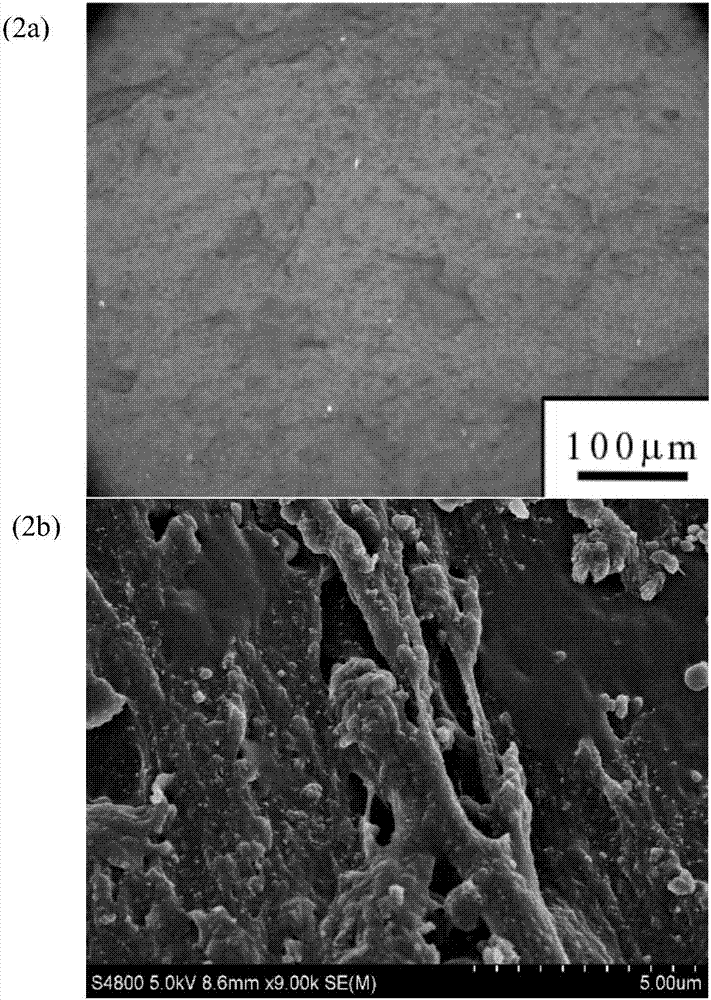
本发明涉及橡塑材料性能评价
技术领域:
,特别涉及一种橡塑材料在强腐蚀环境中的摩擦系数的测试方法。
背景技术:
:橡塑材料是橡胶材料和塑料材料的统称,在石油钻井、化工以及航空航天等领域有广泛的应用。某些橡塑材料的使用环境为强腐蚀环境。例如氢化丁腈橡胶(hnbr)用于油井井筒密封时,由于油井的注入水和采出水中腐蚀性离子的含量较高,因此氢化丁腈橡胶处于强腐蚀环境中。为了保证橡塑材料的正常使用,需要对橡塑材料在强腐蚀环境中的力学性能进行研究,以掌握橡塑材料在强腐蚀环境中的力学性能变化规律。橡塑材料在强腐蚀环境中的摩擦系数是力学性能研究中比较的重要参数。目前,在对橡塑材料在强腐蚀环境中的力学性能进行研究时,通常以橡塑材料在普通环境中的摩擦系数代替其在强腐蚀环境中的摩擦系数。在实现本发明的过程中,本发明人发现现有技术中至少存在以下问题:以普通环境中的摩擦系数代替强腐蚀环境中的摩擦系数不能准确地对橡塑材料在强腐蚀环境中的力学性能进行研究。技术实现要素:为了解决上述的技术问题,本发明实施例提供一种橡塑材料在强腐蚀环境中的摩擦系数的测试方法。具体而言,包括以下的技术方案:一方面,本发明实施例提供一种橡塑材料摩擦系数的测试方法,所述测试方法包括:步骤a,将经过预处理的橡塑材料试样浸泡在浸渍溶液中,在预设温度下老化预设时间;所述浸渍溶液为含有cl-、hco3-、so42-、na+、ca2+的水溶液,其 中,cl-的浓度为12000mg/l~18000mg/l,hco3-的浓度为1000mg/l~1400mg/l,so42-的浓度为150mg/l~250mg/l,na+的浓度为8000mg/l~12000mg/l,ca2+的浓度为250mg/l~350mg/l;步骤b,将老化后的橡塑材料试样固定在滑块的下表面上,将所述滑块和所述老化后的橡塑材料试样置于所述浸渍溶液中,拉动所述滑块使所述老化后的橡塑材料试样和所述滑块一起运动,记录作用在所述滑块上的拉力值和所述老化后的橡塑材料试样受到的正压力值,所述拉力值和所述正压力值的比值即为所述橡塑材料的摩擦系数。进一步地,作为优选,所述浸渍溶液中,cl-的浓度为15000mg/l,hco3-的浓度为12mg/l,so42-的浓度为200mg/l,na+的浓度为10000mg/l,ca2+的浓度为300mg/l。进一步地,步骤a中,所述预设时间为6~10天。进一步地,步骤a中,所述预设温度为20℃~80℃。进一步地,步骤a中,所述橡塑材料试样为长方体,所述橡塑材料试样的长为115mm~120mm、宽为85mm~95mm、厚为1mm~3mm。进一步地,步骤b之后包括:对经历了摩擦系数测试的橡塑材料试样的表面进行清洁处理,然后对所述经历了摩擦系数测试的橡塑材料试样的表面形貌进行观察。进一步地,所述清洁处理具体包括:对所述老化后的橡塑材料试样进行超声清洗,所述超声清洗的时间为0.5~1小时,然后依次用丙酮、乙醇进行清洗。进一步地,所述橡塑材料包括:氢化丁腈橡胶、丁腈橡胶、乙丙橡胶、氯丁橡胶、聚乙烯、聚丙烯、丙烯腈-丁二烯-苯乙烯共聚物、聚四氟乙烯。