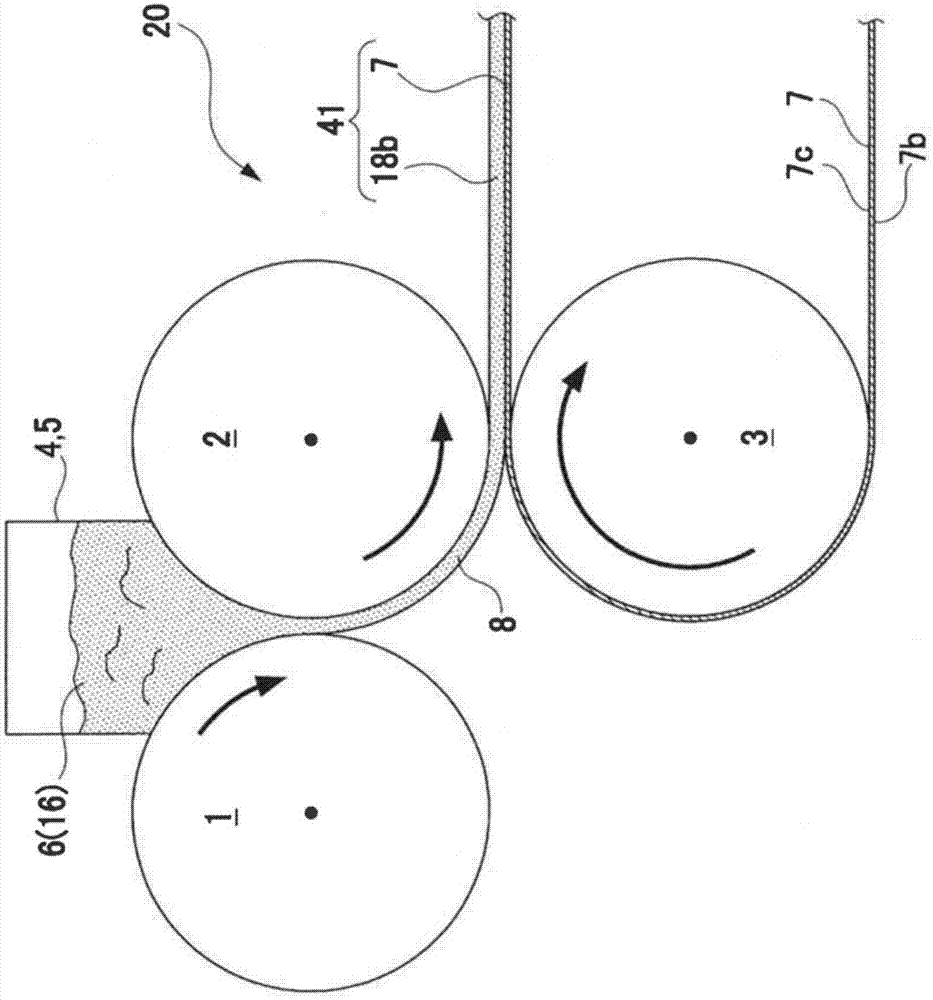
本发明涉及制造构成电池的电极片的方法。详细地说,涉及制造如下的电极片的方法,该电极片在集电箔的第1面上具有第1电极复合材料层且在集电箔的第2面上具有第2电极复合材料层。
背景技术:
:作为电极片(正极片或负极片),已知在集电箔的第1面上具有第1电极复合材料层且在集电箔的第2面上具有第2电极复合材料层的电极片。作为这样结构的电极片的制造方法,已知例如日本特开2013-052353所公开的方法。具体地说,首先,制作包括多个湿润造粒体在内的电极复合材料,所述湿润造粒体通过混合电极活性物质、粘结剂和溶剂并造粒而成。然后,在第1成膜工序中,通过使电极复合材料通过相对向地旋转的第1辊和第2辊的间隙,一边使电极复合材料形成膜状一边使膜状的电极复合材料附着于第2辊的表面。而且,一边使由与第2辊相对向地旋转的第3辊输送的集电箔的第2面与第3辊的表面相接触,一边使集电箔通过第2辊和第3辊的间隙,由此使附着于第2辊的表面的膜状的电极复合材料一边加压一边接触到集电箔的第1面而转印到第1面上,制作在集电箔的第1面上形成了第1电极复合材料层的带第1电极复合材料层的集电箔。而且,在第2成膜工序中,通过使电极复合材料通过相对向地旋转的第4辊和第5辊的间隙,一边使电极复合材料形成膜状一边使膜状的电极复合材料附着于第5辊的表面。而且,一边使由与第5辊相对向地旋转的第6辊输送的带第1电极复合材料层的集电箔的第1电极复合材料层与第6辊的表面相接触,一边使带第1电极复合材料层的集电箔通过第5辊和第6辊的间隙,由此使附着于第5辊的表面的膜状的电极复合材料一边加压一边接触到集电箔的第2面而转印到集电箔的第2面上,制作在带第1电极复合材料层的集电箔的第2面上形成了第2电极复合材料层的电极片。技术实现要素:可是,在上述那样制作的电极片中,有时在集电箔的第1面上形成的第1电极复合材料层的密度比在集电箔的第2面上形成的第2电极复合材料层的密度高,从而在两电极复合材料层之间会产生大的密度差。其原因是:第1电极复合材料层是在第1成膜工序中将电极复合材料在第2辊与第3辊之间压缩而形成的,而该第1电极复合材料层在第2成膜工序中在形成第2电极复合材料层时又在第5辊与第6辊之间被压缩,所以,压缩率比第2电极复合材料层的要高(空隙率低)。因此,在上述那样制作的电极片中,第1电极复合材料层的密度变得比第2电极复合材料层的密度高。存在如下倾向:第1电极复合材料层与第2电极复合材料层之间的密度差越大的电极片,则使用了该电极片的电池的劣化就变得越早。因此,在上述那样制作的电极片中,谋求减小第1电极复合材料层与第2电极复合材料层之间的密度差。本发明提供一种能够减小第1电极复合材料层与第2电极复合材料层之间的密度差的电极片的制造方法。本发明的一个方式是一种电极片的制造方法,制造电极片,该电极片在具有第1面和第2面的集电箔的所述第1面上具有第1电极复合材料层且在所述第2面上具有第2电极复合材料层,所述制造方法的特征在于,包括:第1成膜,使包括将电极活性物质、粘结剂和溶剂混合并造粒而成的多个湿润造粒体的电极复合材料通过相对向地旋转的第1辊和第2辊的间隙,由此一边使所述电极复合材料形成为膜状、一边使形成为膜状的所述电极复合材料附着于所述第2辊的表面,并且,一边使由与所述第2辊相对向地旋转的第3辊输送的所述集电箔的所述第2面与所述第3辊的表面相接触、一边使所述集电箔通过所述第2辊和所述第3辊的间隙,由此使附着于所述第2辊的表面的膜状的所述电极复合材料一边加压一边接触到所述集电箔的所述第1面而转印到所述第1面上,制作在所述集电箔的所述第1面形成了所述第1电极复合材料层的带第1电极复合材料层的集电箔;第2成膜,使所述电极复合材料通过相对向地旋转的第4辊和第5辊的间隙,由此一边使所述电极复合材料形成为膜状、一边使形成为膜状的所述电极复合材料附着于所述第5辊的表面,并且,一边使由与所述第5辊相对向地旋转的第6辊输送的所述带第1电极复合材料层的集电箔的所述第1电极复合材料层与所述第6辊的表面相接触、一边使所述带第1电极复合材料层的集电箔通过所述第5辊和所述第6辊的间隙,由此使附着于所述第5辊的表面的膜状的所述电极复合材料一边加压一边接触到所述带第1电极复合材料层的集电箔的所述第2面而转印到所述第2面上,制作在所述第2面形成了所述第2电极复合材料层的所述电极片;以及辊轧,使所述电极片通过相对向地旋转的第7辊和第8辊的间隙,由此在所述第1电极复合材料层和所述第2电极复合材料层的厚度方向压缩所述第1电极复合材料层和所述第2电极复合材料层;其中,在进行所述辊轧时,配置于所述第1电极复合材料层侧并与所述第1电极复合材料层相接触的所述第7辊的表面温度t7和配置于所述第2电极复合材料层侧并与所述第2电极复合材料层相接触的所述第8辊的表面温度t8满足t7<t8的关系。在上述的制造方法中,通过进行上述那样的第1成膜和第2成膜来制作电极片(轧制之前)。在相关技术中这样制作的电极片中,在集电箔的第1面上形成的第1电极复合材料层的密度比在集电箔的第2面上形成的第2电极复合材料层的密度大,从而在两电极复合材料层之间会产生大的密度差。而与之相对地,在上述的制造方法中,在第2成膜之后具有辊轧,使电极片通过相对向地旋转的第7辊和第8辊的间隙,由此在第1电极复合材料层和第2电极复合材料层的厚度方向压缩所述第1电极复合材料层和所述第2电极复合材料层。而且,在进行该辊轧中,配置于第1电极复合材料层侧并与第1电极复合材料层相接触的第7辊的表面温度t7和配置于第2电极复合材料层侧并与第2电极复合材料层相接触的第8辊的表面温度t8满足t7<t8的关系。这样,使与密度相对低的第2电极复合材料层相接触的第8辊的表面温度t8比与密度相对高的第1电极复合材料层相接触的第7辊的表面温度t7高,由此,能够使第2电极复合材料层的温度比第1电极复合材料层的温度高地进行压缩。由此,在进行辊轧中,能够使第2电极复合材料层比第1电极复合材料层柔软来进行压缩,从而第2电极复合材料层比第1电极复合材料层更易压缩。结果,在进行了辊轧后的电极片中,与进行辊轧之前的电极片相比,第1电极复合材料层与第2电极复合材料层之间的密度差变小。