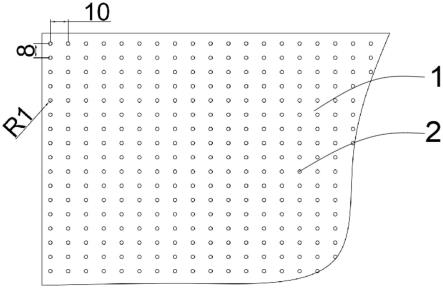
1.本实用新型涉及一种光伏组件用封装胶膜,尤其是涉及一种带特定规律网状结构的、薄型封装胶膜。
背景技术:2.组件在封装过程,分为抽真空及层压两个过程。在层压过程中,胶膜流动与电池、玻璃等组件部件形成良好的粘接。对于白膜胶膜,需要较低的流动性,来降低溢白不良,通常是通过预先交联处理,来降低溢白比例。预交联越高,溢白比例越低,但预交联超过一定程度,电池片隐裂比例会增加,同时胶膜与电池、玻璃的粘接强度也会降低。
3.此外,对于新一代的异质结电池,未来的技术方向是进一步降低银耗,其中一个重要途径,是在银耗降低至100mg/片时,搭配smartwire技术使用,该技术需要将栅线预先与特定的热塑性膜定位、固定,然后通过高温焊接设备形成良好的电接触。但是该方法使用的设备成本高昂,使用的热塑性膜成本也较高。
技术实现要素:4.为了解决上述问题,本实用新型的目的在于提供一种光伏组件用封装胶膜,具有低流动性,与常规胶膜配合使用,提高与电池片或玻璃粘接的可靠性,进一步保证光伏组件的稳定性。
5.本释实用新型采用的技术方案是:一种光伏组件用封装胶膜,所述封装胶膜具有多孔网状结构。
6.通过上述方案,通过将胶膜开孔,将胶膜的流动性可以降至很低,解决溢白的问题。搭配多孔网状结构的胶膜与常规胶膜配合使用使用,通过正常层压的方式即可实现焊带与电池良好的电接触。常规胶膜通过多孔网状结构的胶膜上的通孔渗透至电池表面形成良好的粘接,即可一步成型,制备方法简单,不需要高温焊接步骤,可以极大的降低异质结组件的成本。
7.作为本实用新型的优选方案,所述封装胶膜开设有阵列式通孔。
8.通过将常规胶膜与低流动的开孔胶膜配合使用,层压过程中,常规胶膜通过开孔位置渗透至电池片表面,与电池片形成较好的粘接,而常规胶膜与玻璃也具有较好的粘接,从而保证组件的可靠性,提高组件的使用寿命。
9.作为本实用新型的优选方案,所述通孔为菱形孔,圆形孔,椭圆形孔,方形孔或三角形孔中的一种。
10.通过上述方案,将通孔设计为有规律的阵列式通孔,且通孔的形状为规则形状,可以根据使用需要选择针对性开孔,开模模具易制造,操作简便,提升常规规胶膜通过开孔位置渗透至电池片表面均匀性和粘接力。
11.作为本实用新型的优选方案,所述的通孔(2)的面积占封装胶膜(1)的表面积3%~30%,所述的通孔的面积不小于3.14mm2。
12.通过上述方案,限定通孔的面积大小不小于3.14mm2,确保常规胶顺利的从通孔位置渗透至电池片表面。
13.作为本实用新型的优选方案,所述的通孔的面积占封装胶膜的表面积3%~30%。
14.通过上述方案,限定通孔所占面积,用以在保证传质效果的前提下,节约成本。
15.作为本实用新型的优选方案,相邻通孔的中心点最小间距不小于2mm。
16.通过上述方案,限定相邻通孔的中心点最小间距,避免相邻通孔的常规胶渗入时相互干扰,提高渗透均匀性,并保证网状结构胶膜的强度。
17.作为本实用新型的优选方案,所述的胶膜厚度为50~400微米。
18.通过上述方案,层压过程中该胶膜的渗透深度常规胶能够顺利通过,同时该胶膜的厚度确保常规胶膜、该胶膜以及电池片或者玻璃三者层压后粘接牢固不分离。
19.与现有技术相比,本实用新型的有益效果为:
20.通过将胶膜开孔,将胶膜的流动性可以降至很低,解决溢白的问题。通过将常规胶膜与低流动的开孔胶膜配合使用,层压过程中,常规胶膜通过开孔位置渗透至电池片表面,与电池片形成较好的粘接,而常规胶膜与玻璃也具有较好的粘接,从而保证组件的可靠性。
21.将低温焊带通过点胶的形式固定在电池表面,搭配多孔网状结构的胶膜与常规胶膜配合使用,只要通过正常层压的方式即可实现焊带与电池良好的电接触。常规胶膜通过多孔网状结构的胶膜上的通孔渗透至电池表面形成良好的粘接,即可一步成型,制备方法简单,不需要高温焊接步骤,可以极大的降低异质结组件的成本。
