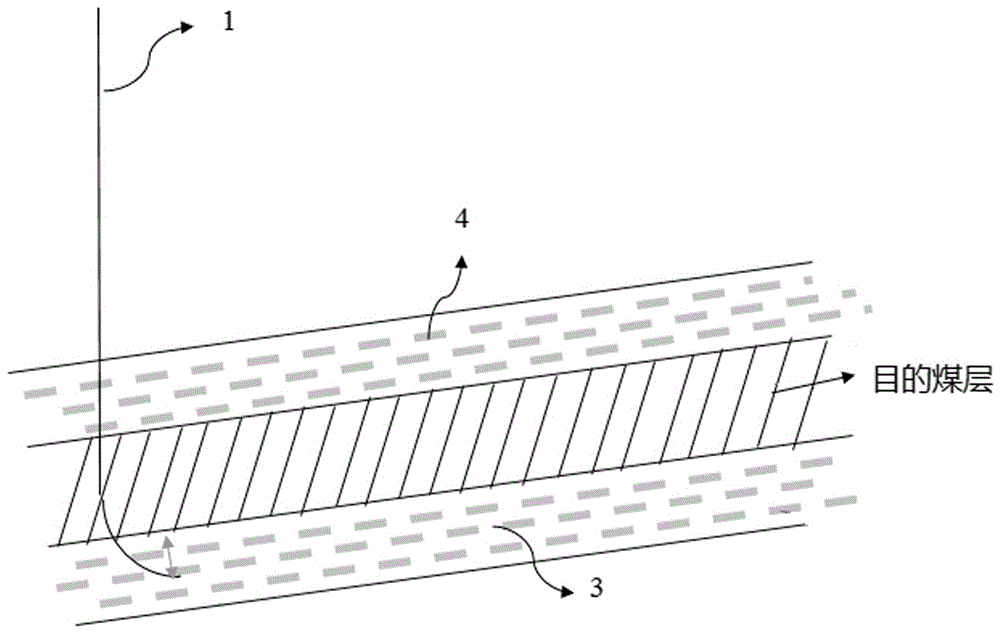
本发明涉及地下流体资源开采
技术领域:
,尤其涉及一种煤层气水平井系统改造方法。
背景技术:
:煤层气通常采用直井、定向井和水平井进行开采,而常用水平井工艺又分为单主支水平井、两主支多分支水平井、单主支下pe管多分支水平井以及多级压裂u型水平井和从式多级压裂水平井,各种开采方式的共同目标是提高煤层气开采效率以及加大投入产出比。由于我国不同地区煤层地质状况的多样性,以及各区块高、中、低煤阶含量不同,开采效果有很大差别。目前对于占比达80%的构造煤、低阶煤仍处于低效开发状态,即投入产出比很差。主要存在问题有:第一,直井、定向井开采效率低。第二,常规水平井工艺在低阶煤、构造煤的煤层中井眼稳定性差、容易坍塌,易发生井漏及垮塌卡钻等复杂事故。第三,即使井眼完成度较好,钻井泥浆(包括可降解泥浆,因井漏的原因)也可能堵塞煤层气渗流通道。第四,在煤层中钻进,依赖煤层钻遇率以提高泄气面积,一旦煤层钻遇率较低,对后期煤层气产量影响非常大;所谓煤层钻遇率,是指在煤层中的进尺与总进尺的比。第五,煤层轨迹对于排采的影响较大;随着煤层倾角的变化,在一些井段容易形成凹槽,投产排采时,形成水塞。当煤层底部存在结构煤并被钻遇时,煤灰在凹槽处聚集,排采时造成“灰堵”,不利于高产。第六,低阶煤层的低渗透率、煤质破碎等特点,造成煤层气井产气量低或者不产气。在实际煤层气开发过程中主要矛盾体现为低阶煤钻井事故较多,钻井周期长,薄煤层的煤层钻遇率低,目的煤层泥浆污染严重,压裂效果差、成本高,水平井钻井成本与钻井进尺成正比,煤层气开采效果却很低,造成投入产出比较差。授权公告号为cn101956548b的专利文件提供了一种在不增加水平井的占地面积的情况下提高多分支水平井的开采面积、提高开采效率的一种煤层气多分支水平井系统。但是该专利提供的方案中,水平井是在煤层中进行钻井的,依然没有解决低阶煤的井眼井壁坍塌问题,以及随开采时间延长,渗流通道逐渐被堵塞,造成后期低产气或不产气的问题,实际开采效率不高。技术实现要素:本发明提供了一种煤层气水平井系统改造方法,具有提高煤层气对于构造煤、低阶煤的开发效率,避免了煤层气水平井的井眼井壁坍塌以及渗流通道堵塞的问题,使煤层气水平井开发过程更平稳可靠,并且具有提高前期钻井施工和后期维护性作业效率的效果。具体技术方案如下:一种煤层气水平井系统改造方法,其中,包括如下步骤:选择低阶煤层或构造煤层进行改造,且煤层厚度在1.5~8.0m;第一水平井轨迹钻穿目的煤层的下底板,然后根据煤层轨迹沿着水平方向钻进300~2000m;第一水平井轨迹与目的煤层下边界距离为0.2~2.0m;井口至第一水平井轨迹进入底板后10~20m可选择下入5寸半~7寸技术套管;第一水平井轨迹采用水泥固井;第一水平井轨迹在目的煤层上边界部位且井斜角45~75°处进行开窗侧钻第二水平井轨迹,然后沿着水平方向钻进300~2000m,第二水平井轨迹与目煤层的上边界距离为0.2~2.0m;第一水平井轨迹水平段至井底与第二水平井轨迹开窗侧钻点至井底分别下入4寸~5寸半生产套管以形成第一水平井与第二水平井;第二水平井向下进行定向射孔,第二水平井进行规模化分段压裂或者拖动压裂;第一水平井向上进行定向射孔,第一水平井进行水力喷射或者小型压裂造缝;下入油管至煤层气下边界进行排水降压采气。