另一方面,本发明实施例提供一种利用上述的测试方法得到的摩擦系数在油井井筒力学分析中的应用。本发明实施例提供的技术方案的有益效果是:本发明实施例提供的橡塑材料摩擦系数的测试方法中,将橡塑材料置于强腐蚀性的浸渍溶液中进行老化,并在强腐蚀性的浸渍溶液中测试作用在老化后的橡塑材料上的拉力值和橡塑材料受到的正压力值,通过计算拉力值和正压力值的比值来得到橡塑材料在强腐蚀环境中的摩擦系数。采用该方法可以对各种 橡胶材料以及塑料材料在强腐蚀环境下的摩擦系数进行测试,并对其老化后的摩擦性能进行快速评价,通过本发明实施例的测试方法得到的摩擦系数与橡塑材料在实际强腐蚀环境中的摩擦系数相吻合,所得结果能够用于橡塑材料在强腐蚀环境中的力学性能分析,有利于提高橡塑材料在强腐蚀环境中的力学性能分析的准确性。附图说明为了更清楚地说明本发明实施例中的技术方案,下面将对实施例描述中所需要使用的附图作简单地介绍,显而易见地,下面描述中的附图仅仅是本发明的一些实施例,对于本领域普通技术人员来讲,在不付出创造性劳动的前提下,还可以根据这些附图获得其他的附图。图1为实施例1、2、3以及4中测试得到的氢化丁腈橡胶试样的摩擦系数;图2为实施例1中氢化丁腈橡胶试样在20℃下在浸渍溶液中老化后的形貌图,其中图2a为光学显微镜观察结果,图2b为扫描电子显微镜观察结果。图3为实施例2中氢化丁腈橡胶试样在40℃下在浸渍溶液中老化后的形貌图,其中图3a为光学显微镜观察结果,图3b为扫描电子显微镜观察结果。图4为实施例3中氢化丁腈橡胶试样在60℃下在浸渍溶液中老化后的形貌图,其中图4a为光学显微镜观察结果,图4b为扫描电子显微镜观察结果。图5为实施例4中氢化丁腈橡胶试样在80℃下在浸渍溶液中老化后的形貌图,其中图5a为光学显微镜观察结果,图5b为扫描电子显微镜观察结果。图6为光学显微镜观察得到的氢化丁腈橡胶在实际强腐蚀环境中的形貌图。具体实施方式为使本发明的技术方案和优点更加清楚,下面将结合附图对本发明实施方式作进一步地详细描述。除非另有定义,本发明实施例所用的所有技术术语均具有与本领域技术人员通常理解的相同的含义。本发明实施例提供一种橡塑材料在强腐蚀环境中的摩擦系数的测试方法,该测试方法包括:步骤a,将经过预处理的橡塑材料试样浸泡在浸渍溶液中,在预设温度下老化预设时间;所述浸渍溶液为含有cl-、hco3-、so42-、na+、ca2+的水溶液,其 中,cl-的浓度为12000mg/l~18000mg/l,hco3-的浓度为1000mg/l~1400mg/l,so42-的浓度为150mg/l~250mg/l,na+的浓度为8000mg/l~12000mg/l,ca2+的浓度为250mg/l~350mg/l;步骤b,将老化后的橡塑材料试样固定在滑块的下表面上,将所述滑块和所述老化后的橡塑材料试样置于所述浸渍溶液中,拉动所述滑块使所述老化后的橡塑材料试样和所述滑块一起运动,记录作用在所述滑块上的拉力值和所述老化后的橡塑材料试样受到的正压力值,所述拉力值和所述正压力值的比值即为所述橡塑材料的摩擦系数。