如以上说明的那样,根据上述的电极片制造方法,能够减小第1电极复合材料层与第2电极复合材料层之间的密度差。此外,进行第1成膜能够采用例如具有第1辊、第2辊和第3辊的辊成膜装置来进行。另外,进行第2成膜能够采用例如具有第4辊、第5辊和第6辊的辊成膜装置来进行。另外,进行第1成膜所采用的辊成膜装置和进行第2成膜所采用的辊成膜装置可以是同一辊成膜装置。在此情况下,第1辊和第4辊为同一辊,第2辊和第5辊为同一辊,第3辊和第6辊为同一辊。但是,在进行第2成膜中,使第2辊和第3辊的间隙(第5辊和第6辊的间隙)比进行第1成膜中的间隙大地加以使用。这是因为,与在进行第1成膜中通到第2辊和第3辊的间隙的集电箔相比,在进行第2成膜中通到第5辊和第6辊的间隙的带第1电极复合材料层的集电箔的厚度厚。另外,湿润造粒体是指在溶剂被电极活性物质的粒子和粘结剂保持(吸收)的状态下它们集合(结合)而成的物质(粒状体)。另外,在上述的制造方法中,在进行第1成膜之后,在进行第2成膜之前,可以设有使在第1面上形成的第1电极复合材料层干燥的第1干燥。而且,在进行第2成膜之后,在进行辊轧之前,可以设有使第2面上的第2电极复合材料层干燥的第2干燥。而且,上述的电极片的制造方法可以是如下的电极片的制造方法:在进行所述辊轧时,将所述第7辊的表面温度t7保持为与比所述电极复合材料所含的所述粘结剂的软化温度ts低50℃的温度即(ts-50)℃相比低的温度,将所述第8辊的表面温度t8保持为所述(ts-50)℃以上的温度。在上述的制造方法中,在进行辊轧中,将第7辊的表面温度t7保持为与比电极复合材料所含的粘结剂的软化温度ts低50℃的温度即(ts-50)℃相比低的温度。而且,将第8辊的表面温度t8保持为(ts-50)℃以上的温度。也就是说,在将与密度相对高的第1电极复合材料层相接触的第7辊的表面温度t7设为比(ts-50)℃低的温度、且将与密度相对低的第2电极复合材料层相接触的第8辊的表面温度t8设为(ts-50)℃以上的温度的状态下,进行辊轧工序。通过将与第2电极复合材料层相接触的第8辊的表面温度t8设为(ts-50)℃以上的温度,能够使第2电极复合材料层所含的粘结剂柔软,能够提高第2电极复合材料层的压缩率。另一方面,通过将与第1电极复合材料层相接触的第7辊的表面温度t7设为比(ts-50)℃低的温度,能够抑制第1电极复合材料层所含的粘结剂变柔软,从而能够使辊轧中的第1电极复合材料层的压缩率比第2电极复合材料层的压缩率低。结果,在进行了辊轧后的正极片中,与进行辊轧之前的正极片相比,第1电极复合材料层与第2电极复合材料层之间的密度差变小。此外,作为电极复合材料所含的粘结剂,能够举出例如pvdf(聚1,1-二氟乙烯)。pvdf的软化温度ts为150℃。因此,在使用pvdf作为粘结剂的情况下,将第7辊的表面温度t7设为比(ts-50)=150-50=100℃低的温度,将第8辊的表面温度t8设为(ts-50)=100℃以上的温度。而且,上述任一的电极片的制造方法可以是如下的电极片的制造方法:在进行所述辊轧时,将所述第7辊的表面温度t7保持为15~35℃的范围内的温度。在上述的制造方法中,在进行辊轧中,将第7辊的表面温度t7保持为15~35℃的范围内的温度(即,常温)。这样,通过将与第1电极复合材料层相接触的第7辊的表面温度t7设为15~35℃的范围内的温度,在辊轧时,能够抑制第1电极复合材料层所含的粘结剂变柔软,从而能够使进行辊轧而得的第1电极复合材料层的压缩率比第2电极复合材料层的压缩率低。由此,在进行了辊轧后的电极片中,与进行辊轧之前的电极片相比,能够减小第1电极复合材料层与第2电极复合材料层之间的密度差。而且,上述任一的电极片的制造方法可以是如下的电极片的制造方法:所述第7辊和所述第8辊的直径为300mm以上。在上述的制造方法中,采用直径(外径)为300mm以上的第7辊和第8辊来进行辊轧。对于采用直径为300mm以上的第7辊和第8辊,以第7辊的表面温度t7和第8辊的表面温度t8满足t7<t8的关系的方式进行辊轧,由此能够有效地提高该辊轧中的第2电极复合材料层的压缩率。由此,能够进一步减小第1电极复合材料层与第2电极复合材料层之间的密度差。具体地说,越增加第7辊和第8辊的直径,则在通过电极片通到第7辊和第8辊的间隙来进行轧制时,第1电极复合材料层和第2电极复合材料层越容易在所述第1电极复合材料层和所述第2电极复合材料层的厚度方向被压缩而越难以在长度方向伸长。这是因为:越增加第7辊和第8辊的直径,则从第7辊和第8辊向第1电极复合材料层和第2电极复合材料层施加的力就越难以在第7辊和第8辊的间隙的位置处在第7辊和第8辊的旋转方向(即,第1电极复合材料层和第2电极复合材料层的长度方向)上施加,而易于在第1电极复合材料层和第2电极复合材料层的厚度方向上施加。因此,在第7辊的表面温度t7和第8辊的表面温度t8满足t7<t8的关系而使得第2电极复合材料层比第1电极复合材料层更易于变形的状态下,采用直径为300mm以上的第7辊和第8辊来进行辊轧,由此与进行辊轧而得的第1电极复合材料层的压缩率相比,能够更有效地提高进行辊轧而得的第2电极复合材料层的压缩率。由此,能进一步减小第1电极复合材料层与第2电极复合材料层之间的密度差。此外,第7辊和第8辊的直径的上限值没有特别限定,但由于优选进行辊轧的轧制装置较小,所以,优选第7辊和第8辊的直径为500mm以下。附图说明以下,将参照附图对本发明的示例性的实施例的特征、优点以及技术和产业的意义进行描述,其中,用相似的符号表示相似的元件。图1是实施方式的第1辊成膜装置的概略图。图2是实施方式的第1辊成膜装置的立体图。图3是表示实施方式的电极片的制造方法的流程的流程图。图4是实施方式的第1辊成膜装置和第1干燥装置的概略图。图5是实施方式的第2辊成膜装置的概略图。图6是实施方式的第2辊成膜装置的立体图。图7是实施方式的第2辊成膜装置和第2干燥装置的概略图。图8是实施方式的轧制装置的概略图。具体实施方式以下,参照附图,对将本发明具体化了的实施方式进行详细地说明。本实施方式是将本发明适用于锂离子二次电池的正极片(电极片)的制造。