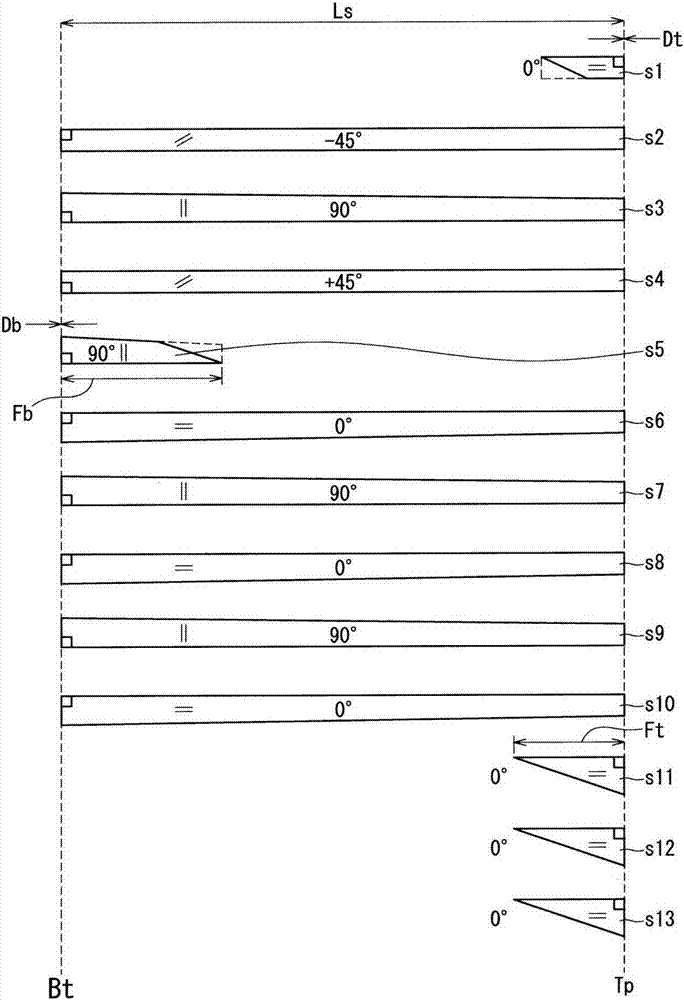
本发明涉及高尔夫球杆。
背景技术:
:提出有考虑重心的位置的高尔夫球杆身。日本特开2012-239574号公报公开了一种杆身重心率为0.52以上0.65以下的杆身。并且,提出有考虑弯曲刚性的分布的高尔夫球杆身。日本特许第5824594号公开了一种杆身,该杆身的ei分布的曲线图具有特定的形状。现有技术文献专利文献专利文献1:日本特开2012-239574号公报专利文献2:日本特许第5824594号公报发明所要解决的课题上述以往的技术对提高杆头速度是有效的。但另一方面,高尔夫球手的要求日益升级。杆身的轻量化是在杆头速度的提高中有效的手段。但是,由于该轻量化,材料的使用量减少,因此设计自由度降低。进行用于一边确保强度一边提高杆头速度的最适合的设计并非是容易的。技术实现要素:本发明的目的在于提供一种高尔夫球杆,该高尔夫球杆所具有的杆身有提高杆头速度的特性,且飞行距离性能优秀。用于解决课题的手段优选的高尔夫球杆具备:杆身,该杆身具有尖端以及柄端;杆头;以及握柄,其中,所述杆身具有多个碳素纤维强化层,所述碳素纤维强化层具有平直层、倾斜层、以及环圈层,当将所述环圈层的重量设为wf,将杆身重量设为ws时,wf/ws为0.18以上,所述杆身重量ws为42g以下。在所述杆身中,将从所述柄端起200mm的地点设为p1,将从该地点p1到所述柄端的区域设为特定球杆柄区域,将所述特定球杆柄区域中的所述环圈层的重量设为wfb,将所述特定球杆柄区域中的杆身重量设为wsb。优选的是,wfb/wsb为0.30以上。优选的是,所述特定球杆柄区域包含3圈以上的所述环圈层。优选的是,所述地点p1处的所述杆身的内径为14.0mm以上。将所述平直层的重量设为wt。优选的是,wf/wt为0.25以上。在所述杆身中,将从所述尖端起830mm的地点处的ei值设为e8,将从所述尖端起930mm的地点处的ei值设为e9,将从所述尖端起1030mm的地点处的ei值设为e10。在本申请中,将所述三个ei值绘制于x轴为从尖端到测定点的距离(mm)并且y轴为所述ei值(kgf·m2)的xy坐标平面中的曲线图被考虑。在该曲线图中,用最小二乘法将这三个点拟合为一次式,并将该一次式的斜率设为m3。优选的是,斜率m3为0.0100以下。在所述杆身中,将从所述尖端起1030mm的地点处的ei值设为e10。优选的是,所述e10为5.0kgf·m2以下。将从所述杆身的尖端到杆身重心的距离设为lg,将所述杆身的长度设为ls。优选的是,lg/ls为0.50以上。发明效果能够得到飞行距离性能优秀的高尔夫球杆。附图说明图1表示具备第一实施方式的杆身的高尔夫球杆。图2是第一实施方式(以及实施例一)的杆身的展开图。图3是第二实施方式(以及实施例二)的杆身的展开图。图4是第三实施方式(以及实施例三)的杆身的展开图。图5是参考例一(以及比较例一)的杆身的展开图。图6是参考例二(以及比较例二)的杆身的展开图。图7是用于说明ei值的测定方法的概况图。图8是绘制有实施例一的从e1到e10的曲线图。图9是表示三点弯曲强度的测定方法的概况图。符号说明2高尔夫球杆4杆头6杆身8握柄ls杆身的长度lg从尖端tp到重心g的距离s1~s13预成型料片材(层)s5(图2)球杆柄部分环圈片材s3、s7、s9(图2)全长环圈片材tp杆身的尖端bt杆身的柄端g杆身的重心具体实施方式以下,一边参照适当的附图一边基于优选的实施方式来对本发明进行详细地说明。另外,在本申请中使用了“层”、“片材”这样的文字。“层”是被卷绕后的称呼,与此相对,“片材”是被卷绕前的称呼。通过卷绕“片材”而形成“层”。即,卷绕后的“片材”形成“层”。本申请的轴向是指杆身的轴向。本申请的周向是指杆身的周向。图1表示本发明的一实施方式所涉及的高尔夫球杆2。高尔夫球杆2具备:杆头4、杆身6、以及握柄8。在杆身6的尖端部分设置有杆头4。在杆身6的球杆柄部分设置有握柄8。杆身6是木杆用杆身。另外,杆头4以及握柄8不被限定。作为杆头4,例示有木型高尔夫球杆头、铁型高尔夫球杆头、推杆杆头等。本实施方式的杆头4是木型高尔夫球杆头。杆身6由多个纤维强化树脂层形成。杆身6是管状体。虽然未图示,但杆身6具有中空结构。如图1所示,杆身6具有尖端tp和柄端bt。在高尔夫球杆2中,尖端tp位于杆头4的内部。在高尔夫球杆2中,柄端bt位于握柄8的内部。图1中双箭头lg所表示的是从尖端tp到杆身重心g的距离。该距离lg沿轴向测定。图1中双箭头ls所表示的是杆身6的长度。在本申请中,lg/ls也称为杆身重心率。即使使杆头重量增加,通过增大杆身重心率也能确保易挥性。因此,杆头速度能够提高,飞行距离能够增大。从该观点来看,lg/ls优选0.50以上,进一步优选0.51以上,更进一步优选0.52以上。当考虑前端部的强度时,lg/ls优选0.61以下,进一步优选0.60以下。杆身6通过卷绕多个预成型料片材而形成。在这些预成型料片材中,纤维实质上取向在一个方向上。像这样的纤维实质上取向在一个方向上的预成型料,也称为ud预成型料,“ud”是unidirection(单向)(日语:ユ二ディレクション)的缩写。另外,也可以使用ud预成型料以外的预成型料。例如,在预成型料片材中,也可以将纤维编织。预成型料片材具有纤维和树脂。该树脂也称为基体树脂。