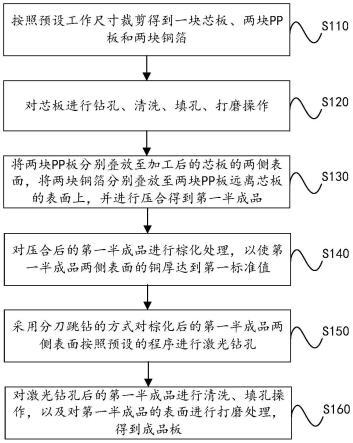
pcb板高速材料及其制作方法
技术领域
1.本技术涉及pcb加工工艺技术领域,特别涉及一种pcb板高速材料及其制作方法。
背景技术:2.目前pcb(印制线路板)产品用到高频高速材料越来越多,其中高速材料也得到较大程度推广,对于现有的pcb板高速材料,尤其涉及含有lopro(low profile copper foil,低轮廓铜箔)材料,通常为多层结构,其由芯板以及多组pp板、铜箔压合而成的,这类铜箔的结晶很细腻(在2微米以下),为等轴晶粒,不含柱状的晶体,且棱线平坦,有此类铜箔的材料都具有铜箔与基材结合力差这一特性,所以此类材料在使用的时候通常会出现一些普通材料所不会出现的问题例如:铜面起泡,这一问题的存在往往会导致产品报废,进而降低生产效率。
技术实现要素:3.本技术旨在至少解决现有技术中存在的技术问题之一。为此,本技术提出一种pcb板高速材料及其制作方法,能够减少pcb板高速材料制作过程中铜箔起泡的现象,从而提高生产效率。
4.第一方面,本技术提供了一种pcb板高速材料的制作方法,包括:
5.按照预设工作尺寸裁剪得到一块芯板、两块pp板和两块铜箔;
6.对所述芯板进行钻孔、清洗、填孔、打磨操作;
7.将两块所述pp板分别叠放至加工后的所述芯板的两侧表面,将两块所述铜箔分别叠放至两块所述pp板远离所述芯板的表面上,并进行压合得到第一半成品;
8.对压合后的所述第一半成品进行棕化处理,以使所述第一半成品两侧表面的铜厚达到第一标准值;
9.采用分刀跳钻的方式对棕化后的所述第一半成品两侧表面按照预设的程序进行激光钻孔;
10.对激光钻孔后的所述第一半成品进行清洗、填孔操作,以及对所述第一半成品的表面进行打磨处理,得到成品板。
11.根据本技术第一方面实施例的pcb板高速材料的制作方法,至少具有如下有益效果:按照预设工作尺寸裁剪得到一块芯板、两块pp板和两块铜箔;对芯板进行钻孔、清洗、填孔、打磨操作;将两块pp板分别叠放至加工后的芯板的两侧表面,将两块铜箔分别叠放至两块pp板远离芯板的表面上,并进行压合得到第一半成品;对压合后的第一半成品进行棕化处理,以使第一半成品两侧表面的铜厚达到第一标准值;采用分刀跳钻的方式对棕化后的第一半成品两侧表面按照预设的程序进行激光钻孔;对激光钻孔后的第一半成品进行清洗、填孔操作,以及对第一半成品的表面进行打磨处理,得到成品板。通过将第一半成品采用激光钻孔的步骤前进行一次棕化处理,使得第一半成品两侧表面的铜厚达到第一标准值,提高铜箔表面的结合力,同时还通过分刀跳钻的方式对第一半成品两侧表面进行激光
钻孔,避免激光镭射时局部产生热量太大导致铜箔与pp板之间分层,从而导致起泡的现象,通过本技术第一方面提供的制作方法能够减少pcb板高速材料制作过程中铜箔起泡的现象,从而提高生产效率。
12.根据本技术第一方面的一些实施例,所述对压合后的所述第一半成品进行棕化处理,以使所述第一半成品两侧表面的铜厚达到第一标准值,包括:获取用于棕化处理的药剂;其中,所述药剂的成分包括硫酸、过氧化氢和键合剂;将所述药剂以预设的线速对压合后的所述第一半成品采用所述药剂进行冲刷,以使所述第一半成品两侧表面的铜厚达到第一标准值。
13.根据本技术第一方面的一些实施例,所述第一标准值为9至11微米。
14.根据本技术第一方面的一些实施例,所述棕化处理的温度在33℃至38℃之间。
