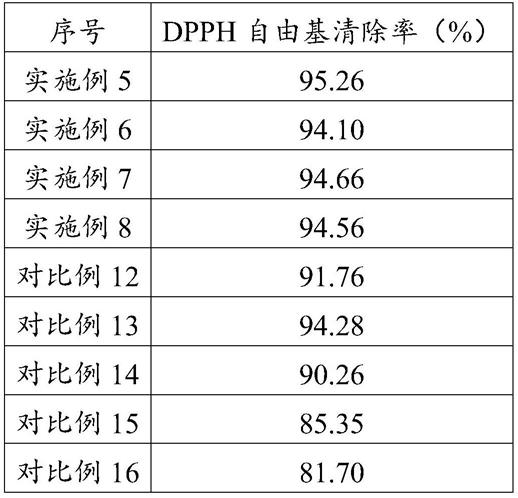
1.本发明属于酵素制备技术领域,具体涉及一种油莎豆粕与沙棘渣混合酵素、制备方法及其应用。
背景技术:2.我国工业和信息化部发布的轻工行业标准《酵素产品分类导则》将酵素定义为,以动物、植物、菌类等为原料,添加或不添加辅料,经微生物发酵制得的含有特定生物活性成分的产品。其生物活性成分包含来自植物原料和微生物所提供的各种营养素和天然植物中的植物类功能性化学成分,以及发酵生成的一些生理活性物质,包括氨基酸、肽类、维生素、多糖、多酚类、黄酮类、醇类、酯类、酶类、矿物元素、有机酸和各种益生菌。
3.油莎豆粕和沙棘渣都是原料加工后的废弃物,油莎豆粕含有丰富的淀粉和蛋白质;沙棘果渣中含有丰富的黄酮、维生素b1、维生素b2、维生素c、维生素e、氨基酸、粗蛋白、粗脂肪、粗纤维、鞣质、糖、三帖及甾体类等活性成分。然而目前油莎豆粕通常被用于酿酒及动物饲料;沙棘渣也常被用于动物饲料,未见二者更多地其他应用方式,进而使油莎豆粕和沙棘渣不能得到充分的利用,造成资源浪费,尤其是以油莎豆粕和沙棘渣为原料的酵素发酵,更是未有相关报道。
4.酵素发酵分为自有菌种发酵和外源添加菌种发酵。自有菌种发酵是利用原料表面附着的酵母菌、乳酸菌、米曲霉等微生物进行发酵。自然发酵的周期较长,自然存在的微生物种类、数量不可控,因此产品的质量参差不齐,难以实现工厂化生产。外源添加菌种发酵虽然能够一定程度地克服自然发酵所存在的微生物种类和数量问题,但是酵素是一种经发酵后微生物代谢的产物,所以酵素食品中含有大量的菌种,这些菌种一般为益生菌,能调节肠道菌群,促进肠道菌群的平衡,所以,正确的发酵工艺和菌种的选择是保证酵素的功能价值的重要因素之一。
5.目前,优质的酵素原材料多为新鲜水果,如:桑葚、猕猴桃、蓝莓、柠檬和百香果等,选择较为单一。因而丰富酵素原材料,研发对应原料的发酵工艺,促进更多类型的酵素产业化仍为本领域努力的方向。
技术实现要素:6.本发明的目的在于提供一种油莎豆粕与沙棘渣混合酵素、制备方法及其应用,本发明提供的方法不仅能够充分利用油莎豆粕和沙棘渣,减少资源浪费,并且可以保证酵素的品质,提升其抗氧化活性。
7.为了实现上述目的,本发明提供如下技术方案:
8.本发明提供了一种油莎豆粕与沙棘渣混合酵素的制备方法,包括以下步骤:将沙棘渣粉与油莎豆粕糖化液混合灭菌,然后依次进行酵母菌发酵和植物乳杆菌与酵母菌共同发酵,得到混合酵素。
9.优选的,所述酵母菌的接种量为0.22~0.28%,发酵温度为28~32℃,发酵时间为
18~25h。
10.优选的,所述酵母菌的接种量为0.25%,发酵温度为30℃,发酵时间为24h。
11.优选的,所述植物乳杆菌的接种量为1.5~2.5%,共同发酵温度为25~35℃,共同发酵时间为6~18h。
12.优选的,所述植物乳杆菌的接种量为2%,共同发酵温度为30℃,共同发酵时间为12h。
13.优选的,所述油莎豆粕糖化液的制备步骤包括:
14.1)将油莎豆粕浆料进行糊化,得到糊化液;
15.2)将糊化液、无水氯化钙和中温α
‑
淀粉酶混合进行酶解,得到酶解液,所述糊化液的ph值为6.2~6.8;
16.所述酶解的温度为55~60℃;所述酶解的时间为75~85min;
17.3)将酶解液和糖化酶混合进行糖化,得到油莎豆粕糖化液;
18.所述酶解液的ph值为4.3~5.0;所述糖化的温度为53~60℃;所述糖化的时间为5~6h。
19.优选的,所述沙棘渣粉与油莎豆粕糖化液的质量体积比为1g:12ml。
20.优选的,所述油莎豆粕的获得方式包括亚临界萃取。