在本实施方式中,作为用于形成正极片的正极复合材料层(电极复合材料层)的正极复合材料(电极复合材料)的材料,使用正极活性物质(电极活性物质)、导电材料、粘结剂和溶剂。此外,在本实施方式中,作为正极活性物质,采用粉末状的锂过渡金属复合氧化物(具体地说,lini1/3mn1/3co1/3o2)。另外,作为导电材料,采用粉末状的乙炔黑。另外,作为粘结剂,采用pvdf(聚1,1-二氟乙烯(聚偏氟乙烯))。另外,作为溶剂,采用nmp(n-甲基吡咯烷酮)。在本实施方式中,在电极复合材料制作工序中,一边将上述各材料混炼一边造粒来制作很多湿润造粒体16,并且,制作包括很多湿润造粒体16的正极复合材料6(电极复合材料)。然后,在第1成膜工序中,使该正极复合材料6呈膜状地附着(涂敷)到集电箔7的第1面7b上,从而制作在集电箔7的第1面7b上形成了第1正极复合材料层18b(第1电极复合材料层)的带第1正极复合材料层的集电箔41(带第1电极复合材料层的集电箔)。然后,在第1干燥工序中,使集电箔7的第1面7b上的第1正极复合材料层18b(第1电极复合材料层)干燥。接下来,在第2成膜工序中,使正极复合材料6呈膜状地附着(涂敷)到带第1正极复合材料层的集电箔41的第2面7c上,从而制作在第2面7c上形成了第2正极复合材料层18c(第2电极复合材料层)的正极片19(电极片)。然后,在第2干燥工序中,使第2面7c上的第2正极复合材料层18c(第2电极复合材料层)干燥。然后,在辊轧工序中,将正极片19的第1正极复合材料层18b和第2正极复合材料层18c在其厚度方向进行压缩。由此,得到第1正极复合材料层18b和第2正极复合材料层18c的密度提高了的正极片19(电极片)。在此,对本实施方式的电极片(正极片19)的制造方法进行详细地说明。图1是实施方式的第1辊成膜装置20的概略图。图2是第1辊成膜装置20的立体图。图3是表示实施方式的电极片(正极片19)的制造方法的流程的流程图。图4是实施方式的第1辊成膜装置20和第1干燥装置50的概略图。图5是实施方式的第2辊成膜装置30的概略图。图6是第2辊成膜装置30的立体图。图7是实施方式的第2辊成膜装置30和第2干燥装置70的概略图。图8是实施方式的轧制装置60的概略图。如图3所示,首先,在步骤s1(电极复合材料制作工序)中,一边将正极活性物质(lini1/3mn1/3co1/3o2)、导电材料(乙炔黑)、粘结剂(pvdf)和溶剂(nmp)混合一边造粒,制作很多湿润造粒体16,并且制作包括很多湿润造粒体16的正极复合材料6。在本实施方式中,在公知的搅拌造粒机(未图示)内,投入正极活性物质、导电材料、粘结剂和溶剂并搅拌,由此一边将它们混合(分散)一边造粒而形成很多湿润造粒体16。由此,得到包括很多湿润造粒体16的正极复合材料6。此外,湿润造粒体16是在作为溶剂的nmp被多个正极活性物质的颗粒和粘结剂保持(吸收)的状态下它们集合(结合)而成的物质(粒状体)。正极复合材料6是这样的湿润造粒体16的集合体。然后,前进到步骤s2(第1成膜工序),使在步骤s1(电极复合材料制作工序)制作出的正极复合材料6形成为膜状,使形成为膜状的正极复合材料6附着于集电箔7的第1面上,从而制作在集电箔7的第1面7b上形成了第1正极复合材料层18b(第1电极复合材料层)的带第1正极复合材料层的集电箔41(带第1电极复合材料层的集电箔)。此外,在本实施方式中,采用图1和图2所示的第1辊成膜装置20来进行步骤s2(第1成膜工序)。如图1和图2所示,第1辊成膜装置20具有第1辊1、第2辊2和第3辊3这3个辊。第1辊1和第2辊2在水平方向(在图1中为左右方向)并列配置。另一方面,第2辊2和第3辊3在垂直方向(在图1中为上下方向)并列配置。另外,第1辊1和第2辊2隔着微小的间隔而相面对(相对向)。同样地,第2辊2和第3辊3也隔着微小的间隔而相面对(相对向)。而且,在第1辊1和第2辊2的相面对部位的上侧,分隔板4、5在辊的宽度方向(轴方向,在图1中为与纸面正交的方向)分开地配置。另外,这3个辊1~3的旋转方向如图1和图2中箭头所示被设定成,相邻(相面对的)的2个辊的旋转方向相互成为反方向、即相面对的2个辊相互成为顺向旋转。并且,被设定成,在第1辊1和第2辊2的相面对部位,这些辊的表面通过旋转而向下移动。另外,被设定成,在第2辊2和第3辊3的相面对部位,这些辊的表面通过旋转而向右移动。另外,关于旋转速度,辊的表面由于旋转的移动速度被设定成,在第1辊1处为最慢,在第3辊3处为最快,在第2辊2处为它们的中间。在这样的第1辊成膜装置20中,在位于第1辊1和第2辊2的相面对部位之上的分隔板4与分隔板5之间的收容空间内,投入在步骤s1(电极复合材料制作工序)中制作的正极复合材料6。另外,在第3辊3绕挂(架设)集电箔7。此外,在步骤s2(第1成膜工序)中,以集电箔7的第2面7c与第3辊3的表面相接触(换言之,第1面7b朝向第3辊3的径向外侧)的方式,在第3辊3绕挂集电箔7。集电箔7是具有第1面7b(表面)和第2面7c(里面)的金属箔(铝箔)。该集电箔7随着第3辊3的旋转而通过第2辊2和第3辊3的相面对部位(间隙),被从第3辊3的右下向右上输送。另外,在集电箔7通到第2辊2和第3辊3的相面对部位(间隙)的状态下,在第2辊2与集电箔7之间仍存在一些缝隙。也就是说,第2辊2与第3辊3之间的缝隙(不存在集电箔7的状态下的缝隙)比集电箔7的厚度稍大。在该步骤s2(第1成膜工序)中,通过使正极复合材料6通过相对向地旋转的第1辊1和第2辊2的间隙,一边使正极复合材料6形成为膜状一边使形成为膜状的正极复合材料6附着于第2辊2的表面。与此同时,一边使由与第2辊2相对向地旋转的第3辊3输送的集电箔7的第2面2c与第3辊3的表面相接触,一边使集电箔7通过第2辊2和第3辊3的间隙,由此使附着于第2辊2的表面的膜状的正极复合材料6一边加压一边接触到集电箔7的第1面7b而转印到第1面7b上。此外,膜状的正极复合材料6在通过第2辊2和第3辊3的间隙时(即,转印到集电箔7的第1面7b上时),在其厚度方向上被压缩,从而其密度提高。