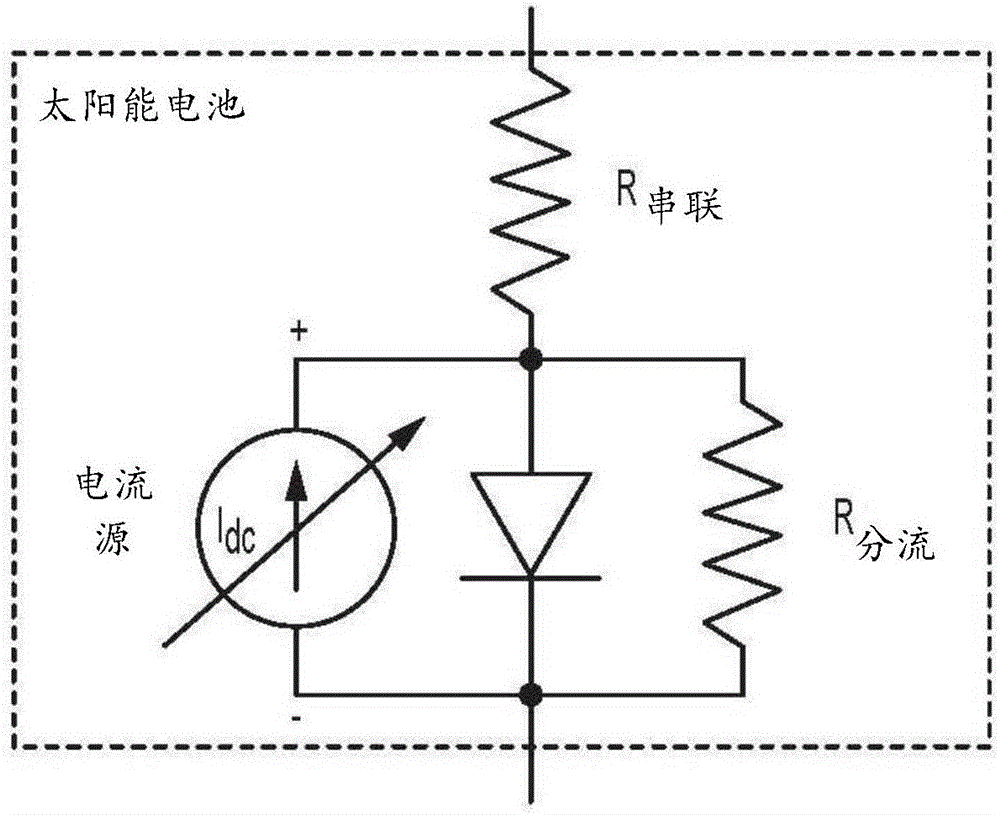
用于光伏太阳能电池和模块中的单片集成旁路开关的系统和方法相关申请的交叉引用本申请要求2012年10月16日提交的临时专利申请61/714,723的权益,所述临时专利申请特此以引用的方式整体并入。发明领域本公开总体涉及太阳能光伏(PV)电池和模块领域,并且更具体来说涉及嵌入在模块叠层中以用于分布式集成阴影管理、从而增强光伏(PV)太阳能电池和模块中的功率和能量采集的单片集成旁路开关(MIBS)。背景晶体硅光伏(PV)模块目前(自2012年起)所占比例高于整个全球PV年需求市场和累计全球装机PV容量的近似85%。晶体硅PV的制造工艺是基于对晶体硅太阳能电池的使用,以由直拉(CZ)硅锭或铸造硅砖制成的单晶硅或多晶硅晶片开始。基于非晶体硅的薄膜PV模块(例如像CdTe、CIGS、有机和无定形硅PV模块)可为低成本制造工艺提供可能性,但是相较于主流晶体硅PV模块(对于商业晶体硅模块而言,提供近似14%一直到约20%的典型范围内、并且大多数情况下约14%到17%的范围内的模块效率),通常为商业薄膜PV模块提供低得多的转换效率(STC模块效率在个位数一直到约14%的范围内),并且相较于得到确认的晶体硅太阳能PV模块,提供未证实的现场可靠性的长期跟踪记录。相较于各种其它PV技术,前沿晶体硅PV模块提供较高的总体能量转换性能、长期现场可靠性、无毒性和寿命周期可持续性。此外,最近的进展和进步已经使晶体硅PV模块的总制造成本处于或低于近似$0.65至$0.80/Wp。击穿单晶硅技术—如基于使用可再用晶体硅模板、薄(例如,晶体硅吸收体厚度为近似10μm一直到约100μm,并且通常≤70μm)外延硅、使用底板附件/叠层的薄硅支撑件和多孔硅剥离技术所制造的高效薄膜单晶硅太阳能电池—在大规模生产时提供高效率(在标准试验条件或STC下太阳能电池和/或模块效率为至少20%)和远远低于$0.50/Wp的PV模块制造成本的前景。图1A是示出典型的太阳能电池如晶体硅太阳能电池或化合物半导体如GaAs太阳能电池的等效电路的示意图。太阳能电池可以被表示为电流源,所述电流源产生显示为IL或还被称为短路电流Isc(在太阳能电池基极和发射极端子电气短路时流动的电流)的光生或光诱导的电流,所述电流源与二极管并联、还与寄生分流电阻并联并且与寄生串联电阻串联。由电流源产生的电流取决于太阳能电池上的太阳光照射功率强度的水平。不合需要的暗电流ID由太阳能电池中的复合损失产生。太阳能电池的端子断开或未连接到任何负载时,跨太阳能电池两端的电压被称为Voc或开路电压。现实的太阳能电池等效电路还包括有穷串联电阻Rs和有穷分流电阻RSH,如图1A和图1B的电路示意图中所示。在理想的太阳能电池中,串联电阻RS为零(即,无串联电阻欧姆功率损耗)并且分流电阻RSH是无穷的(无分流电阻功率耗散损耗)。然而,在实际和现实的太阳能电池中,有穷(非零)串联电阻归因于以下事实:太阳能电池在其半导体吸收层和金属化结构中具有寄生串联电阻部件(即,太阳能电池不是完美的导电体)。在太阳能电池操作期间,此类寄生电阻部件、包括半导体层电阻和金属化电阻造成一些欧姆损耗和功率耗散(并且因此,占空因数降级)。有穷(非无穷)分流电阻由从一个端子到另一个端子的电流的不合需要泄漏引起,所述不合需要泄漏归因于不利影响如基于区域的和边缘诱导的(包括但不限于不完全边缘隔离)分流缺陷以及太阳能电池中的其它非理想因素。此外,理想太阳能电池将具有为零的串联电阻和具有无穷电阻值的分流电阻。图2A同样是示出太阳能电池的等效电路模型的示意图,其示出电流源、光生电流和暗电流(但未示出寄生串联电阻部件和分流电阻部件),并且图2B是示出太阳能电池如晶体硅太阳能电池在电池上有和没有太阳光照射的情况下的典型电流电压(IV)特性的对应定性电流电压(IV)曲线图。IL和ID分别是太阳能电池的所需有效光生电流和不合需要的暗电流。用于光伏(PV)模块中的太阳能电池基本上是光电二极管—它们通过半导体吸收体中的光生载流子(通常为电子和空穴)直接将到达它们的光接收表面处的太阳光转换成电功率。在具有多个太阳能电池的模块中,任何被遮蔽电池不能与层压在同一PV模块内的未被遮蔽电池产生相同量的电功率(或电流)。因为层压在典型PV模块中的所有电池通常串联连接成串,所以功率的差异还导致通过电池的光生电流的差异(被遮蔽电池对比未被遮蔽电池)。如果尝试驱动串联连接的未被遮蔽电池的较高电流通过同样与所述未被遮蔽电池串联连接的被遮蔽(或部分被遮蔽)电池,那么被遮蔽电池(或部分被遮蔽电池)的电压实际上变为负值(即,被遮蔽电池有效地变成反向偏压)。在此反向偏压条件下,被遮蔽电池消耗或耗散大量功率而不是产生功率。由被遮蔽或部分被遮蔽电池消耗和耗散的功率将导致电池变热,从而在模块内被遮蔽电池所定位的地方产生局部热点,并且最终可能导致永久性电池和模块故障,因此在现场产生主要的可靠性故障问题(除非实施保护性措施)。标准(即,通常为包括60个太阳能电池的PV模块)晶体硅PV模块通常在PV模块内被连线成三个20-电池(或在72-电池模块的情况下为24个电池或在96-电池模块的情况下为32个电池)串联连接串,其中具有20个电池的每一串由放置在内部接线盒中的外部旁路二极管(通常为pn结二极管或肖特基二极管)保护。具有20个电池的这些串在接线盒内彼此电气串联连接以形成最终的PV模块组件电气互连并且提供模块的输出电引线,从而通常构成串联连接的太阳能电池。只要PV模块在其表面上接收相对均匀的太阳光辐射并且无电池被遮蔽,那么模块内的电池将产生基本上等量的功率(和电流),其中对于大多数晶体硅PV模块,电池最大功率电压或Vmp大约近似~0.5V到0.6V。因此,对于使用晶体硅电池的包括三个20-电池串联连接子串的60-电池PV模块,跨具有串联连接的20个电池的每一串两端的最大功率电压或Vmp将近似约为10V到12V。在均匀的模块照射条件下,每个外部旁路二极管跨其端子两端将具有约-10V到-12V的反向偏压(例如,当模块在其最大功率点或MPP下操作时),并且旁路二极管保持处于反向偏置截止状态(因此,位于接线盒中的反向偏置外部旁路二极管将不会对模块功率输出造成影响)。在20-电池串中的一个太阳能电池被部分或完全遮蔽的情况下,所述太阳能电池与未被遮蔽电池相比产生较少的电功率(和更小的电流)。因为串中的电池通常电气串联连接,所以被遮蔽电池实际上变为反向偏压并且开始耗散电功率,并且因此将会在反向偏压被遮蔽电池的位置处造成局部热点而不是产生功率。除非采取适当的预防措施,否则被遮蔽电池的功率耗散和所产生的局部变热可能由于潜在的灾难性故障(如反向偏压被遮蔽电池的故障、电池到电池电气互连的故障和/或模块层压材料如模块密封剂和/或底片的故障)而造成较差的电池和模块可靠性,并且由于装机PV系统中的过度变热或热点而造成潜在的火灾危险。晶体硅模块常常使用外部旁路二极管,以便消除以上提及的由太阳能电池的部分或完全遮蔽引起的热点效应,并且防止归因于电池反向偏压变热所产生的潜在的电池和模块可靠性故障和安全危险。如果到达PV模块中的PV电池表面处的太阳光不够均匀(例如,由于一个或多个太阳能电池的完全或甚至部分遮蔽),那么由被遮蔽电池的反向偏压引起的此类热点现象可能永久地损坏受影响的PV电池并且甚至引起火灾危险。旁路二极管(整流器)常常被放置在PV模块内的太阳能电池子串两端,在具有三个20-电池子串的标准60-电池晶体硅太阳能模块中,通常每具有20个太阳能电池的子串有一个外部旁路二极管(所述配置在具有三个24-电池子串的72-电池晶体硅太阳能模块中可以为每具有24个太阳能电池的子串有一个外部旁路二极管;许多其它配置有可能用于具有任何数目的太阳能电池的模块)。跨串联连接的电池串两端具有外部旁路二极管的这种连接配置防止了模块中的反向偏压热点并且允许PV模块在其整个寿命期间在各种实际生活遮蔽或部分遮蔽或污染条件下非常可靠地操作。在不存在电池遮蔽的情况下,串中的每个电池用作与子串中的其它电池具有相对匹配的电流值的电流源,其中子串中的外部旁路二极管与模块中的子串的总电压反向偏置(例如,在晶体硅PV模块中,串联的20个电池跨旁路二极管两端产生近似约10V到12V反向偏压)。在子串中的电池被遮蔽的情况下,被遮蔽电池被反向偏压,从而使用于包括被遮蔽电池的子串的旁路二极管导通,进而允许来自未被遮蔽子串中的良好太阳能电池的电流流过与具有被遮蔽电池的子串相关联的外部旁路二极管。虽然外部旁路二极管(标准主流60-电池晶体硅PV模块接线盒中通常包括三个外部旁路二极管)在电池被遮蔽的情况下保护PV模块和电池,但是旁路二极管实际上还可因遮蔽损失而造成装机PV系统的功率采集和能量产量的显著损失。图3A和图3B是代表性60-电池晶体硅太阳能模块的图,太阳能模块具有串联连接的三个20-电池子串2(每个子串中具有串联连接的20个电池)和在模块中的任何电池被遮蔽或过度部分被遮蔽期间(图3A示出单电池遮蔽,被遮蔽电池6,并且图3B示出多电池部分遮蔽情况,部分被遮蔽行8)保护电池的三个外部旁路二极管4。作为实例,图3A示出在底部行中具有1个被遮蔽电池的60-电池模块(一个20-电池子串受甚至单电池遮蔽影响),并且图3B示出在底部行中具有6个部分被遮蔽电池的60-电池模块(三个20-电池子串都受遮蔽影响)。如果子串中的一个或多个电池被遮蔽(或部分被遮蔽到显著遮蔽程度)(如图3A中所示),那么用于具有被遮蔽电池的子串的外部旁路二极管被启动并且对整个子串分流,由此既通过防止热点保护了被遮蔽电池又使有效模块功率输出降低了约1/3(如果三个子串中的仅一个受太阳能电池遮蔽影响)。如果每子串有至少一个电池被遮蔽(如图3B中所示),那么所有三个旁路二极管都被启动并且对整个模块分流,由此防止了在三个20-电池子串中的每一个中存在至少一个被遮蔽或部分被遮蔽电池时从模块提取任何功率。作为实例,典型的现有技术外部PV模块接线盒可容纳60-电池晶体硅太阳能模块中的三个外部旁路二极管。外部接线盒和相关的外部旁路二极管构成整个PV模块材料清单(BOM)成本的一部分,并且可占PV模块BOM成本的约10%(或约5%至15%)(即,以不包括太阳能电池成本的PV模块BOM成本的百分比计)。此外,外部接线盒还可能是装机PV系统中的现场可靠性故障和火灾危险的来源。虽然大多数当前晶体硅PV模块主要使用外部接线盒,其中外部旁路二极管放置在接线盒中,但是已存在具有前接触电池的PV模块的一些实例,其在模块层压工艺期间将三个旁路二极管直接放置并层压在PV模块组件内,但与前接触太阳能电池分开(然而,每前接触电池的20-电池子串仍然使用一个旁路二极管)。此实例仍然具有外部旁路二极管的局限性,即,即使当单个电池被遮蔽时,旁路二极管也对在子串内具有被遮蔽电池的整个电池子串分流,由此降低了装机PV系统的功率采集和能量产量能力。最小化串联模块串中的模块被遮蔽的可靠性故障影响的一种已知现有技术方法在于跨串联连接的模块两端使用旁路二极管,如图4A和图4B连同图5中所描绘的示例性电路示意性示出。此配置实际上与在每个模块接线盒内具有外部旁路二极管的模块相同。图4A示出串联连接太阳能PV模块串的未被遮蔽电流通路,并且图4B示出同一串联连接太阳能PV模块串,其中一个模块被遮蔽并且跨被遮蔽模块两端的相关联的旁路二极管对所述模块分流并且为串联串提供替代旁路电流通路。图5是具有多个串联连接的太阳能电池的示意性电路模型图,其中外部旁路二极管用于模块子串或串(每个太阳能电池以其等效电路图示出,包括电流源、整流二极管以及寄生串联电阻元件和并联电阻元件)。如果串联连接串中无电池被遮蔽,那么旁路二极管保持处于反向偏置状态并且太阳能电池串正常操作,从而完全致力于太阳能模块发电。如果任何电池部分或完全被遮蔽,那么被遮蔽电池(因此串联连接串中的所有太阳能电池)被反向偏压并且外部旁路二极管因此正向偏置,因此消除了热点、可靠性故障和/或对被遮蔽电池的损坏的可能性。换句话说,当PV模块的至少一部分被遮蔽时,其旁路二极管被正向偏置并且传导电流,从而防止模块串联串中出现性能衰退和可靠性问题。旁路二极管将整个被遮蔽模块(或具有至少一个被遮蔽电池的子串)的电压保持到较小的负电压(例如,-0.5V到0.7V),从而限制模块串阵列输出的总功率降低。图6是示出典型晶体太阳能电池在具有和不具有旁路二极管情况下的电流-电压(I-V)特性的曲线图(实例以pn结旁路二极管示出;对于肖特基二极管,实际电压降将会更小)。旁路二极管将施加到被遮蔽太阳能电池两端的最大反向偏压限制到不超过旁路二极管的导通正向偏压(例如,对于肖特基和pn结旁路二极管,分别位于约0.3V-0.5V之间以及约0.6V-0.7V之间)。图7是示出与图4和图5的晶体硅PV模块类似的晶体硅PV模块代表性实例的图,其中在60-电池模块内每20-电池子串具有一个被遮蔽(或部分被遮蔽)电池(如被遮蔽电池10,共有三个电池被遮蔽,如此代表性实例中所示),其中因为所有三个20-电池子串均由其外部旁路二极管分流以保护被遮蔽电池,三个20-电池子串中的三个被遮蔽电池导致消除了由整个太阳能PV模块提供的电功率。使用每20-电池子串一个外部旁路二极管的布置,三个20-电池子串中具有三个被遮蔽电池的结果在于:从PV模块提取的电功率基本上降为零,即使仅3/60的模块(或60个电池中的3个)受遮蔽影响。此外,这种类型的具有外部旁路二极管的现有技术PV模块布置可导致现场、尤其是在最易受模块遮蔽和/或受污染条件影响的设施中的装机PV系统的显著能量产量降低和功率采集损少。在具有多个模块串的晶体硅PV系统设施中,模块遮蔽影响和其对功率采集和能量产量的不利影响可能比以上所示的具有单个模块串联串的实例大得多。在具有串联连接模块串的多个并联串的太阳能PV系统中,并联串必须与彼此产生近似相同的电压(即,并联串的电压必须密切匹配,否则将存在显著的功率损耗)。因此,使所有并联连接的模块串在近似相同的电压下操作的电气约束不允许被遮蔽串在没有显著的装机PV阵列功率损耗的情况下非常灵活地启动其旁路二极管。因此,在基本上所有情况下,PV模块上影响即使一个串内的一个电池的遮蔽或甚至部分遮蔽也可能实际上切断由整个串产生的功率。作为代表性实例,考虑一个未被遮蔽PV模块串和被遮蔽的一个PV模块串(如上文前一实例中所描述)。最大功率点跟踪(MPPT)能力将允许从第一PV模块串产生满功率并且从第二PV模块串产生满功率的70%。以此方式,两个串达到相同电压(对于具有串联连接模块的并联连接串,来自并联串的电流在相同模块串电压下是可加的)。因此,在这个实例中并使用具有集中式MPPT的集中式DC到AC逆变器,由PV模块阵列产生的功率在没有任何模块遮蔽的情况下将为最大可能功率的85%。这表示PV系统有15%的功率损耗。图8和图9是示出已知PV系统设施的两个实例的图。图8示出现有技术PV模块(例如,每个具有50W输出)的3x6阵列的实例,其中旁路二极管被连接以产生600VDC、900WPV输出。图9示出具有外部模块旁路二极管的3个PV模块和阻塞二极管连同充电电池的串联连接。在常规晶体太阳能PV模块中,串联和并联连接的模块串通常可使用外部旁路(并且在电池充电电路的情况下还可使用阻塞二极管)。然而,类似于前述实例,由于早前概述的问题或性能约束,这些代表性现有技术PV模块设施遭受装机PV系统的电功率采集限制和降低的能量产量。现有技术实现方式的另一个代表性实例是与主要用于聚光PV(或CPV)应用的前接触(太阳能电池正面上的发射极接触指状物和母线)锗衬底上化合物半导体(III-V)多结太阳能电池一起使用的单片化合物半导体旁路二极管。图10是示出此现有技术单片旁路二极管的实例的图,其中使用起始锗衬底上的化合物多结太阳能电池层(以便为多结太阳能电池层的生长提供相对紧密的晶格匹配)制造前接触多结化合物半导体CPV太阳能电池。此现有技术实例示出在还用于制造用于CPV应用的前接触化合物半导体多结太阳能电池的同一起始锗(Ge)晶片上用作所谓的旁路二极管。在这个实例中,肖特基旁路二极管和化合物半导体(在此现有技术情况下为砷化镓及其三元III-V合金)多结太阳能电池均位于太阳能电池的同一面(顶面)上(其中电接触位于太阳能电池光明面和与光明面相反的背面两者上),并且具有不同的材料层堆叠(即,用于肖特基二极管的沉积和处理的材料堆叠与用于多结太阳能电池的沉积和处理的材料堆叠完全相同),从而使太阳能电池制造工艺更加复杂(由于用于肖特基二极管装置的增加的制造工艺步骤和额外材料层)且昂贵(因此,此类实施方案仅针对其中CPV电池相当昂贵、远比晶体硅太阳能电池以及其它非CPV太阳能电池昂贵的CPV应用来演示)。此现有技术实现方式的另一个限制和潜在制造产量和复杂性问题在于:多结太阳能电池和肖特基二极管的材料堆叠厚度或高度是不同的。这表示实现单片金属化接触和使太阳能电池和肖特基二极管互连的进一步挑战和增加的工艺复杂性。由于此现有技术单片肖特基旁路二极管与昂贵多结太阳能电池位于同一昂贵锗衬底上,所以由于增加的工艺步骤而实质上进一步增加了整体工艺复杂性并且增加了此现有技术多结太阳能电池实施方案的制造成本,同时由于将肖特基旁路二极管与电池的有效光明面集成在同一面上(以及旁路二极管与相对小的有效CPV多结电池面积的相对面积比相当大的事实),导致有效太阳能电池和太阳能模块(和装机CPV系统)效率损少或损失。与前发射极接触化合物半导体多结太阳能电池一起在锗衬底上制成的此单片旁路肖特基二极管实质上在太阳能电池和旁路二极管中需要不同的材料层堆叠,因此,实质上使整个单片太阳能电池和肖特基二极管工艺复杂化,增加太阳能电池制造工艺步骤的数目并且提高其总制造成本。虽然在CPV太阳能电池中,由于所使用的相当高的集中度,制造太阳能电池的此类由于增加的工艺步骤而显著增加的工艺复杂性以及成本增加是可接受的,但是在非高度集中的CPV太阳能电池如在晶体硅太阳能电池中不是经济可行的或实用的。图11是示出已知的单片旁路二极管与多结化合物半导体CPV电池的实例的图。图10中所示的现有技术结构的单片肖特基旁路二极管的所有约束和限制(包括工艺复杂性和成本)还适用于图11中所示的单片旁路二极管。此现有技术实例示出与化合物半导体多结(具有用于多层结构的三元GaAs合金的组合)太阳能电池在同一锗(Ge)衬底上用作单片旁路二极管的pn结二极管(替代肖特基二极管)。在这个实例中,pn结旁路二极管和化合物半导体多结太阳能电池两者均位于太阳能电池的同一面(顶面)上,并且具有不同的材料堆叠(因此,工艺和材料层相对于彼此并不协调),从而使太阳能电池制造工艺更加复杂且昂贵(因此,此类实施方案仅针对其中CPV多结太阳能电池远比非CPV单结太阳能电池昂贵的CPV应用来演示)。在这个现有技术实例中,由于pn结旁路二极管与太阳能电池单片集成在同一昂贵锗衬底上(用于相对晶格匹配的III-V二元和三元化合物半导体层的随后生长),进一步增加了整体制造工艺复杂性和成本,同时由于将旁路二极管与电池的有效光明面集成在同一面上,并且由于CPV太阳能电池和相关联的pn结二极管中所使用的材料堆叠结构不同,导致有效太阳能电池和太阳能模块(和装机PV系统)效率损少。此外,这种将旁路pn结二极管单片集成在前接触化合物半导体多结CPV太阳能电池上在太阳能电池和旁路二极管中需要不同的材料层堆叠,因此实质上使整个单片太阳能电池结构及其制造工艺复杂化,增加太阳能电池制造工艺步骤的数目并且提高其制造成本。虽然制造太阳能电池的此类显著增加的工艺复杂性和成本增加在用于CPV系统的昂贵且复杂的CPV太阳能电池中是可接受的,但是在非CPV(非高度集中的PV)太阳能电池如在更广泛使用的晶体硅太阳能电池和模块中不是经济上可行的。一般来说,虽然对于高度集中的CPV应用而言,如图所示的现有技术的在昂贵锗衬底上将旁路二极管(肖特基二极管或pn结二极管)单片集成在昂贵多结前接触太阳能电池上是所述特定应用可接受的(尽管完全不是低成本解决方案),而不管材料堆叠和工艺步骤之间的额外工艺步骤和协调不足、额外制造成本以及增加的与太阳能电池单片集成的制造工艺复杂性,但是针对昂贵起始衬底上的昂贵化合物半导体多结太阳能电池(具有昂贵MOCVD生长多结化合物半导体材料堆叠)所演示的现有技术方法对于主流平板(非集中的或低度至中度集中的)低成本太阳能PV电池和模块而言太过复杂、昂贵且不可接受。另外,如前所述,因为旁路二极管的单片集成的现有技术方法消耗了相当大的面积部分(除此之外由昂贵太阳能电池使用),所以减小了太阳光吸收的有效面积并且因此由于太阳光吸收面积的损失而降低了有效电池效率。在单片旁路二极管与昂贵化合物半导体多结太阳能电池位于昂贵锗衬底上的现有技术演示中,太阳能电池和旁路二极管的金属化和接触位于装置和衬底的两面、包括衬底的光明面和背面上,从而使太阳能电池和旁路二极管的整体单片互连更复杂且昂贵。发明概述因此,已出现了对以下高效太阳能电池的需要,所述高效太阳能电池包括但不限于:高效晶体硅太阳能电池、以及任何晶体半导体(使用硅和/或其它半导体材料,如基于砷化镓的材料)太阳能电池如包括底板的太阳能电池和/或高效背接触太阳能电池,所述高效太阳能电池具有与每个太阳能电池单片集成的旁路开关,所述旁路开关基于大致上协调的制造工艺流程提供装机PV系统的分布式阴影管理、增加的能量和功率采集以及能量产量提高、以及太阳能电池和PV模块保护,并且由于电池层级旁路开关的这种单片集成而不会增加太阳能电池制造工艺复杂性和成本。根据所公开主题,提供具有至少一个单片集成的电池上电子旁路开关(MIBS)的背接触太阳能电池,所述背接触太阳能电池大致上消除或减少了与先前发展的太阳能光伏电池和模块相关联的缺点和能量产量采集限制,以及已知的单片和非单片旁路二极管实现方式的限制和缺点。根据所公开主题的一方面,提供背接触太阳能电池,所述背接触太阳能电池具有单片集成的电池上功率电子器件,更确切地每太阳能电池有至少一个单片旁路开关,如肖特基二极管(包括但不限于超级势垒肖特基二极管)或pn结二极管或基于晶体管的开关。背接触太阳能电池由半导体吸收衬底(例如,由外延生长形成或来自直拉晶片或来自铸造多晶晶片的晶体硅吸收体)以及底板构成,所述半导体吸收衬底具有光捕获正面和与光捕获正面相反的背面。在双面太阳能电池的情况下,背面也可充当第二光捕获表面。第一指叉型金属化图案(称为M1的第一金属化层)定位在半导体衬底的背面上,并且薄底板片材或材料层(例如由电绝缘刚性或柔性材料制成)被附接(例如层压)到并支撑半导体衬底的背面。用于图案化M1的形成方法包括但不限于:合适的金属堆叠(例如,包括Al、NiV)的物理气相沉积(PVD)和图案化(激光烧蚀或掩膜湿法或干法蚀刻图案化)或通过合适的金属膏(如合适的铝或铝硅合金膏)的直接印刷(如丝网印刷或漏版印刷或喷墨印刷)。第二指叉型金属化图案(称为M2的第二太阳能电池金属化层)设置在底板上(并且通过除预先指定的通孔之外的底板与M1电隔离并分开,导电通孔插塞通过预先指定的通孔互连M1和M2层),并且通过穿过底板的导电通孔的图案化阵列在指明位置处电互连到第一指叉型金属化图案(因此产生图案化两层金属化结构)。至少一个单片集成的电池上电子部件如电子旁路开关(例如,肖特基二极管或旁路二极管或晶体管开关)与制造太阳能电池同时并且使用用于制造太阳能电池的基本上相同的工艺步骤被单片制造在用于制造太阳能电池的同一半导体衬底内,并且作为具有所需极性的并联旁路开关(例如,包括但不限于整流肖特基二极管或pn结二极管)使用图案化太阳能电池金属化结构(M1和/或M2)来电互连到太阳能电池端子(例如,太阳能电池基极和发射极端子)。根据本文所提供的描述将明白所公开主题的这些和其它方面以及额外的新颖特征。本
