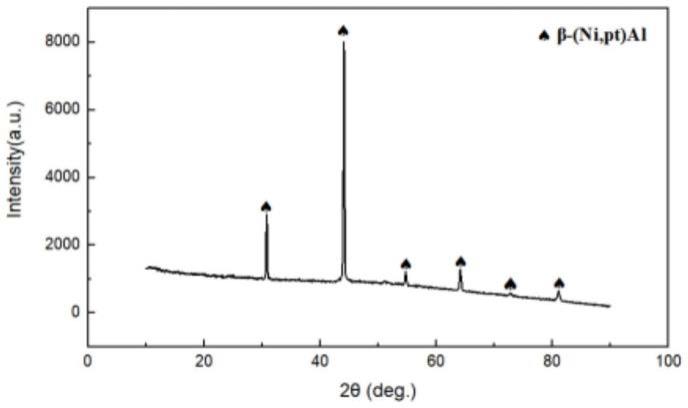
1.本发明涉及高温防护涂层技术领域,具体涉及一种可作为热障涂层粘结层的铂改性铝化物涂层及其制备工艺。
背景技术:2.随着航空发动机及燃气轮机设计技术不断进步,功率、效率和功率密度等性能参数不断提高,提高涡轮前燃气温度是提高发动机热机效率和功率的根本所在。
3.为满足航空发动机及燃气轮机更新换代的升级需求,一方面需要采用高效的冷却技术,另一方面必须采用耐温等级更高的合金材料。根据叶片使用温度的要求,燃气轮机高压涡轮动叶选取了dd5单晶合金(使用温度1100℃以下)。在上述基础上,通过在叶片表面制备先进热障涂层(tbcs)降低实际工作温度也成为提高叶片耐温能力的有效手段之一。
4.相关应用的文献如:
①
中国发明专利:pt+si改性的β-nial热障涂层及其制备方法,申请号201210078703.7;
②
中国发明专利:用于隔热涂层的经铂改性的nicocraly结合涂层,申请号200610169095.5;
③
中国发明专利:一种防护涂层,申请号200410003852.2等。
5.针对单晶高温合金,本发明通过对不同预氧化制度下的铂铝涂层抗高温氧化及热腐蚀性能进行表征及影响规律分析,进一步研发出优化的tbcs单相pt-al粘结层工艺,以期延长tbcs热障涂层的服役时间。
技术实现要素:6.为了延长tbcs热障涂层的服役时间,本发明的目的在于提供一种可作为热障涂层粘结层的铂改性铝化物涂层及其制备工艺。本发明涂层中仅含有稳定的β-(ni,pt)al单相组织,在保证涂层热稳定性的同时提供了足够含量的铝和铂元素。因此可以防止由于相变体积变化导致的涂层表面褶皱,提高tbcs热障的涂层的使用寿命。
7.为了实现上述目的,本发明所采用的技术方案如下:
8.一种可作为热障涂层粘结层的铂改性铝化物涂层,该涂层为β-(ni,pt)al单相涂层,pt、al和ni元素在β-(ni,pt)al相中均匀分布,其中:al元素含量为16-30wt%,pt元素含量为10-40wt%。
9.所述可作为热障涂层粘结层的铂改性铝化物涂层制备过程为:首先在基体上沉积铂元素以形成镀铂层,扩散后通过化学气相沉积(cvd)在所述镀铂基底上沉积al元素,并可通过cvd同时添加zr、hf、si等元素,最终获得可作为热障涂层粘结层的铂改性铝化物涂层;具体包括如下步骤:
10.(1)通过电镀将pt沉积在基体上形成镀铂层;所述镀铂层的厚度为1-8μm。
11.(2)通过热处理将镀铂层中pt元素扩散到基体当中。
12.(3)通过化学气相沉积(cvd)在镀铂层上面沉积al元素形成含有β-(ni,pt)al单相的改性铝化物涂层。
13.步骤(1)中,所述电镀工艺采用的镀液组成为:铂含量为5-25g/l的磷酸氢四氨合铂,1-20g/l的磷酸氢二钠,其余为水;镀液ph值为9-11,镀液温度为70-95℃,电镀电流密度为1-10a/dm2,电镀时间为10分钟到3小时。
14.步骤(2);所述热处理温度为1000-1140℃,热处理时间为1-5小时。
15.步骤(3)中,铝元素的沉积采用化学气相沉积(cvd)。铝元素的沉积过程中,温度900-1100℃,时间3-6小时;沉积之后形成含有β-(ni,pt)al单相的涂层。
16.该铂改性铝化物涂层中还可含有hf元素或zr元素或si元素,hf元素含量为0.1~2wt%,zr元素含量为0.1~2wt%,si元素含量为0.1~6wt%;通过cvd沉积相应元素,形成hf、zr或si改性的β-(ni,pt)al单相涂层。
17.本发明可作为热障涂层粘结层的铂改性铝化物涂层与传统的铂铝涂层相比具有以下优点:
18.1.本发明通过电镀与扩散渗铝结合的方法,制备可作为热障涂层粘结层的铂改性铝化物涂层,电镀配方当中不含有s、cl等影响涂层高温氧化及腐蚀的有害元素,提高了tbcs涂层的高温寿命。
