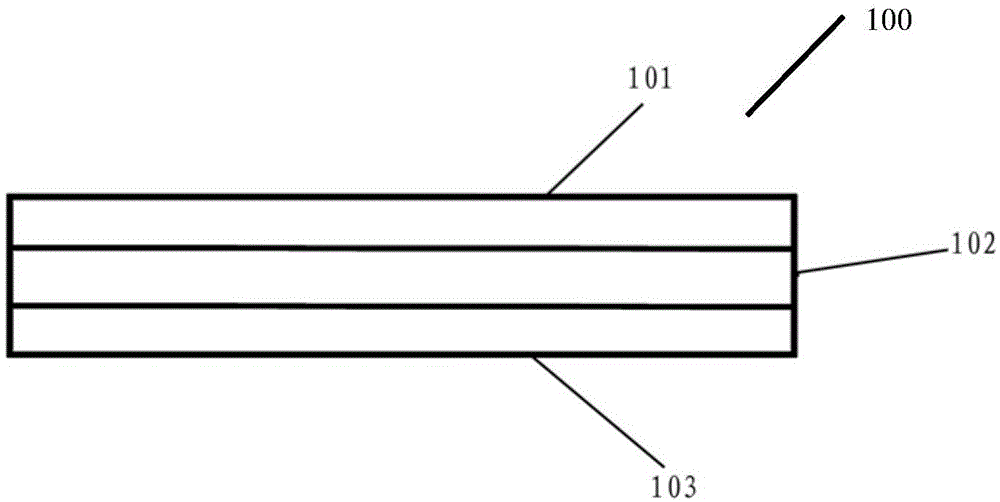
本申请涉及一种绝缘复合薄膜,尤其涉及一种具有优良抗刺穿性能的绝缘复合薄膜。
背景技术:
:绝缘薄膜被用于隔离各类电子器件或部件,以避免电子器件或部件之间、或电子器件或部件中的电子元气件因短路,击穿等引起的失效,并降低电子器件或部件起火的风险,从而保障各类电子元气件的正常工作。针对绝缘薄膜的不同用途,要求绝缘薄膜具有不同工作特性。例如在应用于某些电子器件或部件时,要求绝缘薄膜具有较好的抗刺穿性能,从而在受到外力冲击时,绝缘薄膜不易被刺穿。因此,期望提供一种性能优良的绝缘薄膜。技术实现要素:本申请的目的是提供一种绝缘复合薄膜,该薄膜在具有较小的厚度的情况下,仍然具有较好的抗刺穿性能,同时能够满足绝缘和阻燃的性能要求。根据本申请的第一方面,提供一种绝缘复合薄膜,该薄膜包括:薄膜上层,所述薄膜上层由pp、pc和pet材料中的至少一种制成;薄膜下层,所述薄膜下层由pp、pc和pet材料中的至少一种制成;和薄膜中层,位于薄膜上层和薄膜下层之间,所述薄膜中层由高硬度的热塑性树脂制成;所述薄膜中层的上表面和所述薄膜上层的下表面粘结在一起,所述薄膜中层的下表面和所述薄膜下层的上表面粘结在一起。如上所述的薄膜,所述高硬度的热塑性树脂选自pmma、高硬度pc或par。如上所述的薄膜,所述薄膜中层的厚度占所述薄膜总厚度的6%-20%。如上所述的薄膜,所述薄膜的总厚度为0.1mm-1.0mm。如上所述的薄膜,所述薄膜由挤出成型工艺制成。如上所述的薄膜,所述薄膜上层和/或薄膜下层中含阻燃剂,所述阻燃剂为选自含溴阻燃剂或含氯阻燃剂的有卤阻燃剂,或选自含磷阻燃剂、含氮阻燃剂、磺酸盐类阻燃剂、或含硅阻燃剂的无卤阻燃剂。根据本申请的第二方面,提供一种绝缘复合薄膜,所述薄膜包括至少两层,所述至少两层中包括至少一层由pp、pc和pet材料中的至少一种制成的层,所述至少两层中包括至少一层由高硬度的热塑性树脂制成的层。如上所述的薄膜,所述高硬度的热塑性树脂选自pmma、高硬度pc或par。如上所述的薄膜,所述薄膜的总厚度为0.1mm-1.0mm。如上所述的薄膜,所述薄膜由挤出成型工艺制成。如上所述的薄膜,由pp、pc和pet材料中的至少一种制成的层中的至少一层含阻燃剂,所述阻燃剂为选自含溴阻燃剂或含氯阻燃剂的有卤阻燃剂,或选自含磷阻燃剂、含氮阻燃剂、磺酸盐类阻燃剂、或含硅阻燃剂的无卤阻燃剂。根据本申请的第三方面,提供一种绝缘复合薄膜,该薄膜包括:薄膜基部,所述薄膜基部由pp、pc和pet材料中的至少一种制成;涂布层,所述涂布层由高硬度热固性材料涂布在所述薄膜基部的上表面形成。如上所述的薄膜,所述高硬度热固性材料选自环氧树脂、丙烯酸酯树脂、聚氨酯树脂和酚醛树脂。如上所述的薄膜,所述薄膜基部具有一层或两层以上的结构。如上所述的薄膜,所述薄膜基部中的至少一层包含阻燃剂,所述阻燃剂为选自含溴阻燃剂或含氯阻燃剂的有卤阻燃剂,或选自含磷阻燃剂、含氮阻燃剂、磺酸盐类阻燃剂、或含硅阻燃剂的无卤阻燃剂。如上所述的薄膜,当所述薄膜基部具有三层结构时,所述薄膜基部的所述中层的厚度是所述薄膜基部的总厚度的30-50%。如上所述的薄膜,所述薄膜基部的厚度0.1mm-0.25mm。如上所述的薄膜,所述涂布层的厚度为3μm-7μm。根据本申请的第四方面,提供一种电器部件,所述电器部件包括外壳和位于所述外壳内的印刷电路板,所述印刷电路板上装有电子元件和线路部件,所述印刷电路板被绝缘复合薄膜包围或部分包围,其特征在于,所述绝缘复合薄膜包括:薄膜上层,所述薄膜上层由pp、pc或pet材料制成;薄膜下层,所述薄膜下层由pp、pc或pet材料制成;和薄膜中层,位于薄膜上层和薄膜下层之间,所述薄膜中层由高硬度的热塑性树脂制成;所述薄膜中层的上表面和所述薄膜上层的下表面粘结在一起,所述薄膜中层的下表面和所述薄膜下层的上表面粘结在一起。如上所述的电器部件,所述电器部件是电源适配器或电源供应器。