进一步,第一水平井施工方法包括如下步骤:一开使用d311.2mm牙轮钻头,钻穿基岩风化带20m后,于井深60~80m完钻,下d244.5mm表层套管注水泥全封固;二开使用d215.9mm钻头,钻穿目的煤层后以90°~98°井斜角并保持在目的煤层下0.2~2.0m钻进10~20m后起钻,下入d177.8mm生产套管固井,注水泥封固,水泥浆返至目的煤层顶以上200m;三开使用d152.4mm钻头,根据煤层走向沿水平方向施工第一水平井轨迹,单支钻进300~2000m,下入d114mm生产套管。进一步,第一水平井施工方法包括如下步骤:一开使用d311.2mm牙轮钻头,钻穿基岩风化带20m后,于井深60m完钻,下d244.5mm表层套管,封固地表疏松层、砾石层。下入深度58m,注水泥全封固;二开使用d215.9mm钻头,钻穿目的煤层后以90°~98°井斜角并保持在目的煤层下0.2~2.0m钻进300~2000m完成第一水平井轨迹后起钻,下入d177.8mm生产套管,注水泥固井,水泥浆返至目的煤层顶以上200m。进一步,第二水平井施工方法包括如下步骤:在开窗位置下方2~5m下入可捞式定斜器,避免岩屑进入第一水平井内;起钻更换开窗钻具组合,在井斜角45~75°间进行套管开窗作业;开窗完成后,根据已知第一水平井轨迹及煤层数据,使用d152.4mm钻头沿目的煤层上边界距离为0.2~2.0m、水平井2方向钻进300~2000m完成第二水平井轨迹,下入d114mm生产套管并将套管顶部悬挂在开窗侧钻点,打捞定斜器。进一步,第二水平井对目的层,以60-80m分段向下进行泵送桥塞分簇射孔,建立井筒与目的层的通道,射孔后起出射孔枪进行压裂施工,待全部压裂完成后下入磨铣工具钻磨桥塞,之后完井下泵。进一步,射孔施工包括如下步骤:(1)射孔队到井后,负责人首先核对井号,与现场技术员确定后方能进入井场;(2)射孔队负责人与现场技术员认真核对该井的有关数据和通知单,确认无误后互相填写相关方告知书签字认定;(3)组织召开班前会,根据井场环境及该井施工风险因素的评估,布置风险控制措施,责任落实到人,指定应急逃生路线和集合点;(4)安装电缆防喷器和注脂控制头;(5)连接防喷管;(6)安装隔离短节;(7)安装桥塞坐封工具;(8)安装电子开关;(9)工具串整体连接;(10)安装防喷管吊装装置及密封控制管线;(11)安装地滑轮;(12)起吊防喷管串;(13)连接地面辅助设备;(14)开清蜡闸门;(15)起下工具及坐封桥塞、多簇射孔;(16)放空;(17)卸掉防喷管;(18)拆卸工具。进一步,起下工具及坐封桥塞、多簇射孔的操作步骤如下:(1)检查确认电缆与计量轮、地滑轮的相对位置正确;(2)全开清腊闸门和防掉闸板;(3)操作绞车缓慢下放射孔枪串,待工具串通过防掉闸板后,再将防掉闸板恢复关闭状态;(4)用较慢的速度开始下井,工具下放至距井口70m时,打开软件进行射孔器材的功能测试,确认正常后继续下放;(5)井深100m以上电缆下放速度为600m/h,到达400m时开泵到0.5方/分钟的排量,一旦看到电缆张力增加就慢慢提高电缆速度;(6)当要快到达预订深度时需提前100m告知泵车操作工,提前10m通知泵车准备停泵,提前5m通知停泵;绞车工在通知泵车准备停泵的同时降低电缆速度,一旦看到泵车停泵后的,泵压下降即刻马上停车;(7)上提电缆进行测井,从标准接箍开始丈量上提值,与计算的上提值相符时停车;(8)深度无误后跟现场甲方人员再次确认深度,经同意后操作员通过软件和地面点火面板给井下仪器信号,激发点火座封桥塞;(9)软件显示点火成功,绞车控制面板显示张力变化100kg左右,井口监控人员明显感觉电缆有震动,说明桥塞已座封;(10)桥塞坐封成功后用