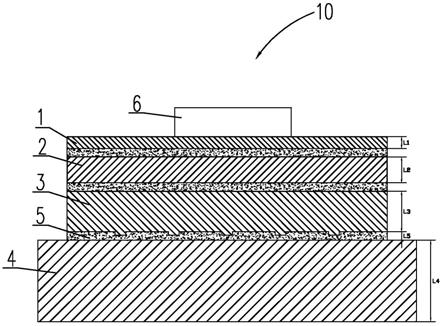
[0001]
本实用新型涉及碳化硅器件封装领域,尤其涉及一种高导热率碳化硅器件封装结构。
背景技术:[0002]
碳化硅功率半导体器件通常包括硅芯片,半导体电路、电路基板及热沉。碳化硅半导体器件可以在250℃~300℃的温度下稳定地操作,可以显着增加功率器件的输出。电路基板具有绝缘性,由导热率较高的氮化铝等组成。热沉具有较高导热率并确保更容易大面积制造的散热器件,例如cu,al,cu-mo或cu-w。使用粘接剂和焊料等将各部件粘接。金属层位于芯片和热沉之间,承担着散热过渡和应力过渡的双重作用,铜的线性热膨胀系数与半导体衬底的热膨胀系数相差较大,封装时热应力施加于衬底。基板由于温度的变化导致反复弯曲,易使陶瓷板及软钎料结合位置产生裂缝,导致封装基板翘曲,粘接部位脱开,可靠性降低。
[0003]
常规减少功率模块基板的翘曲是通过提高热沉热量散失量,从而降低功率模块基板温度水平,进而减小线性膨胀差。随着碳化硅器件功率的增大,热量产生量增加,基板与热沉的散热量以及功率模块基板间温差以及材料翘曲量需进一步的改进。
技术实现要素:[0004]
鉴于此,有必要提供一种高导热率碳化硅器件封装结构,能够有效减少封装结构翘曲,提高碳化硅器件结构的导热率和可靠性。
[0005]
本实用新型为达上述目的所提出的技术方案如下:
[0006]
一种高导热率碳化硅器件封装结构,包括热沉,所述高导热率碳化硅器件封装结构还包括绝缘基板、电路层及金属层,所述绝缘基板位于所述电路层及所述金属层之间,所述金属层的下表面形成有若干导热窗口,并覆盖于所述热沉上,所述电路层的厚度在0.1mm~3.0mm的范围内,用于通过刻蚀形成所需的电路图案,所述绝缘基板用于防止所述电路层与所述金属层电性接触,所述金属层的厚度在0.1mm~4.0mm的范围内,用于减少所述绝缘基板与所述热沉之间线性膨胀差,且所述金属层与所述电路层的厚度之比大于或等于1.4且小于或等于12。
[0007]
进一步地,所述若干导热窗口呈阵列分布,所述若干导热窗口的形状均为圆柱体、长方体或三菱柱体中的一种。
[0008]
进一步地,所述绝缘基板为氮化铝陶瓷材料、氧化铝陶瓷材料或者碳化硅陶瓷材料中一种。
[0009]
进一步地,所述电路层、所述绝缘基板、所述金属层及所述热沉之间每相邻的叠层之间设有粘接层,所述粘接层为活性金属钎焊材料。
[0010]
进一步地,所述热沉为al-sic多孔复合材料。
[0011]
上述实用新型提供的高导热率碳化硅器件封装结构通过将电路层的厚度设计在
0.1mm~3.0mm的范围内,还通过将金属层的厚度设计在0.1mm~4.0mm的范围内,并使得所述金属层与所述电路层的厚度之比大于或等于1.4且小于或等于12。如此,可有效减少器件封装结构翘曲,提高碳化硅器件的可靠性。
附图说明
[0012]
图1为本实用新型的高导热率碳化硅器件封装结构的一较佳实施方式的剖面示意图。
[0013]
图2为图1中金属层及金属层下表面的一较佳实施方式的结构示意图。
[0014]
图3为图1中金属层下表面的另一较佳实施方式的结构示意图。
[0015]
图4为本实用新型的高导热率碳化硅器件封装结构的翘曲测量示意图。
[0016]
主要元件符号说明