根据本申请的第五方面,提供一种电器部件,所述电器部件包括外壳和位于所述外壳内的印刷电路板,所述印刷电路板上装有电子元件和线路部件,所述印刷电路板被绝缘复合薄膜包围或部分包围,其特征在于,所述绝缘复合薄膜包括至少两层,所述至少两层中包括至少一层由pp、pc或pet材料制成的层,所述至少两层中包括至少另一层由高硬度的热塑性树脂制成的层。如上的电器部件,所述电器部件是电源适配器或电源供应器。根据本申请的第五方面,提供一种电器部件,所述电器部件包括外壳和位于所述外壳内的印刷电路板,所述印刷电路板上装有电子元件和线路部件,所述印刷电路板被绝缘复合薄膜包围或部分包围,其特征在于,所述绝缘复合薄膜包括:薄膜基部,所述薄膜基部由pp、pc或pet材料制成;涂布层,所述涂布层由高硬度热固性材料涂布在所述薄膜基部的上表面形成。如上所述的电器部件,所述电器部件是电源适配器或电源供应器。本申请中的绝缘复合薄膜具有良好的绝缘和阻燃性能,因而可以用于电子器件或部件中,并且由于本申请的绝缘复合薄膜具有较小的厚度,本申请的绝缘复合薄膜使电子器件或部件的结构紧凑,且由于本申请的绝缘复合薄膜具有较好的抗刺穿性,当电子器件或部件在受到一定的外力撞击的情况下,不会导致绝缘复合薄膜被刺穿而影响其绝缘性能。附图说明本申请的这些和其它特征和优点可通过参照附图阅读以下详细说明得到更好地理解,在整个附图中,相同的附图标记表示相同的部件,其中:图1为根据本申请的一个实施例的绝缘复合薄膜的剖面示意图;图2为根据本申请的第二实施例的绝缘复合薄膜的剖面示意图;图3为根据本申请的第三实施例的绝缘复合薄膜的剖面示意图;图4为根据本申请的第四实施例的绝缘复合薄膜的剖面示意图;图5是示出了生产根据本申请的一个三层结构的绝缘复合薄膜的一种挤出成型工艺的示意图;图6是示出了生产根据本申请的一个三层结构的绝缘复合薄膜的另一种挤出成型的示意图。图7a和7b示出了电器部件(例如电源适配器或电源供应器)700的结构。具体实施方式下面将参考构成本说明书一部分的附图对本申请的各种具体实施方式进行描述。应该理解的是,虽然在本申请中使用表示方向的术语,诸如“前”、“后”、“上”、“下”、“左”、“右”、等方向或方位性的描述本申请的各种示例结构部分和元件,但是在此使用这些术语只是为了方便说明的目的,基于附图中显示的示例方位而确定的。由于本申请所公开的实施例可以按照不同的方向设置,所以这些表示方向的术语只是作为说明而不应视作为限制。在以下的附图中,同样的零部件使用同样的附图号,相似的零部件使用相似的附图号,以避免重复描述。图1为是根据本申请的一个实施例的绝缘复合薄膜100的剖面示意图。如图1所示,薄膜100包括通过挤出成型工艺而层叠地粘结在一起的薄膜上层101、薄膜中层102和薄膜下层103。薄膜上层101和薄膜下层103由热塑性材料制成。发明人发现,当薄膜上层101和薄膜下层103由聚丙烯(pp)、聚碳酸酯(pc)或聚对苯二甲酸乙二醇酯(pet)中的至少一种制成时,薄膜100具有良好的绝缘性能。用于制成薄膜上层101和薄膜下层103的材料可以相同或不同。作为一种示例,薄膜上层101和薄膜下层103均由pc树脂制成。薄膜上层101和/或薄膜下层103的树脂材料中可选择添加或不添加阻燃剂。当薄膜上层101和/或薄膜下层103中含有阻燃剂时,阻燃剂可以为有卤阻燃剂或无卤阻燃剂。在一个实施例中,有卤阻燃剂可以为含溴阻燃剂或含氯阻燃剂。在一个实施例中,无卤阻燃剂可以为含磷阻燃剂、含氮阻燃剂、磺酸盐类阻燃剂或含硅阻燃剂。在薄膜上层101和/或薄膜下层103的树脂材料中添加了阻燃剂的情况下,使得薄膜100仍然符合rohs的标准要求。薄膜100可以适用于电子电气设备,例如电源适配器的电路板表面等需要绝缘的部分。基于使用环境的要求,薄膜中可以不添加阻燃剂。还是如图1所示,薄膜中层102位于薄膜上层101和薄膜下层103之间,薄膜中层102的上表面和薄膜上层101的下表面粘结在一起,薄膜中层102的下表面和薄膜下层103的上表面粘结在一起,从而使得所述的薄膜100的三层可以层叠地粘结在一起。薄膜中层102由高硬度的热塑性树脂制成,从而使得本申请的绝缘复合薄膜具有较好的抗刺穿性能。所述的高硬度的热塑性树脂是指具有一定硬度,从而使树脂具有一定的抗刺穿性能的热塑性树脂。