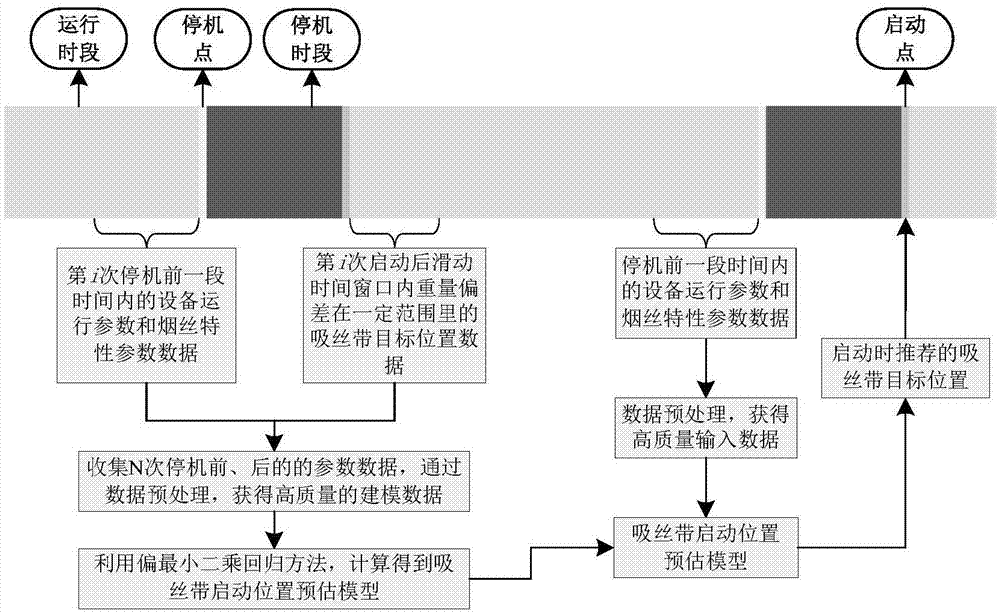
本发明涉及基于卷烟机设备运行参数数据和烟丝特性参数数据,进行烟支重量控制系统吸丝带启动位置的智能预估建模和在线优化设定技术。
背景技术:
:随着近年来烟草行业全球化、新的法律法规以及外部环境的重大变化,中国烟草面临愈来愈严峻的竞争压力和社会压力。在保证产品质量的前提下,有效提升设备的智能化水平和高效运行能力成为卷烟工厂关注的焦点。智能化,即生产设备具有感知、分析、推理和决策等功能;高效运行,即在规定时间内消耗更少的资源生产更多、更好的产品。卷烟机启动运行阶段,由于重量控制系统未投入运行,如何根据停机前设备运行参数和烟丝特性参数的数据分析和挖掘,预估出合理的吸丝带启动位置,降低烟支剔除的数量进而减少烟丝和辅材的消耗,是提升卷烟机智能化水平和高效运行能力的核心问题。zj112卷烟机是中烟机械集团有限责任公司从德国虹霓公司引入protos-90e技术,由常德烟机公司进行技术吸收制造的高速机型,设计额定速度为10000支/分钟。通过“十二五”期间中国烟草机械集团的重点推广,目前zj112卷烟机已经成为国内卷烟工厂的主力机型。zj112卷烟机烟支重量控制系统(srm)主要由烟支重量检测器(微波扫描仪b800v)、烟丝温度传感器(r800v)、烟支重量控制系统执行装置(烟条平准器trm)、烟支重量的控制和监测装置(a800v)、人机交互触摸屏(mlp)等组成。卷烟机烟支重量控制系统对来自微波扫描仪的烟支重量检测值和烟支重量目标值进行评估,如果实际重量与目标重量不符,会计算出一个新的吸丝带位置并传送至烟条平准器,进行吸丝带位置的调节,重量控制系统中吸丝带调整范围为3.5mm,对应线性位置传感器-7v(最高)到+7v(最低)。重量控制系统只有在有连续的卷烟通过微波扫描仪且生产速度超过运行速度阈值后才能被触发,在较低运行速度或当前无烟条存在是,无法进行重量控制。zj112卷烟机说明书中,标准的运行速度阈值为1200支/分钟,推荐的吸丝带启动位置为2.5v。德国虹霓公司最新的win2烟支重量控制系统说明书中,自动计算停机前30分钟所对应的吸丝带位置平均值并推荐为启动位置。上述方法获得的重量控制系统吸丝带启动位置设定值未充分分析和挖掘停机前的设备运行参数和烟丝特性参数数据,亟需一种切实有效的数据分析和预测方法,优化卷烟机开始运行时的吸丝带启动位置。为解决上述问题,公开号为cn108323797a的专利文献公开了一种基于gpr模型的烟支重量控制系统启动位置预测方法及系统,通过烟支重量控制系统平准器的停机前目标位置数据和启动后目标位置数据,利用gpr模型进行平准器启动位置和残差的预测,获得最终的启动位置输出值。卷烟机重新启动后的吸丝带最佳启动位置受停机前设备运行参数和烟丝特性参数的共同影响,该方法仅仅考虑了平准器目标位置(即吸丝带目标位置)这一个设备运行参数,对影响烟支重量的其它设备运行参数未做考虑,同时也未考虑烟丝特性参数影响,造成该gpr模型输入参数不完备,使得该gpr模型不能有效反映其它设备运行参数和烟丝特性参数变化的影响,计算得到的最终启动位置输出值偏离理想启动位置。技术实现要素:针对现有技术的不足,本发明提出一种基于设备运行数据和烟丝特性数据的吸丝带启动位置智能优化设定方法。