技术实现要素:的意图并非为所主张主题的全面描述,而是提供对本主题的某些功能性和实施方案的综述。本领域技术人员将在查阅以下图式和详述之后明白此处所提供的其它系统、方法、特征和优点。例如,虽然本发明的代表性实施方案针对用于使用具有指叉型(或指叉型背接触:IBC)金属化结构的薄单晶硅吸收体的背接触/背结太阳能电池来呈现和描述,但是应理解的是,本发明的单片集成旁路开关实施方案(各种结构和工艺方法)和概念可应用于其它太阳能电池吸收材料和用任何合适的半导体吸收材料制成的其它太阳能电池结构,包括但不限于:具有前结/背接触(和非指叉型图案化互连)的那些(具有包括其它半导体材料如GaAs、GaN等的晶体硅或结构);具有前发射极接触和背面基极接触两者的太阳能电池(具有包括其它半导体材料如GaAs、GaN等的晶体硅或结构);由单晶硅之外的材料制成的太阳能电池;使用比此处所述的那些厚的半导体吸收层的太阳能电池;金属化穿孔卷绕(MWT)太阳能电池;PERC和PERL太阳能电池;硅异质结(SHJ)太阳能电池等。这意图在于包括在本说明书内的所有此类额外的系统、方法、特征和优点都是在任何权利要求的范围内。附图简述结合附图(各个尺寸不按比例示出)根据以下陈述的详细描述,所公开主题的特征、性质和优点可变得更明白,在附图中,相同参考数字指示相同特征,并且其中:图1A和图1B是示出太阳能PV电池的等效电路图的电路示意图,包括电流源、具有电池暗电流的整流二极管、寄生有穷串联电阻和寄生有穷分流电阻;图2A是示出理想太阳能电池的简化等效电路模型的示意图(未示出寄生串联电阻或分流电阻),并且图2B是示出太阳能电池在黑暗条件和有太阳光照射条件两种情况下的电流电压(IV)特性的对应I-V曲线图;图3A和图3B是典型的60-电池晶体硅太阳能模块的代表图,其中实例分别以一个被遮蔽电池(3A)和若干被部分遮蔽电池(3B)示出;图4A是示出串联连接的太阳能模块串的未被遮蔽电流通路的图,并且图4B是示出同一串联连接的太阳能模块串的图,其中一个模块被遮蔽并且外部旁路二极管为串联连接的模块串提供替代旁路电流通路;图5是用于包括多个串联连接的太阳能电池的模块子串的外部旁路二极管的示意图,其中太阳能电池以其等效电路图示出;图6是示出晶体太阳能电池在具有和不具有保护旁路二极管情况下的电流电压(I-V)特性的曲线图;图7是示出代表性现有技术60-电池晶体硅PV模块的实例的图,其中在串联连接的太阳能电池的三个不同的20-电池子串上具有三个被遮蔽电池(其中3个外部旁路二极管未示出—每20-电池串联连接的子串1个外部旁路二极管);图8和图9是示出代表性现有技术PV系统设施的两个实例的图,所述PV系统设施包括以并联和串联模块互连方式(图8示出具有旁路模块中的外部二极管)以及全部串联模块互连方式(图9示出具有外部模块旁路二极管)布置的PV模块阵列;图10和图11是示出通过昂贵化合物半导体生长工艺在昂贵锗衬底上产生的化合物半导体(基于GaAs的)旁路二极管(肖特基二极管或pn结二极管)与昂贵多结化合物半导体集中器PV(CPV)太阳能电池的现有技术单片集成的图;基于Ge和GaAs的多结太阳能电池材料堆叠和制造工艺流程与旁路二极管材料堆叠和制造工艺流程不同并且不协调,因此由于添加旁路二极管而造成显著的额外工艺复杂性和制造成本(在这个演示中,在装置的正面和背面两者上形成电池和旁路二极管金属化);图12是突出显示使用外延硅生长的薄晶体硅、背接触/背结晶体硅太阳能电池制造工艺的关键工艺步骤的代表性工艺流程(针对本发明的一个实施方案,此太阳能电池利用具有两层金属化的底板技术)。实施方案可适用于使用此类型的工艺流程以及许多其它电池制造工艺流程的太阳能电池,包括但不限于根据起始单晶晶片(例如,直拉或CZ)或多晶晶片(来自铸造晶体砖)或外延生长衬底或其它衬底制造方法制造的太阳能电池;图13是示出本发明的分布式单元阴影管理系统实施方案的示意图,其中每太阳能电池(太阳能电池以其等效电路图示出)有一个内部(嵌入式)单片制造旁路开关(即,肖特基二极管或pn结二极管或另一种半导体开关如晶体管开关);本发明的实施方案可每电池使用一个内部单片旁路二极管或每多个太阳能电池使用一个内部单片旁路二极管或每单个太阳能电池使用多个内部单片旁路二极管(这里所描述的实施方案针对每太阳能电池单个单片旁路二极管给出,但是要理解,本发明的设计、工艺和概念也可适用于其它以上提及的布置);图14是示出单片集成旁路开关(MIBS)太阳能电池实施方案的光明面视图的图,所述实施方案使用全周边闭环周缘(周边)MIBS旁路二极管,其中由沟槽隔离区域使二极管衬底与主太阳能电池衬底区域分开且电隔离(此类单片配置可通过底板实现);图15是示出MIBS太阳能电池实施方案的光明面视图的图,其中多个全周边闭环MIBS旁路二极管围绕共享连续底板的多个太阳能电池小块或岛(实例示出为NxN阵列的小块或岛,其中N是整数;可使用其它NxM阵列的小块或岛,其中N和M是不同的整数),从而单片形成太阳能电池—使用沟槽隔离区域、使用小块/岛和相关的MIBS旁路二极管之间共享的连续底板来电隔离所有MIBS区域和太阳能电池小块或岛;图16是示出MIBS装置与背接触/背结太阳能电池实施方案(均共享连续底板的MIBS和相关联的太阳能电池)的顶视图的示意图,所述MIBS装置具有全周边闭环(周缘形状)连续pn结二极管,其包括具有相反n型和p型半导体掺杂极性的区域;图17是示出与背接触/背结太阳能电池实施方案相关联的多个MIBS装置的顶视图的图,所述MIBS装置具有使用定位在太阳能电池的周边边缘周围和附近的多个pn结二极管岛的替代几何MIBS二极管图案,其中多个MIBS岛和太阳能电池共享连续底板;图18A和图18B是单片共享连续底板上的MIBS周边周缘二极管和太阳能电池在使用针对太阳能电池和MIBS装置两者协调的工艺流程的太阳能电池(和并发MIBS)装置工艺的不同阶段的横截面示意图;图19A和图19B是详述背接触背结太阳能电池的MIBS周缘二极管(图19A中的pn结二极管MIBS或图19B中的肖特基二极管MIBS)太阳能电池实施方案在完成形成具有单片集成阴影管理的MIBS使能的背接触/背结太阳能电池的制造工艺之后的横截面示意图;图20A和图20B(图20B是图20A的一部分的展开图)是示出MIBS(使用肖特基二极管或pn结二极管)的第一层金属化图案(M1)实施方案的顶视图的示意图,所述实施方案例如使用相对高导电性的铝(或另一种合适的金属或金属合金)金属化(例如,通过PVD、随后进行图案化、铝或铝硅合金或另一种合适的金属膏的直接丝网印刷形成;或通过另一种合适的M1形成方法形成);图21是具有周边MIBS周缘二极管(使用pn结或肖特基二极管)的指叉背接触(IBC)/背结太阳能电池的背面(选项1);本图示出第二层金属(金属2或M2指状物和母线)图案连同多个导电通孔插塞的示意图,所述导电通孔插塞在指明区域处将图案化M2层互连到图案化金属1(M1)层,从而完成太阳能电池以及MIBS周缘电互连(太阳能电池和MIBS周缘二极管尺寸未按比例示出)。M2指状物图案可与M1指状物图案大体上正交或垂直,并且M2指状物的数目实质上可小于M1指状物的数目,即,M1图案是细间距图案并且M2图案是粗间距图案;图22是具有周边MIBS周缘二极管(使用pn结或肖特基二极管)的指叉背接触(IBC)/背结太阳能电池的背面(选项2);本图示出第二层金属(金属2或M2)图案连同导电通孔插塞,所述导电通孔插塞将图案化M2互连到图案化金属1(M1),从而完成电池以及MIBS周缘电互连(太阳能电池和MIBS周缘二极管尺寸未按比例示出)。M2指状物图案可与M1指状物图案大体上正交或垂直,并且M2指状物的数目实质上可小于M1指状物的数目,即,M1图案是细间距图案并且M2图案是粗间距图案;;图23A到图23L是示出相对MIBS二极管和太阳能电池几何布置的各种代表性实施方案的平面(顶面)图的示意图(这些实例以全正方形太阳能电池示出;相同的一般设计可用于使用其它衬底几何结构如准正方形电池衬底的太阳能电池形状)。这些示意图中的尺寸未按实际比例示出。为总太阳能电池加MIBS面积的一部分的MIBS面积被选择为相对较小(以便使被分配给MIBS的不发电面积部分最小化),例如,小于太阳能电池面积的约1%;图24到图31是用于制造背接触/背结单晶硅太阳能电池和相关联MIBS装置的若干代表性太阳能电池制造工艺流程实施方案(这些代表性实施方案以用于所得太阳能电池的薄外延生长硅衬底示出;本发明的MIBS结构和方法可以与其它太阳能电池结合使用,例如包括但不限于使用由线锯从直拉或CZ锭制造的起始单晶硅晶片或由线锯从铸造多晶硅铸砖制造的起始多晶硅晶片制成的背接触太阳能电池);图32是示出MIBS背接触/背结太阳能电池实施方案的平面(顶面)图的示意图,其中MIBS周缘二极管被形成为分段式pn结二极管;图33A和图33B(图33B是图33A的一部分的展开图)是示出利用分段式pn结二极管结构制成的代表性MIBS周缘二极管的太阳能电池第一层金属化图案(金属1或M1)实施方案的顶部示意图的示意图;以及图34A和图34B(图34B是图34A的一部分的展开图)是示出使用pn结二极管MIBS或肖特基二极管MIBS的太阳能电池的仅第一层金属化(M1层)和MIBS/太阳能电池互连图案(M1)的平面(顶面)图的图。详述以下描述并非以限制意义进行,而是出于描述本公开的一般原理的目的进行。本公开的范围应参考权利要求书来确定。本公开的示例性实施方案在附图中示出,相同数字用于指代各个附图的相同和对应部分。而且虽然参考特定实施方案(如使用单晶硅衬底、单晶硅(如外延硅)太阳能电池吸收层和其它所述的制造材料的背接触太阳能电池)描述本公开,但是本领域技术人员可无需过度实验地将本文所讨论的原理应用于基于不同衬底类型和/或太阳能电池结构和/或整体太阳能电池制造方法的其它太阳能电池(包括使用直拉(CZ)单晶硅或铸造多晶硅起始晶片制成的背接触太阳能电池(因此,太阳能电池衬底无需外延硅沉积),其它背接触太阳能电池(如MWT背接触太阳能电池),使用外延硅吸收体或直拉(CZ)硅起始晶片或铸造多晶硅起始晶片制成的前接触太阳能电池)、其它制造材料(包括除了晶体硅之外的各种半导体材料(如晶体砷化镓、氮化镓、锗等))、技术领域和/或实施方案。此外,起始半导体层的掺杂物浓度/分布(例如p型或n型)被称为本底掺杂。因此,虽然针对指叉型背接触(即,IBC)晶体(单晶或多晶)硅太阳能电池来描述本文的实施方案,但是应理解,所公开的发明方面可适用于更广泛范围的太阳能电池架构(例如,金属穿孔卷绕或MWT背接触太阳能电池、前接触太阳能电池、双面太阳能电池等)和材料(例如,除晶体硅之外,GaAs、Ge等)。如上所述,已知的晶体硅(或其它基于电池的)PV系统中的在存在遮蔽时提供可靠模块操作的现有技术太阳能电池保护和太阳能模块阴影引起的热点预防解决方案常常是基于利用以下之一或其组合:分开或离散旁路二极管,在PV模块中最常见地是每一串联连接的太阳能电池子串(例如,在60-电池或72-电池PV模块中,每子串分别有20个或24个电池)有一个外部离散旁路二极管(通常被放置且电连线在光伏模块接线盒中)(通常每晶体硅PV模块有三个外部旁路二极管被放置在外部模块接线盒中,以便为模块中的所有太阳能电池提供阴影引起的热点保护);此外,可使用连接到PV模块的外部微逆变器(DC到AC)或可替代地DC到DC转换器在模块层级提供最大功率点跟踪(MPPT);和/或在被封装在模块内的电池之间使用所谓的可编程互连技术,以便增加基于电池的PV模块的能量产量。虽然现有技术旁路二极管用于保护被遮蔽电池、预防热点并且防止由于热点和被遮蔽(或被部分遮蔽)的反向偏压电池造成的模块故障,但是由于存在模块遮蔽或污染时的模块功率提取损失,现有技术旁路二极管还可在现实现场操作中导致显著的能量采集降级或能量产量减小(在指定现场操作持续时间(如以年为基础)内,每KWp装机PV模块所采集的能量,以kWh为单位)。例如,假定标准60-电池PV模块设计,单个被遮蔽电池可造成约1/3(或33.33%)的模块功率的损失(接线盒中的现有技术外部旁路二极管将绕过含有被遮蔽电池的整个20-电池子串,以便防止电池的反向偏压),而在现场的正常无遮蔽模块操作条件期间,单个电池通常仅占总模块功率的约1/60(对于典型的60-电池PV模块而言)。类似地,在具有三个被遮蔽电池的情况下并且假定60-电池PV模块中每20-电池子串有一个被遮蔽电池(图7中示出其实例),所有三个外部旁路二极管被启动并且从模块提取的功率降为零(或模块功率的100%损失),而在正常无遮蔽操作条件期间这三个被遮蔽电池仅占模块功率的3/60(或1/20)。相比之下,本文所公开的本发明的分布式单片阴影管理解决方案使用单片集成旁路开关(MIBS)提供具有增加的PV模块功率采集的智能PV电池和智能PV模块并且增加能量产量,所述单片集成旁路开关可以与每个太阳能电池同时制造并且单片集成(因此消除了对具有外部离散旁路二极管的外部接线盒的需要),而在制造太阳能电池时基本上不会递增地增加制造成本。本文所公开的MIBS结构和实现方法还被设计用于增加整体太阳能电池模块可靠性并且延长操作寿命以及其它相关联的益处。另外,所公开系统和方法实现智能PV电池和智能PV模块,它们能够集成额外的分布式电池层级(单元)功率电子器件,从而提供引人注目的PV系统成本和平准化电力成本(LCOE)降低(支持<$1/W装机PV系统成本)以及就能量产量而言的性能改进(实现小于约$0.10/kWh并且甚至小于约$0.06/kWh平准化电力成本或LCOE,这取决于PV安装地点和操作条件的特性)。本发明的实施方案的重要应用包括用于以下各项的电池和模块:住宅屋顶、住宅和商业建筑物中的光伏建筑一体化(BIPV)、商业屋顶、地面安装型公共事业规模的发电厂、汽车、便携式电子设备、便携式和可运送发电应用以及其它专业应用。如前所述,晶体硅光伏(PV)模块目前所占比例高于整个全球PV市场的近似85%。这些晶体硅PV模块的硅晶片材料成本目前构成总晶体硅PV模块制造成本的近似30%到50%。图12是突出显示基于外延硅/多孔硅的薄晶体硅背接触/背结(也称为指叉型背接触或IBC)太阳能电池制造工艺的关键工艺步骤的代表性工艺流程,所述制造工艺显著减少了硅使用并且消除了若干传统制造步骤,从而创造低成本、高效率、背结/背接触单晶电池。具体来说,此工艺流程使用可再用模板和多孔硅的释放层上的外延硅沉积来生产具有用于智能电池和智能模块的层压底板(所述底板可以是附接到太阳能电池背面,并实现具有电池上M1和底板上M2金属化的两层金属化结构的相对较薄(如厚度为约50微米到200微米)、薄柔性或刚性电绝缘片材)的高效太阳能电池。在本发明中,智能电池被描述为具有与其相关联的至少一个单片旁路开关的太阳能电池。本文所述的智能电池包括单片集成旁路开关(MIBS),所述MIBS在太阳能电池工艺期间使用协调的制造工艺流程同时制造(即,MIBS装置与太阳能电池同时制造并且使用用于太阳能电池的相同制造工艺步骤来制造,从而基本上不会增加增量制造成本)。虽然此处的代表性工艺流程(如图13中概述的工艺流程)是基于外延硅和多孔硅剥离工艺以形成太阳能电池半导体吸收层来示出,但是本发明的实施方案还完全适用于使用底板支撑片材、甚至无需使用多孔硅或外延硅工艺(例如,通过使用用来制造太阳能电池的起始半导体晶片)的任何晶体半导体太阳能电池(包括由单晶直拉-CZ-硅起始晶片或单晶浮区-FZ-硅起始晶片或铸造多晶起始晶片或GaAs晶片或由起始线锯晶片或由具有不同半导体材料的外延生长层形成的另一种半导体材料制成的那些太阳能电池)。底板支撑片材可以是具有匹配半导体衬底的热膨胀系数(CTE)的相对良好热膨胀系数的薄柔性片材,例如为合适的预浸材料(如使用织造芳族聚酸胺纤维和合适树脂的组合制成的预浸材料)的50微米到250微米厚的片材。可替代地,在背接触/背结(或也称为IBC)太阳能电池的情况下,底板材料可以由其它合适的柔性(例如,聚合物或塑料)或刚性电绝缘材料制成。底板可以是连续片材,所述连续片材被永久地附接或层压到半导体衬底并且提供若干重要功能,包括:(i)为薄(例如,厚度为几微米一直到超过100微米)半导体衬底提供支撑;(ii)在使用柔性底板结合薄(例如,小于100微米)半导体吸收体的情况下允许制造可弯曲/柔性太阳能电池;(iii)允许制造双层太阳能电池(和MIBS)金属化结构,从而产生显著的架构和性能益处;(iv)允许在半导体层与用作可靠单片支撑层的连续底板中形成沟槽隔离区域;并且(v)允许形成不具有母线的电池上金属涂层(第一层金属或M1),因此消除太阳能电池的电阴影损失;以及(vi)允许形成具有相对粗的(因此,容易制造)金属化间距(与M1相比)并且具有用于PV模块中的电池到电池互连的最终太阳能电池母线的底板上金属涂层(第二层金或M2)。图12中所示的代表性工艺流程以通常由p型(如重掺硼单晶硅晶片)制成的可再用晶体(单晶或多晶)硅模板开始,多孔硅的牺牲层形成到所述硅模板中(例如通过在存在穿过晶片的电流时以HF/IPA或HF/乙酸湿化学法进行表面改性方法来进行电化学蚀刻工艺)。多孔硅层可具有至少两种不同孔隙率:较高孔隙率埋层(用作随后的剥离释放层)和较低孔隙率表层(用作随后的外延种层)。在形成牺牲多孔硅层之后(其用作高质量外延种层以及随后的分开/剥离(或释放)层),形成相对薄的原位掺杂晶体硅层(例如层厚度在几微米一直到约100微米范围内,或更具体来说在几微米一直到约70微米的范围内),其也称为外延硅生长。原位掺杂晶体硅层可例如通过使用化学气相沉积或CVD工艺的大气压外延(也称为APCVD)在包括合适的硅源气体如三氯硅烷或TCS和氢(加合适的掺杂源如磷化氢或PH3)的工艺环境中形成。外延层可以由n型掺杂形成,以便制造较高效太阳能电池(与p型硅相比,n型衬底提供较高少数载流子寿命并且不会遭受B-O配对缺陷,所述配对缺陷导致使用p型硅衬底制成的太阳能电池中的光致衰退)。在完成大部分太阳能电池工艺步骤(例如,背面掺杂的发射极和基极区域、后钝化结构、后基极和发射极接触以及具有细间距指叉型指状物的图案化电池上无母线M1金属化层,所述金属化层由合适的金属化材料如铝或铝硅合金制成)之后,可将相对便宜的底板层(如具有匹配硅的CTE的相对接近的CTE的50微米到250微米厚的柔性预浸材料层)粘结或层压到薄外延硅层以用于永久电池支撑和加固并且允许太阳能电池的两层电池金属化架构。底板材料可由薄(例如,约50微米到250微米)的、柔性的(或如果需要,刚性的)且电绝缘材料片材制成,所述材料片材如通常用于应用如印刷电路板的便宜的柔性预浸材料(具有匹配半导体衬底如芳族聚酰胺纤维的CTE的相对接近的CTE),所述材料满足太阳能电池和PV模块的工艺集成和可靠性要求。除了预浸材料,其它合适的聚合物或塑料材料可用作太阳能电池和MIBS底板材料(柔性或半柔性或刚性的)。随后沿机械弱化的牺牲多孔硅层将工艺已完成大部分(进行了图案化M1层工艺并且与连续底板片材层压)的背接触、背结底板加固的大面积(例如,为至少125mmx125mm或更大的太阳能电池面积、如为至少156mmx156mm全正方形或准正方形格式的尺寸)太阳能电池从可再用模板分开并剥离(例如通过机械释放-MR-工艺),而模板可以再使用很多次(例如,至少几次,并且在一些实例中至少数十次),以进一步最小化总太阳能电池和PV模块制造成本。随后可首先在从模板释放之后暴露的太阳能电池光明面上执行最后的后期电池工艺(包括完成光明面纹理化、钝化和抗反射涂层或ARC沉积,然后是完成通孔插塞和第二层金属化或M2)。