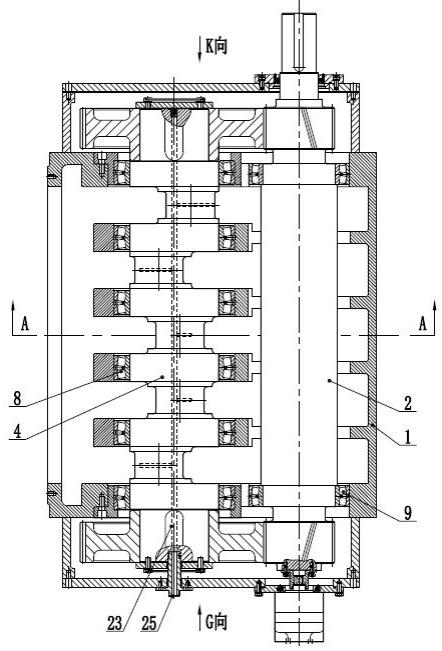
1.本发明涉及润滑技术及机械工程液压技术领域,具体涉及一种用于乳化液泵站的润滑系统和乳化液泵站。
背景技术:2.大型煤炭企业综采工作面支护设备设计的液压动力源普遍使用高压大流量乳化液泵,其工作的连续性、稳定性与可靠性直接影响煤炭企业的生产和经济效益。
3.随着煤矿向智能化、数字化、无人化发展,对设备的可靠性和稳定性要求越来越高,使得泵站的设计理念也发生了变化,由传统的抗污染设计设计、适宜的加工工艺性能、高冗余高余量,向精密控制、高精度要求精准余量设计转变。
4.目前,煤矿乳化液泵站普遍采用传动部件侵入油箱的设计结构,将传动部件箱和油箱合二为一,传统400升以下乳化液泵站完全依靠飞溅润滑,实现传动部件的润滑,而400升以上大流量泵站逐步实现了飞溅润滑和强制润滑相结合的润滑方式。油箱和传动箱合二为一的设计结构比较简单,技术上也很成熟,其存在如下难以克服的问题:(1)油箱和传动箱合二为一,油液存在内循坏,不能实现完全外循环,造成油液质量无法有效控制,特别是传动系统磨损产生的污染物不能及时排出系统,造成传动系统的磨损加剧、故障上升和寿命减低;(2)传动系统易造成油液温度上升、热平衡点向上偏移,不利于油液质量的控制,也不利于油液的稳定性;(3)不利于设备的检修维护,易造成油液的污染和浪费;(4)关键润滑部位做不到精准润滑。
5.近些年来,高端泵站得到迅速发展,其对润滑系统要求越来越高,出现了一些飞溅润滑、同轴强制润滑、外部独立润滑向结合的润滑系统,这种方式采用多系统冗余设计,设计复杂,设备成本也比较高。另外,新系统虽然保证了润滑系统的可靠,但同样加剧了冷却系统的负担,造成油液温度上升过快,油液粘度及热平衡点的偏移等一系列问题。
技术实现要素:6.为了克服现有煤矿乳化液泵站润滑系统的上述缺陷,保证泵的使用寿命和可靠性,本发明提供了一种用于乳化液泵站的润滑系统和乳化液泵站。
7.本发明采用的技术方案如下:一种用于乳化液泵站的润滑系统,所述乳化液泵站包括传动箱体,所述传动箱体内设有依次联动的动力轴、齿轮副、曲轴、连杆、滑块及柱塞。所述润滑系统包括:多个精准润滑末端,被配置为所述传动箱体内的各传动零部件的润滑点供油以实现精准润滑;供油单元,被配置为多个所述精准润滑末端强制输入润滑油,为外循环管路,具有过滤装置、冷却装置、控制装置及油箱,所述油箱独立设置在所述传动箱体之外。
8.优选的,所述精准润滑末端为喷嘴、油孔或油槽。
9.优选的,所述传动零部件包括曲轴轴承、动力轴轴承、齿轮副、滑块、柱塞、连杆轴瓦及连杆衬套。
10.优选的,所述供油单元包括:第一油管,配置为输入润滑油;一号输油通道,一端与所述第一油管连通,另一端连通至所述曲轴轴承的轴承座处的一号喷嘴;二号输油通道,一端与所述第一油管连通,另一端连通至所述动力轴轴承的轴承座处的二号喷嘴;三号输油通道,一端与所述第一油管连通,另一端连通所述齿轮副处的三号喷嘴;四号输油通道,一端与所述第一油管连通,另一端连通至所述滑块处的四号喷嘴;五号输油通道,一端与所述第一油管连通,另一端连通至所述柱塞处的五号喷嘴;六号输油通道,位于所述曲轴内,一端与所述第一油管连通,另一端延伸至所述曲轴的连杆颈外表面;七号输油通道,位于所述连杆的连杆体内,由所述连杆轴瓦延伸至所述连杆衬套。
11.优选的,所述六号输油通道包括轴向通道与径向通道,所述轴向通道由所述曲轴的一端沿轴向延伸至另一端,所述径向通道由所述轴向通道延伸至所述曲轴的连杆颈外表面。
12.优选的,所述六号输油通道与所述第一油管之间通过进油嘴连通。