从化学结构上来说,高硬度的热塑性树脂应当具有优异刚性的官能团结构。例如,主链有大量苯基、或者有丰富支链、或具有高交联密度的高分子热塑性树脂均可以满足本申请对热塑性树脂的硬度要求。在本申请中,高硬度的热塑性树脂可以为聚甲基丙烯酸甲酯(pmma)、高硬度聚碳酸酯(pc)或聚芳酯(par)树脂中的至少一种。作为一种示例,所述的高硬度的热塑性树脂可以为高分子量的pmma树脂。所述的高分子量的pmma树脂应当具有适合的熔融指数(mi),从而能够通过挤出成型工艺生产薄膜100。作为一个示例,高分子量的pmma树脂的熔融指数为1-5(230℃/3.8kg)。薄膜中层102可以不添加或者仅添加少量阻燃剂。由于阻燃剂在薄膜表面层(上层和下层)的阻燃效率比在薄膜内部(中层)高,本申请的薄膜100无论使用有卤还是无卤阻燃剂,均可以在使用较少的阻燃剂的情况下达到和单层绝缘薄膜相同或相近的阻燃性能。由于阻燃剂价格较为昂贵,本申请使得绝缘薄膜的材料成本得以显著降低。在如图1所示的实施例中,所述薄膜100的厚度为0.1-1.0mm。在一个示例中,所述薄膜100的厚度为0.1-0.5mm。在另一个示例中,所述薄膜100的厚度为0.1-0.35mm。在又一个示例中,所述薄膜100的厚度为0.1-0.25mm。发明人发现,图1的绝缘薄膜100由于复合有高硬度的热塑性树脂作为中间层,当图1的绝缘薄膜具有小于单层结构的绝缘薄膜的厚度时,仍然可以具有和较厚的单层结构的绝缘薄膜相当甚至更好的抗刺穿强度。因此,使用图1的绝缘薄膜100的电子器件或部件的结构可以更为紧凑,具有更高的空间设计自由度,且具有降低的成本。举例来说,当图1的绝缘薄膜100用于笔记本电脑的电源适配器时有利于促进笔记本电脑的轻薄化。笔记本电脑的轻薄化依赖于cpu、主板、电池等发热部件的科技进步和主体结构的材料革新,如镁铝、碳纤维材质应用,也和一些辅助材料的革新进步息息相关。笔记本电脑的电源适配器使用绝缘薄膜作为辅助材料实现电子元件之间的绝缘。减小绝缘薄膜的厚度可以使得电源适配器的结构紧凑,符合笔记本电脑的轻薄化趋势。但在检测绝缘薄膜的抗刺穿强度时会用尖锐物(类似电子元件的针脚)刺绝缘薄膜,并且在使用电源适配器时不可避免地会产生碰撞电源适配器而导致电源适配器中的电子元件的针脚刺在绝缘薄膜上的情况,因此要求所使用的绝缘薄膜具有良好的抗刺穿强度。一般使用由无卤阻燃pc制成的单层绝缘薄膜。出于保证足够的抗刺穿强度的考虑,一般使用的无卤阻燃pc单层绝缘薄膜的厚度在0.4mm以上,通常为0.43mm。然而,随着笔记本电脑的轻薄化趋势的发展,这种绝缘薄膜越来越不能满足笔记本电脑电源适配器的设计需求。期望的是,提供一款新型阻燃绝缘薄膜该阻燃绝缘薄膜具有和0.43mm的单层无卤阻燃pc相同的抗刺穿性能的同时具有小于0.40mm且尽量更小的厚度。本申请图1的绝缘薄膜100在厚度小于0.40mm的情况下仍具有和0.43mm的单层无卤阻燃pc绝缘薄膜相同甚至更优的抗刺穿性能。并且,本申请图1的绝缘薄膜100同时满足阻燃绝缘薄膜所需的阻燃和绝缘性能,阻燃性能可达ul94v-2以上,如v-0等级,并且其绝缘性能满足iec62368标准关于辅助绝缘或加强绝缘的标准。发明人指出,由于高硬度热塑性树脂本身硬度较大,其韧性较差,因而通常不具备优良的抗刺穿的性能。当需要考虑制造具备优良抗刺穿的性能的薄膜时,本领域技术人员不使用高硬度热塑性树脂制备薄膜。然而,出乎意料的是,本申请的复合绝缘薄膜在包含高硬度热塑性树脂层的情况下,并未导致复合绝缘薄膜的抗刺穿性能变差,反而使得复合绝缘薄膜获得优良的抗刺穿性能。这是由于,本申请采用韧性较好的pc、pp和pet材料中的至少一种制成本申请的绝缘复合薄膜的至少一层,并采用高硬度的热塑性树脂材料制成本申请的绝缘复合薄膜中的至少另外一层。韧性较好的pc、pp和pet材料中的至少一种制成的层为本申请的绝缘复合薄膜被尖锐物刺的时候不易被刺穿,硬度较高的热塑性树脂材料制成的层使得本申请的绝缘复合薄膜在被尖锐物刺的更能抵抗刺入的力,从而进一步使得本申请的绝缘复合薄膜不易被刺穿。