光明面工艺可包括:例如,完成正面纹理化(例如,使用碱性或酸性湿化学)和表面钝化和抗反射涂层(ARC)沉积(例如,使用包含由PECVD或ALD和PECVD形成的SiNxHy或SiOwHz/SiNxHy或Al2O3/SiNxHy的钝化和ARC层或层堆叠)工艺。可使用利用起始CZ或FZ或多晶硅晶片(代替使用可再用衬底上的多孔硅和外延生长)的工艺来制造上述IBC电池(将不需要图12左侧所示的前3个块或步骤,并且替代地使用起始晶体硅晶片进行如图12中的前三个步骤的右侧所示的太阳能电池制造工艺)。本申请的MIBS实现方法和设计可整合到所公开的太阳能电池制造工艺流程(以及许多其它晶体硅太阳能电池工艺流程,包括但不限于使用线锯起始晶片或外延生长的太阳能电池衬底的那些)中,而不会显著改变或添加制造工艺步骤或手段,并且因此不会显著增加制造太阳能电池的成本。在一个实施方案中,背结/背接触(或IBC)电池设计结合底板实现的两层互连和底板实现的太阳能电池支撑的组合提供在电池层级实现单片集成旁路开关(MIBS)的使能太阳能电池架构,因此消除了结合模块接线盒或结合每个电池使用离散部件(如离散二极管)的需要。除了用作永久性结构支撑/加固并且提供用于高效晶体半导体太阳能电池的底板实现的低成本/高导电性(例如,使用铝和/或铜和/或它们的合金或其它合适的高导电性金属化材料)互连之外,这些底板技术还允许与每个太阳能电池的有效MIBS集成,而不会显著危急太阳能电池功率(因为MIBS面积是太阳能电池面积的很小部分)并且具有可忽略的或无总太阳能电池制造成本增加。本发明的实施方案通过消除现有技术离散旁路二极管的可靠性顾虑和部件成本(还消除了将离散部件焊接或附接到太阳能电池或模块接线盒的需要)来使得使用MIBS的非常经济且可靠的集成阴影管理解决方案成为可能。所述实施方案还提供类似于太阳能电池自身可靠性的极好可靠性(这归因于MIBS和太阳能电池的单片集成和它们使用协调的制造工艺和材料的事实)。底板材料可以是合适材料(例如柔性材料如预浸片材或聚合物或塑料材料)的薄(例如,约50微米到250微米厚;也可以比这个范围更薄或更厚)片材,所述材料具有匹配半导体衬底的热膨胀系数(CTE)的足够接近的CTE,以便避免在薄半导体(例如,晶体硅)层上产生过热引起的CTE失配应力。此外,底板材料应满足后期电池制造工艺的工艺集成要求,具体地包括太阳能电池正面的湿法蚀刻/纹理化期间的耐化学性和随后的正面(单层或多层)钝化和ARC层的PECVD沉积期间的足够的热稳定性。附接到薄半导体衬底的电绝缘底板材料片材还应满足随后的模块级层压工艺热预算和长期现场操作稳定性要求。虽然各种合适的聚合物(如塑料、含氟聚合物、预浸材料等)和合适的非聚合物材料(如玻璃、陶瓷等)可用作底板材料(柔性或刚性底板),但是底板材料选择取决于许多考虑因素,包括但不限于:成本、太阳能电池工艺集成的容易性、长期可靠性、热稳定性、柔性、韧性等。底板的良好材料选择是包含纤维和树脂的合适组合的预浸材料。预浸片材用于许多应用如列印电路板(PCB)的构建块并且可由合适树脂和热膨胀系数或CTE降低的纤维(如芳族聚酰胺纤维)或颗粒的组合制成。底板材料片材可以是便宜的、低CTE(通常CTE<10ppm/℃,或在一些实例中CTE<5ppm/℃,因为半导体材料如晶体硅具有大约3ppm/℃的相对低的CTE值)、薄(通常在约50微米到250微米范围内,并且在一些实例中在约50微米到100微米的更小范围内,以便降低底板片材成本并且加强底板层压的太阳能电池的柔性)预浸片材,所述预浸片材对湿法蚀刻/纹理化化学品(如碱性或酸性纹理化化学成分)具有相对化学耐受性并且在高达至少约180℃(或甚至一直到高约400℃-450℃)的温度下为相对热稳定的。在使用模板上的多孔硅上的外延硅沉积制成的晶体硅太阳能电池的情况下,可在通过图案化M1金属化层(太阳能电池背面上的第一层金属)完成太阳能电池制造工艺之后,在电池半导体衬底仍然位于模板上(即,在太阳能电池衬底剥离工艺之前)时使用真空热层压机将预浸片材附接到太阳能电池衬底背面。可替代地,在使用起始CZ单晶或FZ单晶或铸造多晶晶片(并且不使用模板上的多孔硅上的外延硅沉积)制成的晶体硅太阳能电池的情况下,可在通过图案化M1金属化层(太阳能电池背面上的第一层金属)完成太阳能电池制造工艺之后并且在完成后期工艺步骤(如光明面纹理化、钝化和ARC以及穿过底板的导电通孔插塞和形成于底板上的第二层金属化层或M2)之前,将预浸片材附接到太阳能电池晶片背面。在施加热量(例如,温度高达约200℃到300℃)和压力(例如,压力高达几大气压到约20大气压)的组合后,薄预浸片材被永久地层压或附接到工艺已部分完成的背接触太阳能电池的背面。在使用模板上的多孔硅上的外延硅沉积制成的晶体硅太阳能电池的情况下,通过例如使用脉冲激光划线手段在太阳能电池的周边周围(靠近基于一些预先指定的无管芯区的模板边缘)限定剥离释放周边边界,并且随后使用机械释放或剥离工艺将底板层压的太阳能电池衬底从可再用模板分开并剥离。随后可根据最终指定的太阳能电池尺寸围绕边缘任选地激光修整所释放的底板附接的太阳能电池,以便制备最终的笔直太阳能电池周边边缘。可替代地,在使用起始CZ单晶或FZ单晶或铸造多晶晶片(并且不使用模板上的多孔硅上的外延硅沉积)制成的晶体硅太阳能电池的情况下,无释放工艺并且任选的后层压激光修整工艺可用来移除从太阳能电池(和MIBS)的有效边缘延伸的任何过量预浸材料。随后的工艺步骤(在外延电池的情况下或在基于CZ/FZ/多晶硅晶片的电池的情况下)可包括:(i)在太阳能电池光明面上完成正面纹理化和钝化/ARC工艺;(ii)在电池背面(其是太阳能电池底板)上完成太阳能电池高导电性金属化(第二层金属化或M2可与相关联的M1-M2导电插塞结合形成,其中金属化材料包括铝和/或铜和/或它们的合金或其它合适的金属材料)。使用图案化M2层在层压的太阳能电池底板上形成包括与太阳能电池发射极和基极极性(指状物和母线)的互连的高导电性金属化(例如,包含与银相比相当便宜的铝和/或铜,以减少总太阳能电池材料和制造成本)。在本发明的背接触太阳能电池和MIBS实施方案中,本文所述的太阳能电池设计和制造工艺具有两个金属化层(电池上的M1或第一金属化层和底板上的M2或第二金属化层),所述金属化层由电绝缘底板层分开并且通过导电性通孔插塞根据预先指定的通孔图案互连,所述通孔插塞基于预定互连布置使图案化的M2和M1金属化区域互连。就使用本发明的实施方案的IBC电池而言,M1图案可以是指叉型基极和发射极金属化指状物的相对细间距图案(在M1上无任何母线,以便消除电阴影衰退对太阳能电池效率的影响),而M2图案可以是指叉型基极和发射极金属化指状物的相对粗间距图案,其中M2指状物与M1指状物大体上正交或垂直,并且M2指状物计数大致上小于M1指状物计数(例如,小了约5到50倍)。在底板层压工艺之前,通过例如使用相对薄(具有约几分之一微米一直到约20微米的厚度;通常为由PVD形成的较薄层和由丝网印刷形成的较厚层)层的丝网印刷层或等离子体溅射(PVD)的铝(或铝硅合金)材料层直接在电池背面(M1金属化层)上形成太阳能电池基极和发射极接触金属化图案。在底板附接或层压工艺之前在太阳能电池后面或背面上形成的此第一金属化层(本文称为M1)限定太阳能电池接触金属化图案,如限定IBC电池的基极区域和发射极区域的细间距(例如,近似约0.5毫米一直到几毫米的基极和发射极金属化指状物间距)指叉型背接触(IBC)M1导体指状物。在一些实例中,图案化M1层不具有任何太阳能电池母线,以便消除与太阳能电池金属化母线相关联的任何不利电阴影损失。M1层(也称为太阳能电池接触金属化)提取太阳能电池电流和电压(或太阳能电池电功率)并且将太阳能电池电功率传输到在底板表面上的M1之后形成(并且通过层压或附接的底板片材与图案化M1层物理分开)的第二相对较高导电性太阳能电池金属化层(level)/层(本文称为M2)。在接着形成图案化M1层将底板片材附接或层压到太阳能电池背面之后,并且外延硅太阳能电池的情况下在随后将底板支撑的太阳能电池从模板拆离之后(如果在CZ或FZ单晶硅晶片上或在铸造多晶硅晶片上制造太阳能电池,不适用),并且在完成正面纹理化和钝化和ARC形成制造工艺之后,穿过底板片材形成通孔(着落在图案化的M1层上的指明垫上的孔)并且在底板上形成相对较高片材电导层M2(例如,使用包括铝和/或铜的相对便宜的高导电性金属或金属合金)。通孔(在一些实例中,在连续底板区域内多达数百或数千通孔)被钻入到底板中(例如,通过脉冲激光钻孔工艺)。这些通孔着落在图案化M1指状物(太阳能电池基极和发射极金属指状物)的预先指定的区域上,以用于随后的通过形成于这些通孔中的导电插塞进行的图案化M2与M1层之间的电互连。随后,形成图案化较高导电性金属化层M2(例如通过等离子体溅射、电化学沉积或电镀、将金属箔附接到底板或其组合—使用M2材料,例如包括铝和/或铜的相对便宜且高导电性的导电体)。对于在M1上具有细间距IBC指状物(例如,每IBC太阳能电池数百个M1金属指状物)的指叉型背接触(IBC)太阳能电池而言,图案化M2层可以被设计并且制造成使得其导体指状物与M1大体上正交或垂直—即,M2基极和发射极指状物被制成与M1基极和发射极指状物基本上垂直。M2指状物在基极与发射极极性之间交替并且连接到形成为M2层的一部分的相应基极和发射极母线。因为M2相对于M1的这种正交变换,M2层与M1层相比可具有少得多的IBC指状物(例如,M2指状物与M1指状物相比为少了约5到50倍)。因此,与M1层相比,M2层可具有带有宽得多的M2IBC指状物的更粗糙图案。例如,M2指状物的平均宽度可以是若干毫米到超过1厘米,而M1指状物的平均宽度可以是数百微米一直到超过1毫米。太阳能电池母线可以定位在M2层上而非定位在M1层上,以便消除与太阳能电池上的母线相关联的电阴影损失。而且,因为基极和发射极互连和母线均可定位在太阳能电池背面底板上的M2层上,可在底板上对太阳能电池的基极端子和发射极端子两者提供电接入。图案化M2层还形成导电通孔插塞(例如,使用用于图案化M2层指状物和母线的同一沉积金属层)。使用MIBS的智能单元阴影影响抑制(ISIS)或集成阴影管理。通常,由于PV模块内的太阳能电池的串联布线和互连,PV模块光吸收面上的少量遮挡可能造成大的输出损失。当考虑到包括以电串联和并联布置连接的PV模块阵列的装机PV系统时同样如此。由于电池和模块遮蔽(部分或完全遮蔽)所造成的功率采集能力损失的实例包括下列项。例如,确定以下内容的一项已经发表的研究:PV模块表面积的0.15%、2.6%和11.1%上的遮挡可分别造成3.7%、16.7%和36.5%的输出功率损失,因此在甚至部分遮蔽的情况下也显著降低装机PV系统能量产量。如前所述,当一个被遮住电池的电流由于所述电池的部分或完全遮蔽而下降时,被遮蔽电池可拉低串或子串中串联连线的所有其它电池的电流,或可替代地被遮蔽太阳能电池可由未被遮蔽电池所产生的较大电流反向偏压,从而在被遮蔽电池区域处造成热点和可靠性问题,除非在PV模块的设计和构建中采取校正行动。本文所公开的基于MIBS的ISIS或阴影管理设计单片集成旁路开关(pn结二极管或肖特基二极管—或可替代地另一种半导体开关,如合适的晶体管开关)以允许电力任何被遮住或被遮蔽电池周围的电力自动重选路径(或绕过)以对串联串和PV模块具有最小影响—从而使PV模块的发电能力和PV模块的总能量产量输出最大化—而无需显著地改变太阳能电池制造工艺流程(因此是所谓的协调的工艺流程)并且对总太阳能电池制造成本具有可忽略的或零增加。本发明所述的基于MIBS的ISIS或阴影管理结构和方法通过显著缓解来自与PV模块内的失配电流相关联的热量耗散的任何热引起的应力;所述结构和方法还消除了对具有外部旁路二极管的模块接线盒的需要并且消除了对任何离散旁路开关部件的需要,由此减小了所得智能PV模块的每瓦特成本;并且所述结构和方法还消除了与将离散旁路二极管部件安装和焊接在太阳能电池上相关联的热应力和机械应力。使用与太阳能电池单片集成的旁路开关(MIBS)的智能单元阴影影响抑制(ISIS)或阴影管理解决方案:以下部分描述本发明的各种阴影管理MIBS实现实施方案。作为代表性实例,关于对用于所公开的分布式单元阴影管理(ISIS)系统、在分布式开关中没有显著功率耗散损耗的MIBS导通电阻的选择的考虑因素和标准包括但不限于:-单元旁路开关具有小的导通状态电压降,在一些实例中远小于正向偏置二极管的电压降。例如,假定Vmp=575Mv(最大功率点电压)并且Imp=9.00A(最大功率点电流)(对应于近似Voc=660mV的开路电压和约ISC=9.75A的短路电流),50mV的导通状态电压会造成0.45W的导通状态功率耗散,所述功率耗散小于二极管的功率耗散的约10%(此计算不包括与开关串联电阻R串联相关联的任何损耗)。-单元旁路开关具有很小的导通状态串联电阻以使导通状态开关功率耗散最小化,如导通状态开关R串联小于或等于10mΩ(例如,R串联=5mΩ,开关的欧姆功率耗散=0.405W)。-MIBS可使用具有~0.2V到~0.5V的导通状态或正向偏压的低正向偏压肖特基二极管,或可替代地具有~0.6V到~0.7V的导通状态正向偏压的pn结二极管。与pn结二极管相比,使用最佳肖特基二极管可在MIBS开关由于电池遮蔽而启动时造成较低的功率耗散。可使用具有以下功能性的MIBS结构:-MIBS由于电池遮蔽而导通(MIBS二极管正向偏置)时的低功率耗散。例如,由于其欧姆损耗造成的MIBS功率耗散可以被限制到大约不大于平均电池发电量,并且在一些实例中被限制到平均太阳能电池发电量的一部分。例如,对于5Wp(瓦峰值)太阳能电池而言,MIBS装置设计(如肖特基二极管或pn结二极管)可在以下情况时将太阳能电池串联连接串中的被遮蔽电池中的功率耗散限制到不超过约2W一直到约5W:全电池串电流通过被遮蔽电池MIBS装置(由于肖特基二极管与pn结二极管相比较低的正向偏压,与pn结MIBS相比利用肖特基二极管MIBS有更低的功率耗散)。MIBS二极管被设计用于提供很低的导通电阻,以便在MIBS装置启动时使MIBS功率耗散最小化。-以下情况时的MIBS装置中的相对低的反向漏电流:太阳能电池MIBS截止(反向偏置)或电池未被遮蔽并且在正常的未被遮蔽条件下操作。例如,MIBS装置可以被设计成使得其反向漏电流实质上低于太阳能电池光生电流的1%或甚至低于0.1%。图13是示出在PV模块内每太阳能电池使用一个低功率耗散MIBS装置(例如,包括肖特基二极管或pn结二极管的每个MIBS装置)的分布式单元阴影管理(智能单元阴影影响抑制—ISIS)的示意性电路图。与每多电池子串布置有一个旁路二极管(如在60-电池模块中每20-电池子串布置使用一个旁路二极管时,如在现有技术配置中)相比,这种分布式MIBS(使用pn结二极管或肖特基二极管作为MIBS装置)布置消除了对外部接线盒旁路二极管以及任何离散电池上二极管部件(因此,需要将离散二极管焊接或导电粘合剂附接到太阳能电池,从而导致潜在的现场的可靠性问题)的需要,并且提高了PV设施中的模块的整体能量产量性能。如图所示,因为每太阳能电池使用一个MIBS(整流二极管如肖特基二极管或pn结二极管),整个模块可以被连线为具有模块内的所有太阳能电池、例如电串联连接的所有太阳能电池的单个串(例如,对于60-电池模块,具有串联连接的60个电池的一个串)。可替代地,取决于模块电流和电压要求,模块中的太阳能电池可以串联/并联互连布置的任何组合连线。因此,使用本文所公开的基于MIBS的ISIS或阴影管理架构和制造方法确实简化了模块制造工艺并且降低了模块材料清单(BOM)成本,同时提供了高功率输出性能和现场可靠性。用于PV模块中分布式阴影管理的单片集成旁路开关(MIBS)。本文描述具有单片集成阴影管理解决方案、从而消除了对外部旁路开关和离散旁路开关部件的需要的智能太阳能电池的各种实例。例如并且除其它益处之外,MIBS结构和方法提供以下优点:-单片集成旁路开关(MIBS)可在每个电池上实施,而对电池制造成本具有基本上零增量制造成本(即,因为MIBS与每个太阳能电池一起实现,每电池的制造成本具有可忽略的或零增加)。-与包括PV模块接线盒中的外部离散旁路二极管的传统PV模块相比,MIBS使能的太阳能电池直接在电池层级提供分布式阴影管理,以获得PV模块中的增强的能量产量和增强的能量采集。-在多个制造实施方案(包括本文所述的那些)中,制造MIBS使能的太阳能电池可基本上不添加额外的电池/模块制造成本,并且在提供在模块的环境遮蔽和/或污染的现实现场条件下(例如,在住宅屋顶PV设施上)操作的PV模块的显著增强的能量采集和较高能量产量的同时,可引发可忽略的电池效率/功率损少。-利用MIBS的本发明的单片集成解决方案和工艺是针对具有附接或层压的底板支撑件的相对薄(例如,半导体吸收体或衬底厚度在几微米一直到超过100微米的厚度范围内)的半导体(例如,薄外延硅衬底或薄晶体硅晶片)太阳能电池来提供,基本上不改变太阳能电池工艺流程(因此是协调的制造工艺流程),基本上不增加太阳能电池工艺复杂性并且基本上不增加太阳能电池工艺成本。此外,本文所述的MIBS实施方案可与太阳能电池本身使用相同的材料堆叠层(半导体、电介质和金属层)—因此可使用用于太阳能电池制造的相同工艺手段同时并且以协调的方式来执行太阳能电池和与太阳能电池相关联的MIBS装置的制造工艺。-提供了用于使用pn结二极管或金属电极肖特基二极管的MIBS电池的示例性单片集成解决方案,所述解决方案消除了对离散旁路开关部件和它们到太阳能电池的附接的需要。-提供了低成本和可靠的集成阴影管理解决方案,所述解决方案消除了离散二极管部件的可靠性顾虑和部件成本(并且还消除了对将离散开关部件焊接或通过导电粘合剂附接到太阳能电池的需要)。-因为所公开的MIBS方法和结构与太阳能电池利用相同材料,它们具有与太阳能电池本身相同的极好的长期可靠性。MIBS及其相关联的太阳能电池根据需要使用太阳能电池金属化结构、例如M1层和/或M2层来互连。-因为不存在附接到太阳能电池的离散焊接的旁路二极管部件并且周边MIBS装置可充当太阳能电池的微裂纹防护罩或防护装置,所公开的MIBS方法和结构还可允许减轻薄半导体微裂纹(微裂纹产生和/或蔓延)。例如,MIBS太阳能电池的关键属性和益处包括但不限于:-一般来说,本文所公开的MIBS实施方案可以应用于各种基于电池的PV模块,并且特别是晶体半导体太阳能电池,包括薄(例如,约1μm一直到约100μm厚或甚至更厚的半导体吸收体)晶体半导体(例如,硅和砷化镓)太阳能电池。-本文所公开的MIBS实施方案提供用于产生相对薄的晶体半导体(如薄晶体硅)太阳能电池(其中每个太阳能电池上具有至少一个相对低功率耗散单片集成旁路开关(MIBS))的结构和制造方法,所述结构和制造方法在由多个MIBS使能的太阳能电池制成的PV模块中提供可靠的电池层级阴影管理。-本文所公开的结构和方法是针对使用薄(例如,约1微米一直到约100微米或甚至更厚)外延硅剥离工艺制造的或可替代地使用起始晶体硅晶片(CZ或FZ或多晶硅晶片)制造的并且包括层压或附接的底板支撑件的高效背接触/背结(也称为IBC)太阳能电池来描述。然而,所公开主题的结构和方法还可适用于不同于晶体硅的半导体吸收材料(例如,砷化镓、锗、氮化镓等)以及其它太阳能电池设计(例如,前接触电池或其它背接触非IBC电池)制成的太阳能电池。-本文所公开的MIBS太阳能电池实施方案可以通过薄(半导体电池吸收体厚度小于约200微米并且在一些实例中小于约100微米)半导体吸收体和太阳能电池背面上的永久层压或附接的连续底板支撑层的组合来制造和实现。-MIBS太阳能电池可在太阳能电池的周边周缘上具有单片集成旁路开关(pn结二极管或肖特基二极管),所述开关在太阳能电池制造工艺流程期间形成而不会对电池制造工艺增加任何可感知的增量成本并且不会危急电池功率输出,因为MIBS装置面积消耗仅为有效太阳能电池面积的相对小的一部分(例如,MIBS面积可被选择成小于太阳能电池面积的约1%,并且甚至小于百分之一的一部分,例如约0.1%一直到1%)。-对于多边形太阳能电池而言,周边周缘(边缘定位的)旁路开关二极管可以被形成在多边形面中的任一个上或多个多边形面上或沿所有多边形面连续地被形成。对于相对常见的正方形太阳能电池格式(例如,具有156mmx156mm、210mmx210mm的典型尺寸,或任何其它需要的太阳能电池尺寸,例如电池面积在小于约100cm2到超过1,000cm2范围内的太阳能电池)而言,周边周缘二极管(pn结二极管或肖特基二极管)可以被形成在太阳能电池周边的至少一部分上(在至少一面或拐角或一面的至少一部分或一个拐角的一部分、或其组合上),或被形成为连续闭环(或连续分段式闭环)全周边周缘,所述全周边周缘在太阳能电池的周边周围环绕整个太阳能电池,从而形成由小得多的区域岛周缘封闭的较大太阳能电池岛区域,两者均被支撑在连续底板上(如图14中所示)。-MIBS旁路二极管和太阳能电池共享同一共用连续底板,并且使用在电池制造工艺期间执行的沟槽隔离工艺将它们的半导体层(例如,外延硅或由CZ或FZ或多晶体晶片制成的半导体衬底)与彼此完全隔离,例如通过使用贯穿半导体的脉冲激光划线来形成装置隔离沟槽。隔离沟槽可穿透半导体层(例如,薄外延Si)的整个厚度并且在电绝缘底板上停止。