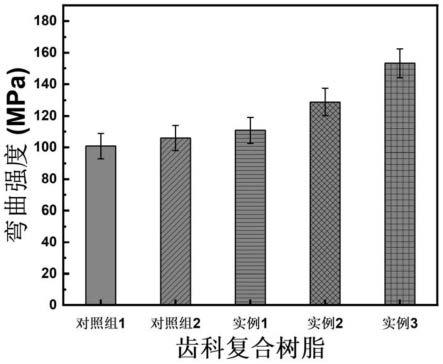
1.本发明属于齿科修复领域,特别涉及一种多级填料构筑齿科复合树脂及其制备方法。
背景技术:2.口腔是人体内十分重要的器官,其内部环境复杂,受体内外多因素的影响,经常会产生一种常见病和多发病——龋病,该病已被世界卫生组织(who)列为21世纪需重点防治的三大非传染性疾病之一。据四次全国口腔健康流行病学调查报告结果表明,随着人们年龄的增长,患龋率逐年递增,现我国人民平均患龋率高达80%以上,若不及时治疗会严重影响人类身体健康和生活质量。龋病的病因较为复杂,其形成的机制主要为:细菌在牙体硬组织表面形成菌斑,并将碳水化合物代谢产生有机酸,酸作用于牙齿,使牙齿中的羟基磷灰石晶体溶解,若该过程不能得到很好地控制,龋齿将最终形成。
3.复合树脂以其美观的色泽、良好的物理化学性能、细胞毒性小以及临床操作方便等优点,在大部分国家和地区已经完全取代传统的银汞合金,成为当前国内外治疗牙体缺损充填修复首选材料。复合树脂主要由有机单体、无机填料和少量光引发体系组成,其中有机树脂含有可聚合反应的基团,在光固化作用下,形成三维网络结构,可赋予材料一定的形状;无机填料主要赋予复合材料优异的力学性能,同时减少复合树脂的聚合收缩。据报道,因力学性能不足所致的树脂修复体折断、因聚合物收缩大所致的微渗漏和二次龋齿的发生、因无机填料填充量低所致的成本增加等种种现象,是造成齿科复合树脂临床使用效果不尽如人意的主要原因。为了解决上述问题,人们试图通过开发新型结构填料、优化有机-无机相界面等措施来提高复合树脂的力学性能,例如,专利cn 104083289 a对二氧化硅纳米纤维表面进行硅烷化改性,制得的复合树脂的弯曲强度为79.8-93.2mpa,该方法得到的复合树脂在有机无机界面形成的作用力较弱,在长期的服役过程中容易发生水解(t.nihei.journal of oral science,2016,58,151-155.);专利cn 108852858a设计了一种红毛丹状sio2填料,该填料表面拥有类似“锯齿”的凸起结构,该结构可增大粒子之间的摩擦力以及粒子与树脂基体的接触面积,改善相界面性能,但“锯齿”结构仅存在于红毛丹状sio2填料表面,因此有机单体仅能在填料表面渗透,未能有效贯穿于填料内部,进而使得有机-无机相界面结合性提高程度受限;专利cn112206171a设计了一种孔径可调的树枝状二氧化硅填料,通过填料-树脂的物理微机械互锁效应,形成“十字绣”般互相铰链的网状结构,从而提高有机-无机相的界面结合力,增强齿科复合树脂的力学性能,但是其填料的填充量较低导致其复合树脂的成本偏高,同时聚合收缩率也没有得到很好的改善。
技术实现要素:4.本发明所要解决的技术问题是提供一种多级填料构筑齿科复合树脂及其制备方法,该复合树脂克服了以树枝状多孔sio2单独做无机填料的齿科复合树脂填充量低的缺陷,进一步提高齿科复合树脂的力学性能并降低其聚合收缩率。
5.本发明提供了一种多级填料构筑齿科复合树脂,所述复合树脂按质量百分比,包括如下组分:
6.多级填料33-89%;
7.树脂基体15-67%;
8.光引发剂0.1-1%;各组分质量百分比之和为100%;
9.其中,所述多级填料由质量比为1:9-9:1的多孔sio2填料和硅烷化无孔sio2填料组成。
10.所述多孔sio2填料的孔径为2-3.5nm,粒径为0.03μm-1.5μm;所述硅烷化无孔sio2填料的粒径为0.05μm-1.2μm。
11.所述树脂基体为双酚a-双甲基丙烯酸缩水甘油酯bis-gma、双甲基丙烯酸二缩三乙二醇酯tegdma、双酚a聚氧乙烯醚双甲基丙烯酸酯ebpdma,双甲基丙烯酸氨基甲酸酯udma中的两种,质量比为1-6:1。
12.所述光引发剂由樟脑醌cq和4-二甲氨基苯甲酸乙酯4-edmab组成,质量比为1:4-6。
