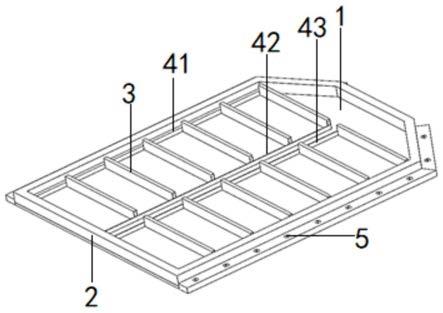
1.本发明属于新能源汽车电池托盘的技术领域,涉及一种新能源汽车用电池托盘及制备方法。
背景技术:2.目前,新能源汽车动力电池系统的重量缺陷与能量密度需求相矛盾,其中电池托盘占电池系统重量的20%-30%左右,电池包占整车重量的30%左右,因此,动力电池系统减重在汽车轻量化中具备经济意义,而其中的铝合金电池托盘的轻量化设计对于新能源汽车动力电池系统的重量缺陷的弥补具有非常重要的现实意义。
3.研究发现,电池托盘的轻量化设计主要包括材料轻量化和结构轻量化两种途径。其中:材料轻量化是通过设计强度高、比重轻的合金材料来实现;而结构轻量化则是通过优化托盘结构,从而减少材料使用量。
4.中国专利cn111334690a公开了一种应用于电池托盘的高强度铝合金型材,其目的是解决现有技术铝合金型材抗拉强度、屈服强度或耐腐蚀性能不佳等问题,但变形铝合金不适合制造结构复杂的零件,难以应用于现在所提倡的一体式电池托盘设计。
5.中国专利cn109860459a公开了一种符合ip67的电动汽车铝合金电池托盘,其目的是为了更好的冷却电池包,其中的铝合金电池托盘重点在于防水和冷却,并未考虑本发明的低成本、高强度和高散热,存在中间区域下沉几率大、冷却性能差、成本高的技术缺陷。
6.中国专利cn110265605a公开了一种电动汽车铝合金电池托盘,其目的是为了快速更换电池和更好的冷却电池包,电池托盘中冷却结构异常复杂,其中的进出液口、进出通道的结构设计使得冷却液体在汽车行进过程中存在漏液的风险,散热的稳定性差,成本高。
技术实现要素:7.本发明解决的技术问题是现有技术中的新能源汽车用电池托盘材质轻量化多采用6系铝合金,轻量化效果尚不理想;而电池托盘结构轻量化则是现有电池托盘底板为了避免中间区域下沉,一般采用较厚的单层铝板或者采用双层铝板在双层铝板之间增加龙骨结构,不利于整车轻量化设计;冷却结构设计异常复杂,成本高。
8.为解决上述技术问题,本发明提供如下技术方案:
9.一种新能源汽车用电池托盘,所述新能源汽车用电池托盘包括底板,所述底板上设置有边梁,所述边梁内设置有散热铝板、加强筋,所述边梁长度方向的两侧设置有若干吊耳;所述加强筋设置在所述边梁的内部,通过所述散热铝板将加强筋之间的容纳空间分隔成若干区域用来放置电池包。
10.优选地,所述边梁的结构为矩形和等腰梯形组合而成,所述矩形包括与所述梯形相连接的左侧边、右侧边、以及底边,所述梯形包括与所述矩形相连接的左腰、右腰和顶边。
11.优选地,所述左侧边、右侧边的内壁分别被左边长条加强筋和右边长条加强筋固定加强,所述两侧边之间的中线两侧等距离分别设置有左中长条加强筋和右中长条加强
筋。
12.优选地,在所述左边长条加强筋和左中长条加强筋之间通过所述散热铝板分隔成左若干区域用来放置左电池包组,在所述右边长条加强筋和左中长条加强筋之间通过所述散热铝板分隔成右若干区域用来放置右电池包组。
13.优选地,所述边梁是由中空的挤压型材首尾焊接形成。
14.优选地,所述吊耳设置于所述边梁的两侧,所需连接螺钉的数量为20,分布均匀,以确保电池托盘的吊耳能够在恶劣行驶条件下承载电池托盘稳定。
15.优选地,整体所述边梁和散热铝板焊接在所述底板上,所述散热铝板在左若干区域和右若干区域均匀排布。
16.优选地,所述散热铝板为中空结构,中空结构内填充有相变材料或冷却液。
17.优选地,所述新能源汽车用电池托盘的材料为高强铝铈合金,其化学成分按质量百分比计为:si 4.5-7.8wt.%、cu 3.2-4.7wt.%、mg 0.2-0.5wt.%、fe0.3-0.52wt.%、mn 0.24-0.5wt.%、ti 0.08-0.12wt.%、zr 0.01-0.05wt.%、v0.08-0.18wt.%、ce 0.06-0.12wt.%,其余为al和不可避免的杂质。
