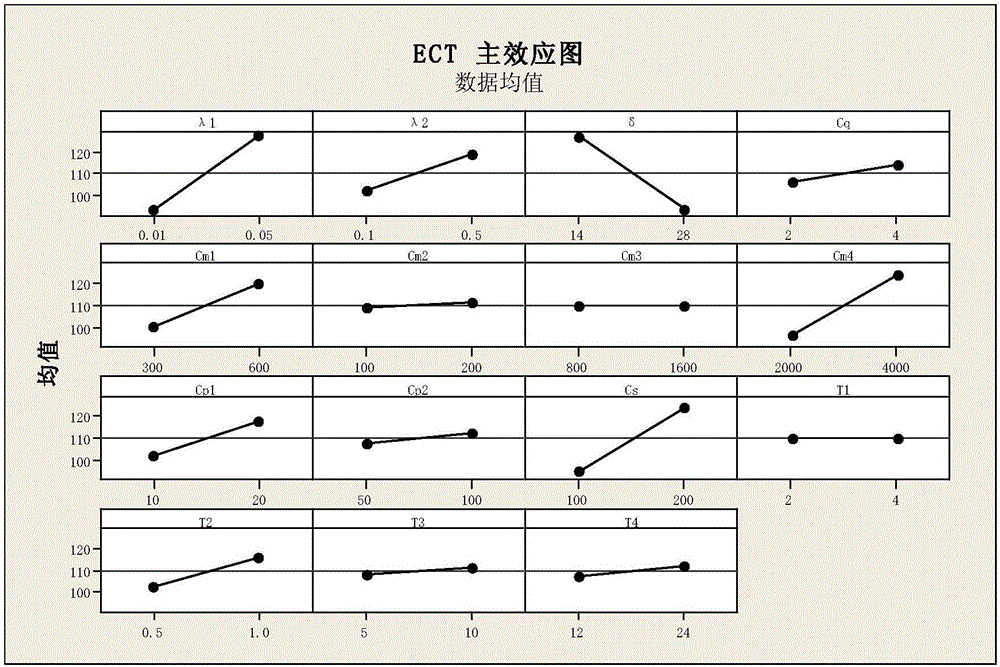
本发明涉及生产系统过程质量与可靠性控制领域,特别涉及一种动态的过程质量控制图和定龄维修联合设计优化控制方法。
背景技术:
:在生产过程中,对设备系统进行预防维修和利用控制图对生产过程进行质量监控是保证产品质量的两种基本手段和方法。由于定时、定龄等预防维修策略和质量控制图两者的集成经济决策相对于单一措施的独立经济决策在生产运行综合费用方面更具经济性,关于预防维修策略和控制图的联合经济设计问题近年来广受关注,是生产系统质量经济效益领域的研究热点之一。自统计过程质量控制和预防维修联合设计问题提出至今,其研究主要集中在系统运行质量成本要素处于静态不变条件下的质量控制图和预防维修参数联合设计的数学建模及其分析领域,并且要求每次维修都修复如新,这与现实生产实际并不相符。在现实生产中,每次维修不仅往往难以修复如新,因此系统每个运行阶段的故障率并非完全一样的,而且由于改进策略的实施、成本要素市场价格变化等因素的影响,系统维修成本、产品质量抽检成本、不合格品的生产费用、维修停机生产损失等质量成本要素在不同维修间隔运行阶段的成本状况也并不一定是确定不变的,而是呈现出动态变化的特征。因此,在每次维修完成后,需要根据系统可靠性变化和运行成本要素结果变化对联合设计的参数方案进行持续的动态调整优化,否则难以实现通过过程质量控制图和预防维修联合设计最大可能降低系统生产运行综合费用的目的。本发明在充分考虑生产系统运行实际状态具有变化性的基础上,提出一种动态的过程质量控制图和定龄维修联合设计优化控制方法,可以解决生产系统过程质量控制图和定龄维修联合设计方案的持续优化问题。技术实现要素:针对上述情况,本发明的目的在于克服现有技术存在的不足而提供一种可以解决生产系统过程质量控制图和定龄维修联合设计方案的持续优化问题的动态的过程质量控制图和定龄维修联合设计方案的控制方法。本发明所采用的技术方案如下,一种动态的过程质量控制图和定龄维修联合设计方案的控制方法,该方法包括以下阶段:第一阶段:构建以维修间隔期生产运行综合费用最小为目标的生产系统过程质量控制图和定龄维修联合设计模型并进行灵敏度分析;第二阶段:基于联合设计模型,根据生产过程质量与维修成本的参数信息,利用遗传算法求解过程质量控制图和定龄维修的设计方案;第三阶段:执行设计方案和管控对策,触发停机维修时判断显著性影响因素的成本水平是否发生变化;第四阶段:优化确定实施方案;根据第三阶段判定结果的不同,本优化过程分为两种情况:(1)如果显著性影响因素值未发生变化,执行步M;(2)如果显著性影响因素值发生了变化,执行步骤N;步骤M:原有联合设计方案不变,优化管控对策并确定执行;步骤N:更新系统过程质量和设备运行可靠性状态信息,利用遗传算法求解联合设计模型产生新的优化设计方案,并确定执行。第一阶段包括以下步骤:步骤A:根据生产系统过程质量控制过程和设备运行过程的特征及其相互关联性,建立生产系统过程质量控制图和维修策略的耦合机制,并由历史数据分析确定生产系统的产品质量特性分布函数和设备运行的寿命分布函数的特征信息;步骤B:基于生产系统过程质量控制图和维修策略的耦合机制及两者的特征信息,在确定所用控制图和相关假设前提下,建立以生产运行综合费用最小为目标的生产系统过程质量控制图和定龄维修联合设计数学模型;步骤C:由步骤B的数学模型,对模型的成本相关参数与目标值的影响关系进行灵敏度分析,识别判定显著性影响因素;步骤D:针对步骤C的显著性影响因素,根据实际生产状况和环境提出改进的管控对策。