21.本发明还提供了上述制备方法制备得到的油莎豆粕与沙棘渣混合酵素,所述混合酵素的dpph自由基清除率为94.10~95.26%。
22.本发明还提供了上述制备方法制备得到的混合酵素在酵素饮品中的应用。
23.本发明提供了一种油莎豆粕与沙棘渣混合酵素的制备方法,其将沙棘渣粉与油莎豆粕糖化液混合灭菌,然后依次进行酵母菌发酵和植物乳杆菌与酵母菌共同发酵,得到混合酵素。本发明提供的方法不仅能够充分利用油莎豆粕和沙棘渣,减少资源浪费,并且可以保证酵素的品质,提升其抗氧化活性。本发明中的油莎豆粕含有丰富的淀粉和蛋白质,经过糖化处理后可以为酵素的发酵菌提供碳源和氮源;沙棘果渣中含有丰富的黄酮、维生素b1、维生素b2、维生素c、维生素e、氨基酸、粗蛋白、粗脂肪、粗纤维、鞣质、糖、三帖及甾体类等活性成分。以上述二者为原料,采用先灭菌再依次接种酵母菌和植物乳杆菌进行混合发酵,利用菌种协同作用提升酵素的营养与风味,使酵素具有抗氧化、提升机体免疫力、润肠通便、保健护肝、美白抗衰老、抑菌消炎等功能。同时,外源添加菌种的发酵方式,可以有效防止有害菌繁殖,保证酵素品质。微生物通过生物转化产生的以及微生物自身生长代谢产生的功能成分,赋予了酵素食品丰富的营养价值。
24.本发明实施例的结果显示:采用本发明提供的方法制备得到的混合酵素的dpph自由基清除率为94.10~95.26%;sod酶活力为14.77~15.58u/ml;总黄酮含量为2.76~2.90mg/ml,过氧化氢酶(cat)活力为32.11umol/min/ml。
附图说明
25.为了更清楚地说明本发明实施例或现有技术中的技术方案,下面将对实施例中所需要使用的附图作简单地介绍。
26.图1为实施例1和对比例1
‑
4制备得到酵母菌发酵液中的酵母菌活菌数结果图;
27.图2为实施例2和对比例5
‑
8制备得到酵母菌发酵液中的酵母菌活菌数结果图;
28.图3为实施例3
‑
4和对比例9
‑
11制备得到酵母菌发酵液中的酵母菌活菌数结果图;
29.图4为对比例12
‑
16制备得到的混合酵素的dpph自由基清除率结果图;
30.图5为对比例17
‑
21制备得到的混合酵素的dpph自由基清除率结果图;
31.图6为对比例22
‑
26制备得到的混合酵素的dpph自由基清除率结果图。
具体实施方式
32.本发明提供了一种油莎豆粕与沙棘渣混合酵素的制备方法,包括以下步骤:
33.将沙棘渣粉与油莎豆粕糖化液混合灭菌,然后依次进行酵母菌发酵和植物乳杆菌与酵母菌共同发酵,得到混合酵素。
34.本发明将沙棘渣粉与油莎豆粕糖化液混合灭菌,得到灭菌后的混合样本。所述沙棘渣粉与油莎豆粕糖化液质量体积比优选为1:(10~15)ml,更优选为1g:12ml。
35.在本发明中,所述沙棘渣粉的粒径优选为150~250目,更优选为200目;所述沙棘渣粉优选的由沙棘渣粉碎得到,粉碎后的沙棘渣粉具有有助于有效成分的释放作用;本发明对沙棘渣的来源没有特殊限定,采用常规榨汁剩余的废弃沙棘渣即可,优选的购自内蒙古宇航人高技术产业有限责任公司。
36.在本发明中,所述油莎豆粕糖化液优选的由油莎豆粕糖化得到,所述油莎豆粕糖化液的主要成分是还原糖和水溶性蛋白质,为酵素发酵提供碳源和氮源。
37.在本发明中,所述油莎豆粕糖化液的制备步骤优选包括:
38.1)将油莎豆粕浆料进行糊化,得到糊化液;
39.2)将糊化液、无水氯化钙和中温α
‑
淀粉酶混合进行酶解,得到酶解液,所述糊化液的ph值为6.2~6.8;
40.所述酶解的温度为55~60℃;所述酶解的时间为75~85min;
