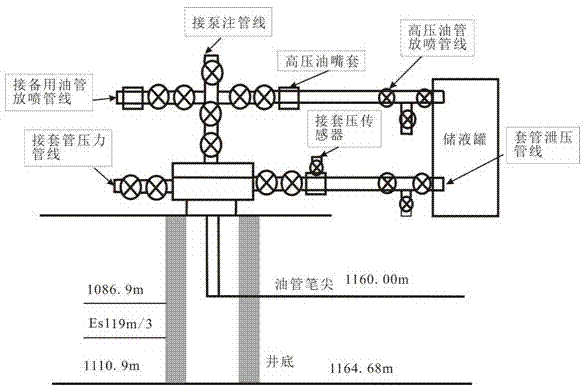
本发明涉及一种稠油油藏开采井酸化解堵方法,尤其涉及一种针对(铁)方解石、(铁)白云石等碳酸盐胶结型砂岩稠油井的混合释热解堵方法。
背景技术:
:稠油热采是油气开采领域中的热点和难点,如何高效合理开采沥青、蜡质含量高的油层,提高稠油油藏的采出程度是摆在我国陆相油气开采面前的关键问题。造成油井堵塞的原因是有机堵塞与无机堵塞共同作用的结果,有机堵塞物主要是沥青质等原油重质组分,在热采过程中原油组分发生变化,轻烃含量减少,重烃类沥青质含量大量增加,含有大量胶质和沥青质的原油重质组分在受到蒸汽驱动运移到产油井近井地带,地层温度较低,流动能力变差,沥青质在岩石孔隙表面大量沉积导致了油藏润湿性的改变,影响油/水相对渗透率造成生产井堵塞。无机堵塞物主要为碳酸盐和硅酸盐,蒸汽矿化度低于地层水矿化度,造成粘土膨胀,渗透率降低。油层的粘土胶结物富含蒙皂石和高岭石,与蒸汽接触会膨胀、分散形成大量固相微粒,迁移至油层深部“架桥”使油层的渗透率降低。如何有效降粘、酸溶碳酸盐和粘土矿物是增加稠油油层采收率的关键。目前酸化技术有了长足的进步,但迄今为止还没有在酸化作业全过程的利用化学放热反应的有效伴热酸溶技术,多借助酸化后的物理热-蒸汽加热技术,无法达到同时原油降粘和酸溶矿物的目标。中国专利公开号为:cn101255789a的专利申请提供了一种油井的酸化解堵方法,主要针对于低渗透油井,酸化的目的主要是解除堵塞,同时尽可能提高低渗透潜力层的渗透率,提高油井产量。其特征在于,在传统酸化施工前向目的层注入液态气体作为增能段塞,所述的液态气体为液氮或者液态二氧化碳,注入量为每米油层1~1.5立方米,优选1.2立方米,注入速度为100~250l/min,优选为200l/min。采用该发明的酸化解堵方法,能够有效的解除地带堵塞,提高油井产量,解堵成功率达98%以上,平均单井增产油井1.5吨/天以上。该专利申请是针对低渗透油井的解堵方法,并非针对中高渗砂岩油藏注水井的深部解堵方法。中国专利公开号为cn101126314a的专利申请提供了一种泡沫段塞分流酸化技术,其方法是通过注入泡沫段塞,利用泡沫流体的分流能力对高渗层进行暂时封堵,将酸液转向低渗层,实现不同渗透率的小层均匀进酸,从而有效解除储层酸溶性堵塞;同时利用泡沫流体的高携带能力和氮气的膨胀能将酸化后的固体颗粒和残酸反排,降低二次伤害。该专利申请适用于注入能力悬殊的非均质油气藏,能解决层间矛盾,达到均匀布酸提高吸酸剖面、均匀改善各层渗透率的目的。技术实现要素:针对上述现有技术,本发明提供了一种针对(铁)方解石、(铁)白云石等碳酸盐胶结型砂岩稠油井的混合释热解堵方法,本发明通过分步对井筒稠油及井筒附近油层作业,可有效提高高蜡、高沥青质稠油的采收率。本发明是通过以下技术方案实现的:一种针对碳酸盐胶结型砂岩稠油井的混合释热解堵方法,包括以下步骤:a.对井筒进行加热,使井筒内及井筒附近(井筒边缘半径1~2m内)的稠油降粘;b.向井筒内注入前置液(酸洗井壁),然后加入主体液;前置液为轻配氯基酸;主体液是由轻配氯基酸和释热聚氟解堵剂按体积比0.8~1.2:0.8~1.2(优选1:1)组成的,注入方式为:交替注入轻配氯基酸和释热聚氟解堵剂;注入后,化学伴热热剥油膜附着,轻配氯基酸缓慢酸溶碳酸盐,防止大颗粒碳酸盐溶蚀脱落后造成微粒运移形成“桥堵”,进行深部解堵;所述轻配氯基酸是由以下重量百分数的组分组成的:氯基酸混合液13%~17%,缓溶剂8%~12%,余量为水或矿化水(矿化水的具体矿化度根据油层水矿化物配置,避免发生盐敏感性);优选的,氯基酸混合液15%,缓溶剂10%,余量为水或矿化水。