300m/h的速度上提工具串,40m后才能加速,但速度不能超过3000m/h;(11)上提工具串到射孔位置过程中,ccl测量接箍曲线,并量取点标差;(12)测量定位时,测量定位速度应小于1000m/h,上提值误差应小于±0.05m;(13)操作员核对接箍深度和套管长度是否与套后放—磁曲线图吻合,接箍深度和套管长度误差在±0.1m;(14)射孔深度确认无误后跟现场甲方人员再次确认深度,经同意后操作员方可点火;(15)软件显示点火成功,绞车控制面板显示张力变化100kg左右,井口监控人员明显感觉电缆有震动,说明射孔枪已起爆;(16)上提电缆过程中,深度在500m以上时,上提速度控制在4000m/h以内,深度在500-100m之间,上提速度控制在2500m/h以内,深度在100-20m之间,上提速度控制在1600m/h以内;(17)工具串起距井口10m时,打开防掉器闸板,停止动力上提,用人工背动或手压电缆将工具串起入防喷管内,关闭防掉器闸板,核实电缆层数和最外层电缆的圈数;(18)通知绞车工缓慢下放电缆,探测防掉器闸板2~3次,与绞车工共同确认工具串完全进入防喷管内,关闭清蜡闸门。进一步,多簇射孔作业结束后按照压裂泵注程序进行压裂施工,压裂施工的步骤如下:(1)连接施工好管线,用活性水循环主压车,循环液返回大罐,管线及井口试压45mpa;(2)泵送第一段桥射联作工具至预定射孔处,桥塞座封后上提射孔枪至第一簇位置,井筒施压20mpa;(3)井筒试压合格后进行射孔作业;(4)提出射孔枪,按泵注程序进行第一段压裂施工,采用光套管注入;(5)压裂完毕后进行下一段桥射作业。进一步,全井压裂施工完成后,放喷排液,油嘴控制放喷;当井口压力大于10mpa时,采用5mm油嘴放喷;当井口压力为10-5mpa时,采用8mm油嘴放喷;5-2mpa时,采用12mm油嘴放喷;小于2mpa时,敞放放喷;井口压力为零后,下磨铣工具钻磨桥塞、冲砂,描述记录返出物情况。进一步,钻磨包括如下步骤:(1)装配钻头短接和钻头到油管末端;(2)油管输送总成到底部直到轻轻的接触到复合桥塞;(3)上提管柱远离复合桥塞顶端1.2~1.8m;(4)保持泵注速度大约0.5m3/min以上;(5)开始泵注带动钻头,转速大约每分钟100~125转;(6)慢慢下放管柱直到泵压增加或悬重减小;(7)开始钻磨桥塞。前几分钟将磨掉中心管的上半部分;(8)当钻磨的时候,任何压力的增加是由于为了平衡钻磨复合桥塞;(9)上提管柱循环,让磨削物远离桥塞上端;(10)施加1t力在复合桥塞上继续钻磨复合桥塞;(11)在钻磨完复合桥塞上部后,上提油管串1.5m,确保下部区域平衡和循环磨削;(12)继续钻磨复合桥塞直到油管串重量和泵压重新恢复;(13)保持排量循环1.5-2个容积,观察出口连续无杂物,停泵;(14)推复合桥塞下半部分到井底或下一个桥塞的上部,若下推过程中遇砂卡,起出钻磨管柱,下冲砂管柱冲砂,再将复合桥塞下半部分推到井底或下一个桥塞的上部;(15)对于多个桥塞的钻磨,在停泵之前继续从步骤7开始钻磨;(16)钻磨第一个桥塞的下部将会些许增加磨铣时间。本发明在目的煤层的上下底板内施工水平分支井,由于低阶煤层、构造带煤层的上顶板和下底板多为砂泥岩或变质岩,稳定性相对煤层较好,可在钻井过程中使用各种泥浆体系而不污染目的层;能有效避免水平井的井眼在钻井中的井漏、煤层垮塌等复杂情况,也可使用国内比较先进的近钻头及旋转导向仪器加快施工进度,促进国内定向仪器及水平的发展。