该方法根据预定义的判断规则自动识别卷烟机生产的停止和开始,收集n次生产停止前一段时间内的卷烟机ve(烟丝供料装置)运行参数数据和烟丝特性参数数据,通过对不同采样率下各个参数数据的重新组织构成预估模型的原始输入数据根据卷烟生产开始后首次进入稳定状态的定义,收集与上述生产停止所对应的n次生产开始后的吸丝带目标位置数据,通过数据均质化处理获得预估模型的原始输出数据对原始建模数据进行归一化处理,获得预估模型的归一化建模数据{x,y},利用偏最小二乘回归方法建立吸丝带启动位置预估模型y=xθ。将本次生产停止前一段时间内的卷烟机ve烟丝供料装置运行参数数据和烟丝特性参数数据,重新组织构成本次停机的输入数据对其进行归一化处理,获得预估模型的归一化输入数据xnew,根据吸丝带启动位置预估模型θ计算得到本次启动时的吸丝带目标位置当卷烟机生产开始时,通过伺服电机将吸丝带自动调整到该推荐启动位置,减少卷烟机生产启动阶段的烟支剔除。该方法基于设备历史运行数据和烟丝特性参数数据的挖掘分析,有效实现了卷烟机启动阶段重量控制系统吸丝带位置的智能优化设定。具体地,本发明提供的卷烟机烟支重量控制系统吸丝带启动位置的智能优化设定方法包括如下步骤:1)收集与卷烟机ve烟丝供料装置运行参数和烟丝特性参数数据,设备运行参数包括重量偏差、吸丝带目标位置、吸丝带当前位置、设备运行速度、风室负压、压实量当前值和压实端位置当前值;烟丝特性参数包括烟丝水分、烟丝温度和烟丝填充值;且,重量偏差、吸丝带目标位置、吸丝带当前位置3个参数的采样频率为高速数采;设备运行速度、风室负压、压实量当前值、压实端位置当前值、烟丝水分、烟丝温度6个参数的采样频率为普通数采;烟丝填充值为离线检验,由多次抽检数据的算术平均值所表征;2)不同采样率下的数据预处理,对重量偏差、吸丝带目标位置、吸丝带当前位置3个高速数采的参数数据进行均值化处理;3)设定设备停止和开始运行的判定规则;4)根据设备停止运行的判定规则,截取第i次停机前一段时间内的卷烟机ve烟丝供料装置运行参数和烟丝特性参数数据,按照重量偏差、吸丝带目标位置、吸丝带当前位置、设备运行速度、风室负压、压实量当前值、压实端位置当前值、烟丝水分、烟丝温度、烟丝填充值的顺序,构成第i次停机的预估模型原始输入数据5)根据设备开始运行的判定规则,获得设备启动时刻,该时刻为启动后首次进入稳定状态的时刻。截取该时刻所对应滑动时间窗口内的吸丝带目标位置数据,将其均值作为第i次启动的吸丝带最佳目标位置,即第i次启动的预估模型原始输出数据6)收集n次设备停机和启动的数据,获得预估模型的原始建模数据按照下述公式对原始建模数据进行归一化处理,消除不同参数量纲的影响,获得预估模型的归一化建模数据{x,y},其中x={x1,x2,…,xn}、y={y1,y2,…,yn};其中,和分别表示原始建模数据中第j个参数的最大值和最小值;和分别表示中的最大值和最小值;利用偏最小二乘回归方法,在建模数据{x,y}上计算得到重量控制系统吸丝带启动位置预估模型y=xθ;计算公式如下:t=xw(ptw)-1=xry=tqt+f=xrqt+f=xθ+f其中,t(n×a)、p(1110×a)与w(1110