其中,氯基酸混合液是由ch2cl2、ch2clf和nh4cl组成的,三者的质量比为0.8~1.2:0.8~1.2:0.8~1.2(优选1:1:1);所述缓溶剂为聚二烯丁基二甲基氯化铵,缓溶剂的作用为:可有效缓速溶解(铁)白云石和(铁)方解石,且可有效防产层出砂;酸化施工过程中,充分利用轻配氯基酸中nhcl4的防膨作用,最大程度抑制了粘土矿物尤其是的蒙脱石的水敏效应;所述释热聚氟解堵剂,是由释热剂、聚氟酸和分溶剂组成的,三者质量比为:释热剂:聚氟酸:分溶剂=1~3:1~3:1~3(优选3:1:3);其中:释热剂是由55%(质量浓度)的硝酸铵溶液和40%的亚硝酸钠溶液(质量浓度)按质量比1:1混合而成的;聚氟酸是8%(质量浓度)的氟硼酸溶液;分溶剂是由12%(质量浓度)的盐酸和1%(质量浓度)的氢氟酸(hf)溶液按质量比1:1混合而成的;制备时,将释热剂、聚氟酸和分溶剂混合混匀即可;c.注入后置液,既可以防止粘土矿物膨胀堵塞油层孔隙和喉道,长期防垢,又可以持续提供化学热能,提高稠油的流动性;然后注入顶替液;所述后置液是由以下重量百分数的组分组成的:铁离子稳定剂2%~10%,粘土防膨剂2%~8%,活性剂2%~5%,水77%~94%;所述铁离子稳定剂选自iron-2066a(可常规市场购买得到的产品);所述粘土防膨剂选自氨基三亚甲基膦酸(atmp);所述活性剂选自质量百分数为3%的氯化铵水溶液;所述顶替液为质量百分数为2%的氯化铵水溶液;d.残液返排:采用慢速返排;酸化(指步骤b、c)时间16h以上(优选16~24h)(由于步骤b中采用轻配氯基酸对碳酸盐矿物进行缓释溶解,使得酸液不会迅速消耗在近井带,进而增大了酸液的波及范围,保证近井带储层溶蚀后的有效渗透半径;因此,酸化时间上需要较长的关井时间,可按照油层厚度适当延长关井时间,保证酸液对油层碳酸盐矿物的有效溶蚀);残渣返排时,需要注重稠油井的产油层特点,慢速返排,可按照每米油层1~1.5m3/h的速率返排,可有效防止油层出砂,同时避免矿物溶蚀残渣和沥青质运移堵塞近井带已经形成的优势通道,从而保证酸化的成功率;e.电热杆泵抽采油。所述步骤a中,对井筒进行加热的方式为电加热或闭式热流体循环加热,加热的目的是:对井筒内及井筒附近的稠油进行降粘,提高井筒内及井筒边缘半径1~2m内油层内稠油的流动性,方便原油抽吸,腾空步骤b所需要注入解堵剂的空间,降低注入的压力,增大注入剂量,提高释热聚氟解堵剂的作业半径。所述步骤b中,注入的主体液的体积为正替入井下油管容积的1.1~1.3倍,如此可使其充满井筒;注入时,关闭套管闸门,交替注入轻配氯基酸和释热聚氟解堵剂,使得释热聚氟解堵剂与轻配氯基酸混合融合,化学反应加热过程剥离附着在储层矿物上的油膜,溶离碳酸盐胶结物,达到对近井带5m~10m的油层增喉扩孔,整体增大稠油井的渗流半径。所述步骤b中,交替注入轻配氯基酸和释热聚氟解堵剂,挤入压力低于油层破裂压力,压力控制在各类井口的额定工作压力范围内,注入排量:0.5~1.0m3/min,关井稳定16h~24h。与现有技术相比,本发明聚焦碳酸盐胶结类型的砂岩稠油层,创新性采用混合释热解堵技术,通过对稠油进行物理化学加热工艺热采,达到了在降粘稠油,分解沥青质缔合体的基础上,剥离附着孔喉处碳酸盐胶结物的油膜,注入针对性强的酸液,酸溶剔除方解石和白云石等碳酸盐胶结物,达到了酸化与降粘的双重效果,从源头上进一步提高稠油油藏的采收率。