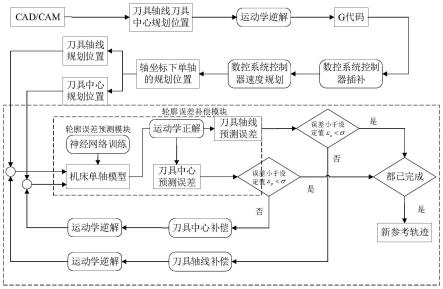
1.本发明属于机床轨迹规划领域,具体涉及一种基于数据驱动的五轴轮廓控制方法。
背景技术:2.五轴机床的轮廓误差与三轴机床的轮廓误差有着很大的不同,三轴机床的轮廓误差只有刀具位置轮廓误差,而对于五轴机床,不仅有刀具位置轮廓误差,刀具位置轮廓误差即为刀具中心轮廓误差,还有刀具方向轮廓误差,刀具方向轮廓误差即为刀具轴线轮廓误差。如图1所示,五轴机床在运行的过程中,期望刀具位置为pd,实际刀具位置为pa,则这两个位置的差值矢量定义为刀具位置跟踪误差e
p
;从期望刀具位置向实际刀具路径作垂线,垂足点pc与期望刀具位置pd的差值矢量定义为刀具位置轮廓误差ε
p
。对于五轴机床,不仅要关注位置的准确性,还要关注刀具方向的准确性,五轴机床的刀具可以呈现不同的方向来加工不同效果的曲面,这就要求刀具的方向要尽可能地精确,图1中od为刀具的期望方向坐标,oa为刀具的实际方向坐标,它们之间存在着一定的差距,将od与oa之间的差值矢量εo定义为刀具方向轮廓误差。只有用刀具位置轮廓误差和刀具方向轮廓误差来表示五轴机床的轮廓误差才能够精确而简便的将其表达出来。
3.在数控机床的轮廓控制方面,交叉耦合控制ccc(cross-couple control)和迭代学习ilc(iterative learning control)是目前较常用的两种方法。交叉耦合控制对负载扰动、双电机位置控制系统引起的同步误差具有良好的抑制作用。迭代学习能以非常简单的方式处理不确定度相当高的动态系统,且仅需较少的先验知识和计算量,同时适应性强,易于实现,且不依赖于动态系统的精确数学模型。目前五轴的轮廓控制方法有伺服整定、模型预测控制、反馈控制等。
4.三轴机床的轮廓误差补偿方案如图2所示,p为规划轨迹,为预测的实际轨迹,p
new
是根据规划轨迹和预测轨迹的差值向规划轨迹反方向计算得到的轨迹,那么就可以将p
new
设为机床新的规划轨迹,在之后的运行过程中,就可以保证实际轨迹更加接近与规划轨迹。
5.五轴机床的交叉耦合控制是根据当前采样时刻的误差补偿后一时刻进行规划,存在补偿滞后的问题。而迭代学习方法必须要重复迭代,且一旦改变轨迹,需要重新进行学习。五轴加工存在刀心位置误差和刀轴方向误差两种误差,且这两种误差之间存在耦合,因此很难对这两种误差进行在线估计和补偿。
6.三轴机床的轮廓误差补偿方案是一次性的补偿,通过这样的补偿方案无法将误差降低到所需要的精度,即三轴机床的补偿方案一次无法补偿彻底,在一次补偿后还会存在一定的误差,也就满足不了加工精度的要求。因此三轴机床的轮廓补偿方案无法应用到五轴机床中。
7.发明专利《一种四轴车床加工轨迹轮廓误差离线补偿方法》(公开号:cn109960215a) 提供了一种四轴车床加工轨迹轮廓误差离线补偿方法属于数控机床加工的轮廓误差补偿领域,涉及一种用于提高封闭式闭环四轴数控车床加工精度的加工轨迹轮
廓误差离线补偿方法。该方法利用初始车削加工代码生成理论刀位点与理论刀轴矢量,构建四轴车床雅可比矩阵,离线计算进给轴实际速度,从而预估车床进给轴随动误差,计算实际刀位点与实际刀轴矢量。采用三次非均匀有理b样条曲线拟合理论刀位点与刀轴标记点,利用切向误差逆推法预估实际刀位点到理论刀位点拟合曲线的垂足,计算刀位点轮廓误差与刀轴矢量轮廓误差。最后,分别对进给轴随动误差进行预补偿。上述专利提到的方法为四轴车床的轮廓误差补偿方法,其并不适用于五轴机床的轮廓误差补偿。
