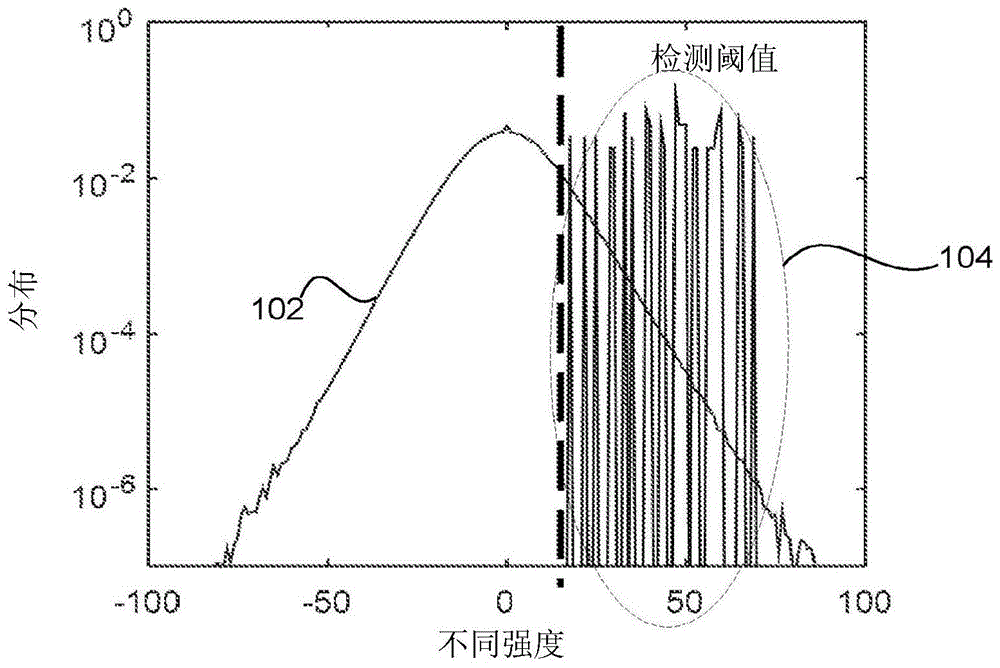
相关申请案的交叉参考本申请案主张由格蕾丝·陈(gracechen)等人在2018年11月7日申请的第62/756,975号先前申请案美国临时申请案的权益,所述申请案的全文出于所有目的以引用的方式并入本文中。本发明大体上涉及晶片检验系统的领域。更特定来说,本发明涉及使用极高敏感度混和式检验系统的缺陷检测。
背景技术:
:通常,半导体制造业涉及使用半导体材料制造集成电路的高度复杂技术,所述半导体材料经分层且图案化到衬底(例如硅)上。归因于大规模的电路集成及半导体装置的尺寸减小,经制造装置已变得对缺陷越来越敏感。即,引起装置中的故障的缺陷正变得越来越小。在装运到终端用户或客户之前装置需要大体上无故障。通常跨全晶片实施缺陷检测以用于半导体制造业中的良率管理。由检验系统(或检验器)发现的缺陷类型、缺陷计数及特征(signature)对半导体制造提供有价值信息以确保在研究开发阶段中建立的制造工艺可加速进行,确保在加速阶段中确认的工艺窗可转移到大批量制造(hvm),且确保hvm中的日常操作是稳定的且处于控制之下。光学检验器是目前市场上提供足够速度以经济地产生全晶片检验的唯一可行平台。归因于晶片上的低预期缺陷计数,已针对hvm实施通过光学检验器的全晶片覆盖。在成熟工艺中,预期缺陷计数通常小于1000。由于这些低计数,结合跨300mm晶片的缺陷的大部分随机位置,历史上一直使用通过光学检验器的全晶片覆盖来监测hvm工艺。然而,随着设计规则缩小,缺陷监测所需的敏感度与光学检验器可提供的敏感度之间的敏感度差距变宽。此敏感度差距是由临界尺寸(cd)长度与光点散布函数(psf)大小之间越来越大的差异所引起。用于当前设计节点的cd与光学psf之间的比率(cd:psf)是小于1:10,且cd:psf比率将针对后代设计节点继续增加。因为现今的cd:psf比率已为1:10,所以单个psf可覆盖若干设计或缺陷结构。因此,一个所产生的光学信号可来自psf内部的单个源(例如doi)或psf内部的多个源(例如doi及晶片噪声假影的组合或仅为若干晶片噪声假影)。此效应引起缺陷检测的不确定性。例如,归因于大cd:psf比率,可从桥接型缺陷或不同类型的图案边缘放置误差扰乱点产生类似光学信号。此效应产生关于如何产生光学信号的不确定性。因此,光学检验器无法区分特定缺陷信号与扰乱点信号,此降低光学检验器清晰检测doi的能力。因此,当前检验系统及方法论具有高敏感度缺陷检测性能差距。因此,持续需要改进的半导体晶片检验器系统及技术。技术实现要素:下文提呈本发明的简化概述以提供本发明的某些实施例的基本了解。此概述并非本发明的广泛综述且其并未识别本发明的关键/重要元件或划定本发明的范围。其唯一目的是以简化形式提呈本文中所揭示的一些概念作为稍后提呈的更详细描述的前序。在一个实施例中,揭示一种检测半导体样本上的缺陷的方法。使用光学检验器以用经选择以检测在跨半导体样本的多个对应位置处的多个候选缺陷及扰乱点位点的积极预定义的阈值检验所述样本,且将所述多个候选缺陷及扰乱点位点及其位置提供到高分辨率分布式探针检验器。使用所述高分辨率分布式探针检验器检验所述样本上的所述多个候选缺陷及扰乱点位点以使所述候选缺陷位点与所述扰乱点位点分离,且所述高分辨率分布式探针检验器包括高分辨率探针阵列。所述高分辨率分布式探针检验器经配置以使所述探针阵列相对于所述样本移动,且所述探针阵列经配置以扫描及获得每一位点的高分辨率图像以使所述候选缺陷位点与所述扰乱点位点分离。使用较高分辨率探针以获得每一候选位点的较高分辨率图像,且所述较高分辨率探针具有高于经配置以获得每一位点的高分辨率图像的所述高分辨率探针的分辨率的分辨率。重检每一候选缺陷的较高分辨率图像以使不利地影响所述样本上的任何装置的操作的真实缺陷与所述候选缺陷分离。在特定实施方案中,所述高分辨率分布式探针检验器包含所述较高分辨率探针。在另一方面中,所述光学检验器是以在约300nm到500nm之间的分辨率使用及配置,且所述微型高分辨率探针中的每一者具有低于约10nm的分辨率。在此方面中,所述探针阵列可经配置以在载物台移动时扫描每一位点,且所述较高分辨率探针具有约1nm或更小的分辨率。在另一实例中,由所述光学检验器检测的所述位点数以百万计且所述候选缺陷位点数以千计或更少,且使用所述高分辨率分布式探针检验器检验所述样本上的所述多个候选缺陷及扰乱点位点以使所述候选缺陷位点与所述扰乱点位点分离花费一小时或更短时间。在另一实例性实施方案中,所述微型高分辨率探针是布置成跨越所述半导体样本的线性阵列,数目在10个探针到100个探针之间,且包括其自身物镜及扫描所述个别位点的扫描电子器件。在一个方面中,所述高分辨率分布式探针检验器包括其上装载所述半导体样本的载物台,且所述载物台经配置以在保持静止的所述微型高分辨率探针中的每一者下方扫描所述半导体样本的扫描带,以提供全半导体样本覆盖。在另一方面中,所述高分辨率分布式探针检验器包括其上装载所述半导体样本的载物台,且所述微型高分辨率探针是可移动的且经配置以在所述载物台保持固定时遍及所述半导体样本的扫描带扫描。在另一方面中,所述高分辨率分布式探针检验器包括其上装载所述半导体样本的载物台,且所述载物台及所述微型高分辨率探针都是可移动的且经配置以在所述微型高分辨率探针中的每一者下方扫描所述半导体样本的扫描带。在进一步方面中,所述微型高分辨率探针经配置以在所述载物台经配置以旋转时径向移动,且所述扫描带是圆形的。在另一实例中,所述微型高分辨率探针是布置于待在所述半导体样本上方居中的多个辐条中且每一辐条经配置以在所述载物台经配置以旋转时径向移动,且所述扫描带是圆形的。