沟槽隔离的宽度取决于用于隔离划线的激光束(例如,纳秒脉冲激光束)的性质以及半导体层厚度,并且半导体层厚度可以是在例如约1微米一直到约100微米甚至更大的范围内(可形成较窄的沟槽,以便减小面积相关的损失)。一般而言,较窄的沟槽隔离宽度可以是有利的。实际上,沟槽隔离宽度可以是大约数十微米。可替代地,沟槽隔离区域可以通过使用不同于脉冲激光划线的技术来形成,例如通过机械分割或超声波划线或另一种方法来形成。合适的沟槽隔离形成工艺如脉冲激光划线或切割工艺选择性地切穿半导体层,并且在切穿半导体衬底的厚度之后有效地在底板片材上停止而不会显著地移除底板材料(因此,维持了连续底板片材的完整性)。此外,使用共享的制造工艺流程与太阳能电池同时制造的单片集成旁路开关(MIBS)除其它之外可提供以下优点:-可制造集成旁路开关而对太阳能电池或PV模块添加可忽略或基本上零增量制造成本。-消除了对将离散旁路开关附接到太阳能电池或太阳能电池底板的需要。-解决了将离散部件如离散二极管附接(例如,焊接)到太阳能电池并且永久地将此类电池与所附接的离散部件层压在太阳能模块中的潜在可靠性顾虑。-因为不存在离散部件凸起,维持了太阳能电池与单片集成旁路开关的整体平面性;并且消除了对使用较厚模块密封材料(如EVA或聚烯烃)以适应离散部件形貌和凸起的需要。-消除了离散旁路开关(例如,二极管或晶体管)和/或具有外部旁路二极管的外部接线盒的成本。-消除了在太阳能电池上进行离散旁路开关部件组装工艺(例如,部件焊接)的成本。与太阳能电池本身相比,MIBS太阳能电池可具有实质上相同的可靠性,因为MIBS结构可以由相同的太阳能电池材料和工艺(半导体衬底、电介质、金属化和底板材料)制成并且与太阳能电池单片集成。因为未危急太阳能电池和PV模块的整体可靠性(由于使用稳健的单片旁路二极管代替被焊接到电池的离散部件),这使银行可贴现性问题和顾虑最小化。单片集成旁路开关(MIBS)可以是pn结二极管,如在太阳能电池岛周围的周缘pn结二极管。可替代地,MIBS可以是金属接触肖特基二极管(与pn结二极管相比,其通常可提供较小的正向偏压),如在太阳能电池岛周围的由例如n型硅上的铝或铝硅合金肖特基接触制成的周缘肖特基二极管。如果利用周缘二极管设计,那么单片集成旁路开关(MIBS)周缘还可在制造太阳能电池期间和/或之后提供减轻或消除太阳能电池中的微裂纹的产生和/或蔓延的额外益处。这归因于以下事实:通过沟槽隔离区域与太阳能电池岛分开的MIBS周缘还可充当防止边缘引起和边缘蔓延的微裂纹的护罩或防护装置。本文所述的太阳能电池实施方案实现具有与电池永久附接的(例如,层压的)底板和与电池集成的MIBS装置的智能太阳能电池和智能太阳能模块,如背接触太阳能电池,包括背接触/背结IBC电池。图14是示出使用全周边闭环周缘MIBS旁路二极管20的MIBS太阳能电池实施方案的示意图,所述MIBS旁路二极管20通过全周边激光划线隔离沟槽22与太阳能电池岛24分开。MIBS旁路二极管20和太阳能电池岛24被附接到共用且共享的背面底板(未示出),并且由共用的原始连续且随后被划分的太阳能电池半导体衬底(来自起始半导体晶片或衬底)形成。隔离沟槽可通过划线方法、例如通过脉冲激光划线、等离子体划线或机械分割穿过太阳能电池衬底24到定位在电池背面上的底板来形成。图14示出具有闭环全周边周缘二极管(pn结二极管或肖特基二极管)的MIBS使能的太阳能电池的光明面(也称为正面或顶面)视图。如在此实施方案中所示,太阳能电池24是全正方形电池并且可具有例如像156mm乘156mm的尺寸,尽管也可以使用其它太阳能电池形状和尺寸。太阳能电池24可以是薄半导体(例如来自起始CZ或FZ或多晶晶片的薄外延硅或薄晶体硅)背接触背结太阳能电池。全周边周缘二极管22可具有十微米到约一千微米范围内的宽度,例如100微米到500微米范围内的二极管宽度。将周缘旁路二极管与太阳能电池分开并隔离的全周边贯穿硅的沟槽可具有例如几微米一直到约100微米的近似范围内的隔离宽度(可能甚至为大于约100微米的宽度,尽管不太希望使用更大宽度),所述隔离宽度取决于激光束直径和半导体层厚度。由纳秒(ns)脉冲激光划线形成的典型沟槽隔离宽度可以是约20微米一直到约100微米,尽管沟槽隔离宽度可以更小。虽然脉冲激光烧蚀或划线是形成沟槽隔离区域的有效且已证实的方法,但是应注意的是,也可以使用其它非机械和机械划线技术替代脉冲激光划线来形成用于所以MIBS太阳能电池实施方案的沟槽隔离区域。替代非激光方法包括等离子体划线、超声或声学钻进/划线、喷水钻进/划线或能够以足够的特殊分辨率(即,相对窄的沟槽隔离宽度)选择性地对半导体衬底(吸收体)层进行切割或划线的其它合适的机械分割或划线方法。术语单片集成电路用来描述被制造到一片半导体材料层(也称为半导体衬底)上的多个半导体装置和对应电互连。因此,通常在一片或一层薄的连续半导体材料如晶体硅上制造单片集成电路。本文所述的集成太阳能电池和旁路开关结构是单片半导体集成电路,因为集成太阳能电池和旁路开关(MIBS)装置均在一片半导体衬底层(来自起始半导体晶片或通过外延沉积形成的生长半导体层)上被形成/制造。此外,附接到半导体衬底层背面的连续底板的组合使得根据所公开主题的单片集成太阳能电池和旁路开关(或单片集成旁路开关MIBS)实施方案成为可能。图15是示出具有多个全周边闭环MIBS旁路二极管例如MIBS旁路二极管26的MIBS太阳能电池实施方案的光明面视图的示意图,其中所述旁路二极管26的半导体衬底通过全周边隔离沟槽27与电池30a半导体衬底电隔离,通过全周边激光划线(或如上所述的另一种合适的划线方法)沟槽如电池隔离沟槽(切穿半导体衬底并且着落或终止在共享的连续底板片材上的沟槽)28与多个太阳能电池(或共享连续底板并共享M1和M2金属化层的太阳能电池岛—也称为iCellTM)30a-30p隔离,以便基于都定位在共用的连续底板上的多个电池岛或片块形成小型电池阵列(包括多个小型电池或较小的电池岛—也称为iCellTM的太阳能电池),所述多个电池岛或片块共享共用的(并且在一些实施方案中为连续的)共享底板并且由共用的原始连续且随后被划分的太阳能电池半导体衬底(通过沟槽隔离图案执行划分)形成。图15示出MIBS使能的太阳能电池的光明面示意图,所述太阳能电池包括位于共享的连续永久性附接底板片材和单个原始半导体衬底(来自起始CZ或FZ或多晶晶片或如利用外延沉积生长)上的多个小型电池和全周边闭环周缘二极管)。每个小型电池岛30a-30p可具有全周边隔离沟槽(着落或终止在共享的连续底板片材上的贯穿半导体划线或切割区域)和全周边MIBS周缘二极管(如用于电池30a的MIBS旁路二极管26和周边隔离沟槽27)—因此每个小型电池具有对应MIBS周缘二极管,或换句话说每小型电池可能存在至少一个MIBS周缘二极管,所有区域都共享用于iCellTM的同一共享的连续底板。在一些实例中,全周边沟槽隔离间隙(例如,27)和MIBS装置(例如,26)的总面积被制成是相关联的小型电池(例如,30a)的总面积的相对小的一部分(小于约几个百分点并且具体地小于约1%)。这是确保使分配给非光生太阳能电池区域的面积最小化以获得最大的有效总面积太阳能电池和PV模块效率的设计规则。在iCellTM配置中共享共用的连续底板片材的小型电池可以通过电池金属化图案设计来电串联连接,虽然小型电池的其它电互连如并联或串联和并联的组合也是可能且实际的。这些互连通过整个iCellTMM1和M2金属化层形成。作为代表性实例,图15示出在共享的连续底板上制成iCellTM的相等大小和形状的小型电池的4x4阵列,并且每个小型电池具有对应全周边闭环周缘二极管(肖特基二极管或pn结二极管)。具有多个小型电池和相关联的MIBS装置的半导体区域均来自单个原始连续半导体衬底(来自起始半导体晶片或通过如外延生长的沉积方法生长),随后被分割以通过沟槽隔离区域在各个装置衬底之间形成电隔离。一般而言,这种架构可使用NxN小型电池阵列和对应全周边闭环周缘二极管,其中N是等于或大于二的整数,以便形成小型电池阵列。而且,虽然图15示出用于全正方形太阳能电池的对称NxN小型电池阵列,但是小型电池设计可具有NxM小型电池不对称阵列。小型电池可以是正方形(当N=M、用于正方形主电池时)或矩形(当N不等于M和/或主电池是矩形而不是正方形时)或各种其它几何形状如多边形如六边形。此外,包括主电池或iCellTM(主电池是指小型电池阵列,所述小型电池共享共用的连续底板片材并且均来源于同一原始太阳能电池半导体衬底(来自起始线锯晶片或通过如外延生长的沉积方法生长),所述半导体衬底随后通过沟槽隔离区域被划分成小型电池区域)的小型电池可任选地具有大致上相等面积,尽管这不是所需要的。小型电池阵列中的小型电池可以使用由合适的切割或划线技术如激光划线或等离子体划线(或喷水划线或超声划线等)形成的沟槽隔离来与彼此电隔离。此外,每个小型电池半导体衬底使用沟槽隔离间隙与其对应相邻全周边闭环MIBS二极管半导体衬底电隔离,虽然所述衬底共享同一连续电绝缘底板。太阳能电池上的所有沟槽隔离区域可以在电池制造工艺流程过程中的同一制造工艺步骤、例如单个工艺步骤如脉冲激光划线工艺步骤期间形成。MIBS二极管可以是用作MIBS装置或阴影管理开关的pn结二极管。产生MIBS使能的太阳能电池的pn结MIBS二极管制造工艺除其它之外可具有以下属性和益处:-在一些太阳能电池工艺设计、如具有如本发明中所述的底板使能的两层金属化结构的IBC太阳能电池中,对实现MIBS的主要太阳能电池制造工艺流程基本上不存在改变或增加的工艺步骤/手段(例如,假定背结/背接触晶体硅太阳能电池制造使用外延硅和多孔硅/剥离工艺结合可再用晶体硅模板或使用来自起始CZ/FZ单晶硅晶片的硅衬底或来自起始铸造多晶硅晶片的硅衬底,并且使用太阳能电池与MIBS装置之间共享的电绝缘连续底板)。因此,连同太阳能电池一起实现MIBS基本上不存在增加的制造成本。-在利用晶体半导体吸收层如由外延剥离电池工艺形成或来自起始晶体(CZ单晶或FZ单晶或铸造多晶晶片)的半导体衬底层的背接触/背结(或IBC)太阳能电池设计中,在完成涉及背接触、背结电池工艺步骤的大部分(背面掺杂基极区域和发射极区域、背面钝化、基极和发射极接触开口和图案化M1金属化层)的电池工艺之后,可执行以下工艺(作为各种可能的工艺流程的实例来提供—IBC工艺流程的许多变体和实施方案是可能的并且并非所有都包括在本发明中并且在本发明中得到明确描述):(i)将底板片材附接或层压到太阳能电池背面;(ii)在使用可再用模板上的多孔硅上的外延生长硅层的情况下:预释放半导体衬底(即,薄外延硅衬底)的沟槽隔离划线(例如,使用纳秒脉冲激光划线手段或可替代地使用另一种划线手段如等离子体划线或机械分割划线),以限定外延硅剥离释放边界(注意,当在CZ单晶晶片或FZ单晶晶片或铸造多晶晶片上而不使用可再用模板上的外延硅生长制造太阳能电池和MIBS时,不需要这个步骤);(iii)在使用可再用模板上的多孔硅上的外延生长硅层的情况下:机械剥离释放底板支撑的电池并且将其从可再用晶体硅模板拆离(注意:当在CZ单晶晶片或FZ单晶晶片或铸造多晶晶片上而不使用可再用模板上的外延硅生长制造太阳能电池和MIBS时,不需要这个步骤);(iv)任选地对底板层压的电池进行激光修整(例如,使用纳秒或微秒或皮秒脉冲激光源)以便进行精确修整并且建立最终所需要的太阳能电池结合其相关联MIBS的精确尺寸;(v)在太阳能电池的光明面上进行纳秒脉冲激光划线(或等离子体划线或机械分割划线或喷水划线或另一种合适的划线技术),以形成沟槽隔离区域并且限定内部太阳能电池半导体岛和周边周缘二极管半导体区域,此步骤将MIBS区域提供并限定成使得其半导体区域通过沟槽隔离(沟槽间隙)区域与太阳能电池半导体区域电隔离;(vi)以及,随后根据需要进行电池光明面任选湿法蚀刻(例如,以使硅衬底变薄,如果需要的话)、纹理化和纹理化后表面清洁,接着是额外的电池工艺步骤如PECVD光明面钝化和抗反射涂层沉积,以及最后完成后面电池金属化、包括贯穿底板以对图案化M1层的预先指定区域提供接入的通孔,和形成图案化第二层金属化(或图案化M2)和导电通孔插塞(例如,通过M2金属根据导电通孔插塞的预先指定的图案渗透穿过互连图案化M2和图案化M1的钻进通孔来形成)。在上述代表性工艺流程中并且在使用可再用模板上的多孔硅上的外延生长硅层以获得太阳能电池和其相关联MIBS的情况下,沟槽隔离划线工艺和手段可任选地与用于对底板层压的太阳能电池和MIBS衬底进行预释放沟槽划线和/或释放后精确修整的工艺和手段相同。-可(例如,使用纳秒脉冲激光源)执行激光划线(或能够形成穿过半导体衬底层的整个厚度、以可忽略地移除或切入底板片材并且不会危急连续底板片材的完整性的方式终止并着落在底板片材上的相对狭窄沟槽的任何合适的划线或切割工艺)沟槽隔离工艺,以在薄半导体衬底层内形成完整的贯穿半导体(例如,在基于硅的太阳能电池和MIBS的情况下为贯穿硅)沟槽区域,所述沟槽区域穿过半导体层(例如,外延硅或来自起始晶体硅晶片的硅衬底)的整个厚度并且以极少地或可忽略地移除底板材料的方式大致上停止在底板处—由此形成MIBS二极管的电隔离半导体周缘区域(例如,当形成n型IBC电池时为n型晶体硅)和太阳能电池的半导体岛区域,从而呈现n型基极(因此,n型半导体电池和MIBS衬底层)和p+发射极太阳能电池(其为背接触/背结或IBC太阳能电池的共同掺杂类型)。如果需要的话,半导体衬底可以是p型硅层(因此为太阳能电池的p型基极),并且电池背面上的掺杂场发射极区域可以是n+掺杂(例如,磷或砷掺杂)结区域。pn结MIBS二极管图案可以是许多可能的图案设计之一。例如,在一个MIBS二极管图案中,周边周缘二极管p+发射极区域(与IBC太阳能电池掺杂发射极区域同时形成)可以是夹在n型基极区域(n型半导体还在太阳能电池岛内用作太阳能电池的基极)之间(或由其环绕)的连续闭环带,这个图案在图16中示出(尺寸并未按比例示出)。图16是示出具有全周边闭环连续pn结二极管的MIBS背接触/背结(即,IBC)太阳能电池实施方案的顶视图的示意图(此处未按比例示出MIBS周缘二极管宽度和其它相对电池尺寸)。这个代表性实施方案使用n型半导体层(即,IBC太阳能电池的n型基极)来描述。然而,类似结构可使用p型半导体层(即,IBC太阳能电池的p型基极)来制成。太阳能电池岛40(例如,具有n型基极的IBC太阳能电池)由使太阳能电池半导体衬底40与MIBS周缘半导体衬底区域隔离的全周边沟槽隔离区域36环绕,MIBS周缘半导体衬底区域包括n型(例如,磷或砷掺杂)区域38和p+掺杂(例如,硼或镓掺杂)表面区域34(内部n掺杂区域38和外部n掺杂区域32环绕或夹着p+掺杂区域34);并且n掺杂衬底区域还位于p+掺杂区域下面,并且外部n掺杂区域32与彼此电连通并且在p+掺杂表面区域34的侧边和下面环绕p+掺杂表面区域34,从而形成MIBS装置的pn结二极管),所有区域都共享共用的连续底板并且由共用的原始连续且随后使用沟槽隔离间隙划分的太阳能电池半导体衬底形成。图16示出全周边MIBS周缘二极管的p+掺杂硅衬底(充当太阳能电池的场发射极结和pn结二极管的p+区域)区域和n掺杂硅衬底(太阳能电池岛40中的n掺杂衬底区域还充当太阳能电池基极区域)区域,所述全周边MIBS周缘二极管与太阳能电池40被附接或层压到同一共用的连续底板片材或衬底。在具有n型基极和p+发射极的IBC太阳能电池的这个代表性实例中,太阳能电池本身具有n型硅太阳能电池基极和p+掺杂硅太阳能电池发射极结区域。在肖特基二极管而不是pn结二极管用作MIBS的情况下,MIBS周缘区域中的p+掺杂区域34可以用通向n型硅的铝或铝硅合金肖特基接触来替换(因此稍后情景中的MIBS区域中不存在p+掺杂,以便允许形成Al/n型硅肖特基接触)。在一些实例中,与pn结二极管相比,肖特基接触整流器可提供优秀的MIBS装置,因为与pn结二极管相比,肖特基二极管可被制成具有更小正向偏压(例如,与pn结二极管的约0.6V到0.8V相比,肖特基二极管的约0.2V到0.5V),因此,与pn结MIBS相比,肖特基二极管MIBS具有更小功率耗散。图16示出掺杂MIBSpn结二极管区域:形成p+n结二极管的p+掺杂二极管区域34以及夹着或环绕或包封p+掺杂闭环带的环绕的n型硅区域32和38。使用协调并且同时的MIBS和太阳能电池制造工艺流程,MIBSpn结二极管的p+掺杂区域可与主太阳能电池的p+发射极(在具有双掺杂选择性发射极和掺杂发射极接触区域的太阳能电池的情况下,为场发射极或p+掺杂发射极接触区域)在背接触/背结(即,IBC)太阳能电池制造工艺流程期间使用作为太阳能电池基极区域的原位掺杂n型外延硅或不依赖外延的n型起始晶片(例如,CZ或FZ单晶晶片或铸造多晶晶片)一起并且同时形成。类似地,既在太阳能电池用作其基极区域(在具有n型基极的IBC太阳能电池的情况下)又用于太阳能电池的相关联MIBS的n型硅区域是太阳能电池的n型半导体基极(例如,在使用可再用模板上的多孔硅上的外延生长硅的情况下,在原位掺杂外延硅沉积工艺期间形成)。用于MIBS二极管的轻掺杂或n型区域的导电(例如,因M1层而成为金属的)欧姆接触的n+掺杂区域也可与用于太阳能电池的n型基极区域的导电(例如,因M1层而成为金属的)欧姆接触的称为n+掺杂基极接触区域的更重掺杂区域一起并且同时形成。因此,MIBSpn结二极管装置层和制造工艺步骤与没有MIBS的太阳能电池本身的那些基本上协调并且相同,因此对于MIBS二极管实现连同太阳能电池制造可能仅存在可忽略的或基本上无增加的制造成本。全周边p+掺杂区域34(由n型衬底区域包封并环绕)可占沟槽隔离的周缘半导体衬底表面积的一部分到大部分(例如,约5%到约95%,并且更具体地约20%到约80%),并且可以通过内部n型区域38和外部n型区域32(内部n型区域和外部n型区域基本上是n型衬底区域)与沟槽隔离的周缘二极管的边缘和MIBS的侧壁边缘分开,以保持p+n结边缘和耗尽区域边缘远离MIBS周缘pn结二极管边缘或侧壁(以便防止反向漏电流的衰退或增加并且防止pn结二极管的击穿电压的衰退或减小)。p+掺杂区域(与太阳能电池发射极同时形成)形成MIBSpn结周缘二极管以用于部分或完全遮蔽情况下的集成电池层级阴影管理和太阳能电池的反向偏压保护。可保持MIBSp+n结二极管及其相关耗尽区域边缘远离(凹入)周缘二极管的钝化边缘(隔离沟槽36处的内边界和形成周缘二极管的侧壁边缘的外边界),以便确保良好旁路二极管性能以及相关的低反向漏电流和高反向击穿电压。还可在形成太阳能电池光明面钝化和ARC层的同时并且使用用于形成太阳能电池光明面钝化和ARC层的相同钝化和ARC工艺来钝化沟槽隔离的MIBS周缘pn结二极管的边缘,形成太阳能电池光明面钝化和ARC层是例如通过等离子体增强的化学气相沉积或PECVD工艺来沉积氢化氮化硅或氢化氮化硅和下伏钝化层的组合,所述下伏钝化层包含无定形硅或无定形氧化硅或无定形氮氧化硅或无定形碳氧化硅或二氧化硅或氧化铝或其组合。作为实例,假定周缘(包括内部n型区域38、外部n型区域32和p+掺杂区域34)半导体(例如,晶体硅)总宽度为例如约400微米,那么p+掺杂区域可具有约300微米的宽度并且与每个侧壁边缘分开约50微米(换句话说,内部n型区域38、外部n型区域32各自具有约50微米的宽度)。可替代地并且作为另一个实例,假定周缘(包括内部n型区域38、外部n型区域32和p+掺杂区域34)半导体(例如,晶体硅)总宽度为例如约600微米,那么p+掺杂区域可具有约200微米的宽度并且与每个侧壁边缘分开约200微米(换句话说,内部n型区域38、外部n型区域32各自具有约200微米的宽度)。根据所公开主题,更小和更大的其它绝对和相对尺寸是可能的。而且,虽然图16的MIBS二极管实施方案在这里被示出为闭环全周边周缘pn结二极管,但是MIBS的许多其它实施方案是可能的,包括但不限于:非闭环沟槽隔离的MIBS周缘二极管、群聚在太阳能电池的边缘附近或边缘处的沟槽隔离的MIBS二极管岛(在图17中示出)、分布遍及太阳能电池区域的沟槽隔离的MIBS二极管岛等。可替代地,并且参考图16所示的结构描述,MIBS周缘二极管可具有全周边闭环连续肖特基二极管而不是如上所述并且在图16中示出的pn结二极管(MIBS周缘二极管宽度和其它相对电池尺寸未按比例示出)。在肖特基二极管MIBS实施方案中,形成图16的p+n结二极管的p+二极管区域34可替代地不被形成并且用轻掺杂n型硅(其可以与用于太阳能电池n型基极或太阳能电池n型硅衬底本身的n型硅相同)来替换,所述轻掺杂n型硅用于形成合适的肖特基势垒接触,例如铝/n型Si肖特基势垒接触闭环带,其中铝肖特基势垒接触基本上所具有的整体结构与如图16中所示并且由n型硅衬底区域环绕或包封并且夹着的p+二极管区域34的结构相同。在使用可再用模板上的多孔硅上的外延生长硅层的情况下,用于随后的铝肖特基势垒接触的MIBS二极管的n型硅区域可以与主太阳能电池的n型外延基极在背接触/背结太阳能电池制造工艺流程期间使用原位掺杂n型外延硅沉积一起并且同时形成以作为太阳能电池基极区域。类似地并且在使用可再用模板上的多孔硅上的外延生长硅层的情况下,n型硅区域(既用于太阳能电池基极又用于MIBS肖特基二极管的非肖特基/欧姆接触区域)可以是在外延硅沉积工艺期间形成的太阳能电池的同一原位掺杂外延基极。可替代地,在使用起始晶体硅晶片(如CZ单晶或FZ单晶或铸造多晶晶片)替代外延硅沉积的情况下,来自起始晶体硅晶片的n型硅衬底既充当用于随后的铝肖特基势垒接触形成的MIBS二极管n型区域又用作主太阳能电池的n型基极区域。