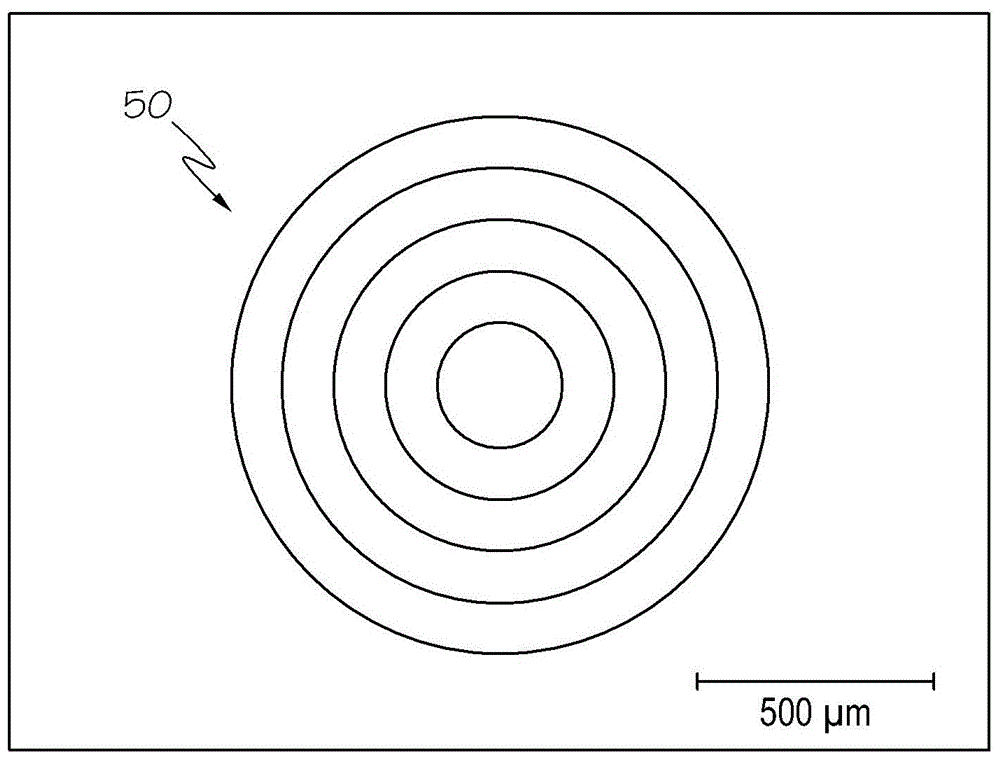
枝晶状微结构中枝晶臂间距的自动量化方法本申请要求于2012年4月12日提交的美国临时申请61/623,145的优先权。技术领域本发明总体上涉及金属铸件的微结构细度的量化,且更具体地涉及金属铸件的枝晶状微结构中的枝晶臂间距(DAS)的自动量化,从而避免必须手动地进行这种测量。
背景技术:所有铸造铝基部件(例如,发动机本体、气缸盖、变速器部件等)的得到微结构在性质上通常由合金成分且更具体地由固化条件确定。在亚共晶合金(即,含有比共晶与其它合金成分相对应的铝更多的铝的合金,以便在固化时减少二次枝晶臂间距,其示例包括A356和319,均为Al-7%Si-Mg变体)中,材料往往枝晶状地固化。例示枝晶状固化的其它这种铝合金示例包括354、355、360、380、383等。该合金族的典型微结构包括一次枝晶相和第二颗粒相(如,硅颗粒和富含铁的金属间化合物)。铸造结构中的这些相的相对数量、大小和形态主要取决于铸造条件以及合金成分。枝晶单元大小(DCS)和DAS(有时称为二次枝晶臂间距(SDAS))已经长时间用来量化铸件的细度,继而可以用于获得材料和相对属性的更好理解,其中,作为通用规则,具有较小DAS的铸造部件往往具有更好的延展性和相关机械属性。与铝合金铸件(总体上)以及DAS属性(具体地)有关的讨论可见于由本发明受让者拥有的许多其它专利申请中,包括于2009年1月20日提交的美国专利申请12/356,226、于2009年3月12日提交的美国专利申请12/402,538、于2009年5月12日提交的美国专利申请12/454,087以及于2011年3月8日提交的美国专利申请12/932,858,其全部通过参考在此引入。已经做了许多工作来描述枝晶精细化及其与固化条件的关系,在1950年Alexander和Rhines开始,其首先建立成分和固化速率对某些枝晶特征的影响的定量基础。下表1概述了已知文献来描述枝晶结构的细度的定量项。在这些中,Spear和Gardner(1963)使用枝晶单元大小定量地描述了枝晶结构的尺度,其通过随机线性拦截获得且在其图3(a)中称为DCSli。在Spear和Gardner之后,Jaquet和Hotz(1992)在其研究中也使用DCSli来量化枝晶体。Levy等(1969)、Oswalt和Misra(1980)、Radhakrishna等(1980)和Flemings等(1991)均讨论DAS来量化枝晶结构。在这些方法中,DAS通过线性拦截方法获得,其中,选择线来与一系列限定好的二次枝晶臂相交。McLellan(1982)使用枝晶单元数量(CPUA)来量化微结构且声称其比DAS更准确地描述了变形过程。然而,Levy等(1969)已经批判地分析了DAS和CPUA两者的测量以表征铸造结构,且指出,DAS测量的标准偏差小于CPUA测量,而且CPUA计算的平均单元大小大于平均DAS。CPUA的测量涉及枝晶体的一次、二次和三次臂,而DAS测量通常仅仅涉及二次臂间距。与DAS手动测量有关的方法由本发明受让者经常使用,从而进行铝铸件的DAS测量。这种过程通常首先包括制备金相样品,其根据已知标准(例如,用于金相样品制备的美国测试协会和材料标准指导,AmericanSocietyofTestingandMaterialsStandardGuideforPreparationofMetallographicSpecimens(也称为ASTME3))制备,其一部分在下表2中复制。