作为该纤维,例示有碳素纤维以及玻璃纤维。典型的是该基体树脂为热硬化性树脂。作为预成型料片材的基体树脂,例示有热硬化性树脂以及热可塑性树脂。从杆身强度的观点来看,优选环氧树脂作为基体树脂。杆身6通过所谓的片材卷绕制造法制造。在预成型料中,基体树脂处于半硬化状态。在杆身6中,预成型料片材被卷绕并且被硬化。该硬化是指半硬化状态的基体树脂硬化。该硬化通过加热而达成。在杆身6的制造工序中包含加热工序。该加热使预成型料片材的基体树脂硬化。图2是构成杆身6的预成型料片材的展开图。图2表示构成杆身6的片材。杆身6由多个片材构成。在图2的实施方式中,杆身6由13张片材构成。杆身6具有从第一片材s1到第十三片材s13的片材。该展开图依照从杆身的半径方向内侧的顺序展示构成杆身的片材。从图2中位于上侧的片材开始依次卷绕。在图2中,图的左右方向与轴向一致。在图2中,图的右侧是杆身的尖端侧。在图2中,图的左侧是杆身的球杆柄侧。图2不仅表示卷绕的顺序,也表示轴向上的配置。例如在图2中,片材s1的一端位于尖端tp。杆身6具有平直层和倾斜层。在图2中,记载有纤维的取向角度。记载为“0°”的片材是平直片材。平直片材构成平直层。平直层是将纤维的取向相对于轴向设为实质上为0°的层。由于卷绕时的误差等原因,通常,纤维的取向相对于杆身轴线方向不完全平行。在平直层中,相对于杆身轴线的纤维的绝对角度θa为10°以下。绝对角度θa是杆身轴线与纤维方向所成角度的绝对值。即,绝对角度θa为10°以下是指纤维方向与杆身轴线方向所成的角度af为-10度以上+10度以下。在图2的第一实施方式中,平直片材是片材s1、片材s6、片材s8、片材s10、片材s11、片材s12以及片材s13。平直层有助于弯曲刚性以及弯曲强度的提高。倾斜层能够提高杆身的扭转刚性以及扭转强度。优选的是,倾斜层具有纤维的取向彼此向反方向倾斜的两张片材对。优选的是,该片材对包含所述角度af为-60°以上-30°以下的层和所述角度af为30°以上60°以下的层。即,优选的是,在倾斜层中,所述绝对角度θa为30°以上60°以下。在杆身6中,构成倾斜层的片材是片材s2以及片材s4。在图2中的每个片材上记载有所述角度af。角度af的加(+)以及减(-)表示互相贴合的倾斜片材的纤维向彼此相反方向倾斜。在本申请中,倾斜层用的片材也称为倾斜片材。环圈层是纤维沿杆身的周向配置的层。优选的是,在环圈层中,所述绝对角度θa被设为相对于杆身轴线实质上为90°。但是,有由于卷绕时的误差等引起的纤维的取向相对于杆身轴线方向不完全为90°的情况。通常,在该环圈层中,所述绝对角度θa为80°以上。该绝对角度θa的上限值为90°。即,环圈层的绝对角度θa为90°以下。环圈层有助于提高杆身的压溃刚性以及压溃强度。压溃刚性是指相对于压溃变形的刚性。压溃变形由将杆身向杆身的半径方向内侧压溃的力产生。在典型的压溃变形中,杆身剖面从圆形变为椭圆形。压溃强度是对抗压溃变形的强度。压溃强度也能与弯曲强度产生关联。此外,能够与弯曲变形联动而产生压溃变形。特别是在壁厚较薄的轻量杆身中,该联动性较大。压溃强度的提高有助于弯曲强度的提高。在图2的实施方式中,环圈层用的预成型料片材是片材s3、片材s5、片材s7、以及片材s9。环圈层用的预成型料片材也称为环圈片材。杆身6具有夹于倾斜层s2、s4的环圈层s3。在图2的实施方式中,使用拼合体片材。拼合体片材通过贴合多个片材而形成。在图2的实施方式中,形成四组拼合体片材。第一拼合体片材是片材s2与片材s3以及片材s4的组合。第二拼合体片材是片材s5与片材s6的组合。第三拼合体片材是片材s7与片材s8的组合。第四拼合体片材是片材s9与片材s10的组合。如上所述,在本申请中,片材以及层根据纤维的取向角度来分类。此外,在本申请中,片材以及层也根据轴向的长度来分类。在轴向的整体上配置的层称为全长层。在轴向的整体上配置片材称为全长片材。卷绕后的全长片材形成全长层。并且,在轴向上部分地配置的层称为部分层。在轴向上部分地配置的片材称为部分片材。卷绕后的部分片材形成部分层。全长层中的倾斜层称为全长倾斜层。在本申请中,全长层中的平直层称为全长平直层。在本申请中,全长层中的环圈层称为全长环圈层。在本申请中,部分层中的平直层称为部分平直层。在以下,对该杆身6的制造工序的概况进行说明。[杆身制造工序的概况](1)裁剪工序在裁剪工序中,将预成型料片材裁剪成所希望的形状。通过该工序而切割出图2所示的各片材。此外,裁剪可以通过裁剪机完成,也可以通过手工作业完成。在手工作业的情况下,例如,使用切割刀。(2)贴合工序在该工序中,多个片材被贴合,从而制作出所述拼合体片材。在贴合工序中,也可以使用加热或加压。(3)卷绕工序在卷绕工序中,准备心轴。典型的心轴是金属制。在该心轴上涂布有脱模剂。此外,在该心轴上还涂布有具有粘接性的树脂。该树脂也称为粘性树脂(tackifyingresin)。将裁剪后的片材卷绕于该心轴。该粘性树脂使向心轴贴合片材端部变得容易。通过该卷绕工序而得到卷绕体。在该卷绕体中,在心轴的外侧卷绕有预成型料片材。该卷绕是通过例如在平面上使卷绕对象物滚动而进行的。该卷绕可以通过手工作业来进行,也可以通过机器来进行。该机器称为滚动机。(4)绕带工序在绕带工序中,将带卷绕于所述卷绕体的外周面。该带也称为缠绕带。该缠绕带被赋予张力地卷绕。通过该缠绕带而将压力施加于卷绕体。