在任一种情况(使用n型晶体起始晶片而无需外延,或使用n型外延硅生长)下,提供用于MIBS肖特基二极管的低电阻欧姆接触的n型区域(定位在肖特基接触(如铝/n型硅肖特基接触带)的至少一面或两个面上,因此夹着或环绕金属(例如,铝)肖特基接触带,并且与铝肖特基势垒接触的边缘间隔开以防止分流或增加的反向漏电流)的重掺杂区域的n+掺杂区域(例如,更重掺杂区域—掺杂有n型掺杂剂如磷)也可与用于太阳能电池的n型基极区域的低电阻欧姆接触的n+掺杂区域一起形成。因此,如同MIBSpn结二极管,MIBS肖特基势垒二极管装置层和制造工艺步骤与不具有MIBS的太阳能电池的那些基本上协调并且相同,因此对MIBS肖特基势垒二极管实现方式增加可忽略的或零增量制造成本。MIBS装置的全周边铝/n型硅肖特基势垒接触区域可占沟槽隔离的周边周缘表面积的一小部分(低至几个百分点)一直到大部分(例如,大到约95%),并且在一些实例中可以通过内部n型区域和外部n型区域(环绕肖特基势垒接触区域的钝化且n+接触的n型区域)与沟槽隔离的周缘二极管的边缘和所述结构的侧壁边缘间隔开并分开,以便保持肖特基势垒(例如,铝/n型硅)肖特基接触边缘和半导体耗尽区域边缘远离钝化MIBS周缘二极管边缘或侧壁(以便防止肖特基势垒二极管特性、如反向偏置电流和反向击穿电压以及正向偏置特性的衰退)。铝/n型硅肖特基接触区域形成用于电池层级阴影管理和反向偏置保护的MIBS肖特基周缘二极管。通过重掺杂n+接触区域进行的与轻掺杂n型区域的肖特基势垒金属(例如,铝或铝硅合金)接触以及与环绕的n型区域的欧姆金属(例如,铝或铝硅合金)接触可使用与图案化M1相同的金属层并且在形成太阳能电池的图案化M1层的同时并使用用于形成太阳能电池的图案化M1层的相同工艺来形成在MIBS装置上。可通过内部n型硅区域和外部n型硅区域(未由肖特基势垒金属覆盖的环绕的n型区域)边界保持MIBS装置肖特基势垒接触如铝/n型硅或铝硅合金/n型硅肖特基势垒接触远离周缘二极管的钝化边缘,以便确保良好旁路二极管性能特性,包括正向偏置特性和反向偏置特性。沟槽隔离的MIBS周缘肖特基二极管的边缘还可在沉积太阳能电池光明面钝化和ARC层的同时被钝化,沉积是例如通过PECVD(用于沉积单个或多个钝化层和ARC层)工艺或原子层沉积或ALD(例如,用于沉积氧化铝钝化层)和PECVD(用于沉积氢化氮化硅钝化层/ARC层)工艺的组合进行。用于太阳能电池光明面的相同钝化和ARC工艺以及薄膜也在MIBS正面(与图案化M1面相反的一面)上形成钝化。图17是示出具有替代MIBS二极管几何图案的MIBS背接触/背结(或IBC)太阳能电池实施方案的顶视图的示意图,替代MIBS二极管几何图案使用与太阳能电池相关联的多个pn结二极管岛。重要地,并且如先前关于图16所述,这个实施方案还可利用肖特基势垒二极管MIBS替代pn结二极管MIBS。图17的MIBS二极管太阳能电池包括太阳能电池50和群聚在太阳能电池的周边边缘周围和附近的多个分段式或分开的MIBS二极管岛48(MIBS二极管尺寸未按比例示出),并且所有MIBS岛和太阳能电池衬底共享共用的连续底板并且由共用的原始连续且随后被沟槽隔离划分的太阳能电池半导体衬底(如前所述,由起始硅晶片形成或通过外延硅剥离工艺形成)形成。虽然这个代表性实施方案示出太阳能电池50和群聚在太阳能电池的周边边缘周围和附近的多个分段式或分开的MIBS二极管岛48,但是应理解,替代实施方案和设计可使用根据任何所需图案分布遍及整个太阳能电池衬底区域(并且不仅仅是群聚在太阳能电池的周边边缘周围和附近的多个分段式或分开的MIBS二极管岛48。在具有n型半导体(基极)层的IBC电池的情况下,MIBS二极管岛48是由p+掺杂结区域46(与太阳能电池p+场发射极和/或发射极接触扩散区域同时形成形成的pn结MIBS二极管岛,并且MIBS二极管岛48同样可以可替代地是肖特基二极管岛(包括通向n型硅的合适的肖特基势垒金属接触如铝或铝硅合金接触),p+掺杂结区域46由n掺杂(轻n掺杂)硅区域44(其可以与用作太阳能电池的基极区域的原始n型半导体衬底相同)环绕并包封,并且MIBS半导体衬底通过全周边隔离沟槽42与太阳能电池50衬底电隔离,所述全周边隔离沟槽42着落并终止在共享的连续电绝缘底板片材或衬底上。MIBS装置的多个pn结二极管岛可以制成任何几何形状,例如包括但不限于:方形或圆形或矩形或其它多边形形状,并且具有例如在小于约100微米一直到约数百微米的范围内并且可大至几毫米的侧边尺寸。沟槽隔离的MIBS二极管岛的数目可以在至少两个到数十个或甚至几百个MIBS岛范围内。MIBS岛可以根据任何所需分布图案分布遍及太阳能电池衬底(包括但不限于:遍及太阳能电池衬底区域或群聚在太阳能电池的边缘周围和附近的统一矩形分布图案或任何其它所需分布图案)。所有MIBS二极管岛48具有沟槽隔离边缘,以用于使MIBS二极管硅岛与太阳能电池硅衬底区域(所有区域都共享同一连续电绝缘底板片材或衬底)适当电隔离。如图17(针对MIBS与n型基极/衬底IBC太阳能电池所述的实例)中所示,MIBS岛中的每一个的p+掺杂结区域可以通过n掺杂区域44(其可以与作为太阳能电池n型基极区域的n型硅衬底材料层相同并且与来自起始晶片的原始n型硅衬底层或生长n型外延层相同)与沟槽隔离的MIBS二极管的边缘间隔开并分开。p+掺杂区域(与太阳能电池p+场发射极和/或p+发射极接触扩散区域同时形成并且使用用于其形成的相同工艺来形成,后者针对利用选择性发射极工艺的IBC)同时形成每个MIBS岛中的pn结二极管。形成于MIBS岛中的p+n结可以与MIBSpn结二极管的钝化边缘间隔开并且保持远离钝化边缘(以便保持半导体pn结耗尽层边缘远离边缘并且实现最佳的pn结二极管正向偏置和反向偏置特性,而无任何边缘引起的降级)。MIBS二极管岛的边缘(以及前表面区域)在沉积太阳能电池光明面钝化和ARC层的同时被钝化,沉积是例如通过PECVD钝化工艺(或PECVD和另一种工艺如ALD的组合,如果需要的话)进行。作为代表性实例,假定MIBS二极管岛侧边尺寸为例如约500微米,p+掺杂区域46可具有约400微米的侧边尺寸,与每个侧壁边缘分开约50微米(换句话说,邻近p+掺杂区域的n掺杂区域44的宽度为约50微米),虽然其它尺寸和布置也是可能的。可替代地,并且作为众多可能性中的另一种代表性实例,假定MIBS二极管岛侧边尺寸为例如约600微米,p+掺杂区域46可具有约200微米的侧边尺寸,与每个侧壁边缘分开约200微米(换句话说,邻近p+掺杂区域的n掺杂区域44的宽度为约200微米)图18A和图18B是共享的连续底板衬底(被永久地层压或附接到原始半导体衬底,太阳能电池及其相关联的MIBS装置由原始半导体衬底形成)上的MIBS周缘二极管和太阳能电池在太阳能电池和MIBS工艺的不同阶段的横截面图。如在其它附图中,在这些附图中,MIBS边缘二极管和太阳能电池相对尺寸未按比例示出。这个代表性实例示出沟槽隔离(例如,脉冲激光切割或划线穿过半导体衬底)工艺之前或之后的底板层压的太阳能电池半导体衬底,所述沟槽隔离工艺用于限定并且分开周边(如全周边周缘)MIBS二极管硅衬底区域和太阳能电池硅衬底区域(两者均由来自起始硅晶片的同一原始硅衬底或外延硅剥离工艺形成)。在使用外延硅剥离工艺制造的背接触/背结太阳能电池的情况下,在通过完成图案化M1金属化层完成背接触/背结太阳能电池工艺之后并且在完成底板层压和从可再用模板外延剥离并拆离太阳能电池之后,通过从光明面划线穿过硅衬底来执行沟槽隔离工艺。可替代地,在使用晶体硅(例如,CZ单晶或FZ单晶或铸造多晶)晶片制造的背接触/背结太阳能电池的情况下,在通过完成图案化M1金属化层完成背接触/背结太阳能电池工艺之后并且于在太阳能电池背面上完成底板层压工艺之后,通过从光明面划线穿过硅衬底来执行沟槽隔离工艺。图18A是示出被附接或层压到背接触/背结(IBC)太阳能电池60的相对薄的(例如,在约50微米到250微米的厚度范围内)底板片材(如合适的芳族聚酰胺纤维预浸材料)62的横截面图,太阳能电池60在太阳能电池衬底制造之后包括薄(例如,从约一微米一直到约200微米,并且更具体地在小于约100微米的厚度范围内)硅衬底,例如具有约5微米到80微米范围内的半导体衬底厚度的外延硅层、或具有约50微米到200微米范围内的层压后硅衬底厚度的硅晶片(CZ单晶或FZ单晶或铸造多晶硅晶片)(未示出太阳能电池结构性细节)。如图所示,外延硅层具有n型本底掺杂。在用于太阳能电池的外延硅剥离工艺的情况下,薄硅衬底制造步骤可包括通过完成图案化M1金属化层进行模板上背接触/背结电池工艺、底板层压以及从可再用硅模板外延硅剥离释放并分开(当使用起始硅晶片替代外延剥离硅衬底时,工艺中不使用剥离释放和分开)。图18A示出形成沟槽隔离区域(例如,通过脉冲激光划线形成)之前的背接触/背结电池,沟槽隔离区域对MIBS周缘二极管衬底进行限定并电隔离或划分并且充当MIBS周缘二极管隔离边界。薄底板片材62可以是柔性电绝缘预浸片材,其具有约50微米到200微米范围内的厚度,并且具有匹配硅衬底的相当接近的CTE(例如,通过使用合适的芳族聚酰胺纤维/树脂预浸材料)。薄底板片材62被层压(例如,通过热/真空/压力层压)到背接触/背结太阳能电池60的后面,并且充当由太阳能电池和MIBS周缘二极管共享的共用的连续底板衬底。底板保持共享底板的集成太阳能电池和MIBS装置以及图案化M1和M2层的整体结构完整性。图18B是示出被附接到其在图18A中的连续底板片材62的太阳能电池60在形成沟槽隔离区域64(例如,通过脉冲激光划线或另一种合适的方法)之后的横截面图,沟槽隔离区域64用于限定并且隔离MIBS周缘二极管66和太阳能电池岛68。沟槽隔离工艺切穿半导体衬底层的整个厚度,从而形成沟槽隔离窄间隙(例如,具有几微米一直到数百微米的宽度、并且更具体地具有<100微米沟槽宽度的沟槽),而没有显著地挖入连续底板片材中(这取决于底板片材的厚度,对于沟槽隔离工艺存在一定余量,即移除几微米到约数十微米暴露的沟槽区域中的底板材料,在一些实例中移除相对少量底板材料片材或不移除底板材料片材)。例如,太阳能电池岛68可具有约156mmx156mm或约210mmx210mm范围内的正方形(或准正方形)侧边尺寸(可选择用于太阳能电池的其它尺寸,以提供仅几cm2到数百cm2并且甚至超过1000cm2宽范围内的太阳能电池面积)。沟槽隔离区域64可具有几微米一直到约100微米(或甚至更大)范围内的宽度。脉冲激光开槽能够形成具有近似约20微米到60微米(因此,出于太阳能电池与MIBS装置之间的沟槽隔离的重要目的浪费很少硅衬底)的相对窄宽度(所述宽度为合乎需要的)的沟槽隔离区域。MIBS周缘二极管区域66可以是具有约200微米到600微米(更小或更大宽度也是可能的)范围内的宽度的全周边周缘二极管,并且可以是pn结二极管或肖特基势垒二极管旁路开关。在一些实例中,全周边周缘二极管的总宽度被选择成尽可能小,以便使MIBS装置面积为太阳能电池总面积的相对小的一部分(以便最大化太阳能电池和所得太阳能PV模块的总面积效率)。整个太阳能电池和MIBS制造工艺(如丝网印刷、激光烧蚀等)的分辨能力确定最小化全周边周缘MIBS装置的可实现宽度的能力。图19A和图19B是详述位于共享的连续底板62上的图18B中所示的背接触/背结太阳能电池的MIBS周缘或全周边二极管太阳能电池实施方案在完成形成MIBS使能的背接触/背结IBC太阳能电池的制造工艺之后的横截面图,所述制造工艺包括太阳能电池(和MIBS装置)的纹理化表面上的正面钝化和ARC涂布,在太阳能电池中显示为钝化/ARC涂层70并且在MIBS装置中显示为钝化/ARC涂层72。这里未示出太阳能电池和MIBS结构细节,如图案化M1和M2金属化层。图19A示出使用pn结周边周缘二极管旁路开关的MIBS实现方式。沟槽隔离的MIBS周缘pn结二极管区域72包括n掺杂(例如,磷掺杂)区域和p+掺杂(例如,重硼掺杂)区域并且用作pn结二极管旁路开关。MIBS周缘pn结二极管区域72可以是全周边周缘二极管,其具有例如约200微米到600微米范围内的宽度(更小或更大的尺寸也是可能的,如前所述)。MIBS周缘二极管和太阳能电池相对尺寸未按比例示出。在一个制造实施方案中,图19A示出在完成MIBS使能的背接触/背结(IBC)太阳能电池的制造工艺之后的底板层压(或底板附接)的MIBS使能的太阳能电池,完成所述制造工艺包括通过图案化第一层金属化或M1(例如由丝网印刷制或PVD铝或铝硅合金或包括镍的另一种合适的金属等制成)完成背接触/背结电池工艺,底板层压,从晶体硅可再用模板外延硅剥离释放并分开(如果使用外延硅剥离工艺形成衬底的话—当使用起始晶体硅晶片时,这种工艺不适用),形成限定MIBS周缘二极管边界的沟槽隔离区域(例如,通过脉冲激光划线或切割),任选的硅蚀刻、纹理化和纹理化后清洁,钝化和ARC沉积(例如,通过PECVD或ALD和PECVD的组合),以及在底板上制造最后的图案化第二层金属或M2(连同导电通孔插塞)。如图19A中可以看出,用于形成太阳能电池的p+发射极区域(场发射极区域和/或重掺杂发射极接触区域)的工艺也可用于形成用于MIBSpn结形成的p+结掺杂。由例如铝或铝合金(如具有某种硅添加物的铝)制成的图案化M1金属(未示出)不仅提供太阳能电池的接触金属化或第一层金属化,而且产生用于MIBSpn结二极管的金属化接触(通过n+掺杂接触窗通向p+区域和n-型衬底区域)。MIBSpn结二极管的n掺杂硅区域由还充当太阳能电池的基极区域的同一n型硅衬底(例如,当使用起始n型晶体硅晶片而无需外延时来自n型硅晶片,或当使用外延硅剥离工艺形成太阳能电池和MIBS衬底时来自由外延沉积形成的原位掺杂n型晶体硅层)形成—衬底本体区域掺杂也可称为衬底的本底掺杂。图案化M1和M2金属化结构完成所需的单片太阳能电池和MIBSpn结二极管电互连,并且还确保MIBS二极管端子被适当地互连到相应太阳能电池基极端子和发射极端子,以便提供电池层级集成阴影管理和连续的抵抗遮蔽的太阳能电池保护。如图19A中可以看出,MIBSpn结二极管的侧壁边缘和顶面也使用用于钝化太阳能电池的光明面和边缘(钝化/ARC涂层70)的相同钝化层和工艺来钝化。图19A未示出太阳能电池和MIBS结构的一些细节,如图案化M1和M2金属化、后面钝化层、M1接触孔、穿过底板的M1-M2通孔以及MIBS装置结构中用于n型衬底M1连接的n+掺杂接触窗。图19B示出使用周边肖特基周缘二极管旁路开关的MIBS实现方式。隔离的肖特基周缘二极管旁路开关区域74包括n掺杂区域以及内部n+区域和外部n+区域并且用作肖特基二极管旁路开关。肖特基周缘二极管旁路开关区域74可以是具有200微米到600微米范围内的宽度(这个尺寸可以被选择成大于或小于这个范围)的全周边周缘二极管。在一个制造实施方案中,图19B示出在完成MIBS使能的背接触/背结太阳能电池的制造工艺之后的底板层压或底板附接的MIBS使能的太阳能电池,完成所述制造工艺包括通过图案化第一层金属化或M1(例如由合适的导电体如铝或铝硅合金制成,所述导电体可充当重掺杂硅上的有效欧姆接触以及轻掺杂硅上的有效肖特基势垒接触)完成背接触/背结电池工艺,底板层压,当使用外延剥离硅衬底时从晶体硅可再用模板外延硅剥离释放并分开(当使用起始晶体硅晶片替代外延剥离衬底时,这种工艺不适用或不需要),形成限定MIBS周缘肖特基二极管边界的沟槽隔离(例如,通过脉冲激光划线或切割),任选的硅薄化蚀刻、纹理化和纹理化后清洁,形成钝化和ARC(例如,通过PECVD或PECVD与另一种工艺如ALD的组合),以及在底板上制造最后的图案化第二层金属或M2(连同导电M1-M2通孔插塞)。如图19B中可以看出,还用作太阳能电池的基极区域的n型硅衬底(例如,当使用外延剥离工艺时通过原位掺杂外延沉积形成,或当不使用外延剥离工艺时来自起始n型晶体硅晶片)也用作MIBS肖特基二极管的n型硅衬底区域。由例如铝或合适的铝合金(如具有某种硅添加物的铝)制成的M1金属(未示出)不仅制造太阳能电池的M1欧姆接触金属化(对于太阳能电池的基极区域,通过n+掺杂接触开口,并且对于发射极接触区域,通过p+掺杂接触开口),而且产生MIBS肖特基二极管的金属化接触(轻掺杂n型硅衬底区域上的非欧姆肖特基势垒接触和通过重掺杂n+掺杂区域通向n型硅的欧姆接触)。MIBS二极管的轻掺杂n型硅衬底区域来自用于太阳能电池并且充当其基极区域的同一n型衬底(例如,当使用外延硅剥离工艺时,所述n型衬底可通过原位掺杂n型外延硅沉积形成,或当不使用外延硅剥离工艺时来自起始n型晶体硅晶片)。用于与n型硅衬底的MIBS肖特基二极管欧姆接触的n型硅区域的重掺杂n+扩散掺杂可在产生太阳能电池的重掺杂n+掺杂基极接触区域的同时并且使用也用于产生太阳能电池的重掺杂n+掺杂基极接触区域的相同工艺来形成(为随后的图案化M1金属化作准备)。图案化M1和M2金属化层结构的组合完成太阳能电池和MIBS肖特基二极管电互连,并且确保MIBS二极管端子被适当地连接到太阳能电池端子,以便提供电池层级集成阴影管理和太阳能电池保护。如图19B中可以看出,MIBS肖特基二极管的侧壁边缘和顶面也使用用于形成太阳能电池的光明面和边缘上的钝化和ARC层(标注为钝化/ARC涂层70)的相同钝化和ARC层和工艺来钝化。此外,图19B未示出太阳能电池结构的一些结构细节,包括但不限于图案化M1和M2金属化层。本文所公开的MIBS实施方案采用沟槽隔离结合共享的底板衬底来建立MIBS与太阳能电池的半导体衬底区域之间的划分和电隔离。产生沟槽隔离区域的一种方法是脉冲(如纳秒脉冲)激光划线。以下是对使用如用于先前所述的全周边MIBS周缘二极管或pn结或肖特基二极管的激光划线工艺形成沟槽隔离区域的关键考虑因素和激光属性的概述,所述沟槽隔离区域将MIBS二极管衬底区域与太阳能电池衬底区域划分并电隔离:-用于沟槽隔离形成的脉冲激光划线可使用处于划线和切穿硅所普遍使用的并且已证实的合适波长(例如,以相对良好的选择性烧蚀半导体层以相对于底板材料切穿半导体衬底层的绿色或红外线波长或另一种合适的波长)的纳秒脉冲激光源。激光源可具有平顶(也称为高帽)或非平顶(例如,高斯)激光束轮廓。有可能使用以下脉冲激光源波长,所述脉冲激光源波长在硅中是高吸收性的,但是可部分或完全传输穿过底板(因此,在完成贯穿半导体层的激光切割并且光束到达底板片材之后,切穿半导体层而不会显著移除底板材料)。例如,可使用纳秒脉冲IR或绿色激光束,其可有效切穿硅衬底层并且部分传输穿过底板材料(因此,在沟槽隔离切割期间移除少到可忽略量的底板材料)。-可选择纳秒脉冲激光源的脉冲激光束直径和其它性质,使得隔离划线宽度在几微米一直到数十微米的范围内,因为远大于约100微米的宽度将会过大并且导致宝贵硅衬底区域的不必要浪费以及太阳能电池和模块的总面积效率的一定程度的降低。因此,与高度所期望的太阳能电池面积相比,最小化沟槽隔离区域是有益的。实际上,纳秒脉冲激光切割可产生具有约20微米一直到约60微米期望范围内的宽度的沟槽隔离区域。例如,对于156mmx156mm太阳能电池,就沟槽隔离区域作为电池面积的一小部分而言,30微米的沟槽隔离宽度对应于0.077%的面积比。与太阳能电池面积相比,这表示相当可忽略的面积,换句话说,这个小比例提供太阳能电池面积的可忽略浪费并且确保总面积太阳能电池和模块效率的可忽略损失。-在如本文所述的背接触/背结太阳能电池制造工艺中,当使用起始晶体硅晶片制造太阳能电池和相关联的MIBS装置时,可在底板层压工艺之后(并且在使用外延硅剥离工艺制造的太阳能电池和MIBS的情况下,在完成底板层压工艺和随后从可再用模板剥离释放被层压电池之后,并且在对太阳能电池进行脉冲激光修整之后或之前)立即执行形成沟槽隔离的纳秒(ns)脉冲激光划线或切割。在使用外延硅剥离工艺制造的太阳能电池和MIBS的情况下,沟槽隔离划线或切割工艺可任选地使用用于对外延硅层进行预释放划线以限定剥离释放边界和/或用于被层压太阳能电池的释放后修整的同一脉冲激光手段和源。因此,为了形成沟槽隔离区域,不需要额外的激光工艺手段。-形成沟槽隔离的纳秒(ns)脉冲激光划线还可用于将完全隔离的MIBS周缘二极管区域限定在隔离的太阳能电池岛外部,所述太阳能电池岛由所述周缘环绕并限定。可替代地,ns脉冲激光划线工艺可形成其它设计的MIBS二极管,如呈多个MIBS二极管岛设计以及许多其它可能的MIBS图案设计的MIBS二极管。-脉冲激光划线可用于(从光明面)切穿薄(如小于200微米,并且更具体地小于100微米)硅衬底层并且大致上停止在底板材料片材上。如果期望和/或需要的话,简单的实时原位激光划线工艺端点确定(如使用反射率监测)可用于工艺控制和终点确定,以便在实现完整贯穿半导体层激光切割的同时最小化对底板片材进行的挖槽或材料移除。-在剩余的太阳能电池制造工艺步骤期间,随后可湿法蚀刻(例如,作为太阳能电池光明面湿法蚀刻/纹理化工艺的一部分)、纹理化后清洁并且钝化(通过钝化和ARC层的沉积)太阳能电池和MIBS周缘二极管区域的侧壁。以下参照利用pn结二极管作为MIBS装置实现方式的太阳能电池描述关键的工艺流程属性。-太阳能电池工艺流程对于MIBS装置实现方式而言可保持基本上不变并且是协调的(因此为可忽略到零增加的增量制造成本),其中与每个太阳能电池一起实现MIBSpn结二极管不需要额外的制造工艺手段。