要分析样品的表面预期具有足够的质量以反映颗粒的最真实可能大小和形状。在一种形式中,抛光平面将包括共晶相,与周围的基体相比看起来更暗。因而,在一种形式中,金相样品被最终抛光以获得平坦的几乎镜像表面光洁度。化学蚀刻可以用于增强枝晶结构的对比度,其中,在一种形式中,蚀刻可以根据ASTME407。优选地,样品被清洁和干燥,同时抛光缺陷(例如,曳尾、点蚀、擦痕、拉出物(pullout)和应变)应当保持最小。类似地,测试条件和偏差应当事先一致。在优选形式中,每个样品将在许多视场检查,其中每个经受高(例如,100×)放大,取决于材料微粒的细度。在此之后,应当获取要测量的视场的图像。在一种形式中,线性拦截方法可以用于测量DAS,其中,选择三个或更多枝晶体,每个视场可见枝晶躯干带有至少三个枝晶臂。由此,从第一枝晶臂的外边缘到最后枝晶臂的内边缘画一条线;该示例在图6中示出。可以记录每个枝晶体的距离d,同时还可以记录每个测量值计数的枝晶臂的编号n1、n2、n3等。这些动作对每个视场重复。当前,在图像分析器中可以自动地确定共晶体的体积百分比和DCS。局部冷却速率不仅影响微结构细度,而且影响孔隙形成。因而,DAS往往更经常用来量化微结构细度。DAS测量的问题在于其必须通过在图像分析器中识别限定好的枝晶臂而手动测量。不幸的是,这是非常耗时的且很大程度上取决于进行测量的用户或个人的技能。
技术实现要素:不能自动地考虑铸造部件的DAS和相关材料属性变化通过本文公开的本发明各个方面解决,其中,金属铸件的枝晶微结构中DAS的稳固、准确和自动测量可以用于产品质量控制以及用于产品性能和耐用性分析。根据一个实施例,公开了一种自动地预测铸造部件内的DAS和相关材料属性的分布的方法。所述方法包括获取感兴趣铸件位置的微量样品。在该上下文中,微量样品是在微结构分析的标准过程中制备的金相样品。一种这样的标准过程包括上述ASTME3。样品然后被自动分析。在一种形式中,可以使用使用DCS线性拦截(DCSli)方法或平均面积等效圆直径方法(DCSed)的DCS图像分析器。由此,测量DCS值根据两种方法中的一种转换为DAS。与DCS值相对应的量化DAS值优选去核(pit)为用户便利格式,例如适合于人读取的打印输出或者可以随后由计算机输出装置、计算机可读算法或其它合适手段操作的计算机可读格式。如当前配置的,自动化可以通过可以在数字计算机上执行、运行或以其他方式进行的程序或相关算法进行,以便产生DAS的得到数据表示。在优选形式中,数字计算机优选包括输入、输出、处理单元(通常称为中央处理单元(CPU))和存储器中的一个或多个,存储器可以在计算机存储器中临时或者永久性存储这种代码、程序或算法从而代码中包含的指令可以由处理单元基于输入数据操作,使得由代码和处理单元产生的输出数据可以经由输出提供给另一个程序或用户。在一种形式中,存储器的数据容纳部分(也称为工作存储器)称为随机存取存储器(RAM),而存储器的指令容纳部分(也称为永久存储器)称为只读存储器(ROM)。数据总线或相关线路组和有关电路形成可以将输入、输出、CPU和存储器以及任何外围设备互连的合适数据通信路径,从而允许系统操作为集成整体。这种计算机系统称为具有vonNeumann架构(也称为通用或存储程序计算机)。类似地,采用vonNeumann架构的显著特征以便执行数据获取、操控或相关计算功能中的至少一些的特定调节计算机或计算机相关数据处理装置被认为在本发明的范围内。