41.3)将酶解液和糖化酶混合进行糖化,所述酶解液的ph值为4.3~5.0;
42.所述糖化的温度为53~60℃;所述糖化的时间为5~6h。
43.本发明优选将油莎豆粕浆料进行糊化,得到糊化液。
44.在本发明中,所述油莎豆粕浆料优选的由油莎豆粕粉和水混合得到;所述油莎豆豆粕粉和水的质量比优选为1:(15~25),更优选为1:(18~23),进一步优选为1:20。
45.在本发明中,所述油莎豆粕粉的粒径优选为20~40目,更优选为30目;所述油莎豆粕粉优选的由油莎豆粕粉碎得到,粉碎后的油莎豆粕粉能够使淀粉从豆粕中释放出来,以便更好地与酶结合。在本发明中,所述油莎豆粕优选以油莎豆为原料,且通过亚临界萃取得到;本发明对亚临界萃取的具体步骤没有特殊限定,采用本领域常规亚临界萃取步骤即可;在本发明的实施例中,具体可选择购自内蒙古赤峰地区生产的圣漠1号。
46.在本发明中,所述糊化的方式优选的包括:沸水浴10~20min进行糊化;所述糊化的时间优选为13~18min,更优选为15min。
47.得到糊化液后,本发明优选将糊化液、无水氯化钙和中温α
‑
淀粉酶混合进行酶解,得到酶解液。在本发明中,所述糊化液的ph值优选为6.2~6.8,更优选为6.4~6.6,进一步优选为6.5。在本发明中,所述酶解的温度优选为55~60℃,更优选为56~58℃,进一步优选为57℃;所述酶解的时间为75~85min,更优选为78~82min,进一步优选为80min。
48.在本发明中,所述中温α
‑
淀粉酶优选为食品级中温α
‑
淀粉酶,优选的购自于北京
索莱宝科技有限公司;中温淀粉酶的产物更易溶于水,并且中温淀粉酶作用较快,de上升快。在本发明中,所述中温α
‑
淀粉酶能够使淀粉中的α
‑
1,4糖苷键水解生成小分子糊精和其他低聚糖。
49.在将糊化液、无水氯化钙和中温α
‑
淀粉酶混合前,本发明优选的还包括将糊化液冷却至22~25℃,使酶解更有效进行。
50.在本发明中,所述糊化液和无水氯化钙的质量比优选为100:(0.005~0.015),更优选为100:(0.008~0.012),进一步优选为100:0.01。
51.在本发明中,所述无水氯化钙能使中温α
‑
淀粉酶耐高温保持液化过程中淀粉酶活力。
52.在本发明中,所述淀粉酶的用量以制备所述糊化液的油莎豆粕浆料中油莎豆粕粉的质量计,所述油莎豆粕粉的质量与所述α
‑
淀粉酶的酶活的比例优选为:1g:(7~7.5)u,更优选为1g:(7.2~7.4)u,进一步优选为1g:7.3u。
53.得到酶解液后,本发明优选将酶解液和糖化酶混合进行糖化。在本发明中,所述酶解液的ph值为4.3~5.0。
54.在本发明中,所述糖化酶优选为购自于上海源叶生物科技有限公司的s10017
‑
250g糖化酶;s10017
‑
250g糖化酶能够将糊精、低聚糖中的α
‑
1,6糖苷键和α
‑
1,4糖苷键切断,生成葡萄糖。
55.在本发明中,所述糊化液的用量以制备所述糊化液的油莎豆粕浆料中油莎豆粕粉的质量计,所述油莎豆粕粉的质量与和所述糖化酶的酶活的比例优选为1g:(120~140)u,更优选为1g:(123~125)u,进一步优选为1g:124u。
56.在本发明中,所述糖化的温度优选为53~60℃,更优选为54~56℃,进一步优选为55℃;所述糖化的时间为5~6h,更优选为5.2~5.5h,进一步优选为5.3h。
57.在糖化结束后,本发明优选还包括将糖化后的酶解液在沸水浴中加热10min使酶失活,过滤酶解液得到糖化液。本发明对酶解液的过滤方式没有特殊限定,采用本领域常规过滤方式即可。
