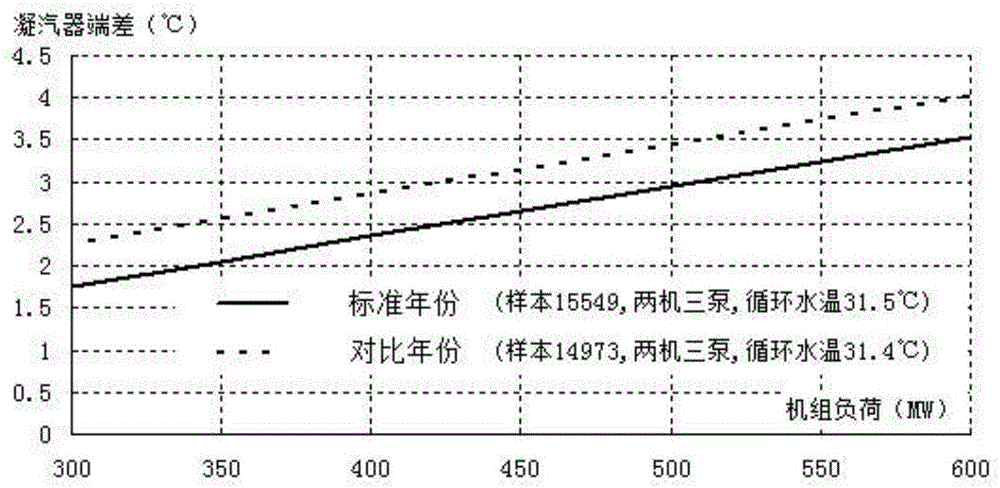
本发明涉及一种基于运行数据统计分析的凝汽器换热性能评价方法,属于火力发电
技术领域:
。
背景技术:
:凝汽器是火力发电机组冷端系统的主要设备,作为一个汽水换热设备,由低压缸排汽温度与循环水出水温度相减得出的凝汽器端差是其关键的评价指标,反映了凝汽器换热性能的优劣,较小的凝汽器端差反映较优的凝汽器换热性能,较大的凝汽器端差反映较劣的凝汽器换热性能,凝汽器端差水平的高低直接影响到整个机组运行的经济性能。但是,现有技术的评价方法,对凝汽器换热性能的评价往往在一个或数个约定工况下进行,覆盖面小,比对工况也往往因引入额外的修正而带来一定的误差,因此难以实现全面准确的评价。如果利用检测设备对凝汽器进行检测评价,一方面需要增加成本投入,另一方面难以实时进行评价。针对目前现有技术中存在的上述缺陷,实有必要进行研发,解决现有技术中存在的缺陷。技术实现要素:针对现有技术的缺陷,本发明的目的在于提供一种不需要额外修正,能够实现实时、全面、准确评价,无需增加投入成本的基于运行数据统计分析的凝汽器换热性能评价方法。为实现上述目的,本发明的技术方案为:一种基于运行数据统计分析的凝汽器换热性能评价方法,包括以下步骤:第一步,对凝汽器以及相关设备进行检测,确定所有设备正常运行,第二步,收集标准离散数据,确保收集的标准离散数据准确可靠,确定采样周期值,收集每个采样周期内的机组负荷、循环水泵运行组合、低压缸排汽温度、循环水出水温度、循环水进水温度数据,然后由低压缸排汽温度与循环水出水温度相减得出凝汽器端差数据;第三步,对标准离散数据进行细化分组,剔除不可靠数据后进行分组,每一分组中,对应一种循环水泵运行组合与一定的循环水进水温度,统计凝汽器端差随机组负荷变化数据;第四步,对细化分组的标准离散数据分别进行数据拟合,得到标准拟合公式,建立标准数据拟合模型,第五步,收集对比离散数据,再次收集采样周期内的机组负荷、循环水泵运行组合、低压缸排汽温度、循环水出水温度、循环水进水温度数据,然后计算凝汽器端差数据;第六步,对再次采集的对比离散数据根据标准离散数据的细化分组方式进行细化分组,每一分组中,对应一种循环水泵运行组合与一定的循环水进水温度,统计凝汽器端差随机组负荷变化数据;第七步,对细化分组的对比离散数据分别进行数据拟合,得到对比拟合公式,建立对比数据拟合模型;第八步,根据需要选取一组机组负荷数据带入标准数据拟和模型,得到不同循环水泵组合、不同循环水进水温度边界条件下的凝汽器端差数据,进而获得全面的凝汽器换热性能状况;第九步,选取一组机组负荷数据代入对比拟合公式,得到一组凝汽器端差并与标准数据拟合模型求出的凝汽器端差对应相减,逐一比较相同循环水泵组合、相同循环水进水温度边界条件下,对比数据拟和模型、标准数据拟和模型的差异性,得到两组凝汽器端差数据的平均偏差值,进而求出总的平均偏差值,得到凝汽器换热性能的变化幅度,对凝汽器换热性能进行评价,判断是否工作异常。本发明通过采集对比年份的运行数据,进而与正常年份的运行数据进行对比,对凝汽器性能进行评价,进而评价凝汽器等相关设备的运行情况。数据采集通过传感器可以自动完成,后续的处理都通过微处理器或者电脑软件根据本发明自动进行,能够有效减少检测成本投入并且能够减少购买各种用于检测的仪器设备。进一步,第二步,收集标准离散数据的运行周期为一年,采样周期的间隔为每5分钟收集一次。进一步,第三步,剔除采集数据中不宜进行凝汽器换热性能评价的数据,包括:机组启动期间数据、机组停机期间数据、循环水泵运行组合切换期间数据。剔除不合理数据,能够有效减少误差,使得本发明的评价方法更加合理可靠。进一步,第三步,根据需要,对循环水进水温度按照3-7摄氏度之间任一温度值进行分组。