根据另一个实施例,公开了一种自动地预测铸造部件内的DAS和相关材料属性的分布的方法。所述方法包括:选择要分析的铸造材料;使用图像分析器来自动地确定与所选择材料相对应的DCS信息;以及然后通过以下中的至少一种将DCS信息转换为DAS信息:(a)经验关系和(b)DCS和DAS信息之间的理论关系。根据本发明的另一方面,公开一种制造物品。所述物品包括实施有计算机可读程序代码的计算机可使用介质,用于量化铸造材料的DAS属性,使得其可以用于上述通用计算机或特定调节计算机。具体地,这种计算机可读程序代码包括:用于使得计算机接收或读取与铸造材料样品获取的数字信息相对应的数据的一部分,以及用于使得计算机处理信息为DCS信息的一部分,除了基于这两种形式信息之间的理论关系或经验关系将DCS转换为DAS的一部分之外。此外,实施在计算机可使用介质上的程序包括用于输出DAS信息的一部分。这种输出可以是机器可读或人可读形式。由此,计算机可使用介质上的DAS的确定以自动方式进行,从而不需要如上所述手动地获取这种信息。在更具体形式中,使用图像分析器(或相关设备)来自动地确定与所选择铸造材料相对应的枝晶单元大小信息可以通过使用上述DCSli或DCSed来进行。另外,分析位置可以使用标准金相技术(例如,与上述ASTME3相对应)来确定。在具体形式中,被读取或以其他方式接收的数字信息是数字图像的形式,例如可通过图像分析器、与图像分析器协作的设备或本领域技术人员已知的其它方法扫描的图像。在另一个具体形式中,铸造材料总体上可以是铝合金,具体地是亚共晶铝合金。方案1.一种自动地量化铸造材料的枝晶微结构中的枝晶臂间距的方法,所述方法包括:从所述铸造材料选择感兴趣位置;自动地分析所述感兴趣位置以量化其中的枝晶单元大小;以及通过所述枝晶单元大小和所述枝晶臂间距之间的经验关系和理论关系中的至少一个将所述量化枝晶单元大小转换为量化枝晶臂间距。方案2.根据方案1所述的方法,其中,所述枝晶单元大小和所述枝晶臂间距之间的所述经验关系表示如下:DAS=a*DCS+b其中,a和b是所述铸造材料特定的材料常数。方案3.根据方案1所述的方法,其中,所述枝晶单元大小和所述枝晶臂间距之间的所述理论关系表示如下:DAS=(1-Veu)*DCS其中,Veu限定所述感兴趣位置特定的微结构中的共晶相的实际体积比例。方案4.根据方案1所述的方法,其中,所述感兴趣位置使用标准金相技术确定。方案5.根据方案4所述的方法,其中,所述标准金相技术根据用于金相样品制备的美国测试协会和材料标准指导执行。方案6.根据方案1所述的方法,其中,所述量化枝晶单元大小使用枝晶单元大小线性拦截方法确定。方案7.根据方案1所述的方法,其中,所述量化枝晶单元大小使用平均面积等效圆直径方法确定。方案8.根据方案1所述的方法,其中,所述自动地分析所述感兴趣位置使用图像分析器执行。方案9.根据方案1所述的方法,其中,所述铸造材料包括亚共晶铝合金。方案10.根据方案1所述的方法,还包括:以用户便利格式输出所述量化枝晶臂间距。方案11.一种自动地量化枝晶微结构中的枝晶臂间距的方法,所述方法包括:选择要分析的铸造材料;使用图像分析器来自动地确定与所述选择材料相对应的枝晶单元大小信息;以及通过所述枝晶单元大小信息和枝晶臂间距信息之间的经验关系和所述枝晶单元大小信息和所述枝晶臂间距信息之间的理论关系中的至少一个将所述枝晶单元大小信息转换为所述枝晶臂间距信息。