本发明实施例提供的橡塑材料摩擦系数的测试方法中,将橡塑材料置于强腐蚀性的浸渍溶液中进行老化,并在强腐蚀性的浸渍溶液中测试作用在老化后的橡塑材料上的拉力值和橡塑材料受到的正压力值,通过计算拉力值和正压力值的比值来得到橡塑材料在强腐蚀环境中的摩擦系数。通过本发明实施例的测试方法得到的摩擦系数与橡塑材料在实际强腐蚀环境中的摩擦系数相吻合,所得结果能够用于橡塑材料在强腐蚀环境中的力学性能分析,有利于提高橡塑材料在强腐蚀环境中的力学性能分析的准确性。同时本发明实施例提供的测试方法操作简单、容易实现、重复性以及再现性良好。进一步地,在上述的测试方法中,cl-、hco3-、so42-、na+以及ca2+的浓度可以在限定的范围内任意取值,例如cl-的浓度可以为13000mg/l、14000mg/l、15000mg/l、16000mg/l、17000mg/l等;hco3-的浓度可以为1100mg/l、1200mg/l、1300mg/l等;so42-的浓度可以为160mg/l、180mg/l、200mg/l、220mg/l、240mg/l等、na+的浓度可以为9000mg/l、10000mg/l、12000mg/l等;ca2+的浓度可以为260mg/l、280mg/l、300mg/l、320mg/l、340mg/l等。其中,本发明实施例中,浸渍溶液的组成优选:cl-的浓度为15000mg/l,hco3-的浓度为12mg/l,so42-的浓度为200mg/l,na+的浓度为10000mg/l,ca2+的浓度为300mg/l。采用该组成的浸渍溶液能够使最终得到的摩擦系数更符合实际情况。可以利用nahco3、cacl2、nacl以及na2so4来配制上述强腐蚀性的浸渍溶液。进一步地,在上述的测试方法中,步骤a中,在浸渍溶液中老化的预设时间为6~10天,例如可以为7天、8天、9天等,优选8天。进一步地,在上述的测试方法中,步骤a中,在浸渍溶液中老化的预设温 度为20℃~80℃,例如可以为30℃、40℃、50℃、60℃、70℃等进一步地,在上述的测试方法中,步骤a中,橡塑材料试样的形状优选为长方体,其中,长方体的长可以为115mm~120mm,例如116mm、117mm、118mm、119mm等;长方体的宽可以为85mm~95mm,例如86mm、88mm、90mm、92mm、94mm等;长方体的厚可以为1mm~3mm,例如1.5mm、2mm、2.5mm等。其中,本发明实施例中,橡塑材料试样的尺寸优选为长117mm、宽90mm、厚2mm。进一步地,本发明实施例的测试方法中,步骤b之后还包括:对经历了摩擦系数测试的橡塑材料试样的表面进行清洁处理,然后对上述经历了摩擦系数测试的橡塑材料试样的表面形貌进行观察。其中,清洁处理具体包括:对老化后的橡塑材料试样进行超声清洗,超声清洗的时间为0.5~1小时,然后依次用丙酮、乙醇进行清洗。本领域技术人员可以理解的是,可以通过光学显微镜和扫描电子显微镜(sem)对橡塑材料试样的表面形貌进行观察。通过对橡塑材料试样的表面形貌进行观察,来对橡塑材料的摩擦性能作更深入的研究。进一步地,本领域技术人员可以理解的是,本发明实施例的测试方法中所用仪器应至少包括:浸没在本发明实施例提供的浸渍溶液中的实验台;用于牵引滑块的牵引部件;用于检测拉力值和正压力值的力传感器;用于检测橡塑材料试样和滑块在实验台上滑动速度的速度传感器,当速度传感器检测到的滑块和橡塑材料试样的滑动速度在一定范围内保持稳定时力传感器检测到的拉力值和正压力值即为计算摩擦系数所需的拉力值和正压力值。