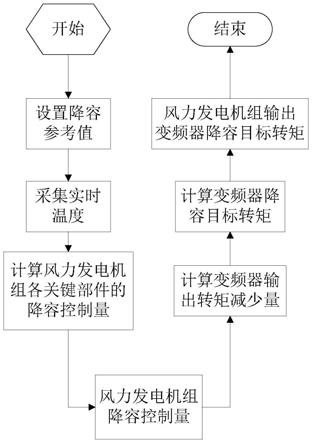
1.本发明涉及风力发电技术领域,具体涉及一种双馈型风力发电机组降容控制策略算法。
背景技术:2.风电行业在近些年得到长足发展,在能源供给方面的角色越来越显著。风电制造企业和研究单位都在不断的通过技术革新提高风能利用率。由于风电机组工作环境复杂多样,风电机组内的机械传动系统以及电气元器件很容易受到环境因素影响,如温度的变化以及外界风速的变化,都会使得各类系统零部件处于临界范围内运行进而出现故障,通常双馈风力发电机组的故障大多数发生在齿轮箱、叶片、发电机和电气系统等设备部件上,这些部件的成本占风电机组费用的80%以上;而其中齿轮箱、发电机发生的故障最为严重,此类故障发生后会造成风电机组长时间的停机,停机后的维修时间、维修成本也较高,而且会造成更大程度的电量损失,影响发电量。
3.通常,为了避免机组状态进一步恶化导致各类故障的发生,都需要制定具有针对性的控制算法来对风力发电机组进行控制。目前风力发电机组的控制算法都仅仅只以环境温度为参考值,即当环境温度超出该风力发电机组的环境温度阈值范围时,对照事先设定的高温降容/低温升容控制表对风力发电机组的输出功率进行降/升容控制,未针对风力发电机组其他重要部件的物理量的变化对风力发电机组的输出功率进行功率输出控制,无法避免风力发电机组的其他重要部件因为风力发电机组的输出功率过大而导致的故障发生。
技术实现要素:4.本发明的目的是针对现有技术对应的不足,提供一种双馈型风力发电机组降容控制策略算法,使风力发电机组的所有关键部件均可以保证在正常温度范围内运行,不会因为自身高温而产生故障,保证了风力发电机组的正常运行,避免风力发电机组因为风力发电机组的输出功率过大或者环境温度引起风力发电机组的重要部件或者关键部位温度过高导致故障发生,造成重大安全事故。
5.本发明的目的是采用下述方案实现的:一种双馈型风力发电机组降容控制策略算法,包括以下步骤:
6.1)设置变频器降容参考值、发电机轴承降容参考值、发电机绕组降容参考值、齿轮箱轴承降容参考值、齿轮箱油温降容参考值、风速降容参考值;
7.2)采集变频器实时温度、发电机轴承实时温度、发电机绕组实时温度、齿轮箱轴承实时温度、齿轮箱实时油温、实时风速;
8.3)当变频器实时温度≥变频器降容参考值时,计算变频器降容控制量;
9.4)当发电机轴承实时温度≥发电机轴承降容参考值时,计算发电机轴承降容控制量;
10.5)当发电机绕组实时温度≥发电机绕组降容参考值时,计算发电机绕组降容控制
量;
11.6)当齿轮箱轴承实时温度≥齿轮箱轴承降容参考值时,计算齿轮箱轴承降容控制量;
12.7)当齿轮箱实时油温≥齿轮箱油温降容参考值时,计算齿轮箱油温降容控制量;
13.8)当实时风速≥风速降容参考值时,计算风速降容控制量;
14.9)设变频器降容控制量、发电机轴承降容控制量、发电机绕组降容控制量、齿轮箱轴承降容控制量、齿轮箱轴承降容控制量、齿轮箱油温降容控制量、风速降容控制量之中的最大值为风力发电机组降容控制量;
15.10)通过下列公式计算出变频器输出转矩减少量:
[0016][0017]
式中,torque为变频器输出转矩减少量,p为风力发电机组降容控制量,speed为发电机转速,π为圆周率;
[0018]
11)按照下列公式计算变频器降容目标转矩:
[0019]
变频器降容目标转矩=变频器实时转矩-变频器输出转矩减少量;
[0020]
12)风力发电机组按照变频器降容目标转矩进行运行。
[0021]
优选地,若变频器降容控制量/发电机轴承降容控制量/发电机绕组降容控制量/齿轮箱轴承降容控制量/齿轮箱油温降容控制量/风速降容控制量为风力发电机组降容控制量,按照下列公式计算风力发电机组降容控制量:
[0022]
p=k
·
pn·
(q
实-q
参
)
[0023]
式中,p为风力发电机组降容控制量,k为风力发电机组降容系数,pn为风力发电机组额定功率,q
实
为变频器实时温度/发电机轴承实时温度/发电机绕组实时温度/齿轮箱轴承实时温度/齿轮箱实时油温/实时风速,q
参
为变频器降容参考值/发电机轴承降容参考值/发电机绕组降容参考值/齿轮箱轴承降容参考值/齿轮箱油温降容参考值/风速降容参考值。
[0024]
优选地,所述变频器实时温度为变频器igbt模块多个测试点的最大温度值。
[0025]
优选地,所述发电机轴承实时温度为发电机前轴承实时温度、发电机后轴承实时温度中的最大值。
[0026]
优选地,所述发电机绕组实时温度为发电机六组绕组的最大实时温度。
[0027]
优选地,所述齿轮箱轴承实时温度为齿轮箱前轴承实时温度、齿轮箱后轴承实时温度中的最大值。
[0028]
优选地,所述齿轮箱实时油温为齿轮箱进口实时油温、齿轮箱出口实时油温的最大值。
[0029]
优选地,根据风力发电机组的硬件性能设置风力发电机组停机阈值,若实时风速≥风力发电机组停机阈值,则风力发电机组停机。
[0030]
本发明的优点在于,风力发电机组的所有关键部件均可以保证在正常温度范围内运行,不会因为自身高温而产生故障,一旦温度过高,风力发电机组自动减小输出转矩以达到降低部件自身温度的目的。
附图说明
[0031]
图1为本发明的流程图。
具体实施方式
[0032]
如图1所示,一种双馈型风力发电机组降容控制策略算法,包括以下步骤:
[0033]
1)设置变频器降容参考值、发电机轴承降容参考值、发电机绕组降容参考值、齿轮箱轴承降容参考值、齿轮箱油温降容参考值、风速降容参考值;
[0034]
本实施例中,上述各风力发电机组关键部位的降容参考值均为在风力发电机组标定试验中得到的标定值,或者经验值。
[0035]
2)采集变频器实时温度、发电机轴承实时温度、发电机绕组实时温度、齿轮箱轴承实时温度、齿轮箱实时油温、实时风速;
[0036]
3)当变频器实时温度≥变频器降容参考值时,计算变频器降容控制量;
[0037]
所述变频器实时温度为变频器igbt模块多个测试点的最大温度值。
[0038]
位于变频器内的机侧igbt模块为整流模块,通过该整流模块将发电机的不规律电流通过整流模块整流为的直流电,所以
[0039]
位于变频器内的网侧igbt模块为逆变模块,通过该逆变模块对直流进行逆变,使之成为可控的交流电;
[0040]
本实施例的双馈型风力发电机组中,整流模块/逆变模块均分布设置有3个ntc温度传感器,所述ntc温度传感器均每秒采集一次实时温度,取其最大值作为变频器实时温度,以保证对实时温度的准确判断。
[0041]
4)当发电机轴承实时温度≥发电机轴承降容参考值时,计算发电机轴承降容控制量;
[0042]
所述发电机轴承实时温度为发电机前轴承实时温度、发电机后轴承实时温度中的最大值,以保证对实时温度的准确判断。
[0043]
本实施例中,采用2个pt100温度传感器每秒分别对应采集发电机前轴承实时温度、发电机后轴承实时温度。
[0044]
5)当发电机绕组实时温度≥发电机绕组降容参考值时,计算发电机绕组降容控制量;
[0045]
所述发电机绕组实时温度为发电机六组绕组的最大实时温度。
[0046]
本实施例中,采用6个pt100温度传感器每秒采集一次发电机绕组实时温度,6个pt100温度传感器分别对应采集发电机机侧u相绕组u1、发电机网侧u相绕组u2、发电机机侧v相绕组v1、发电机网侧v相绕组v2、发电机机侧w相绕组w1、发电机网侧w相绕组w2上的实时温度,取其中最大的实时温度作为发电机绕组实时温度。