分组过细,会使得数据过多,计算过于复杂,分组过少,会导致建立的模型不准确,按照3-7摄氏度之间任一温度值进行分组,能够保证建立的模型准确的同时简化计算。进一步,第四步,600MW汽轮机组凝汽器的所述标准拟合公式包括若干组细化标准公式:第一组,循环水泵组合:两机三泵,循环水进水温度为28.6摄氏度y=6.7403*10-3x+2.3100*10-2第二组,循环水泵组合:两机三泵,循环水进水温度为31.5摄氏度y=5.9362*10-3x-2.2600*10-2第三组,循环水泵组合:两机两泵,循环水进水温度为8.7摄氏度y=4.1725*10-3x+3.0194第四组,循环水泵组合:两机两泵,循环水进水温度为12.5摄氏度y=5.8822*10-3x+2.0179第五组,循环水泵组合:两机两泵,循环水进水温度为17.5摄氏度y=6.9926*10-3x+1.1085第六组,循环水泵组合:两机两泵,循环水进水温度为22.6摄氏度y=5.6772*10-3x+7.7691*10-1第七组,循环水泵组合:两机两泵,循环水进水温度为27摄氏度v=6.4443*10-3x-5.1300*10-2x为机组负荷,y为凝汽器端差。进一步,第五步,收集的对比离散数据至少对应一种循环水泵运行组合与一定的循环水进水温度。根据需要对比离散数据可以只收集一组凝汽器端差随机组负荷变化数据,进而对应标准离散数据的同一条件下的细化标准公式,进行对比,对凝汽器换热性能进行初步评价。这种评价方法虽然存在一定的误差,但是需要收集数据的较少,能够实现对凝汽器换热性能的快速实时评价。进一步,第七步,对比拟合公式包括若干组细化对比公式。与现有技术相比,本发明具有以下有益效果:本发明根据机组负荷、循环水泵运行组合、低压缸排汽温度、循环水出水温度、循环水进水温度数据,利用统计分析方法,分别建立标准数据拟合模型、对比数据拟合模型,两者进行对比,得到全面的凝汽器换热性能状况。本发明根据需要对比离散数据可以只收集一组凝汽器端差随机组负荷变化数据,进而对应标准离散数据的同一条件下的细化标准公式,进行对比,对凝汽器换热性能进行初步评价。这种评价方法虽然存在一定的误差,但是需要收集数据的较少,能够实现对凝汽器换热性能的快速实时评价。本发明通过采集对比年份的运行数据,进而与正常年份的运行数据进行对比,对凝汽器性能进行评价,进而评价凝汽器等相关设备的运行情况。数据采集通过传感器可以自动完成,后续的处理都通过微处理器或者电脑软件根据本发明自动进行,能够有效减少检测成本投入并且能够减少购买各种用于检测的仪器设备。本发明能够实时对凝汽器换热性能进行评价,进而实现对凝汽器性能的实时监测,成本低,投入少。附图说明图1为本发明第一种凝汽器端差随机组负荷变化示意图;图2为本发明第二种凝汽器端差随机组负荷变化示意图;图3为本发明第三种凝汽器端差随机组负荷变化示意图;图4为本发明第四种凝汽器端差随机组负荷变化示意图;图5为本发明第五种凝汽器端差随机组负荷变化示意图;图6为本发明第六种凝汽器端差随机组负荷变化示意图;图7为本发明第七种凝汽器端差随机组负荷变化示意图。具体实施方式为了使本发明的目的、技术方案及优点更加清楚明白,以下结合附图及实施例,对本发明进行进一步详细说明。应当理解,此处所描述的具体实施例仅仅用以解释本发明,并不用于限定本发明。相反,本发明涵盖任何由权利要求定义的在本发明的精髓和范围上做的替代、修改、等效方法以及方案。进一步,为了使公众对本发明有更好的了解,在下文对本发明的细节描述中,详尽描述了一些特定的细节部分。对本领域技术人员来说没有这些细节部分的描述也可以完全理解本发明。