该压力有助于减小空隙。(5)硬化工序在硬化工序中,完成绕带工序后的卷绕体被加热。由于该加热而引起基体树脂硬化。在该硬化过程中,基体树脂暂时变为流动化。通过该基体树脂的流动化,能够排出片材间或片材内的空气。缠绕带的紧固力促进该空气的排出。该硬化的结果是得到硬化层叠体。(6)心轴的拔出工序以及缠绕带的去除工序在硬化工序后,进行心轴的拔出工序与缠绕带的去除工序。优选的是,在心轴的拔出工序后进行缠绕带的去除工序。(7)两端切除工序在该工序中,切除硬化层叠体的两端部。该切断使尖端tp的端面以及柄端bt的端面平坦化。(8)研磨工序在该工序中,研磨硬化层叠体的表面。在硬化层叠体的表面残留有作为缠绕带的痕迹的螺旋状的凹凸。通过研磨来消除该凹凸并使表面变得平滑。(9)涂装工序在研磨工序后的硬化层叠体上进行涂装。在本申请中,层与片材使用相同的符号。例如,由片材s1形成的层是层s1。在杆身6中,全长片材是片材s2、片材s3、片材s4、片材s6、片材s7、片材s8、片材s9、以及片材s10。片材s2以及片材s4是全长倾斜片材。片材s6、片材s8、及片材s10是全长平直片材。片材s3、片材s7、以及片材s9是全长环圈片材。在杆身6中,部分片材是片材s1、片材s5、片材s11、片材s12,以及片材s13。片材s1、片材s11、片材s12、以及片材s13是尖端部分片材。片材s5是球杆柄部分片材。图2中由双箭头dt所表示的是尖端部分片材与尖端tp的距离。距离dt沿轴向测定。在击球时,应力容易集中于杆颈部的端面附近。从该观点来看,距离dt优选20mm以下。进一步优选的是,距离dt为10mm以下。距离dt也可以为0mm。在本实施方式中,距离dt为0mm。图2中由双箭头ft所表示的是尖端部分片材的长度(全长)。该长度ft沿轴向测定。在击球时,应力容易集中于杆颈部的端面附近。从该观点来看,长度ft优选50mm以上,进一步优选100mm以上,更进一步优选150mm以上。从杆身的重心位置的观点来看,长度ft优选400mm以下,进一步优选350mm以下,更进一步优选300mm以下。图2中由双箭头db所表示的是球杆柄部分片材与柄端bt的距离。距离db沿轴向测定。从杆身的重心位置的观点来看,距离db优选100mm以下。距离db进一步优选70mm以下,更进一步优选50mm以下。距离db也可以是0mm。在本实施方式中,距离db为0mm。图2中由双箭头fb所表示的是球杆柄部分片材的长度(全长)。该长度fb沿轴向测定。从杆身的重心位置的观点来看,球杆柄部分片材的重量优选较大的重量。从该观点来看,长度fb优选250mm以上,进一步优选300mm以上,更进一步优选350mm以上。过大的长度fb使移动杆身的重心位置的效果降低。从该观点来看,长度fb优选650mm以下,进一步优选600mm以下,更进一步优选580mm以下,更优选560mm以下。在图2的实施方式中,具有一张球杆柄部分片材。也可以设置有多张(两张以上)球杆柄部分片材。球杆柄部分片材s5是环圈片材。球杆柄部分片材s5的距离db为0mm。球杆柄部分片材s5配置于全长倾斜片材s2、s4的外侧。在球杆柄部分片材s5的外侧,至少设置有一张全长平直片材。片材s1是平直尖端部分片材。该片材s1配置于全长倾斜片材s2、s4的内侧。片材s11是平直尖端部分片材。该片材s11配置于最外侧的全长平直层s10的外侧。片材s12是平直尖端部分片材。片材s12配置于片材s11的外侧。片材s13配置于片材s12的外侧。在本实施方式中,使用玻璃纤维强化预成型料。在本实施方式中,玻璃纤维实质上取向在一个方向上。即该玻璃纤维强化预成型料是ud预成型料。也可以使用ud预成型料以外的玻璃纤维强化预成型料。例如,也可以将玻璃纤维编织。在本实施方式中,片材s1是玻璃纤维强化片材。在本实施方式中,纤维强化片材s1配置于倾斜层s2、s4的内侧。玻璃纤维强化预成型料以外的预成型料是碳素纤维强化预成型料。片材s1以外的片材是碳素纤维强化片材。另外,作为碳素纤维,例示有pan系以及沥青系。玻璃纤维的压缩断裂应变较大。该玻璃纤维有利于冲击吸收能量的提高。通过使尖端部分层由玻璃纤维强化层形成,而提高杆身前端部相对于击球的冲击的强度。作为用于低弹性层的纤维,除玻璃纤维外,还例示有低弹性碳素纤维。优选的低弹性碳素纤维是沥青系碳素纤维。通过增加球杆柄部分的重量,能够增大杆身重心率。但是,当球杆柄部分的重量增加时,球杆柄部分的弯曲刚性容易变得过大。在该情况下,球杆柄部分难以弯曲,曲腕近似效果(后述)减少。通过使球杆柄部分层由环圈层形成,能够提高杆身重心率并抑制球杆柄部分的弯曲刚性。在该杆身6中,通过杆身重心率与曲腕近似效果(后述)的相乘效果来增大杆头速度。[夹层结构]图2的层叠结构具有第一环圈层s3、第二环圈层s5、第三环圈层s7以及第四环圈层s9。第二环圈层s5相比于第一环圈层s3位于外侧。在第一环圈层s3与第二环圈层s5之间存在中间层。该中间层是除环圈层以外的层(倾斜层)。第三环圈层s7(全长环圈层)相比于第二环圈层s5(球杆柄部分环圈层)位于外侧。在第二环圈层s5(球杆柄部分环圈层)与第三环圈层s7(全长环圈层)之间,存在中间层。该中间层是环圈层以外的层(平直层)。第四环圈层s9(全长环圈层)相比于第三环圈层s7(全长环圈层)位于外侧。在第三环圈层s7(全长环圈层)与第四环圈层s9(全长环圈层)之间,存在中间层。