在特定实施例中,所述高分辨率分布式探针检验器是扫描电子显微镜(sem),且所述微型高分辨率探针中的每一探针包括微机电系统技术。在另一实例中,所述微型高分辨率探针包括多个原子力显微镜(afm)探针、多个近场探针或多个近端光学探针。在替代实施例中,本发明涉及一种用于检测半导体样本上的缺陷的混和式检验器系统。此系统包含光学检验器,所述光学检验器经配置以用经选择以检测在跨半导体样本的多个对应位置处的多个候选缺陷及扰乱点位点的积极预定义的阈值检验所述样本,且所述多个候选缺陷及扰乱点位点及其位置是提供到所述系统的高分辨率分布式探针检验器。所述高分辨率分布式探针检验器经配置以检验所述样本上的所述多个候选缺陷及扰乱点位点以使所述候选缺陷位点与所述扰乱点位点分离,且所述高分辨率分布式探针检验器包括微型高分辨率探针阵列。所述高分辨率分布式探针检验器经配置以使所述探针阵列相对于所述样本移动,且所述探针经配置以扫描及获得每一位点的高分辨率图像以使所述候选缺陷位点与所述扰乱点位点分离。所述系统还包含较高分辨率探针,所述较高分辨率探针经配置以(i)获得每一候选位点的较高分辨率图像,其中所述较高分辨率探针具有高于经配置以获得每一位点的高分辨率图像的所述高分辨率探针的分辨率的分辨率,及(ii)重检每一候选缺陷的较高分辨率图像以使不利地影响所述样本上的任何装置的操作的真实缺陷与所述候选缺陷分离。所述系统还可经配置以执行上述操作的任何组合。下文参考图进一步描述本发明的这些及其它方面。附图说明图1是依据强度差值而变化的典型背景信号及典型小缺陷信号分布的图表。图2是说明根据本发明的一个实施例的混和式检验过程的流程图。图3a说明根据本发明的个一般实施方案的具有扫描带扫描(swathing)能力及高分辨率子场扫描的高分辨率多探针架构。图3b说明根据本发明的一个实施例的用于在载物台在下面移动时用电子束扫描缺陷的简化跟踪模式技术。图3c说明简化帧模式技术。图3d说明简化扫描带模式技术。图4a说明根据本发明的一个实施例的具有固定位置的高分辨率探针阵列及在此高分辨率探针下方移动的晶片。图4b展示根据本发明的替代实施例的可操作以相对于固定晶片移动的高分辨率探针阵列系统的示意图。图4c展示根据本发明的另一替代实施例的可操作以相对于在正交于探针移动方向的方向上移动的晶片而移动的高分辨率探针阵列。图4d说明根据本发明的又另一实施例的在载物台及晶片旋转时沿着单轴移动的高分辨率探针阵列。图4e说明根据本发明的另一实施例的具有径向移动的若干组线性布置的高分辨率探针的辐条布置及具有旋转移动的晶片。图5a到5d展示根据本发明的若干实施例的混和式检验系统的变动。图6是根据本发明的特定实施方案的光学检验系统的图解表示。图7是根据本发明的特定实施方案的适于将带电粒子聚焦于多柱中的分布式高分辨率系统的图解表示。具体实施方式在以下描述中,陈述许多特定细节以提供对本发明的透彻理解。可在不具有这些特定细节的一些或全部的情况下实践本发明。在其它例子中,未详细描述众所周知的过程操作以免不必要地模糊本发明。虽然将结合特定实施例描述本发明,但应理解,并不希望将本发明限于所述实施例。大cd:psf比率可导致总是嵌入于用于光学检验器的背景分布信号函数的尾端中的小缺陷的信号。图1是依据强度差值而变化的典型背景信号分布102(例如,背景像素的数目)及典型小缺陷信号分布104(例如,缺陷像素的数目)的图表。如此实例中所展示,小缺陷信号104可与噪声分布102的尾端混淆。例如,如果光学检验阈值被设置为低,那么较高数目个扰乱点信号连同实际缺陷信号被标记为候选缺陷。随着半导体装置具有越来越减小的cd,doi与扰乱点信号之间的混淆程度变得更加严重。此混淆导致光学检验器无法以可接受扰乱点比率检测小缺陷。高分辨率扫描系统(例如电子束检验器(ebi))可为用于解决此光学敏感度差距的次优解决方案。然而,由于不足晶片处理量,高分辨率扫描系统在大批量制造工艺中无法进行检验。例如,尽管ebi的分辨率足够高以分辨小半导体结构,但ebi目前无法提供半导体制造良率监测可接受的处理量。归因于不足处理量,采用这些高分辨率系统(例如ebi)限于研究及开发阶段。因为高分辨率系统通常无法提供全晶片扫描,所以其对于在hvm(大批量制造)检验中的采用提出挑战。在本发明的某些实施例中,用混和式光学及分布式高分辨率检验器系统来解决敏感度缺陷检测性能差距。经组合的系统一起改变检验典范。一般来说,高分辨率系统包含用于迅速扫描大量潜在缺陷位点的快速、分布式探针架构。因此,混和式检验器系统利用光学检验器及分布式、高分辨率系统两者的优势。例如,此混和式检验器可在2小时内以全晶片覆盖提供当前设计节点5nm缺陷的检测。此外,混和式检验器可处置随机或系统性的缺陷分布。可对光学检验器设置积极阈值以实现至少一5nm缺陷敏感度,使得可在光学扫描中检测doi(受关注缺陷)。用于光学检验器的积极阈值经选择以有可能导致来自第一检验阶段的5百万个到2千万个候选缺陷及扰乱点位点。接着,可将这些位点的位置发送到高分辨率检验器以进行doi/扰乱点分离。为在少于2小时内实现全晶片检验覆盖,此高分辨率检验器可操作以在1小时或更短时间内找到5百万个到2千万个随机出现的位点且执行doi/扰乱点分离。经指定位点计数范围可基于制造工艺及装置设计参数而改变。换句话说,混和式检验系统含有(1)产生用于5nm缺陷检测的足够位点信号且具有在少于1小时内扫描全晶片的能力的光学检验器,及(2)具有在少于1小时内找到跨晶片随机分布的5百万个到2千万个位点且针对经找到的每一位点执行缺陷检测的能力的高分辨率、快速检验器。图2是说明根据本发明的一个实施例的混和式检验过程200的流程图。首先,在操作202中使用光学检验器以用经选择以检测在跨样本(例如,半导体晶片)的多个位置处的大量候选缺陷及扰乱点位点的阈值检验所述样本。