方案12.根据方案11所述的方法,其中,所述铸造材料包括亚共晶铝合金。方案13.根据方案12所述的方法,其中,所述铝合金选自包括319和A356的组。方案14.根据方案11所述的方法,其中,所述枝晶单元大小信息的所述自动确定使用枝晶单元大小线性拦截方法和平均面积等效圆直径方法中的至少一种进行。方案15.根据方案14所述的方法,其中,所述枝晶单元大小信息和所述枝晶臂间距信息之间的所述经验关系表示如下:DAS=a*DCS+b其中,a和b是所述铸造材料特定的材料常数。方案16.根据方案14所述的方法,其中,所述枝晶单元大小信息和所述枝晶臂间距信息之间的所述理论关系表示如下:DAS=(1-Veu)*DCS其中,Veu限定所述感兴趣位置特定的微结构中的共晶相的实际体积比例。方案17.根据方案11所述的方法,其中,所述转换使用基于计算机的数据处理装置执行。方案18.一种制造物品,包括实施有计算机可读程序代码的计算机可使用介质,用于自动地量化铸造材料的枝晶臂间距,所述制造物品中的所述计算机可读程序代码包括:用于使得所述计算机接收与铸造材料样品内的感兴趣位置的数字信息有关的数据的计算机可读程序代码部分;用于使得所述计算机处理所述数字信息为枝晶单元大小信息的计算机可读程序代码部分;用于使得所述计算机基于经验关系和理论关系中的至少一个通过算法将所述枝晶单元大小信息转换为对应枝晶臂间距的计算机可读程序代码部分;以及用于使得所述计算机产生与所述枝晶臂间距相对应的输出的计算机可读程序代码部分。方案19.根据方案18所述的制造物品,其中,用于使得所述计算机处理所述数字信息为枝晶单元大小信息的所述计算机可读程序代码部分包括使用枝晶单元大小线性拦截方法和平均面积等效圆直径方法中的一种。方案20.根据方案19所述的制造物品,其中,所述铸造材料样品包括亚共晶铝合金。方案21.根据方案20所述的制造物品,其中,所述枝晶单元大小信息和所述枝晶臂间距信息之间的所述经验关系表示如下:DAS=a*DCS+b其中,a和b是所述亚共晶铝合金特定的材料常数。方案22.根据方案20所述的制造物品,其中,所述枝晶单元大小信息和所述枝晶臂间距信息之间的所述理论关系表示如下:DAS=(1-Veu)*DCS其中,Veu限定所述感兴趣位置特定的微结构中的共晶相的实际体积比例。附图说明具体实施例的以下详细描述在与所附附图结合地阅读时可以被最好地理解,其中相同的结构用相同的附图标记指代,并且其中:图1是示出了两种不同铸造铝合金319和A356经验和理论的公开DAS和DCS关系(局部微结构中的共晶相体积比例的变化百分比)连同DAS和DCS测量值的曲线图;图2A至2D示出了可以如何建立DCS和DAS之间的经验和理论关系;图3A示出了根据现有技术的借助于用于测量枝晶结构的大小(例如DCSli)和DAS的线性拦截方法的铸造铝合金的显微照片;图3B示出了图3A的显微照片的表示,具体单元结构的更多细节使用已知半自动技术表示,其中,长度除以枝晶体数量;图4使用基于经验的关系示出了铝合金A356和319的DAS和DCS之间的关系;图5示出了根据本发明的图示各个步骤的流程图;图6A和6B示出了实现DAS测量的示例性方法;和图7示出了根据本发明的方面的可以用于自动地量化枝晶臂间距的图像分析器。附图所述的实施例本质上是说明性的,且不旨在限制由权利要求限定的实施例。此外,附图和实施例的各个方面将鉴于以下详细说明更完全清楚和理解。