[0047]
6)当齿轮箱轴承实时温度≥齿轮箱轴承降容参考值时,计算齿轮箱轴承降容控制量;
[0048]
所述齿轮箱轴承实时温度为齿轮箱前轴承实时温度、齿轮箱后轴承实时温度中的最大值。
[0049]
本实施例中,采用2个pt100温度传感器每秒分别对应采集齿轮箱前轴承实时温度、齿轮箱后轴承实时温度,取其中的最大值作为齿轮箱轴承实时温度。
[0050]
7)当齿轮箱实时油温≥齿轮箱油温降容参考值时,计算齿轮箱油温降容控制量;
[0051]
所述齿轮箱实时油温为齿轮箱进口实时油温、齿轮箱出口实时油温的最大值。
[0052]
本实施例中,采用2个pt100温度传感器每秒分别对应采集齿轮箱进口实时油温、齿轮箱出口实时油温,取其中的最大值作为齿轮箱实时油温。
[0053]
8)当实时风速≥风速降容参考值时,计算风速降容控制量;
[0054]
本实施例中,采用超声波风速风向仪每10毫秒进行一次实时风速的采集,风速降容参考值为24m/s,即一旦风力发电机组检测到60秒内实时风速均大于24m/s,则计算此时的风速降容控制量用于风力发电机组降容。
[0055]
根据风力发电机组的硬件性能设置风力发电机组停机阈值,若实时风速≥风力发电机组停机阈值,则风力发电机组停机,以保护风力发电机组在风力过大时产生故障导致重大安全事故。
[0056]
9)设变频器降容控制量、发电机轴承降容控制量、发电机绕组降容控制量、齿轮箱轴承降容控制量、齿轮箱轴承降容控制量、齿轮箱油温降容控制量、风速降容控制量之中的最大值为风力发电机组降容控制量;
[0057]
10)通过下列公式计算出变频器输出转矩减少量:
[0058][0059]
式中,torque为变频器输出转矩减少量,p为风力发电机组降容控制量,speed为发电机转速,π为圆周率;
[0060]
本实施例中,按照下列公式计算风力发电机组降容控制量:
[0061]
p=k
·
pn·
(q
实-q
参
)
[0062]
式中,p为风力发电机组降容控制量,k为风力发电机组降容系数,pn为风力发电机组额定功率,q
实
为变频器实时温度/发电机轴承实时温度/发电机绕组实时温度/齿轮箱轴承实时温度/齿轮箱实时油温/实时风速,q
参
为变频器降容参考值/发电机轴承降容参考值/发电机绕组降容参考值/齿轮箱轴承降容参考值/齿轮箱油温降容参考值/风速降容参考值。
[0063]ⅰ.若选取变频器降容控制量为风力发电机组降容控制量,风力发电机组降容系数k=0.2;
[0064]ⅱ.若选取发电机轴承降容控制量/发电机绕组降容控制量/齿轮箱轴承降容控制量/齿轮箱油温降容控制量为风力发电机组降容控制量,风力发电机组降容系数k=0.1;
[0065]ⅲ.若选取风速降容控制量为风力发电机组降容控制量,风力发电机组降容系数k=0.0625;
[0066]
k与pn的乘积实际上就是风力发电机组降容率,风力发电机组降容系数k是在风力发电机组标定试验中得到的标定值,或者经验值。
[0067]
11)按照下列公式计算变频器降容目标转矩:
[0068]
变频器降容目标转矩=变频器实时转矩-变频器输出转矩减少量;
[0069]
12)风力发电机组按照变频器降容目标转矩进行运行,所述风力发电机组的所有关键部件均可以保证在正常温度范围内运行,不会因为自身高温而产生故障,一旦温度过高,风力发电机组自动减小输出转矩以达到降低部件自身温度的目的。
[0070]
以上所述仅为本发明的优选实施例,并不用于限制本发明,本领域的技术人员在不脱离本发明的精神的前提下,对本发明进行的改动均落入本发明的保护范围。