例如,潜在缺陷及扰乱点位点数目为通常跨全晶片随机分布的至少五百万个位点(数以百万计)且包含与经检测位点的总数目混合在一起的超过约1000个(例如,通常在约1000个到5000个的范围内,或数以千计或更少)候选缺点位点。可利用任何合适缺陷检验技术,例如裸片对裸片、单元对单元、裸片对数据库等。一般来说,比较相同设计的晶片区域的参考图像与测试图像,且如果差异大于积极预定义的阈值,那么标记潜在缺陷/扰乱点。一般来说,选择积极预定义的阈值以捕获所要尺寸的缺陷,其中所述所要缺陷的尺寸取决于半导体工艺中所使用的设计节点。对于5nm设计节点,受关注缺陷将为约5nm。对于更先进设计节点,受关注缺陷可小于5nm。任何合适系统可用于实施可采用任何合适形式的第一阶段光学工具。例如,光学检验器可操作以调整各种光学参数(例如波长、照明及偏光参数),使得系统可在大小不同的制造工艺及结构设计中针对小到5nm的缺陷产生最佳信号。光学检验器还可配置以通过积极定限执行检测以允许超过2亿个对象通过光学检测阶段。此配置确保可通过混和式检验的第一阶段检测或标记5nm缺陷。光学检验器还优选地能够在少于1小时内扫描全晶片。运行良好的一个实例性工具是可从加利福尼亚州米尔皮塔斯市的科磊公司(kla-tencorcorpofmilpitas,ca)购得的2930、2935及3900检验系统。将多个经检测候选缺陷及扰乱点位点及其位置提供到高分辨率、分布式探针检验器。接着可在操作204中用高分辨率、分布式探针检验工具检验经检测位点以使候选缺陷与扰乱点分离。例如,基于由分布式探针工具提供的高分辨率图像发现1k个到5k个候选缺陷且使其与扰乱点缺陷分离。一般来说,可通过使用用以检测候选缺陷的任何合适过程(例如裸片对裸片、单元对单元、裸片对数据库检验等)而分析高分辨率图像。还可或替代性地使用用于学习缺陷vs.扰乱点分类的神经网络或算法/模型及机器学习算法以在此第二阶段中区分缺陷与扰乱点。使用复杂计算方法用于无噪声参考产生的其它方法还可用作用于高分辨率探针系统的检测算法。另外,利用半导体装置设计文件的检测算法还可用作用于高分辨率探针的检测算法。为基于其物理形态将经检测doi进一步分类成不同doi等级(bin),使用较高分辨率系统,如206中所说明。可在操作206中将来自操作204的经确认doi的位置传递到所述较高分辨率探针。较高分辨率探针具有大约1nm(或更小)的像素分辨率,使得可分析来自较高分辨率系统的图像以区分不同类型的缺陷(举例来说,例如桥接及突出)。一般来说,重检阶段包含对缺陷类型的分类,包含使影响良率或装置功能的“真实”缺陷与并不影响良率或装置功能的扰乱点类型缺陷分离。通常,可在此重检步骤中发现10个到50个(或50个到100个)最终缺陷。重检过程可通过如与将不影响装置功能等的扰乱点类型缺陷相反将实际影响良率的缺陷分类及分离为真实缺陷(包含缺陷类型(例如,桥接、突出缺陷))的一或多个各种学习算法或模型来完成。接着可在操作208中确定样本是否通过检验。例如,可确定晶片上的最终缺陷是否将不利地影响此晶片上的装置的功能。如果样本通过,那么检验过程可结束。例如,可进一步处理、切割晶片样本且将其封装成经封装装置。如果样本并未通过,那么可修复或丢弃样本。例如,可移除特定结构或将特定结构添加到晶片以消除特定缺陷的效应。此外,可调整用于制造晶片的工艺以消除(例如)形成于后续晶片上的缺陷。过程200接着可结束。可在制造工艺调整之后制造经修复晶片及/或后续晶片。一般来说,多探针检验器在大有效区域中提供高分辨率,如与如由单探针系统提供的在小区域中的高分辨率相反。即,多个分布式探针具有一起提供大有效视场(fov)的多个物镜。多探针检验器经配置以提供等于或小于10nm的分辨率,如相较于在200nm到500nm之间的光学检验器分辨率。在特定实施方案中,多探针检验器对于每一候选位点提供5nm到10nm分辨率。图3a说明根据本发明的一个一般实施方案的经配置以具有扫描带扫描及高分辨率子场扫描能力的分布式探针架构300的实例。架构300包含具有以分布式方式(例如线性阵列)布置的多个探针(例如304a及304b)的多探针系统302。所述分布式系统通常包含具有每小时扫描至少5百万个位点的分离物镜的任何合适数目个微型化探针。探针还包含其自身扫描电子器件以扫描个别位点。在所说明实例中,30个探针经布置使得可在少于1小时内找到并检验晶片上的至少5百万个位点。当然,其它探针计数(例如在约10个探针到100个探针之间)将有可能起作用以实现如本文中所指定的所要处理量。这些探针的尺寸是小的,使得所述探针最有可能用mems(微机电)技术及组件制造。在一个实例中,晶片306经装载到分布式高分辨率系统300的可移动载物台上且所述载物台经配置以在保持静止的探针下方扫描晶片306的扫描带。例如,载物台扫描第一x线性方向(例如,310),在y方向上移动,且接着在静止探针下方在第二相反x方向上扫描另一扫描带。载物台跨晶片来回重复扫描扫描带以提供全晶片覆盖。此外,来自不同扫描的若干组扫描带可彼此交错。即,第一组扫描带是在探针阵列下方(或由探针阵列)扫描,使得所述扫描带之间具有空间。换句话说,在第一扫描中跳过扫描带区域。接着在第一组扫描带之间的空间内扫描第二组扫描带。重复扫描带扫描以填充扫描带之间的空间直到扫描全晶片。一般来说,可在每一扫描期间跳过扫描带,且扫描带接着可在分离扫描中交错。如果高分辨率探针是基于电子束的,那么跳过扫描带可导致对晶片的较少损坏。可跳过任何合适数目个扫描带或线。一般来说,跳过线的扫描图案可引起对特定材料(例如光致抗蚀剂,其易于在由带电粒子束扫描的区域中收缩)的较少损坏。