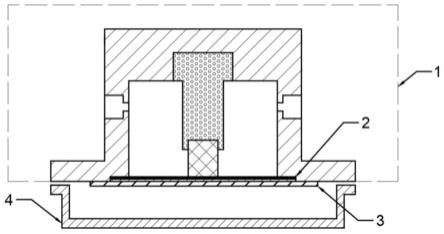
1.本发明属于电子学领域,具体涉及一种测量介质导体沉积界面微波表面电阻的装置及方法。
背景技术:2.无源器件是微波器件的重要组成部分,介质导体沉积界面的微波表面电阻反映导体的损耗,进而影响着无源器件的性能。导体沉积在不同的介质上时,其与介质沉积面的微波表面电阻是不同的,因此获得介质导体沉积界面准确的微波表面电阻,对无源器件的高精度设计来说非常重要。
3.国内外目前普遍采用谐振法对单导体的微波表面电阻进行测量,比较常见的有空腔谐振器法、平行板谐振器法、微带线谐振器法以及介质谐振器法(曾成,罗正祥,张其劭,羊恺.镜像法高温超导薄膜表面电阻测试装置的改进[j].电子科技大学学报,2009,38(02):214-217)。用的较多的方法为空腔谐振器法,如图1所示,该方法的谐振器由金属腔壁和两块密封金属板构成,通过测量所构成的谐振器的品质因数,进行相应的公式推导,便可获得导体的微波表面电阻值。但空腔谐振器法是以待测导体为材料进行腔体设计的,会受限制于待测导体的材料特性,所需待测导体材料尺寸较大,同时谐振器的加工周期较长,会造成待测导体材料和时间的浪费。更为关键的是,这种方法只能测得导体表面的电阻值,由于导体趋肤效应的限制,很难对介质导体沉积界面的微波表面电阻进行准确测量。
技术实现要素:[0004]
针对上述现有技术中存在的问题,本发明提供了一种测量介质导体沉积界面微波表面电阻的装置及方法,实现对介质导体沉积界面微波表面电阻的直接测量,尤其适合大批量测试。
[0005]
为了实现上述目的,本发明提供如下技术方案:
[0006]
一种测量介质导体沉积界面微波表面电阻的装置,其特征在于,包括测试座、校准组件、密封腔和支撑板;
[0007]
所述测试座包括底端面开放的屏蔽腔、介质柱、输入耦合结构、输出耦合结构和介质支撑装置,输入耦合结构和输出耦合结构对称分布于屏蔽腔两侧,介质柱位于屏蔽腔内部,并通过介质支撑装置与屏蔽腔固定,介质柱的底端面与屏蔽腔的底端面处于同一平面;
[0008]
待测介质导体样品放置于介质柱和屏蔽腔的底端面,并通过可拆卸的支撑板紧固待测介质导体样品,待测介质导体样品与测试座构成工作模式为te
011
模式的介质谐振器;其中,所述待测介质导体样品通过将导体沉积在介质上所得,其介质一面朝向介质谐振器内部,导体一面与支撑板相贴合;
[0009]
所述校准组件可拆卸地设置于介质柱和屏蔽腔的底端面;
[0010]
所述密封腔可拆卸地设置于屏蔽腔的底端面外延,以罩住校准组件,或支撑板及待测介质导体样品。
[0011]
进一步地,所述校准组件包括校准板、校准座和校准介质板;其中,所述校准板采用沉积界面微波表面电阻已知的介质导体,代替待测介质导体样品,放置于介质柱和屏蔽腔的底端面;所述校准介质板包括两块与待测介质导体样品中介质层的尺寸和材料相同的介质板,代替待测介质导体样品和支撑板,放置于介质柱和屏蔽腔的底端面,并且校准座与测试座的结构相同,与测试座相对放置,二者关于校准介质板对称。
[0012]
进一步地,所述测试座与介质柱、介质支撑装置同中心轴。
[0013]
进一步地,所述屏蔽腔采用硬金属材料;介质柱采用低损耗、高介电常数的高q值材料,包括金红石、蓝宝石、氧化铍陶瓷等;介质支撑装置采用低损耗的高介电常数材料,包括尼龙、聚四氟乙烯、聚乙烯泡沫等。
[0014]
进一步地,待测介质导体样品的尺寸大于屏蔽腔的底端面开放区域尺寸。
[0015]
进一步地,所述输入耦合装置和输出耦合装置均为耦合孔转同轴结构。
[0016]
进一步地,对工作在te
011
模式下的介质谐振器,利用其边界条件,通过对麦克斯韦方程分析,计算得到介质谐振器的谐振频率和物理尺寸。