具体实施方式首先参考图1和7,如上所述,两种方法中的一种用于将测量或取样DCS值转换为DAS。如上所述,预测铸造部件内的DAS分布的自动方法可以包括获取感兴趣铸件位置的微量样品且通过基于计算机的图像分析器进行分析。具体地参考图7,图像分析器系统(本文也称为图像分析系统、图像分析器等)300包括计算机310或相关数据处理设备,包括处理单元310A(可以是一个或多个微处理器的形式)、一个或多个信息输入机构310B(包括键盘、鼠标或其它装置,例如语音识别接收器(未示出))以及一个或多个装载机310C(可以是磁性或光学存储器或相关存储装置(CD、DVD、USB端口等形式)的形式)、一个或多个显示屏或相关信息输出310D、存储器310E和计算机可读程序代码装置(未示出),以处理与铝合金有关的接收信息的至少一部分。本领域技术人员将理解,存储器310E可以是随机存取存储器(RAM,也称为大容量存储器,可以用于数据的临时存储)的形式和只读存储器(ROM)形式的指令存储存储器。除了未示出的其它形式的输入(例如,通过互联网或外部数据源的相关连接)之外,装载机310C可以工作从而将数据或程序指令从一个计算机可使用介质(例如,闪存或前述CD、DVD或相关介质)装载到另一个(例如,存储器310E)。本领域技术人员将理解,计算机300可以作为自主(即,独立)单元存在,或者可以是更大网络(例如,在云计算中遇到的,其中,各种计算、软件、数据访问和存储服务可以位于全异物理位置)的一部分。计算资源的这种分离并不影响这种系统分类为计算机。在具体形式中,计算机可读程序代码可以装载到作为存储器310E的一部分的ROM。这种计算机可读程序代码也可以形成为制造物品的一部分,从而容纳在代码中的指令位于可磁性读取或者光学读取盘或其它相关非临时机器可读介质上,例如闪存装置、CD、DVD、EEPROM、软盘或能够存储机器可执行指令和数据结构的其它这种介质。这种介质能够由具有处理单元310A的计算机310或其它电子装置访问,处理单元310A用于编译来自于计算机可读程序代码的指令。计算机领域技术人员将理解,形成图像分析系统300的一部分的计算机310还可以包括附加芯片组以及用于在处理单元310A和其它装置(例如,前述输入、输出和存储器装置)之间传送数据和相关信息的总线和相关布线。在程序代码装置装载到ROM中后,系统300的计算机310变为配置成以本文所述的方式确定最佳铸造部件的特定目的机器。在另一方面,系统300可以仅仅是指令代码(包括各个程序模块(未示出)),而在又一方面,系统300可包括指令代码和上述计算机可读介质两者。本领域技术人员将理解,除了输入310B(尤其是在输入大量数据的情况下)所示的手动输入方法之外,存在接收数据和相关信息的其它方法,且提供这种数据以便允许处理单元310A操作的任何常规装置在本发明的范围内。因而,输入310B还可以是高吞吐量数据线路(包括上述互联网连接)的形式,以便接收大量的代码、输入数据或其它信息到存储器310E中。信息输出310D配置成将与期望铸造方法有关的信息提供给用户(例如,在信息输出310D是所示的屏幕的形式时)或者另一程序或模型。类似地,本领域技术人员将理解,与输入310B和输出310D有关的特征可以组合成单个功能单元,例如图形用户接口(GPI)。图像分析系统300用于从图像322提取信息,具体地使用金相技术以将结构与感兴趣材料物理属性相关联。这些属性包括(但不限于)拉伸强度、屈服强度、伸长率和硬度。