技术实现要素:8.本发明的目的之一在于提供一种基于数据驱动的五轴轮廓控制方法,通过利用五轴机床的单轴跟踪误差来预测五轴机床的轮廓误差,针对五轴机床刀具中心误差和刀具轴线方向误差,单独对两部分的误差进行预测,通过预先设置好的训练集,根据规划轨迹来对运行时的跟踪误差进行预测,同时对轮廓误差进行补偿,补偿部分利用了经神经网络训练得到的机床单轴模型,通过机床单轴模型这一正向误差模型来对误差进行多次迭代补偿,通过选取较小的补偿系数使补偿后的轨迹有着较小的变化,能够保证轨迹的光滑性,一次补偿后再计算误差再进行补偿,直到补偿到所需要的精度,这样的补偿方法最终可以将轮廓误差和刀轴误差降低到很小。
9.为实现上述发明目的,本发明采取的技术方案如下:
10.一种基于数据驱动的五轴轮廓控制方法,包括如下步骤:
11.步骤s1.通过一系列预设的训练集轨迹训练机床单轴的神经网络模型,获取能预测机床轮廓误差的正向误差模型,正向误差模型为机床单轴的神经网络预测模型,所述正向误差模型通过预测机床的单轴跟踪误差来预测机床的轮廓误差,所述轮廓误差包括刀具中心预测误差和刀具轴线预测误差,将刀具中心和刀具轴线的规划位置进行处理得到在轴坐标系下单轴的刀具中心和刀具轴线的规划位置,将单轴的规划位置输入至正向误差模型中,所述正向误差模型根据单轴的刀具中心和刀具轴线的规划位置来预测机床运行后的单轴刀具中心位置以及单轴刀具轴线位置,并计算机床的刀具中心的规划位置和预测的单轴刀具中心位置之间的差值,以及计算机床的刀具轴线的规划位置和预测的单轴刀具轴线位置之间的差值,以获取机床单轴的刀具中心预测误差和刀具轴线预测误差;由于机床的各轴之间耦合关系并不强,所以可以通过预测五轴机床的单轴跟踪误差来预测五轴机床的轮廓误差;
12.步骤s2.在获取机床的刀具中心预测误差和刀具轴线预测误差后,通过正向误差模型来对轮廓误差进行预补偿,以使所述正向误差模型以不断迭代的方式来对刀具中心预测误差和刀具轴线预测误差进行补偿,并且在补偿轮廓误差的过程中,单独对刀具中心和刀具轴线的预测误差进行补偿;以此来实现对非重复性加工误差的主动控制,此种迭代补偿方法可以将刀具轴线误差和刀具中心误差分开进行补偿,使得补偿过程更加简便,最终可以将刀具中心误差和刀具轴线误差降低到很小;
13.步骤s3.完成一次补偿后再计算刀具中心预测误差和刀具轴线预测误差,如误差值仍不符合设定阈值,则继续进行补偿,直到补偿到所需要的精度,当完成刀具轴线补偿过程和刀具中心补偿过程后,生成达到给定误差精度的机床运行轨迹。
14.优选的,所述步骤s2中通过选取设定的小补偿系数使补偿后的轨迹有着较小的变
化,能够保证轨迹的光滑性、良好的轨迹运行特性以及系统的稳定性。
15.优选的,所述机床为五轴机床。五轴机床为应用于数控加工中的五轴机床。
16.优选的,所述正向误差模型为轮廓误差单轴预测模型。轮廓误差的预测与估计最重要的部分为轮廓误差单轴预测模型,轮廓误差单轴预测模型是根据大量的机床轨迹数据进行神经网络训练得到,也就是说,此模型为机床单轴模型,该模型可以根据系统的刀具中心或刀具轴线的规划位置来预测实际的机床运行后的单轴的刀具中心位置以及单轴刀具轴线位置,最终得到的是机床的单轴规划位置与预测出的单轴实际位置的差,即机床的单轴刀具中心预测误差和单轴刀具轴线预测误差。