更具体地说,首先,在第1辊成膜装置20的分隔板4与分隔板5之间的收容空间内,投入在步骤s1(电极复合材料制作工序)中制作的正极复合材料6。投入的正极复合材料6被供给到相对向地旋转的第1辊1和第2辊2的相面对部位的间隙内,通过第1辊1和第2辊2的旋转而经过两辊1、2之间的间隙而成为膜状(参照图1、图2)。此时,第2辊2的旋转速度比第1辊1的旋转速度快,所以,相比第1辊1的表面,正极复合材料6(湿润造粒体16)在第2辊2的表面被更大地拉伸,从而第2辊2表面处的液桥面积比第1辊1表面处的液桥面积大,由此正极复合材料6(湿润造粒体16)被担载(附着)于第2辊2的表面。并且,担载(附着)于第2辊2的表面的膜状的正极复合材料6(将其称为第1膜状正极复合材料8)随着第2辊2的旋转而被输送(参照图1、图2)。于是,在第2辊2和第3辊3的相面对部位,集电箔7的第1面7b和第1膜状正极复合材料8相遇,在第2辊2与第3辊3之间夹着集电箔7和第1膜状正极复合材料8。此外,第2辊2和第3辊3的相面对部位处的间隙尺寸(最小间隙尺寸)比集电箔7的厚度和第1膜状正极复合材料8的厚度之和小。因此,在第2辊2与第3辊3之间夹着集电箔7和第1膜状正极复合材料8时,从第2辊2的表面朝向集电箔7的第1面7b对第1膜状正极复合材料8施加按压载荷。由此,能够使附着于第2辊2的表面的第1膜状正极复合材料8一边加压一边接触到集电箔7的第1面7b,所以,第1膜状正极复合材料8从第2辊2转印(附着)到随着第3辊3一起旋转的集电箔7的第1面7b上。此时,第1膜状正极复合材料8在其厚度方向上被压缩而成为第1正极复合材料层18b,从而得到在集电箔7的第1面7b上形成了第1正极复合材料层18b的带第1正极复合材料层的集电箔41(带第1电极复合材料层的集电箔)。然后,前进到步骤s3(第1干燥工序),使带第1正极复合材料层的集电箔41干燥(使第1正极复合材料层18b干燥)。具体地说,如图4所示,使带第1正极复合材料层的集电箔41通过第1干燥装置50(干燥炉)的内部,由此使在集电箔7的第1面7b上形成的第1正极复合材料层18b干燥。由此,除去(蒸发)被第1正极复合材料层18b(湿润造粒体16)吸收(保持)的溶剂。然后,前进到步骤s4(第2成膜工序),使正极复合材料6呈膜状地附着(涂敷)到带第1正极复合材料层的集电箔41的第2面7c上,从而制作在集电箔7的第2面7c上形成了第2正极复合材料层18c(第2电极复合材料层)的正极片19(电极片)。此外,在本实施方式中,采用图5和图6所示的第2辊成膜装置30来进行步骤s4(第2成膜工序)。以下进行详细地说明。如图5和图6所示,第2辊成膜装置30具有第4辊31、第5辊32和第6辊33这3个辊。第4辊31和第5辊32在水平方向(在图5中为左右方向)并列配置。另一方面,第5辊32和第6辊33在垂直方向(在图5中为上下方向)并列配置。另外,第4辊31和第5辊32隔着微小的间隔而相面对(相对向)。同样地,第5辊32和第6辊33也隔着微小的间隔而相面对(相对向)。而且,在第4辊31和第5辊32的相面对部位的上侧,分隔板4、5在辊的宽度方向(轴方向,在图5中为与纸面正交的方向)分开地配置。此外,第2辊成膜装置30是将前述的第1辊成膜装置20稍稍扩大了第2辊2和第3辊3的相面对部位处的间隙尺寸而得的,除此之外与第1辊成膜装置20完全相同。因此,第4辊31是第1辊1的等同品,第5辊32是第2辊2的等同品,第6辊33是第3辊3的等同品。在这样的第2辊成膜装置30中,在分隔板4与分隔板5之间的收容空间内,投入在步骤s1(电极复合材料制作工序)中制作的正极复合材料6。另外,在第6辊33绕挂进行了步骤s3(第1干燥工序)的处理的带第1正极复合材料层的集电箔41。详细地说,以使带第1正极复合材料层的集电箔41的第1正极复合材料层18b与第6辊33的表面相接触(换言之,第2面7c朝向第6辊33的径向外侧)的方式,在第6辊33绕挂带第1正极复合材料层的集电箔41。带第1正极复合材料层的集电箔41随着第6辊33的旋转而通过第5辊32和第6辊33的相面对部位(间隙),被从第6辊33的右下向右上输送。另外,在带第1正极复合材料层的集电箔41通到第5辊32和第6辊33的相面对部位(间隙)的状态下,在第5辊32与带第1正极复合材料层的集电箔41之间仍存在一些缝隙。也就是说,第5辊32与第6辊33之间的缝隙(不存在带第1正极复合材料层的集电箔41的状态下的缝隙)比带第1正极复合材料层的集电箔41的厚度稍大。在该步骤s4(第2成膜工序)中,通过使正极复合材料6通过相对向地旋转的第4辊31和第5辊32的间隙,一边使正极复合材料6形成为膜状一边使形成为膜状的正极复合材料6附着于第5辊32的表面。与此同时,一边使由与第5辊32相对向地旋转的第6辊33输送的带第1正极复合材料层的集电箔41的第1正极复合材料层18b与第6辊33的表面相接触,一边使带第1正极复合材料层的集电箔41通过第5辊32和第6辊33的间隙,由此使附着于第5辊32的表面的膜状的正极复合材料6一边加压一边接触到带第1正极复合材料层的集电箔41的第2面7c而转印到第2面7c上。此外,膜状的正极复合材料6在通过第5辊32和第6辊33的间隙时(即,转印到集电箔7的第2面7c上时),在其厚度方向上被压缩,从而其密度提高。更具体地说,首先,在第2辊成膜装置30的分隔板4与分隔板5之间的收容空间内,投入在步骤s1(电极复合材料制作工序)中制作的正极复合材料6。投入的正极复合材料6被供给到相对向地旋转的第4辊31和第5辊32的相面对部位的间隙内,通过第4辊31和第5辊32的旋转而经过两辊之间的间隙而成为膜状,并且,担载(附着)于第5辊32的表面(参照图5和图6)。并且,担载(附着)于第5辊32的表面的膜状的正极复合材料6(将其称为第2膜状正极复合材料48)随着第5辊32的旋转而被输送(参照图5和图6)。于是,在第5辊32和第6辊33的相面对部位,带第1正极复合材料层的集电箔41的第2面7c和第2膜状正极复合材料48相遇,在第5辊32与第6辊33之间夹着带第1正极复合材料层的集电箔41和第2膜状正极复合材料48。此外,第5辊32和第6辊33的相面对部位处的间隙尺寸(最小间隙尺寸)比带第1正极复合材料层的集电箔41的厚度和第2膜状正极复合材料48的厚度之和小。