本发明具有如下有益效果:1.采用电加热或闭式热流体循环技术,加热井筒附近1~2m半径的稠油降粘抽吸,腾空主体注入液的空间,降低注入的压力,增大注入剂量,有利于发挥主体液的作用半径。2.混合释热技术,采用电加热或闭式热流体循环技术,在主体酸化液中伴注释热聚氟解堵剂,发挥化学释热技术,酸化全过程受控于温度影响,有效剥离稠油油膜,提高酸液清除碳酸盐胶结物的效率。3.交替注入轻配氯基酸和释热聚氟解堵剂,使得释热聚氟解堵剂与轻配氯基酸混合融合,化学反应加热,剥离附着在储层矿物上的油膜,溶离碳酸盐胶结物,且有效防止出砂,溶离碳酸盐胶结物,整体增大稠油井的渗流半径。4、酸化施工过程中,充分利用轻配氯基酸中nhcl4的防膨作用,最大程度抑制了粘土矿物尤其是的蒙脱石的水敏效应。后置液有效防膨、防铁离子沉淀,有助于酸液及残渣返排。本发明的方法,解决了现有的常规酸化方法不适用于稠油油层酸化的难题,采用混合释热技术,提高原油流变性的同时,剥离碳酸盐胶结物表面的油膜,增大碳酸盐胶结物与酸液的接触表面积,化学释热提高酸岩反应温度,有效发挥所用主体酸液对碳酸盐胶结物的溶离效应,提高了措施成功率和酸化的有效期,从而可提高、中、乃至部分低渗稠油油藏的采收率。本发明的方法,针对碳酸盐胶结类型砂岩稠油层采用化学伴热技术,全过程加热降低稠油粘度,提高原油流变性,在剥离碳酸盐胶结物表面油膜的同时,采用轻配氯基酸(ch2cl2+chclf+nhcl4)一方面防止粘土膨胀,另一方面酸溶方解石和白云石等为主的碳酸盐胶结物,疏通砂岩储层喉道和孔隙中的填堵矿物,在酸化清洗碳酸盐胶结物时采用“热剥-缓溶-交替-慢排的工艺,即:化学伴热热剥油膜附着,轻配氯基酸缓慢酸溶碳酸盐,防止大颗粒碳酸盐溶蚀脱落后造成微粒运移形成“桥堵”。交替注入轻配氯基酸和释热聚氟解堵剂,对稠油持续化学加热,防止稠油粘结碳酸盐残渣堵塞油层,交替注入提高碳酸盐胶结物的溶蚀率。残液返排采用慢速返排,以免引起近井带油层堵塞。转入开采时,采用电热杆泵抽,达到对稠油的有效开采。前期的化学伴热热剥油膜附着,为酸化解堵奠定基础;交替注入主体酸液-热聚氟解堵剂配合轻配氯基酸兼顾酸溶碳酸盐胶结物,以实现深部解堵,后置液注入释热聚氟解堵剂、粘土防膨剂、铁离子稳定剂,使得既有长效防垢作用,又有防止原油油污吸附作用,化学伴热和电热杆泵抽技术共同提高稠油油层的采收率。附图说明图1:油层中盐酸盐胶结物发育产状及特征示意图,其中,①、②、③、④分别为不同位置的示意图。图2:施工管柱示意图。具体实施方式下面结合实施例对本发明作进一步的说明。下述实施例中所涉及的仪器、试剂、材料等,若无特别说明,均为现有技术中已有的常规仪器、试剂、材料等,可通过正规商业途径获得。下述实施例中所涉及的实验方法,检测方法等,若无特别说明,均为现有技术中已有的常规实验方法,检测方法等。实施例1:g54-x4井酸化设计及实施效果实施酸化改造层位:沙一段;井段:1086.9m~1100.9m。1油井基本数据及酸化层段基本情况1.1钻井基础数据,如表1所示。表11.2油层数据,如表2所示。