该中间层是环圈层以外的层(全长平直层)。在本申请中,在两个环圈层间存在中间层的结构也称为夹层结构。图2的层叠结构具有多个夹层结构。在杆身的变形中,由于挠曲变形而导致压溃变形。在该压溃变形中,杆身剖面形状的曲率根据周向位置而变化。即,在根据压溃变形而变成椭圆形状的情况下,曲率小的部分与曲率大的部分混在一起。由于环圈层的纤维沿周向取向,环圈层难以追随该曲率的变化。另一方面,由于平直层以及倾斜层的纤维没有沿周向取向,平直层以及倾斜层容易追随所述曲率的变化。因此,在环圈层重叠的情况下,由于该环圈层间的半径方向位置的不同而导致容易产生层间剥离。另一方面,在将平直层或倾斜层与环圈层重叠的情况下,层间剥离比较不容易发生。从这些观点来看,优选两层环圈层不重叠。优选多层环圈层全部不相互重叠。在环圈层之间,优选夹有环圈层以外的层。在全部多层环圈层中的环圈层彼此之间,优选夹有环圈层以外的层。在环圈层之间,优选夹有平直层以及/或者倾斜层。即,优选所述夹层结构。该夹层结构提高弯曲强度。从轻量化的观点来看,平均每一层的环圈层的厚度优选0.05mm以下。从提高环圈层的效果的观点来看,平均每一层的环圈层的厚度优选0.02mm以上。环圈层s3、环圈层s7以及环圈层s9是全长层。因此,夹层结构的效果遍及杆身的全长奏效,杆身整体的强度被提高。图3是表示第二实施方式的层叠结构的展开图。图3与图2的不同点在于,不存在夹于倾斜层的全长环圈层,代替于此而配置有全长平直层s4。图4是表示第三实施方式的层叠结构的展开图。当与图2的实施方式相比较时,在该第三实施方式中,没有环圈层s9,代替于此而配置有全长平直层s9。图5是表示参考例一的层叠结构的展开图。当与图2的实施方式相比较时,在该参考例一中,没有全长环圈层s3。此外,在参考例一中,代替全长环圈层s7而配置有全长平直层s6。该参考例一的层叠结构也可以成为实施例。图6是表示参考例二的层叠结构的展开图。但与图2的实施方式相比较时,在该参考例二中,没有全长环圈层s3。此外,在参考例二中,代替图2的实施方式中的全长环圈层s7、s9而配置有全长平直层s6、s8。在本申请中,将环圈层的重量设为wf(g)。并且,将杆身重量设为ws(g)。优选的是考虑wf/ws。在本申请中,将离柄端bt起200mm的地点设为p1(图1参照)。将从该地点p1到所述柄端的区域设为特定球杆柄区域rb。将特定球杆柄区域rb中的环圈层的重量设为wfb(g)。将特定球杆柄区域rb中的杆身重量设为wsb(g)。为了测定wsb,可以测定在地点p1切断杆身6而得到的部件的重量。优选的是考虑wfb/wsb。如上所述,从压溃刚性的观点来看,使用环圈层。环圈层本身是公知的。环圈层有助于杆身的强度也是公知的。但是,环圈层是将纤维相对于杆身轴向配置为直角的层,因此环圈层被认为不直接地有助于弯曲强度。若考虑纤维的取向,则认为对弯曲强度的贡献大的显然应当是平直层,并认为环圈层不过是起到辅助的作用。在杆身重量ws为42g以下的超轻量杆身中,预成型料的使用量被限定。因此,对弯曲强度的贡献大的平直层的重量wt被限定,弯曲强度容易降低。在该轻量杆身中,作为本领域技术人员的技术常识,若使环圈层过多,则平直层的重量wt被进一步限制,弯曲强度降低。然而,本发明的发明人认真研究的结果是,发现在42g以下的超轻量杆身中,通过被认为是过剩的量的环圈层,能够提高弯曲强度。具体而言,了解到将wf/ws设为0.18以上是有效的。过去认为,在具有全长倾斜层以及全长平直层并且通过尖端部分层来进行增强的超轻量杆身中,分配于环圈层的重量是被限定的。但是,现在了解到18重量%以上的环圈层使弯曲强度提高。从这样的观点来看,wf/ws优选0.18以上,进一步0.19以上,更进一步优选0.20以上,更优选0.21以上。从防止平直层的重量wt变得过小的观点来看,wf/ws优选0.40以下,进一步优选0.38以下,更进一步优选0.35以下。从提高杆身的整体的弯曲强度的观点来看,全长环圈层的圈数优选2圈以上,进一步优选3圈以上。从防止平直层的重量wt变得过小的观点来看,全长环圈层的圈数优选5圈以下,进一步优选4圈以下。了解到特定球杆柄区域rb中的环圈层能够进一步增加。从纤维的取向可知,环圈层对弯曲刚性的贡献几乎没有。因此,通过将多个环圈层配置于杆身的球杆柄部分,能够抑制球杆柄部分的弯曲刚性,并能够使球杆柄部分的强度提高。通过抑制球杆柄部分的弯曲刚性,曲腕近似效果(后述)提高。并且,通过将多个环圈层配置于杆身的球杆柄部分,能够抑制球杆柄部分的弯曲刚性,并提高杆身重心率。从这样的观点来看,wfb/wsb优选0.30以上,进一步优选0.32以上,更进一步优选0.35以上。从抑制特定球杆柄区域rb中的平直层变得过小的观点来看,wfb/wsb优选0.55以下,进一步优选0.50以下,更进一步优选0.45以下。从提高wfb/wsb并得到上述的效果的观点来看,特定球杆柄区域rb优选包含3圈以上的环圈层,进一步优选包含4圈以上的环圈层。在图2的实施方式中,特定球杆柄区域rb包含4圈环圈层。在图3的实施方式中,特定球杆柄区域rb包含3圈环圈层。在图4的实施方式中,特定球杆柄区域rb包含3圈环圈层。并且,在图5的实施方式中,特定球杆柄区域rb包含2圈环圈层。并且,在图6的实施方式中,特定球杆柄区域rb不包含环圈层。