因此,在第5辊32与第6辊33之间夹着带第1正极复合材料层的集电箔41和第2膜状正极复合材料48时,从第5辊32的表面朝向带第1正极复合材料层的集电箔41的第2面7c对第2膜状正极复合材料48施加按压载荷。由此,能够使附着于第5辊32的表面的第2膜状正极复合材料48一边加压一边接触到带第1正极复合材料层的集电箔41的第2面7c,所以,第2膜状正极复合材料48从第5辊32转印(附着)到随着第6辊33一起旋转的带第1正极复合材料层的集电箔41的第2面7c上。此时,第2膜状正极复合材料48在其厚度方向上被压缩而成为第2正极复合材料层18c,由此在集电箔7的第2面7c上形成第2正极复合材料层18c而得到正极片19。然后,前进到步骤s5(第2干燥工序),使正极片19(第2正极复合材料层18c)干燥。具体地说,如图7所示,使正极片19通过第2干燥装置70(干燥炉)的内部,由此使在集电箔7的第2面7c上形成的第2正极复合材料层18c干燥。由此,除去(蒸发)被第2正极复合材料层18c(湿润造粒体16)吸收(保持)的溶剂。在上述那样制作的正极片19中,有时在集电箔7的第1面7b上形成的第1正极复合材料层18b的密度比在集电箔7的第2面7c上形成的第2正极复合材料层18c的密度高,从而在两电极复合材料层之间产生大的密度差。其原因是:第1正极复合材料层18b是在第1成膜工序(步骤s2)中将正极复合材料6在第2辊2与第3辊3之间压缩而形成的,而该第1正极复合材料层18b在第2成膜工序(步骤s4)中在形成第2正极复合材料层18c时又在第5辊32与第6辊33之间被压缩,所以,压缩率比第2正极复合材料层18c的要高(空隙率低)。因此,在上述那样制作的正极片19中,存在第1正极复合材料层18b的密度变得比第2正极复合材料层18c的密度高的倾向。针对于此,在本实施方式的制造方法中,在步骤s5(第2干燥工序)后,具有使正极片19通到相对向地旋转的第7辊61和第8辊62的间隙而将第1正极复合材料层18b和第2正极复合材料层18c在其厚度方向进行压缩的步骤s6(辊轧工序)(参照图3)。具体地说,在步骤s6(辊轧工序)中,采用具有一对辊(第7辊61和第8辊62)的轧制装置60(参照图8)来压缩正极片19的第1正极复合材料层18b和第2正极复合材料层18c。此外,第7辊61和第8辊62的相面对部位处的间隙尺寸(最小间隙尺寸)比在步骤s5(第2干燥工序)中制作的正极片19的厚度小。如图8所示,本实施方式的轧制装置60具有第7辊61、第8辊62、测定第7辊61的表面(与第1正极复合材料层18b相接触的面)的温度t7的第1温度传感器141、以及测定第8辊62的表面(与第2正极复合材料层18c相接触的面)的温度t8的第2温度传感器142。而且,轧制装置60具有用于将第7辊61的表面(与第1正极复合材料层18b相接触的面)的温度t7保持为第1温度的第1冷却器110、将第8辊62的表面(与第2正极复合材料层18c相接触的面)的温度t8保持为第2温度(比第1温度高的温度)的第2冷却器120、以及用于加热第8辊62的表面的加热器130。第1冷却器110具有供热介质循环的循环路径112和控制热介质的温度的第1本体部111。第1本体部111基于由第1温度传感器141测定出的第7辊61的表面温度t7来调整在循环路径112循环的热介质的温度,以将第7辊61的表面温度t7保持为第1温度。由此,在本实施方式的轧制装置60中,能够将第7辊61的表面温度t7保持为第1温度。另外,第2冷却器120具有供热介质循环的循环路径122和控制热介质的温度的第2本体部121。第2本体部121基于由第2温度传感器142测定出的第8辊62的表面温度t8来调整在循环路径122循环的热介质的温度,以将第8辊62的表面温度t8保持为第2温度。另外,加热器130是ih加热器,具有发热部132、133和控制器131。控制器131基于由第2温度传感器142测定出的第8辊62的表面温度t8来调整发热部132、133的发热量,以将第8辊62的表面温度t8保持为第2温度。由此,在本实施方式的轧制装置60中,能够将第8辊62的表面温度t8保持为比第1温度高的第2温度。采用这样的轧制装置60,在本实施方式的辊轧工序(步骤s6)中,设为配置于第1正极复合材料层18b侧并与第1正极复合材料层18b相接触的第7辊61的表面温度t7和配置于第2正极复合材料层18c侧并与第2正极复合材料层18c相接触的第8辊62的表面温度t8满足t7<t8的关系,来压缩正极片19的第1正极复合材料层18b和第2正极复合材料层18c。这样,使与密度相对低的第2正极复合材料层18c相接触的第8辊62的表面温度t8比与密度相对高的第1正极复合材料层18b相接触的第7辊61的表面温度t7高,由此,能够使第2正极复合材料层18c的温度比第1正极复合材料层18b的温度高地进行压缩。由此,在辊轧工序(步骤s6)中,能够使第2正极复合材料层18c比第1正极复合材料层18b柔软地进行压缩,从而第2正极复合材料层18c比第1正极复合材料层18b更易压缩。结果,在进行了辊轧工序(步骤s6)后的正极片19中,与进行辊轧工序之前的正极片19相比,第1正极复合材料层18b与第2正极复合材料层18c之间的密度差变小。详细地说,在本实施方式的辊轧工序(步骤s6)中,将第7辊61的表面温度t7保持为与比正极复合材料6所含的粘结剂的软化温度ts低50℃的温度即(ts-50)℃相比低的温度。另一方面,将第8辊62的表面温度t8保持为(ts-50)℃以上的温度。也就是说,在将与密度相对高的第1正极复合材料层18b相接触的第7辊61的表面温度t7保持为比(ts-50)℃低的第1温度、且将与密度相对低的第2正极复合材料层18c相接触的第8辊62的表面温度t8保持为(ts-50)℃以上的第2温度的状态下,进行辊轧工序。通过将与第2正极复合材料层18c相接触的第8辊62的表面温度t8保持为(ts-50)℃以上的第2温度,能够使第2正极复合材料层18c所含的粘结剂柔软而能够提高第2正极复合材料层18c的压缩率。