13.优选的,所述供油单元还包括:油箱,配置为存储润滑油,作为所述第一油管的输入端;油泵,配置为向所述第一油管泵入润滑油,串接于所述第一油管;第二油管,配置为回流润滑油,一端连通所述传动箱体,另一端连通所述油箱;过滤器,串接于所述第一油管,置于所述油泵前;冷却器,串接于所述第一油管,置于所述油泵后。
14.优选的,所述供油单元还包括:集油池,配置为收集所述精准润滑末端的润滑油,设置于所述传动箱体底部的最低处,与所述第二油管的一端连通。
15.优选的,所述供油单元还包括:控制装置,配置为实现所述油泵在所述乳化液泵站启泵前的超前启动、及实现所述乳化液泵站停泵后的滞后停机。
16.一种乳化液泵站,包括有所述的润滑系统。
17.本发明是一种独立、外置、外循环且对传动部件精准润滑的润滑系统,具有如下有益效果:1.将油箱与齿轮箱分开,所有润滑均采用强制润滑,通过独立的控制装置实现完全可控的润滑方式,避免了传统的油箱和传动箱一体结构存在的由于安装布置倾角等造成的飞溅润滑失效问题;2.解决了飞溅润滑造成油温上升、系统发热的问题,有利于降低油液发热,从而保证油液的稳定和润滑效果;3.外循环使传动部件污染物能及时排除,避免系统因污染带来的损坏和寿命降低,解决了由于油液污染造成的传动系统失效问题;4.实现对煤矿乳化液泵站关键部位的精准润滑,避免了飞溅润滑或者飞溅-强制结合润滑的润滑不充分的弊端;5.有利于油液的管理,实现润滑系统的闭环管理,解决了以往乳化液泵站维修检修过程造成易造成油液污染、且维修检修后必须彻底换油的弊端;6.独立的外循环润滑系统可独立控制,容易实现可以实现超前启动和滞后停机,从而实现乳化液泵站启泵前、停泵后的超前、滞后润滑冷却,保证传动部件的润滑可靠;7.此种润滑方式相对于目前飞溅润滑与外独立润滑冗余设计的双润滑系统,简单可靠,避免了双润滑系统不可避免的油温上升以及由于油液粘温特性造成的对润滑油脂要求高、开泵初期压力高、后期润滑油压下降较大、不利于润滑系统监控保护等缺点。
附图说明
18.图1是本发明实施例的示意图。
19.图2是本发明实施例中a-a剖视示意图。
20.图3是本发明实施例中k向旋转示意图。
21.图4是本发明实施例中g向示意图。
22.图5是本发明实施例的润滑原理图。
23.传动箱体1、动力轴2、齿轮副3、曲轴4、连杆5、滑块6、柱塞7、曲轴轴承8、动力轴轴承9、连杆轴瓦10、连杆衬套11、第一油管12、一号输油通道13、一号喷嘴14、二号输油通道15、二号喷嘴16、三号输油通道17、三号喷嘴18、四号输油通道19、四号喷嘴20、五号输油通道21、五号喷嘴22、六号输油通道23、七号输油通道24、进油嘴25、油箱26、油泵27、第二油管28、过滤器29、冷却器30、集油池31、控制装置32。
具体实施方式
24.下面结合附图与实施例对本发明作进一步说明。
25.如图1~4所示,本实施例为一型五柱塞、曲轴六点支撑的卧式乳化液泵站,该型乳化液泵站由传动箱体1及传动箱体内的诸多传动零部件组成,而传动零部件包括依次联动的动力轴2、齿轮副3、曲轴4、连杆5、滑块6及柱塞7。
26.具体的,动力轴2通过两端的动力轴轴承9安装在传动箱体1内;曲轴4通过曲轴轴承8安装在传动箱体1内;动力轴2为齿轮轴,与曲轴4上的齿轮一起组成齿轮副3;连杆5的大头端设连杆轴瓦10,安装于曲轴4的连杆颈处;连杆5的小头端设连杆衬套11,安装于滑块6上;滑块6安装在传动箱体1内的滑道内,带动柱塞7沿缸套水平移动。
27.如图1~5所示,本实施例的润滑系统包括供油单元及多个精准润滑末端,精准润滑末端分别为各关键传动零部件供油以润滑,而供油单元用于为多个所述精准润滑末端强制输入润滑油。