17.优选的,所述步骤s2中先对刀具中心预测误差进行补偿,补偿直到满足设定阈值或者迭代次数超过设定值,再对刀具轴线预测误差进行补偿;或者对刀具中心预测误差和刀具轴线预测误差同时进行补偿。这样最终可以使刀具位置轮廓误差和刀具轴线轮廓误差都达到加工所需要的误差精度。
18.优选的,所述步骤s1中对刀具中心和刀具轴线的规划位置的数据进行处理的方法如下:
19.通过cad/cam计算得到刀具中心和刀具轴线的规划位置,经过运动学逆解,得到机床各轴的运动参数,生成g代码,将g代码放入数控系统进行插补以及速度规划,以获取单轴的规划加速度、规划速度、规划位置数据,将所述规划加速度、规划速度、规划位置数据转换为轴坐标系下机床各单轴的规划位置数据,并将各单轴的规划位置数据分为单轴刀具中心规划位置以及单轴刀具轴线规划位置。对经cad/cam计算得到的刀具中心和刀具轴线的规划位置数据进行处理,可以保证进入正向误差模型的数据为单轴刀具中心规划位置和/或单轴刀具轴线规划位置。
20.优选的,所述步骤s1中所述正向误差模型获取的单轴的刀具中心预测误差和刀具轴线预测误差方法如下:
21.在单轴刀具中心规划位置以及单轴刀具轴线规划位置之后,将单轴刀具中心规划位置以及单轴刀具轴线规划位置放入正向误差模型中,通过机床单轴模型进行误差预测,得到单轴刀具中心预测误差与单轴刀具轴线预测误差,然后通过运动学正解,得到工件坐标系下机床单轴的刀具轴线预测误差以及刀具中心预测误差,完成五轴轮廓误差的预测与估计。
22.如图3所示的轮廓补偿模块中展示了同时补偿的流程,刀具轴线补偿过程和刀具中心补偿过程同时进行。
23.优选的,所述步骤s3中对于刀具轴线预测误差进行补偿的过程如下:
24.步骤a1.对得到的刀具轴线预测误差进行衡量,若刀具轴线预测误差小于刀具轴线误差阈值δo,则刀具轴线预测误差已经达到所需要的精度,同时刀具轴线轨迹已经达到了要求的精度,无需再进行迭代,刀具轴线预测误差补偿过程结束;若刀具轴线预测误差大于等于刀具轴线误差阈值δo,则刀具轴线预测误差未达到所需要的精度,同时表明刀具轴线轨迹未达到要求的精度,需要进行步骤a2的迭代补偿来进一步提高精度;
25.步骤a2.迭代过程为:将刀具轴线预测误差补偿到原轨迹,得到刀具轴线预测轨迹,对其进行运动学逆解,得到单轴的刀具轴线预测轨迹,将其称为一次补偿后的刀具轴线轨迹,再将其放入神经网络中,并通过训练好的正向误差模型进行误差预测,得到一次补偿
后的单轴刀具轴线预测误差,通过运动学正解得到工件坐标系下的一次补偿轨迹的刀具轴线预测误差,再检验一次补偿后的刀具轴线预测误差是否小于刀具轴线误差阈值δo,若小于刀具轴线误差阈值δo,则表明补偿后的刀具轴线预测误差达到给定误差标准,此时补偿过程结束,若未达标准,则继续进行二次补偿,直到补偿后的刀具轴线预测误差达到给定误差标准或者迭代次数到达设定的给定次数后,则补偿过程结束。
26.优选的,所述步骤s3中对于刀具中心预测误差进行补偿的过程如下:
27.步骤b1.对得到的刀具中心预测误差进行衡量,若刀具中心预测误差小于刀具中心误差阈值δo,则刀具中心预测误差已经达到所需要的精度,同时刀具中心轨迹已经达到了要求的精度,无需再进行迭代,刀具中心预测误差补偿过程结束;若刀具中心预测误差大于等于刀具中心误差阈值δo,则刀具中心预测误差未达到所需要的精度,同时表明刀具中心轨迹未达到要求的精度,需要进行步骤b2的迭代补偿来进一步提高精度;