当考虑超轻量杆身的重量的制约时,包含于特定球杆柄区域rb的环圈层的圈数优选6以下,进一步优选5以下。本申请中的“圈”是指卷绕数。被连续360°卷绕的一层为1圈。如上所述,在图2的实施方式中,特定球杆柄区域rb包含4圈环圈层。在该图2的实施方式中,每1圈的片材不同。即,在特定球杆柄区域rb中,被卷绕的环圈片材的个数与圈数一致。如此,一张环圈片材也可以是1圈。并且,例如,一张环圈片材也可以是2圈。从抑制杆身重量ws并提高wfb/wsb的观点来看,杆身6优选具有作为球杆柄部分层的环圈层(球杆柄部分环圈层)。在图3的实施方式中,片材s5是球杆柄部分环圈层。在杆身6中,将平直层的重量设为wt。优选的是,在本申请中考虑wf/wt。如上所述,了解到在本发明中,在42g以下的超轻量杆身中,通过被认为是过剩的量的环圈层,能够提高弯曲强度。为了维持杆身的轻量性,有必要伴随环圈层的增加而减少平直层或倾斜层。在该情况下,减少平直层被认为会使弯曲强度降低。但是,本发明的发明人明确了增加环圈层并减少平直层也能够提高强度。该效果也称为过剩环圈效果。发现该过剩环圈效果的理由还未明了。从通过上述过剩环圈效果来使强度的提高和轻量性这两者同时成立的观点来看,wf/wt优选0.25以上,进一步优选0.35以上,更进一步优选0.45以上。从抑制wt变得过小的观点来看,wf/wt优选0.70以下,进一步优选0.65以下,更进一步优选0.60以下。如上所述,本发明在超轻量杆身中有效。从该观点来看,杆身重量ws优选42g以下,进一步优选41g以下,更进一步优选40g以下,更优选39g以下。从强度的观点来看,杆身重量ws优选30g以上,进一步优选32g以上,更进一步优选34g以上。优选的是,考虑上述地点p1处的杆身的内径。通过增大杆身的球杆柄部分的外径,能够减轻安装的握柄的重量。其原因在于,在安装于杆身的握柄的外径相等的条件下,杆身的外径越大,则握柄的壁厚越小。并且,握柄的轻量化与球杆的轻量化相关联。在超轻量杆身中,杆身自身的壁厚小,但通过增大杆身的内径,也能够增大杆身的外径。但是,当杆身的内外径变大时,弯曲刚性提高。因此,当杆身的球杆柄部分的内外径变大时,该球杆柄部分的挠曲(弯曲变形)变少,曲腕近似效果(后述)降低。在此,在本实施方式中,特定球杆柄区域rb中环圈层的比例增大。由此,球杆柄部分的弯曲刚性被抑制。即,通过增加环圈层的比例,即使球杆柄部分增粗,也能够确保该球杆柄部分的挠曲。作为结果,能够实现握柄的轻量化并确保球杆柄部分的挠曲。伴随握柄的轻量化的球杆的轻量化有助于杆头速度的提高。通过在该效果上加上球杆柄部分的挠曲的效果(曲腕近似效果),能够进一步提高杆头速度。从这样的观点来看,上述地点p1处的杆身的内径优选14.0mm以上,进一步优选14.1mm以上,更进一步优选14.2mm以上,更优选14.3以上。从抑制球杆柄部分处的过度的弯曲刚性的观点来看,上述地点p1处的杆身的内径优选16mm以下,进一步优选15.8mm以下,更进一步优选15.6mm以下。从同样的观点来看,上述地点p1处的杆身的外径优选15.0mm以上,进一步优选15.1mm以上,更进一步优选15.2mm以上,更优选15.3以上。从抑制球杆柄部分处的过度弯曲刚性的观点来看,上述地点p1处的杆身的外径优选18mm以下,进一步优选17.8mm以下,更进一步优选17.6mm以下。此外,杆身6的特定球杆柄区域rb是越往杆头侧则越细的锥形状。即,在特定球杆柄区域rb处的杆身6的外径越靠近柄端bt越大。因此,握柄重量的进一步轻量化变得可能。轻量的杆身的壁厚小。但是,通过增大杆身的球杆柄部的内径,即使壁厚小,也能够增大球杆柄部的外径。从该观点来看,特定球杆柄区域rb处的杆身的壁厚优选0.70mm以下,进一步优选0.60mm以下,更进一步优选0.56mm以下。从强度的观点来看,特定球杆柄区域rb的杆身的壁厚优选0.30mm以上,进一步优选0.35mm以上,更进一步优选0.40mm以上。在本申请中,在杆身的各位置测定ei值。ei值是表示弯曲刚性的指标。[ei值的测定]图7表示ei值的测定方法。ei使用intesco公司制造的2020型(最大负载500kg)的万能材料试验机来测定。通过第一支承点t1与第二支承点t2,杆身6被从下方支承。一边维持该支承,一边从上方向测定点t3施加负载f1。负载f1的朝向是铅垂方向向下。点t1与点t2之间的距离为200mm。测定点t3的位置是将点t1与点t2之间二等分的位置。测定施加负载f1时的弯曲量h。负载f1由压子r1提供。压子r1的前端是曲率半径为5mm的圆筒面。压子r1的向下方的移动速度为5mm/分钟。在负载f1到达20kgf(196n)的时候,停止压子r1的移动,并测定此时的弯曲量h。弯曲量h是点t3在垂直方向上的位移量。ei值利用下式算出。ei(kgf·m2)=f1×l3/(48×h)其中,f1为最大负载(kgf),l为支承点间距离(m),h为弯曲量(m)。最大负载f1为20kgf,支承点间距离l为0.2m。[e1~e10]作为ei的测定点,例示有如下的10个地点。