可选择所跳过线的数目使得收缩量可相当于线边缘粗糙度且不显著影响总线边缘。取决于电势的分布,跳过扫描带线可为既降低有害效应(例如聚合物收缩、带电、污染等)且又增加总处理量的有价值技术。在每一扫描带在探针302中的每一者下方移动时,每一探针经配置以扫描存在于此探针扫描区域内的每一缺陷位点。如所展示,晶片针对每一探针的扫描区域移动通过n个扫描带。在此实例中,每一探针扫描带是约50μm高。当探针在潜在缺陷(例如缺陷308)(还展示于扩展区域312及314b中)上方移动时,所述探针接着可操作以跨此缺陷区域(缺陷区域314a及扩展缺陷区域314b)快速扫描。如所展示,针对靠近潜在缺陷308的扫描带区域展示扩展视图312。在扩展视图312中,探针的缺陷区域314a在所说明架构中具有1μmx1μm(或最多50μmx1μm)的尺寸。在所说明实例中,探针在正交于晶片移动方向的y方向上扫描,此导致在扫描区域上方的扫描图案316,从而导致针对此缺陷308对150个到350个像素进行成像。高分辨率、分布式探针检验器还可采用任何形式。例如,每一探针或柱可包括用于聚焦、扫描及其它合适功能的组件。通过实例,高分辨率、分布式探针检验工具是呈具有多个分布式微型柱的扫描电子显微镜(sem)、多个原子力显微镜(afm)探针、具有多个探针的近场微波工具,或多个近端光学探针的形式。合适微型化电子束柱技术是进一步描述于第8,698,094b1号美国专利及第8,455,838b2号美国专利中,所述专利出于所有目的以引用的方式并入本文中。可行高分辨率近场微波探针技术是描述于具有公开案第2013/0088245号的美国专利申请案中,所述申请案出于所有目的以引用的方式并入本文中。实例性高分辨率afm探针配置是进一步描述于第8,997,258b2号美国专利中,所述专利针对出于目的以引用的方式并入本文中。用于第二阶段的一个实例性高分辨率检验器是具有柱阵列系统以在1小时或更短时间内实现5百万个到2千万个位点的处理量的sem。例如,所述sem检验器包含线性柱阵列及扫描带扫描连续移动的精确载物台。其它探针及移动布置在本文中进一步描述。在特定实例中,线性探针阵列中的每一探针经优选微型化,因此阵列可跨越晶片。例如,探针可由微机电系统(mems)技术形成。当然,其它类型的探针可如本文中进一步描述那样实施。线性阵列(或类似者)中的每一探针可具有成像视场(fov),所述成像视场(fov)具有大致在50umx50um与100umx100um之间的尺寸。因此,10探针阵列将具有500umx500um到1mmx1mm的有效fov尺寸。在此第二遍次检验期间,当任何探针与由第一阶段光学检验器标记为潜在缺陷位点的位置交叉时,可获取小图像图块(例如,具有1umx1um尺寸的扫描区域314)。在其fov内,每一探针可经配置为具有允许在载物台以恒定速度移动时最大化被找到位点的数目的独立二维定位操纵。每一探针还优选可操作以独立地跟踪载物台运动,从而导致高质量缺陷图像。在一个实施方案中,阵列或探针可为微型电子束柱。在此实施方案下,在载物台以50mm/s的恒定载物台速度移动且在5mn像素大小下每像素的目标电子(e/p)大于1500的情况下,具有10个柱的分布式微型电子束柱可(例如)在少于1小时内在300mm晶片上每小时覆盖至少5百万个位点。一般来说,第二阶段检验器可覆盖5百万个到2千万个(或更多)随机分布的位点且产生这些位点的高分辨率图像,使得可区分doi位点与扰乱点位点。可在各种光点尺寸(例如4nm、7nm、10nm及15nm光点直径)下满足处理量能力。在特定基于mems的柱阵列检验器实施例中,各自基于mems的柱的光点直径经设计为在4nm到15nm的范围内。以下表1展示针对各自具有独立射束操纵能力的10个基于mems的柱实现的5百万个随机分布位点的处理量计算。通过添加更多基于mems的柱,尽管不需要但可覆盖甚至更高数目个位点。表1跨晶片的n个位点n个基于mems的柱5,000,0001010,000,0002050,000,000100图3b说明根据本发明的一个实施例的用于在载物台在下面移动时用电子束扫描缺陷的简化跟踪模式技术350。在用于电子束柱实施方案的跟踪模式中,射束在晶片移动时移动(针对高处理量)。在此实例中,射束从在固定位置中的阵列的探针(或柱)发射。柱扫描场由具有列a到f及行1到3的网格表示。每一网格位置可对应于像素。缺陷354含于具有2列x3行(或2x3像素)的尺寸的缺陷区域中。首先,载物台使缺陷相对于柱扫描场移动到位置352a,使得缺陷区域对准到柱扫描场的右边缘且在时间步长1获取扫描场位置f1的数据。接着,载物台使缺陷区域向左移动一个像素到位置352b,且射束向下移动一个像素且向左移动一个像素以在时间步长2获取扫描场位置e2的数据。同样,载物台使缺陷区域向左移动一个像素到位置352c,且射束向下及向左移动一个像素(“跟踪”)以在时间步长3获取扫描场位置d3的数据。接着,射束移动回到顶部(驰返),且载物台使缺陷区域向左移动一个像素到位置352d且在时间步长4获取扫描场位置d1的数据。此过程针对定位于352e及352f处的缺陷区域继续进行,射束针对所述缺陷区域移动以分别在时间5获取扫描场位置c2处的数据及在时间6获取扫描场位置b3处的数据。在6个时间步长之后,通过射束移动356完全扫描缺陷。上述跟踪模式技术表示优于帧模式及扫描带模式技术的改进(例如,显著增加的处理量)。图3c说明简化帧模式技术370。在帧模式中,缺陷区域搁置在柱扫描场下面,且射束以图案376移动。通过射束扫描缺陷,所述射束在时间序列1到6中移动到缺陷区域的每一像素,使得在时间1到6获取数据。图3d说明简化扫描带模式技术390。在扫描带模式中,晶片缺陷区域对准到柱扫描场的右边缘且停止于位置392a处。