一种基于运行数据统计分析的凝汽器换热性能评价方法,包括以下步骤:第一步,对凝汽器以及相关设备进行检测,确定所有设备正常运行。第二步,收集标准离散数据,确保收集的标准离散数据准确可靠。收集采样周期内的机组负荷、循环水泵运行组合、低压缸排汽温度、循环水出水温度、循环水进水温度数据,然后由低压缸排汽温度与循环水出水温度相减得出凝汽器端差数据。收集标准离散数据的运行周期为一年,采样周期的间隔为每5分钟收集一次。第三步,对标准离散数据进行细化分组,剔除不可靠数据,剔除采集数据中不宜进行凝汽器换热性能评价的数据,包括:机组启动期间数据、机组停机期间数据、循环水泵运行组合切换期间数据,每一分组中,对应一种循环水泵运行组合与一定的循环水进水温度,统计凝汽器端差随机组负荷变化数据。根据需要,对循环水进水温度按照3-7摄氏度之间任一温度值进行分组。第四步,对细化分组的标准离散数据分别进行数据拟合,得到标准拟合公式,建立标准数据拟合模型,600MW汽轮机组凝汽器的所述标准拟合公式包括若干组细化标准公式:第一组,循环水泵组合:两机三泵,循环水进水温度为28.6摄氏度y=6.7403*10-3x+2.3100*10-2第二组,循环水泵组合:两机三泵,循环水进水温度为31.5摄氏度y=5.9362*10-3x-2.2600*10-2第三组,循环水泵组合:两机两泵,循环水进水温度为8.7摄氏度y=4.1725*10-3x+3.0194第四组,循环水泵组合:两机两泵,循环水进水温度为12.5摄氏度y=5.8822*10-3x+2.0179第五组,循环水泵组合:两机两泵,循环水进水温度为17.5摄氏度y=6.9926*10-3x+1.1085第六组,循环水泵组合:两机两泵,循环水进水温度为22.6摄氏度y=5.6772*10-3x+7.7691*10-1第七组,循环水泵组合:两机两泵,循环水进水温度为27摄氏度y=6.4443*10-3x-5.1300*10-2x为机组负荷,y为凝汽器端差。第五步,收集对比离散数据,再次收集采样周期内的机组负荷、循环水泵运行组合、低压缸排汽温度、循环水出水温度、循环水进水温度数据,然后计算凝汽器端差数据。第六步,对再次采集的对比离散数据根据标准离散数据的细化分组方式进行细化分组,每一分组中,对应一种循环水泵运行组合与一定的循环水进水温度,统计凝汽器端差随机组负荷变化数据;第七步,对细化分组的对比离散数据分别进行数据拟合,得到对比拟合公式,建立对比数据拟合模型;第八步,根据需要选取一组机组负荷数据带入标准数据拟和模型,得到不同循环水泵组合、不同循环水进水温度边界条件下的凝汽器端差数据,进而获得全面的凝汽器换热性能状况;第九步,选取一组机组负荷数据代入对比拟合公式,得到一组凝汽器端差并与标准数据拟合模型求出的凝汽器端差对应相减,逐一比较相同循环水泵组合、相同循环水进水温度边界条件下,对比数据拟和模型、标准数据拟和模型的差异性,得到两组凝汽器端差数据的平均偏差值,进而求出总的平均偏差值,得到凝汽器换热性能的变化幅度,对凝汽器换热性能进行评价,判断是否工作异常。为更清楚的说明本发明技术方案,对某600Mw汽轮机组凝汽器换热性能进行评价。对汽轮机设备以及凝汽器进行检测,确定所有设备正常运行,获取一整年的标准离散数据,作为标准年份数据,后续数据用其作为参考对比。获取该汽轮机组对比年份的数据,采集周期为“5分钟”,即每间隔五分钟采集一次:机组负荷、循环水泵运行组合、低压缸排汽温度、循环水出水温度、循环水进水温度数据,剔除机组启动期间数据、机组停机期间数据、循环水泵运行组合切换期间数据后如表1所示。表1时间段采集样本数预处理后样本数两年(正常年份+对比年份)210240190109由低压缸排汽温度与循环水出水温度相减得出凝汽器端差数据,并按照循环水泵运行组合、“5℃”温度区间的循环水进水温度进行分组,细分区间结果如表2所示。