13.本发明还提供了一种多级填料构筑齿科复合树脂的制备方法,包括如下步骤:
14.(1)多孔sio2填料的制备:通过将醇、环己烷和正硅酸四乙酯teos搅拌成混合溶液,随后加入表面活性剂、尿素和水的混合溶液,水热反应,并经自然冷却,离心洗涤,煅烧制得;
15.(2)硅烷化无孔sio2填料的制备:首先在乙醇、氢氧化铵和水搅拌混合溶液中加入正硅酸四乙酯teos,经过油浴条件下搅拌回流,冷却、离心洗涤,真空干燥后制得无孔sio2;再将无孔sio2分散至环己烷中,随后加入正丙胺和γ-mps的混合溶液,室温搅拌,最后冷却,离心洗涤,真空干燥制得;
16.(3)多级填料的构筑:选用等粒径的多孔sio2填料和硅烷化无孔sio2填料复合作为初级填料,然后借助等球体紧密堆积模型理论计算初级填料正四面体空隙和正八面体空隙中充填不同粒径的硅烷化无孔sio2填料(二级填料)的最大尺寸,得到多级填料;
17.(4)齿科复合树脂的制备:将上述多级填料、树脂基体和光引发剂混合均匀,得到未固化复合树脂膏,经过光固化,得到多级填料构筑齿科复合树脂。
18.所述步骤(1)中的醇为乙醇、异丙醇、正戊醇、正丁醇、正己醇、正庚醇中的一种;表面活性剂为十六烷基三甲基溴化铵ctab或聚氧乙烯聚氧丙烯醚嵌段共聚物f127。
19.所述步骤(1)中的醇、环己烷和正硅酸四乙酯teos的体积比为1:10-30:1-10;表面活性剂、尿素和水的质量比为1:0.1-0.5:10-30。两种混合溶液之间的体积比为1.1-1.4:1。
20.所述步骤(1)中的水热反应的工艺参数为:在聚四氟乙烯高温高压水热釜中,80-250℃反应2-7h;煅烧的工艺参数为:煅烧温度为420-680℃,煅烧时间为4-10h。
21.所述步骤(2)中的乙醇、氢氧化铵和水的体积比为3-20:2-10:1;环己烷、正丙胺和γ-mps的体积比为100-150:0.1-2:0.3-1.5;无孔sio2与环己烷的质量体积比为1-10g:100-150ml。
22.所述步骤(2)中的油浴反应的工艺参数为:在50-80℃油浴锅中反应1-3h;真空干燥的工艺参数为:干燥温度为70-120℃,干燥时间为8-14h。
23.所述步骤(3)中初级填料的粒径均为200-550nm;充填的硅烷化无孔sio2二级填料
的粒径为60-190nm。硅烷化后的无孔sio2填料和树脂基体之间的界面结合效果更佳。
24.所述步骤(1)、(2)中冷却的方式为自然冷却;离心洗涤的工艺条件为:用乙醇、丙酮或去离子水离心洗涤。
25.所述步骤(3)中多级填料的初级填料和二级填料质量比为1-4:1。
26.所述步骤(4)中光固化的工艺条件为:将未固化的复合树脂膏填入硅橡胶模具内并使用led灯固化10-230s,脱模后即可得到复合树脂样条。随后将样条室温避光储存2~3天,测试前用碳化硅砂纸打磨样品表面以除去树脂表面未完全固化层。
27.有益效果
28.(1)本发明制备的多级填料构筑齿科复合树脂,制备方法简单,反应条件温和,且多级填料与树脂基体混合效果好,相比于树枝状多孔sio2单独做无机填料,其填料填充量得到明显提高,可应用于齿科复合修复树脂领域;
29.(2)本发明制备的多级填料构筑齿科复合树脂,与传统的齿科修复复合树脂相比,通过调整多孔sio2和硅烷化无孔sio2的添加比例,复合树脂的力学性能得到进一步改善,同时表现出较低的聚合收缩率;同时由于采用不同粒径的sio2无机填料相互结合方式,大大增加了复合树脂无机填料的填充量,降低了复合树脂单体的质量分数,从而使复合树脂的制作成本大幅度下降。
附图说明
30.图1为实施例1得到的树枝状多孔sio2粒子的sem图;
31.图2为实施例1得到的硅烷化无孔sio2粒子的sem图;
32.图3为实施例1-3得到的复合树脂以及对比例1的弯曲强度;