柱在时间步长1到3从顶部扫描到底部(图案396);记录信息;且接着移动回到顶部。同时,晶片向左前进一个像素到位置396b且与晶片像素的第二列对准到柱扫描的左边缘。柱接着在时间步长4到6中再次向下扫描(图案396)以捕获最后3个晶片像素。在某些实施例中,用于扫描所有缺陷的时间不能超过扫描带扫描晶片所花费的时间,且载物台移动的有效扫描长度不能超过柱的fov尺寸。柱最小覆盖区可受串扰限制,所述串扰还可限制柱的最大数目及可实现的最大处理量。第二阶段检验器可经配置以按任何合适方式扫描候选位点。图4a到4e说明各种第二阶段检验器配置及扫描技术。在所有情况中,第一阶段检验器对每一潜在缺陷/扰乱点位点提供位置坐标,且检验器操作以通过各种位置确定机构精确地移动到样本上的每一潜在位点。此可通过如图4a中所展示那样移动载物台、如图4b中所展示那样移动探针阵列、如图4c中所展示那样移动载物台及探针阵列两者,或如图4d及4e中所展示那样使载物台旋转来实现。为精确地跟踪操纵载物台或阵列的轨道的运动的探针位置,激光干涉器反馈机构可用于精细调谐探针定位。所述激光干涉器可安装于载物台上或探针阵列上。每一探针的精细位置调谐经独立地操作以实现用于每一探针的最高位置准确度。在所有这些实例中,每一探针经配置以扫描在其相应扫描带中的每一候选位点。图4a说明根据本发明的一个实施例的具有固定位置的探针402的线性阵列及其上具有在固定探针402下方移动的晶片的载物台404。在此实施例中,检验器还可包含用于准确地确定相对于每一探针的晶片位置的一对干涉器406。可视需要使用更多激光干涉器。干涉器是沿着载物台的x轴及y轴两者定位以跟踪两个方向。额外激光干涉器可用于跟踪探针的位置。此可为最少两个(x&y)直到最大每探针一个。还可使用静态高度图实施或用定位于每一探针处的传感器动态实施z高度映射。例如,所述z高度传感器可为光学的以便实现任何表面的高度映射。单独单个探针的焦深可能不足以补偿样本高度的变动。此实施例还包含相对较大腔室以适应使晶片在探针下方来回移动的载物台移动。此外,载物台跨晶片来回扫描,使得此布置与周转时间及由减速及加速引起的振动相关联。图4b展示根据本发明的替代实施例的可操作以相对于固定晶片载物台移动的分布式探针系统。如所展示,线性探针阵列412在如图4b中所指示的探针扫描方向上移动并扫描,而载物台及晶片414保持于固定位置中。此外,检验器可包含用于确定沿着n数目个轴的位置的n轴干涉器(例如,416)。在此实施例中,腔室可相对较小,这是因为在探针仅遍及此载物台扫描时载物台是静止的。然而,探针可使用移动伸缩囊(bellow)以实现2d移动。此实施例还具有相关联的周转时间及振动效应。图4c展示根据本发明的另一替代实施例的可操作以相对于正交于探针移动方向移动的晶片载物台424而移动的探针系统422的线性阵列。在此实例中,第一干涉器镜面426a与探针一起安装以跟踪在一个方向上的移动及位置,而第二镜面426b与载物台424一起安装以跟踪在另一、正交方向上的移动及位置。当然,检验器可包含用于跟踪其它移动方向(例如z、倾斜或旋转)的额外干涉器。此实施方案与小腔室、低质量及低阿贝(abbe)误差以及缓慢载物台扫描相关联。然而,探针可使用伸缩囊以实现1d移动。此实施例还具有相关联的周转时间及振动效应。图4d说明根据本发明的又另一实施例的在载物台及晶片434旋转时沿着单轴移动的探针阵列432。此系统包含用于跟踪探针移动及位置的至少一个径向干涉器镜面436a,以及用于跟踪载物台的移动及位置的高分辨率旋转编码器436b。当然,检验器可包含用于跟踪其它移动方向的额外干涉器。此实施例还不具有任何相关联的周转时间或振动效应,这是因为在检验期间射束来回扫描,而晶片仅自旋而不加速或减速。图4e说明根据本发明的另一实施例的线性探针阵列的辐条布置及旋转载物台。如所展示,探针阵列(例如,442a及442b)各自布置于围绕晶片载物台444的固定辐条位置处,且每一阵列可沿着径向方向移动。载物台及晶片444经配置以在探针辐条下面旋转,所述探针辐条在晶片旋转时径向移动。检验器还可包含用于跟踪探针移动的径向镜面(例如,446a及446b)及用于跟踪载物台的移动及位置的高精度旋转编码器448。此实施例可与小腔室、低质量、低阿贝误差及用于2d移动的移动伸缩囊相关联。此实施例也不具有任何相关联的周转时间或振动效应,这是因为射束来回扫描,而仅晶片自旋。本文中所描述的双载物台系统实施例可以任何合适方式实施。图5a到5d展示根据本发明的若干实施例的混和式检验系统(500、520、530、540)的变动。在所有图中,经组合检验器分别包含机器人晶片处置系统502、光学检验器504、高分辨率、分布式检验器506、晶片装载位置508及晶片装载位置510。机器人晶片处置系统502经配置以往返于光学检验器504及高分辨率、分布式检验器506以及往返于晶片装载位置508及晶片装载位置510转移晶片。光学检验器504经配置以检测如上文所描述的包含扰乱点位点的潜在缺陷位点。高分辨率、分布式检验器506经配置以快速扫描位点以区分潜在缺陷位点与扰乱点位点。晶片装载位置508及晶片装载位置510经配置以固持一或多个晶片。在大多数情况中,其固持多个晶片。所述晶片可来自同一批次或来自不同批次。在图5a及5d中,光学检验器504及高分辨率、分布式检验器506是经由机器人晶片处置系统502集成的不同系统。在图5b中,高分辨率、分布式检验器506集成到光学检验器504中或反之亦然。在图5c中,高分辨率、分布式检验器506或光学检验器504集成到机器人晶片处置系统502中,其中另一检验器504/506与晶片处置系统502分离。