18.所述的新能源汽车用电池托盘的制备方法,所述制备方法包括如下步骤:
19.s1、原料选择:按所述高强铝铈合金成分进行配比,原料为纯铝和其他原料的中间铝合金;其中,mg元素需考虑10%-20%的烧损进行铝镁中间合金的选择,fe元素需考虑杂质的存在;
20.s2、预处理:将原材料在200-230℃下预热20-30min;
21.s3、熔炼:将步骤s2预处理后的原料,纯铝和铝硅、铝铜、铝锰、铝铁中间合金,按顺序依次加入炉内,炉内温度加热到730
±
50℃,保温20-30min,得到熔体;
22.s4、铝液处理:将步骤s3的熔体充分搅拌后,加入用量为熔体质量的0.5-1.0wt.%的除渣剂和精炼剂,精炼10-20min后扒去浮渣,之后静置20-30min;
23.s5、中间合金加入:向步骤s4中扒去浮渣的熔体中加入铝铈、铝镁和铝钛硼中间合金,充分进行搅拌;
24.s6、铸件:直至步骤s5中加入的中间合金都完全熔化后,再保温20-30min,之后进行浇注,待冷却后取出高强铝铈合金铸件;
25.s7、将高强铝铈合金铸件加工得到新能源汽车用电池托盘的底板、边梁、散热铝板、加强筋和吊耳,从而经过装配得到新能源汽车用电池托盘。通过对该材料托盘构件的有限元模拟,发现该材料和结构能够满足新能源汽车电池托盘所需的性能要求。
26.优选地,步骤s6所制备的高强铝铈合金铸件的二次枝晶臂间距平均为20μm。
27.优选地,与中国专利cn110643862a所公开的压铸铝硅合金力学性能(屈服强度150~190mpa,抗拉强度280~320mpa)相比,本发明提供的汽车电池托盘的铝硅铜合金,在不采用压铸工艺的情况下,合金屈服强度达170mpa以上,抗拉强度达250mpa以上。
28.优选地,步骤s6所制备的高强铝铈合金铸件屈服强度可达170mpa以上,抗拉强度可达250mpa以上,延伸率3.2%以上,硬度99hv以上。
29.优选地,步骤s7装配得到新能源汽车用电池托盘的底板结构的强度要求和厚度相比传统的电池托盘的底板结构分别降低了17%和25%。
30.本发明实施例提供的上述技术方案,至少具有如下有益效果:
31.上述方案中,本发明采用边梁和加强筋、散热铝板构成电池托盘的支撑结构,用来承受电池模块的重量,降低了底板结构的强度要求和厚度。
32.本发明的若干吊耳的结构设计能够避免吊耳在长时间的汽车颠簸或遭遇剧烈碰撞时传统电池托盘焊缝处失效断裂的问题。且吊耳是设置于边框两侧,能够起到承载整个电池系统的作用。为保证在复杂行驶条件下电池托盘仍能承载稳定,故而吊耳采用实体结构。
33.本发明的电池托盘包括底板、设置在底板四周的边梁和散热铝板,三者共同分割成容纳电池包的空间;底板和加强筋、散热板共同承受电池模块的重量,底板采用实体结构减小电池托盘的结构变形;边梁采用中空结构以满足轻量化要求。
34.本发明的加强筋由左边长条加强筋、右边长条加强筋和左中长条加强筋和右中长条加强筋的4部分组成;左边长条加强筋、右边长条加强筋紧挨边梁左右两边的内侧,可起到减弱边梁与底板连接处的应力集中的作用;而左中长条加强筋和右中长条加强筋则可起到减小底板中部变形的作用。
35.本发明的散热铝板,是用来隔离电池包和提高电池托盘的支撑强度,同时在内部填充相变材料或冷却液用来吸收电池释放的热量,而采用中空结构和内部填充相变材料或冷却液的结构设计则能够同时提高散热性能和促进轻量化。
附图说明
36.为了更清楚地说明本发明实施例中的技术方案,下面将对实施例描述中所需要使用的附图作简单地介绍,显而易见地,下面描述中的附图仅仅是本发明的一些实施例,对于本领域普通技术人员来讲,在不付出创造性劳动的前提下,还可以根据这些附图获得其他的附图。
37.图1为本发明新能源汽车用电池托盘的俯视图;
38.图2为本发明新能源汽车用电池托盘的侧视图;
