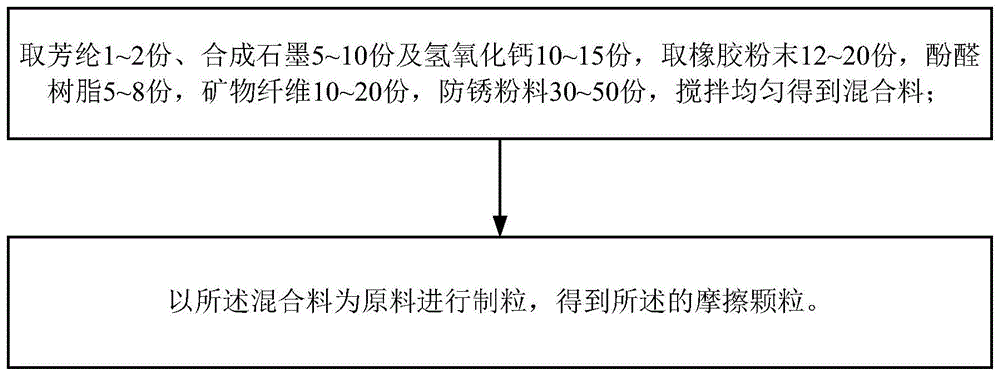
本发明涉及汽车零部件技术,具体涉及一种防锈摩擦颗粒、制备方法及用途。
背景技术:
:随物质水平的提高,国内汽车大量普及,对乘用车的安全性、舒适性的要求越来越高。刹车片是汽车制动系统关键部件,因此对刹车片的系数稳定性、耐磨性、耐高温性、舒适性等提出更高的要求。普通乘用车使用金属刹车片和nao刹车片。铸铁材质的刹车盘以及刹车片中的钢棉、铁粉,在较高湿度环境下驻车较长时间都容易生锈。导致刹车盘和刹车片之间由于生锈而产生一定的粘结力,称为锈粘结,严重影响制动舒适性及安全性。当前电子驻车系统的普及更是加剧了这一问题。弹性摩擦颗粒是指摩擦材料中应用的多组分复合的大颗粒材料。目前应用的弹性摩擦颗粒的制造工艺主要是橡胶混炼及使用溶剂的湿法造粒技术,存在污染气体排放、能耗高、工艺复杂、与基体结合强度差、物料浪费等问题。技术实现要素:鉴于以上所述现有技术的缺点,本发明的目的至少在于提供一种防锈摩擦颗粒、制备方法及用途,基于这种摩擦颗粒制成的刹车装置能够有效的改善了锈粘结问题,提高了制动舒适性及安全性。并且本发明提出的摩擦颗粒制备方法具有工艺路线短,能耗低,无污染物排放、与基体结合强度高、物料无浪费等优点。为实现上述目的及其他相关目的,本发明的一个实施方式提供一种防锈摩擦颗粒,所述摩擦颗粒以质量计包括以下组分:橡胶粉末12~20份,合成石墨5~10份,酚醛树脂5~8份,芳纶1~2份,导热矿物纤维10~20份,氢氧化钙10~15份,防锈粉料30~50份。可选地,所述橡胶粉末为粉末丁腈橡胶、粉末丁苯橡胶、轮胎粉中的一种或者其中几种的组合物。可选地,所述防锈粉料为亚磷酸钙、复合铁钛粉、三聚磷酸铝中的一种或者其中几种的混合物。可选地,所述粉末丁腈橡胶和粉末丁苯橡胶细度均为40~400目。可选地,所述轮胎粉细度大于40目。可选地,所述亚磷酸钙、复合铁钛粉、三聚磷酸铝的细度为大于300目。为实现上述目的及其他相关目的,本发明的一个实施方式提供一种防锈摩擦颗粒制备方法,包括步骤:取芳纶1~2份、合成石墨5~10份及氢氧化钙10~15份,取橡胶粉末12~20份,酚醛树脂5~8份,矿物纤维10~20份,防锈粉料30~50份,搅拌均匀得到混合料;以所述混合料为原料进行制粒,得到所述的摩擦颗粒。可选地,所述搅拌均匀得到混合料的步骤包括:取芳纶1~2份、合成石墨5~10份及氢氧化钙10~15份加入到高速搅拌机中搅拌1~3分钟;再取橡胶粉末12~20份,酚醛树脂5~8份,矿物纤维10~20份,防锈粉料30~50份加入高速搅拌机中继续搅拌6~10分钟,得到混合料。可选地,所述以所述混合料为原料进行制粒,得到所述的摩擦颗粒包括步骤:将所述混合料投入至造粒机中,制出摩擦颗粒;对所述摩擦颗粒进行筛选,得到符合条件的摩擦颗粒。为实现上述目的及其他相关目的,本发明提供一种防锈摩擦颗粒的用途,防锈摩擦颗粒用于制备刹车装置,所述防锈摩擦颗粒为所述的防锈摩擦颗粒,和/或所述防锈摩擦颗粒为通过所述方法制得的防锈颗粒。本发明提出的摩擦颗粒制备方法具有工艺路线短,能耗低,无污染物排放、与基体结合强度高、物料无浪费等优点。