[0017]
碳化硅封装结构
ꢀꢀꢀꢀꢀꢀꢀꢀꢀꢀꢀꢀꢀꢀꢀꢀ
10
[0018]
电路层
ꢀꢀꢀꢀꢀꢀꢀꢀꢀꢀꢀꢀꢀꢀꢀꢀꢀꢀꢀꢀꢀꢀꢀꢀ1[0019]
绝缘基板
ꢀꢀꢀꢀꢀꢀꢀꢀꢀꢀꢀꢀꢀꢀꢀꢀꢀꢀꢀꢀꢀꢀ2[0020]
金属层
ꢀꢀꢀꢀꢀꢀꢀꢀꢀꢀꢀꢀꢀꢀꢀꢀꢀꢀꢀꢀꢀꢀꢀꢀ3[0021]
导热窗口
ꢀꢀꢀꢀꢀꢀꢀꢀꢀꢀꢀꢀꢀꢀꢀꢀꢀꢀꢀꢀꢀꢀ
32
[0022]
热沉
ꢀꢀꢀꢀꢀꢀꢀꢀꢀꢀꢀꢀꢀꢀꢀꢀꢀꢀꢀꢀꢀꢀꢀꢀꢀꢀ4[0023]
粘接层
ꢀꢀꢀꢀꢀꢀꢀꢀꢀꢀꢀꢀꢀꢀꢀꢀꢀꢀꢀꢀꢀꢀꢀꢀ5[0024]
如下具体实施方式将结合上述附图进一步说明本实用新型。
具体实施方式
[0025]
为了使本实用新型的目的、技术方案及优点更加清楚明白,下面结合附图和具体实施例对本实用新型作进一步详细说明。应当理解,此处所描述的具体实施例仅仅用以解释本实用新型,并不用于限定本实用新型。
[0026]
本实用新型提供了一种高导热率碳化硅器件封装结构10。请参考图1,图1 为本实用新型的一较佳实施方式的剖面示意图。所述高导热率碳化硅器件封装结构10包括电路层1、绝缘基板2、金属层3及热沉4。所述绝缘基板2位于所述电路层1及所述金属层3之间,所述金属层3的下表面覆盖于所述热沉4上。
[0027]
所述电路层1由铜或铜合金构成的铜板形成,用于通过刻蚀形成所需的电路图案。所述电路层1的厚度在0.1mm~3.0mm的范围内。所述绝缘基板2为氮化铝陶瓷材料、氧化铝陶瓷材料或者碳化硅陶瓷材料中一种,用于防止所述电路层1与所述金属层3电性接触。所述绝缘基板2的厚度在0.3mm~1.0mm的范围内。所述金属层3由铜或铜合金构成的铜板形成,用于减少所述绝缘基板2 与所述热沉4之间线性膨胀差,承担着散热过度和应力过度的双重作用。所述金属层3的厚度在0.1mm~4.0mm的范围内。所述金属层3的厚度与所述电路层1的厚度之比大于或等于1.4且小于或等于12。
[0028]
进一步地,所述电路层1、所述绝缘基板2、所述金属层3及所述热沉4之间每相邻的叠层之间均设有粘接层5。所述粘接层5为活性金属钎焊材料,如金锡焊料。所述粘接层5的厚度在0.015mm~0.3mm的范围内。
[0029]
具体而言,当所述金属层3厚度l3太大时,所述金属层3热膨胀将导致所述绝缘基
板2破裂;当所述金属层的厚度l3太小时,所述金属层3强度不够,所述绝缘基板2与所述热沉4之间将产生翘曲。当所述电路层1的厚度l1太小时,所述电路层1与所述绝缘基板2之间的粘接层5中的粘合材料可能通过加热而渗出所述电路层1的表面;当所述电路层1的厚度l1过大时,由于金属膨胀系数大于陶瓷的膨胀系数,所述绝缘基板2在受热后可能会破裂。而当所述电路层1的厚度l1大于所述金属层3的厚度l3时,所述电路层1的热膨胀影响将增加,从而产生翘曲。
[0030]
如此一来,通过合理设置所述电路层1与所述金属层3的厚度比例关系,可有效减少所述电路层1、所述绝缘基板2、所述金属层3与所述热沉4之间产生的翘曲。
[0031]