表2层位井段m砂层厚度m渗透率10-3μm2实射井段m实射厚度m声波时差μs/ftes111086.9-1127.840.921.7541086.9-10947.181-112es111086.9-1127.840.921.7541097.3-1100.63.385-112es11+21086.9-1127.840.921.7541102.3-1110.98.658-1072作业情况及施工目的2.1作业情况该井于2004.5.11日ps防砂投产,共加入0.3-0.6mm覆膜砂21.6立方米。初期日产液3.5t,日产油2.7t,含水22.9%,动液面954m。目前正常生产时,日产液1.0t,日产油0.4t,综合含水54.4%,动液面865m。2013.3.14日日产液下降为0.2t,测液面561m,后停产,分析认为原油属于稠油,加生产过程中碳酸盐胶结物和盐类结垢堵塞近井带。为挖潜停产老油井的产油能力,提高g54区块的稠油采收率,决定对该井原井段酸化改造施工作业。2.2生产数据:如表3所示。表32.3施工目的:根据地质方案要求进行酸化,解除地层堵塞,探寻提高g54区块稠油采收率节能增效的技术方法。3设计依据3.1地质油藏条件该井碎屑岩油气显示,钻井液相对密度:1.10g/cm3-1.15g/cm3,粘度36mpa.s-45mpa.s,槽面油气水无显示。目前生产es1,实射井段1086.9m-1094m、1097.3m-1100.6m、1102.3m-1110.9m,19m/3层,属常温常压系统,周围无对应注水井。油稠,原油粘度为2689mpa.s,密度0.971g/cm3,凝固点-6℃。3.2储层伤害分析由图1①岩石光学图片可以看出,储层构架以砂质颗粒为主,碳酸盐胶结物以局部富集为特点,其它填隙物类型的量较少,渗透性潜在伤害主要来自于碳酸盐对土酸中氢氟酸的敏感伤害;图1②可以看出,储层构架中出现了生物碎屑和砂心鲕,泥模胶结也是普遍的,伤害主要由颗粒接触处的泥模和显微晶碳酸盐微粒的阻滞造成;图1③可以看到微晶方解石的充填和胶结(染色红色部分),孔隙大多为方解石致密胶结,残余粒间孔极少见,伤害主要是碳酸盐的胶结造成储层渗透性的破坏;图1④可以看到典型的砂心鲕粒结构,这类储层伤害的主因就是后期亮晶白云石(隐晶结构为主)的马牙状胶结,存在少量残余粒间孔,渗透性逐渐变差。3.3本设计依据3.1《g54-x4井油井酸化地质设计》3.2本设计所采用的法律、法规要求、标准、规范及操作规程符合国家相关法律法规、行业标准及规范。4酸化改造难点及主要工艺措施4.1酸化改造难点:层段跨度大,施工应尽量提高注入排量,提高各层改造效果。地层压力低,工作液返排困难。4.2主要工艺措施4.2.1对井筒进行加热(加热5~8小时),使井筒内及井筒附近(井筒边缘半径1~2m内)的稠油降粘;4.2.2向井筒内注入前置液,然后注入主体液,前置液为轻配氯基酸;主体液是由轻配氯基酸和释热聚氟解堵剂按体积比1:1组成的,注入方式为:交替注入轻配氯基酸和释热聚氟解堵剂;注入后,化学伴热热剥油膜附着,轻配氯基酸缓慢酸溶碳酸盐;所述轻配氯基酸是由以下重量百分数的组分组成的:氯基酸混合液15%,缓溶剂10%,余量为水;其中,氯基酸混合液是由ch2cl2、ch2clf和nh4cl组成的,三者的质量比为1:1:1;所述缓溶剂为聚二烯丁基二甲基氯化铵;所述释热聚氟解堵剂,是由释热剂、聚氟酸和分溶剂组成的,三者质量比为:释热剂:聚氟酸:分溶剂=3:1:3;其中:释热剂是由55%的硝酸铵溶液和40%的亚硝酸钠溶液按质量比1:1混合而成的;聚氟酸是8%的氟硼酸溶液;分溶剂是由12%的盐酸和1%的氢氟酸溶液按质量比1:1混合而成的;4.2.3注入后置液,既可以防止粘土矿物膨胀堵塞油层孔隙和喉道,长期防垢,又可以持续提供化学热能,提高稠油的流动性;然后注入顶替液;所述后置液是由以下重量百分数的组分组成的:铁离子稳定剂8%,粘土防膨剂5%,活性剂3%,水84%;所述铁离子稳定剂选自iron-2066a;所述粘土防膨剂选自氨基三亚甲基膦酸;所述活性剂选自质量百分数为3%的氯化铵水溶液;所述顶替液为质量百分数为2%的氯化铵水溶液;4.2.4残液返排采用慢速返排。