另一方面,通过将与第1正极复合材料层18b相接触的第7辊61的表面温度t7保持为比(ts-50)℃低的第1温度,能够抑制第1正极复合材料层18b所含的粘结剂变柔软,从而能够使辊轧工序中的第1正极复合材料层18b的压缩率比辊轧工序中的第2正极复合材料层18c的压缩率低。结果,在进行了辊轧工序(步骤s6)后的正极片19中,与进行辊轧工序之前的正极片19相比,第1正极复合材料层18b与第2正极复合材料层18c之间的密度差变小。此外,在本实施方式中,作为粘结剂,采用pvdf(聚1,1-二氟乙烯)。pvdf的软化温度ts为150℃。因此,在本实施方式辊轧工序(步骤s6)中,利用第1冷却器110,进行温度调整使得第7辊61的表面温度t7为比(ts-50)=150-50=100℃低的第1温度,利用第2冷却器120和加热器130,进行温度调整使得第8辊62的表面温度t8为(ts-50)=100℃以上的第2温度。更详细地说,在本实施方式的辊轧工序(步骤s6)中,利用第1冷却器110,将第7辊61的表面温度t7保持为15~35℃的范围内的温度(即,常温)。这样,通过将与第1正极复合材料层18b相接触的第7辊61的表面温度t7保持为15~35℃的范围内的温度,能够抑制在辊轧时第1正极复合材料层18b所含的粘结剂(pvdf)变柔软,从而能够使辊轧工序(步骤s6)中的第1正极复合材料层18b的压缩率比辊轧工序(步骤s6)中的第2正极复合材料层18c的压缩率低。由此,在进行了辊轧工序(步骤s6)后的正极片19中,与进行辊轧工序之前的正极片19相比,能够减小第1正极复合材料层18b与第2正极复合材料层18c之间的密度差。上述那样制作出的正极片19例如能够用作锂离子二次电池的正极片。具体地说,例如,正极片19与负极片和分隔件组合而形成电极体。接着,将端子部件安装于该电极体后,在电池盒内收容电极体和电解液。由此,完成锂离子二次电池。(实施例1~7和比较例1)在实施例1~7和比较例1中,在步骤s6(辊轧工序)中,仅在使第7辊61的表面温度t7和第8辊62的表面温度t8不同这一点不同,其它都相同,来制作正极片19。具体地说,在实施例1中,在步骤s6(辊轧工序)中,将第7辊61的表面温度t7保持为25℃、且将第8辊62的表面温度t8保持为100℃,压缩正极片19的第1正极复合材料层18b和第2正极复合材料层18c。另外,在实施例2中,在步骤s6(辊轧工序)中,将第7辊61的表面温度t7保持为25℃、且将第8辊62的表面温度t8保持为150℃,压缩正极片19的第1正极复合材料层18b和第2正极复合材料层18c。另外,在实施例3中,在步骤s6(辊轧工序)中,将第7辊61的表面温度t7保持为25℃、且将第8辊62的表面温度t8保持为200℃,压缩正极片19的第1正极复合材料层18b和第2正极复合材料层18c。另外,在实施例4中,在步骤s6(辊轧工序)中,将第7辊61的表面温度t7保持为35℃、且将第8辊62的表面温度t8保持为200℃,压缩正极片19的第1正极复合材料层18b和第2正极复合材料层18c。另外,在实施例5中,在步骤s6(辊轧工序)中,将第7辊61的表面温度t7保持为15℃、且将第8辊62的表面温度t8保持为200℃,压缩正极片19的第1正极复合材料层18b和第2正极复合材料层18c。另外,在实施例6中,在步骤s6(辊轧工序)中,将第7辊61的表面温度t7保持为35℃、且将第8辊62的表面温度t8保持为100℃,压缩正极片19的第1正极复合材料层18b和第2正极复合材料层18c。另外,在实施例7中,在步骤s6(辊轧工序)中,将第7辊61的表面温度t7保持为15℃、且将第8辊62的表面温度t8保持为100℃,压缩正极片19的第1正极复合材料层18b和第2正极复合材料层18c。另外,在比较例1中,在步骤s6(辊轧工序)中,将第7辊61的表面温度t7保持为25℃、且将第8辊62的表面温度t8也保持为25℃,压缩正极片19的第1正极复合材料层18b和第2正极复合材料层18c。然后,对实施例1~7和比较例1的正极片19,调查第1正极复合材料层18b与第2正极复合材料层18c之间的密度差(g/cc)。该结果在表1中示出。此外,在实施例1~7和比较例1中,在进行步骤s6(辊轧工序)的处理之前的正极片19中,均是第1正极复合材料层18b的密度比第2正极复合材料层18c的密度高、且第1正极复合材料层18b与第2正极复合材料层18c之间的密度差(g/cc)为0.85(g/cc)。另外,在实施例1~7和比较例1中,采用直径为390mm的第7辊61和第8辊62来进行步骤s6(辊轧工序)的处理。【表1】第7辊的表面温度t7(℃)第8辊的表面温度t8(℃)密度差(g/cc)比较例125250.7实施例1251000.08实施例2251500.05实施例3252000.09实施例4352000.07实施例5152000.07实施例6351000.08实施例7151000.07如表1所示,在比较例1的正极片中,第1正极复合材料层18b与第2正极复合材料层18c之间的密度差为0.7(g/cc)。而与之相对地,在实施例1~7的正极片19中,第1正极复合材料层18b与第2正极复合材料层18c之间的密度差均为0.09(g/cc)以下。如前述那样,在比较例1中,使第7辊61的表面温度t7和第8辊62的表面温度t8为相等的温度(具体地说为25℃)来进行步骤s6(辊轧工序)的处理。而与之相对地,在实施例1~7中,使第8辊62的表面温度t8比第7辊61的表面温度t7高(满足t7<t8的关系)地进行步骤s6(辊轧工序)的处理。由这些结果可知,通过使第8辊62的表面温度t8比第7辊61的表面温度t7高(满足t7<t8的关系)地进行步骤s6(辊轧工序)的处理,与使t7=t8的情况相比,能够减小第1正极复合材料层18b与第2正极复合材料层18c之间的密度差。其原因能够如下考虑。具体地说,使与密度相对低的第2正极复合材料层18c相接触的第8辊62的表面温度t8比与密度相对高的第1正极复合材料层18b相接触的第7辊61的表面温度t7高,由此,能够使第2正极复合材料层18c的温度比第1正极复合材料层18b的温度高地进行压缩。