39.图3为本发明实施例1的高强铝铈合金铸件的组织结构图,其中:a为光镜组织结构图,b为电镜组织结构图;
40.图4为本发明所制备的新能源汽车用电池托盘分别在静止状态、颠簸状态、急转弯、急刹车下不同区域变形量的有限元模拟结果示意图;
41.图5为本发明所制备的新能源汽车用电池托盘分别在静止状态、颠簸状态、急转弯、急刹车下不同区域效应力云图;
42.附图标记说明如下:
43.1-底板;2-边梁;3-散热铝板;41-左边长条加强筋;42-左中长条加强筋;43-右中长条加强筋;44-右边长条加强筋;5-吊耳。
具体实施方式
44.为使本发明要解决的技术问题、技术方案和优点更加清楚,下面将结合附图及具体实施例进行详细描述。
45.如图1和2所示,一种新能源汽车用电池托盘,所述新能源汽车用电池托盘包括底板1,所述底板1上设置有边梁2,所述边梁2内设置有散热铝板3、加强筋(由左边长条加强筋
41、左中长条加强筋42、右中长条加强筋43、右边长条加强筋44组成),所述边梁2长度方向的两侧设置有若干吊耳5;所述加强筋(由左边长条加强筋41、左中长条加强筋42、右中长条加强筋43、右边长条加强筋44组成)设置在所述边梁2的内部。
46.其中,所述边梁2的结构为长方形和等腰梯形组合而成,所述长方形包括与所述梯形相连接的左侧边、右侧边、以及底边,所述等腰梯形包括与所述矩形相连接的左腰、右腰和顶边。
47.其中,所述左侧边、右侧边的内壁分别被左边长条加强筋41和右边长条加强筋44固定加强,所述两侧边之间的中线两侧等距离分别设置有左中长条加强筋42和右中长条加强筋43。
48.其中,在所述左边长条加强筋41和左中长条加强筋42之间通过所述散热铝板3分隔成左若干区域用来放置左电池包组,在所述右边长条加强筋44和右中长条加强筋43之间通过所述散热铝板3分隔成右若干区域用来放置右电池包组。
49.其中,所述边梁是由中空的挤压型材首尾焊接形成。
50.其中,所述吊耳5设置于所述边梁的两侧,所需连接螺钉的数量为20,分布均匀,以确保电池托盘的吊耳5能够在恶劣行驶条件下承载电池托盘稳定。
51.其中,整体所述边梁2和散热铝板3焊接在所述底板1上,所述散热铝板3在左若干区域和右若干区域均匀排布。
52.其中,所述散热铝板3为中空结构,中空结构内填充有相变材料或冷却液。
53.实施例1
54.所述新能源汽车用电池托盘的材料为高强铝铈合金,其化学成分按质量百分比计为:si 4.5wt.%、cu 4.7wt.%、mg 0.5wt.%、fe 0.3wt.%、mn 0.5wt.%、ti 0.12wt.%、zr 0.01wt.%、v 0.18wt.%、ce 0.06wt.%,其余为al和不可避免的杂质。
55.所述的新能源汽车用电池托盘的制备方法,所述制备方法包括如下步骤:
56.s1、原料选择:按所述高强铝铈合金成分进行配比,原料为纯铝和其他原料的中间铝合金;其中,mg元素需考虑12%的烧损进行铝镁中间合金的选择,fe元素需考虑杂质的存在;
57.s2、预处理:将原材料在200℃下预热20min;
58.s3、熔炼:将步骤s2预处理后的原料,纯铝和铝硅、铝铜、铝锰、铝铁中间合金,按顺序依次加入炉内,炉内温度加热到760℃,保温30min,得到熔体;
59.s4、铝液处理:将步骤s3的熔体充分搅拌后,加入用量为熔体质量的0.8wt.%的除渣剂和精炼剂,精炼13min后扒去浮渣,之后静置25min;
60.s5、中间合金加入:向步骤s4中扒去浮渣的熔体中加入铝铈、铝镁和铝钛硼中间合金,充分进行搅拌;
61.s6、铸件:直至步骤s5中加入的中间合金都完全熔化后,再保温24min,之后进行浇注,待冷却后取出高强铝铈合金铸件;
62.s7、将高强铝铈合金铸件加工得到新能源汽车用电池托盘的底板、边梁、散热铝板、加强筋和吊耳,从而经过装配得到新能源汽车用电池托盘。