33.图4为实施例1-3得到的复合树脂以及对比例1的压缩强度;
34.图5为实施例1-3得到的复合树脂以及对比例1的聚合收缩率;
35.图6为实施例1-3得到的复合树脂以及对比例1的最大填充量。
具体实施方式
36.下面结合具体实施例,进一步阐述本发明。应理解,这些实施例仅用于说明本发明而不用于限制本发明的范围。此外应理解,在阅读了本发明讲授的内容之后,本领域技术人员可以对本发明作各种改动或修改,这些等价形式同样落于本技术所附权利要求书所限定的范围。
37.实施例1
38.(1)树枝状多孔sio2颗粒的制备
39.将1.5ml戊醇、30ml环己烷和2.5mlteos混合并搅拌成混合溶液,随后向上述混合溶液里加入1.8g ctab、1g尿素和30g水的混合溶液。上述搅拌均匀的混合液倒入聚四氟乙烯高温高压水热釜中,130℃反应4h,反应结束后自然冷却至室温,离心、丙酮和去离子水洗涤之后550℃煅烧6h,得到粒径大小为500nm的树枝状多孔sio2粒子,sem结果如图1所示,通过sem图像得出,该sio2粒子具有均一的粒径大小,且该粒子表面具有分布均匀的孔结构。
40.(2)硅烷化无孔sio2粒子的制备
41.将460ml乙醇、320ml氢氧化铵和70ml去离子水混合并搅拌成混合溶液,随后加入
40ml正硅酸乙酯,在60℃油浴条件下回流搅拌2h并冷却至室温。用无水乙醇和去离子水离心洗涤,在110℃条件下真空干燥12h后,将其超声分散在100ml环己烷中,然后加入0.14ml丙胺和0.53mlγ-mps,先室温下搅拌30min,然后在60℃下搅拌1h。反应结束后自然冷却至室温,用环己烷和去离子水离心洗涤,在真空烘箱中80℃干燥12h得到粒径大小为500nm硅烷化无孔sio2粒子,sem结果如图2所示,通过sem图像得出,该sio2粒子具有均一粒径大小,且该粒子为无孔球型结构。按照上述反应顺序和条件,将乙醇、氢氧化铵、去离子水、teos试剂用量分别改为780ml、40ml、70ml和40ml,其余试剂用量不变,最终得到粒径为190nm的硅烷化无孔sio2粒子。
42.(3)“多孔+无孔”多级填料的构筑
43.选用粒径均为500nm的树枝状多孔sio2和硅烷化无孔sio2复合做初级填料,其质量比为3:7,后借助等球体紧密堆积模型理论计算初级填料正四面体空隙和正八面体空隙最大尺寸,选用粒径为190nm的硅烷化无孔sio2做二级填料,得到“多孔+无孔”多级填料。
44.(4)复合树脂的制备
45.按照表1所示配方,首先采用手工预混的方式,将上述粒径均为500nm的树枝状多孔sio2和硅烷化无孔sio2、有机单体和光引发剂体系混合,待无机填料充分被树脂基体润湿时,放入三辊研磨机(exakt 80e,德国)二次混合,经真空负压处理后,得到未固化复合树脂膏。随后经过可见光固化(波长为430-490nm),得到齿科复合树脂。
46.表1复合树脂的组分及各组分的含量
[0047][0048]
(5)复合树脂的表征
[0049]
参照国际标准《iso 4049-2009》,利用万能试验机(instron 5900,美国)测试该复合树脂的弯曲强度和压缩强度分别为105.9
±
8.0mpa和389.5
±
35.1mpa;根据阿基米德原理,用密度天平(ml 204,switzerland)测试修复树脂固化前后的密度,通过计算得出该复合树脂的聚合收缩率为5.5
±
0.5%;采用手工预混的方式,利用三辊研磨机(exakt 80e,德国)将无机填料、有机基体和光引发剂均匀混合,利用分析天平(al204)称量并通过计算得填料最大填充量为65.0
±
1.0wt%。
[0050]
实施例2
[0051]
(1)树枝状多孔sio2粒子的制备
[0052]