[0017]
本发明还提出了上述装置实现测量介质导体沉积界面微波表面电阻的方法,其特征在于,包括以下步骤:
[0018]
步骤1:将校准板装配在测试座上,并采用支撑板固定,使用密封腔密封固定,将所得测试装置保持在待测介质导体样品的工作温度,测得无载品质因数q1;
[0019]
步骤2:将校准座和校准介质板与测试座进行固定,并使用密封腔密封固定,将所得测试装置保持在待测介质导体样品的工作温度,测得无载品质因数q2;
[0020]
步骤3:将待测介质导体样品装配在测试座上,并采用支撑板固定,使用密封腔密封固定,将所得测试装置保持在待测介质导体样品的工作温度,测得无载品质因数q0;
[0021]
步骤4:根据公式
[0022][0023]
计算得到待测导体样品的微波表面电阻rs;其中,r
s1
为校准板的沉积界面微波表面电阻。
[0024]
与现有技术相比,本发明的有益效果如下:
[0025]
本发明提出了一种测量介质导体沉积界面微波表面电阻的装置及方法,采用te
011
模式作为介质谐振器的工作模式,在此工作模式下介质谐振器的无载品质因数和测试灵敏度很高;并通过设置特定的装置结构,仅进行一次无损测量即可获得介质导体沉积界面的微波表面电阻,解决因导体层趋肤深度限制而导致无法准确测试介质导体沉积界面微波表面电阻的问题,同时具有较高的测试效率,尤其适合大批量工业化的测试。
附图说明
[0026]
图1为传统空腔谐振器法中谐振器的剖面构造图;
[0027]
图2为本发明实施例1提出的测量介质导体沉积界面微波表面电阻的装置中测试座的剖面构造图;
[0028]
图3为本发明实施例1提出的测量介质导体沉积界面微波表面电阻的装置加载待测介质导体样品后的剖面构造图;
[0029]
图4为本发明实施例1提出的测量介质导体沉积界面微波表面电阻的装置加载校准板后的剖面构造图;
[0030]
图5为本发明实施例1提出的测量介质导体沉积界面微波表面电阻的装置加载校准座和校准介质板后的剖面构造图;
[0031]
附图中各标记说明如下:
[0032]
1—测试座;2—待测介质导体样品;3—支撑板;4—密封腔;5—屏蔽腔;6—谐振腔;7—输入耦合结构;8—输出耦合结构;9—介质支撑装置;10—介质柱;11—校准介质板;12—校准板;13—校准座。
具体实施方式
[0033]
为使本发明的目的、技术方案和优点更加清楚明白,下面结合实施例和附图,对本发明作进一步的详细说明,本发明的示意性实施方式及其说明仅用于解释本发明,并不作为对本发明的限定。
[0034]
实施例1
[0035]
本实施例提出了一种测量介质导体沉积界面微波表面电阻的装置,包括测试座1、校准组件、密封腔4和支撑板3。所述测试座1的结构如图2所示,包括底端面开放的屏蔽腔5、介质柱10、输入耦合结构7、输出耦合结构8和介质支撑装置9。
[0036]
所述输入耦合结构7和输出耦合结构8对称分布于屏蔽腔5两侧腔壁上,均为耦合孔转同轴结构,能够有效地避免发生直接耦合,具有较高的测试精度。
[0037]
所述介质柱10位于屏蔽腔5内部,并通过介质支撑装置9与屏蔽腔5固定,介质柱10的底端面与屏蔽腔5的底端面处于同一平面,并且测试座1与介质柱10、介质支撑装置9同中心轴。
[0038]
待测介质导体样品2放置于介质柱10和测试腔体5的底端面,尺寸大于测试腔体5的底端面开放区域尺寸,并通过可拆卸的支撑板3紧固待测介质导体样品2。待测介质导体样品2与测试座1构成工作模式为te
011
模式的介质谐振器,中空区域为谐振腔6。所述待测介质导体样品2通过将导体沉积在介质上所得,其介质一面朝向介质谐振器内部,导体一面与支撑板3相贴合。此时测量介质导体沉积界面微波表面电阻的装置加载待测介质导体样品2后的剖面构造如图3所示。