58.在本发明中,将沙棘渣粉与油莎豆粕糖化液混合后,优选采用高压蒸汽灭菌方式进行灭菌,本发明对高压蒸汽灭菌的方法没有特殊限定,采用本领域常规高压蒸汽灭菌方式即可。
59.得到灭菌后的混合样本后,本发明在所述混合样本中接种酵母菌进行发酵,得到酵母菌发酵液。
60.在本发明中,以灭菌后的混合样本体积计,所述酵母菌的接种量优选为0.22~0.28%,更优选为0.23~0.26%,进一步优选为0.25%;所述发酵温度优选为28~32℃,更优选为29~31℃,进一步优选为30℃;所述发酵时间优选为18~25h,更优选为23~25h,进一步优选为24h。在本发明中,所述酵母菌发酵的作用为:在前期有氧条件下酵母菌能够迅速出芽繁殖,增加了酵母菌的数量,同时消耗发酵液中的氧气,促成微氧环境有助于乳酸菌生长;同时油莎豆粕经酵母菌发酵能够产生多种氨基酸、维生素等,以此作为生长因子可以促进后续植物乳杆菌的生长。
61.在接种酵母菌之前,本发明优选的还包括将所述灭菌后的混合样本冷却至23℃,本发明对冷却方法没有特殊限定,能够达到冷却目的即可。
62.得到酵母菌发酵液后,本发明在所述酵母菌发酵液中接种植物乳杆菌继续共同发酵,得到混合酵素。
63.在本发明中,以灭菌后的混合样本体积计,所述植物乳杆菌的接种量优选为1.5~2.5%,更优选为1.8~2.2%,进一步优选为2%;所述共同发酵温度优选为25~35℃,更优选为28~32℃,进一步优选为30℃;所述共同发酵时间优选为6~18h,更优选为10~14h,进一步优选为12h。在本发明中,植物乳杆菌与酵母菌采用的是相似的发酵生长条件,有很好的共生基础,通过先酵母菌发酵再植物乳杆菌与酵母菌共同发酵的的方式,不仅可以提高发酵速度,促进黄酮等抗氧化成分从沙棘渣中释放出来,加速有益产物的积累,而且会产生丰富,良好的风味物质,同时,植物乳杆菌进入人体内后,还可以通过改善肠道菌群的组成,进而发挥更多的有益作用。
64.在植物乳杆菌发酵之后,本发明优选的还包括对所述植物乳杆菌进行过滤得混合酵素,本发明对过滤的方法没有特殊限定,采用本领域常规过滤方式即可。
65.本发明还提供了上述制备方法制备得到的油莎豆粕与沙棘渣混合酵素,所述混合酵素的dpph自由基清除率为94.10~95.26%。在本发明中,所述酵素具有抗氧化、提升机体免疫力、润肠通便、保健护肝、美白抗衰老、抑菌消炎等功能。
66.本发明还提供了上述制备方法制备得到的混合酵素在酵素饮品中的应用。
67.为了进一步说明本发明,下面结合实施例对本发明提供的技术方案进行详细地描述,但不能将它们理解为对本发明保护范围的限定。
68.实施例1
69.将5g沙棘渣粉碎至200目,加入60ml油莎豆粕糖化液,混合均匀,之后进行高压蒸汽灭菌,冷却后接入0.25%酵母菌,置于30℃发酵24小时,得到酵母菌发酵液。
70.油莎豆粕糖化液的制备:
71.将油莎豆粕磨碎,按照料液比(质量比)1:20的比例打浆均质,沸水浴15min使淀粉糊化,冷却后调节ph为6.5,加入0.01%糊化液质量的无水氯化钙,每克油莎豆粕粉添加7.3u中温α
‑
淀粉酶,温度控制为57℃,酶解时间为80min,之后调节ph为4.5,每克油莎豆粕粉加入124u糖化酶,温度调节到55℃,糖化时间5.3h,糖化结束之后在沸水浴中加热10min使酶失活,最后将酶解液过滤得到糖液。
72.对比例1
73.除了酵母菌接种量为0.10%以外,其余与实施例1相同。
74.对比例2
75.除了酵母菌接种量为0.15%以外,其余与实施例1相同。
76.对比例3
77.除了酵母菌接种量为0.20%以外,其余与实施例1相同。
78.对比例4