通过上顶板规模压裂造缝,形成低阶煤透气的天然过滤屏障,解决了低阶煤层气渗流通道易于堵塞的问题;通过下底板水力喷射或者小型压裂造缝,为低阶煤透水降压创造条件,而且可以防止煤粉过度采出,通过直井的排水降压采气实现低阶煤层气高效开采。本发明实现了排水与采气的分离,提高了排采效率。上述说明仅是本发明技术方案的概述,为了能够更清楚了解本发明的技术手段,而可依照说明书的内容予以实施,并且为了让本发明的上述和其它目的、特征和优点能够更明显易懂,以下特举本发明的具体实施方式。附图说明通过阅读下文优选实施方式的详细描述,各种其他的优点和益处对于本领域普通技术人员将变得清楚明了。附图仅用于示出优选实施方式的目的,而并不认为是对本发明的限制。而且在整个附图中,用相同的参考符号表示相同的部件。在附图中:图1为本发明的煤层气水平井系统改造方法的第一水平井轨迹着陆段示意图;图2为本发明的煤层气水平井系统改造方法的第一水平井轨迹示意图;图3为本发明的煤层气水平井系统改造方法的第二水平井轨迹套管开窗示意图;图4为本发明的煤层气水平井系统改造方法的第二水平井轨迹示意图。具体实施方式为了更好地了解本发明的目的、功能以及具体设计方案,下面结合附图,对本发明的煤层气水平井系统改造方法作进一步详细的描述。如图1-4所示,本发明的煤层气水平井系统包括水平井组,水平井组包括第一水平井轨迹1和第二水平井轨迹2,第一水平井轨迹1和第二水平井轨迹2的位置位于地质结构相对稳定的煤层下底板3和上顶板2;第一水平井轨迹1为倒l型,第一水平井轨迹1和第二水平井轨迹2相连,形成倒f型水平井组。具体来说,第一水平井轨迹1设置在煤层的下底板3,第二水平井轨迹2设置在煤层的上顶板2,其中第二水平井轨迹2为套管开窗井或侧钻井;第二水平井轨迹2进行规模化压裂,其作用是作为产气井;第一水平井轨迹1进行小型压裂,其作用是作为排水井,根据实际地质条件区分使用。下面根据施工顺序对本发明的煤层气水平井系统进行介绍。第一步,选择低阶煤层或构造煤层进行改造,且煤层厚度在1.5~8.0m。第二步,第一水平井轨迹1钻穿目的煤层的下底板3,然后根据煤层轨迹沿着水平方向钻进300~2000m;第一水平井轨迹1与目的煤层下边界距离为0.2~2.0m。第三步,井口至第一水平井轨迹1进入底板3后10~20m可选择下入5寸半~7寸技术套管。第四步,第一水平井轨迹1采用水泥固井。第五步,第一水平井轨迹1在目的煤层上边界部位,井斜角45~75°处进行开窗侧钻第二水平井轨迹2,然后沿着水平方向钻进300~2000m,第二水平井轨迹2与目煤层的上边界距离也为0.2~2.0m。值得注意的是,此方式也可以对未压裂的低产水平井进行改造。第六步,第一水平井轨迹1水平段至井底与第二水平井轨迹2开窗侧钻点至井底分别下入4寸~5寸半生产套管以形成第一水平井与第二水平井;第七步,第二水平井向下进行定向射孔,第二水平井进行规模化分段压裂或者拖动压裂。第八步,第一水平井向上进行定向射孔,第一水平井进行水力喷射或者小型压裂造缝。第九步,下入油管至煤层气下边界进行排水降压采气。下面以具体的实施例对上述施工顺序进行详细介绍实施例一如图1所示,水平井一开(即第一水平井轨迹1的竖直段)使用d311.2mm牙轮钻头,钻具组合:φ311.15mmpdc+φ177.8mmx/o+φ177mmdc+φ165mmdc+φ165mmx/o+φ127mmdp,坂土浆钻井液钻穿基岩风化带20m后,于井深60~80m完钻,下d244.5mm表层套管注水泥全封固,一开主要作用是封固地表疏松层、砾石层。