附图说明
22.图1为实施例一中网状结构封装胶膜的结构示意图;
23.图2为实施例二中网状结构封装胶膜结构示意图;
24.图3实施例三中网状结构封装胶膜结构示意图;
25.图4为实施例四中网状结构封装胶膜的结构示意图;
26.图5实施例五组件的结构示意图。
27.图中附图标记为:
28.1,封装胶膜;2、通孔;3、玻璃;4、常规封装胶膜;5、网状结构封装胶膜;6、电池;7、背板。
具体实施方式
29.如图1-4所示,一种光伏组件用封装胶膜,所述封装胶膜具有多孔网状结构。
30.一种光伏组件用封装胶膜,所述封装胶膜1具有多孔网状结构。通过将胶膜开孔,将胶膜的流动性可以降至很低,解决溢白的问题。搭配多孔网状结构的胶膜与常规胶膜配合使用使用,通过正常层压的方式即可实现焊带与电池良好的电接触。常规胶膜通过多孔网状结构的胶膜上的通孔渗透至电池表面形成良好的粘接,即可一步成型,制备方法简单,不需要高温焊接步骤,可以极大的降低异质结组件的成本。
31.进一步地,所述封装胶膜1开设有阵列式通孔2。通过将常规胶膜与低流动的开孔胶膜配合使用,层压过程中,常规胶膜通过开孔位置渗透至电池片表面,与电池片形成较好的粘接,而常规胶膜与玻璃也具有较好的粘接,从而保证组件的可靠性,提高组件的使用寿
命。
32.进一步地,所述通孔2为菱形孔,圆形孔,椭圆形孔,方形孔或三角形孔中的一种。将通孔2设计为有规律的阵列式通孔2,且通孔2的形状为规则形状,可以根据使用需要选择针对性开孔,开模模具易制造,操作简便,提升常规规胶膜通过开孔位置渗透至电池片表面均匀性和粘接力。
33.进一步地,作为本实用新型的优选方案,所述的通孔2的面积不小于3.14mm2,限定通孔2的面积大小不小于3.14mm2,确保常规胶顺利的从通孔2位置渗透至电池片表面。
34.进一步地,所述的通孔2的面积占封装胶膜1的表面积3%~30%,用以在保证传质效果的前提下,节约成本。
35.进一步地,相邻通孔2的中心点最小间距不小于2mm。限定相邻通孔2的中心点最小间距,避免相邻通孔2的常规胶渗入时相互干扰,提高渗透均匀性,并保证网状结构胶膜的强度。
36.为了能够更清楚地理解本发明的技术内容,特举以下实施例详细说明。
37.实施例1:
38.本实施例结构如图1,胶膜厚度50微米,其开设阵列式的通孔为圆形孔,通孔面积为3.14mm2,横向相邻的阵列式通孔中心点间距为10mm,纵向相邻的阵列式通孔中心点间距为8mm。
39.实施例2:
40.本实施例结构如图2,胶膜厚度为400微米,其开设阵列式的通孔为椭圆形孔,通孔面积为6.28mm2,相邻的阵列式通孔中心点间距8mm。
41.实施例3:
42.本实施例结构如图3,胶膜厚度为100微米,其开设阵列式的通孔为菱形孔,通孔面积为24mm2,相邻的阵列式通孔中心点间距10mm。
43.实施例4:
44.本实施例结构如图4,胶膜厚度为200微米,其开设阵列式的通孔为方形孔,通孔面积为36mm2,相邻的阵列式通孔中心点间距为16mm。
45.实施例5:
46.本实施例为组件如图5,从上到下依次为玻璃3,常规封装胶膜4,网状结构封装胶膜5,电池6,网状结构封装胶膜5,常规封装胶膜4和背板7,其中,网状结构封装胶膜5的结构如实施例3所示,常规封装胶膜4为普通市面一般的封装胶膜,背板7可以为普通背板或者玻璃。
47.以上所述仅为本发明的较佳实施例,并非用以限定本发明的实质技术内容范围,本发明的实质技术内容是广义地定义于申请的权利要求范围中,任何他人完成的技术实体或方法,若是与本技术的权利要求范围所定义的完全相同,也或是一种等效的变更,均将被视同本发明保护范围。