(测定点1):从尖端tp起离开130mm的地点(测定点2):从尖端tp起离开230mm的地点(测定点3):从尖端tp起离开330mm的地点(测定点4):从尖端tp起离开430mm的地点(测定点5):从尖端tp起离开530mm的地点(测定点6):从尖端tp起离开630mm的地点(测定点7):从尖端tp起离开730mm的地点(测定点8):从尖端tp起离开830mm的地点(测定点9):从尖端tp起离开930mm的地点(测定点10):从尖端tp起离开1030mm的地点在本申请中,将所述测定点1的ei值设为e1。将所述测定点2的ei值设为e2。将所述测定点3的ei值设为e3。将所述测定点4的ei值设为e4。将所述测定点5的ei值设为e5。将所述测定点6的ei值设为e6。将所述测定点7的ei值设为e7。将所述测定点8的ei值设为e8。将所述测定点9的ei值设为e9。将所述测定点10的ei值设为e10。如上所述,通过抑制球杆柄部分的弯曲刚性,能够提高杆头速度。从该观点来看,作为从尖端tp起1030mm的地点的ei值的e10优选5.0(kgf·m2)以下,进一步优选4.5(kgf·m2)以下,更进一步优选4.3(kgf·m2)以下,更优选4.0(kgf·m2)以下。当e10过小时,挠曲恢复不足,杆头速度降低。从该观点来看,e10优选2.8(kgf·m2)以上,进一步优选3.0(kgf·m2)以上,更进一步优选3.2(kgf·m2)以上。关于刚性分布,优选的是考虑斜率m3。该斜率m3基于上述e8、e9以及e10算出。在将三个ei值(e8、e9、e10)绘制于x轴为从尖端tp到测定点的距离(mm)且y轴为ei值(kgf·m2)的xy坐标平面中的曲线图中,当用最小二乘法将这三个点拟合为一次式时,该一次式的斜率为m3。通过使斜率m3平缓,在下杆的初期阶段杆身的球杆柄部分变得容易挠曲。其结果是杆头速度提高。从该观点来看,斜率m3优选0.0100以下,进一步优选0.0080以下,更进一步优选0.0050以下。当该斜率m3过小时,有球杆柄部分的弯曲刚性过小、挠曲恢复不足的情况。从该观点来看,斜率m3优选0.0039以上,进一步优选0.0040以上,更进一步优选0.0041以上。在本申请中,考虑基于多个ei值而制成的曲线图。该曲线图是xy坐标平面。该曲线图的x轴是从尖端tp到所述测定点的距离(mm)。该曲线图的y轴是ei值(kgf·m2)。图8表示该曲线图的一例。图8是绘制有实施例一(后述)的从e1到e10的曲线图。绘制于曲线图的十个点的坐标(x,y)为(130,e1)、(230,e2)、(330,e3)、(430,e4)、(530,e5)、(630,e6)、(730,e7)、(830,e8)、(930,e9)以及(1030,e10)。关于刚性分布,考虑斜率m1以及斜率m2。m1是通过(130,e1)以及(230,e2)的直线的斜率。m2是用最小二乘法将(330,e3)、(430,e4)、(530,e5)、(630,e6)以及(730,e7)这五点拟合后的直线的斜率。如上所述,m3是用最小二乘法将(830,e8)、(930,e9)以及(1030,e10)这三点拟合后的直线的斜率。此外,利用最小二乘法来向直线的拟合能够通过使用微软公司的表格计算软件“excel2010”的“线性拟合”功能而容易地进行。也可以使用该软件的“linest”函数。此外,“excel”是微软公司注册商标。在图8的情况下,斜率m1为-0.0013,斜率m2为0.0028,斜率m3为0.0043。通过使杆身的中间部分挠曲并确保挠曲量,能够增大挠曲恢复并提高杆头速度。此外,如上所述,通过抑制斜率m3,球杆柄部分的挠曲增大且杆头速度增加。从这些观点来看,m1、m2以及m3优选满足以下条件。(a)-0.015≤m1≤0(b)0.0008≤m2≤0.0080(c)0.0040≤m3≤0.0100(d)m2<m3即,斜率m1优选-0.015以上,并优选0以下。斜率m2优选0.0008以上,并优选0.0080以下。斜率m3优选0.0040以上,并优选0.0100以下。m3优选比m2大。一般而言,在下杆的前半程维持曲腕。曲腕是指手腕的弯曲。对本领域技术人员而言,维持曲腕也表现为“曲腕积蓄”。为了提高杆头速度,优选维持该曲腕到即将击球前,并在即将击球前释放曲腕。但是,业余高尔夫球手的曲腕的释放过早,因此杆头速度低。通过最优化弯曲刚性分布,在下杆的初期阶段,杆身的球杆柄部分挠曲。因此,变为与曲腕积蓄同样的状态。通过将该挠曲在即将击球前释放,与曲腕的释放相同,能够提高杆头速度。该效果也称为曲腕近似效果。此外,挠曲的释放也称为“挠曲恢复”。在下杆的初期阶段(从顶点刚开始回击)中,特别是向杆身球杆柄侧增加弯曲应力。通过抑制e10并减小斜率m3,在下杆的初期阶段中球杆柄部的挠曲增大。通过该挠曲的增大,曲腕近似效果提高。并且,在本实施方式中,由于杆身重心率高,因而达成易挥性。因此,实现杆头速度的进一步提高。如上所述,使用环圈层作为球杆柄部分层。因此,球杆柄部分的刚性被抑制,所述曲腕近似效果提高。并且,球杆柄部分层有助于增大杆身重心率。球杆柄部分层靠近握柄,因此容易影响手感。环圈层没有沿轴向取向的纤维。并且,在环圈层中,沿周向取向的相邻纤维之间存在基体树脂,因此通过基体树脂,容易吸收沿轴向传递而来的振动。其结果,通过球杆柄部分环圈层,能够提高击球时的手感。此外,球杆柄部的良好的挠曲被认为也有助于手感的提高。作为能够调整从e1到e10以及从斜率m1到m3的设计项目,例示有如下的从(a1)到(a8)。通过适当地设定这些设计项目,能够得到所希望的杆身。