酸化时间上需要较长的关井时间,一般16h~24h,保证酸液对油层碳酸盐矿物的有效溶蚀,在残渣返排时,需要注重稠油井的产油层特点,慢速返排,可按照每米油层1m3/h~1.5m3/h的速率返排,可有效防止油层出砂,同时避免矿物溶蚀残渣和沥青质运移堵塞近井带已经形成的优势通道,从而保证酸化的成功率。4.2.5电热杆泵抽采油。5酸液配方具体用量及施工参数设计5.1酸液配方设计5.1.1井筒加热并注入前置液10t酸洗井壁。5.1.2主体液:轻配氯基酸和释热聚氟解堵剂20t。5.1.3后置液:混合液10t。5.1.4顶替液:2%(质量百分比浓度)nh4cl溶液10t。5.2施工参数设计5.2.1注入方式:油管注入;5.2.2管柱组合:见图2;5.2.3注入排量:0.5~1.0m3/min;5.2.4井口:井口采用250型井口和250型四通底座。5.2.5施工限压:20mpa。5.2.6酸压作业:井筒加热兵正挤前置液(轻配氯基酸)10m3,泵压6.9-7mpa,排量700-1000l/min;正挤主体液(轻配氯基酸和释热聚氟解堵剂混合)20m3,泵压2.9-3.1mpa,排量700-1000l/min;正挤后置液(后置液)10m3,泵压4.3mpa,排量1400-1500l/min,正挤顶替液(氯化铵)15m3,泵压5.2mpa,排量1400-1500l/min。6酸化准备工作6.1化工公司准备工作按施工设计配方要求配酸,要求备料要留有10%余量,保证现场酸量和浓度达到设计要求,确保施工按设计进行。6.2作业队准备工作:6.2.1起原井管柱:起出井内全部生产管柱。6.2.2探冲砂:下笔尖探冲砂至1130m。6.2.3完成酸化管柱:上提探冲砂管柱完深1060m,完成酸化施工管柱,下井管柱必须认真检查、丈量准确,下井管柱必须认真检查、丈量准确,要求油管质量合格,抗内压值不低于50mpa。油管接箍及变换接头强度要求合格,丝扣涂密封脂上紧,保证不刺不漏不断脱。执行标准《常规修井作业规程第5部分:井下作业井筒准备》sy/t5587.5-2004。6.2.4装井口井口采用原井全套250井口,套管四通一侧闸门接反洗井管线,另一侧接放喷管线,放喷管线必须采用外径73mm,j55钢级以上硬管线,耐压35mpa以上,出口接不小于120°的钢制弯头,整个井口要用四道绷绳固定在地锚上。6.2.4配合施工准备:(1)井场备15m3池子1个(带隔板),2m3玻璃钢池子1个,排液专用罐1个,要求洁净无杂物(酸化施工严禁采用15m3铁池子盛放酸液);(2)备700型泵车3部、配套高压管汇1套;(3)400型泵车1台,本区达标污水20m3、空罐车2部;(4)井场要备足量液绳/尺,作业队要安排好计量人员,施工时配合酸化指挥人员计量液量。另外井场要备有足够的苏打水。7酸化效果酸化改造后初期日液8.3t,较酸压前增加7.3t,日油3.9t,增加3.5t,动液面570m,回升295m,后期产油能力维持在3t/d,24个月共计累油2100t,增产效果显著。