79.除了酵母菌接种量为0.30%以外,其余与实施例1相同。
80.实施例1和对比例1~4中得到的酵母菌发酵液中酵母菌的活菌数如图1所示,由图1可以看出,随着接种量的增加,酵母菌发酵液中的酵母菌活菌数呈现先上升后下降的趋势,且在接种量为0.25%时,酵母菌的活菌数达到峰值4.175
×
108cfu/ml。在本发明中,所述酵母菌活菌数的检测方法参照国家标准《gb 4789.15
‑
2016食品安全国家标准食品微生
物检验霉菌和酵母计数》。
81.实施例2
82.将5g沙棘渣粉碎至200目,加入60ml油莎豆粕糖化液,混合均匀,之后进行高压蒸汽灭菌,冷却后接入0.23%酵母菌,置于30℃发酵24小时,得到酵母菌发酵液。
83.油莎豆粕糖化液的制备方法与实施例1相同。
84.对比例5
85.除了发酵温度为20℃以外,其余与实施例2相同。
86.对比例6
87.除了发酵温度为25℃以外,其余与实施例2相同。
88.对比例7
89.除了发酵温度为35℃以外,其余与实施例2相同。
90.对比例8
91.除了发酵温度为40℃以外,其余与实施例2相同。
92.实施例2和对比例5~8中得到的酵母菌发酵液中酵母菌的活菌数如图2所示,由图2可以看出,随着发酵温度的提高,酵母菌发酵液中的酵母菌活菌数呈现先上升后下降的趋势,且在发酵温度为30℃时,酵母菌的活菌数达到峰值8.267
×
107cfu/ml。
93.实施例3
94.将5g沙棘渣粉碎至200目,加入60ml油莎豆粕糖化液,混合均匀,之后进行高压蒸汽灭菌,冷却后接入0.26%酵母菌,置于30℃发酵24小时,得到酵母菌发酵液。
95.油莎豆粕糖化液的制备方法与实施例1相同。
96.实施例4
97.除了发酵时间为18h以外,其余与实施例3相同。
98.对比例9
99.除了发酵时间为6h以外,其余与实施例3相同。
100.对比例10
101.除了发酵时间为12h以外,其余与实施例3相同。
102.对比例11
103.除了发酵时间为30h以外,其余与实施例3相同。
104.实施例3
‑
4和对比例9~11中得到的酵母菌发酵液中酵母菌的活菌数如图3所示,由图3可以看出,随着发酵时间的增加,酵母菌发酵液中的酵母菌活菌数呈现先上升、稳定、后下降的趋势,且在发酵时间为24h时,酵母菌的活菌数达到峰值1.330
×
108cfu/ml。
105.实施例5
106.将5g沙棘渣粉碎至200目,加入60ml油莎豆粕糖化液,混合均匀,之后进行高压蒸汽灭菌,冷却后接入0.25%酵母菌,置于30℃发酵24小时;之后加入2%植物乳杆菌,在30℃条件下发酵12小时,过滤得到混合酵素。
107.油莎豆粕糖化液的制备方法与实施例1相同。
108.实施例6
109.将5g沙棘渣粉碎至200目,加入60ml油莎豆粕糖化液,混合均匀,进行高压蒸汽灭菌,冷却后接入0.25%酵母菌,置于30℃发酵24小时;之后进行高压蒸汽灭菌,冷却后加入
2%植物乳杆菌,在25℃条件下发酵6小时,过滤得到混合酵素。
110.油莎豆粕糖化液的制备方法与实施例1相同。
111.实施例7
112.将5g沙棘渣粉碎至200目,加入60ml油莎豆粕糖化液,混合均匀,进行高压蒸汽灭菌,冷却后接入0.25%酵母菌,置于30℃发酵24小时;之后加入1.5%植物乳杆菌,在30℃条件下发酵18小时,过滤得到混合酵素。
113.油莎豆粕糖化液的制备方法与实施例1相同。
114.实施例8
115.将5g沙棘渣粉碎至200目,加入60ml油莎豆粕糖化液,混合均匀,进行高压蒸汽灭菌,冷却后接入0.25%酵母菌,置于30℃发酵24小时;之后加入2.5%植物乳杆菌,在35℃条件下发酵12小时,过滤得到混合酵素。