因此,本申请的复合绝缘薄膜由于复合了由pc、pp和pet材料中的至少一种制成的薄膜层和由高硬度热塑性树脂材料制成的薄膜层而获得了优良的抗刺穿性能。并且,由于硬度较高的热塑性树脂材料制成的层使得本申请的绝缘复合薄膜在被尖锐物刺的更能抵抗刺入的力,相比单纯由pc、pp和pet材料中的至少一种制成的绝缘薄膜,本申请的复合绝缘薄膜可以具有更薄的厚度,但仍然具有和单纯由pc、pp和pet材料中的至少一种制成的绝缘薄膜相当甚至更优的抗刺穿性。并且,在本申请的一个实施方案中,薄膜中层由pmma制成。发明人指出,由于一般地,pmma被认为阻燃效果不佳,本领域技术人员并不会将其用于制备绝缘薄膜。然而出人意料的是,本申请发明人发现,当使用pmma作为本申请图1所示的绝缘薄膜100中的高硬度中间层时,本申请图1的绝缘薄膜100仍然具有良好的阻燃性能,甚至可以达到和0.43mm的单层无卤阻燃pc相同的阻燃等级。在一个实施例中个,薄膜中层102的厚度为薄膜100的总厚度的6-20%的情况。在另一个实施例中,薄膜中层102的厚度为薄膜100的总厚度的8-14%。在一个实施例中,当薄膜中层102的厚度为小于薄膜100的总厚度的20%时,薄膜100的阻燃等级至少达v-2等级。对于三层结构的薄膜100来说,薄膜上层101的厚度和薄膜下层103的厚度可以相同,也可以不同。当薄膜上层101的厚度和薄膜下层103的厚度不同时,在一个实施例中,薄膜上层的厚度为薄膜100的总厚度的10-30%,薄膜下层的厚度为薄膜100的总厚度的50-84%。在一个实施例中,薄膜100可以进一步包括在薄膜上层101和薄膜下层103之间的另外的树脂层,使薄膜100具有四层或者四层以上的结构。具有四层或四层以上的结构的绝缘薄膜包括至少一层高硬度的热塑性树脂制成的层,该至少一层高硬度的热塑性树脂制成的层可以例如位于薄膜上层101和薄膜下层103之间。以下通过表1说明图1的绝缘薄膜100的性能特点。表1中的绝缘复合薄膜实施例1-4中的复合绝缘薄膜均具有三层结构,且它们的上下层均由无卤阻燃pc制成、中间层均由pmma制成。表1上表1中薄膜的抗刺穿强度测试方法参考了落镖测试方法,数值越高,抗刺穿效果越好。如表1所示:1.单层的pmma薄膜抗刺穿性能较差,即使具有一定的厚度如达到0.43mm,其抗刺穿性能也不佳。然而,令人惊讶的是,本申请的复合绝缘薄膜在具有由高硬度热塑性树脂制成的中间层的情况下,获得了优良的抗刺穿性能。本申请的复合绝缘薄膜的抗刺穿性远优于单层pmma的抗刺穿性。在具有和单层无卤阻燃pc相同厚度或更小厚度的情况下,本申请的复合绝缘薄膜表现出与单层无卤阻燃pp相当甚至更优的抗刺穿性。2.当绝缘薄膜中的由高硬度热塑性树脂制成的中间层的厚度为绝缘薄膜的总厚度的9-20%时,绝缘薄膜具有最优的抗刺穿性能,且其抗刺穿性能甚至好于厚度比其大的单层无卤阻燃pc。3.当绝缘薄膜中的由高硬度热塑性树脂制成的中间层的厚度控制为不超过总厚度的20%时,绝缘薄膜的阻燃性能至少达到v-2等级,甚至于可以达到v-0等级。4令人惊讶地,虽然pmma的阻燃性不佳,但将其作为高硬度热塑性树脂层和无卤阻燃pc材料复合得到的如图1所示的绝缘薄膜100具有优良的阻燃等级,其阻燃等级可达v-2、或v-0级别。5.本申请的复合绝缘薄膜具有优良的绝缘性能。并且,本申请的复合绝缘薄膜在厚度很小的情况下,其绝缘性能也能满足使用环境的要求。由于以上优点,如图1所示的复合绝缘薄膜100具有优良有抗刺穿和阻燃性能,同时,如图1所示的复合绝缘薄膜100具有更小的厚度,因此,当如图1所示的复合绝缘薄膜100用于电子器件或部件时,能节约电子器件或部件的空间,使电子器件的设计更紧凑,使电子器件或部件的空间设计更自由。图2示出了根据本申请的另一种实施例的绝缘复合薄膜200的剖面示意图,该薄膜200与图1中的薄膜100的唯一区别在于:其中薄膜200仅具有层叠而成的上层201和下层202。在该实施例中,上层201是由高硬度的热塑性树脂制成,上层201的厚度为薄膜200的总厚度的6-20%。下层202由pp、pc和pet树脂材料中的至少一种制成。