28.步骤b2.迭代过程为:将刀具中心预测误差补偿到原轨迹,得到刀具中心预测轨迹,对其进行运动学逆解,得到单轴的刀具中心预测轨迹,将其称为一次补偿后的刀具中心轨迹,再将其放入神经网络中,并通过训练好的正向误差模型进行误差预测,得到一次补偿后的单轴刀具中心预测误差,通过运动学正解得到工件坐标系下的一次补偿轨迹的刀具中心预测误差,再检验一次补偿后的刀具中心预测误差是否小于刀具中心误差阈值δo,若小于刀具中心误差阈值δo,则表明补偿后的刀具中心预测误差达到给定误差标准,此时补偿过程结束,若未达标准,则继续进行二次补偿,直到补偿后的刀具中心预测误差达到给定误差标准或者迭代次数到达设定的给定次数后,则补偿过程结束。
29.有益效果:
30.本发明的方案使数控系统在运行新的轨迹时,能对已有的轨迹依据大量数据训练得到作为神经网络预测模型的机床单轴模型,该机床单轴模型为正向误差模型,并通过该模型对轨迹进行提前预测与估计,这样可以使机床上在不执行实际运行轨迹的条件下,只需要通过对已知轨迹进行神经网络拟合的方法,即可预测得到五轴机床的单轴轮廓误差。这样可使得在单轴上的训练集更加容易实现,激励系统会更加充分。此外,本发明提出的通过迭代的方式不断降低轮廓误差,并对轨迹不断进行补偿直到达到所需精度的方法,在补偿的过程中,本发明利用利用神经网络学习到的机床单轴模型多次对单轴轮廓误差进行补偿,这样做的好处在于单轴的预测与补偿是非耦合的,既可以降低预测与补偿的难度,又可以节省大量时间。此外,这种补偿方式可以用适中的补偿系数来使得轨迹改变较小,使得轨迹更加光滑,同时不会改变轨迹运行特性,也不会激发起系统高频模态。最终,本发明不仅将轮廓误差和刀轴误差最终降低很小,同时也保证了系统运行综合性能良好。
31.本发明的五轴轮廓控制方法可应用于数控加工中的五轴机床,也可应用于需要多电机协同工作以得到高精度运行轨迹的系统,例如机器人、数控机床以及印刷机等依靠伺服系统,需要多个运动轴配合进行运动的系统。
附图说明
32.图1为背景技术中五轴机床运行过程中刀具位置轮廓误差与刀具方向轮廓误差图;
33.图2为背景技术中三轴机床的轮廓误差补偿流程图;
34.图3为本发明基于数据驱动的五轴轮廓控制方法流程图;
具体实施方式
35.为了更清楚地说明本发明实施例或现有技术中的技术方案,下面将对照附图说明本发明的具体实施方式。显而易见地,下面描述中的附图仅仅是本发明的一些实施例,对于本领域普通技术人员来讲,在不付出创造性劳动的前提下,还可以根据这些附图获得其他的附图,并获得其他的实施方式。
36.下面以具体实施例详细介绍本发明的技术方案。
37.如图3所示,一种基于数据驱动的五轴轮廓控制方法,包括如下步骤:
38.步骤s1.通过一系列预设的训练集轨迹训练机床单轴的神经网络模型,获取能预测机床轮廓误差的正向误差模型,正向误差模型为机床单轴的神经网络预测模型,所述正向误差模型通过预测机床的单轴跟踪误差来预测机床的轮廓误差,所述轮廓误差包括刀具中心预测误差和刀具轴线预测误差,将刀具中心和刀具轴线的规划位置进行处理得到在轴坐标系下单轴的刀具中心和刀具轴线的规划位置,将单轴的规划位置输入至正向误差模型中,所述正向误差模型根据单轴的刀具中心和刀具轴线的规划位置来预测机床运行后的单轴刀具中心位置以及单轴刀具轴线位置,并计算机床的刀具中心的规划位置和预测的单轴刀具中心位置之间的差值,以及计算机床的刀具轴线的规划位置和预测的单轴刀具轴线位置之间的差值,以获取机床单轴的刀具中心预测误差和刀具轴线预测误差;由于机床的各轴之间耦合关系并不强,所以可以通过预测五轴机床的单轴跟踪误差来预测五轴机床的轮廓误差;