116.油莎豆粕糖化液的制备方法与实施例1相同。
117.对比例12
118.将5g沙棘渣粉碎至200目,加入60ml油莎豆粕糖化液,混合均匀,进行高压蒸汽灭菌,冷却后接入0.25%酵母菌,置于30℃发酵24小时;之后加入2%植物乳杆菌,分别在25℃条件下发酵24小时,过滤得到混合酵素。
119.油莎豆粕糖化液的制备方法与实施例1相同。
120.对比例13
121.除了加入植物乳杆菌后的发酵温度为30℃以外,其余与对比例12相同。
122.对比例14
123.除了加入植物乳杆菌后的发酵温度为35℃以外,其余与对比例12相同。
124.对比例15
125.除了加入植物乳杆菌后的发酵温度为40℃以外,其余与对比例12相同。
126.对比例16
127.除了加入植物乳杆菌后的发酵温度为45℃以外,其余与对比例12相同。
128.对比例17
129.将5g沙棘渣粉碎至200目,加入60ml油莎豆粕糖化液,混合均匀,进行高压蒸汽灭菌,冷却后接入0.25%酵母菌,置于30℃发酵24小时;之后加入1%植物乳杆菌,分别在35℃条件下发酵24小时,过滤得到混合酵素。
130.对比例18
131.除了植物乳杆菌的接种量为1.5%以外,其余与对比例17相同。
132.对比例19
133.除了植物乳杆菌的接种量为2.0%以外,其余与对比例17相同。
134.对比例20
135.除了植物乳杆菌的接种量为2.5%以外,其余与对比例17相同。
136.对比例21
137.除了植物乳杆菌的接种量为3.0%以外,其余与对比例17相同。
138.对比例22
139.将5g沙棘渣粉碎至200目,加入60ml油莎豆粕糖化液,混合均匀,进行高压蒸汽灭
菌,冷却后接入0.25%酵母菌,置于30℃发酵24小时;之后加入2%植物乳杆菌,在35℃条件下分别发酵6h小时,过滤得到混合酵素。
140.对比例23
141.除了加入植物乳杆菌后的的发酵时间为12h以外,其余与对比例22相同。
142.对比例24
143.除了加入植物乳杆菌后的的发酵时间为18h以外,其余与对比例22相同。
144.对比例25
145.除了加入植物乳杆菌后的的发酵时间为24h以外,其余与对比例22相同。
146.对比例26
147.除了加入植物乳杆菌后的的发酵时间为30h以外,其余与对比例22相同。
148.测试例1
149.dpph自由基清除率的测定方法:
150.1)用无水乙醇配制0.2mm dpph溶液,避光保存;
151.2)移取2ml dpph与2ml样液进行混合,摇匀,室温下避光处静置反应30min后,以等体积无水乙醇调零,测定517nm波长处吸光度值(a
i
);
152.3)测定2ml样品与2ml无水乙醇混合后的吸光度值(a
j
);
153.4)测定2ml dpph与2ml无水乙醇混合后的吸光度值(a0)。
154.计算公式如下:dpph自由基清除率(%)=[a0–
(a
i
–
a
j
)]
×
100/a0[0155]
参考文献:[1]li bo,du wenkai,jin jianchang,et al.preservation of(
‑
)
‑
epigallocatechin
‑3‑
gallate antioxidant properties loaded in heat treatedβ
‑
lactoglobulin nanoparticles.[j].journal of agricultural and food chemistry,2012,60(13):3477
‑
84.