63.其中,如图3所示,步骤s6所制备的高强铝铈合金铸件的二次枝晶臂间距平均为19.5
±
3.3μm,合金中含有较多的强化相。
64.其中,步骤s6所制备的高强铝铈合金铸件屈服强度可达186mpa,抗拉强度可达257mpa,延伸率可达3.8%,硬度可达104.2hv。
65.实施例2
66.所述新能源汽车用电池托盘的材料为高强铝铈合金,其化学成分按质量百分比计为:si 5.6wt.%、cu 3.9wt.%、mg 0.35wt.%、fe 0.50wt.%、mn 0.45wt.%、ti 0.08wt.%、zr 0.02wt.%、v 0.16wt.%、ce 0.10wt.%,其余为al和不可避免的杂质。
67.所述的新能源汽车用电池托盘的制备方法,所述制备方法包括如下步骤:
68.s1、原料选择:按所述高强铝铈合金成分进行配比,原料为纯铝和其他原料的中间铝合金;其中,mg元素需考虑19%的烧损进行铝镁中间合金的选择,fe元素需考虑杂质的存在;
69.s2、预处理:将原材料在207℃下预热22min;
70.s3、熔炼:将步骤s2预处理后的原料,纯铝和铝硅、铝铜、铝锰、铝铁中间合金,按顺序依次加入炉内,炉内温度加热到770℃,保温23min,得到熔体;
71.s4、铝液处理:将步骤s3的熔体充分搅拌后,加入用量为熔体质量的0.7wt.%的除渣剂和精炼剂,精炼14min后扒去浮渣,之后静置26min;
72.s5、中间合金加入:向步骤s4中扒去浮渣的熔体中加入铝铈、铝镁和铝钛硼中间合金,充分进行搅拌;
73.s6、铸件:直至步骤s5中加入的中间合金都完全熔化后,再保温27min,之后进行浇注,待冷却后取出高强铝铈合金铸件;
74.s7、将高强铝铈合金铸件加工得到新能源汽车用电池托盘的底板、边梁、散热铝板、加强筋和吊耳,从而经过装配得到新能源汽车用电池托盘。
75.其中,步骤s6所制备的高强铝铈合金铸件的二次枝晶臂间距平均为19.9
±
2.8μm,合金中含有较多的强化相。
76.其中,步骤s6所制备的高强铝铈合金铸件屈服强度可达181mpa,抗拉强度可达251mpa,延伸率可达3.5%,硬度可达113.1hv。
77.实施例3
78.所述新能源汽车用电池托盘的材料为高强铝铈合金,其化学成分按质量百分比计为:si 6.3wt.%、cu 4.3wt.%、mg 0.42wt.%、fe 0.48wt.%、mn 0.46wt.%、ti 0.12wt.%、zr 0.05wt.%、v 0.18wt.%、ce 0.12wt.%,其余为al和不可避免的杂质。
79.所述的新能源汽车用电池托盘的制备方法,所述制备方法包括如下步骤:
80.s1、原料选择:按所述高强铝铈合金成分进行配比,原料为纯铝和其他原料的中间铝合金;其中,mg元素需考虑16%的烧损进行铝镁中间合金的选择,fe元素需考虑杂质的存在;
81.s2、预处理:将原材料在225℃下预热25min;
82.s3、熔炼:将步骤s2预处理后的原料,纯铝和铝硅、铝铜、铝锰、铝铁中间合金,按顺序依次加入炉内,炉内温度加热到740℃,保温26min,得到熔体;
83.s4、铝液处理:将步骤s3的熔体充分搅拌后,加入用量为熔体质量的0.5-1.0wt.%的除渣剂和精炼剂,精炼17min后扒去浮渣,之后静置23min;
84.s5、中间合金加入:向步骤s4中扒去浮渣的熔体中加入铝铈、铝镁和铝钛硼中间合
金,充分进行搅拌;
85.s6、铸件:直至步骤s5中加入的中间合金都完全熔化后,再保温28min,之后进行浇注,待冷却后取出高强铝铈合金铸件;
86.s7、将高强铝铈合金铸件加工得到新能源汽车用电池托盘的底板、边梁、散热铝板、加强筋和吊耳,从而经过装配得到新能源汽车用电池托盘。
87.其中,步骤s6所制备的高强铝铈合金铸件的二次枝晶臂间距平均为17.8