实施例2针对碳酸盐胶结型砂岩稠油井的混合释热解堵方法步骤如下:a.对井筒进行加热(加热6小时)(电加热),使井筒内及井筒附近(井筒边缘半径1~2m内)的稠油降粘;b.向井筒内注入前置液(酸洗井壁),然后加入主体液;注入的主体液的体积为正替入井下油管容积的1.2倍;前置液为轻配氯基酸;主体液是由轻配氯基酸和释热聚氟解堵剂按体积比1:1组成的,注入方式为:交替注入轻配氯基酸和释热聚氟解堵剂;注入后,化学伴热热剥油膜附着,轻配氯基酸缓慢酸溶碳酸盐,防止大颗粒碳酸盐溶蚀脱落后造成微粒运移形成“桥堵”,进行深部解堵;轻配氯基酸是由以下重量百分数的组分组成的:氯基酸混合液15%,缓溶剂10%,余量为矿化水(矿化水的具体矿化度根据油层水矿化物配置,避免发生盐敏感性);其中,氯基酸混合液是由ch2cl2、ch2clf和nh4cl组成的,三者的质量比为1:1:1;所述缓溶剂为聚二烯丁基二甲基氯化铵;所述释热聚氟解堵剂,是由释热剂、聚氟酸和分溶剂组成的,三者质量比为:释热剂:聚氟酸:分溶剂=3:1:3;其中:释热剂是由55%(质量浓度)的硝酸铵溶液和40%的亚硝酸钠溶液(质量浓度)按质量比1:1混合而成的;聚氟酸是8%(质量浓度)的氟硼酸溶液;分溶剂是由12%(质量浓度)的盐酸和1%(质量浓度)的氢氟酸(hf)溶液按质量比1:1混合而成的;制备时,将释热剂、聚氟酸和分溶剂混合混匀即可;c.注入后置液,既可以防止粘土矿物膨胀堵塞油层孔隙和喉道,长期防垢,又可以持续提供化学热能,提高稠油的流动性;然后注入顶替液;所述后置液是由以下重量百分数的组分组成的:铁离子稳定剂6%,粘土防膨剂5%,活性剂3%,水86%;所述铁离子稳定剂选自iron-2066a;所述粘土防膨剂选自氨基三亚甲基膦酸(atmp);所述活性剂选自质量百分数为3%的氯化铵水溶液;所述顶替液为质量百分数为2%的氯化铵水溶液;d.残液返排:采用慢速返排;酸化(指步骤b、c)时间20h;残渣返排时,需要注重稠油井的产油层特点,慢速返排,可按照每米油层1~1.5m3/h的速率返排,可有效防止油层出砂,同时避免矿物溶蚀残渣和沥青质运移堵塞近井带已经形成的优势通道,从而保证酸化的成功率;e.电热杆泵抽采油。实施例3针对碳酸盐胶结型砂岩稠油井的混合释热解堵方法步骤如下:a.对井筒进行加热(加热8小时)(闭式热流体循环加热),使井筒内及井筒附近(井筒边缘半径1~2m内)的稠油降粘;b.向井筒内注入前置液(酸洗井壁),然后加入主体液;注入的主体液的体积为正替入井下油管容积的1.3倍;前置液为轻配氯基酸;主体液是由轻配氯基酸和释热聚氟解堵剂按体积比0.8:1.2组成的,注入方式为:交替注入轻配氯基酸和释热聚氟解堵剂;注入后,化学伴热热剥油膜附着,轻配氯基酸缓慢酸溶碳酸盐,防止大颗粒碳酸盐溶蚀脱落后造成微粒运移形成“桥堵”,进行深部解堵;轻配氯基酸是由以下重量百分数的组分组成的:氯基酸混合液13%%,缓溶剂12%,余量为水;其中,氯基酸混合液是由ch2cl2、ch2clf和nh4cl组成的,三者的质量比为0.8:1.2:0.8;所述缓溶剂为聚二烯丁基二甲基氯化铵;所述释热聚氟解堵剂,是由释热剂、聚氟酸和分溶剂组成的,三者质量比为:释热剂:聚氟酸:分溶剂=2:1:2;其中:释热剂是由55%(质量浓度)的硝酸铵溶液和40%的亚硝酸钠溶液(质量浓度)按质量比1:1混合而成的;聚氟酸是8%(质量浓度)的氟硼酸溶液;分溶剂是由12%(质量浓度)的盐酸和1%(质量浓度)的氢氟酸(hf)溶液按质量比1:1混合而成的;制备时,将释热剂、聚氟酸和分溶剂混合混匀即可;c.