[0156]
[2]ah
‑
na kim et al.degradation kinetics of phenolic content and antioxidant activity of hardy kiwifruit(actinidia arguta)puree at different storage temperatures[j].lwt
‑
food science and technology,2018,89:535
‑
541.
[0157]
采用上述方法对实施例5~8和对比例12~26中混合酵素的dpph自由基清除率,结果如表1。
[0158]
表1实施例5~8和对比例12~26中混合酵素的dpph自由基清除率结果
[0159][0160][0161]
由以上实施例可以得出,采用本发明提供的方法可以提高混合酵素的抗氧化活性,其dpph自由基清除率为94.10~95.26%,显著高于对比例中制备得到的混合酵素的dpph自由基清除率。可见,本发明提供的方法不仅能够充分利用油莎豆粕和沙棘渣,减少资源浪费,并且可以保证酵素的品质,提升其抗氧化活性。
[0162]
测试例2
[0163]
对实施例5~8和对比例12~26制备得到的混合酵素进行品鉴,品鉴标准及结果如表2。
[0164]
表2混合酵素品鉴表
[0165][0166][0167]
由表2可以得出,采用本发明制备方法得到的酵素经感官评定色泽均匀,为淡褐红色;有一定的浓稠度,目测无杂质和沉淀物,明晰清彻;口感细腻,为酸中带甜,甜中微酸,口味绵滑,醇厚清爽,无涩味、苦酸、浓呛以及其他异味;香气协调,风味突出。
[0168]
对比例中制备得到的酵素经感官评定具备为酸中带甜,但是味道偏酸,有果味,但酒味较浓。
[0169]
测试例3
[0170]
对实施例5~8和对比例12~26中的混合酵素的sod酶活力、总黄酮含量和过氧化氢酶活力(cat)进行检测,结果如表4。
[0171]
其中,sod酶活力测定采用苏州科铭生物技术有限公司生产的超氧化物歧化酶sod试剂盒(nbt法)进行测定;过氧化氢酶活力测定采用苏州格锐思生物科技有限公司生产的过氧化氢酶(cat)试剂盒进行测定;总黄酮含量测定参照《sn/t 4592
‑
2016出口食品中总黄酮的测定》测定。
[0172]
表4实施例5~8和对比例12~26中的混合酵素的sod酶活力、总黄酮含量和过氧化氢酶活力(cat)检测结果
[0173][0174][0175]
经测定,本发明提供的混合酵素的sod酶活力为14.77~15.58u/ml;总黄酮含量为2.76~2.90mg/ml,过氧化氢酶(cat)活力为32.11umol/min/ml。且本发明提供的混合酵素的sod酶活力、总黄酮含量和过氧化氢酶(cat)活力均显著高于对比例。
[0176]
尽管上述实施例对本发明做出了详尽的描述,但它仅仅是本发明一部分实施例,而不是全部实施例,人们还可以根据本实施例在不经创造性前提下获得其他实施例,这些实施例都属于本发明保护范围。