(a1)杆身(心轴)的锥度(a2)尖端部分层的轴向长度(a3)尖端部分层的厚度(a4)尖端部分层的纤维弹性率(a5)球杆柄部分层的轴向长度(a6)球杆柄部分层的厚度(a7)球杆柄部分层的纤维弹性率(a8)部分层的轴向位置作为调整杆身重心率的方法,例示有如下的从(b1)到(b6)。通过适当地设定这些设计项目,能够得到所希望的杆身。(b1)球杆柄部分层的厚度(b2)球杆柄部分层的轴向长度(b3)尖端部分层的厚度(b4)尖端部分层的轴向长度(b5)杆身(心轴)的锥度(b6)各片材的形状以下的表1以及表2表示可能使用的预成型料的例子。这些预成型料在市场上有售。能够选择适当的预成型料,以得到所希望的规格。【表1】表1能使用的预成型料的例子拉伸强度、拉伸弹性率是遵照jisr7601:1986“碳素纤维试验方法”测定的值。【表2】表2能使用的预成型料的例子拉伸强度、拉伸弹性率是遵照jisr7601:1986“碳素纤维试验方法”测定的值。【实施例】以下,通过实施例来使本发明的效果更加清楚,但本发明不应该基于该实施例的记载而被限定地解释。[实施例一]制作具有图2所示的层叠结构的杆身。通过与所述杆身6相同的制造方法而得到实施例一的杆身。利用上述的设计项目来调整规格。各片材所使用的预成型料如下。并且,球杆柄部分环圈层s5的轴向长度fb为270mm。片材s1:玻璃纤维强化预成型料(纤维弹性率为7tf/mm2)片材s2:碳素纤维强化预成型料(纤维弹性率为40tf/mm2)片材s3:碳素纤维强化预成型料(纤维弹性率为30tf/mm2)片材s4:碳素纤维强化预成型料(纤维弹性率为40tf/mm2)片材s5:碳素纤维强化预成型料(纤维弹性率为24tf/mm2)片材s6:碳素纤维强化预成型料(纤维弹性率为24tf/mm2)片材s7:碳素纤维强化预成型料(纤维弹性率为30tf/mm2)片材s8:碳素纤维强化预成型料(纤维弹性率为33tf/mm2)片材s9:碳素纤维强化预成型料(纤维弹性率为30tf/mm2)片材s10:碳素纤维强化预成型料(纤维弹性率为24tf/mm2)片材s11:碳素纤维强化预成型料(纤维弹性率为10tf/mm2)片材s12:碳素纤维强化预成型料(纤维弹性率为24tf/mm2)片材s13:碳素纤维强化预成型料(纤维弹性率为24tf/mm2)该实施例一的10个ei值在下记的表3中表示。在实施例一中,用最小二乘法将e8、e9以及e10的曲线图上的三点拟合后的一次式为y=0.0043x-0.8349。[实施例二]采用图3所示的层叠结构,其余与实施例一同样地进行,得到实施例二的杆身。该实施例二的10个ei值在下记的表4中表示。此外,在该实施例二中,各片材所使用的预成型料如下。片材s1:玻璃纤维强化预成型料(纤维弹性率为7tf/mm2)片材s2:碳素纤维强化预成型料(纤维弹性率为40tf/mm2)片材s3:碳素纤维强化预成型料(纤维弹性率为40tf/mm2)片材s4:碳素纤维强化预成型料(纤维弹性率为24tf/mm2)片材s5:碳素纤维强化预成型料(纤维弹性率为24tf/mm2)片材s6:碳素纤维强化预成型料(纤维弹性率为24tf/mm2)片材s7:碳素纤维强化预成型料(纤维弹性率为30tf/mm2)片材s8:碳素纤维强化预成型料(纤维弹性率为33tf/mm2)片材s9:碳素纤维强化预成型料(纤维弹性率为30tf/mm2)片材s10:碳素纤维强化预成型料(纤维弹性率为24tf/mm2)片材s11:碳素纤维强化预成型料(纤维弹性率为10tf/mm2)片材s12:碳素纤维强化预成型料(纤维弹性率为24tf/mm2)片材s13:碳素纤维强化预成型料(纤维弹性率为24tf/mm2)[实施例三]采用图4所示的层叠结构,其余与实施例一同样地进行,得到实施例三的杆身。该实施例三的10个ei值在下记的表5中表示。此外,在该实施例三中,各片材所使用的预成型料如下。片材s1:玻璃纤维强化预成型料(纤维弹性率为7tf/mm2)片材s2:碳素纤维强化预成型料(纤维弹性率为40tf/mm2)片材s3:碳素纤维强化预成型料(纤维弹性率为30tf/mm2)片材s4:碳素纤维强化预成型料(纤维弹性率为40tf/mm2)片材s5:碳素纤维强化预成型料(纤维弹性率为24tf/mm2)片材s6:碳素纤维强化预成型料(纤维弹性率为24tf/mm2)片材s7:碳素纤维强化预成型料(纤维弹性率为30tf/mm2)片材s8:碳素纤维强化预成型料(纤维弹性率为33tf/mm2)片材s9:碳素纤维强化预成型料(纤维弹性率为24tf/mm2)片材s10:碳素纤维强化预成型料(纤维弹性率为24tf/mm2)片材s11:碳素纤维强化预成型料(纤维弹性率为10tf/mm2)片材s12:碳素纤维强化预成型料(纤维弹性率为24tf/mm2)片材s13:碳素纤维强化预成型料(纤维弹性率为24tf/mm2)[比较例一]采用图5所示的层叠结构,其余与实施例一同样地进行,得到比较例一的杆身。利用上述的设计项目来调整规格。各片材所使用的预成型料如下。