-可在光明面或正面上执行限定全周边MIBS周缘二极管区域和太阳能电池岛(或用于MIBS二极管布置的任何其它设计)的沟槽隔离工艺,例如在通过图案化M1层完成电池工艺和将底板层压到硅衬底之后(并且在由外延硅剥离工艺制成的太阳能电池的情况下,在外延衬底释放工艺之后)执行,并且在由外延硅剥离工艺制成的太阳能电池的情况下,所述沟槽隔离工艺可使用作为释放手段的一部分用于预释放硅划线的同一脉冲激光源。沟槽隔离激光划线完全地对硅衬底层进行划线,并且大致上停止在底板上、移除了极少或可忽略的底板材料。-可利用形成太阳能电池p+掺杂场发射极(或在利用选择性发射极工艺的IBC电池工艺的情况下的太阳能电池p+掺杂发射极接触区域,包括用于场发射极和用于发射极接触区域的两种不同发射极重掺杂区域)的相同工艺步骤同时形成MIBSpn结二极管p+掺杂结区域。MIBSpn结二极管n掺杂区域可以与用作太阳能电池衬底和基极区域的起始n型晶体硅晶片相同(或在由外延硅剥离工艺制成的太阳能电池的情况下,与原位掺杂外延太阳能电池基极区域相同)。例如,用于制造背结/背接触太阳能电池的相同太阳能电池发射极和基极掺杂工艺(如具有APCVD、激光烧蚀和热工艺)还可用于同时形成所需的p+/n周缘二极管装置结构并且无增加的增量工艺成本。-可设计金属-1(M1)和金属-2(M2)导电体图案,使得MIBSpn结二极管的p+掺杂电极连接到太阳能电池的n型基极,并且MIBS二极管的n型衬底区域欧姆接触(通过与太阳能电池n+掺杂基极接触区域一起形成的n+掺杂接触区域)电极连接到太阳能电池的p+发射极。可以分布式格式设计这些适当形成的连接,以便每当MIBS二极管由于太阳能电池遮蔽而启动并且绕过太阳能电池时最小化不合乎需要的电流拥挤和局部热点。-可在第二层金属M2图案(其可形成在底板的暴露表面上,换句话说形成在与太阳能电池光明面相反的平面上)上形成电池母线(基极和发射极母线)和指叉型基极和发射极指状物的最终粗间距图案。图案化M2还单片完成太阳能电池与其MIBS装置的互连。M1图案仅具有细间距指叉型基极和发射极指状物而不具有母线,以便消除归因于母线的电遮蔽。在以下部分中,描述使用pn结二极管MIBS实现实施方案的所需的MIBS二极管面积。为了示例性目的,这个实例针对156mmx156mm太阳能电池描述。最小的MIBS旁路二极管面积由如以下考虑因素控制:二极管的最大容许正向偏置(导通状态)电阻—或换句话说,当MIBS二极管由于太阳能电池遮蔽而启动并且正向偏置时的电阻。假定n型衬底区域(太阳能电池基极)具有约3x1015cm-3的磷掺杂,这对应于约1.60Ω.cm的n型衬底(或n型基极区域)电阻率。而且,进一步假定相对薄的晶体硅基极区域厚度为约40μm(微米),可如下计算三个不同水平的容许串联电阻值(不包括接触电阻)所需的MIBS旁路二极管面积(作为粗略指南,这个实例被提供为非常近似的数量级计算):对于最大容许串联电阻Rs=0.010Ω(对于5W电池,最大功率耗散R.I2=1W):-面积=(1.6Ω.cmx40x10-4cm)/0.01Ω=0.64cm2(MIBS装置面积是太阳能电池面积的~0.26%)-156mmx156mm电池的周缘宽度:0.64/(15.6x4)=0.010cm=0.10mm或100微米对于最大容许串联电阻Rs=0.005Ω(对于5W电池,最大功率耗散R.I2=0.5W):-面积=(1.6Ω.cmx40x10-4cm)/0.005Ω=1.28cm2(MIBS装置面积是太阳能电池面积的~0.52%)-156mmx156mm电池的周缘宽度:1.28/(15.6x4)=0.020cm=0.20mm或200微米对于最大容许串联电阻Rs=0.002Ω(对于5W电池,最大功率耗散R.I2=0.1W):-面积=(1.6Ω.cmx40x10-4cm)/0.002Ω=3.20cm2(MIBS装置面积是太阳能电池面积的~1.30%)-156mmx156mm电池的周缘宽度:3.20/(15.6x4)=0.050cm=0.50mm或500微米基于以上近似计算,对于156mmx156mm太阳能电池,约100μm到500μm范围内的MIBS周缘二极管宽度是合理的(就限制导通电阻引起的功率耗散、同时维持相对小的MIBS与太阳能电池面积比而言),其中周缘二极管面积近似为太阳能电池面积的~0.26%到~1.3%。图20A是示出具有周边MIBS周缘pn结二极管的背接触/背结(IBC)太阳能电池(如图16中所示)的例如使用铝或铝硅合金金属化(或另一种合适的金属或金属合金材料)的第一层金属化图案(M1)实施方案(在将连续底板层压到半导体衬底之前,形成在电池和MIBS背面表面上的图案化M1金属层)的平面图的示意图。图20B是出于描述性目的提供的图20A的展开选择视图。图20A和图20B示出形成为图案化M1层(例如,铝或铝硅合金)指叉型基极和发射极金属指状物96,以及形成MIBSpn结二极管p和n接触的铝(或铝硅或另一种合适的导电体)金属化接触的无母线指叉型太阳能电池基极和发射极金属。沟槽隔离区域86将太阳能电池半导体衬底与MIBS旁路二极管半导体衬底区域划分并电隔离。铝(或铝硅合金或另一种合适的金属)接触金属定位在太阳能电池的n掺杂区域上、显示为基极金属化指状物88,并且还定位在MIBS旁路二极管的n掺杂区域92上、显示为n掺杂区域金属化接触82(通过n+掺杂接触扩散区域形成铝或铝硅合金欧姆接触)。铝或铝硅合金接触金属定位在太阳能电池的p+掺杂区域上、显示为发射极金属化指状物90)上,并且还定位在MIBS旁路二极管的p+掺杂区域94上、显示为p+掺杂区域金属化接触84(通过掺杂p+接触扩散区域)。图案化M1铝或铝硅合金金属化层可通过铝或铝合金膏层的图案化丝网印刷形成,或通过铝或铝合金(如铝硅)的物理气相沉积(PVD)之后进行图案化工艺(如激光烧蚀)形成。铝或铝硅合金层(M1层)的厚度对于通过PVD形成的M1铝而言可以在1微米的一小部分一直到约几微米范围内,并且对于通过铝或铝硅合金膏的丝网印刷形成的铝或铝硅合金而言可以在几微米一直到约数十微米(例如,约20微米)范围内。可替代地,在背接触背结(IBC)太阳能电池的周边MIBS周缘肖特基二极管MIBS实现实施方案中,第一层金属化(M1)图案(例如铝或铝硅合金金属化)可与图20A和图20B中所示的相同。在如参考图20B所述的周边MIBS周缘肖特基二极管MIBS实现方式中,电池包括无母线指叉型太阳能电池基极和发射极金属(例如,铝或铝硅合金)欧姆指状物96,以及形成轻掺杂n型硅上的MIBS二极管非欧姆肖特基势垒接触和重掺杂n+硅上的欧姆接触(后者用于通向n型衬底的欧姆接触)的铝或铝硅金属化接触。作为图案化M1的一部分,铝(或铝硅合金)接触金属定位在形成于太阳能电池的n型衬底区域上的重掺杂n+区域上或定位成与所述n+区域重叠、显示为基极金属化欧姆指状物88,并且还定位在形成于MIBS肖特基旁路二极管的n型衬底区域上的n+掺杂欧姆接触区域92上、显示为n掺杂区域金属化接触82(接触n掺杂硅衬底的重掺杂n+接触扩散区域)。铝或铝硅接触金属(作为图案化M1层的一部分)还定位在太阳能电池的重p+掺杂区域上、显示为发射极金属化欧姆指状物90(通过p+掺杂接触扩散区域)。作为图案化M1的一部分,铝或铝硅肖特基势垒接触金属84还直接定位在MIBS旁路二极管的轻掺杂n型衬底区域94上,例如仅定位在n型表面上,以便形成整流器的肖特基势垒区域。图案化M1铝或铝硅合金(或另一种合适的材料)金属化层可通过铝或铝硅(或另一种合适的导电材料)膏层的图案化丝网印刷形成,或通过铝或铝硅(或另一种合适的导电材料)的物理气相沉积(PVD)之后进行图案化工艺(如激光烧蚀)形成。铝层的厚度对于通过PVD形成的M1铝或铝硅合金而言可以在在1微米的一小部分一直到几微米范围内,并且对于通过对应膏的丝网印刷形成的铝或铝硅而言可以在几微米一直到约数十微米(例如,一直到约20微米)范围内。背接触/背结IBC太阳能电池和相关联的MIBS二极管被金属化并互连以形成完整的太阳能电池。示例性金属化使用结合并且由太阳能电池和MIBS共享的底板实现的两层金属化结构,其具有第一层接触金属化图案(M1)和第二层最终图案化金属化层(M2),M1由例如铝或合适的铝合金(如具有少量百分比硅的铝)制成、在底板附接/层压之前形成,M2由例如较厚的高导电性导电体(包括铝和/或铜或其组合)制成并且任选地具有额外层如势垒层和/或顶部焊料层。M1与M2之间的层间连接可使用在形成图案化M2层之前穿过在底板层中钻出或形成的通孔的导电通孔插塞来形成,其中底板充当电绝缘层间电介质层。上述两层单片太阳能电池和MIBS金属化结构的关键属性如下:-第一层金属M1(例如在底板附接和层压之前形成于太阳能电池背面上)可以是由PVD(等离子体溅射蒸发、离子束沉积等)铝(或铝合金)或丝网印刷铝(或铝合金)膏制成的图案化铝层(和/或包含铝的合金,如Al和Si)。-图案化M1充当接触金属化并且在太阳能电池上形成指叉型基极和发射极金属化线(在一些实施方案中,在M1上不存在母线,以便消除或最小化与母线相关联的电遮蔽)。-在一些实施方案中,图案化指叉型M1金属化指状物不会延伸超出太阳能电池岛以在下面与沟槽隔离区域重叠并且不会延伸到MIBS周缘二极管区域。使用图案化M2层和导电通孔插塞进行太阳能电池与其相关联MIBS装置之间的电互连,所述导电通孔插塞根据预先指定的互连设计形成图案化M1与M2层之间的图案化互连。-在用于MIBS的全周边周缘二极管设计的情况下,M1铝或铝合金金属化层可被设计以形成三个同心的全周边连续铝金属化环(对于正方形电池,显示为正方形环),以便电欧姆接触MIBS周缘二极管的p+掺杂结区域以及内部和外部n掺杂衬底区域(通过n+掺杂接触扩散区域)。-可使用利用相对便宜的低电阻率导电体材料(包括铜和/或铝(或其组合))的丝网印刷和/或PVD(如用于例如包括铝的金属化的等离子体溅射和/或热蒸发和/或电子束蒸发)和/或电化学沉积或电镀(例如,用于包括铜的金属化)或其它金属化工艺(或其组合)来形成M2金属层。-图案化M2金属可以被图案化在通过多个导电通孔插塞连接到指叉型电池上M1指状物的大体上正交的指叉型指状物中。在这种设计中,太阳能电池的较粗间距的M2指状物相对于太阳能电池的指叉型较细间距的M1指状物的正交布置允许M2指状物的数目显著小于M1指状物的数目。例如,太阳能电池可具有在底板层压之前直接形成于电池上的数百个M1指状物,而在底板层压之后所形成的M2指状物的数目通常可以比M1指状物的数目小近似5倍到约50倍。-图案化M2金属还可将MIBSpn结二极管的重p+掺杂和n型衬底接触M1金属化分别连接到太阳能电池的基极母线和发射极母线。可替代地,在使用肖特基势垒二极管用于MIBS的情况下,图案化M2金属还可将MIBS肖特基二极管的肖特基势垒接触(例如,轻掺杂n型硅上的铝或铝硅合金非欧姆肖特基接触)和n型欧姆接触M1金属化分别连接到太阳能电池的基极母线和发射极母线。此外,重要的是要注意,虽然已结合使用薄晶体硅吸收层和连续底板的背接触/背结晶体硅太阳能电池解释本文所述的实施方案,但是应理解的是,所公开主题的方面可由本领域技术人员应用于其它太阳能电池和模块实现方式,包括但不限于:非IBC背接触太阳能电池(包括但不限于MWT太阳能电池);前接触太阳能电池和对应的PV模块;非晶体硅太阳能电池和模块,如由晶体GaAs、GaN、Ge和/或其它元素和化合物半导体制成的那些;以及各种基于晶片的太阳能电池,包括由晶体半导体晶片(如CZ单晶硅晶片、FZ单晶硅晶片和铸造多晶硅晶片)制成的背接触/前结、背接触/背结和前接触太阳能电池。然而,如前所述,背接触电池的使用在某些方面可为有利的,如MIBS实现方式可应用于背接触电池而不会显著影响最终的模块制造。此外,电池的背面上的发射极和基极互连引线两者的可用性可进一步简化用于增强的能量采集以及额外的电池层级监测和控制功能的电池上电子器件的整体实现方式。图21是具有周边MIBS周缘二极管(例如pn结二极管或肖特基势垒二极管)的背接触/背结太阳能电池的背面的示意图,示出第二层金属化图案(M2)实施方案。在这种设计中,图案化M2定位在共享的电绝缘底板上并且通过底板片材与M1层实体分开。图案化M2层包括:基极母线104,其连接到MIBSpn结二极管的p+掺杂区域M1欧姆接触金属(例如还形成为图案化M2金属化层的一部分的图20B中的p+掺杂区域金属化接触84);发射极母线102,其连接到MIBSpn结二极管n掺杂衬底区域M1金属欧姆接触(例如图20B中的n掺杂区域金属化接触82);导电通孔插塞100,其根据预先指定的图案(每个M2基极指状物通过导电通孔插塞来连接到所有M1基极指状物,并且每个M2发射极指状物通过导电通孔插塞来连接到所有M1发射极指状物)将M2指状物互连到M1指状物;以及发射极指叉型指状物112和基极指叉型指状物106。图21示出相对于M1指状物以大体上正交或垂直取向覆盖在图案化M1层(这幅图中未示出)上的图案化M2层,图案化M1层可以是例如包括无母线指叉型太阳能电池基极和发射极金属指状物以及形成MIBS二极管欧姆接触的铝(或铝硅合金)金属化接触的图案化M1层,如图20A中所示的M1层。MIBS周缘二极管(pn结二极管或肖特基势垒二极管)和太阳能电池以及相关金属化尺寸未按相对比例示出。可通过以下方式形成多个导电通孔插塞100:钻出穿过底板并且着落在预期M1区域(而不刺穿焊盘垫上的M1层)的通孔,并且随后通过M2金属化工艺形成将M2金属化的所需部分互连到M1金属化层的指定部分的导电通孔插塞(即,M2发射极指状物通过导电通孔插塞连接到M1发射极指状物以及通向MIBSn型衬底的M1接触;M2基极指状物通过导电通孔插塞连接到M1基极指状物以及通向pn结二极管的p+区域或通向肖特基势垒二极管的肖特基势垒M1金属区域的M1接触)。通过导电通孔插塞连接的图20A中所示的M1图案和图21中所示的M2图案的组合完成了整个太阳能电池和相关联MIBS装置金属化以及MIBS端子到太阳能电池端子的单片分布式互连,所述互连随后可用于形成电池层级的单片集成阴影管理互连。出于电极性区域别的目的,图21以两种灰色调示出M2层。M2图案的深灰色部分包括太阳能电池基极母线104,其连接到下伏M1金属化区域的MIBS周缘pn结二极管p+掺杂区域(或如果使用肖特基二极管用于MIBS的话,则连接到肖特基二极管铝/n型硅肖特基接触)。如这个代表性实施方案中所示,通过位于太阳能电池衬底的三个侧边上的导电通孔插塞进行用于MIBS到太阳能电池互连的M2-M1互连,所述导电通孔插塞在基极母线104以及M2的左侧边和右侧边上的两个垂直基极母线指状物108内(每个侧边上一个指状物)。这种结构在太阳能电池的基极与MIBSpn结二极管的pn结二极管p+端子(或MIBS肖特基二极管的铝(或铝硅)/n型硅肖特基势垒接触端子)之间形成分布式互连。M2内部上的显示为连接到基极母线104的垂直指状物的指叉型基极指状物106通过导电通孔插塞连接到下伏M1指叉型基极指状物(未示出)。使用M2图案相对于图20A中所示的M1图案的正交变换,M2基极指状物的数目与M1基极指状物的数目相比可以显著减小,通常减小了近似5倍到约50倍。M2图案的浅灰色部分包括太阳能电池发射极母线102,其连接到形成为下伏M1金属化区域一部分的MIBS周缘pn结二极管n型硅衬底欧姆接触或MIBS周缘肖特基势垒二极管n型硅欧姆接触(通过用于n型硅欧姆接触的n+掺杂接触扩散)。如图所示,通过太阳能电池的三个侧边上的导电通孔插塞进行互连,所述导电通孔插塞在发射极母线102以及左侧边和右侧边上的四个发射极母线指状物110内(每个侧边上两个指状物)。这种结构在太阳能电池的发射极与MIBSpn结二极管或MIBS肖特基势垒二极管的n型硅衬底(通过用于欧姆接触的n+接触扩散)端子之间形成分布式互连。M2内部上的显示为连接到发射极母线的发射极指叉型指状物112通过导电通孔插塞连接到下伏M1指叉型发射极指状物。此外,通过使用M2图案相对于M1图案的正交变换,M2发射极指状物的数目与M1发射极指状物的数目相比可以显著减小,通常减小了近似5倍到约50倍。由于M2图案正交变换,M2图案(例如,指状物)可比M1指状物图案具有大得多的最小尺寸(或平均指状物宽度)。例如,与图案化M1层上的指叉型太阳能电池基极和发射极指状物相比,M2上的指叉型太阳能电池基极和发射极指状物以及母线具有宽得多的金属指状物,并且还可具有大得多的指状物间间距。在这种配置中,最窄的M2指状物是用于MIBS周缘二极管端子与太阳能电池端子之间的M2-M1互连(通过导电通孔插塞连接)的侧边指状物(基极母线指状物108和发射极母线指状物110)。在这种配置中,通过从M2到M1的导电通孔插塞在太阳能电池和MIBS的三个侧边上形成太阳能电池到MIBS装置连接。图22是具有周边MIBS周缘二极管(例如pn结二极管或肖特基势垒二极管)的背接触/背结太阳能电池的背面的示意图,示出替代的第二层金属化图案(M2)实施方案。图案化M2定位在共享的电绝缘连续底板上并且通过层压的底板与M1层实体分开。图案化M2包括:基极母线124,其连接到MIBSpn结二极管p+掺杂区域M1金属(例如图20B中的p+掺杂区域金属化接触84);发射极母线122,其连接到MIBS二极管n掺杂衬底区域M1金属欧姆接触(例如图20B中的n掺杂区域金属化接触82);导电通孔插塞120,其将M2连接到M1;以及指叉型发射极指状物128(通过导电通孔插塞连接到M1指叉型发射极指状物)和指叉型基极指状物126(通过导电通孔插塞连接到M1指叉型基极指状物)。图22示出覆盖在图案化M1层(下伏M1层未示出)上的图案化M2层,图案化M1层可以是例如像图20A中所示的包括无母线指叉型太阳能电池基极和发射极金属指状物以及形成MIBS二极管金属化欧姆接触的铝或铝硅合金金属化接触的图案化M1层。MIBS周缘二极管(pn结二极管或肖特基势垒二极管)和太阳能电池以及相关金属化尺寸未按相对比例示出。多个导电通孔插塞120将M2金属化的所需部分连接到M1金属化层的指定部分,并且可以通过钻出穿过底板直至预期M1区域的通孔、随后在M2金属化期间形成导电通孔插塞来形成。通过导电通孔插塞连接的图20A中所示的M1图案和图22中所示的M2图案的组合完成了整个太阳能电池和MIBS装置金属化以及MIBS端子到太阳能电池端子的单片分布式互连,这随后可用于形成电池层级的单片集成阴影管理互连。出于电极性区域别的目的,图22以两种不同灰色调示出M2。M2图案的深灰色部分包括太阳能电池基极母线124,其通过太阳能电池的两个侧边(一个侧边是母线侧边)上的导电通孔插塞连接到下伏M1金属化区域的MIBS周缘pn结二极管p+掺杂区域(或如果使用肖特基势垒二极管用于MIBS的话,则连接到肖特基势垒二极管铝/n型硅肖特基接触),导电通孔插塞在基极母线以及显示为M2的左侧边上的垂直指状物的基极母线指状物130内。这种结构在太阳能电池的基极区域与MIBSpn结二极管的p+端子(或MIBS肖特基势垒二极管的铝/n型硅肖特基接触端子)之间形成分布式互连。M2内部上的显示为垂直指状物的指叉型基极指状物126通过导电通孔插塞连接到基极母线并且还连接到下伏M1指叉型基极指状物。M2图案相对于M1图案的正交变换允许M2基极指状物的数目与M1基极指状物的数目相比显著减小,通常减小了近似5倍到约50倍。M2图案的浅灰色部分包括太阳能电池发射极母线122,其连接到形成为下伏图案化M1金属化区域一部分的MIBS周缘pn结二极管n型硅衬底欧姆接触(通过通向n+掺杂区域的欧姆接触)或MIBS周缘肖特基势垒二极管n型硅衬底欧姆接触(通过用于n型硅欧姆接触的n+接触扩散)(M2-M1连接通过在太阳能电池的两个侧边上的导电通孔插塞形成,所述导电通孔插塞在发射极母线以及M2的右侧边上的垂直发射极母线指状物132内)。这种结构在太阳能电池的发射极与MIBSpn结二极管或MIBS肖特基势垒二极管的n型硅衬底(通过用于欧姆接触的n+接触扩散)端子之间形成分布式互连。M2内部上的显示为垂直指状物的指叉型发射极指状物128通过导电通孔插塞连接到发射极母线并且还连下伏M1指叉型发射极指状物。此外,通过使用M2图案相对于M1图案的正交变换,M2发射极指状物的数目与M1发射极指状物的数目可以显著减小,通常减小了近似5倍到约50倍。由于M2图案正交变换,M2图案(例如,指叉型指状物)可比M1图案(或M1平均指状物宽度)具有大得多的最小尺寸(或平均指状物宽度)。例如,与形成于M1层上的指叉型太阳能电池基极和发射极指状物相比,M2上的指叉型基极指状物126、指叉型发射极指状物128和母线可具有宽得多的金属指状物或线,并且还可具有大得多的指状物间间距。在这种配置中,最窄的M2指状物可以是用于MIBS周缘二极管端子与太阳能电池端子之间通过导电通孔插塞进行的M2-M1互连)的两个侧边指状物(垂直基极母线指状物130和垂直发射极母线指状物132)。在这种配置中,在太阳能电池和MIBS的两个侧边上形成太阳能电池到MIBS装置电互连(通过从M2到M1的导电通孔插塞连接)。这种配置允许太阳能电池和MIBS侧边(换句话说,两个侧边不用于主太阳能电池母线)上的较宽指状物:垂直基极母线指状物130和垂直发射极母线指状物132形成太阳能电池与MIBS装置之间的分布式互连。本文所述的MIBS装置利用肖特基势垒二极管或pn结二极管。如果肖特基势垒二极管用作MIBS,那么可使用定位在MIBS硅衬底区域中的轻掺杂n型硅上作为肖特基接触的铝金属电极或具有一些硅含量的铝。与肖特基势垒二极管MIBS实施方案相关的关键属性和描述包括:-MIBS肖特基势垒二极管可通过在半导体表面上(如在硅上)形成两个金属接触(来自同一M1层)来制成。