水平井二开(即第一水平井轨迹1的折弯段)使用d215.9mm钻头,钻具组合:φ215.9mmpdc+φ172mm*1.5°motor+φ172mmfv+φ172mmubho+φ172mmnmdc+φ127mmdp+φ127mmhwdp;钻穿目的煤层后以90°~98°井斜角并保持在目的煤层下0.2~2.0m钻进10~20m后起钻,下入d177.8mm生产套管固井,注水泥封固,水泥浆返至目的煤层顶以上200m。二开主要作用是确定目的层并完成着陆。如图2所示,水平井三开(即第一水平井轨迹1的水平段)使用d152.4mm钻头,近钻头仪器钻具组合:φ152.4mmpdc+φ120mmnearbitsub+φ120mmmotor(1.50deg.)+φ120mmf/v+φ120mmubho+φ120mmnmdc+127mmgap+φ120mmnmdc+φ89mmdp,地质条件稳定的地层推荐近钻头仪器,总体成本低、机械钻速快、周期短、能快速稳定跟进煤层走向,也可根据地质条件使用常规em仪器或旋转导向仪器;再根据煤层走向沿水平方向施工第一水平井轨迹1,单支钻进300~2000m,下入d114mm生产套管至井底不大于50m,并将套管顶部悬挂在d177.8mm套管鞋以上10~20m内。第一水平井轨迹1的主要作用是:下入套管,通过小型压裂,解决煤层气水平井主井眼煤层坍塌、采气通道堵塞问题,在地质条件稳定的煤层底板3建立一种稳定的煤层气多分支水平井开发排水、疏灰通道,为钻井施工和后期维护性作业提供稳定的井眼环境。在开窗位置下方2~5m下入可捞式定斜器,避免岩屑进入第一水平井轨迹1;起钻更换开窗钻具组合,如图3所示,在井斜角45~75°间进行套管开窗作业;将工具下至切割位置后,先启动转盘或顶驱,钻柱旋转正常后,方能启动钻井泵,向钻柱内泵入钻井液。切割套管完毕后,继续旋转工具10分钟,以修整切割断面。然后试加钻压,能加上钻压,证明切割成功,可以加压进行锻铣作业,锻铣过程应密切观察扭矩的变化和跳钻情况。若出现跳钻现象,可降低转速和钻压,使工具工作平稳。待恢复正常后,再逐步恢复原钻压和转速,以找到最优工作参数。锻铣过程中派专人在振动筛处观察钻井液中返出物情况,以判断是否锻铣完毕,一旦预计锻铣套管锻铣完全,决定停止钻进,循环钻井液一周,清洗井眼。然后起钻,在工具未进入套管前,缓慢上提钻具,使之顺利进入套管,然后方能按正常速度起钻。如图4所示,开窗完成后,根据已知第一水平井轨迹1及煤层数据,使用d152.4mm钻头沿目的煤层上边界距离为0.2~2.0m、第一水平井轨迹1的方向钻进300~2000m完成第二水平井轨迹2,下入d114mm生产套管至井底不大于50m,并将套管顶部悬挂在开窗侧钻点,打捞定斜器完井。第二水平井轨迹2的主要作用是:下入套管,通过规模压裂,解决煤层气水平井主井眼煤层坍塌、采气通道堵塞问题,在地质条件稳定的煤层顶板2建立稳定的煤层气多分支水平井开发采气通道,为钻井施工和后期维护性作业提供稳定的井眼环境。实施例二水平井一开(即第一水平井轨迹1的竖直段)使用d311.2mm牙轮钻头,钻穿基岩风化带20m后,于井深60m完钻,下d244.5mm表层套管,封固地表疏松层、砾石层。下入深度58m,注水泥全封固。二开(即第一水平井轨迹1的折弯段和水平段)使用d215.9mm钻头,钻具组合:φ215.9mmpdc+φ172mm*1.5°motor+x/o+φ172mmfv+φ172mmubho+φ172mmnmdc+nmdc+gap+nmdc+φ127mmhwdp+φ127mmdp;可使用近钻头仪器或旋转导向仪器加快机械钻速,在钻穿目的煤层后以90°~98°井斜角并保持在目的煤层下0.2~2.0m钻进300~2000m完成第一水平井轨迹1后起钻,下入d177.8mm生产套管,注水泥固井,水泥浆返至目的煤层顶以上200m。