表2对细化分组的标准离散数据分别进行数据拟合,得到标准拟合公式,建立标准数据拟合模型,所述标准拟合公式包括若干组细化标准公式:第一组,循环水泵组合:两机三泵,循环水进水温度为28.6摄氏度y=6.7403*10-3x+2.3100*10-2第二组,循环水泵组合:两机三泵,循环水进水温度为31.5摄氏度y=5.9362*10-3x-2.2600*10-2第三组,循环水泵组合:两机两泵,循环水进水温度为8.7摄氏度y=4.1725*10-3x+3.0194第四组,循环水泵组合:两机两泵,循环水进水温度为12.5摄氏度y=5.8822*10-3x+2-0179第五组,循环水泵组合:两机两泵,循环水进水温度为17.5摄氏度y=6.9926*10-3x+1.1085第六组,循环水泵组合:两机两泵,循环水进水温度为22.6摄氏度y=5.6772*10-3x+7.7691*10-1第七组,循环水泵组合:两机两泵,循环水进水温度为27摄氏度y=6.4443*10-3x-5.1300*10-2x为机组负荷,y为凝汽器端差。对采集的对比离散数据根据标准离散数据的细化分组方式进行细化分组,对细化分组的对比离散数据分别进行数据拟合,得到对比拟合公式,建立对比数据拟合模型,对比拟合公式包括若干组细化对比公式。第一组,循环水泵组合:两机三泵,循环水进水温度为28.6摄氏度y=6.4080*10-3x+7.2560*10-1第二组,循环水泵组合:两机三泵,循环水进水温度为31.5摄氏度y=5.7920*10-3x+5.4320*10-1第三组,循环水泵组合:两机两泵,循环水进水温度为8.7摄氏度y=5.5201*10-3x+3.3830第四组,循环水泵组合:两机两泵,循环水进水温度为12.5摄氏度y=6.7117*10-3x+2.4958第五组,循环水泵组合:两机两泵,循环水进水温度为17.5摄氏度y=5.5010*10-3x+2.5063第六组,循环水泵组合:两机两泵,循环水进水温度为22.6摄氏度y=5.1618*10-3x+1.6638第七组,循环水泵组合:两机两泵,循环水进水温度为27摄氏度y=6.3726*10-3x+5.2130*10-1x为机组负荷,y为凝汽器端差。根据上述公式,绘制对比曲线,如图1-7所示,根据需要选取一组机组负荷数据分别代入对比拟合公式、标准拟合公式,得到两组凝汽器端差,两组凝汽器端差数据对应相减得到一组偏差值,进而求出总的偏差值和和平均偏差值。可得到凝汽器换热性能下降幅度,结果如表3所示:相比正常年份,在不同的循环水泵组合、循环水进水温度条件下,对比年份凝汽器换热性能均有了一定幅度的下降,总的凝汽器端差上升0.69℃,说明凝汽器工作异常,进而对设备进行检查,发现是与凝汽器相配套的胶球在线清洗系统没有正常工作引起。表3本发明根据机组负荷、循环水泵运行组合、低压缸排汽温度、循环水出水温度、循环水进水温度数据,利用统计分析方法,分别建立标准数据拟合模型、对比数据拟合模型,两者进行对比,得到全面的凝汽器换热性能状况。通过采集对比年份的运行数据,进而与正常年份的运行数据进行对比,对凝汽器性能进行评价,进而评价凝汽器等相关设备的运行情况。数据采集通过传感器可以自动完成,后续的处理都通过微处理器或者电脑软件自动进行,能够有效减少检测成本投入并且能够减少购买各种用于检测的仪器设备。本发明能够实时对凝汽器换热性能进行评价,进而实现对凝汽器性能的实时监测,成本低,投入少。以上所述仅为本发明的较佳实施例而已,并不用以限制本发明,凡在本发明的精神和原则之内所作的任何修改、等同替换和改进等,均应包含在本发明的保护范围之内。当前第1页1 2 3