例1
[0049]
如图1和图2所示,该对比例1提供一种燃气轮机的高温涡轮静子叶片。其燃气轮机
的高温涡轮静子叶片结构如实施例1至实施例3所示,包括叶片叶身1、上端壁2、下端壁3、上端壁导轨8、下端壁导轨7、第一冲击冷却盖板5、第二冲击冷却盖板6和冲击衬套4。涡轮静子叶片通过第一挂钩13和第二挂钩14与上端壁导轨8配合并固定在燃机本体上,支撑环15与下端壁导轨7配合并将涡轮静子叶片组件固定在支撑环15上。
[0050]
冷却空气通过上端壁2的第一冲击冷却盖板5对上端壁2进行冷却,然后冷却空气通过上端壁冲击腔17进入冲击衬套4内部,并对叶片叶身1进行冲击冷却,冲击冷却后的乏气在叶片内部冲击腔19中,通过第一冷气喷射孔9进入主流燃气。下端壁3的冷却空气通过第二冲击冷却盖板6对下端壁3进行冷却,然后冷却空气通过下端壁冲击腔18壁面上的第二冷气喷射孔10进入下端壁3的燃气侧。
[0051]
其中,该对比例1提供的燃气轮机的涡轮静子叶片结构与实施例1至实施例3的涡轮静子叶片结构的不同之处在于,在涡轮静子叶片的上端壁和/或下端壁形成端壁尾缘高温区16。这是因为:下端壁3的下端壁导轨7后部由于冷气侧压力较低,上端壁2的上端壁导轨8后部冷气侧压力也较低,无法布置冲击冷却,且燃气侧由于冷气喷射孔10的气膜覆盖作用并不显著;从而导致出现端壁尾缘高温区16。该缺陷会导致该端壁尾缘高温区16出现烧蚀、氧化、裂纹等问题。
[0052]
实施例1
[0053]
图3是本实用新型实施例1的燃气轮机的涡轮静子叶片的结构示意图,图4是图3的b
‑
b向视图。如图3和图4所示,燃气轮机的涡轮静子叶片包括叶片叶身1、上端壁2、下端壁3、上端壁导轨8、下端壁导轨7、第一冲击冷却盖板5、第二冲击冷却盖板6和冲击衬套4。涡轮静子叶片通过第一挂钩13和第二挂钩14与上端壁导轨8配合并固定在燃机本体上,支撑环15与下端壁导轨7配合并将高温静子叶片组件固定在支撑环15上。
[0054]
冷却空气通过上端壁2的第一冲击冷却盖板5对上端壁2进行冷却,然后冷却空气通过上端壁冲击腔17进入冲击衬套4内部,并对叶片叶身1进行冲击冷却,冲击冷却后的乏气在叶片内部冲击腔19中,通过第一冷气喷射孔9进入主流燃气。下端壁3的冷却空气通过第二冲击冷却盖板6对下端壁3进行冷却,然后冷却空气通过下端壁冲击腔18壁面上的第二冷气喷射孔10进入下端壁3的燃气侧。
[0055]
本实用新型实施例1提供的涡轮静子叶片在端壁尾缘高温区16设置下端壁尾缘空腔21,下端壁尾缘空腔21由下端壁尾缘空腔盖板22固定在下端部3上密封形成,下端壁尾缘空腔21的冷却空气来自于叶片内部冲击腔19的叶片叶身冷却空气乏气,通过下端壁尾缘空腔入口201进入下端壁尾缘空腔21。下端壁尾缘空腔21内的冷却空气通过下端壁尾缘空腔通孔23对下端壁3的端壁尾缘高温区16进行冷却,从而有效降低该区域的温度,显著缓解由于高温导致的烧蚀、氧化、裂纹等问题。
[0056]
实施例2
[0057]
图5是本实用新型实施例2提供的燃气轮机的涡轮静子叶片的结构示意图,图6是图5的c
‑
c向剖视图。如图5和图6所示,本实用新型实施例2与本实用新型实施例1的结构不同之处在于:在端壁尾缘高温区16设置下端壁尾缘空腔21,下端壁尾缘空腔21由下端壁尾缘空腔盖板22固定在下端壁3上密封形成,下端壁尾缘空腔21的冷却空气来自于下端壁3的下端壁冲击腔18的端壁冲击冷却空气乏气,通过下端壁尾缘空腔入口202(即第一通孔)进入下端壁尾缘空腔21。下端壁尾缘空腔21内的冷却空气通过下端壁尾缘空腔通孔23对下端
壁3的端壁尾缘高温区16进行冷却,从而有效降低该区域的温度,显著缓解由于高温导致的烧蚀、氧化、裂纹等问题。
[0058]
实施例3
[0059]
图7是本实用新型实施例3提供的燃气轮机的涡轮静子叶片的结构示意图,图8是图7的d
‑
d向剖视图。如图7和图8所示,本实用新型实施例3与本实用新型实施例1的结构不同之处在于:
[0060]
在端壁尾缘高温区16设置上端壁尾缘空腔和下端壁尾缘空腔21,下端壁尾缘空腔21由下端壁尾缘空腔盖板22固定在下端壁3上密封形成,下端壁尾缘空腔21的冷却空气来自于压气机排气,通过下端壁尾缘空腔入口203(即第二通孔)进入下端壁尾缘空腔21。下端壁尾缘空腔21被隔板24分割成蛇形通道,包括第一冷却通道25、第二冷却通道26和第三冷却通道27,冷却空气沿上述蛇形通道对端壁区域进行均匀的对流冷却。下端壁尾缘空腔21内的冷却空气通过下端壁尾缘空腔通孔23对端壁尾缘高温区16进行进一步冷却。
[0061]
通过以上冷却设计,可以有效降低端壁尾缘区域的温度水平,降低温度梯度水平,显著缓解由于高温导致的烧蚀、氧化、裂纹等问题。
[0062]
以上所述的具体实施例,对本实用新型的目的、技术方案和有益效果进行了进一步详细说明,应理解的是,以上所述仅为本实用新型的具体实施例而已,并不用于限制本实用新型,凡在本实用新型的精神和原则之内,所做的任何修改、等同替换、改进等,均应包含在本实用新型的保护范围之内。