×a)分别是x的得分矩阵、负载矩阵与权重矩阵,r(1110×a)是直接从x计算得分的权重矩阵;q(a×1)是y的负载向量;θ(1110×1)是最终的吸丝带启动位置预估模型;a是保留的潜变量个数,通过交叉检验方法确定;f(n×1)是吸丝带启动位置预估模型的残差向量;7)将本次生产停止前一段时间内的卷烟机ve烟丝供料装置运行参数数据和烟丝特性参数数据,重新组织构成本次停机的输入数据对其进行归一化处理,获得预估模型的归一化输入数据xnew,根据吸丝带启动位置预估模型θ计算得到本次启动时的吸丝带目标位置8)当卷烟机生产开始时,通过伺服电机将吸丝带自动调整到步骤3)获得的推荐的启动位置,减少卷烟机生产启动阶段的烟支剔除。作为优选,步骤1)中重量偏差、吸丝带目标位置、吸丝带当前位置3个参数的采样频率为每间隔20毫秒采集一次数据,设备运行速度、风室负压、压实量当前值、压实端位置当前值、烟丝水分、烟丝温度6个参数的采样频率为每间隔2秒采集一次数据,烟丝填充值为离线检验,每个烟丝桶离线抽检4次,认为同一桶烟丝的填充值基本不变,由4次抽检数据的算术平均值所表征;由于卷烟机运行速度不同,消耗一桶烟丝大致需要1~1.5小时,该时段内烟丝填充值取为恒定值。作为优选,采用窗口大小为10、步长大小为10的滑动时间窗口,对重量偏差、吸丝带目标位置、吸丝带当前位置3个高速数采的参数数据进行均值化处理,处理后上述3个参数相邻样本点的时间间隔为0.2秒,处理后每个高速数采参数的10个样本点对应每个普通数采参数的1个样本点和离线检验参数的1个样本点。作为优选,根据20ms采集一次的重量偏差数据,当前时刻之前的200个采样点重量偏差方差为0时,判定设备停止运行,停机时刻为当前时刻减去4秒钟;设备停止运行后,当前时刻之前的200个采样点重量偏差方差不为0时,判定设备开始运行,启动时刻为当前时刻。作为优选,步骤2)中采用窗口大小为10、步长大小为10的滑动时间窗口,对重量偏差、吸丝带目标位置、吸丝带当前位置3个高速数采的参数数据进行均值化处理,处理后上述3个参数相邻样本点的时间间隔为0.2秒,处理后每个高速数采参数的10个样本点对应每个普通数采参数的1个样本点和离线检验参数的1个样本点。作为优选,所述步骤5)根据设备开始运行的判定规则,获得设备启动时刻。从启动时刻开始,采用窗口大小为50、步长大小为1的滑动时间窗口,判断滑动时间窗口内的重量偏差样本点首次均在20mg以内的时刻点,该时刻为启动后首次进入稳定状态的时刻;截取该时刻所对应滑动时间窗口内的吸丝带目标位置数据(1×50维),将其均值作为第i次启动的吸丝带最佳目标位置,即第i次启动的预估模型原始输出数据作为优选,所述步骤4)和步骤7)中的截取停机前一段时间的数据均为截取停机前1分钟内。本发明的有益效果在于:通过对zj112卷烟机设备运行参数数据和烟丝特性参数数据的深入分析和挖掘,建立了重量控制系统吸丝带启动位置预估模型。将本次停机前的设备运行参数数据和烟丝特性参数数据送入吸丝带启动位置预估模型,获得本次启动时的吸丝带目标位置。