±
3.2μm,合金中含有较多的强化相。
88.其中,步骤s6所制备的高强铝铈合金铸件屈服强度可达193mpa,抗拉强度可达263mpa,延伸率可达3.7%,硬度可达99.5hv。
89.实施例4
90.所述新能源汽车用电池托盘的材料为高强铝铈合金,其化学成分按质量百分比计为:si 7.12wt.%、cu 3.33wt.%、mg 0.18wt.%、fe 0.47wt.%、mn 0.37wt.%、ti 0.08wt.%、zr 0.03wt.%、v 0.09wt.%、ce 0.08wt.%,其余为al和不可避免的杂质。
91.所述的新能源汽车用电池托盘的制备方法,所述制备方法包括如下步骤:
92.s1、原料选择:按所述高强铝铈合金成分进行配比,原料为纯铝和其他原料的中间铝合金;其中,mg元素需考虑10%的烧损进行铝镁中间合金的选择,fe元素需考虑杂质的存在;
93.s2、预处理:将原材料在200℃下预热30min;
94.s3、熔炼:将步骤s2预处理后的原料,纯铝和铝硅、铝铜、铝锰、铝铁中间合金,按顺序依次加入炉内,炉内温度加热到780℃,保温20min,得到熔体;
95.s4、铝液处理:将步骤s3的熔体充分搅拌后,加入用量为熔体质量的0.5wt.%的除渣剂和精炼剂,精炼10min后扒去浮渣,之后静置20min;
96.s5、中间合金加入:向步骤s4中扒去浮渣的熔体中加入铝铈、铝镁和铝钛硼中间合金,充分进行搅拌;
97.s6、铸件:直至步骤s5中加入的中间合金都完全熔化后,再保温23min,之后730℃进行浇注,待冷却后取出高强铝铈合金铸件;
98.s7、将高强铝铈合金铸件加工得到新能源汽车用电池托盘的底板、边梁、散热铝板、加强筋和吊耳,从而经过装配得到新能源汽车用电池托盘。
99.其中,步骤s6所制备的高强铝铈合金铸件的二次枝晶臂间距平均为20.6
±
4.9μm,合金中含有较多的强化相。
100.其中,步骤s6所制备的高强铝铈合金铸件屈服强度可达177mpa,抗拉强度可达255mpa,延伸率可达3.5%,硬度可达99.8hv。
101.实施例5
102.所述新能源汽车用电池托盘的材料为高强铝铈合金,其化学成分按质量百分比计为:si 7.10wt.%、cu 3.27wt.%、mg 0.21wt.%、fe 0.43wt.%、mn 0.37wt.%、ti 0.09wt.%、zr 0.03wt.%、v 0.12wt.%、ce 0.08wt.%,其余为al和不可避免的杂质。
103.所述的新能源汽车用电池托盘的制备方法,所述制备方法包括如下步骤:
104.s1、原料选择:按所述高强铝铈合金成分进行配比,原料为纯铝和其他原料的中间铝合金;其中,mg元素需考虑15%的烧损进行铝镁中间合金的选择,fe元素需考虑杂质的存
在;
105.s2、预处理:将原材料在210℃下预热28min;
106.s3、熔炼:将步骤s2预处理后的原料,纯铝和铝硅、铝铜、铝锰、铝铁中间合金,按顺序依次加入炉内,炉内温度加热到730℃,保温25min,得到熔体;
107.s4、铝液处理:将步骤s3的熔体充分搅拌后,加入用量为熔体质量的1.0wt.%的除渣剂和精炼剂,精炼16min后扒去浮渣,之后静置28min;
108.s5、中间合金加入:向步骤s4中扒去浮渣的熔体中加入铝铈、铝镁和铝钛硼中间合金,充分进行搅拌;
109.s6、铸件:直至步骤s5中加入的中间合金都完全熔化后,再保温22min,之后730℃进行浇注,待冷却后取出高强铝铈合金铸件;
110.s7、将高强铝铈合金铸件加工得到新能源汽车用电池托盘的底板、边梁、散热铝板、加强筋和吊耳,从而经过装配得到新能源汽车用电池托盘。
111.其中,步骤s6所制备的高强铝铈合金铸件的二次枝晶臂间距平均为18.7
±
4.6μm,合金中含有较多的强化相。