以制备金相样品开始,转换显微镜320用于产生图像322,图像322由照相机330捕获。通常,许多图像322通过使用机动载物台340和载物台图案350获取。灰度阈值然后在构成图像分析软件的基于计算机的例程或算法360中在这些数字图像322上进行,其可以存储在存储器310E或其它合适计算机可读介质中。例程360然后测量图像322的阈值像素。该数据然后被分析以产生最终结果。载物台控制器370(采用类似操纵杆的控制器)用于将微量样品从一个区域移动到显微镜320中的另一个区域,其中,三维(笛卡尔)x、y和z(焦点)载物台移动由载物台控制器370控制。这允许移动经过载物台图案以允许分析样品上的多个视场。该自动载物台图案(包括自动聚焦特征)允许在短时间段内捕获大量的数据。载物台控制器370的操纵杆允许载物台移动,同时通过显微镜320的目镜观察样品,以利于选择进行分析的具体区域。具体地参考图1,在第一方法中,使用从不同材料的测试数据产生的经验公式:DAS=a*DCS+b(1)其中,a和b是材料常数,而在第二方法中,使用基于物理(即,理论)的方程:DAS=(1-Veu)*DCS(2)其中,Veu是局部微结构中的共晶相的实际体积比例。该第二方法提供金属铸件的枝晶微结构中DAS的稳固和自动测量,不仅用于产品质量控制,而且用于产品性能和耐用性分析。在上文方程(1)和(2)的经验或基于物理(即,理论)的方法中,铸造铝合金(例如,A356和319)的枝晶结构中的DAS可以从DCS和共晶体积比例Veu中的一个或两者的测量来自动确定。类似地,在方程(2)中,Veu=k*feu,,其中,feu是合金(在均衡条件中)的共晶相的理论体积比例,k(>1)是在增加固化(冷却)速率(即,具有减少DAS)的情况下适应共晶相体积比例增加的系数。本文公开的发明特别好地适合于亚共晶金属(即,具有枝晶结构)。显著地,本发明有助于消除DAS的冗长耗时手动测量以及减少依赖于操作者的误差,其中,否则可能存在相对大的标准偏差(通常在±20%的量级)。这继而提供更准确和可靠的DAS数据,以及节省实验室工程师时间和成本。在一个具体形式中,获取微量样品,其然后使用DCSli或DCSed在图像分析器300中自动分析DCS。测量DCS值然后根据上述经验或基于物理(即,理论)的方法转换为DAS。显著地,本发明的方法将提供金属铸件的枝晶微结构中的DAS的稳固和自动测量,其可以不仅用于产品质量控制,而且用于产品性能和耐用性分析。首先参考图2A至2D连同图5一起,示出了与使用DCSli自动地确定DAS有关的步骤。首先参考图2A,示出了照相微结构10的图像,显示了要分析区域。微结构10由一次铝枝晶体20(白色)和共晶体Si和Fe富含颗粒30(黑色)和共晶体铝40(不是枝晶体,而是占据紧挨共晶体颗粒30的位置)构成。接下来参考图2B,具有已知长度(在示例性形式中显示为500微米)的五个同心圆50用作图像分析器系统300(如图7所示)中的网格,以估计图2A所示的枝晶微结构10的DCS。DCS值使用如下估计:(3)其中,L是五个圆的总长度(周长),n是在单元边界拦截的五个圆形线的拦截的总数量。接下来参考图2C,图2A的微结构10叠置在图2B的同心圆50上,同时图像分析器300测量共晶区域30和40的DCS和体积百分比。图2C还示出了图像分析器300中的DCS的自动测量过程,其中,处理微结构10的叠置五个圆图像在图像分析器300中放大和然后侵蚀一次或更多次,以使得共晶区域30和40完全填充,以确定部段(拦截)数量。