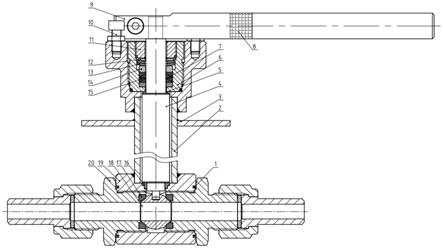
[0001]
本实用新型涉及阀门技术领域,具体涉及一种超低温球阀。
背景技术:[0002]
适用于介质温度-150℃以下的阀门称之为超低温阀门,包括超低温球阀,在液化天然气、液化石油气、化工、食品、空分装置及其它超低温行业都会用到超低温球阀,目前一些超低温球阀尚处于发展阶段,相关技术还未成熟,球阀在使用过程中易泄漏,使用寿命较低,结构复杂,可靠性不高等缺点。如液化天然气对阀门的材料及结构要求非常严格,材料不合格及结构不稳定,都会造成壳体及密封面的外漏或内漏,甚至导致液化天然气介质泄漏引起爆炸。
技术实现要素:[0003]
本实用新型所要解决的技术问题是:超低温球阀使用中易泄漏,使用寿命较低,本实用新型提供了解决上述问题的一种超低温球阀。
[0004]
本实用新型通过下述技术方案实现:
[0005]
一种超低温球阀,包括阀体和两个接头,两个接头相对端轴向侧壁加工有外螺纹,阀体上加工有内螺纹,两个接头的相对端由阀体的内螺纹孔两端旋入,通过内外螺纹的旋合实现阀体与两个接头连接为一体结构;所述阀体的轴向两端端面设置有密封槽,所述密封槽内安装有密封环,所述密封环压紧在阀体端面与接头外螺纹端部台阶面之间。
[0006]
目前一些超低温球阀尚处于发展阶段,相关技术还未成熟,球阀在使用过程中易泄漏,使用寿命较低,结构复杂,可靠性不高等缺点。如液化天然气对阀门的材料及结构要求非常严格,材料不合格及结构不稳定,都会造成壳体及密封面的外漏或内漏,甚至导致液化天然气介质泄漏引起爆炸。基于该技术背景,本实用新型改进现有超低温球阀结构,设计接头与阀体之间采用螺纹连接,可方便维修拆卸,接触部位设计金属对金属密封,并使用密封环进行额外密封,从而实现双重密封以杜绝泄漏问题。此外,两个接头通过与阀体螺栓可拆卸连接。
[0007]
进一步优选,所述接头内设有安装槽,所述安装槽内固定阀座,阀球通过阀座软密封固定;接头的安装槽加工有与阀球外圆一致的形状;在阀座失效后,所述与阀球外圆一致的形状与阀球接触实现硬密封。
[0008]
本实用新型设计阀球与接头之间实现硬密封和软密封双重密封。接头上安装阀座的槽有与阀球外圆周向相吻合的部位,当阀座由于失火或者磨损失效后,接头与阀球之间可实现硬密封,可最大程度的减轻泄漏。
[0009]
进一步优选,所述接头内密封安装阀球,所述阀球上还设有泄压孔;在阀球转动阀门关闭位置时,所述泄压孔用于连通阀体中腔与管道上游空间。
[0010]
本实用新型通过在阀球上设置有泄压孔,当阀门处于关闭位置时,密封在阀体中腔的介质由于温升原因体积增大,产生较大压力时,可通过泄压孔向管道上游泄压,从而避
免过高压力导致的阀门结构损坏。
[0011]
进一步优选,所述阀体的另一端与加长阀盖焊接连接,所述加长阀盖间隙配合套设在阀杆外。
[0012]
加长阀盖与阀体焊接一体化固定连接,利于保障两者连接处的密封性和连接刚度。
[0013]
进一步优选,还包括阀杆,所述阀杆用于连接手柄和设置在接头内的阀球;所述阀杆位于手柄的端部套设有填料函,所述填料函与阀杆之间的环形空腔内由下至上依次填充有v型填料i、v型填料ii、填料垫片、蝶形弹簧和蝶形弹簧垫片,且通过填料压紧螺母旋接在填料函顶部压紧固定。
[0014]
本实用新型的阀杆采用两片v形填料、并使用碟形弹簧加载以实现动载荷密封,可改进密封并减少磨损,且在使用过程中能补偿磨损并降低作用扭矩。
[0015]
进一步优选,所述阀杆的长度为165mm。
[0016]
通过增大阀杆的长度,主要用于延长介质与填料之间距离,对填料起到保护作用。
[0017]
进一步优选,还包括阀杆,所述阀杆用于连接手柄和设置在接头内的阀球;阀杆上部轴承与阀杆下部轴承和/或阀座的摩擦系数在0.05~0.11之间。
[0018]
阀杆上部轴承与阀杆下部轴承采用摩擦系数极小的耐超低温高分子材料,将阀杆与阀体、填料函隔开以避免金属对金属摩擦,延长阀杆的使用寿命,降低操作扭矩的同时提供平顺的手感;阀座采用摩擦系数极小的耐超低温高分子材料,故可实现较小的操作扭矩和优异的密封效果。
[0019]
进一步优选,所述手柄的长度为172mm。
[0020]
通过设计加长的手柄位于阀门较高位置,远离介质,降低操作扭矩且避免操作时出现冷灼伤。
[0021]
本实用新型具有如下的优点和有益效果:
[0022]
1、本实用新型改进现有超低温球阀结构,设计接头与阀体之间采用螺纹连接,可方便维修拆卸,接触部位设计金属对金属密封,并使用密封环进行额外密封,从而实现双重密封以杜绝泄漏问题;
[0023]
2、本实用新型设计阀球与接头之间实现硬密封和软密封双重密封。接头上安装阀座的槽有与阀球外圆周向相吻合的部位,当阀座由于失火或者磨损失效后,接头与阀球之间可实现硬密封,可最大程度的减轻泄漏;