注入后置液,既可以防止粘土矿物膨胀堵塞油层孔隙和喉道,长期防垢,又可以持续提供化学热能,提高稠油的流动性;然后注入顶替液;所述后置液是由以下重量百分数的组分组成的:铁离子稳定剂2%,粘土防膨剂8%,活性剂2%,水88%;所述铁离子稳定剂选自iron-2066a;所述粘土防膨剂选自氨基三亚甲基膦酸(atmp);所述活性剂选自质量百分数为3%的氯化铵水溶液;所述顶替液为质量百分数为2%的氯化铵水溶液;d.残液返排:采用慢速返排;酸化(指步骤b、c)时间24h;残渣返排时,需要注重稠油井的产油层特点,慢速返排,可按照每米油层1~1.5m3/h的速率返排,可有效防止油层出砂,同时避免矿物溶蚀残渣和沥青质运移堵塞近井带已经形成的优势通道,从而保证酸化的成功率;e.电热杆泵抽采油。实施例4针对碳酸盐胶结型砂岩稠油井的混合释热解堵方法步骤如下:a.对井筒进行加热(加热5小时)(电加热),使井筒内及井筒附近(井筒边缘半径1~2m内)的稠油降粘;b.向井筒内注入前置液(酸洗井壁),然后加入主体液;注入的主体液的体积为正替入井下油管容积的1.1倍;前置液为轻配氯基酸;主体液是由轻配氯基酸和释热聚氟解堵剂按体积比1.2:0.8组成的,注入方式为:交替注入轻配氯基酸和释热聚氟解堵剂;注入后,化学伴热热剥油膜附着,轻配氯基酸缓慢酸溶碳酸盐,防止大颗粒碳酸盐溶蚀脱落后造成微粒运移形成“桥堵”,进行深部解堵;轻配氯基酸是由以下重量百分数的组分组成的:氯基酸混合液17%,缓溶剂8%,余量为矿化水(矿化水的具体矿化度根据油层水矿化物配置,避免发生盐敏感性);其中,氯基酸混合液是由ch2cl2、ch2clf和nh4cl组成的,三者的质量比为1.2:0.8:1.2;所述缓溶剂为聚二烯丁基二甲基氯化铵;所述释热聚氟解堵剂,是由释热剂、聚氟酸和分溶剂组成的,三者质量比为:释热剂:聚氟酸:分溶剂=1:3:1;其中:释热剂是由55%(质量浓度)的硝酸铵溶液和40%的亚硝酸钠溶液(质量浓度)按质量比1:1混合而成的;聚氟酸是8%(质量浓度)的氟硼酸溶液;分溶剂是由12%(质量浓度)的盐酸和1%(质量浓度)的氢氟酸(hf)溶液按质量比1:1混合而成的;制备时,将释热剂、聚氟酸和分溶剂混合混匀即可;c.注入后置液,既可以防止粘土矿物膨胀堵塞油层孔隙和喉道,长期防垢,又可以持续提供化学热能,提高稠油的流动性;然后注入顶替液;所述后置液是由以下重量百分数的组分组成的:铁离子稳定剂10%,粘土防膨剂2%,活性剂5%,水83%;所述铁离子稳定剂选自iron-2066a;所述粘土防膨剂选自氨基三亚甲基膦酸(atmp);所述活性剂选自质量百分数为3%的氯化铵水溶液;所述顶替液为质量百分数为2%的氯化铵水溶液;d.残液返排:采用慢速返排;酸化(指步骤b、c)时间16h;残渣返排时,需要注重稠油井的产油层特点,慢速返排,可按照每米油层1~1.5m3/h的速率返排,可有效防止油层出砂,同时避免矿物溶蚀残渣和沥青质运移堵塞近井带已经形成的优势通道,从而保证酸化的成功率;e.电热杆泵抽采油。上述虽然结合实施例对本发明的具体实施方式进行了描述,但并非对本发明保护范围的限制,所属领域技术人员应该明白,在本发明的技术方案的基础上,本领域技术人员不需要付出创造性劳动即可做出的各种修改或变形仍在本发明的保护范围以内。当前第1页12