并且为了提高薄膜200的阻燃性能,在下层202中还添加有阻燃剂。两层结构的薄膜200可以达到和如图1中所示的薄膜100相同的绝缘以及抗刺穿性能,且两层结构的薄膜可以具有v-2级别的阻燃性。图3中示出了本申请的另一个实施例的绝缘复合薄膜300的剖面示意图,其中,薄膜300包括薄膜基部305和涂布层301,其中涂布层301是由高硬度热固性材料涂布在薄膜基部305的上表面而形成的。与用于制成图1中的薄膜100的薄膜中层102的高硬度热塑性树脂相似的是,构成薄膜300的涂布层301的高硬度热固性材料也具有一定的硬度,从而使薄膜300能够具有优良的抗刺穿性能。作为一种示例,高硬度热固性材料可以为环氧树脂、丙烯酸酯树脂、聚氨酯树脂或者酚醛树脂,例如丙烯酸酯uv漆。所述薄膜基部305可以由热塑性树脂制成。发明人发现,当所述薄膜基部305由pp、pc和pet树脂材料中的至少一种制成时,所述薄膜300具有良好的绝缘性能。所述的薄膜基部305可以为一层结构,也可以具有两层或两层以上的结构。当薄膜基部305具有两层以上的结构时,通过流延热压成型工艺将两个或两个以上的层叠粘结形成薄膜基部305。在如图3所示的实施例中,薄膜基部305具有依次粘结的三个层,即上层302、中层303和下层304。而在如图4所示的实施例中,薄膜基部405则具有依次粘结的两个层,即上层402和下层403。在一个实施例中,薄膜基部305可以被构造为具有至少一层包含阻燃剂的层,以提高阻燃性要求。在一个实施例中,薄膜基部305的上层302和下层304中包含阻燃剂,而中层303中不包含阻燃剂。在一个实施例中,薄膜基部305的上层302和下层304均由含有无卤阻燃剂的无卤阻燃pc制成,而中层303则由不含有阻燃剂的pc制成。图3中所示的涂布层301是通过涂布工艺得到的。在一个实施例中,将经高温融化的热固性树脂涂布在薄膜基部305的表面,热固性树脂随着温度降低固化在薄膜基部305的表面,从而形成涂布层301。如图3所述,涂布层301的厚度远小于薄膜基部305的厚度。在一个实施例中,薄膜基部305的厚度为0.1-0.25mm,涂布层301的厚度为3-7μm,薄膜300的总厚度在0.25mm左右。在一个实施例中,中层303的厚度为薄膜基部305的总厚度的30-50%。在另一个实施例中,中层303的厚度为薄膜基部305的总厚度的44%,并且上层302和下层304的厚度均为薄膜基部305的总厚度的28%。以下通过表2说明图3的绝缘薄膜300的性能特点。表2中的薄膜基部上层为无卤阻燃pc、中间层为纯pc、下层为无卤阻燃pc,上中下三层厚度占薄膜基部总厚度的比例为分别为28%、/44%和/28%。表2中薄膜实施例5具有涂布在薄膜上层的上表面上的涂布层,该涂布层由丙烯酸酯uv漆构成,涂布层厚度为5μm。表2样品名称市售单层阻燃pc薄膜基部绝缘复合薄膜实施例5厚度0.43mm0.25mm0.25mm抗刺穿强度/g59.449.659.8阻燃性(ul94)v-0vtm-0vtm-0上表2中薄膜的抗刺穿强度测试方法参考了落镖测试方法,数值越高,抗刺穿效果越好。如表2中所示,如本申请中图3所示的绝缘复合薄膜实施例5仅有0.25mm的厚度,但是其抗刺穿性能和0.43mm厚度的单层阻燃pc相当,并达到与单层阻燃pc相当的阻燃性能,例如达到ul94vtm-2(或v-2)以上,例如vtm-0(或v-0)等级。因此,实施例5中的绝缘复合薄膜性能优越,且厚度很小,适用于同时有抗刺穿和阻燃性能需求的电子元件。使用该绝缘薄膜能节约电子元件的空间,使电子元件的设计更紧凑。图4示出了另一个实施例的绝缘复合薄膜400的剖面示意图,该薄膜400与图3中的薄膜300的唯一区别在于:薄膜基部405仅具有上层402和下层403。在一个实施例中,根据使用环境要求,至少所述下层403中应当包含阻燃剂。其余部分与图3所示的示例类似,图4中所示的实施例可满足iec62368标准关于辅助绝缘的要求。另外,除了本申请列举的实施例外,将薄膜基部设置成三层以上,也在本申请的保护范围内。