将1.5ml戊醇、30ml环己烷和2.5mlteos混合并搅拌成混合溶液,随后向上述混合溶液里加入1.8gctab、1g尿素和30g水的混合溶液。上述搅拌均匀的混合液倒入聚四氟乙烯高温高压水热釜中,130℃反应4h,反应结束后自然冷却至室温,离心、丙酮和去离子水洗涤之后550℃煅烧6h,得到粒径大小为500nm的树枝状多孔sio2粒子。
[0053]
(2)硅烷化无孔sio2粒子的制备
[0054]
将460ml乙醇、320ml氢氧化铵和70ml去离子水混合并搅拌成混合溶液,随后加入40ml正硅酸乙酯,在60℃油浴条件下回流搅拌2h并冷却至室温。用无水乙醇和去离子水离心洗涤,在110℃条件下真空干燥12h后,将其超声分散在100ml环己烷中,然后加入0.14ml丙胺和0.53mlγ-mps,先室温下搅拌30min,然后在60℃下搅拌1h。反应结束后自然冷却至室温,用环己烷和去离子水离心洗涤,在真空烘箱中80℃干燥12h得到粒径大小为500nm硅烷化无孔sio2粒子。按照上述反应顺序和条件,将乙醇、氢氧化铵、去离子水、teos试剂用量分别改为400ml、30ml、10ml和90ml,其余试剂用量不变,最终得到粒径为60nm的硅烷化无孔sio2粒子。
[0055]
(3)“多孔+无孔”多级填料的构筑
[0056]
选用粒径均为500nm的树枝状多孔sio2和硅烷化无孔sio
20
复合做初级填料,其质量比为3:7,后借助等球体紧密堆积模型理论计算初级填料正四面体空隙和正八面体空隙,选用粒径为60nm的硅烷化无孔sio2做二级填料,得到“多孔+无孔”多级填料。
[0057]
(4)复合树脂的制备
[0058]
按照表2所示配方,首先采用手工预混的方式,将上述粒径均为500nm的树枝状多孔sio2和硅烷化无孔sio2、有机单体和光引发剂体系混合,待无机填料充分被树脂基体润湿时,放入三辊研磨机(exakt 80e,德国)二次混合,经真空负压处理后,得到未固化复合树脂膏。随后经过可见光固化(波长为430-490nm),得到齿科复合树脂。
[0059]
表2复合树脂的组分及各组分的含量
[0060][0061]
(5)复合树脂的表征
[0062]
参照国际标准《iso 4049-2009》,利用万能试验机(instron 5900,美国)测试该复合树脂的弯曲强度和压缩强度分别为128.8
±
8.6mpa和366.6
±
12.3mpa;根据阿基米德原理,用密度天平(ml 204,switzerland)测试修复树脂固化前后的密度,通过计算得出该复
合树脂的聚合收缩率为4.6
±
0.8%;采用手工预混的方式,利用三辊研磨机(exakt 80e,德国)将无机填料、有机基体和光引发剂均匀混合,利用分析天平(al204)称量并通过计算得填料最大填充量为69.0
±
2.0wt%。
[0063]
实施例3
[0064]
(1)树枝状多孔sio2颗粒的制备
[0065]
将1.5ml戊醇、30ml环己烷和2.5ml teos混合并搅拌成混合溶液,随后向上述混合溶液里加入1.8g ctab、1g尿素和30g水的混合溶液。上述搅拌均匀的混合液倒入聚四氟乙烯高温高压水热釜中,130℃反应4h,反应结束后自然冷却至室温,离心、丙酮和去离子水洗涤之后550℃煅烧6h,得到粒径大小为500nm的树枝状多孔sio2粒子。
[0066]
(2)硅烷化无孔sio2粒子的制备
[0067]
将460ml乙醇、320ml氢氧化铵和70ml去离子水混合并搅拌成混合溶液,随后加入40ml正硅酸乙酯,在60℃油浴条件下回流搅拌2h并冷却至室温。用无水乙醇和去离子水离心洗涤,在110℃条件下真空干燥12h后,将其超声分散在100ml环己烷中,然后加入0.14ml丙胺和0.53mlγ-mps,先室温下搅拌30min,然后在60℃下搅拌1h。反应结束后自然冷却至室温,用环己烷和去离子水离心洗涤,在真空烘箱中80℃干燥12h得到粒径大小为500nm硅烷化无孔sio2粒子。依据实施例1-2,通过改变乙醇、氢氧化铵、去离子水、teos试剂用量,分别合成粒径为60nm和190nm的硅烷化无孔sio2。