19.2.本发明涂层铝含量较低,涂层热处理工艺合理,不影响基体力学性能。
20.3.本发明β-(ni,pt)al粘结层高温氧化性能良好,表面涂敷ysz后1100℃热循环寿命可达1100次/小时循环。
21.4.本发明β-(ni,pt)al粘结层还可含有hf、zr和si中的一种或两种,用作tbc的粘结涂层具有比mcraly及传统铂铝粘结层更为优异的服役寿命。
附图说明
22.图1实施例1中渗铝之后样品的xrd图谱分析。
23.图2是实施例2中铂改性铝化物涂层的扫描图谱、元素含量检测位置及元素含量。
24.图3是实施例3中铂改性铝化物涂层1100℃恒温氧化曲线。
25.图4是实施例1中涂敷ysz顶层的铂改性铝化物扫描图谱。
26.图5是实施例3中涂敷顶层ysz涂层的铂改性铝化物涂层1100℃保温5分钟炉冷5分钟测试热冲击1500次试样外观。
27.图6是实施例4中zr改性β-(ni,pt)al表面eds线扫描图谱。
28.图7是实施例4中ptzral涂层与ptal涂层在1100℃恒温氧化动力学曲线。
29.图8是实施例5中ptsial涂层的截面eds线扫描图谱。
30.图9是实施例5中ptsial涂层与ptal涂层在1100℃恒温氧化动力学曲线。
具体实施方式
31.为了进一步理解本发明,以下结合实例对本发明进行描述,但实例仅为对本发明的特点和优点做进一步阐述,而不是对本发明权利要求的限制。
32.实施例1:
33.本实施例基材采用单晶镍基高温合金dd5(rene5),其化学成分如下(质量百分比):co:7.5%,cr:7%,w:5%,mo:1.5%,al:6.2%,ta:6.5%,re:3%,ni:余量。
34.将直径为30毫米的高温合金棒用线切割加工成厚5毫米的圆片,在圆片的上方正
中间位置切φ3mm的圆孔,以方便电镀和气相沉积的过程中悬挂。
35.电镀溶液组成为:磷酸氢根四氨合铂15g/l(按电镀液中铂浓度计算),磷酸氢二钠10g/l,其余为水。
36.高温合金样品磨抛后在压力为0.3mpa的喷砂机中喷砂。然后将样品超声清洗后吹干备用。然后该样品浸入到王水溶液中30秒,然后浸入到蒸馏水中。
37.制得的样品接下来立即电镀。条件如下:
38.电流密度=1a/dm2;
39.温度=95℃;
40.ph=11;
41.沉积时间=60分钟;
42.电镀铂层厚度为5微米。
43.渗铝采用化学气相沉积,采用的渗铝源为铬铝合金粉,无惰性剂,活性剂为氯化铵,在真空状态下渗铝5小时,温度为1050℃,升温速率为6℃/min。渗铝后所得涂层的截面图如图5所示,由eds分析得出,涂层厚度为33微米,涂层内的平均铂含量为28wt.%,xrd结果分析涂层内部组织为β-(ni,pt)al单相组织(图1)。
44.图4为制备ysz顶层的铂改性铝化物扫描图谱。
45.实施例2:
46.基体合金采用与实施例1相同的dd5(rene5)高温合金,将直径为13毫米的高温合金棒用线切割加工成厚2毫米的圆片,在圆片的上方正中间位置切φ3mm的圆孔,以方便电镀和气相沉积的过程中悬挂。
47.电镀溶液组成为:磷酸氢根四氨合铂10g/l(按电镀液中铂浓度计算),磷酸氢二钠8g/l,其余为水。
48.高温合金样品磨抛后在压力为0.3mpa的喷砂机中喷砂。然后将样品超声清洗后吹干备用。然后该样品浸入到王水溶液中30秒,然后浸入到蒸馏水中。
49.制得的样品接下来立即电镀。条件如下:
50.电流密度=2a/dm2;
51.温度=90℃;
52.ph=10;
53.沉积时间=40分钟;
54.电镀铂层厚度为4微米。
55.渗铝采用化学气相沉积,采用的渗铝源为铬铝合金粉,无惰性剂,活性剂为氯化铵,在真空状态下渗铝5小时,温度为1090℃,升温速率为6℃/min。渗铝后所得涂层的截面图如图5所示,由eds分析得出,涂层厚度为40微米,涂层内的平均铂含量为19wt.%(图2)。