图5示意性地示出了生产根据本申请的一个实施例的绝缘复合薄膜100的挤出成型工艺过程的一个挤出成型流水线500。如图5所示,挤出成型流水线500包括第一挤出机501和第二挤出机502。第一挤出机501包括一个加料斗509和容腔510。加料斗509用于容纳含有阻燃剂的pc粒子。容腔510中设有驱动螺杆511。加料斗509的出口和容腔510的前端入口512相连通,容腔510的后端出口513和管道506的入口相连通,而管道506的出口和分配器503的第一入口514相连通。第二挤出机502包括一个加料斗515和容腔516。加料斗515用于容纳pmma粒子。容腔516中设有驱动螺杆517。加料斗515的出口和容腔516的前端入口518相连通,容腔516的后端出口519和管道507的入口相连通,而管道507的出口和分配器503的第二入口520相连通。分配器503的第一入口514和分配器的第一支管521的入口以及第二支管522的入口相连通,分配器503的第二入口520和分配器的第三支管523入的口连通。如图5所示,第三支管523位于第一支管521和第二支管522之间。第一支管521的出口、第二支管522的出口和第三支管523的出口在分配器的出口524处汇合。分配器的出口524和管道525的入口相连,管道525的出口连通模头504的模腔526的入口。模头504的模腔526具有适当的宽度和深度,使得其足以容纳从分配器管道输送而来的物料,且模腔526为扁平状使得从输送器管道输送而来的物料在其中被模压为扁平状。经模压的物料从模腔526的出口被输送到成型辊设备505。成型辊设备505包括互相靠近放置的多个成型辊。从模头模腔输送到成型辊设备的物料在多个成型辊之间受到拉伸、辊压和冷却,以使其达到期望的厚度并成型为薄膜。图5中示出了这样的三个成型辊505.1、505.2和505.3。在其他实施例中也可以只有两个成型辊或多于两个成型辊。按照图5所示的挤出成型流水线500,本申请生产绝缘复合薄膜100的过程如下:在生产过程中,对第一挤出机501和第二挤出机502的容腔510和516加热,并使第一挤出机501和第二挤出机502的驱动螺杆511和517旋转。将含有阻燃剂的pc粒子加入第一挤出机501的加料斗509。第一挤出机501的驱动螺杆511的旋转将加料斗509中的含有阻燃剂的pc粒子推入容腔510内。由于容腔510被加热,且含有阻燃剂的pc粒子进入容腔510内后因摩擦生热产生熔化而呈熔融状态。受到驱动螺杆511的旋转产生的推进力的影响,呈熔融状态的含有阻燃剂的pc被朝向容腔510的后端出口513输送。驱动螺杆511的旋转产生的推进力使得熔融状态的含有阻燃剂的pc从熔腔510的后端出口513流出容腔510,接着经由和容腔510的后端出口513相连通的管道506的入口进入管道506。熔融状态的含有阻燃剂的pc从管道506的出口流出,到达分配器503的第一入口514。在分配器的第一入口514,熔融状态的含有阻燃剂的pc被分配成两股,第一股进入分配器的第一支管521成为第一熔融阻燃pc,第二股进入分配器的第二支管522成为第二熔融阻燃pc。类似地,将pmma粒子加入第二挤出机502的加料斗515。第二挤出机502的驱动螺杆517的旋转将加料斗515中的pmma粒子推入容腔516内。由于容腔516被加热,且pmma进入容腔516内后因摩擦生热产生熔化而呈熔融状态。受到驱动螺杆517的旋转产生的推进力的影响,呈熔融状态的pmma被朝向容腔516的后端出口519输送。驱动螺杆517的旋转产生的推进力使得熔融状态的pmma从熔腔516的后端出口519流出容腔516,接着经由和容腔516的后端出口519相连通的管道507的入口进入管道507。熔融状态的pmma从管道507的出口流出,到达分配器503的第二入口520,并经由该第二入口520进入分配器的第三支管523。需要注意的是,对于pmma粒子的这种操作和上面描述的对含有阻燃剂的pc粒子的操作同时进行。