112.其中,步骤s6所制备的高强铝铈合金铸件屈服强度可达170mpa,抗拉强度可达260mpa,延伸率可达4.3%,硬度可达103.7hv。
113.实施例6
114.所述新能源汽车用电池托盘的材料为高强铝铈合金,其化学成分按质量百分比计为:si 7.20wt.%、cu 3.27wt.%、mg 0.19wt.%、fe 0.46wt.%、mn 0.24wt.%、ti 0.11wt.%、zr 0.04wt.%、v 0.12wt.%、ce 0.08wt.%,其余为al和不可避免的杂质。
115.所述的新能源汽车用电池托盘的制备方法,所述制备方法包括如下步骤:
116.s1、原料选择:按所述高强铝铈合金成分进行配比,原料为纯铝和其他原料的中间铝合金;其中,mg元素需考虑10%-20%的烧损进行铝镁中间合金的选择,fe元素需考虑杂质的存在;
117.s2、预处理:将原材料在230℃下预热25min;
118.s3、熔炼:将步骤s2预处理后的原料,纯铝和铝硅、铝铜、铝锰、铝铁中间合金,按顺序依次加入炉内,炉内温度加热到750℃,保温26min,得到熔体;
119.s4、铝液处理:将步骤s3的熔体充分搅拌后,加入用量为熔体质量的0.5-1.0wt.%的除渣剂和精炼剂,精炼17min后扒去浮渣,之后静置22min;
120.s5、中间合金加入:向步骤s4中扒去浮渣的熔体中加入铝铈、铝镁和铝钛硼中间合金,充分进行搅拌;
121.s6、铸件:直至步骤s5中加入的中间合金都完全熔化后,再保温24min,之后进行浇注,待冷却后取出高强铝铈合金铸件;
122.s7、将高强铝铈合金铸件加工得到新能源汽车用电池托盘的底板、边梁、散热铝板、加强筋和吊耳,从而经过装配得到新能源汽车用电池托盘。
123.其中,步骤s6所制备的高强铝铈合金铸件的二次枝晶臂间距平均为19.3
±
3.8μm,合金中含有较多的强化相。
124.其中,步骤s6所制备的高强铝铈合金铸件屈服强度可达171mpa,抗拉强度可达262mpa,延伸率可达3.2%,硬度可达100.9hv。
125.通过对实施例1-6所装配得到新能源汽车用电池托盘的有限元模拟,发现新能源汽车用电池托盘的材料和结构能够满足新能源汽车电池托盘所需的性能要求。结合附图4-5的模拟结果可知,本发明所制备的电池托盘,在多种行驶条件下底板最大变形不超过0.7mm,等效应力小于40mpa。
126.上述方案中,本发明采用边梁和加强筋、散热铝板构成电池托盘的支撑结构,用来承受电池模块的重量,降低了底板结构的强度要求和厚度。
127.本发明的若干吊耳的结构设计能够避免吊耳在长时间的汽车颠簸或遭遇剧烈碰撞时传统电池托盘焊缝处失效断裂的问题。且吊耳是设置于边框两侧,能够起到承载整个电池系统的作用。为保证在复杂行驶条件下电池托盘仍能承载稳定,故而吊耳采用实体结构。
128.本发明的电池托盘包括底板、设置在底板四周的边梁和散热铝板,三者共同分割成容纳电池包的空间;底板和加强筋、散热板共同承受电池模块的重量,底板采用实体结构减小电池托盘的结构变形;边梁采用中空结构以满足轻量化要求。
129.本发明的加强筋由左边长条加强筋、右边长条加强筋和左中长条加强筋和右中长条加强筋的4部分组成;左边长条加强筋、右边长条加强筋紧挨边梁左右两边的内侧,可起到减弱边梁与底板连接处的应力集中的作用;而左中长条加强筋和右中长条加强筋则可起到减小底板中部变形的作用。
130.本发明的散热铝板,是用来隔离电池包和提高电池托盘的支撑强度,同时在内部填充相变材料或冷却液用来吸收电池释放的热量,而采用中空结构和内部填充相变材料或冷却液的结构设计则能够同时提高散热性能和促进轻量化。
131.以上所述是本发明的优选实施方式,应当指出,对于本技术领域的普通技术人员来说,在不脱离本发明所述原理的前提下,还可以做出若干改进和润饰,这些改进和润饰也应视为本发明的保护范围。