在开窗位置下方2~5m下入可捞式定斜器,避免岩屑进入第一水平井轨迹1内;起钻更换开窗钻具组合,在井斜角45~75°间进行套管开窗作业;开窗完成后,根据已知第一水平井轨迹1及煤层数据,使用d152.4mm钻头沿目的煤层上边界距离为0.2~2.0m、水平井2方向钻进300~2000m完成第二水平井轨迹2,下入d114mm生产套管至井底不大于20~50m,并将套管顶部悬挂在开窗侧钻点,打捞定斜器完井。方案2较之方案1,方案2为二开完井,钻头大,难度加大,钻速较低,工期时间长。但井眼较大,与地层接触面积随之增大,各种工具及排采泵的选择多。第二水平井轨迹2进行规模化分段压裂或者拖动压裂的方法为:首先在上水平井向下进行定向射孔,然后进行规模化分段压裂或者拖动压裂,由于上底板3为砂岩或变质岩,质地坚硬,压裂液沿着上顶板2和低阶煤层间进行造缝,通过定向射孔的孔眼进行压裂,而且压裂后的支撑砂可进入低阶煤层一定距离,进一步形成低阶煤层气的有效通道,增大煤层气的渗流通道。具体来说,对目的层,以60-80m分段进行泵送桥塞分簇射孔,建立井筒与目的层的通道,射孔后起出射孔枪进行压裂施工,待全部压裂完成后下入磨铣工具钻磨桥塞,之后完井下泵。射孔要求如下:1.优选储层物性好的储层段对应进行射孔。2.多簇射孔,射孔簇尽量分散分布,增加新裂缝起裂的可能性。3.同一趟管柱施工的射孔簇总长度要适应防喷管的长度。4.避开固井质量差的层段和套管节箍(在测固井质量和校深后调整)。5.根据水平钻遇情况,每段按照3个射孔簇,1m/簇,8孔/m(现场使用1m枪,射孔枪装弹8发)。射孔枪技术性能射孔枪型号耐压(mpa)孔密(孔/m)相位(°)891058水平向下60射孔弹术性能射孔弹型号耐温/时间(℃/h)装药量(g/发)穿孔孔径(mm)平均穿深(mm)dp36rdx23120/48238.6635设备、工具参数表序号名称主要性能参数数量1测井车长×高×宽:9.0m×2.05m×3.2m;前轴7350kg,后轴15000kg,总装质量22350kg。1台2同轴电缆外径8mm,单芯+屏蔽层,耐温175℃,耐压105mpa7000m3吊车50t,40m拔杆1台4ccl磁定位仪承压105mpa,耐温175℃,2支5桥塞坐封工具baker20外径93mm,耐温175℃,耐压105mpa1支6桥塞工具点火头外径89mm,耐温175℃,耐压105mpa2个7多级点火头承压105mpa,耐温175℃,外径89mm,可实现40级选择点火3套8注脂密封头密封8mm电缆,密封压力70mpa1套9防喷管内径130mm,耐压70mpa20m10电缆防喷器内径130mm,耐压70mpa,配8mm电缆闸板1套11捕集器内径130mm,耐压70mpa1套12试压泵最高输出压力105mpa2套13空气站5方/min1台14转换法兰法兰转防喷管由壬2个射孔施工工序:1.射孔队到井后,负责人首先核对井号,与现场技术员确定后方能进入井场。2.射孔队负责人与现场技术员认真核对该井的有关数据和通知单,确认无误后互相填写相关方告知书签字认定。3.组织召开班前会,根据井场环境及该井施工风险因素的评估,布置风险控制措施,责任落实到人,指定应急逃生路线和集合点。4.安装电缆防喷器和注脂控制头5.连接防喷管6.安装隔离短节7.安装桥塞坐封工具8.