与zj112卷烟机烟支重量控制系统吸丝带启动位置的推荐值固定为2.5v,以及德国公司最新的win2烟支重量控制系统吸丝带启动位置的推荐值选取为停机前30分钟所对应的吸丝带位置平均值相比,本发明计算得到的吸丝带启动位置更加靠近卷烟机启动后首次进入稳定状态时刻的吸丝带位置,减少了烟支重量控制系统投入运行前以及投运后过渡状态下所产生的不合格烟支,补齐了卷烟机启动阶段的智能化短板,提升了设备的高效运行能力。附图说明图1为本发明的卷烟机烟支重量控制系统吸丝带位置智能优化设定方法的原理示意图;图2为不同采样率下各个参数的数据对应结构图;图3为烟支重量控制系统吸丝带启动位置实际值与预估值的对比;图4为烟支重量控制系统吸丝带启动位置预测偏差。具体实施方式为了更好的理解本发明的技术方案,以下结合说明书附图对本发明的实施方式作进一步描述。本实施是用于常德烟草机械有限责任公司zj112高速卷烟机烟支重量控制系统(srm)吸丝带启动位置的智能优化设定方法。zj112卷烟机烟支重量控制系统主要由烟支重量检测器(微波扫描仪b800v)、烟丝温度传感器(r800v)、烟支重量控制系统执行装置(烟条平准器trm)、烟支重量的控制和监测装置(a800v)、人机交互触摸屏(mlp)等组成。卷烟机烟支重量控制系统对来自微波扫描仪的烟支重量检测值和烟支重量目标值进行评估,如果实际重量与目标重量不符,会计算出一个新的吸丝带位置并传送至烟条平准器,进行吸丝带位置的调节,重量控制系统中吸丝带调整范围为3.5mm,对应线性位置传感器-7v(最高)到+7v(最低)。本发明的卷烟机烟支重量控制系统吸丝带启动位置智能优化设定方法的实现框图如图1所示,方法主要分为以下几步:1)收集与卷烟机重量控制系统相关的设备运行参数和烟丝特性参数数据。其中设备运行参数包括:重量偏差、吸丝带目标位置、吸丝带当前位置、设备运行速度、风室负压、压实量当前值、压实端位置当前值;烟丝特性参数包括:烟丝水分、烟丝温度、烟丝填充值。重量偏差、吸丝带目标位置、吸丝带当前位置3个参数的采样频率为每间隔20毫秒采集一次数据(高速数采)。设备运行速度、风室负压、压实量当前值、压实端位置当前值、烟丝水分、烟丝温度6个参数的采样频率为每间隔2秒采集一次数据(普通数采)。烟丝填充值为离线检验,投料前每个烟丝桶离线抽检4次,认为同一桶烟丝的填充值基本不变,由4次抽检数据的算术平均值所表征;由于卷烟机运行速度不同,消耗一桶烟丝大致需要1~1.5小时,该时段内烟丝填充值取为恒定值。2)不同采样率下的数据预处理:采用窗口大小为10、步长大小为10的滑动时间窗口,对重量偏差、吸丝带目标位置、吸丝带当前位置3个高速数采的参数数据进行均值化处理,处理后上述3个参数相邻样本点的时间间隔为0.2秒,处理后每个高速数采参数的10个样本点对应每个普通数采参数的1个样本点和离线检验参数的1个样本点,各参数的数据对应结构如图2所示。3)设备停止和开始运行的判定:根据20ms采集一次的重量偏差数据,当前时刻之前的200个采样点重量偏差方差为0时,判定设备停止运行,停机时刻为当前时刻减去4秒钟;设备停止运行后,当前时刻之前的200个采样点重量偏差方差不为0时,判定设备开始运行,启动时刻为当前时刻。