28.如图1~4所示,精准润滑末端包括有:曲轴轴承8的轴承座处的一号喷嘴14;动力轴轴承9的轴承座处的二号喷嘴16;齿轮副3处的三号喷嘴18;滑块6处的四号喷嘴20;柱塞7处的五号喷嘴22;连杆轴瓦10处的油孔或油槽;连杆衬套11处油孔或油槽。
29.如图1~5所示,供油单元可以分为独立于传动箱体1外的与设置于传动箱体1上的两部分,其中独立于传动箱体1外的部分包括:第一油管12,作为润滑油的输入油管;油箱26,存储润滑油,作为第一油管12的输入端;油泵27,串接于第一油管12,作为强制润滑的动力源;第二油管28,一端连通传动箱体1,另一端连通至油箱26,作为润滑油的回流油管;过滤器29,串接于第一油管12,置于油泵27前,起过滤作用;
冷却器30,串接于第一油管12,置于油泵27后,起冷却作用;控制装置32,控制油泵27的启闭,以实现乳化液泵站启泵前、停泵后的超前、滞后润滑冷却,此处的超前启动、滞后关闭可通过延时电路、可编程控制器或手动控制来实现。
30.如图1~5所示,供油单元中设置于传动箱体1上的部分包括:一号输油通道13,与第一油管12连通,为一号喷嘴14供油,润滑冷却曲轴轴承8;二号输油通道15,与第一油管12连通,为二号喷嘴16供油,润滑冷却动力轴轴承9;三号输油通道17,与第一油管12连通,为三号喷嘴18供油,润滑冷却齿轮副3;四号输油通道19,与第一油管12连通,为四号喷嘴20供油,润滑冷却滑块6;四号输油通道21,与第一油管12连通,为五号喷嘴22供油,润滑冷却柱塞7;六号输油通道23,位于曲轴4内,分为轴向通道与径向通道,轴向通道由曲轴4的一端沿轴向延伸至另一端,轴向通道的一端堵死、另一端通过通过进油嘴25与第一油管12连通,径向通道由轴向通道延伸至曲轴4的连杆颈外表面,为连杆轴瓦10供油,以润滑冷却;七号输油通道24,位于连杆5的连杆体内,由连杆轴瓦10延伸至连杆衬套11,为连杆衬套11供油,以润滑冷却;集油池31,设置于传动箱体1底部的最低处,与第二油管28的一端连通,用于收集各精准润滑末端的润滑油。
31.本实施例是一种独立、外置、外循环且对传动部件精准润滑的润滑系统,具有如下优点:1.将油箱与齿轮箱分开,所有润滑均采用强制润滑,通过独立的控制装置实现完全可控的润滑方式,避免了传统的油箱和传动箱一体结构存在的由于安装布置倾角等造成的飞溅润滑失效问题;2.解决了飞溅润滑造成油温上升、系统发热的问题,有利于降低油液发热,从而保证油液的稳定和润滑效果;3.外循环使传动部件污染物能及时排除,避免系统因污染带来的损坏和寿命降低,解决了由于油液污染造成的传动系统失效问题;4.实现对煤矿乳化液泵站关键部位的精准润滑,避免了飞溅润滑或者飞溅-强制结合润滑的润滑不充分的弊端;5.有利于油液的管理,实现润滑系统的闭环管理,解决了以往乳化液泵站维修检修过程造成易造成油液污染、且维修检修后必须彻底换油的弊端;6.独立的外循环润滑系统可独立控制,容易实现可以实现超前启动和滞后停机,从而实现乳化液泵站启泵前、停泵后的超前、滞后润滑冷却,保证传动部件的润滑可靠;7.此种润滑方式相对于目前飞溅润滑与外独立润滑冗余设计的双润滑系统,简单可靠,避免了双润滑系统不可避免的油温上升以及由于油液粘温特性造成的对润滑油脂要求高、开泵初期压力高、后期润滑油压下降较大、不利于润滑系统监控保护等缺点。
32.显然,本发明的上述实施例仅仅是为了说明本发明所作的举例,而并非对本发明的实施方式的限定。属于本发明的实质精神所引申出的显而易见的变化或变动仍属于本发明的保护范围。