[0068]
(3)“多孔+无孔”多级填料的构筑
[0069]
选用粒径均为500nm的树枝状多孔sio2和硅烷化无孔sio2复合做初级填料,其质量比为3:7,后借助等球体紧密堆积模型理论计算初级填料正四面体空隙和正八面体空隙,选用粒径为60nm和190nm的硅烷化无孔sio2做二级填料,得到“多孔+无孔”多级填料。
[0070]
(4)复合树脂的制备
[0071]
按照表3所示配方,首先采用手工预混的方式,将上述粒径均为500nm的树枝状多孔sio2和硅烷化无孔sio2、有机单体和光引发剂体系混合,待无机填料充分被树脂基体润湿时,放入三辊研磨机(exakt 80e,德国)二次混合,经真空负压处理后,得到未固化复合树脂膏。随后经过可见光固化(波长为430-490nm),得到齿科复合树脂。
[0072]
表3复合树脂的组分及各组分的含量
[0073][0074]
(5)复合树脂的表征
[0075]
参照国际标准《iso 4049-2009》,利用万能试验机(instron 5900,美国)测试该复合树脂的弯曲强度和压缩强度分别为153.2
±
9.2mpa和430.8
±
17.4mpa;根据阿基米德原理,用密度天平(ml 204,switzerland)测试修复树脂固化前后的密度,通过计算得出该复合树脂的聚合收缩率为2.6
±
0.4%;采用手工预混的方式,利用三辊研磨机(exakt 80e,德国)将无机填料、有机基体和光引发剂均匀混合,利用分析天平(al204)称量并通过计算得填料最大填充量为75.0
±
2.0wt%。
[0076]
对比例1
[0077]
按照实施例1制备粒径大小为500nm树枝状多孔sio2无机填料,并按照表4所示配方制备齿科修复复合树脂。首先采用手工预混的方式,将上述树枝状多孔sio2颗粒、有机单体和光引发剂体系混合,待无机填料充分被树脂基体润湿时,放入三辊研磨机(exakt 80e,德国)二次混合,经真空负压处理后,得到未固化复合树脂膏。随后经过可见光固化,得到齿科复合树脂,作为对照组1。
[0078]
表4复合树脂的组分及各组分的含量
[0079][0080]
本对比例与实施例1-3制得的复合树脂的填料最大填充量、弯曲强度、压缩强度、聚合收缩率结果分别如图3-6所示,可知与树枝状多孔sio2无机填料单独填充复合树脂(对照组1)相对比,本发明“多孔+无孔”多级填料构筑齿科复合树脂填料最大填充量和力学性
能均高于对照组1,聚合收缩率均低于对照组1,即本发明构筑的“多孔+无孔”多级填料有利于提高齿科复合树脂的填料填充量、力学性能,并降低其聚合收缩率。
[0081]
对比例2
[0082]
按照实施例1制备粒径大小为500nm硅烷化无孔sio2无机填料,并按照表5所示配方制备齿科修复复合树脂。首先采用手工预混的方式,将上述树枝状多孔sio2颗粒、有机单体和光引发剂体系混合,待无机填料充分被树脂基体润湿时,放入三辊研磨机(exakt 80e,德国)二次混合,经真空负压处理后,得到未固化复合树脂膏。随后经过可见光固化,得到齿科复合树脂,作为对照组1。
[0083]
表5复合树脂的组分及各组分的含量
[0084][0085]
本对比例与实施例1-3制得的复合树脂的填料最大填充量、弯曲强度、压缩强度、聚合收缩率结果分别如图3-6所示,可知与硅烷化无孔sio2无机填料单独填充复合树脂(对照组2)相对比,本发明“多孔+无孔”多级填料构筑齿科复合树脂填料最大填充量和力学性能均高于对照组2,聚合收缩率均低于对照组2,即本发明构筑的“多孔+无孔”多级填料有利于提高齿科复合树脂的填料填充量、力学性能,并降低其聚合收缩率。