因而,微结构10的处理图像然后在图像分析器300中与来自于同心圆50的图像组合,以允许其确定同心圆50的多少部段由共晶区域30和40断开或拦截。同心圆50中的部段总数量是上述方程(3)中的值n。可以看出,图2C的暗区域与共晶颗粒30和共晶铝40的合并相对应。接下来参考图2D,示出了使用方程(2)所述的理论关系自动计算的DAS的曲线图相对于感测或手动测量的DAS进行比较。图2D中的每个数据点表示来自于水平轴的手动测量DAS值和来自于竖直轴的计算DAS值两者。实线表示计算DAS值与手动测量DAS精确相同。两条虚线是手动测量DAS值的一个标准偏差内的平均手动测量DAS,所有这种数据点都在该极限内。接下来参考图4,示出了DAS和DCS之间的关系,其中,实验数据之间的良好线性相关性明显。而图1示出了DCS和DAS之间的理论关系,对于不同体积的共晶体(注意到例如0,0起点),图4(形成图1的子组,因为图1中的虚线与图4中的线相同)示出了直线方程。在DCS自动确定(如上所述)之后,DAS然后可以使用方程(1)经验地估计。对于被分析的测试数据,从DCS值估计DAS的总体误差在5%内,在统计学上是显著的。对于A356和319(均包含6至7%Si),经验方程为:DAS=0.6334xDCS-8.4459(DCS>15μm)(4)其中,R2是线性回归的拟合良好性测量;在图1和4所示的型式中,R2(0.0和1.0之间的无单位分数)为0.9516。通过参考,0.0的R2值表示已知沿横坐标(即,x轴)的值并不能帮助预测对应纵坐标(即,y轴)值。在这种情况下,在X和Y值之间没有线性关系,最佳拟合线是穿过所有Y值的平均值的水平线。相比而言,当R2等于1.0时,所有点准确地位于直线上,没有分散,从而知道X值导致Y值的准确预测。DAS和DCS之间的差与共晶相的体积比例Veu有关。线性拦截方法通过将测量数据与最佳拟合直线方程相关而产生。在上述线性拦截方法(DCSli)中,DCS等于线的总长度值(例如,同心圆50的五个圆的周长)除以单元边界处拦截的总数量。因而,线性拦截方法用于获得DCS值,继而用于基于上述方程(1)或(2)转换为DAS值。因而,线性拦截方法自动地获取DAS,而与采用基于经验方法还是基于物理的方法无关。可以看出,方程(3)中使用的DCS值并不考虑与共晶相或区域30、40的体积比例Veu有关的单元边界的宽度。换句话说,DCS方法通过将共晶相30、40的体积比例Veu简单地作为枝晶体20的一部分处理而过高估计枝晶单元大小。与区域30、40相对应的共晶相的体积比例Veu可能是显著的,取决于合金成分。在铝合金A356(7%Si)和319(6%Si,3.5%Cu)中,共晶相的体积比例Veu是大约50%。将理解的是,在附图中识别的相或区域30和40的黑色和白色表示使之难以识别和区分它们,因为它们看起来合并在一起(由于两者均表示为黑色);然而,本领域技术人员将理解,其它表示(例如,彩色)将更清楚地显示分界位置。如上所述,DAS还可以使用上文的基于物理的方程(2)确定。对于铸造铝合金,共晶相的理论体积比例feu可以从本领域技术人员已知的现有相图或计算热力软件确定。例如,共晶相的理论体积比例feu对于A356(7%Si,0.4%Mg)和319(6%Si,1%Fe,0.5%Mn,3.5%Cu)分别是大约49%和43%。实际上,铝铸件的固化从未处于均衡条件。