所制备的摩擦颗粒应用到摩擦材料中能够有效降低制动噪音、防止热衰退、改善速度压力敏感性、提高耐磨性,极大地改善了刹车片的综合性能。附图说明图1显示为本发明所述方法的流程图。具体实施方式以下由特定的具体实施例说明本发明的实施方式,熟悉此技术的人士可由本说明书所揭露的内容轻易地了解本发明的其他优点及功效。一种防锈摩擦颗粒,所述摩擦颗粒以质量计包括以下组分:橡胶粉末12~20份,合成石墨5~10份,酚醛树脂5~8份,芳纶1~2份,导热矿物纤维10~20份,氢氧化钙10~15份,防锈粉料30~50份。将防锈与弹性摩擦颗粒结合,在降低制动噪音、防止热衰退、改善摩擦速度压力敏感性、提高耐磨性的同时,利用上述摩擦颗粒制成的刹车盘能够有效提高刹车片的防锈性能。在某一实施方式中,所述橡胶粉末为粉末丁腈橡胶、粉末丁苯橡胶、轮胎粉中的一种或者其中几种的组合物。在某一实施方式中,所述防锈粉料为亚磷酸钙、复合铁钛粉、三聚磷酸铝中的一种或者其中几种的混合物。利用本发明所述的摩擦颗粒制成的刹车盘,防锈粉料通过与铁离子反应在铸铁刹车盘表面或者钢棉表面形成致密保护层,阻止氧化反应的进一步发生,从而达到抑制生锈的目的。在某一实施方式中,所述粉末丁腈橡胶和粉末丁苯橡胶细度均为40~400目。该细度有利于得到成分均匀的摩擦颗粒。在某一实施方式中,所述轮胎粉细度大于40目。轮胎粉是回收旧轮胎后进行粉碎制得的粉末,选用该细度的轮胎粉既能保证整体效果又能控制成本。在某一实施方式中,所述亚磷酸钙、复合铁钛粉、三聚磷酸铝的细度为大于300目。300目是对应一个相对比较小的颗粒尺寸,有助于缓蚀剂在混合料中分散的更加均匀,同时该细度为常见的加工细度,不需要特殊定制,能够降低成本。如图1所示,一种防锈摩擦颗粒制备方法,包括步骤:取芳纶1~2份、合成石墨5~10份及氢氧化钙10~15份,取橡胶粉末12~20份,酚醛树脂5~8份,矿物纤维10~20份,防锈粉料30~50份,搅拌均匀得到混合料;以所述混合料为原料进行制粒,得到所述的摩擦颗粒。通过物理咬合方式制得成型颗粒。造粒时,在外部压力作用下,颗粒粉末之间空隙不断被压缩,形成致密的颗粒,通过颗粒之间的物理咬合作用联结成完整的具有一定强度的整体;在外部挤压力消除后,颗粒组分中的大量橡胶组分以其高弹性发生回弹,使颗粒整体机械强度降低并具有一定的内部孔隙。在此过程中弹性颗粒中的粘合剂树脂不会发生固化反应,而在后续热压工序中,与摩擦材料中的其他组分一同固化,因此保证摩擦材料整体强度不会降低。物理咬合方式是对颗粒成型机理的概括性描述,指代造粒步骤。颗粒是由多种不同成分的粉末通过一定形式的力而互相结合、形成统一整体的。本发明中这个力由物理咬合方式提供。可以理解为:粉末形状不规则,表面凹凸不平;在外力作用下,一部分粉末表面的凸起嵌入临近粉末表面的凹坑,由此构成一个统一的整体。在某一实施方式中,所述搅拌均匀得到混合料的步骤包括:取芳纶1~2份、合成石墨5~10份及氢氧化钙10~15份加入到高速搅拌机中搅拌1~3分钟;芳纶是一种人工合成的有机纤维,通常会带有大量的静电荷。1~3min搅拌的目的是转移这部分电荷。