请参考图2及图3,所述金属层3的下表面形成有若干导热窗口32。所述若干导热窗口32埋设于所述金属层3与所述热沉4之间的粘接层5中。所述若干导热窗口32呈阵列分布。所述若干导热窗口32的形状均为圆柱体、长方体或三菱柱体中的一种。所述若干导热窗口32的厚度小于或等于所述粘接层5的厚度,以保证粘接可靠性。所述若干导热窗口32的厚度在0.005mm~0.2mm的范围内。如此,可在热导率相对较低的粘结层5中设置通道,增大了导热接触面积,从而高效地导出热量;同时阵列分布的导热窗口32也有助于增强所述金属层3的强度,减小所述金属层3的厚度。如此,可进一步地减少器件封装结构翘曲,提高碳化硅器件的导热率和可靠性。
[0032]
所述热沉4为al-sic多孔体复合材料,其中sic粉末的重量占比为92%以上。在本实施方式中,sic粉末的重量占比为96%以上,且含有金属元素(如铁、镍和钴元素)的质量少。al/sic陶瓷复合材料可以通过熔渗法来制备,具体而言,通过熔融渗透法将al渗透到三维sic陶瓷网络结构孔中,制得复合材料冷却至室温并从腔室中取出,经过研磨工艺,放电加工工艺和抛光工艺等,产生具有预定形状的热沉。
[0033]
需要说明的是,上述提供的封装结构,其不但可以用于与碳化硅器件模块封装,还可以用于与其他半导体功率器件封装,从而达到提高散热效率,减小翘曲变形的目的。
[0034]
请参考图4,图4为本实用新型的一较佳实施方式的高导热率碳化硅器件封装结构翘曲测量示意图。将所述热沉4和所述金属层3接合表面的中心c设置为测量区域s的中心,将测量区域s最长长度设置为l。当所述热沉4在测量区域s中加热到250℃时,长度l在垂直方向移动的翘曲值为x,范围在-40
×
10-6 (mm-1
)~40
×
10-6
(mm-1
)之间;当所述热沉4冷却到30℃时,长度l在垂直方向移动的翘曲值为y,范围在-20
×
10-6
(mm-1
)~20
×
10-6
(mm-1
)之间。x和 y的差值(y-x)在-15.0
×
10-6
(mm-1
)~15.0
×
10-6
(mm-1
)之间。由此看出,本实用新型提供的高导热率碳化硅器件封装结构可有效地减少器件封装结构翘曲。
[0035]
综上所述,本实用新型提供的高导热率碳化硅器件封装结构通过将电路层1 的厚度设计在0.1mm~3.0mm的范围内,还通过将金属层3的厚度设计在 0.1mm~4.0mm的范围内,并使得所述金属层3与所述电路层1的厚度之比大于或等于1.4且小于或等于12。如此,可有效减少器件封装结构翘曲,提高碳化硅器件的导热率和可靠性。
[0036]
以上内容是结合具体/优选的实施方式对本实用新型所作的进一步详细说明,不能认定本实用新型的具体实施只局限于这些说明。对于本实用新型所属技术领域的普通技术人员来说,在不脱离本实用新型构思的前提下,其还可以对这些已描述的实施方式做出若干替代或变型,而这些替代或变型方式都应当视为属于本实用新型的保护范围。在本说明书的描述中,参考术语“一种实施例”、“一些实施例”、“优选实施例”、“示例”、“具体示
例”、或“一些示例”等的描述意指结合该实施例或示例描述的具体特征、结构、材料或者特点包含于本实用新型的至少一个实施例或示例中。在本说明书中,对上述术语的示意性表述不必须针对的是相同的实施例或示例。而且,描述的具体特征、结构、材料或者特点可以在任一个或多个实施例或示例中以合适的方式结合。此外,在不相互矛盾的情况下,本领域的技术人员可以将本说明书中描述的不同实施例或示例以及不同实施例或示例的特征进行结合和组合。