在一个操作中,来自晶片装载位置508及/或510的一些晶片具有在光学检验器506处检测的潜在缺陷及扰乱点位点,且此后,具有在高分辨率、分布式检验器506处产生的所述位点的高分辨率图像以用于使潜在缺陷位点与扰乱点位点分离。可在两个检验器未自系统移除的情况下由所述两个检验器检验晶片,例如,减少晶片处置以及与其相关联的处理量问题。如果光学检验器与呈sem系统的形式的分布式、高分辨率系统集成,那么两个检验器可共享同一真空腔室。然而,独立sem检验器仅需要单个较小真空腔室。此经组合系统的某些实施例在少于2小时内允许5nm全晶片检验敏感度。混和式检验器系统利用光学检验器及高分辨率系统的优势。此混和式系统的检验器一起提供光学检验器或高分辨率检验器都无法单独实现的解决方案(其将解决行业性能差距)。总的来说,在某些实施方案中提供在少于2小时内实现跨300mm晶片的5nm缺陷敏感度的高敏感度、高处理量混和式检验器。第一阶段光学检验器可利用积极阈值检验以允许通过光学检验器阶段检测doi,且第二阶段检验器接着使用高分辨率用于在第一阶段中检测的位点的doi与扰乱点区分。可实施用于如本文中所描述在第一阶段中检测大量潜在缺陷及扰乱点位点的任何合适光学检验工具。特定检验器工具实施例提供灵活波长选择以便覆盖广泛范围的晶片材料性质及结构。此外,检验工具可操作以提供较短波长且可包含灵活偏光选择以便获得最佳信号。检验系统还可操作以收集一次扫描中的更多信息以改进检验处理量、缺陷分类、扰乱点抑制。一般来说,用于实施本发明的技术的适用光学检验工具可包含用于产生选定波长的入射光射束以检测不同材料类型及结构类型中的缺陷的至少一个光源。此检验还可包含用于将所述入射射束引导到受关注区域的照明光学器件、用于引导响应于入射射束从受关注区域发射的输出射束的集光光学器件、用于检测输出射束且从所述经检测输出射束产生图像或信号的传感器,及用于控制检验工具的组件及促进缺陷检测的控制器。在一个实施例中,检验工具包含用于产生及收集广泛范围的波长(高于190nm到950nm)的光的照明及集光模块。检验器工具还可提供用于平行及垂直电子场的偏光选项及用于跨针对长及短波长路径中的每一者的波长范围而应用的一组副频带波长滤波器。图6是根据本发明的特定实施方案的光学检验系统600的图解表示。如所展示,系统600包含产生照明光605的宽带光源(例如,照明器604)。光源的实例包含激光驱动光源、高功率等离子体光源、透穿照射光源(例如,卤素灯或xe灯)、滤光灯、led光源等。除宽带光源之外,检验系统还可包含任何合适数目及类型的额外光源。来自光源的入射射束可通常行进穿过用于中继(例如,塑形、聚焦或调整焦点偏移、过滤/选择波长、过滤/选择偏光状态、重设大小、放大、降低失真等)所述射束朝向样本的任何数目及类型的透镜。照明器604可包含用于产生具有选定波长范围的入射射束的任何合适光学元件。例如,照明器604可包含具有个别地插入(或旋转)到照明路径中以改变照明射束的波长的可选择带通滤波器的滤光色轮601。通常,每一检验波长范围可基于其照明及集光光瞳孔径形状的优化、入射及集光路径的偏光、放大倍率、像素大小或其任何组合来选择。照明器还可包含可用于进一步定义入射射束的光谱的一或多个额外光谱滤波器(例如,603)。例如,每一光谱滤波器可进一步用于优化预期捕获的缺陷的敏感度。分离偏光滤波器606还可选择性地定位于入射射束路径中以进一步优化针对不同波长范围的检验敏感度。光瞳中继器(未展示)还可用于对入射光进行重新成像且将光瞳聚焦到物镜632处的系统光瞳上。50-50光束分离器628可用于将光发送到物镜632。50-50光束分离器628还可经布置以朝向集光光学器件发送从样本反射或散射的光。共轭到系统光瞳(定位于物镜处)的光瞳可用于入射射束路径中。每一光瞳或孔径可具有特定形状以模糊光路径的部分以最大化用于选定波长范围的信号。物镜632优选地针对用于缺陷检测的所有可选择波长优化。例如,物镜632具有包含透镜涂层的组合物及用于校正色差的布置。在替代实施例中,物镜632可为全反射物镜或折射或组合(反射折射)配置。接着可通过另一二向色光束分离器637接收从样本反射或散射的所得输出射束,所述二向色光束分离器637可经布置以经由自动聚焦系统635将自动聚焦插入到物镜632中。自动聚焦射束可具有与不同检验频带分离的波长。用于自动聚焦的波长只要其不在用于选定检验波长范围中的任一者的检验波带中便可被改变。组件的成本及可用性可影响自动聚焦插入所定位之处。自动聚焦波长带可为40nm或更小以最小化归因于晶片材料响应的焦平面变化。例如,自动聚焦系统635可使用led光源。二向色光束分离器637可经布置以反射自动聚焦波带且透射所述区域上方及下方的所有光。50-50光束分离器628还可经配置以依高效率(例如,通过使用涂层)传递自动聚焦光。此元件可改进自动聚焦的光效率达将近4倍。如果自动聚焦波长远高于可选择检验波长范围,那么自动聚焦射束将受不同于检验成像系统的热诱发焦点变化影响。系统可包含对归因于环境(温度、压力)、透镜加热等的焦点变化提供反馈的机构。通过实例,自动聚焦系统635可包含呈温度及压力传感器的形式的反馈机构及安装于晶片卡盘的侧面上用于评估焦平面变化的校准晶片。基于反馈,自动聚焦系统635可调整透镜元件中的一或多者(例如通过移动透镜以形成可调整气隙)以引入焦点校正。校正的频率还可基于此反馈确定。输出射束可由任何合适数目及类型的集光光学器件引导及塑形,例如光瞳中继器(透镜群组640)及镜面638、偏光器607、孔径609及用于变焦及将输出射束聚焦到传感器654上的光学元件610及612。通过实例,传感器654可呈ccd(电荷耦合装置)或tdi(时延积分)检测器、光电倍增管(pmt)或其它传感器的形式。