进入分配器503的第一支管521的第一熔融阻燃pc、进入分配器503的第三支管523的熔融状态的pmma以及进入分配器的第二支管522的第二熔融阻燃pc在分配器的出口524处汇合,从而叠和在一起,并经由和分配器出口521相连通的管道525进入模头504的模腔526,以便在模腔526内受到模压形成扁平状熔融物。将该受模压过的扁平状熔融物输送到成型辊505.1和505.2之间,接受成型辊505.1和505.2对其施加的拉伸和压合力,同时被成型辊505.1和505.2冷却从而形成具有预定厚度的片或膜100’。膜100’继续被送入成型辊505.2和505.3之间进一步冷却或退火,形成根据本申请的一个实施例的绝缘复合薄膜100。根据需要,从模头输出来的经模压的扁平状熔融物可以只经过两个成型辊或多于两个成型辊而成型。图6示出了生产根据本申请的一个实施例的绝缘复合薄膜100的另一种挤出成型工艺过程的工艺流水线600。如图6所示,挤出成型流水线600包括第一挤出机601、第二挤出机602、第三挤出机603。第一挤出机601、第二挤出机602、第三挤出机603分别包括一个加料斗611、612、613、容腔614、615、616和驱动螺杆617、618和619。第一和第三挤出机611和613的加料斗用于容纳含有阻燃剂的pc粒子,第二挤出机612的加料斗用于容纳pmma粒子。第一挤出机601的加料斗611的出口和容腔614的前端入口620相连通,容腔614的后端出口624和管道607的入口相连通,而管道607的出口和分配器604的第一入口627相连通。类似地,第二挤出机602的加料斗612的出口和容腔615的前端入口622相连通,容腔615的后端出口625和管道608的入口相连通,而管道608的出口和分配器604的第二入口628相连通。第三挤出机603的加料斗613的出口和容腔616的前端入口623相连通,容腔616的后端出口626和管道609的入口相连通,而管道609的出口和分配器604的第三入口629相连通。分配器604的第一入口627和分配器的第一支管630的入口相连通,分配器604的第二入口628和分配器的第二支管631的入口相连通,分配器604的第三入口629和分配器的第三支管632入口连通。如图6所示,第二支管631位于第一支管630和第三支管632之间。第一支管630的出口、第二支管631的出口和第三支管632的出口在分配器的出口633处汇合。分配器的出口633和管道634的入口相连通,管道634的出口连通模头605的模腔635的入口。模头605的模腔635具有适当的宽度和深度,使得其足以容纳从分配器管道输送而来的物料,且模腔635为扁平状使得从输送器管道输送而来的物料在其中被模压为扁平状。经模压的物料从模腔635的出口被输送到成型辊设备610。成型辊设备610包括互相靠近放置的多个成型辊。从模头模腔输送到成型辊设备的物料在多个成型辊之间受到拉伸、辊压和冷却,以使其达到期望的厚度并成型为薄膜。图6中示出了这样的三个成型辊610.1、610.2和610.3。在其他实施例中也可以只有两个成型辊或多于两个成型辊。按照图6所示的挤出成型流水线600,本申请生产绝缘复合薄膜100的过程如下:在生产过程中,对第一挤出机601、第二挤出机602、第三挤出机603的容腔614、615和616加热,并使第一挤出机601、第二挤出机602和第三挤出机603的驱动螺杆617、618和619旋转。将含有阻燃剂的pc粒子加入第一挤出机601的加料斗611。第一挤出机601的驱动螺杆617的旋转将加料斗611中的含有阻燃剂的pc粒子推入容腔614内。由于容腔614被加热,且含有阻燃剂的pc粒子进入容腔614内后因摩擦生热产生熔化而呈熔融状态。受到驱动螺杆617的旋转产生的推进力的影响,呈熔融状态的含有阻燃剂的pc被朝向容腔614的后端出口624输送。驱动螺杆617的旋转产生的推进力使得熔融状态的含有阻燃剂的pc从熔腔614的后端出口624流出容腔614,接着经由和容腔614的后端出口624相连通的管道607的入口进入管道607。熔融状态的含有阻燃剂的pc从管道607的出口流出,到达分配器604的第一入口627,进入分配器604的第一支管630,进入分配器604的第一支管630的含有阻燃剂的pc为第一熔融阻燃pc。