[0039]
所述校准组件可拆卸地设置于介质柱10和测试腔体5的底端面,包括校准板12、校准座13和校准介质板11。所述校准板12采用沉积界面微波表面电阻已知的介质导体,代替待测介质导体样品2,放置于介质柱10和屏蔽腔5的底端面,装置加载校准板12后的剖面构造如图4所示。所述校准介质板11包括两块与待测介质导体样品2中介质层的尺寸和材料相同的介质板,代替待测介质导体样品2和支撑板3,放置于介质柱10和屏蔽腔5的底端面,并且校准座13与测试座1的结构相同,代替密封腔4,与测试座1相对放置,二者关于校准介质板11对称,装置加载校准座13和校准介质板11后的剖面构造如图5所示。其中,校准座13和校准介质板11可通过螺钉、磁吸或卡接的方式固定在屏蔽腔5的底端面外延。
[0040]
所述密封腔4可拆卸地设置于屏蔽腔5的底端面外延,以罩住校准组件,或支撑板3及待测介质导体样品2。
[0041]
其中,所述屏蔽腔5采用黄铜镀银,其内直径约为40mm,内高度约为20mm;介质柱10
采用低损耗、高介电常数的高q值材料,具体为蓝宝石,直径约为10mm,高度约为5mm;介质支撑装置9采用低损耗的高介电常数材料,具体为聚四氟乙烯,下半部分直径约为10mm,高度约为10mm,上半部分直径约为15mm,高度约为5mm。
[0042]
本实施例中待测介质导体样品2与测试座1构成的介质谐振器在测试频率下的无载品质因数q0与待测介质导体样品微波表面电阻rs的关系式为:
[0043]q0-1
=x+yrsꢀꢀꢀꢀꢀꢀꢀꢀꢀꢀꢀꢀꢀꢀꢀꢀꢀꢀꢀꢀꢀꢀꢀꢀ
(1)
[0044]
其工作模式为te
011
,x、y均为与待测介质导体样品沉积界面微波表面电阻无关的常数,由测试方式所决定,公式推导过程如下:
[0045]
由待测介质导体样品2、屏蔽腔5腔壁和电介质材料(包括介质支撑装置9以及介质柱10)构成的介质谐振器的无载品质因数q0可表示为:
[0046][0047]
式中,ω0是介质谐振器的谐振角频率;pc是屏蔽腔5所消耗的功率;pd是电介质材料所消耗的功率;p
sample
是待测介质导体样品2的沉积界面微波表面电阻rs所消耗的功率;w是指在谐振频率f0时,工作模式te
011
一个周期内存储在介质谐振腔中的平均能量。
[0048]
根据电磁场理论,若已知介质谐振腔内的电磁场分布,其计算公式如下:
[0049][0050][0051][0052][0053]
式中,v
rod
、v
ring
、vsub和v
air
分别是介质谐振腔内介质柱10、介质支撑装置9、待测介质导体样品2的介质层和空气所占据的体积;s
ag
和s
sample
分别是屏蔽腔5内表面和待测介质导体样品2的介质层的表面积;ε
′
1-jε
″1、ε
′
2-jε
″2和ε
′
3-jε
″3分别是介质柱10、介质支撑装置9和待测介质导体样品2的介质层的介电常数;ε0、μ0分别为真空中的介电常数和磁导率;e为施加的电场强度,h为施加的磁场强度,h
t
为施加的切向磁场强度;r
sag
和r
ssample
分别为屏蔽腔5和待测介质导体样品2的沉积界面微波表面电阻。
[0054]
综合上述公式可得:
[0055][0056]
式中:
[0057][0058]
[0059]
式中x、y是电磁场积分的比值,在介质谐振腔固定,待测介质导体样品2的微扰不改变介质谐振腔场分布的条件下,x、y的值与待测介质导体样品2本身没有关系,也不会因待测介质导体样品2的变化而改变,同时由于x、y都是与电磁场幅度无关的定值,所以确定x、y的值后,通过测量加载待测介质导体样品2时介质谐振腔的无载品质因数q0,可求出其微波表面电阻rs:
[0060][0061]