15.根据本技术第一方面的一些实施例,所述采用分刀跳钻的方式对棕化后的所述第一半成品两侧表面按照预设的程序进行激光钻孔,包括:根据预设的程序得到所述第一半成品两侧表面上每个孔位的位置信息;按照预设的规则将所述位置信息划分为多个区域;其中,每个区域均设置有多个待加工的孔位;采用激光的方式依次在每个所述区域打一个孔并循环多次,直至所有所述孔位加工完成。
16.根据本技术第一方面的一些实施例,所述对激光钻孔后的所述第一半成品进行清洗、填孔操作,包括:采用等离子清洗的方式对所述第一半成品进行处理;并对所述第一半成品进行沉铜、板电、vcp填孔以及减铜的处理。
17.根据本技术第一方面的一些实施例,所述对所述第一半成品的表面进行打磨处理,包括:对所述第一半成品的表面依次采用陶瓷刷和不织布进行打磨处理;其中,所述陶瓷刷和所述不织布的打磨目数为800目。
18.根据本技术第一方面的一些实施例,所述得到成品板,包括:对处理完成后的所述第一半成品进行多层加工,得到成品板。
19.根据本技术第一方面的一些实施例,还包括:对所述成品板的表面进行图形电镀、碱性蚀刻、aoi检测、感光油墨喷涂;并对所述成品板进行测试检测。
20.第二方面,本技术提供了一种pcb板高速材料,通过如第一方面任一项实施例所述的pcb板高速材料的制作方法得到的。
21.根据本技术第二方面实施例的pcb板高速材料的制作方法,至少具有如下有益效果:果:按照预设工作尺寸裁剪得到一块芯板、两块pp板和两块铜箔;对芯板进行钻孔、清洗、填孔、打磨操作;将两块pp板分别叠放至加工后的芯板的两侧表面,将两块铜箔分别叠放至两块pp板远离芯板的表面上,并进行压合得到第一半成品;对压合后的第一半成品进行棕化处理,以使第一半成品两侧表面的铜厚达到第一标准值;采用分刀跳钻的方式对棕化后的第一半成品两侧表面按照预设的程序进行激光钻孔;对激光钻孔后的第一半成品进行清洗、填孔操作,以及对第一半成品的表面进行打磨处理,得到成品板。通过将第一半成品采用激光钻孔的步骤前进行一次棕化处理,使得第一半成品两侧表面的铜厚达到第一标准值,提高铜箔表面的结合力,同时还通过分刀跳钻的方式对第一半成品两侧表面进行激光钻孔,避免激光镭射时局部产生热量太大导致铜箔与pp板之间分层,从而导致起泡的现象,本技术第二方面提供的制作方法能够减少pcb板高速材料中铜箔起泡的现象,从而提高生产效率。
22.本技术的附加方面和优点将在下面的描述中部分给出,部分将从下面的描述中变得明显,或通过本技术的实践了解到。
附图说明
23.本技术的附加方面和优点结合下面附图对实施例的描述中将变得明显和容易理解,其中:
24.图1为本技术的一个实施例的pcb板高速材料的制作方法的流程图;
25.图2为本技术的另一实施例的pcb板高速材料的制作方法的流程图;
26.图3为本技术的另一实施例的pcb板高速材料的制作方法的流程图;
27.图4为本技术的另一实施例的pcb板高速材料的制作方法的流程图;
28.图5为本技术的另一实施例的pcb板高速材料的制作方法的流程图。
具体实施方式
29.下面详细描述本技术的实施例,所述实施例的示例在附图中示出,其中自始至终相同或类似的标号表示相同或类似的元件或具有相同或类似功能的元件。下面通过参考附图描述的实施例是示例性的,仅用于解释本技术,而不能理解为对本技术的限制。
30.在本技术的描述中,需要理解的是,涉及到方位描述,例如上、下、前、后、左、右等指示的方位或位置关系为基于附图所示的方位或位置关系,仅是为了便于描述本技术和简化描述,而不是指示或暗示所指的装置或元件必须具有特定的方位、以特定的方位构造和操作,因此不能理解为对本技术的限制。