同样地,在第三挤出机603的加料斗613中加入含有阻燃剂的pc粒子,该含有阻燃剂的pc粒子以和第一挤出机601的加料斗611中的含有阻燃剂的pc粒子相同的方式被送到分配器604的第三支管632中,进入分配器604的第三支管632的含有阻燃剂的pc为第二熔融阻燃pc。在第二挤出机602的加料斗612中加入pmma粒子,该pmma粒子以和第一挤出机601的加料斗611中的含有阻燃剂的pc粒子相同的方式被送到分配器604的第二支管631中。应当注意的是,以上将含有阻燃剂的pc和pmma分别送到分配器的第一支管630、第二支管631和第三支管632中的操作同时进行。和图5所示的工艺流水线中挤压工艺类似,进入分配器604的第一支管630的第一熔融阻燃pc、进入分配器604的第二支管631的熔融状态的pmma以及进入分配器的第三支管632的第二熔融阻燃pc在分配器的出口633处汇合,从而叠合在一起,并经由和分配器出口633相连通的管道634进入模头605的模腔635,以便在模腔635内受到模压形成扁平状的熔融物。将该受模压过的扁平状熔融物输送到成型辊610.1和610.2之间,接受成型辊610.1和610.2对其施加的拉伸和压合,从而形成具有预定厚度的片或膜100’。膜100’继续被送入成型辊610.2和610.3之间进一步接受冷却或退火,形成根据本申请的一个实施例的绝缘复合薄膜100。根据需要,从模头输出来的经模压的扁平状熔融物可以只经过两个成型辊或多于两个成型辊而成型。传统上,用挤出成型工艺生产出的产品的中间层的厚度占产品总厚度的百分比较高。而采用本申请的挤出成型工艺生产的绝缘复合薄膜,其中间层的厚度占绝缘复合薄膜的总厚度的比率较低,绝缘复合薄膜中间层的厚度仅为薄膜总厚度的6%-20%。采用本申请的挤出成型工艺,在中间层的厚度占绝缘薄膜的总厚度的比率较低的情况下,各层仍能均匀分布。在图5和图6所示的挤出成型生产工艺中,第一熔融阻燃pc、熔融状态的pmma和第二熔融阻燃pc在分配器里叠合在一起。但是,本领域的技术人员应当知道,第一熔融阻燃pc、熔融状态的pmma和第二熔融阻燃pc也可以在模头里叠合在一起。虽然图3和图4所示的绝缘复合薄膜300和400是通过在薄膜基部的表面按uv漆的标准操作流程涂布丙烯酸酯uv漆然后固化而成。至于薄膜基部,薄膜基部可以共同流延热压工艺制得。薄膜基部为多层结构的情况下,也可以利用如图5和图6所示的挤出成型生产工艺生产薄膜基部。本申请中的绝缘复合薄膜具有小的厚度,并同时具有较好的阻燃性和抗刺穿性,可用于电源适配器的电路板,使电源适配器的结构更加紧凑,体积更小。由于本申请中的绝缘复合薄膜具有优良的抗刺穿性,当电源适配器跌落受到外力撞击时,薄膜不易被外壳或电路板上的元件刺穿而导致短路。图7a和7b示出使用本申请的绝缘复合薄膜702的电器部件(电源适配器或电源供应器)700的装配结构。如图7a所示,印刷电路板(未示出)被本申请的复合绝缘薄702膜围绕(或部分围绕)。印刷电路板上装有电子元件和线路部件(例如电阻、电容、电感、三极管、二极管、导线、引脚等)。本申请的复合绝缘薄膜702被屏蔽层701(一般为金属片隔层)包围以防止电磁干扰。如图7b所示,印刷电路板被本申请的绝缘复合薄膜702和屏蔽层701围绕(或部分围绕)。被本申请的绝缘复合薄膜702和屏蔽层701围绕的印刷电路板被装配到电器部件的外壳(未示出)中。应该说明的是,任何和图7a和7b中所示的电器部件(电源适配器或电源供应器)的装配结构相同或相似的电器部件都可以采用本申请的绝缘复合薄膜。由于本申请的绝缘复合薄膜具有很小的厚度,但具有优异的抗刺穿性能,且同时具有满足要求的阻燃和绝缘性能,在电器部件(例如电源适配器或电源供应器)中使用本申请的绝缘复合薄膜使得电器部件的结构更为紧凑,提高电器部件的空间设计自由度。尽管本文中仅对本申请的一些特征进行了图示和描述,但是对本领域技术人员来说可以进行多种改进和变化。因此应该理解,所附的权利要求旨在覆盖所有落入本申请实质精神范围内的上述改进和变化。当前第1页12