由于固化铝枝晶体的受限溶质扩散(固化速率增加),共晶相的实际体积比例Veu通常大于理论值feu。对于具有高扩散性元素(如,Si)的合金,系数k从1至1.1,而在具有低扩散性元件(如,Cu)的合金中,系数k从1至1.2。这与实验数据很好地相符,如图1和4所示。接下来参考图3A和3B,示出了典型合金微结构110的示例以图示如何使用线性拦截方法来测量枝晶结构的大小(如DCSli),示出了根据现有技术的DAS,而图3B示出了在具有图像分析软件的图像分析器300中由已知半自动技术确定的图3A的图像的单元结构。如上所述,图像分析器可以是进行先进图像编辑、增强和分析的机器(和/或软件)。在该方法中,L2的长度除以枝晶体数量(在该情况下,5),以得到DAS。在一种形式中,DCSed参数定义为平均面积等效直径,而在上表1中讨论的题为枝晶单元大小的Cáceres等文献使用另一参数,枝晶单元的平均面积等效圆直径DCSed,由半自动技术测量,以限定枝晶体120。在该上下文中,半自动方法是这样的方法:分析的一部分涉及使用手动步骤(例如,在一个或多个中间步骤中)。这粗略地等同于也在表1中阐述的Jaquet和Hotz的枝晶单元大小的测量方法。常见的是使用图3A所示的方法手动测量DAS和DCS。具体地参考图3B,在图2A和2C的所有共晶区域30、40缩减为线表示之后,示出了分析结果。因而,所有区域(由区域A表示)都认为是一次枝晶单元。圆C具有与代表性区域A相同的面积。接下来参考图5,根据本发明的方面的流程图图示了自动地量化所研究材料的微量样品的DAS的各个步骤200。如上所述,步骤200中的许多(或全部)可以自动化(例如,通过配置成由计算机或相关处理器驱动装置操作的合适算法)。最初,制备所研究材料的微量样品(未示出,但是总体上与图2A所示类似)(210)。在一种形式中,微量样品首先从感兴趣铸件的一部分切割。分割样品然后用树脂热安装,以形成短圆柱体,在圆柱体的一端上具有分割样品的感兴趣表面。在安装之后,样品被湿磨(例如,用砂纸等)以暴露金属表面。样品用越来越细的研磨介质连续研磨。一旦获取与微量样品有关的信息(例如,数字图像)(220),该信息可以被处理(230)。例如,在信息是扫描数字图像的情况下,其于是可以以与上述图2C类似的方式处理。线性拦截方法(如上所述)(240)可以用于分析图像以产生DCS信息(250)。由此,DCS信息基于面积或体积百分比经受图像分析(260)。之后,DAS可以通过上述基于经验或基于理论的方法中的一个或另一个计算(270)。这种信息可以输出给用户或附加量化后程序、例程算法以及打印输出或存储器装置,以便随后使用。要注意的是,以特定方式“配置”或者体现特定属性或者以特定方式工作的实施例的部件的本文叙述是与预期使用叙述不同的结构叙述。更具体地,本文参考部件“配置”的方式表示部件的现有物理状况,因而用作部件的结构因素的确定叙述。类似地,为了描述和限定本文实施例的目的,注意本文中使用术语“基本上”、“显著地”和“大约”表示可能归因于任何定量比较、数值、测量值或其他表示的固有不确定性程度,因而可表示定量表示可以偏离所述参考值而不会导致所述主题的基本功能发生改变的程度。参考其特别实施例详细描述了本发明的实施例,将清楚的是,在不脱离所附权利要求限定的实施例的范围的情况下可以进行修改和变化。更特别地,尽管本发明实施例的一些方面在本文中认定为优选的或特别有利的,但认为本发明的实施例并不必限制于这些优选方面。