由此,在辊轧工序(步骤s6)中,能够使第2正极复合材料层18c比第1正极复合材料层18b柔软而进行压缩,从而第2正极复合材料层18c比第1正极复合材料层18b更易压缩。尤其是,在实施例1~7中,将第7辊61的表面温度t7保持为与比正极复合材料6所含的粘结剂(pvdf)的软化温度ts(=150℃)低50℃的温度即(ts-50)=100℃相比低的温度。另一方面,将第8辊62的表面温度t8保持为(ts-50)=100℃以上的温度。也就是说,在将与密度相对高的第1正极复合材料层18b相接触的第7辊61的表面温度t7保持为比(ts-50)℃低的第1温度、且将与密度相对低的第2正极复合材料层18c相接触的第8辊62的表面温度t8保持为(ts-50)℃以上的第2温度的状态下,进行辊轧工序。这样,通过将与第2正极复合材料层18c相接触的第8辊62的表面温度t8保持为(ts-50)℃以上的第2温度,能够使第2正极复合材料层18c所含的粘结剂柔软而能够提高第2正极复合材料层18c的压缩率。另一方面,通过将与第1正极复合材料层18b相接触的第7辊61的表面温度t7保持为比(ts-50)℃低的第1温度,能够抑制第1正极复合材料层18b所含的粘结剂变柔软,从而能够使辊轧工序中的第1正极复合材料层18b的压缩率比第2正极复合材料层18c的压缩率低。更详细地说,在实施例1~7中,将第7辊61的表面温度t7保持为15~35℃的范围内的温度(即,常温)。这样,通过将与第1正极复合材料层18b相接触的第7辊61的表面温度t7保持为15~35℃的范围内的温度,能够防止在辊轧时第1正极复合材料层18b所含的粘结剂(pvdf)变柔软,从而能够使辊轧工序(步骤s6)中的第1正极复合材料层18b的压缩率比辊轧工序(步骤s6)中的第2正极复合材料层18c的压缩率低足够多。换言之,能够使辊轧工序(步骤s6)中的第2正极复合材料层18c的压缩率比辊轧工序(步骤s6)中的第1正极复合材料层18b的压缩率高足够多。由此能够认为,在实施例1~7中,通过进行辊轧工序(步骤s6),已使得正极片19中的第1正极复合材料层18b与第2正极复合材料层18c之间的密度差变得极小。(实施例8~10和比较例2)在实施例8~10和比较例2中,在步骤s6(辊轧工序)中,仅在使第7辊61的表面温度t7及第8辊62的表面温度t8不同这一点不同,其它都相同,来制作正极片19。不过,在实施例8~10和比较例2中,与实施例1~7和比较例1不同的是,采用直径为150mm的第7辊61和第8辊62来进行步骤s6(辊轧工序)的处理。具体地说,在实施例8中,在步骤s6(辊轧工序)中,将第7辊61的表面温度t7保持为25℃、且将第8辊62的表面温度t8保持为100℃,压缩正极片19的第1正极复合材料层18b和第2正极复合材料层18c。另外,在实施例9中,在步骤s6(辊轧工序)中,将第7辊61的表面温度t7保持为25℃、且将第8辊62的表面温度t8保持为150℃,压缩正极片19的第1正极复合材料层18b和第2正极复合材料层18c。另外,在实施例10中,在步骤s6(辊轧工序)中,将第7辊61的表面温度t7保持为25℃、且将第8辊62的表面温度t8保持为200℃,压缩正极片19的第1正极复合材料层18b和第2正极复合材料层18c。另外,在比较例2中,在步骤s6(辊轧工序)中,将第7辊61的表面温度t7保持为25℃、且将第8辊62的表面温度t8也保持为25℃,压缩正极片19的第1正极复合材料层18b和第2正极复合材料层18c。然后,对实施例8~10和比较例2的正极片19,调查第1正极复合材料层18b与第2正极复合材料层18c之间的密度差(g/cc)。该结果在表2中示出。此外,在实施例8~10和比较例2中,在进行步骤s6(辊轧工序)的处理之前的正极片19中,均是第1正极复合材料层18b的密度比第2正极复合材料层18c的密度高、且第1正极复合材料层18b与第2正极复合材料层18c之间的密度差(g/cc)为0.85(g/cc)。【表2】第7辊的表面温度t7(℃)第8辊的表面温度t8(℃)密度差(g/cc)比较例225250.68实施例8251000.65实施例9251500.62实施例10252000.57如表2所示,在比较例2的正极片中,第1正极复合材料层18b与第2正极复合材料层18c之间的密度差为0.68(g/cc)。而与之相对地,在实施例8~10的正极片19中,第1正极复合材料层18b与第2正极复合材料层18c之间的密度差均为0.65(g/cc)以下,密度差比比较例2小。如前述那样,在比较例2中,使第7辊61的表面温度t7和第8辊62的表面温度t8为相等的温度(具体地说为25℃)来进行步骤s6(辊轧工序)的处理。而与之相对地,在实施例8~10中,使第8辊62的表面温度t8比第7辊61的表面温度t7高(满足t7<t8的关系)地进行步骤s6(辊轧工序)的处理。由这些结果可知,通过使第8辊62的表面温度t8比第7辊61的表面温度t7高(满足t7<t8的关系)地进行步骤s6(辊轧工序)的处理,与使t7=t8的情况相比,能够减小第1正极复合材料层18b与第2正极复合材料层18c之间的密度差。而且,可知,使第7辊61的表面温度t7为与比正极复合材料6所含的粘结剂(pvdf)的软化温度ts低50℃的温度即(ts-50)℃相比低、且使第8辊62的表面温度t8为(ts-50)℃以上为宜。更具体来说,将第7辊61的表面温度t7设为15~35℃的范围内的温度为宜。(实施例11~13和比较例3)在实施例11~13和比较例3中,在步骤s6(辊轧工序)中,仅在使第7辊61的表面温度t7及第8辊62的表面温度t8不同这一点不同,其它都相同,来制作正极片19。不过,在实施例11~13和比较例3中,与实施例1~7和比较例1不同的是,采用直径为300mm的第7辊61和第8辊62来进行步骤s6(辊轧工序)的处理。具体地说,在实施例11中,在步骤s6(辊轧工序)中,将第7辊61的表面温度t7保持为25℃、且将第8辊62的表面温度t8保持为100℃,压缩正极片19的第1正极复合材料层18b和第2正极复合材料层18c。