56.实施例3:
57.基体合金采用dd419(cmsx-4)高温合金,其化学成分如下(质量百分比):co:9.6%,cr:6.46%,w:6.34%,mo:0.6%,al:5.46%,ti:1.01%,ta:6.49%,re:2.9%,ni:余量。
58.将直径为13毫米的高温合金棒用线切割加工成厚2毫米的圆片,在圆片的上方正中间位置切φ3mm的圆孔,以方便电镀和气相沉积的过程中悬挂。
59.电镀溶液组成为:磷酸氢根四氨合铂3g/l(按电镀液中铂浓度计算),磷酸氢二钠5g/l,其余为水。
60.高温合金样品磨抛后在压力为0.3mpa的喷砂机中喷砂。然后将样品超声清洗后吹干备用。然后该样品浸入到王水溶液中30秒,然后浸入到蒸馏水中。
61.制得的样品接下来立即电镀。条件如下:
62.电流密度=3a/dm2;
63.温度=95℃;
64.ph=11;
65.沉积时间=60分钟;
66.电镀铂层厚度为3微米。
67.渗铝采用化学气相沉积,采用的渗铝源为铬铝合金粉,无惰性剂,活性剂为氯化铵,在真空状态下渗铝4小时,温度为1100℃,升温速率为6℃/min。
68.图3是本实施例中铂改性铝化物涂层1100℃恒温氧化曲线,1100℃恒温氧化1000小时后涂层氧化增重不超过0.35mg/cm2,表现出优异的抗高温氧化性能。
69.图5是本实施例中涂敷顶层ysz涂层的铂改性铝化物涂层1100℃保温5分钟炉冷5分钟测试热冲击1500次试样外观,ysz涂层无明显剥落,显示出tbcs涂层优异的抗热冲击性能。
70.实施例4:
71.基体合金采用与实施例1相同的dd5(rene5)高温合金,将直径为13毫米的高温合金棒用线切割加工成厚2毫米的圆片,在圆片的上方正中间位置切φ3mm的圆孔,以方便电镀和气相沉积的过程中悬挂。
72.电镀溶液组成为:磷酸氢根四氨合铂8g/l(按电镀液中铂浓度计算),磷酸氢二钠8g/l,其余为水。
73.高温合金样品磨抛后在压力为0.3mpa的喷砂机中喷砂。然后将样品超声清洗后吹干备用。然后该样品浸入到王水溶液中30秒,然后浸入到蒸馏水中。
74.制得的样品接下来立即电镀。条件如下:
75.电流密度=2a/dm2;
76.温度=90℃;
77.ph=10;
78.沉积时间=40分钟;
79.电镀铂层厚度为3微米。
80.渗铝采用化学气相沉积,采用的渗铝源为铬铝合金粉,无惰性剂,活性剂为氯化氢及氯化锆,在真空状态下渗铝4小时,温度为1085℃,升温速率为6℃/min。渗铝后所得涂层的表面形貌如图6所示,由eds分析得出,涂层当中含有白色的富zr相,ptzral涂层在1100℃的恒温氧化性能优于ptal涂层(图7)。
81.实施例5:
82.基体合金采用与实施例1相同的dd5(rene5)高温合金,将直径为13毫米的高温合金棒用线切割加工成厚2毫米的圆片,在圆片的上方正中间位置切φ3mm的圆孔,以方便电镀和气相沉积的过程中悬挂。
83.电镀溶液组成为:磷酸氢根四氨合铂2g/l(按电镀液中铂浓度计算),磷酸氢二钠8g/l,其余为水。
84.高温合金样品磨抛后在压力为0.3mpa的喷砂机中喷砂。然后将样品超声清洗后吹干备用。然后该样品浸入到王水溶液中30秒,然后浸入到蒸馏水中。
85.制得的样品接下来立即电镀。条件如下:
86.电流密度=2a/dm2;
87.温度=90℃;
88.ph=10;
89.沉积时间=80分钟;
90.电镀铂层厚度为4微米。
91.渗铝采用化学气相沉积,采用的渗铝源为铬铝合金粉和硅粉,无惰性剂,活性剂为氯化铵,在真空状态下渗铝5小时,温度为1090℃,升温速率为6℃/min。渗铝后所得涂层的截面图如图8所示,由eds分析得出,si主要富集在涂层外层及互扩散区,ptsial涂层在1100℃的恒温氧化性能优于ptal涂层(图9)。