39.步骤s2.在获取机床的刀具中心预测误差和刀具轴线预测误差后,通过正向误差模型来对轮廓误差进行预补偿,以使所述正向误差模型以不断迭代的方式来对刀具中心预测误差和刀具轴线预测误差进行补偿,并且在补偿轮廓误差的过程中,单独对刀具中心和刀具轴线的预测误差进行补偿;以此来实现对非重复性加工误差的主动控制,此种迭代补偿方法可以将刀具轴线误差和刀具中心误差分开进行补偿,使得补偿过程更加简便,最终可以将刀具中心误差和刀具轴线误差降低到很小;
40.步骤s3.完成一次补偿后再计算刀具中心预测误差和刀具轴线预测误差,如误差值仍不符合设定阈值,则继续进行补偿,直到补偿到所需要的精度,当完成刀具轴线补偿过程和刀具中心补偿过程后,生成达到给定误差精度的机床运行轨迹。
41.所述机床为五轴机床。五轴机床为应用于数控加工中的五轴机床。所述步骤s2中通过选取设定的小补偿系数使补偿后的轨迹有着较小的变化,能够保证轨迹的光滑性、良好的轨迹运行特性以及系统的稳定性。
42.所述正向误差模型为轮廓误差单轴预测模型。轮廓误差的预测与估计最重要的部分为轮廓误差单轴预测模型,轮廓误差单轴预测模型是根据大量的机床轨迹数据进行神经网络训练得到,也就是说,此模型为机床单轴模型,该模型可以根据系统的刀具中心或刀具轴线的规划位置来预测实际的机床运行后的单轴的刀具中心位置以及单轴刀具轴线位置,最终得到的是机床的单轴规划位置与预测出的单轴实际位置的差,即机床的单轴刀具中心预测误差和单轴刀具轴线预测误差。
43.所述步骤s2中先对刀具中心预测误差进行补偿,补偿直到满足设定阈值或者迭代
次数超过设定值,再对刀具轴线预测误差进行补偿;或者对刀具中心预测误差和刀具轴线预测误差同时进行补偿。这样最终可以使刀具位置轮廓误差和刀具轴线轮廓误差都达到加工所需要的误差精度。
44.如图3所示,所述步骤s1中对刀具中心和刀具轴线的规划位置的数据进行处理的方法如下:
45.通过cad/cam计算得到刀具中心和刀具轴线的规划位置,经过运动学逆解,得到机床各轴的运动参数,生成g代码,将g代码放入数控系统进行插补以及速度规划,以获取单轴的规划加速度、规划速度、规划位置数据,将所述规划加速度、规划速度、规划位置数据转换为轴坐标系下机床各单轴的规划位置数据,并将各单轴的规划位置数据分为单轴刀具中心规划位置以及单轴刀具轴线规划位置。对经cad/cam计算得到的刀具中心和刀具轴线的规划位置数据进行处理,可以保证进入正向误差模型的数据为单轴刀具中心规划位置和/或单轴刀具轴线规划位置。
46.所述步骤s1中所述正向误差模型获取的单轴的刀具中心预测误差和刀具轴线预测误差方法如下:
47.在单轴刀具中心规划位置以及单轴刀具轴线规划位置之后,将单轴刀具中心规划位置以及单轴刀具轴线规划位置放入正向误差模型中,通过机床单轴模型进行误差预测,得到单轴刀具中心预测误差与单轴刀具轴线预测误差,然后通过运动学正解,得到工件坐标系下机床单轴的刀具轴线预测误差以及刀具中心预测误差,完成五轴轮廓误差的预测与估计。
48.如图3所示的轮廓补偿模块中展示了对刀具中心预测误差和刀具轴线预测误差同时补偿的流程,使得刀具轴线补偿过程和刀具中心补偿过程同时进行。
49.所述步骤s3中对于刀具轴线预测误差进行补偿的过程如下:
50.步骤a1.对得到的刀具轴线预测误差进行衡量,若刀具轴线预测误差小于刀具轴线误差阈值δo,则刀具轴线预测误差已经达到所需要的精度,同时刀具轴线轨迹已经达到了要求的精度,无需再进行迭代,刀具轴线预测误差补偿过程结束;若刀具轴线预测误差大于等于刀具轴线误差阈值δo,则刀具轴线预测误差未达到所需要的精度,同时表明刀具轴线轨迹未达到要求的精度,需要进行步骤a2的迭代补偿来进一步提高精度;
51.步骤a2.迭代过程为:将刀具轴线预测误差补偿到原轨迹,得到刀具轴线预测轨迹,对其进行运动学逆解,得到单轴的刀具轴线预测轨迹,将其称为一次补偿后的刀具轴线轨迹,再将其放入神经网络中,并通过训练好的正向误差模型进行误差预测,得到一次补偿后的单轴刀具轴线预测误差,通过运动学正解得到工件坐标系下的一次补偿轨迹的刀具轴线预测误差,再检验一次补偿后的刀具轴线预测误差是否小于刀具轴线误差阈值δo,若小于刀具轴线误差阈值δo,则表明补偿后的刀具轴线预测误差达到给定误差标准,此时补偿过程结束,若未达标准,则继续进行二次补偿,直到补偿后的刀具轴线预测误差达到给定误差标准或者迭代次数到达设定的给定次数后,则补偿过程结束。
52.所述步骤s3中对于刀具中心预测误差进行补偿的过程如下:
53.步骤b1.对得到的刀具中心预测误差进行衡量,若刀具中心预测误差小于刀具中心误差阈值δo,则刀具中心预测误差已经达到所需要的精度,同时刀具中心轨迹已经达到了要求的精度,无需再进行迭代,刀具中心预测误差补偿过程结束;若刀具中心预测误差大
于等于刀具中心误差阈值δo,则刀具中心预测误差未达到所需要的精度,同时表明刀具中心轨迹未达到要求的精度,需要进行步骤b2的迭代补偿来进一步提高精度;
54.步骤b2.迭代过程为:将刀具中心预测误差补偿到原轨迹,得到刀具中心预测轨迹,对其进行运动学逆解,得到单轴的刀具中心预测轨迹,将其称为一次补偿后的刀具中心轨迹,再将其放入神经网络中,并通过训练好的正向误差模型进行误差预测,得到一次补偿后的单轴刀具中心预测误差,通过运动学正解得到工件坐标系下的一次补偿轨迹的刀具中心预测误差,再检验一次补偿后的刀具中心预测误差是否小于刀具中心误差阈值δo,若小于刀具中心误差阈值δo,则表明补偿后的刀具中心预测误差达到给定误差标准,此时补偿过程结束,若未达标准,则继续进行二次补偿,直到补偿后的刀具中心预测误差达到给定误差标准或者迭代次数到达设定的给定次数后,则补偿过程结束。
55.本发明利用一系列预设的训练集轨迹训练五轴机床单轴的神经网络模型,在单轴上的训练集可以更加容易实现,激励系统会更加充分,从而可以更加精准的预测五轴机床两个独立的刀心位置误差和刀轴方向误差,来获得机床的正向误差模型,该正向误差模型可以作为机床单轴模型,通过得到的模型对刀具中心预测误差和刀具轴线预测误差进行预补偿,通过神经网络以不断迭代的方式来对轮廓误差进行进一步的补偿,并且在补偿轮廓误差的过程中,可以分别对刀具中心轮廓误差和刀具轴线轮廓误差进行预测补偿,最终可以使刀具中心轮廓误差和刀具轴线轮廓误差都达到加工所需要的误差精度,这样的方法可以显著提高五轴数控机床在加工过程中对任意轨迹的加工精度。
56.以上对本发明所提供的实施例进行了详细阐述。本文中应用了具体个例对本发明的原理及实施方式进行了阐述,以上实施例的说明只是用于帮助理解本发明的核心思想。应当指出,对于本技术领域的普通技术人员来说,在不脱离本发明的原理的前提下,还可以本发明进行若干改进和修饰,这些改进和修饰也落入本发明权利要求的保护范围内。