再取橡胶粉末12~20份,酚醛树脂5~8份,矿物纤维10~20份,防锈粉料30~50份加入高速搅拌机中继续搅拌6~10分钟,得到混合料。6~10min搅拌是为了使混合料充分搅拌均匀。但在搅拌过程中,搅拌机的主轴叶片和飞刀都会对纤维有切割打碎的作用,因此搅拌时间也不宜过长。在某一实施方式中,搅拌时间为8分钟。在某一实施方式中,所述以所述混合料为原料进行制粒包括步骤:将所述混合料投入至造粒机中,制出摩擦颗粒。造粒机为对辊式干法辊压造粒机,通过造粒机中的对辊及破碎装置控制造粒直径为1~5mm。造粒直径在这个范围内既能保证颗粒成型,又能保证颗粒均匀,从而保证了刹车片的成分均匀。在某一实施方式中,在制出摩擦颗粒后的步骤后还包括:对所述摩擦颗粒进行筛选,得到符合条件的摩擦颗粒,所述条件为摩擦颗粒的直径为1~5mm。造粒直径在这个范围内既能保证颗粒成型,又能保证颗粒均匀,从而保证了刹车片的成分均匀。在某一实施方式中,在上述对所述摩擦颗粒进行筛选还包括步骤,将不符合条件的摩擦颗粒重新投入造粒机进行制粒、筛选,直至得到符合条件的摩擦颗粒。上述制备方法的具体实施方式如下:实施例1混料。取芳纶2份、合成石墨5份及氢氧化钙10份加入到高速搅拌机中搅拌2分钟;取粉末丁腈橡胶3份,轮胎粉6份,粉末丁苯橡胶3份,酚醛树脂5份,矿物纤维16份,亚磷酸钙15份、复合铁钛粉15份、三聚磷酸铝20份等剩余材料加入高速搅拌机中继续搅拌8分钟。造粒。将混合料投入到对辊式干法辊压造粒机中进行造粒,所述颗粒的形状及粒径由对辊及破碎装置控制,直径为2~4mm。筛分。振动筛选出合格颗粒,不合格颗粒可重新投入料斗制粒。实施例2混料。取芳纶1份、合成石墨10份及氢氧化钙15份加入到高速搅拌机中搅拌2分钟;取粉末丁腈橡胶10份,粉末丁苯橡胶6份,酚醛树脂8份,矿物纤维20份,亚磷酸钙10份、复合铁钛粉20份等剩余材料加入高速搅拌机中继续搅拌8分钟。造粒。将混合料投入到对辊式干法辊压造粒机中进行造粒,所述颗粒的形状及粒径由对辊及破碎装置控制,直径为小于2mm。筛分。振动筛选出合格颗粒,不合格颗粒可重新投入料斗制粒。对比例1本实例与实施例1的唯一区别在于制粒过程以重晶石替代多元防锈复合粉料。以重晶石替代相应材料为业内常用对比方式,为业内专业人士所熟知。对比例2本实例与实施例2的唯一区别在于制粒过程以重晶石替代多元防锈复合粉料。锈粘结力测试结果见下表:对比例1对比例2实验例1实验例2粘结力/n1121384653一种防锈摩擦颗粒的用途,防锈摩擦颗粒用于制备刹车装置,所述防锈摩擦颗粒为所述的防锈摩擦颗粒,和/或所述防锈摩擦颗粒为通过所述方法制得的防锈颗粒。在某一实施方式中,所述防锈摩擦颗粒占所述刹车装置中摩擦材料的总质量的10%~40%。这样既能保证防锈摩擦颗粒的应用效果,又不会影响刹车片的其他性能,同时能控制刹车片的制作成本。上述实施例仅例示性说明本发明的原理及其功效,而非用于限制本发明。任何熟悉此技术的人士皆可在不违背本发明的精神及范畴下,对上述实施例进行修饰或改变。因此,举凡所属
技术领域:
中具有通常知识者在未脱离本发明所揭示的精神与技术思想下所完成的一切等效修饰或改变,仍应由本发明的权利要求所涵盖。当前第1页1 2 3