通过对介质谐振腔内部的电磁场分布进行求值可以确定x、y的值,但求解过程十分复杂,可以利用实验技术来确定x、y的值。
[0062]
同理,装置加载校准板12后构成的介质谐振腔,以及装置加载校准座13和校准介质板11后构成的介质谐振腔,适用上述推导过程,符合公式(7)。
[0063]
进而,本实施例还提出了上述装置实现测量介质导体沉积界面微波表面电阻的方法,工作温度可为4.2~800k,方法包括以下步骤:
[0064]
步骤1:将校准板12装配在测试座1上,并采用支撑板3固定,使用密封腔4密封固定,将所得测试装置保持在待测介质导体样品2的工作温度,测得无载品质因数q1;
[0065]
步骤2:将校准座13和校准介质板11与测试座1进行固定,并使用密封腔4密封固定,将所得测试装置保持在待测介质导体样品2的工作温度,测得无载品质因数q2;
[0066]
步骤3:将待测介质导体样品2装配在测试座1上,并采用支撑板3固定,使用密封腔4密封固定,将所得测试装置保持在待测介质导体样品2的工作温度,测得无载品质因数q0;
[0067]
步骤4:将步骤1和2所得无载品质因数q1和无载品质因数q2分别带入公式(7)中,得到x=1/q2、y=1/q
1-x/r
s1
,进而得到在测试频率下待测介质导体样品2的微波表面电阻rs为:
[0068][0069]
计算得到待测介质导体样品2的沉积界面微波表面电阻rs;其中,r
s1
为校准板12的沉积界面微波表面电阻。
[0070]
采用本实施例所述装置及方法,在11.5ghz左右的谐振频率f0、室温下,分别测得加载校准板12后,加载校准介质板11和校准座13后,以及加载待测介质导体样品2后,所构成的介质谐振器的无载品质因数。
[0071]
由于待测介质导体样品2的沉积界面微波表面电阻rs与电导率σ满足:
[0072][0073]
其中,ω为工作角频率,μ为样品磁导率。进而,可通过计算电导率测试值σ与电导率标称值σ0之间的误差,以衡量本实施例所述装置及方法用于测试介质导体沉积界面的微波表面电阻的准确度。
[0074]
当采用的校准介质板11的相对介电常数∈r=3.8时,结果如表格1所示。加载校准介质板11和校准座13后构成的介质谐振器的无载品质因数为11918;加载电导率标称值σ0=5.8
×
107s/m的校准板12后构成的介质谐振器的无载品质因数为8903;加载电导率标称值σ0分别为4.1
×
107s/m和6.1
×
107s/m的待测介质导体样品2,构成的介质谐振器的无载品
质因数分别为8499和8968;通过测试得到电导率σ分别为4.0933
×
107s/m和6.1214
×
107s/m,误差均在0.4%以内。
[0075]
当采用的校准介质板11的相对介电常数∈r=23.5时,结果如表格2所示。加载校准介质板11和校准座13后构成的介质谐振器的无载品质因数为12173;加载电导率标称值σ0=5.8
×
107s/m的校准板12后构成的介质谐振器的无载品质因数为8313;加载电导率标称值σ0分别为4.1
×
107s/m和6.1
×
107s/m的待测介质导体样品2,构成的介质谐振器的无载品质因数分别为7843和8378;通过测试得到电导率σ分别为4.1080
×
107s/m和6.0995
×
107s/m,误差均在0.2%以内。
[0076]
表格1
[0077][0078]
表格2
[0079][0080]
综上测试结果表明本实施例所述装置的测试精度很高。
[0081]
需要说明的是,本发明及附图给出了本测试方法较佳的实施例,目的是为了帮助读者更好地理解本发明,本发明可以有各种更改和变化。凡在本技术的精神和原理之内所作的任何修改、替换、改进等,均应包含在本技术的权利要求范围之内。