所述第二阶段包括以下步骤:步骤E:基于matlab语言利用遗传算法求解联合设计模型;步骤F:根据求解结果确定过程质量控制图和定龄维修的设计方案。所述第三阶段包括以下步骤:步骤G:执行设计方案和管控对策,记录系统运行的过程质量和设备运行信息,尤其是系统产量、合格品、不合格品、质量抽检成本、抽检时间、抽检次数、设备运行可靠性状态信息等;步骤H:触发停机维修时,根据记录的过程质量和设备运行状态信息,判定显著性影响因素值在这一阶段的运行过程中是否发生变化。本发明的技术方案产生的积极效果如下:(1)本方案可以实现针对实施过程显著性因素的数据变化重新优化确定实施方案,与传统技术相比,具有能够实现设计方案根据系统运行实际变化情况持续改进和优化的优点;(2)本方案实施无需要求每次维修都修复如新这一假设前提,并且考虑了成本要素市场价格是个动态变化过程等问题,与传统技术相比,具有更符合生产实际情况的优点;(3)本方案模型的运行时间都是基于系统实际运行状态数据实时更新测定,不再需根据控制图的ARL进行估计,与传统技术相比,具有数据更精确的优点。本发明给出了一种动态的生产系统过程质量控制图和定龄维修联合设计优化控制方法,充分考虑了生产系统实际运行状态具有阶段变化性的现实特征,可以解决生产系统过程质量控制图和定龄维修联合设计方案的持续优化问题。附图说明图1为本发明为实现动态的对生产系统过程质量控制图和定龄维修联合设计优化控制的流程图。图2为本发明测试用生产系统的联合模型灵敏度分析结果主效应图。图3为本发明测试用生产系统的联合模型灵敏度分析结果方差分析表。图4本发明测试用生产系统联合模型基本参数在不同维修间隔期的动态信息数据表。图5为本发明测试用生产系统的过程质量控制图和定龄维修在不同运行周期的联合设计方案结果。具体实施方式以下以一个测试生产系统为例,对本发明的实施方式作进一步详细说明。动态的过程质量控制图和定龄维修联合设计方案的控制方法,如图1、2、3、4、5所示,该方法的具体如下步骤:步骤1:分析系统建立维修策略和控制图监测的耦合机制;假设系统存在三种可能状态:受控、失控、故障。已知在每个维修间隔期内,系统由受控转为失控和由失控转为故障停机的时间点t分别服从参数为λ1和λ2的指数分布,密度函数分别为f1(u)和f2(v);系统输出的过程质量特性为X,受控时X~N(μ,σ2),失控时X~N(μ+δ,σ2);采用控制图监控系统过程质量特性X,维修事件由控制图报警、系统故障或定龄维修时间到达三种情况触发。基于以上假设,经分析可知,在一个维修间隔周期内,系统的维修方式和控制图监测存在以下5种可能形成停机维修事件的耦合机制:事件S1:从上一次维修完成后开始,系统在整个定期维修周期内一直受控且控制图未误发报警信号,最后运行到达定期维修时间点触发停机维修,形成定龄维修事件;事件S2:从上一次维修完成后开始,系统一直受控,但控制图在第i次抽检时误发报警信号触发停机维修行为,形成补偿维修事件;事件S3:从上一次维修完成后开始,系统运行至u时刻(u发生在