所用的仪器还可以包括控制单元,力传感器可以与控制单元电连接,控制单元对力传感器检测到的拉力值和正压力值进行分析计算从而得出橡塑材料在强腐蚀环境中的摩擦系数。本发明实施例提供的测试方法适用于对各种橡胶材料以及塑料材料在强腐蚀环境中的摩擦系数进行测试,并对其老化后的摩擦性能进行快速评价。举例来说,橡胶材料包括但不限于氢化丁腈橡胶、丁腈橡胶、乙丙橡胶以及氯丁橡胶等;塑料材料包括但不限于聚乙烯、聚丙烯、丙烯腈-丁二烯-苯乙烯共聚物以及聚四氟乙烯等。下面以氢化丁腈橡胶为例,对本发明实施例提供的测试方法作进一步地详细描述。氢化丁腈橡胶(hnbr)是由丁腈橡胶通过对丁二烯链段中双键进行选择加氢后所得到的一种新型特种橡胶。由于其丁二烯链段中双键被氢化后达到饱和状态,因此氢化丁腈橡胶不仅具有良好的耐油性能、物理机械性能和加工使用性能,同时还具有较高的耐热、耐高压、耐氧化性能以及耐酸性汽油环境的能力,在化工、石油钻井、航天航空等诸多领域广泛应用。氢化丁腈橡胶在石油钻井行业主要用于制成胶筒进行井筒密封,在油田开发生产过程中,胶筒会和油井套管发生摩擦,因此,在对井筒进行力学分析时,氢化丁腈橡胶的摩擦系数是较为重要的参数。而由于油井的注入水和采出水中腐蚀性离子的含量较高,氢化丁腈橡胶处于强腐蚀的环境中,因此为了保证井筒力学分析的准确性,需要对氢化丁腈橡胶在强腐蚀环境中的摩擦系数进行测试。实施例1本实施例提供一种氢化丁腈橡胶在强腐蚀环境中的摩擦系数的测试方法,所用强腐蚀性的浸渍溶液的化学组成如表1所示。表1强腐蚀性浸渍溶液的化学组成离子种类cl-hco3-so42-na+ca2+含量(mg/l)15000120020010000300本实施例的测试方法的步骤如下:步骤1,将氢化丁腈橡胶切割加工为117mm×90mm×2mm的长方体试样,并对氢化丁腈橡胶试样进行预处理,清除其表面的杂质和油污。步骤2,向1l水中加入1650mg的nahco3、830mg的cacl2、23850mg的nacl以及300mg的na2so4配制上述强腐蚀性浸渍溶液。步骤3,将步骤1所得预处理后的氢化丁腈橡胶试样浸泡于步骤2所得强腐蚀性浸渍溶液进行老化,浸泡温度为20℃,浸泡时间为8天。步骤4,将老化后的氢化丁腈橡胶试样固定在滑块的下表面上,将滑块和老化后的氢化丁腈橡胶试样置于上述强腐蚀性浸渍溶液中,拉动滑块使老化后的氢化丁腈橡胶试样和滑块一起运动,记录作用在滑块上的拉力值和老化后的橡塑材料受到的正压力值,按照以下公式计算氢化丁腈橡胶在强腐蚀性环境中的 摩擦系数:μ=f/fn,其中,μ代表氢化丁腈橡胶在强腐蚀环境中的摩擦系数;f代表拉力值,单位为n;fn代表正压力值,单位为n。摩擦系数如图1所示。步骤5,对经历了步骤4中摩擦系数测试的氢化丁腈橡胶试样进行超声清洗,超声清洗的时间为1小时,超声清洗后再依次用丙酮、乙醇进行清洗。利用光学显微镜和扫描电镜对上述清洗后的氢化丁腈橡胶试样的表面形貌进行观察,结果分别如图2a和图2b所示。