安装电子开关9.工具串整体连接10.安装防喷管吊装装置及密封控制管线11.安装地滑轮12.起吊防喷管串13.连接地面辅助设备14.开清蜡闸门15.起下工具及坐封桥塞、多簇射孔(1)检查确认电缆与计量轮、地滑轮的相对位置正确。(2)全开清腊闸门和防掉闸板。(3)操作绞车缓慢下放射孔枪串,待工具串通过防掉闸板后,再将防掉闸板恢复关闭状态。(4)用较慢的速度开始下井,工具下放至距井口70m时,打开软件进行射孔器材的功能测试,确认正常后继续下放。(5)井深100m以上电缆下放速度为600m/h,到达400m时开泵到0.5方/分钟的排量,一旦看到电缆张力增加就慢慢提高电缆速度。(6)当要快到达预订深度时需提前100m告知泵车操作工,提前10m通知泵车准备停泵,提前5m通知停泵;绞车工在通知泵车准备停泵的同时降低电缆速度,一旦看到泵车停泵后的,泵压下降即刻马上停车。(7)上提电缆进行测井,从标准接箍开始丈量上提值,与计算的上提值相符时停车。(8)深度无误后跟现场甲方人员再次确认深度,经同意后操作员通过软件和地面点火面板给井下仪器信号,激发点火座封桥塞。要求:点火座封桥塞时井口有专人进行监控,其他无关人员远离井口。(9)软件显示点火成功,绞车控制面板显示张力变化100kg左右,井口监控人员明显感觉电缆有震动,说明桥塞已座封。要求:桥塞座封位置应距离前后射孔段最少10m,以确保成功座封及可靠的密封。(10)桥塞坐封成功后用300m/h的速度上提工具串,40m后才能加速,但速度不能超过3000m/h。(11)上提工具串到射孔位置过程中,ccl测量接箍曲线,并量取点标差。(12)测量定位时,测量定位速度应小于1000m/h,上提值误差应小于±0.05m。(13)操作员核对接箍深度和套管长度是否与套后放—磁曲线图吻合,接箍深度和套管长度误差在±0.1m。(14)射孔深度确认无误后跟现场甲方人员再次确认深度,经同意后操作员方可点火。(15)软件显示点火成功,绞车控制面板显示张力变化100kg左右,井口监控人员明显感觉电缆有震动,说明射孔枪已起爆。(16)上提电缆过程中,深度在500m以上时,上提速度控制在4000m/h以内,深度在500-100m之间,上提速度控制在2500m/h以内,深度在100-20m之间,上提速度控制在1600m/h以内。(17)工具串起距井口10m时,打开防掉器闸板,停止动力上提,用人工背动或手压电缆将工具串起入防喷管内,关闭防掉器闸板,核实电缆层数和最外层电缆的圈数。(核实上提深度,确保电缆及工具全部进入防喷管内,防止闸板将电缆割断)(18)通知绞车工缓慢下放电缆,探测防掉器闸板2~3次,与绞车工共同确认工具串完全进入防喷管内,关闭清蜡闸门。16.放空17.卸掉防喷管18.拆卸工具19.压裂施工多簇射孔作业结束后按照压裂泵注程序进行压裂施工。20.其余各段压裂施工结束后每次停泵测压降30分钟,然后按以上4.~18.所述程序完成其余段的泵送桥塞多簇射孔、钻铣桥塞与压裂一体化联作施工。压裂施工所采用的压裂砂为天然石英砂,性能指标:28mpa下,破碎率≤14%。压裂液为活性水,可选用清水+0.5%kcl。配液要求为:加入kcl过程中进行搅拌循环,保证kcl充分溶解。压裂施工的施工工序如下:(1)连接施工好管线,用活性水循环主压车,循环液返回大罐,管线及井口试压45mpa。(2)泵送第一段桥射联作工具至预定射孔处,桥塞座封后上提射孔枪至第一簇位置,井筒施压20mpa。(3)井筒试压合格后进行射孔作业。(4)提出射孔枪,按泵注程序进行第一段压裂施工,采用光套管注入。