4)根据设备停止运行的判定规则,截取第i次停机前一段时间内(1分钟)设备运行参数和烟丝特性参数数据,按照重量偏差(1×300维)、吸丝带目标位置(1×300维)、吸丝带当前位置(1×300维)、设备运行速度(1×30维)、风室负压(1×30维)、压实量当前值(1×30维)、压实端位置当前值(1×30维)、烟丝水分(1×30维)、烟丝温度(1×30维)、烟丝填充值(1×30维)的顺序,重新组织构成第i次停机的预估模型原始输入数据5)根据设备开始运行的判定规则,获得设备启动时刻。从启动时刻开始,采用窗口大小为50、步长大小为1的滑动时间窗口,判断滑动时间窗口内的重量偏差样本点首次均在±20mg以内的时刻点,该时刻为启动后首次进入稳定状态的时刻。截取该时刻所对应滑动时间窗口内的吸丝带目标位置数据(1×50维),将其均值作为第i次启动的吸丝带最佳目标位置,即第i次启动的预估模型原始输出数据6)收集n次设备停机和启动的数据,获得预估模型的原始建模数据按照下述公式对原始建模数据进行归一化处理,消除不同参数量纲的影响,获得预估模型的归一化建模数据{x,y},其中x={x1,x2,…,xn}、y={y1,y2,…,yn}。其中,和分别表示原始建模数据中第j个参数的最大值和最小值;和分别表示中的最大值和最小值。利用偏最小二乘回归方法,在建模数据{x,y}上计算得到重量控制系统吸丝带启动位置预估模型y=xθ。计算公式如下:t=xw(ptw)-1=xry=tqt+f=xrqt+f=xθ+f其中,t(n×a)、p(1110×a)与w(1110×a)分别是x的得分矩阵、负载矩阵与权重矩阵,r(1110×a)是直接从x计算得分的权重矩阵。q(a×1)是y的负载向量。θ(1110×1)是最终的吸丝带启动位置预估模型。a是保留的潜变量个数,通过交叉检验方法确定。f(n×1)是吸丝带启动位置预估模型的残差向量。7)根据设备停止运行的判定规则,自动截取本次停机前一段时间内(1分钟)设备运行参数和烟丝特性参数数据,组织构成本次停机的原始输入数据对其进行归一化处理,消除不同参数量纲的影响,获得预估模型的归一化输入数据xnew,根据吸丝带启动位置预估模型θ计算得到本次启动时的吸丝带目标位置烟支重量控制系统吸丝带启动位置真实值与预估值的对比结果如图3所示,吸丝带启动位置预测偏差如图4所示。从图3、图4中可以看出,吸丝带启动位置预估模型的预测结果还是比较满意的,预测误差基本在±0.8v以内。通过吸丝带启动位置预测结果的数学统计,平均绝对误差mae为0.2806,均方根误差rmse为0.3764。预测误差绝对值在各个区间的占比如下表1所示:表1指标(v)0~0.20.2~0.40.4~0.60.6~0.80.8~1>1占比(%)46.5931.2312.415.191.832.75与公开号为cn108323797a的专利文献公开的一种基于gpr模型的烟支重量控制系统启动位置预测方法及系统相比,本文所提方法的吸丝带启动位置预测结果均方根误差rmse指标提升了8.19%,数学统计结果表明所提方法能够满足卷烟机启动阶段对吸丝带启动位置合理设定的要求。该方法基于设备历史运行数据和烟丝特性参数数据的挖掘分析,有效实现了卷烟机启动阶段重量控制系统吸丝带位置的智能优化设定。该方法针对卷烟机生产停止后,再次生产时由于重量控制系统延迟启动和吸丝带启动位置设置不合理造成的启动阶段烟支剔除较多的问题。当前第1页12