从图2a可以看出,在20℃下老化后的氢化丁腈橡胶表面摩擦痕迹较轻,有小部分橡胶开始剥落,有坑洞开始产生。从图2b可以看出,此时橡胶内部的填料颗粒和橡胶基体没有明显的变化,填料颗粒可以和橡胶基体稳定熔融结合。实施例2本实施例提供一种氢化丁腈橡胶在强腐蚀环境中的摩擦系数的测试方法,本实施例与实施例1的不同之处在于,步骤3中浸泡温度为40℃。本实施例中所得摩擦系数如图1所示。经历了步骤4中摩擦系数测试的氢化丁腈橡胶试样的表面形貌如图3所示。从图3a可以看出,在40℃下老化后的氢化丁腈橡胶在经历摩擦之后,表面有橡胶脱落,且存在坑洞,并且坑洞的深度和数量均大于图2a中所示的坑洞的深度和数量。这是因为随着温度的升高,氢化丁腈橡胶分子链活性更大,发生老化现象更加严重,在摩擦过程中更容易脱落下来。从图3b可以看出,此时橡胶内部少量的填料颗粒和橡胶基体开始出现解离,填料颗粒与橡胶基体的结合能力降低。实施例3本实施例提供一种氢化丁腈橡胶在强腐蚀环境中的摩擦系数的测试方法,本实施例与实施例1的不同之处在于,步骤3中浸泡温度为60℃。本实施例中所得摩擦系数如图1所示。经历了步骤4中摩擦系数测试的氢化丁腈橡胶试样的表面形貌如图4所示。从图4a可以看出,在60℃下老化后的氢化丁腈橡胶在经历摩擦之后,表面 有大面积的橡胶脱落,橡胶表面变得粗糙不平。这是因为随着温度的进一步提高,橡胶的老化加重,橡胶中的分子链发生变化而且生成了更容易脱落的老化产物被磨掉,从而使得橡胶表面形貌更加不平。图4b显示此时橡胶内部大量的填料颗粒和出现在橡胶基体表面,填料颗粒与橡胶基体的结合能力降低,基体表面已出现少量孔洞。实施例4本实施例提供一种氢化丁腈橡胶在强腐蚀环境中的摩擦系数的测试方法,本实施例与实施例1的不同之处在于,步骤3中浸泡温度为80℃。本实施例中所得摩擦系数如图1所示。经历了步骤4中摩擦系数测试的氢化丁腈橡胶试样的表面形貌如图5所示。从图4a可以看出,在80℃下老化后的氢化丁腈橡胶在经历摩擦之后,表面形貌更加不平,表面一层橡胶基本全部脱落,并且在新的下层橡胶中产生了新的坑洞,老化程度比图3a、图4a所示更加严重。这是因为在高温下橡胶的老化更加严重从而橡胶的耐磨性能降低。图5b显示橡胶内部的填料颗粒与橡胶基体完全失去结合力,填料颗粒因为摩擦而脱落,致使基体表面留下大量的孔洞。根据图1所示,采用本发明实施例的测试方法得到的氢化丁腈橡胶在强腐蚀环境中的摩擦系数随温度变化的曲线与实际生产中的规律相一致。将图2a、3a、4a以及5a与图6对比可以看出,按照本发明实施例提供的测试方法进行摩擦系数测试后的氢化丁腈橡胶的表面形貌与实际油田生产开发过程中氢化丁腈橡胶摩擦后的表面形貌基本相同,在表面都有大面积的、较深的点蚀坑形成。由此可见,采用本发明实施例的测试方法得到的氢化丁腈橡胶在强腐蚀环境中的摩擦系数与氢化丁腈橡胶在实际强腐蚀环境中的摩擦系数相吻合。同时,本发明实施例提供的测试方法还具有良好的重复性和再现性。以上所述仅是为了便于本领域的技术人员理解本发明的技术方案,并不用以限制本发明。凡在本发明的精神和原则之内,所作的任何修改、等同替换、改进等,均应包含在本发明的保护范围之内。当前第1页12