片材s1:玻璃纤维强化预成型料(纤维弹性率为7tf/mm2)片材s2:碳素纤维强化预成型料(纤维弹性率为40tf/mm2)片材s3:碳素纤维强化预成型料(纤维弹性率为40tf/mm2)片材s4:碳素纤维强化预成型料(纤维弹性率为24tf/mm2)片材s5:碳素纤维强化预成型料(纤维弹性率为24tf/mm2)片材s6:碳素纤维强化预成型料(纤维弹性率为24tf/mm2)片材s7:碳素纤维强化预成型料(纤维弹性率为33tf/mm2)片材s8:碳素纤维强化预成型料(纤维弹性率为30tf/mm2)片材s9:碳素纤维强化预成型料(纤维弹性率为24tf/mm2)片材s10:碳素纤维强化预成型料(纤维弹性率为10tf/mm2)片材s11:碳素纤维强化预成型料(纤维弹性率为24tf/mm2)片材s12:碳素纤维强化预成型料(纤维弹性率为24tf/mm2)该比较例一的10个ei值在下记的表6中表示。[比较例二]采用图6所示的层叠结构,其余与实施例一同样地进行,得到比较例二的杆身。利用上述的设计项目来调整规格。各片材所使用的预成型料如下。片材s1:玻璃纤维强化预成型料(纤维弹性率为7tf/mm2)片材s2:碳素纤维强化预成型料(纤维弹性率为40tf/mm2)片材s3:碳素纤维强化预成型料(纤维弹性率为40tf/mm2)片材s4:碳素纤维强化预成型料(纤维弹性率为24tf/mm2)片材s5:碳素纤维强化预成型料(纤维弹性率为24tf/mm2)片材s6:碳素纤维强化预成型料(纤维弹性率为24tf/mm2)片材s7:碳素纤维强化预成型料(纤维弹性率为33tf/mm2)片材s8:碳素纤维强化预成型料(纤维弹性率为24tf/mm2)片材s9:碳素纤维强化预成型料(纤维弹性率为24tf/mm2)片材s10:碳素纤维强化预成型料(纤维弹性率为10tf/mm2)片材s11:碳素纤维强化预成型料(纤维弹性率为24tf/mm2)片材s12:碳素纤维强化预成型料(纤维弹性率为24tf/mm2)该比较例二的10个ei值在下记的表7中表示。[比较例三]将球杆柄部分平直层s4的纤维弹性率变为40t,其余与比较例二同样地进行,得到比较例三的杆身。这些从实施例一到实施例三以及从比较例一到比较例三的规格的评价结果在下记的表8中表示。下记的表9表示实施例一的杆身的各位置的内径以及外径。此外,实施例一的杆身的杆身全长ls为1175mm。【表3】表3实施例一的ei值从尖端起的距离(mm)ei值(kgf·m2)e11301.66e22301.54e33301.39e44301.66e55301.97e66302.32e77302.56e88302.73e99303.06e1010303.58【表4】表4实施例二的ei值从尖端起的距离(mm)ei值(kgf·m2)e11301.65e22301.55e33301.41e44301.68e55302.00e66302.36e77302.62e88302.89e99303.13e1010303.66【表5】表5实施例三的ei值从尖端起的距离(mm)ei值(kgf·m2)e11301.79e22301.76e33301.63e44301.94e55302.32e66302.72e77303.03e88303.34e99303.64e1010304.24【表6】表6比较例一的ei值从尖端起的距离(mm)ei值(kgf·m2)e11301.79e22301.75e33301.62e44301.93e55302.30e66302.71e77303.01e88303.33e99303.61e1010305.10【表7】表7比较例二的ei值从尖端起的距离(mm)ei值(kgf·m2)e11301.90e22301.91e33301.81e44302.16e55302.58e66303.04e77303.39e88303.75e99304.38e1010305.58【表8】表8实施例以及比较例的规格的评价结果【表9】表9实施例一的内径以及外径评价方法如下。[三点弯曲强度]三点弯曲强度依照sg式三点弯曲强度试验来测定。该试验是日本的制品安全协会规定的试验。测定点被设为b点以及c点。b点是从尖端tp起525mm的地点。c点是从柄端bt起175mm的地点。图9表示三点弯曲强度的测定方法。如该图9所示,在两个支承点e1、e2从下方支承杆身6,并且压子r在负载点e3处从上方向下方施加负载f。压子r的下降速度为20mm/分钟。在压子r的前端安装有硅橡胶st。负载点e3的位置是将支承点e1与支承点e2之间二等分的位置。该负载点e3是测定点。在测定b点以及c点的情况下,所述跨距s被设为300mm。测定杆身6破损时的负载f的值(峰值)。该负载f在表8中表示。[手感]在各杆身上安装杆头以及握柄而得到高尔夫球杆。作为杆头,使用邓禄普体育用品株式会社制的商品名为“ゼクシオナイン”的一号木杆杆头(杆面倾角10.5°)。10名高尔夫球手使用该高尔夫球杆来进行实际击球并评价手感。该手感被作为击球感和易挥性的综合评价。在1点到5点的五个阶段中作出感官评价。点数越高则评价越高。10名高尔夫球手的平均值在表8中表示。如表8所示,实施例比比较例的评价高。如表9所示,在实施例一的杆身中,特定球杆柄区域的壁厚薄至0.6mm以下,但特定球杆柄区域rb的内径大,因此能够在该区域rb确保大的外径。因此,能够减小握柄的壁厚,从而使球杆的轻量化变得可能。并且,在实施例一中,wfb/wsb较大,因此虽然特定球杆柄区域rb的杆身的内外径大,但是e10小。因此,确保了球杆柄部分的挠曲,杆头速度较大。由以上可知,本发明的优势明显。产业上的可利用性以上说明的发明能够适用于所有的高尔夫球杆。当前第1页12