第r个抽样间隔期)由受控转为失控状态,控制图在第j次抽检时发出了正确报警信号触发停机维修,形成状态维修事件;事件S4:从上一次维修完成后开始,系统运行至u时刻(u发生在第r个抽样间隔期)由受控转为失控状态,由于控制图一直漏发报警信号,系统一直失控运行至定期维修时间点触发停机维修,形成状态维修事件;事件S5:从上一次维修完成后开始,系统运行至u时刻(u发生在第r个抽样间隔期)由受控转为失控状态,但由于控制图一直漏发警报,系统运行至v时刻(v发生在第m个抽样间隔期)进一步转为故障停机状态,形成故障维修事件。步骤2:建立以上各维修事件的周期期望运行时间长度函数ET(Si);若记控制图的参数为(n,h,w),犯第一类错误和第二类错误的概率分别为a和β;定期维修的间隔周期为Td=(k+1)h;定龄维修时间为T1,补偿维修时间为T2,状态维修时间为T3,故障维修时间为T4,则分析可知,各维修事件的周期期望运行时间长度为:步骤3:建立以上各维修事件的周期期望运行成本函数EC(Si);假设系统的过程质量检测时间不计,系统故障、控制图报警或到达定龄维修点立即进行相应维修,系统修好后马上投入运行,则系统成本主要由以下几部分组成:系统维修成本、产品抽检成本、不合格品的生产费用、维修停机生产损失。记平均每次定龄维修成本为Cm1,平均每次补偿维修成本为Cm2,平均每次状态维修成本为Cm3,平均每次故障维修成本为Cm4;平均每个样品的抽检成本为Cq;系统正常时单位时间不合格品生产费用为Cp1,系统异常时单位时间不合格品生产费用为Cp2;维修停机单位时间生产损失为Cs。由此可得S1事件的周期期望运行成本为:同理可得,EC(S2)=Σi=1k(Cm2+Cq×in+Cp1×ih+Cs×T2)×(1-a)i-1×a×∫ih∞f1(u)du---(7)]]>EC(S3)=Σj=1kΣr=1j∫(r-1)hrh∫jh-u∞[Cm3+Cq×jn+Cp1×u+Cp2×(jh-u)+Cs×T3]×[(1-a)r-1βj-r(1-β)×f1(u)×f2(v)]dvdu---(8)]]>EC(S4)=Σr=1k+1∫(r-1)hrh∫(k+1)h-u∞{Cm3+Cq×(k+1)n+Cp1×u+Cp2×[(k+1)h-u]+Cs×T3)}×(1-a)r-1βk+1-r×f1(u)×f2(v)dvdu---(9)]]>EC(S5)=Σm=1k+1Σr=1m{(1-a)r-1βm-r∫(r-1)hrhf1(u)×∫(m-1)hmh[Cm4+Cq×(m-1)h+Cp1×u+Cp2×(v-h)+Cs×T4]f2(v-u)dvdu}---(10)]]>步骤4:建立生产系统的过程质量控制和定龄维修联合设计目标函数;以两次维修间隔期内期望单位时间生产运行综合费用最小为目标,可得目标函数为minECT=E(C)E(T)=Σi=15EC(Si)Σi=15ET(Si)---(11)]]>式中:EC(Si)-事件Si状态下的周期期望运行成本;ET(Si)-事件Si状态下的周期期望运行时间;i=1,2,3,4,5。步骤5:进行模型参数的灵敏度分析,并根据结果提出过程管控对策;灵敏度分析利用mintab16方差分析模块的主效应图分析功能进行计算,如图2所示。