31.在本技术的描述中,如果有描述到第一、第二只是用于区分技术特征为目的,而不能理解为指示或暗示相对重要性或者隐含指明所指示的技术特征的数量或者隐含指明所指示的技术特征的先后关系。
32.本技术的描述中,除非另有明确的限定,设置、安装、连接等词语应做广义理解,所属技术领域技术人员可以结合技术方案的具体内容合理确定上述词语在本技术中的具体含义。
33.第一方面,参照图1,本技术提供了一种pcb板高速材料的制作方法,包括但不限于以下步骤:
34.步骤s110:按照预设工作尺寸裁剪得到一块芯板、两块pp板和两块铜箔;
35.步骤s120:对芯板进行钻孔、清洗、填孔、打磨操作;
36.步骤s130:将两块pp板分别叠放至加工后的芯板的两侧表面,将两块铜箔分别叠放至两块pp板远离芯板的表面上,并进行压合得到第一半成品;
37.步骤s140:对压合后的第一半成品进行棕化处理,以使第一半成品两侧表面的铜厚达到第一标准值;
38.步骤s150:采用分刀跳钻的方式对棕化后的第一半成品两侧表面按照预设的程序进行激光钻孔;
39.步骤s160:对激光钻孔后的第一半成品进行清洗、填孔操作,以及对第一半成品的表面进行打磨处理,得到成品板。
40.需要说明的是,芯板为该pcb板高速材料的骨架部分,其为一种双面覆铜的板子,
pp板为一种主要由聚丙烯组成的板子,铜箔的厚度为0.33oz。
41.示例性的,对所述芯板进行钻孔、清洗、填孔、打磨操作的步骤具体为,将裁剪后的芯板依次进行钻埋孔、等离子清洗、沉铜、板电、干膜、镀孔、树脂塞孔、陶瓷磨板、绘制外层图形、内层aoi(automated optical inspection,自动光学检测)、棕化的操作。
42.根据本技术第一方面实施例的pcb板高速材料的制作方法,至少具有如下有益效果:按照预设工作尺寸裁剪得到一块芯板、两块pp板、两块铜箔;对芯板进行钻孔、清洗、填孔、打磨操作;将两块pp板、两块铜箔分别依次叠放在芯板的两侧,并进行压合得到第一半成品;对第一半成品进行棕化处理,以使第一半成品两侧表面的铜厚达到第一标准值;采用分刀跳钻的方式对第一半成品两侧表面按照预设的程序进行激光钻孔;对第一半成品进行清洗、填孔操作,以及对第一半成品的表面进行打磨处理,得到成品板。通过将第一半成品采用激光钻孔的步骤前进行一次棕化处理,使得第一半成品两侧表面的铜厚达到第一标准值,提高铜箔表面的结合力,同时还通过分刀跳钻的方式对第一半成品两侧表面进行激光钻孔,避免激光镭射时局部产生热量太大导致铜箔与pp板之间分层,从而导致起泡的现象,通过本技术第一方面提供的制作方法能够减少pcb板高速材料制作过程中铜箔起泡的现象,从而提高生产效率。
43.参照图2,可以理解的是,在步骤s140中,可以但不仅限于包括以下步骤:
44.步骤s210:获取用于棕化处理的药剂;其中,药剂的成分包括硫酸、过氧化氢和键合剂;
45.步骤s220:将药剂以预设的线速对压合后的第一半成品采用药剂进行冲刷,以使第一半成品两侧表面的铜厚达到第一标准值。
46.需要说明的是,键合剂的作用是能够将铜箔的表面和pp板的表面粘合起来,通过采用特定的药水对第一半成品进行棕化处理,提高第一半成品表面铜厚,比现有技术中常规的铜厚8
±
1μm略厚,从而提高铜箔与pp板之间的结合力,减少pcb板高速材料制作过程中铜箔起泡的现象,从而提高生产效率。
47.可以理解的是,第一标准值为9至11微米,区别于常规的铜厚8
±
1μm,在激光钻孔的步骤前添加了棕化的步骤,提高铜箔与pp板之间的结合力,从而能够减少pcb板高速材料制作过程中铜箔起泡的现象,从而提高生产效率。