另外,在实施例12中,在步骤s6(辊轧工序)中,将第7辊61的表面温度t7保持为25℃、且将第8辊62的表面温度t8保持为150℃,压缩正极片19的第1正极复合材料层18b和第2正极复合材料层18c。另外,在实施例13中,在步骤s6(辊轧工序)中,将第7辊61的表面温度t7保持为25℃、且将第8辊62的表面温度t8保持为200℃,压缩正极片19的第1正极复合材料层18b和第2正极复合材料层18c。另外,在比较例3中,在步骤s6(辊轧工序)中,将第7辊61的表面温度t7保持为25℃、且将第8辊62的表面温度t8也保持为25℃,压缩正极片19的第1正极复合材料层18b和第2正极复合材料层18c。然后,对实施例11~13和比较例3的正极片19,调查第1正极复合材料层18b与第2正极复合材料层18c之间的密度差(g/cc)。该结果在表3中示出。此外,在实施例11~13和比较例3中,在进行步骤s6(辊轧工序)的处理之前的正极片19中,均是第1正极复合材料层18b的密度比第2正极复合材料层18c的密度高、且第1正极复合材料层18b与第2正极复合材料层18c之间的密度差(g/cc)为0.85(g/cc)。【表3】第7辊的表面温度t7(℃)第8辊的表面温度t8(℃)密度差(g/cc)比较例325250.68实施例11251000.09实施例12251500.08实施例13252000.1如表3所示,在比较例3的正极片中,第1正极复合材料层18b与第2正极复合材料层18c之间的密度差为0.68(g/cc)。而与之相对地,在实施例11~13的正极片19中,第1正极复合材料层18b与第2正极复合材料层18c之间的密度差均为0.1(g/cc)以下,与比较例3相比,密度差极小。如前述那样,在比较例3中,使第7辊61的表面温度t7和第8辊62的表面温度t8为相等的温度(具体地说为25℃)来进行步骤s6(辊轧工序)的处理。而与之相对地,在实施例11~13中,使第8辊62的表面温度t8比第7辊61的表面温度t7高(满足t7<t8的关系)地进行步骤s6(辊轧工序)的处理。由这些结果可知,通过使第8辊62的表面温度t8比第7辊61的表面温度t7高(满足t7<t8的关系)地进行步骤s6(辊轧工序)的处理,与使t7=t8的情况相比,能够减小第1正极复合材料层18b与第2正极复合材料层18c之间的密度差。而且,可知,将第7辊61的表面温度t7设为与比正极复合材料6所含的粘结剂(pvdf)的软化温度ts低50℃的温度即(ts-50)℃相比低、且将第8辊62的表面温度t8设为(ts-50)℃以上为宜。更具体地说,将第7辊61的表面温度t7保持为15~35℃的范围内的温度为宜。(第7辊61和第8辊62的直径的探讨)前述的实施例1、实施例8和实施例11在将第7辊61的表面温度t7保持为25℃且将第8辊62的表面温度t8保持为100℃来进行步骤s6(辊轧工序)这一点上是一致的(参照表1~表3)。但是,第7辊61和第8辊62的直径(外径)不同。具体地说,在实施例1中,将第7辊61和第8辊62的直径设为390mm。在实施例8中,将第7辊61和第8辊62的直径设为150mm。在实施例11中,将第7辊61和第8辊62的直径设为300mm。如表2所示,在采用直径为150mm的第7辊61和第8辊62来进行步骤s6(辊轧工序)的实施例8中,第1正极复合材料层18b与第2正极复合材料层18c之间的密度差为0.65g/cc。而与之相对地,如表1所示,在采用直径为390mm的第7辊61和第8辊62来进行步骤s6(辊轧工序)的实施例1中,能够使第1正极复合材料层18b与第2正极复合材料层18c之间的密度差为0.1g/cc以下(具体地说为0.08g/cc)。同样地,如表3所示,在采用直径为300mm的第7辊61和第8辊62来进行步骤s6(辊轧工序)的实施例11中,也能够使第1正极复合材料层18b与第2正极复合材料层18c之间的密度差为0.1g/cc以下(具体地说为0.09g/cc)。这样,在实施例1和实施例11中,与实施例8相比,能够大幅降低第1正极复合材料层18b与第2正极复合材料层18c之间的密度差。由这些结果可知,可以说优选将第7辊61和第8辊62的直径设为300mm以上。更具体地说,可以说,对于直径为300mm以上的第7辊61和第8辊62,通过以第7辊的表面温度t7和第8辊的表面温度t8满足t7<t8的关系的方式进行辊轧工序(步骤s6),能够有效地提高该辊轧中的第2正极复合材料层18c的压缩率。由此,可以说能够进一步减小第1正极复合材料层18b与第2正极复合材料层18c之间的密度差。此外,这也由实施例2、实施例9和实施例12的密度差的比较、以及实施例3、实施例10和实施例13的密度差的比较所证实。以上,结合实施方式(实施例1~13)对本发明进行了说明,但本发明不限于上述实施方式,当然能够在不脱离其要旨的范围内进行适当地改变。例如,在实施方式中,作为本发明的电极片的制造方法,例示了制造正极片的方法。但是,也可以将本发明适用于负极片的制造方法。另外,在实施方式中,在第1成膜工序(步骤s2)之后,在第2成膜工序(步骤s4)之前,设有使在集电箔7的第1面7b上形成的第1正极复合材料层18b干燥的第1干燥工序(步骤s3)。而且,在第2成膜工序(步骤s4)之后,在辊轧工序(步骤s6)之前,设有使集电箔7的第2面7c上的第2正极复合材料层18c干燥的第2干燥工序(步骤s5)。但是,也可以不进行第1干燥工序(步骤s3)和第2干燥工序(步骤s5)就进行辊轧工序(步骤s6)。即使在此情况下,通过在辊轧工序(步骤s6)中,使第8辊62的表面温度t8比第7辊61的表面温度t7高(满足t7<t8的关系)地进行步骤s6(辊轧工序)的处理,与使t7=t8的情况相比,能够减小第1正极复合材料层18b与第2正极复合材料层18c之间的密度差。而且,可以说,更优选将第7辊61的表面温度t7设为与比正极复合材料6所含的粘结剂(pvdf)的软化温度ts低50℃的温度即(ts-50)℃相比低、且将第8辊62的表面温度t8设为(ts-50)℃以上。更具体地说,可以说优选将第7辊61的表面温度t7设为为15~35℃的范围内的温度。当前第1页12