步骤6:利用遗传算法求解联合设计模型,确定实施方案;遗传算法采用matlab语言编程实现,种群规模popsize=50,交叉概率pc=0.6,变异概率pm=0.1,最大遗传代数maxgen=100。步骤7:执行过程质量控制和定龄维修的设计方案以及过程管控对策;方案执行过程中,收集相关参数的基础信息数据。步骤8:判定是否停机维修;根据停机维修的触发条件,判定是否停机维修;如果不停机维修,继续运行,执行步骤9,如果停机维修,执行步骤10。步骤9:原有联合设计方案不变,优化管控对策并确定执行;步骤10:停机维修后优化确定下一个运行周期的设计方案和管控对策;停机维修时,基于新收集的参数基础信息数据,分析判定显著性因素结果是否变化:如果无变化,提出新的过程管控对策并结合原有设计方案执行下一个运行周期;如果有变化,则根据变化结果优化确定下一个运行周期的设计方案,并结合原有管控对策执行下一个运行周期。整个实施控制的流程图如图1所示。(1)测试系统定义。测试用设备系统定义如下:系统发生异常前的受控时间服从参数λ1的指数分布,故障停机前的失控时间服从参数λ2的指数分布;受控状态下输出质量特性X~N(77,82),失控时引起X的均值漂移值为δ,过程质量采用控制图(n,h,w)进行监控,定龄维修周期长度为Td=(k+1)h,系统停机维修行为由控制图报警、故障或到达定龄维修时间点三个事件触发,n,h,w,k均为决策变量;成本因素包括平均每个样品的抽检成本Cq,定龄维修的单次平均成本Cm1、补偿维修的单次平均成本Cm2、状态维修的单次平均成本Cm3、故障维修的单次平均成本Cm4,系统受控时单位时间不合格品生产费用Cp1、系统失控时单位时间不合格品生产费用Cp2、维修停机的单位时间生产损失Cs;时间因素包括系统运行时间T、定龄维修时间T1、补偿维修时间T2、状态维修时间T3、故障维修时间T4。(2)测试系统联合模型参数的的灵敏度分析。基于测试系统定义,为联合模型参数灵敏度分析结果如图2和图3所示,即该系统联合设计的显著性因素为λ1,δ、Cm4和Cs,针对以上显著性因素提出过程管控对策;(3)测试系统初始过程设计方案求解。基于图4中的初始数据信息,利用遗传算法求解联合设计模型,得到过程质量控制和定龄维修的初始设计方案见图5中的初始过程设计方案结果数据。遗传算法采用matlab语言编程实现,种群规模popsize=50,交叉概率pc=0.6,变异概率pm=0.1,最大遗传代数maxgen=100。(4)执行初始设计方案和过程管控对策触发停机维修。根据初始设计方案和过程管控对策,执行生产系统的过程质量控制和定龄维修活动,收集过程质量和设备运行可靠性和维护的相关基础信息。(5)停机维修后下一运行周期设计方案的优化。在增加上一个运行过程所收集的相关基础信息数据后,分析得到的模型参数新数据见图4中的更新数据,发现显著性因素的结果具有显著变化;基于更新数据计算得到的下一个运行周期的过程质量控制和定龄维修优化设计方案见图5中的优化方案结果数据。遗传算法的参数设置与(3)相同。本发明在系统的全寿命周期内,将每个维修间隔期作为一个决策阶段,并在每个阶段都根据更新数据借助遗传算法对系统过程质量控制图和定龄维修进行联合设计或管控对策的优化,通过这种持续优化获得更符合生产实际的执行方案,从而实现降低生产运行综合成本的目的。当前第1页1 2 3