可形成于半导体衬底的重掺杂区域上的一个金属接触是欧姆接触(例如,通过放置在n型衬底的指明区域上的n+掺杂区域形成),并且另一个接触形成于半导体衬底的轻掺杂n型区域上并且形成提供二极管整流电性质的金属与n型半导体肖特基势垒(非欧姆)接触。同一金属(M1图案)可用于MIBS肖特基二极管的肖特基势垒(非欧姆)接触和n型衬底欧姆接触(后者通过n型衬底上的n+掺杂区域形成)两者,这对于太阳能电池制造具有极小或没有额外的制造成本。-如果n型硅用于半导体衬底(如用于如本文所述的晶体硅背接触/背结电池的太阳能电池基极区域),那么铝或具有某些硅含量的铝合金可用作肖特基势垒金属。这些材料提供极好的肖特基势垒二极管性能性质并且与太阳能电池工艺流程和材料兼容。铝具有小于n型硅功函数的功函数并且在轻掺杂n型硅上形成良好的肖特基势垒,其中轻掺杂硅表面由还用作太阳能电池基极和吸收体的n型硅衬底层提供。铝或具有某些硅含量的铝合金还可用作肖特基二极管的另一个端子的n+掺杂硅上的欧姆接触(即,通过n+掺杂区域形成与n型硅衬底的欧姆接触)。-就高性能肖特基势垒二极管而言,不论对于前接触还是背接触太阳能电池,相较于p型硅衬底,可使用n型硅衬底。n型硅衬底的使用还对制造没有任何本体光引起的衰退(通常通过p型硅晶片来观察)的高效太阳能电池有利。-对n掺杂硅上的铝肖特基势垒接触金属电极(也称为肖特基接触)施加正电势产生跨硅层两端的较小电势降,因此减小了电子从轻掺杂n型硅衬底注入到铝肖特基接触电极的势垒高度。因此,更多电子将朝向金属扩散而不是扩散到硅中,并且净电流将流过结。这是肖特基势垒二极管的正向偏置或导通状态。这种正向偏置状况是在遮蔽情况下为太阳能电池提供保护的MIBS状态。-当对肖特基铝金属电极施加负电压(或反向偏压)时,跨势垒两端的电势上升,从而增加了耗尽层宽度并且抑制了电子从n型硅衬底注入到金属电极中。所得的电势势垒限制流到金属电极的电子并且产生可忽略的电流(MIBS肖特基二极管的截止状态—这种反向偏置状况表示无太阳能电池遮蔽时的MIBS状态)。用作MIBS,铝半导体肖特基接触结可提供极好的整流性质。虽然大电流可在正向偏置(导通状态)下存在,可忽略电流在反向偏置(截止状态)时流动,但是两者都是MIBS的所需性质。-在一些实例中,相较于MIBS实现方式中的pn结二极管,可使用肖特基势垒二极管。肖特基势垒二极管与pn结二极管相比具有较小的导通状态正向偏压(例如,肖特基二极管近似为~0.2V到0.5V对比pn结二极管为~0.6V到0.8V),从而当肖特基势垒二极管用作MIBS时(当太阳能电池被遮蔽时,MIBS装置导通以保护太阳能电池),由MIBS装置产生较低功率耗散。肖特基势垒二极管相较于pn结二极管的较小功率耗散是相当有利的并且使肖特基势垒二极管成为MIBS装置的优良选择。-MIBS周缘肖特基二极管MIBS实现方式可使用相对轻掺杂n型硅衬底作为主掺杂二极管区域。在使用外延硅剥离太阳能电池工艺与外延生长n型基极的太阳能电池衬底制造工艺和背接触/背结太阳能电池设计中,MIBS二极管的n型硅区域可由作为外延n掺杂硅(或太阳能电池的基极区域)的同一衬底形成,并且MIBS二极管的n型硅区域和外延n掺杂硅在电池工艺期间使用沟槽隔离来与彼此电隔离。在这种情况下,用于肖特基铝接触的区域具有与太阳能电池基极掺杂(例如,近似为3x1015cm-3的磷掺杂,同时取决于太阳能电池设计要求,所述掺杂可大于或小于这个量)相同的轻n型掺杂,而不具有重掺杂n+基极接触扩散区域。也可使用作为图案化M1金属化层的一部分的铝(或具有某些硅含量的铝合金)通过形成于n型衬底(肖特基二极管的第二端子)的指明区域上的n+掺杂(重掺杂磷)欧姆接触区域形成与n型硅衬底的欧姆接触。-通过使用与n型硅衬底区域通过重掺杂n+掺杂接触扩散区域进行的铝欧姆接触形成MIBS肖特基势垒二极管的欧姆接触(这使用同样形成用于背结/背接触太阳能电池的基极欧姆接触的n+掺杂区域的相同工艺并且在相同工艺期间形成)。-用于形成铝(或铝硅)与n型硅肖特基接触和铝(或铝硅)与n+硅(和n型硅)欧姆接触的铝(或Al/Si合金)层可以是用于形成太阳能电池中的指叉型基极和发射极接触金属化的同一金属-1(M1)铝(和/或铝硅)层。例如,所述层可以是与硅进行高质量电欧姆(和肖特基)接触的具有某些硅含量(防止结穿刺或铝穿刺到硅中的几个百分点的硅)的高导电性铝层。可使用铝(或铝合金)膏或铝(或铝合金)墨(同样,例如,具有防止结穿刺的硅含量百分比)的丝网印刷、漏版印刷、气溶胶喷射印刷或喷墨印刷、之后进行膏或墨的热固化来形成图案化M1铝层。可替代地,金属1(M1)可由另一种合适的方法、例如如等离子体溅射、热或电子束蒸发、离子束沉积的沉积方法或另一种毯式沉积方法、之后进行M1图案化(例如,通过激光烧蚀或湿法蚀刻图案化)来形成。M1铝或铝合金层的厚度可取决于铝层的电阻率。通常,如物理气相沉积或PVD(例如,等离子体溅射或热蒸发或电子束蒸发)技术沉积出具有近本体导电性(例如,~3μΩ.cm的电阻率)的铝层,因此M1铝层的所需厚度可以在约100nm一直到2000nm的近似范围内(由于M1-M2两层金属化架构,将不需要更厚的M1金属)。另一方面,由铝或铝合金膏或墨形成M1通常产生较低的所得金属导电性(远小于本体铝的导电性),如~30μΩ.cm到~200μΩ.cm范围内的材料电阻率。因此,如果由膏或墨产生M1,那么将需要更厚的金属层(例如,约1微米一直到约20微米厚度范围内的丝网印刷M1)。图23A到图23L是示出相关MIBS二极管和太阳能电池几何布置的各种代表性实施方案的平面图的示意图,所述实施方案针对MIBS与全正方形太阳能电池来示出。太阳能电池和MIBS尺寸未按实际或相对比例示出。如在图23的代表性实施方案中可看出,MIBS二极管总面积(包括任何相关联沟槽隔离的面积)可远小于太阳能电池面积(MIBS和沟槽隔离总面积与太阳能电池面积的分数被选择为<1%,并且常常不大于约0.3%)。当然,可利用更大的面积比(其具有降低总面积电池和模块效率的不合需要的后果)。。图23A示出如本文先前所述的全周边闭环周缘MIBS设计,其包括由全周边MIBS周缘二极管144环绕的太阳能电池岛140,全周边MIBS周缘二极管144由全周边沟槽隔离区域142划分并电分开。而且,虽然这种设计可具有某些益处,但是也可使用无穷数目的其它MIBS太阳能电池设计可能性。例如,图23B、图23C和图23F示出非全周边MIBS二极管设计的实例,其中MIBS二极管可被制成为位于正方形太阳能电池的1个、2个或3个侧边上的非闭环周缘二极管(与形成于正方形太阳能电池的所有4个侧边上的全周边MIBS二极管形成对比)。图23B示出具有位于一个侧边上的MIBS周缘二极管的太阳能电池,其包括太阳能电池区域146、沟槽隔离区域148以及由沟槽隔离区域148划分并电分开的非全周边MIBS周缘二极管150。图23C示出具有位于两个侧边上的MIBS周缘二极管的太阳能电池,其包括太阳能电池区域152、沟槽隔离区域154以及由沟槽隔离区域154划分并电分开的非全周边MIBS周缘二极管156。图23F示出具有位于三个侧边上的MIBS周缘二极管的太阳能电池,其包括太阳能电池区域170、沟槽隔离区域172以及由沟槽隔离区域172划分并电分开的非全周边MIBS周缘二极管174。作为另一个实施方案,图23D示出被配置为太阳能电池区域内的单个岛的MIBS,其包括在太阳能电池区域158内由闭环沟槽隔离区域160限定并电隔离/划分的岛状MIBS二极管162。(图23D示出位于太阳能电池中心周缘的MIBS岛的实例,尽管所述岛可定位在太阳能电池区域中的任何地方)。MIBS岛可以呈任何几何形状(图23D和图23E示出呈矩形的MIBS二极管岛;可使用其它多边形或其它几何形状)。图23E示出呈多个离散MIBS岛(其可通过M1和M2金属化图案电互连)形式的MIBS实现方式,其包括在太阳能电池区域164内由闭环沟槽隔离区域166限定并电隔离/划分的多个岛状MIBS二极管168。在图23G所示的另一个实施方案中,MIBS装置可以定位在太阳能电池的拐角中。图23G包括在太阳能电池区域176的一个拐角中由沟槽隔离区域178限定并电隔离的拐角MIBS二极管180。虽然图23G示出三角形拐角MIBS,但是拐角MIBS的形状可以是任何几何形状(例如,正方形、矩形等)。此外,拐角MIBS装置的数目可以不只一个,例如,如图23H中所示的两个拐角MIBS装置、三个拐角MIBS装置或如图23I中所示的四个拐角MIBS装置。图23H示出包括多个拐角MIBS二极管186的配置,拐角MIBS二极管186在太阳能电池区域182的两个拐角中由沟槽隔离区域184限定并电隔离/划分。图23I示出包括多个拐角MIBS二极管192的配置,拐角MIBS二极管192在太阳能电池区域188的四个拐角中由沟槽隔离区域190限定并电隔离/划分。在图23J所示的另一个实施方案中,MIBS装置可以形成为从太阳能电池的一个拐角延伸到相对对角的对角线带。图23J示出包括窄对角线带状MIBS二极管198的配置,窄对角线带状MIBS二极管198由从太阳能电池区域194的一个拐角延伸到相对拐角的沟槽隔离区域196限定并电隔离/划分。可替代地,MIBS装置可以是在太阳能电池的两个相对侧边之间延伸的单条带(如图23K所示)或在太阳能电池的两个相对侧边之间延伸的多条带(如图23L所示)。图23K示出包括边到边带状MIBS二极管204的配置,边到边带状MIBS二极管204由沟槽隔离区域202限定并电隔离/划分,并且在太阳能电池区域200的中心并从一个侧边到相对侧边被定位。图23J示出包括多个边到边带状MIBS二极管210的另一种配置,边到边带状MIBS二极管210由从太阳能电池区域206的一个侧边到相对侧边的沟槽隔离区域208限定并电隔离/划分。图23中所示的代表性结构仅仅是关于太阳能电池的本质上无穷数目的可能MIBS几何设计中的MIBS几何设计的几个实例。而且,虽然这里针对全正方形太阳能电池来示出实例,但是应理解的是,所公开主题的各种概念和实施方案可应用于制成为具有任何几何形状(包括但不限于准正方形、矩形、六边形、其它多边形、圆形等)的太阳能电池。图24到图31是使用薄外延硅剥离和可再用晶体硅模板制造背接触/背结单晶硅太阳能电池和相关联MIBS装置(pn结二极管或肖特基势垒二极管)的各种代表性工艺流程实施方案。而且,虽然以下太阳能电池和MIBS制造工艺流程被提供为具有底板和两层金属化(电池上M1和底板上M2)的薄(例如,小于100微米)外延硅背结/背接触太阳能电池的实例,但是应理解的是,本文所公开的设计、概念和各种实施方案可扩展到并应用到与各种其它太阳能电池设计和技术集成的MIBS,其它太阳能电池包括但不限于:在由本体单晶硅锭或铸造多晶砖或多晶条带形成的晶体硅晶片(如使用浆料或金刚石线锯、氢离子灌注和剥落、金属应力引起的剥落等获得的晶体硅晶片)上制造的晶体硅太阳能电池;使用n型硅晶片的标准厚度CZ或FZ单晶硅晶片前接触同质结和异质结太阳能电池;由硅之外的半导体材料(如砷化镓、氮化镓等)制成的前接触或背接触太阳能电池;以及使用单个金属化层或使用两个或更多个金属层的多层金属化的各种金属化方案。工艺流程示出的是,MIBS装置(在本文中描述为pn结二极管或肖特基势垒二极管)可以在增加可忽略到零的工艺复杂性、制造工艺手段或MIBS相关的增量制造成本的同时与高效背接触/背结底板层压的太阳能电池单片集成。基本上所有本文所公开的实施方案利用与可能已用于太阳能电池制造相同的用于MIBS实现方式的材料层和工艺。图24是用于制造具有pn结二极管MIBS实现方式的外延硅太阳能电池的代表性工艺流程实施方案。图24的工艺流程示出使用制造工艺制造高效背接触/背结太阳能电池连同其相关联MIBSpn结二极管的选项,所述制造工艺利用两次APCVDBSG工艺(称为双BSG选择性发射极工艺)来形成选择性发射极区域的重掺杂p+场发射极和更重掺杂p++掺杂欧姆接触(所有p+和p++区域都掺杂硼)区域。太阳能电池和MIBS共用衬底由形成既充当外延种层又充当剥离释放层的牺牲多孔硅(手段1)之后可再用晶体硅模板上的n型硅的外延沉积形成。原位掺杂外延层(由手段2形成)具有背接触/背结太阳能电池的n型衬底和基极区域所需的n型掺杂(n型掺杂还用于MIBSpn结二极管n型衬底)。随后在外延层由模板支撑时执行背接触/背结电池工艺(通过图案化M1层进行的电池工艺)的大部分。这些工艺步骤可使用铝或铝硅合金膏的APCVD(大气压力化学气相沉积)、脉冲激光烧蚀、炉内热工艺以及丝网印刷和固化(通过图24中的手段11进行)的组合以获得图案化M1来完成通过M1金属化层形成进行的背结/背接触太阳能电池工艺步骤。在太阳能电池被支撑在可再用晶体硅模板上时执行这些工艺。然后,将底板永久地附接并层压到模板上的太阳能电池的背面(手段12)。随后(在手段13中),通过激光划线以限定释放边界、机械剥离释放和任选的所剥离太阳能电池的激光修整来从可再用模板剥离并拆离太阳能电池(和其相关联MIBS)。通过例如使用还用于执行硅的预释放划线和/或太阳能电池和MIBS周边边界的释放后修整的同一脉冲激光源或手段从所拆离底板层压的太阳能电池的光明面进行划线,来形成用于划分并电隔离MIBS衬底区域的沟槽隔离区域。随后,完成剩余的后期太阳能电池(和MIBS)工艺步骤(手段14到18)。这些步骤包括:光明面纹理化和纹理化后湿法清洁(纹理化后湿法清洁还可清洁激光划线的隔离沟槽并且移除沟槽隔离区域中的任何激光产生的损坏)、PECVD光明面钝化7ARC(其还钝化MIBS前表面和侧壁/边缘)、和最终的底板上的高导电性图案化M2金属化和导电通孔(例如通过使用丝网印刷、PVD和/或电镀中的一种或其适当组合)。在图24的工艺流程中,与太阳能电池一起实现MIBS不需要任何额外的制造工艺手段或工艺步骤。使用在释放之前用于划线和/或在释放之后用于修整太阳能电池的相同手段或激光源来形成沟槽隔离区域。因此,对于MIBS太阳能电池实现方式存在可忽略到零增量成本。图24的工艺流程作为代表性实例来提供,但这种工艺流程的许多其它变体有可能制造太阳能电池和相关联MIBS而不会增加制造工艺复杂性或成本。虽然图24中的工艺流程针对使用外延硅剥离衬底形成制成的太阳能电池和MIBS示出并描述,但是可使用类似工艺流程在起始晶体硅晶片上制成太阳能电池和相关联MIBS装置而无需外延硅剥离衬底形成。这可通过使用起始FZ或CZ或铸造线锯晶体硅晶片来完成(因此,消除了手段1和2)。在这种情况下,将不存在剥离释放,并且手段13处所示的工艺步骤将形成沟槽隔离区域。图24中所示的所有其它工艺步骤将与针对外延硅剥离工艺所示的相同。此外,n型外延硅层(或在使用CZ或FZ或多晶晶片替代外延硅衬底的情况下的n型晶体硅晶片)充当用于太阳能电池和MIBS装置两者的单片衬底。这种n型层充当太阳能电池的吸收衬底和基极以及MIBSpn结二极管的n型衬底区域。形成p+场发射极和p++掺杂发射极接触区域的发射极工艺还形成pn结二极管的MIBSp+(和/或p++)区域。形成n+重掺杂区域的APCVDPSG辅助工艺既用于太阳能电池基极欧姆接触区域又用于通向pn结二极管的n型衬底区域的MIBS欧姆接触。太阳能电池M1-M2金属化与MIBSpn结二极管进行接触,并且完成MIBSpn结二极管作为集成阴影管理旁路开关与太阳能电池的单片互连。图25是使用单(替代双)APCVDBSG制造具有MIBSpn结二极管、无选择性发射极的外延硅太阳能电池的工艺流程实施方案。这个工艺流程示出使用以下工艺流程高效背接触/背结太阳能电池和相关联MIBSpn结二极管的制造选项,所述工艺流程利用一次APCVDBSG工艺形成重硼掺杂p+发射极(称为双BSG选择性发射极)。此外,n型外延硅层充当用于太阳能电池和MIBS装置两者的单片衬底。此n型层充当太阳能电池的吸收体和基极区域以及MIBSpn结二极管的n型衬底区域。形成p+场发射极区域的发射极工艺还形成MIBSpn结二极管的MIBSp+区域。形成n+重掺杂区域的APCVDPSG辅助工艺既用于太阳能电池基极欧姆接触区域又用于通向pn结二极管的n型衬底区域的MIBS欧姆接触。太阳能电池M1-M2金属化用于与MIBSpn结二极管进行接触,并且完成MIBSpn结二极管作为集成阴影管理旁路开关与太阳能电池的单片互连。虽然图25中的工艺流程针对使用外延硅剥离衬底形成制成的太阳能电池和MIBS示出并描述,但是可使用类似工艺流程在起始晶体硅晶片上制成太阳能电池和相关联MIBS装置而无需外延硅剥离衬底形成。这可通过使用起始FZ或CZ或铸造线锯晶体硅晶片来完成(因此,消除了手段1和2)。在这种情况下,将不存在剥离释放,并且手段11处所示的工艺步骤将形成沟槽隔离区域。图25中所示的所有其它工艺步骤将与针对外延硅剥离工艺所示的相同。图26到图31是用于制造具有用作MIBS装置的肖特基势垒二极管的太阳能电池的工艺流程实施方案。所公开工艺流程的方面可以结合和/或扩展到用于根据所公开主题的MIBS太阳能电池实现方式的各种其它工艺技术。图26是用于制造具有MIBS铝/n型硅肖特基势垒二极管的外延太阳能电池(具有选择性发射极的太阳能电池)的工艺流程。图26的工艺流程示出制造高效背接触/背结太阳能电池连同其相关联MIBS肖特基势垒二极管的选项,所述工艺流程利用两次APCVDBSG工艺来形成选择性发射极区域的重掺杂p+场发射极和更重掺杂p++掺杂发射极欧姆接触(所有p+和p++区域都掺杂硼)区域(称为双BSG选择性发射极)。太阳能电池和MIBS共用衬底由形成充当外延种层和剥离释放层两者的牺牲多孔硅层(手段1)之后可再用晶体硅模板上的n型硅的外延沉积形成。原位掺杂外延层(通过手段2形成)具有所需的用于背接触/背结太阳能电池的基极的n型掺杂(所述n型掺杂还用于MIBS肖特基势垒二极管衬底)。背接触/背结电池工艺的大部分可在外延层由模板支撑时执行。这些工艺步骤可使用铝膏的APCVD(大气压力化学气相沉积)、脉冲激光烧蚀、炉内热工艺以及丝网印刷和固化(通过图26中的手段12)的组合来完成通过M1金属化层进行的背结背接触太阳能电池工艺步骤。所有这些工艺在太阳能电池被支撑在可再用硅模板上时执行。为实现MIBS肖特基势垒二极管的制造,对流程添加一个特定工艺手段(手段8),以便紧接在APCVDPSG/USG工艺之后并且在炉内退火工艺之前对PSG/UGS层执行皮秒脉冲(或飞秒脉冲或纳秒脉冲)激光烧蚀。这单个添加的工艺步骤和手段允许随后在图案化M1工艺期间制造肖特基接触(铝或铝硅与n型硅接触)。然后,将底板永久地附接并层压到模板上的太阳能电池的背面(手段13)。随后(在手段14中),将太阳能电池(和其相关联MIBS)从可再用模板剥离并拆离(通过激光划线以限定释放边界、机械剥离释放和所剥离太阳能电池的激光修整),并且通过例如使用用于执行硅的预释放划线和/或太阳能电池和MIBS周边边界的释放后修整的同一脉冲激光源或手段从所拆离底板层压的太阳能电池的光明面划线,来形成限定并电隔离MIBS区域的沟槽隔离区域。随后,完成剩余的后期太阳能电池(和MIBS)工艺步骤(手段15到19),包括:光明面纹理化和纹理化后湿法清洁(纹理化后湿法清洁还可清洁激光划线的隔离沟槽)、PECVD光明面钝化和ARC沉积(其还可钝化MIBS前表面和侧壁/边缘)以及最终的底板上的高导电性M2金属化(使用丝网印刷、PVD和/或电镀中的一种或其适当组合)。图26的MIBS肖特基二极管太阳能电池实现方式仅需要一个额外的制造工艺手段(手段8)来执行一个额外的工艺步骤(紧接在APCVDPSG/USG工艺之后的PSG/USG烧蚀)。使用在释放之前用于划线和/或在释放之后用于修整太阳能电池的相同手段或激光源来形成沟槽隔离区域。因此,使用图26的代表性制造工艺流程实现这种MIBS肖特基二极管实现方式连同太阳能电池存在相当小的增量成本。虽然图26的工艺流程针对使用外延硅剥离衬底形成制成的太阳能电池和MIBS示出并描述,但是可使用类似工艺流程在起始晶体硅晶片上制成太阳能电池和相关联MIBS装置而无需外延硅剥离衬底形成。这可通过使用起始FZ或CZ或铸造线锯晶体硅晶片来完成(因此,消除了手段1和2)。在这种情况下,将不存在剥离释放,并且手段14处所示的工艺步骤将形成沟槽隔离区域。图26中所示的所有其它工艺步骤将与针对外延硅剥离工艺的相同。图26的工艺流程作为代表性实例来示出,并且这种工艺流程的许多其它变体有可能制造太阳能电池和其相关联MIBS的组合而不会增加制造工艺复杂性或显著的成本增加。此外,n型外延硅层(或在使用晶片替代外延硅剥离工艺的情况下的n型硅晶片)充当用于太阳能电池和MIBS装置两者的单片衬底。此n型硅衬底层充当太阳能电池的吸收体和基极以及MIBS肖特基势垒二极管的n型衬底区域(包括M1铝与n型硅肖特基接触)。形成n+重掺杂区域的APCVDPSG辅助工艺既可用于太阳能电池基极欧姆接触又可用于通向MIBS肖特基二极管的n型区域的MIBS欧姆接触。太阳能电池M1-M2金属化与MIBS肖特基势垒二极管进行接触,并且完成MIBS肖特基势垒二极管作为集成阴影管理旁路开关与太阳能电池的单片互连。图26的工艺流程示出的是,MIBS装置(在这种情况下为肖特基势垒二极管)可以与高效背接触/背结底板层压的太阳能电池单片集成,而不会增加任何额外材料或材料层、具有仅一个增加的简单工艺步骤(手段8)并且具有相当小的MIBS相关的增量制造成本。图26的实施方案可使用与已用于太阳能电池制造相同的用于MIBS实现方式的材料层和工艺。