[0024]
3、本实用新型通过在阀球上设置有泄压孔,当阀门处于关闭位置时,密封在阀体中腔的介质由于温升原因体积增大,产生较大压力时,可通过泄压孔向管道上游泄压,从而避免过高压力导致的阀门结构损坏;
[0025]
4、本实用新型的阀杆采用两片v形填料、并使用碟形弹簧加载以实现动载荷密封,可改进密封并减少磨损,且在使用过程中能补偿磨损并降低作用扭矩。
[0026]
5、本实用新型利于降低操作扭矩,阀杆上部轴承与阀杆下部轴承采用摩擦系数极小的耐超低温高分子材料,将阀杆与阀体、填料函隔开以避免金属对金属摩擦,延长阀杆的使用寿命,降低操作扭矩的同时提供平顺的手感;阀座采用摩擦系数极小的耐超低温高分子材料,故可实现较小的操作扭矩和优异的密封效果。
附图说明
[0027]
此处所说明的附图用来提供对本实用新型实施例的进一步理解,构成本申请的一部分,并不构成对本实用新型实施例的限定。在附图中:
[0028]
图1为本实用新型的一种超低温球阀结构示意图。
[0029]
附图中标记及对应的零部件名称:1-密封环,2-加长阀盖,3-滴水板,4-阀杆,5-阀杆上部轴承,6-填料函,7-填料ii,8-标签,9-手柄,10-限位螺栓,11-填料压紧螺母,12-蝶形弹簧垫片,13-蝶形弹簧,14-填料垫片,15-填料i,16-阀杆下部轴承,17-阀座,18-阀球,19-阀体,20-接头。
具体实施方式
[0030]
为使本实用新型的目的、技术方案和优点更加清楚明白,下面结合实施例和附图,对本实用新型作进一步的详细说明,本实用新型的示意性实施方式及其说明仅用于解释本实用新型,并不作为对本实用新型的限定。
[0031]
实施例1
[0032]
本实施例提供了一种超低温球阀,包括接头20、阀座17、阀球18、阀杆4、加长阀盖2和手柄9;接头20是连接阀体19和管道的中间装置,阀体19用于承压并连接各零件,阀球18是使流道开启或者关闭的装置。
[0033]
阀座17安装于接头20内,阀球18通过阀座17密封固定,加长阀盖2与阀体19连接,阀杆4的轴向两端连接到手柄9和阀球18上,可通过手柄9进行转动,并利用限位螺栓10进行限位,从而实现球阀的启闭。
[0034]
有两个接头20,两个接头20相对端轴向侧壁加工有外螺纹,阀体19上加工有内螺纹,两个接头20的相对端由阀体19的内螺纹孔两端旋入,通过内外螺纹的旋合实现阀体19与两个接头20连接为一体结构;所述阀体19的轴向两端端面设置有密封槽,所述密封槽内安装有密封环1,所述密封环1压紧在阀体19端面与接头20外螺纹端部台阶面之间。
[0035]
实施例2
[0036]
在实施例1的基础上进一步改进,接头20内设有安装槽,安装槽内固定阀座17,阀球18通过阀座17软密封固定;接头20的安装槽加工有与阀球外圆一致的形状,这样在阀座17一旦失效以后可以与阀球相接触从而实现硬密封。
[0037]
阀球18上还设有泄压孔;在阀球18转动阀门关闭位置时,泄压孔用于连通阀体19中腔与管道上游空间。阀体19的另一端与加长阀盖2焊接连接,加长阀盖2间隙配合套设在阀杆4外。
[0038]
阀杆4位于手柄9的端部套设有填料函6,填料函6与阀杆4之间的环形空腔内由下至上依次填充有v型填料i15、v型填料ii7、填料垫片14、蝶形弹簧13和蝶形弹簧垫片12,且通过填料压紧螺母11旋接在填料函6顶部压紧固定。其中,填料i15和填料117用于对阀杆4进行密封,填料垫片14用于传递碟形弹簧13对填料的压紧力,碟形弹簧13对填料产生压紧力,碟形弹簧垫片12是对碟形弹簧13起支撑作用的装置,填料压紧螺母11实现对填料的压紧或者放松。
[0039]
实施例3
[0040]
在实施例2的基础上进一步改进,还包括阀杆4,所述阀杆4用于连接手柄9和设置
在接头20内的阀球18;阀杆上部轴承5、阀杆下部轴承16和阀座17均采用摩擦系数极小的耐超低温高分子材料。
[0041]
阀杆上部轴承5用于隔开阀杆4与填料函6,避免金属对金属摩擦;阀杆下部轴承16用于隔开阀杆4和阀体19,避免金属对金属摩擦.
[0042]
手柄9的长度为172mm,加长的手柄9位于阀门较高位置,远离介质,降低操作扭矩且避免操作时出现冷灼伤。
[0043]
此外,在加长盖板2上还焊接有滴水板3,滴水板3用于避免阀门运行中产生的冷凝水滴落到阀体19和保温层上。在手柄9上包覆标签8,指示阀门的启闭方向。
[0044]
以上所述的具体实施方式,对本实用新型的目的、技术方案和有益效果进行了进一步详细说明,所应理解的是,以上所述仅为本实用新型的具体实施方式而已,并不用于限定本实用新型的保护范围,凡在本实用新型的精神和原则之内,所做的任何修改、等同替换、改进等,均应包含在本实用新型的保护范围之内。