光瞳中继器640可经设计以形成系统光瞳(在物镜632处)的图像以用于将特定孔径(609)插入于集光路径中以优化针对每一波长范围的检验敏感度。可选择不同孔径设置以实现样本上的不同入射角。偏光滤波器(605或607)可定位于照明或集光路径中以用于还优化检验敏感度的目的。系统还可包含控制器或计算机系统(例如,690)。例如,可由控制器690处理由每一检测器捕获的信号,所述控制器690可包含具有经配置以将来自每一传感器的模拟信号转换成数字信号以用于处理的模拟转数字转换器的信号处理装置。控制器可经配置以分析经感测光射束的强度、图像、相位及/或其它特性。控制器可经配置(例如,具有编程指令)以提供用于显示所得测试图像及其它检验特性的用户接口(例如,在计算机屏幕上),如本文中进一步描述。控制器还可包含用于提供用户输入(例如改变波长、偏光或孔径配置、观看检测结果数据或图像、设置检验工具配方)的一或多个输入装置(例如,键盘、鼠标、操纵杆)。可以硬件及/或软件的任何合适组合实施本发明的技术。控制器通常具有耦合到输入/输出端口的一或多个处理器及经由适当总线及其它通信机构的一或多个存储器。控制器可为软件及硬件的任何合适组合且通常经配置以控制检验系统的各种组件。例如,控制器可控制照明源的选择性激活、照明或输出孔径设置、波长带、焦点偏移设置、偏光设置等。控制器还可经配置以接收由每一检测器产生的图像或信号且分析所得图像或信号以确定样本上是否存在候选缺陷/扰乱点、特性化存在于样本上的缺陷或以其它方式特性化样本。例如,控制器可包含经编程以实施本发明的方法实施例的指令的处理器、存储器及其它计算机外围设备。因为这些信息及程序指令可实施于特殊配置的计算机系统上,所以此系统包含可存储于计算机可读媒体上用于执行本文中所描述的各种操作的程序指令/计算机程序代码。机器可读媒体的实例包含(但不限于):磁性媒体,例如硬盘、软盘及磁带;光学媒体,例如cd-rom光盘;磁光媒体,例如光学磁盘;及经特殊配置以存储及执行程序指令的硬件装置,例如只读存储器装置(rom)及随机存取存储器(ram)。程序指令的实例包含例如通过编译过程产生的机器程序代码及含有可由计算机使用解译器执行的较高阶程序代码的文件两者。可实施用于如本文中所描述在第一阶段中将潜在缺陷位点与扰乱点位点分离的任何合适高分辨率、分布式检验工具。大体上参考图7,描述根据本发明的特定实施方案的适于将带电粒子聚焦于多个探针中的分布式高分辨率系统700。在一个实例中,系统700包含布置于线性阵列支撑件706中的多个探针(例如,702a及702b)。多个带电粒子源(例如,707a及707b)可经布置以产生带电粒子束且将其引导朝向探针中的每一者,其中每一探针将其对应带电粒子束引导朝向样本(例如,晶片701)。替代性地,每一源可与每一探针集成。每一带电粒子源可包含所属领域中已知的任何源。例如,源902可包含(但不限于)一或多个电子枪。每一探针或柱可包含用于聚焦由其相应带电粒子源发射的其对应射束的任何数目个透镜及组件、跨晶片样本的缺陷区域扫描其射束的偏转器,及响应于照射带电粒子束检测来自晶片样本的发射且形成高分辨率图像的检测器。在一个方面中,透镜阵列中的每一柱是基于微型mems的柱。在一些实施例中,每一柱可进一步包含一组电子光学元件。所述一组电子光学器件可包含所属领域中已知的适于将电子束聚焦及/或引导到样本701的选定部分上的任何电子光学元件。在一个实施例中,所述一组电子光学元件包含一或多个电子光学透镜。例如,电子光学透镜可包含(但不限于)用于从电子束源收集电子的一或多个聚光透镜。通过另一实例,电子光学透镜可包含(但不限于)用于将对应电子束聚焦到样本701的选定区域上的一或多个物镜。在一些实施例中,可以受控角度将每一电子束引导到样本701。因为所提供的晶片系统坐标并不一定与sem坐标系重合,所以控制精细扫描角度可改进坐标系之间的匹配且显著促进取样性能/准确度。在一些实施例中,用于每一柱的所述一组电子光学元件包含一或多个电子束扫描元件。例如,所述一或多个电子束扫描元件可包含(但不限于)适于控制射束相对于样本701的表面的位置的一或多个扫描线圈或偏转器。在此方面,一或多个扫描元件916可用于以选定扫描方向或图案跨样本701扫描电子束。例如,可相对于特定结构的特征放置(例如,以双向方向及相对于目标线成角度)以倾斜或垂直双向扫描来扫描样本701。控制器系统718可通信地耦合到电子光学元件中的一或多者(例如一或多个扫描元件)。因此,控制器系统718可经配置以经由传输到每一组通信耦合的电子光学元件的控制信号来调整一或多个电子光学参数及/或控制扫描方向。在一些实施例中,每一柱可包含用于每一柱的包含电子收集器(例如,二次电子收集器)的检测器组合件(或与所述检测器组合件相关联)。检测器组合件可进一步包含(例如)基于阻滞场原理的能量过滤器。在此方面,所述能量过滤器可经配置以阻止低能量二次电子而使高能量二次电子(即,反向散射电子)通过。如果未激活能量过滤器,那么根据检测系统的收集效率检测所有二次电子。通过从总电子图像减去高能量电子图像,可获得低能量二次电子图像。检测器组合件可进一步包含用于检测来自样本表面的电子(例如,二次电子)的检测器(例如,闪烁元件及pmt检测器)。在一些实施例中,检测器组合件的所述检测器包含光检测器。例如,检测器的pmt检测器的阳极可包含磷阳极,所述磷阳极是由所述pmt检测器的通过阳极吸收的级联电子通电且可随后发射光。光检测器又可收集通过磷阳极发射的光以便对样本906进行成像。光检测器可包含所属领域中已知的任何光检测器,例如(但不限于)ccd检测器或ccd-tdi检测器。系统700可包含额外/替代检测器类型,例如(但不限于)everhart-thornley型检测器。