图27示出用于具有MIBS铝/n型硅肖特基势垒二极管的外延太阳能电池(不具有发射极的太阳能电池)的代表性制造工艺流程。这个工艺流程示出使用以下工艺流程制造高效背接触/背结太阳能电池连同其相关联MIBS肖特基势垒二极管的选项,所述工艺流程利用一次APCVDBSG工艺形成重掺杂p+发射极(所谓的单BSG发射极—无选择性发射极)。除了在这个流程中使用单BSG替代先前流程(图26)中所述的双BSG之外,图26和图27的工艺流程相当。虽然图27中的工艺流程针对使用外延硅剥离衬底形成制成的太阳能电池和MIBS示出并描述,但是可使用类似工艺流程在起始晶体硅晶片上制成太阳能电池和相关联MIBS装置而无需外延硅剥离衬底形成。这可通过使用起始FZ或CZ或铸造线锯晶体硅晶片来完成(因此,消除了手段1和2)。在这种情况下,将不存在剥离释放,并且手段12处所示的工艺步骤将形成沟槽隔离区域。图27中所示的所有其它工艺步骤将与针对外延硅剥离工艺的相同。图28示出用于具有MIBS铝/n型硅肖特基二极管的外延太阳能电池(不具有选择性发射极工艺的太阳能电池)的另一种代表性制造工艺流程。这个工艺流程示出使用以下工艺流程制造高效背接触/背结太阳能电池和其相关联MIBS肖特基势垒二极管的选项,所述工艺流程利用一次APCVDBSG工艺形成重掺杂p+发射极(所谓的单BSG非选择性发射极)。在这个实施方案中,为了实现MIBS肖特基势垒二极管的制造,对流程添加一个特定工艺手段(手段5;APCVDUSG或无掺杂氧化物),以便沉积无掺杂氧化物层来保护n型硅区域,n型硅区域随后将用于MIBS肖特基接触(使用M1铝或铝硅合金)。此添加的手段5还可通过使得太阳能电池n+掺杂区域能够与p+发射极区域分开(从而通过形成分开的结来防止邻接的结)来用于太阳能电池工艺流程。随后用于开出基极和发射极接触的皮秒脉冲(或飞秒脉冲或纳秒脉冲)激光烧蚀手段(手段9)还用于开出MIBS肖特基接触的n型硅区域。这个单个添加的工艺步骤和手段(手段5)允许随后在图案化M1工艺期间制造肖特基接触(铝与n型硅接触)。如实现MIBS肖特基势垒二极管的这个工艺流程中所示,在此实施方案中,与太阳能电池一起实现MIBS仅需要一个额外的制造工艺手段(手段5)来执行仅1个额外的工艺步骤(两个激光烧蚀工艺步骤之间的APCVDUSG)。虽然图28中的工艺流程针对使用外延硅剥离衬底形成制成的太阳能电池和MIBS示出并描述,但是可使用类似工艺流程在起始晶体硅晶片上制成太阳能电池和相关联MIBS装置而无需外延硅剥离衬底形成。这可通过使用起始FZ或CZ或铸造线锯晶体硅晶片来完成(因此,消除了手段1和2)。在这种情况下,将不存在剥离释放,并且手段13处所示的工艺步骤将形成沟槽隔离区域。图28中所示的所有其它工艺步骤将与针对外延硅剥离工艺的相同。图29示出用于具有MIBS铝/n型硅肖特基势垒二极管的外延太阳能电池(具有选择性发射极的太阳能电池)的另一个代表性制造工艺流程。这个工艺流程示出使用以下工艺流程制造高效背接触/背结太阳能电池连同其相关联MIBS肖特基势垒二极管的选项,所述工艺流程利用两次APCVDBSG工艺来形成用于选择性发射极区域的重掺杂p+场发射极和更重掺杂p++掺杂发射极欧姆接触(所有p+和p++区域都掺杂硼)区域(称为双BSG选择性发射极工艺)。为了实现MIBS肖特基势垒二极管的制造,在现有太阳能电池制造手段(手段9用于开出基极和发射极接触孔并且暴露n型硅肖特基接触窗)中执行一个特定额外的工艺,以便对n+硅层执行皮秒脉冲(或飞秒脉冲)激光烧蚀,从而形成用于与M1形成MIBS肖特基接触的暴露的轻掺杂n型硅区域。这个单个添加的工艺步骤(所述工艺步骤可在不添加任何专门制造手段的情况下通过将额外的激光烧蚀源添加到手段9来完成)允许随后在图案化M1形成工艺期间制造肖特基接触(铝与n型硅接触)。如实现MIBS肖特基势垒二极管的此工艺流程中所示,在此实施方案中,与太阳能电池一起实现MIBS仅需要一个额外的工艺步骤(所述工艺步骤可以在现有接触烧蚀手段—手段9中完成,以执行n+硅烧蚀从而形成暴露的轻掺杂n型硅区域)。上述工艺流程示出的是,MIBS装置(在这种情况下为肖特基势垒二极管)可以与高效背接触/背结底板层压的太阳能电池单片并且简单地集成,而不会增加任何额外材料或材料层、并且具有仅一个增加的工艺步骤(在还用于形成基极和发射极接触开口的共享的太阳能电池制造手段9中执行)、并且具有相当小的MIBS相关的增量制造成本。虽然图29中的工艺流程针对使用外延硅剥离衬底形成制成的太阳能电池和MIBS示出并描述,但是可使用类似工艺流程在起始晶体硅晶片上制成太阳能电池和相关联MIBS装置而无需外延硅剥离衬底形成。这可通过使用起始FZ或CZ或铸造线锯晶体硅晶片来完成(因此,消除了手段1和2)。在这种情况下,将不存在剥离释放,并且手段13处所示的工艺步骤将形成沟槽隔离区域。图29中所示的所有其它工艺步骤将与针对外延硅剥离工艺的相同。图30示出用于具有MIBS铝/n型硅肖特基势垒二极管的外延太阳能电池(具有非选择性发射极的太阳能电池)的另一个代表性制造工艺流程。这个工艺流程示出使用以下工艺流程制造高效背接触/背结太阳能电池连同其相关联MIBS肖特基势垒二极管的选项,所述工艺流程利用一次APCVDBSG工艺形成重掺杂p+发射极区域(所谓的单BSG非选择性发射极)。为了实现MIBS肖特基势垒二极管的制造,在现有太阳能电池制造手段(还用于开出基极和发射极接触孔的手段7)中执行一个特定额外的工艺,以便对n+硅层执行皮秒脉冲(或飞秒脉冲或纳秒脉冲)激光烧蚀,从而形成用于与图案化M1形成MIBS肖特基接触的暴露的轻掺杂n型硅区域。这个单个添加的工艺步骤(所述工艺步骤可在不添加任何专门制造手段的情况下完成)允许随后在图案化M1形成工艺期间形成肖特基接触(铝与n型硅接触)。如实现MIBS肖特基势垒二极管的此工艺流程中所示,在此实施方案中,与太阳能电池一起实现MIBS仅需要一个额外的工艺步骤(所述工艺步骤可以在现有接触烧蚀手段—手段7中完成,以执行n+硅烧蚀从而形成暴露的轻掺杂n型硅区域)。上述工艺流程示出的是,MIBS装置(在这种情况下为肖特基势垒二极管)可以与高效背接触/背结底板层压的太阳能电池单片并且简单地集成,而不会增加任何额外材料或材料层、并且具有仅一个增加的工艺步骤(在还用于形成基极和发射极接触开口的共享的太阳能电池制造手段7中执行)、并且具有相当小的MIBS相关的增量制造成本。虽然图30中的工艺流程针对使用外延硅剥离衬底形成制成的太阳能电池和MIBS示出并描述,但是可使用类似工艺流程在起始晶体硅晶片上制成太阳能电池和相关联MIBS装置而无需外延硅剥离衬底形成。这可通过使用起始FZ或CZ或铸造线锯晶体硅晶片来完成(因此,消除了手段1和2)。在这种情况下,将不存在剥离释放,并且手段11处所示的工艺步骤将形成沟槽隔离区域。图30中所示的所有其它工艺步骤将与针对外延硅剥离工艺的相同。图31示出用于具有MIBS铝/n型硅肖特基势垒二极管的外延太阳能电池(具有原位掺杂外延p++/p+发射极的太阳能电池)的另一个代表性制造工艺流程。这个工艺流程示出使用以下工艺流程制造高效背接触/背结太阳能电池连同其相关联MIBS肖特基势垒二极管的选项,所述工艺流程利用原位p++/p+发射极的外延沉积(在形成n型基极区域之后在外延硅工艺结束时沉积)。这个原位发射极工艺消除了对APCVDBSG发射极掺杂的需要(因为在外延硅工艺期间已经原位形成发射极结)。使用利用手段6对p++/p+原位形成的发射极硅进行激光烧蚀形成的n型硅开口执行肖特基势垒二极管制造,手段6是还用于使用氧化物激光烧蚀开出基极和发射极接触开口并且还使用纳秒脉冲激光退火进行接触后退火的同一工艺手段。这使得能够在MIBS衬底区域上形成M1(铝)与n型硅肖特基接触。太阳能电池和MIBS共用衬底由硅的外延沉积形成:初始地是基极区域的n型硅掺杂(对于外延硅层厚度的大部分),并且随后是p+掺杂外延发射极薄层,之后是p++掺杂发射极接触层薄层。在形成既充当外延种层又充当剥离释放层的牺牲多孔硅(手段1)之后,在可再用晶体硅模板上形成原位掺杂(基极和发射极)外延层。原位掺杂外延层(通过手段2形成)具有所需的用于背接触/背结太阳能电池的基极的n型基极掺杂(所述n型基极掺杂还用于MIBS肖特基势垒二极管衬底)以及用于太阳能电池发射极区域的p++/p+掺杂。随后在外延层由模板支撑时执行背接触/背结电池工艺(通过图案化M1层进行的工艺)的大部分。这些工艺步骤可使用铝膏的APCVD(大气压力化学气相沉积)、脉冲激光烧蚀和退火、以及丝网印刷和固化(通过图31中的手段8)的组合来完成通过M1金属化层进行的背结/背接触太阳能电池工艺步骤。在太阳能电池被支撑在可再用硅模板上时可执行所有这些工艺。为了实现MIBS肖特基势垒二极管的制造,在现有太阳能电池制造手段(还用于开出基极和发射极接触孔的手段6)中执行一个特定额外的工艺,以便对p++/p+硅层执行皮秒脉冲(或飞秒脉冲或纳秒脉冲)激光烧蚀,从而形成用于与图案化M1形成MIBS肖特基接触的暴露的轻掺杂n型硅区域。这个单个添加的工艺步骤(所述工艺步骤可在不添加任何专门制造手段的情况下完成)允许随后在M1工艺期间制造肖特基接触(铝与n型硅接触)。然后,将底板永久地附接并层压到模板上的太阳能电池的背面(手段9)。随后(在手段10中),将太阳能电池(和其相关联MIBS)从可再用模板剥离并拆离(通过激光划线以限定释放边界、机械剥离释放和所剥离太阳能电池的激光修整),并且通过在一些实施例中使用还用于执行硅的预释放划线和/或太阳能电池和MIBS周边边界的释放后修整的同一脉冲激光源或手段从所拆离底板层压的太阳能电池的光明面划线,来形成划分并电隔离MIBS区域的沟槽隔离区域。随后,完成剩余的后期太阳能电池(和MIBS)工艺步骤(手段11到15),包括:光明面纹理化和纹理化后湿法清洁(所述纹理化后湿法清洁还清洁激光划线的隔离沟槽)、PECVD光明面钝化和ARC形成(其还可钝化MIBS前表面和侧壁/边缘)以及最终的底板上的高导电性M2金属化和导电通孔插塞(使用丝网印刷、PVD和/或电镀中的一种或其适当组合)。如实现MIBS肖特基势垒二极管的此工艺流程中所示,在此实施方案中,与太阳能电池一起实现MIBS仅需要一个额外的工艺步骤(所述工艺步骤可以在现有接触烧蚀手段—手段6中完成,以执行p++/p+硅烧蚀从而形成暴露的轻掺杂n型硅区域)。实际上使用在释放之前用于划线和/或在释放之后用于修整太阳能电池的相同手段或激光源来形成沟槽隔离区域。因此,使用这个特定的代表性制造工艺流程实现本发明的MIBS肖特基二极管实施方案连同太阳能电池基本上存在相当小的增量成本。这个工艺流程作为代表性实例来示出,并且这种工艺流程的许多其它变体是可能的,以便制造太阳能电池及其相关联MIBS装置的组合而不会增加制造工艺复杂性或成本。此外,n型外延硅层充当用于太阳能电池和MIBS装置两者的单片衬底。此n型硅衬底层充当太阳能电池的吸收体和基极以及MIBS肖特基势垒二极管的n型衬底区域(包括M1铝与n型硅肖特基接触)。形成n+重掺杂区域的APCVDPSG辅助工艺既用于太阳能电池基极欧姆接触又用于与MIBS肖特基势垒二极管的n型衬底区域的MIBS欧姆接触。太阳能电池M1-M2金属化还用于与MIBS肖特基势垒二极管进行接触,并且完成MIBS肖特基势垒二极管作为集成阴影管理旁路开关与太阳能电池的单片互连。上述工艺流程示出的是,MIBS装置(在这种情况下为肖特基势垒二极管)可以与高效背接触/背结底板层压的太阳能电池单片并且简单地集成,而不会增加任何额外材料或材料层、并且具有仅一个增加的工艺步骤(所述工艺步骤可在还用于形成基极和发射极接触开口的共享的太阳能电池制造手段6中执行)、并且具有相当小的或可忽略的MIBS相关的增量制造成本。本发明的实施方案使用与已用于太阳能电池相同的用于MIBS实现方式的材料层和工艺。以上提及的代表性工艺流程示出本发明的若干实施方案,所述实施方案使用单片制造工艺实现肖特基势垒二极管或pn结二极管MIBS装置与太阳能电池的,而对主要太阳能电池工艺流程具有可忽略或小的成本增加。周边MIBS二极管可具有夹在n型区域之间的连续闭环p+掺杂结(如图16中可见)或分散在MIBS硅周缘的n型硅区域中的分段式p+掺杂岛(如图32中可见)。分段式p+掺杂岛可允许M2略微从单片集成太阳能电池和MIBS衬底的外边缘凹入。而且,虽然图32中示出一个分段式岛设计,但是其它分段式设计也是可能的。图32是示出在MIBSn型硅衬底区域内具有多个分段式pn结区域或导的MIBS背接触/背结太阳能电池实施方案的平面图的示意图(示出在M1金属化之前的情况)。太阳能电池岛220由沟槽隔离区域226环绕,沟槽隔离区域226使太阳能电池220与MIBS周缘区域划分并隔离,所述MIBS周缘区域包括n掺杂区域222和pn结岛区域224,所有区域都共享共用的连续底板并且由共用的原始连续并且随后被划分的太阳能电池半导体衬底形成。在这种结构中,通过全周边闭环沟槽隔离使太阳能电池岛220与全周边周缘pn结二极管划分并隔离。图32中所示的用于MIBSpn结二极管的相同设计还可应用于肖特基势垒二极管,其中岛区域226是M1铝与n型硅肖特基接触区域。图33A是示出在MIBSn型硅衬底区域内使用多个分段式pn结区域或岛的代表性MIBS周缘二极管的第一层金属化图案(M1)的平面图的图(示出在M1金属化之后的情况连同代表性M1图案),如图32中所示的。图33B是出于描述性目的提供的图33A的展开选择图。MIBS周缘二极管和太阳能电池尺寸未按比例示出。此特定实例示出使用全周边闭环沟槽隔离与全周边周缘pn结二极管划分并隔离的主太阳能电池岛。这种设计允许网格型M1图案与MIBS装置的n型硅衬底区域进行欧姆接触(因此,允许用于MIBS装置与太阳能电池的M2-M1互连的其它M2设计替代方案)。以上所示的用于MIBSpn结二极管的相同设计还可应用于肖特基势垒二极管(其中周缘岛是M1铝与n型硅肖特基接触区域)。图33A和图33B示出无母线指叉型太阳能电池基极和发射极金属(M1)(例如铝)指状物235以及形成MIBS二极管p+和n型衬底欧姆接触的铝金属化接触。沟槽隔离区域244使太阳能电池与MIBS旁路二极管区域划分并隔离。铝接触金属定位在太阳能电池的n掺杂区域上、显示为基极金属化指状物236,并且还定位在MIBS旁路二极管的n掺杂区域230上、显示为n掺杂区域金属化接触234(通过n+接触扩散区域进行欧姆接触)。铝接触金属定位在太阳能电池的p+掺杂区域上、显示为发射极金属化指状物238,并且还定位在MIBS旁路二极管的p+掺杂区域232上、显示为p+掺杂区域金属化接触242(通过p+接触扩散区域进行接触)。图案化M1铝金属化层可通过铝或铝合金膏层的丝网印刷形成或通过铝或铝硅合金的物理气相沉积(PVD)之后进行图案化工艺来形成。铝层的厚度对于通过PVD形成的M1铝而言可以在1微米的一小部分一直到几微米的范围内,并且对于通过铝膏的丝网印刷形成的铝而言可以在几微米一直到数十微米(例如,约20微米)范围内。对于Al/n-Si肖特基势垒二极管MIBS,用于肖特基接触的n型硅上的铝接触可以是由纯铝或具有某些硅添加物的铝合金制成的膏,以便减轻或消除铝穿刺到硅中的可能性(相同膏用于太阳能电池M1单次印刷或叠层印刷)。任选地,可通过若干技术之一来抑制或减轻MIBSpn结二极管中的任何太阳能光生效应,所述技术包括对太阳能电池光明面上的MIBS二极管周缘进行线端激光照射以降低钝化并且显著增加MIBS周缘二极管的前表面复合速率(FSRV)。可替代地,可用合适的便宜黑色光阻滞墨水涂布MIBS二极管周缘表面,此类光阻滞墨水可通过喷墨或丝网印刷来涂覆。可替代地,可使用以下M1图案设计,所述M1图案设计最大化pn结接触的M1金属接触区域覆盖率,并且因此增加MIBS装置中(而不是太阳能电池中)的金属接触复合损失。以上所述的金属化结构具有以两层金属化方案使用M1和M2层两者的组合的太阳能电池和MIBS二极管(例如,pn结二极管或肖特基势垒二极管)的金属化和互连。在另一种金属化结构中,M1层处发生MIBS的完全金属化,并且M2仅用于太阳能电池的最终高导电性金属化。这种方法在MIBSpn结或肖特基二极管与小型电池的阵列或平铺的小型电池电池阵列集成从而形成主电池(由串联连接的小型电池或沟槽隔离砖制成的主电池)(如图15中所示)时特别吸引人。M1层处的MIBS的完全金属化还可用于不具有平铺电池的太阳能电池。仅M1MIBS金属化和MIBS二极管(pn结二极管或肖特基势垒二极管)与相关联太阳能电池的互连允许:(i)M2仅专用于通过着落在太阳能电池的指叉型M1指状物上的导电M2-M1通孔插塞进行的太阳能电池金属化和互连;(ii)消除着落在MIBS二极管金属化区域上的M2-M1通孔插塞;(iii)使M2相对于整个MIBS集成太阳能电池周边边缘凹入并偏移,这对于某些M2金属化工艺如当使用镀铜进行的单侧M2镀铜手段时可能有吸引力。图34A是示出具有周边MIBS周缘pn结二极管的背接触/背结太阳能电池(如图16中所示)的仅第一层金属化和MIBS/太阳能电池互连图案(M1)的平面图的图。在图34A的结构中,第一层金属(M1金属化图案)用于仅使用M1来完全互连太阳能电池和相关联MIBpn结二极管,并且因此可利用专门用于最终太阳能电池金属化的任何额外的金属化层(如形成在底板上的M2金属化层),在此情况下,导电M2-M1通孔插塞仅着落在太阳能电池的指叉型发射极和基极M1指状物上并且连接到所述指状物。图34B是出于描述性目的提供的图34A的展开选择图。图34A和图34B的结构包括指叉型太阳能电池基极和发射极金属(M1)(例如铝或铝硅合金)指叉型指状物250以及形成MIBS二极管p+和n型衬底欧姆接触的铝金属化接触。沟槽隔离区域260使太阳能电池与MIBS旁路二极管区域划分并隔离。铝或铝硅合金接触金属定位在太阳能电池的n掺杂区域上、显示为基极金属化指状物256,并且还定位在MIBS旁路二极管的n掺杂区域252上、显示为n掺杂区域金属化接触264(通过n+接触扩散区域进行接触)。铝接触金属定位在太阳能电池的p+掺杂区域上、显示为发射极金属化指状物258,并且还定位在MIBS旁路二极管的p+掺杂区域254上、显示为p+掺杂区域金属化接触262(通过p+接触扩散区域进行接触)。类似地,图34A和图34B可用于针对在n型硅肖特基势垒二极管上使用铝的全周边周缘二极管示出仅第一层金属化和MIBS/太阳能电池互连图案(M1)。如上,在这种情况下,第一层金属(M1金属化图案)用于仅使用M1来完全互连太阳能电池和相关联MIB肖特基势垒二极管,并且因此任何额外的金属化层(如底板上的M2金属化层)可专门用于最终太阳能电池金属化,在此情况下,导电M2-M1通孔插塞仅着落在太阳能电池的指叉型发射极和基极M1指状物上并且连接到所述指状物。在如参考图34A和图34B所述的针对在n型硅肖特基势垒二极管上使用铝的全周边周缘二极管的实现方式的仅第一层金属化和MIBS/太阳能电池互连图案(M1)中,电池包括无母线指叉型太阳能电池基极和发射极金属(铝)欧姆指状物250以及形成MIBS二极管肖特基和欧姆接触的铝金属化接触。铝接触金属定位在太阳能电池的n掺杂区域上、显示为基极金属化欧姆指状物256,并且还定位在MIBS肖特基旁路二极管的欧姆接触n掺杂区域252上、显示为n掺杂区域金属化欧姆接触264(接触n掺杂硅的n+接触扩散区域)。铝接触金属定位在太阳能电池的p+掺杂区域上、显示为发射极金属化欧姆指状物258(通过p+接触扩散区域)。铝肖特基接触金属262定位在MIBS旁路二极管的轻掺杂n型区域254上,例如仅定位在n型表面上。虽然本文已结合使用由多孔硅牺牲和外延硅剥离工艺形成的薄(小于200μm厚度并且薄如小于100μm厚度)晶体硅吸收层以及相关联的连续底板的背接触背结晶体硅太阳能电池描述MIBS实施方案,但是应理解的是,根据所公开主题的MIBS实施方案可应用于其它太阳能电池和PV模块实现方式,包括但不限于以下各项:-由通过无切口薄硅剥落技术(如质子或氢离子灌注和剥落、金属应力引起的薄硅剥落)制造的晶体硅或由浆料或金刚石线锯制成的任何厚度的晶体硅晶片制成的太阳能电池衬底和所得太阳能电池。-使用其它晶体半导体材料如晶体砷化镓、氮化镓、锗、碳化硅、其它化合物半导体等制成的太阳能电池。-非IBC背接触太阳能电池(包括但不限于MWT太阳能电池)。-前接触太阳能电池和包括此类前接触电池的PV模块。-由使用线锯和其它切片技术制成的晶体半导体晶片(如CZ或FZ单晶硅晶片或铸造多晶硅晶片)制成的基于晶片的太阳能电池,包括背接触/背结和前接触太阳能电池两者,其中太阳能电池晶片附接到底板。因为可以实现MIBS实施方案而不会不利地影响最终的模块组件,所以背接触/背结电池在一些应用中可以是有利的。对于各种MIBS实施方案,电池(例如,使用被支撑在底板上的背接触/背结(IBC)太阳能电池如薄晶体半导体)的背面上的发射极和基极互连引线两者的可用性是有利的。此外,本文所公开的太阳能电池实施方案可以用各种材料封装为电池模块,如刚性玻璃覆盖的模块或不具有玻璃罩盖的柔性的轻量光伏模块叠层。提供示例性实施方安的前述描述以使得本领域的任何技术人员能够制造或使用所要求的主题。本领域的技术人员将容易明白对这些实施方案的各种修改,并且本文定义的一般原理可以在不使用创新能力的情况下应用于其它实施方案。因此,所要求的主题不意图局限于本文所示的实施方案,而是根据与本文所公开的原理和新颖特征一致的最宽广范围。