48.可以理解的是,棕化处理的温度在33℃至38℃之间,以进一步提高棕化的效果,减少pcb板高速材料制作过程中铜箔起泡的现象。
49.参照图3,可以理解的是,在步骤s150中,可以包括但不仅限于以下步骤:
50.步骤s310:根据预设的程序得到第一半成品两侧表面上每个孔位的位置信息;
51.步骤s320:按照预设的规则将位置信息划分为多个区域;其中,每个区域均设置有多个待加工的孔位;
52.步骤s330:采用激光的方式依次在每个区域打一个孔并循环多次,直至所有孔位加工完成。
53.对于在孔位密集的区域激光钻孔,由于镭射的过程中孔位的附近会产生大量的热量,长时间在附近的区域进行打孔会导致线路板持续处于高温的状态,容易导致铜箔与pp板之间分离,从而起泡,甚至变形,在本技术的方案中,根据预先设定的程序得到在第一半成品两侧表面需要打孔的每个孔位的位置信息,根据每个孔位的位置信息按照预设的规则
镀孔-树脂塞孔-陶瓷磨板(陶瓷刷+不织布)-外层图形-内层aoi-棕化;
70.对于第一半成品加工(c+d+e+f):开料(铜箔和pp板)-压合(压合使用铜箔为0.33oz铜箔)-镭射前棕化(棕化后铜厚9-11μm)-激光钻孔(分刀跳钻)-等离子清洗-沉铜-板电-vcp填孔-减铜-陶瓷磨板(陶瓷刷+不织布)-外层图形-内层aoi-棕化;
71.对于第二半成品加工(b+c+d+e+f+g):开料(铜箔和pp板)-二次配对-压合(压合使用铜箔为0.33oz铜箔)-镭射前棕化(棕化后铜厚9-11μm)-激光钻孔(分刀跳钻)-等离子清洗-沉铜-板电-vcp填孔-减铜-陶瓷磨板(陶瓷刷+不织布)-外层图形-内层aoi-棕化;
72.形成8层结构的成品板(a+b+c+d+e+f+g+h):开料(铜箔和pp板)-三次配对-压合(压合使用铜箔为0.33oz铜箔)-镭射前棕化(棕化后铜厚9-11μm)-激光钻孔(分刀跳钻)-钻孔-等离子清洗-沉铜-板电-vcp填孔-镀孔前干膜-盲孔填平-树脂塞孔-陶瓷磨板(陶瓷刷+不织布)-钻孔2-等离子清洗2-沉铜2-板电2-外层图形-图形电镀-碱性蚀刻-外层aoi-感光油墨-字符-沉镍金-成型-电测试-目检-fqa-包装-入库。
73.第二方面,本技术还提供了一种pcb板高速材料,通过如第二方面任一项实施例的pcb板高速材料的制作方法得到的。
74.根据本技术第二方面实施例的pcb板高速材料的制作方法,至少具有如下有益效果:按照预设工作尺寸裁剪得到一块芯板、两块pp板、两块铜箔;对芯板进行钻孔、清洗、填孔、打磨操作;将两块pp板、两块铜箔分别依次叠放在芯板的两侧,并进行压合得到第一半成品;对第一半成品进行棕化处理,以使第一半成品两侧表面的铜厚达到第一标准值;采用分刀跳钻的方式对第一半成品两侧表面按照预设的程序进行激光钻孔;对第一半成品进行清洗、填孔操作,以及对第一半成品的表面进行打磨处理,得到成品板。通过将第一半成品采用激光钻孔的步骤前进行一次棕化处理,使得第一半成品两侧表面的铜厚达到第一标准值,提高铜箔表面的结合力,同时还通过分刀跳钻的方式对第一半成品两侧表面进行激光钻孔,避免激光镭射时局部产生热量太大导致铜箔与pp板之间分层,从而导致起泡的现象,本技术第二方面提供的制作方法能够减少pcb板高速材料中铜箔起泡的现象,从而提高生产效率。
75.上面结合附图对本技术实施例作了详细说明,但是本技术不限于上述实施例,在所属技术领域普通技术人员所具备的知识范围内,还可以在不脱离本技术宗旨的前提下,作出各种变化。