虽然前文描述在二次电子的收集的上下文中集中于每一检测器组合件,但此不应被解释为限制本发明。本文中应认知,每一检测器组合件可包含所属领域中已知的用带电粒子束对样本表面或块体进行成像或特性化的任何装置或装置组合。例如,每一检测器组合件可包含所属领域中已知的经配置以收集反向散射电子、欧杰(auger)电子、经传输电子或光子(例如,通过表面响应于入射电子发射的x射线)的任何粒子检测器。晶片样本701支撑于与载物台708耦合的卡盘710上。在典型布置中,所述载物台具有其上定位及附装晶片的可旋转卡盘。在某些实施例中,载物台701、卡盘710及/或阵列支撑件706可经配置以具有移动机构以在一或多个方向(包含x、y、z、倾斜及旋转方向)上移动。每一柱可一起移动或独立移动。这些移动机构可采用由一或多个螺丝起子及步进发动机、具有反馈位置的线性驱动、带致动器及步进发动机、磁场等驱动的粗糙等级移动机构及精细等级移动机构两者的形式。所述移动机构还可实施滚柱轴承、空气轴承、滑动塑料轴承、挠曲悬架或磁场悬架等。在其它实施例中,柱系统可替代性地或另外在一或多个方向(包含x、y、z、倾斜及旋转方向)上移动。干涉器镜面可随着载物台708及/或阵列支撑件706沿着移动方向中的每一者定位,如参考图4a到e的实施例所示范。在图7中,镜面714a及714b定位于载物台708的每一x及y轴上,且镜面714c及714d定位于阵列支撑件708的每一x及y轴上。所述镜面形成干涉器系统的部分以用于准确地确定位点位置。如果载物台或阵列并不移动,那么可移除其对应镜面。控制器系统718可经配置以用于控制系统700的任何合适组件,以及接收及处理由柱的检测器获取的高分辨率图像。控制系统718可通信地耦合到系统700的各种组件。控制系统可包含用于控制、处理及分析的一或多个处理器及电子组件。控制系统718可经配置以经由到每一源的控制信号调整一或多个带电粒子源参数。例如,控制系统718可经配置以经由传输到电子束源的控制电路的控制信号改变由每一源发射的电子束的射束电流。在一些实施例中,控制系统718通信地耦合到样本载物台708及/或柱组合件。控制系统718可经配置以经由传输到样本载物台708的控制信号调整一或多个载物台参数。控制系统718可经配置以经由传输到样本载物台708及/或柱组合件的控制电路的控制信号改变样本扫描速度及/或控制扫描方向。例如,控制系统718可经配置以改变样本701及/或柱组合件线性平移的速度及/或控制样本701及/或柱组合件线性平移的方向(例如,x方向或y方向)。在一些实施例中,控制系统718通信地耦合到每一检测器或检测器组合件。控制系统718可经配置以经由传输到每一检测器的控制信号调整一或多个图像形成参数。例如,控制系统718可经配置以调整用于二次电子的提取电压或提取场强度。所属领域的一般技术人员将了解,“控制系统718”可包含一或多个计算系统或控制器,例如经配置以执行嵌入于由至少一个非暂时性信号承载媒体存储的程序指令中的一或多个指令集的一或多个处理器。计算系统924可控制各种扫描。控制系统718可经配置以由可包含有线及/或无线部分的传输媒体从其它系统接收及/或获取数据或信息(例如,经检测信号/图像、统计结果、参考或校准数据、训练数据、模型、经提取特征或变换结果、经变换数据集、曲线拟合、定性及定量结果等)。以此方式,所述传输媒体可用作控制系统718与其它系统(例如,存储器板载检验器系统、外部存储器、参考检验器源或其它外部系统)之间的数据链路。例如,控制系统718可经配置以经由数据链路从存储媒体(例如,内部或外部存储器)接收来自光学检验器的位点位置。例如,使用检验器700系统获得的结果可存储于永久或半永久存储器装置(例如,内部或外部存储器)中。在此方面,结果可从板载存储器或从外部存储器系统导入。此外,控制系统718可经由传输媒体将数据发送到其它系统。例如,由控制系统718确定的定性及/或定量结果(例如度量值)可经传送并存储于外部存储器中。在此方面,候选缺陷数据结果可被导出到另一系统。控制系统718可包含(但不限于)个人计算机系统、大型计算机系统、工作站、图像计算机、并行处理器或所属领域中已知的任何其它装置。一般来说,术语“计算系统”可经广泛定义以涵盖具有执行来自存储器媒体的指令的一或多个处理器的任何装置。程序指令可存储于计算机可读媒体(例如,存储器)中。示范性计算机可读媒体包含只读存储器、随机存取存储器、磁盘或光盘或磁带。计算算法是通常针对其中使用一或多个方法的计量应用(例如计算硬件的设计及实施方案、平行化、计算分布、负载平衡、多服务支持、动态负载优化等)而优化。可在固件、软件、fpga、可编程光学组件等中完成算法的不同实施方案。分离高分辨率系统可用于缺陷重检。此系统通常将具有高于第二阶段检验器的分辨率。在替代实施例中,第二阶段检验器可包含经特别配置以实现高于其它扫描柱的分辨率的一或多个柱。在电子束柱实例中,作为第二阶段系统的一部分或与第二阶段系统分离的系统经配置以如相较于施加到第二阶段柱的电流的电流施加较低电流到重检柱,使得重检柱实现相对高于第二阶段柱的分辨率。在其它实施例中,较高分辨率探针系统及高分辨率分布式探针系统可为不同类型的系统,例如用于较高分辨率系统的afm探针及用于分布式探针的电子束系统或本文中所描述的探针的任何组合。本文所呈现的本发明的某些实施例通常解决半导体检验及工艺控制的领域,且并不限于上文所概述的硬件、算法/软件实施方案及架构以及使用案例。尽管已为了清楚了解的目的相当详细地描述前述发明,但将明白,可在所附权利要求书的范围内实践某些改变及修改。应注意,存在实施本发明的过程、系统及设备的许多替代方式。因此,本实施例应被视为说明性而非限制性,且本发明不限于本文中给定的细节。当前第1页12