(5)压裂完毕后进行下一段桥射作业(后续施工按步骤2至步骤4反复施工)。泵注程序:(第一段模拟)压后作业(1)全井施工完成后,放喷排液,油嘴控制放喷。(2)当井口压力大于10mpa时,采用5mm油嘴放喷;当井口压力为10-5mpa时,采用8mm油嘴放喷;5-2mpa时,采用12mm油嘴放喷;小于2mpa时,敞放放喷。(3)放喷作业监测要求:放喷液进计量罐计量,每隔2小时观察记录放喷情况,包括时间、油嘴尺寸、井口压力、累计液量、水质表述、出灰出砂描述等。(4)井口压力为零后,下磨铣工具钻磨桥塞、冲砂,描述记录返出物情况。钻磨步骤:(1)装配钻头短接和钻头到油管末端:钻具组合:2-7/8"tbg油管+2-7/8"tg※50mpa单流阀+变扣接头+螺杆钻具(5lz95-7l)+五刀翼磨鞋(2)油管输送总成到底部直到轻轻的接触到复合桥塞。(3)上提管柱远离复合桥塞顶端1.2~1.8m。(4)保持泵注速度大约0.5m3/min以上。(5)开始泵注带动钻头,转速大约每分钟100~125转。(6)慢慢下放管柱直到泵压增加或悬重减小。(7)开始钻磨桥塞。前几分钟将磨掉中心管的上半部分。(8)当钻磨的时候,任何压力的增加是由于为了平衡钻磨复合桥塞。(9)上提管柱循环,让磨削物远离桥塞上端。(10)施加1t力在复合桥塞上继续钻磨复合桥塞。(11)在钻磨完复合桥塞上部后,上提油管串1.5m,确保下部区域平衡和循环磨削。(12)继续钻磨复合桥塞直到油管串重量和泵压重新恢复。(13)保持排量循环1.5-2个容积,观察出口连续无杂物,停泵。(14)推复合桥塞下半部分到井底或下一个桥塞的上部,若下推过程中遇砂卡,起出钻磨管柱,下冲砂管柱冲砂,再将复合桥塞下半部分推到井底或下一个桥塞的上部。(15)对于多个桥塞的钻磨,在停泵之前继续从步骤7开始钻磨。(16)钻磨第一个桥塞的下部将会些许增加磨铣时间。注意:在磨进过程中,应注意泵压变化,磨到胶筒部位时,泵压有可能突然升高,此时应停泵,但要保持悬重,轻微的活动管柱,待压力恢复正常后继续磨进。在下水平井向上进行水力喷射或者小型压裂造缝,目的是形成排水、排气通道,通过水的重力作用,流到下底板3分支水平井(第一水平井的水平段),然后在直井中(第一水平井的竖直段)下入油管至煤层气下边界进行排水降压采气。本发明所提供的一种煤层气f型水平井系统不仅适用于煤层气的开采,同时也适用于其它使用排水降压法开采的地质矿藏。本发明在目的煤层的上下底板内施工水平分支井,由于低阶煤层、构造带煤层的上顶板和下底板多为砂泥岩或变质岩,稳定性相对煤层较好,可在钻井过程中使用各种泥浆体系而不污染目的层;能有效避免水平井的井眼在钻井中的井漏、煤层垮塌等复杂情况,也可使用国内比较先进的近钻头及旋转导向仪器加快施工进度,促进国内定向仪器及水平的发展。通过上顶板规模压裂造缝,形成低阶煤透气的天然过滤屏障,解决了低阶煤层气渗流通道易于堵塞的问题;通过下底板水力喷射或者小型压裂造缝,为低阶煤透水降压创造条件,而且可以防止煤粉过度采出,通过直井的排水降压采气实现低阶煤层气高效开采。本发明实现了排水与采气的分离,提高了排采效率。最后应说明的是:以上实施例仅用以说明本发明的技术方案,而非对其限制;尽管参照前述实施例对本发明进行了详细的说明,本领域的普通技术人员应当理解:其依然可以对前述各实施例所记载的技术方案进行修改,或者对其中部分技术特征进行等同替换;而这些修改或者替换,并不使相应技术方案的本质脱离本发明各实施例技术方案的精神和范围。当前第1页12