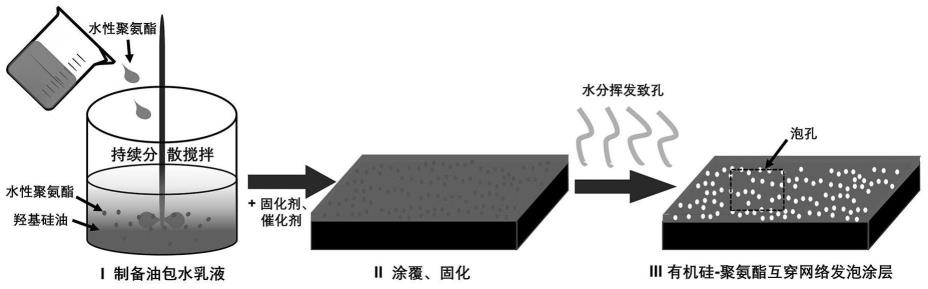
1.本发明属于合成革技术领域,具体涉及一种有机硅合成革发泡涂层及其制备方法。
背景技术:2.有机硅作为一种可不依赖于石油资源而生产的一类有机化工材料,因其特有的-si-o-si-结构而具备耐高低温、耐老化、耐磨、疏水以及生理惰性等诸多优异性能,多年来以助剂的形式在皮革/合成革领域得到广泛应用。随着合成革工业清洁化的不断推进以及制造技术的不断完善,近几年,有机硅材料开始以涂层形式被应用于合成革制造,即新一代有机硅合成革。有机硅合成革涂层的构建主要基于乙烯基硅油与含氢硅油间的硅氢加成反应体系,生产过程无需使用任何有机溶剂,无气体产生,可大大减少环境污染,产品无挥发性有机物(vocs)。鉴于其独特的资源、性能和环保优势,基于有机硅涂层材料的合成革可满足当今高品质生态合成革的市场需求,具有极大的发展前景。
3.然而,有机硅合成革作为一种新兴产品,其发展历程不长。与目前市场上占据主流的聚氨酯合成革相比仍存在较多不完善之处。其中,在合成革结构方面,传统聚氨酯合成革通常由表面效应层、面层、中间发泡层、粘接层和基材五个部分组成,每一部分在合成革的整体性能体现中均发挥着至关重要的作用。但由于制造技术和涂层材料的不匹配,目前可适用于有机硅合成革的发泡涂层技术相对匮乏。而发泡层在赋予合成革丰满手感、泡感和丰满度以及提升合成革品质和市场竞争力方面起关键作用。因此,结合合成革物性要求和工艺特征,丰富有机硅发泡涂层制备技术,将为有机硅合成革的进一步推广和应用奠定重要基础。
4.中国专利cn111691193a公开了一种发泡有机硅合成革及其制备方法;该发明公开了一种发泡有机硅合成革,该发泡有机硅合成革由依次层叠设置的面层、发泡层和基层组成;面层包括乙烯基聚硅氧烷、乙烯基mq硅树脂、白炭黑、含氢聚硅氧烷、铂系催化剂和抑制剂;发泡层包括乙烯基聚硅氧烷、乙烯基mq硅树脂、α,ω-二羟基聚硅氧烷、羟基硅油、白炭黑、含氢聚硅氧烷、铂系催化剂、抑制剂和增粘剂。该发泡有机硅合成革利用化学发泡制备发泡层,发泡层泡孔大小分布均匀,形态为均匀球形,降低了有机硅的使用量进而降低了成本,但具有良好的力学性能和轻量化的特点。该发明还提供了发泡有机硅合成革的制备方法,简单易于操作,易于推广,且设备场地成本投入少,适合工业化规模生产。
5.现有技术利用硅氢与羟基间反应脱氢气原理的化学发泡方法进行发泡。该方法发泡与涂层硫化同步进行,将存在发泡与硫化速率难以协调、发泡过程难于控制的问题,进而增加实际工艺操作难度、泡孔尺寸及涂层物性难以调控。
6.现有技术采用有机硅单一组分制备发泡层,由于有机硅为非极性聚合物,而合成革基材多为极性材料,如聚对苯二甲酸乙二醇酯(pet),尼龙等,故还将存在涂层力学强度与层间粘接力不足的问题。
技术实现要素:7.本发明的目的是针对上述现有技术的不足,充分结合合成革发泡涂层物性要求,提供一种有机硅合成革发泡涂层的制备方法,包括如下步骤:
8.(1)将水性聚氨酯以10-50ml/h的速度加入羟基硅油中,混合,得到羟基硅油-水性聚氨酯油包水乳液;所述水性聚氨酯和羟基硅油的质量比为30-50:50-70;
9.(2)向所述羟基硅油-水性聚氨酯油包水乳液中加入固化剂和催化剂,混合后涂覆于离型纸表面,得到待固化涂层;所述羟基硅油、固化剂和催化剂的质量比为100:2:0.1-0.3;
10.(3)将所述待固化涂层烘烤后干燥,得到所述有机硅合成革发泡涂层。
11.优选的,所述步骤(1)中,将50-70份羟基硅油加入配料罐中并置于分散机下,于100-500r/min转速下对其进行充分搅拌。在持续搅拌条件下,采用蠕动泵以10-50ml/h的速度将30-50份水性聚氨酯缓慢加入至羟基硅油中,加入完毕后即可得到羟基硅油-水性聚氨酯油包水乳液。
12.优选的,所述步骤(2)中,涂覆的厚度为0.8-1.0mm。
13.优选的,所述步骤(3)中,烘烤的温度为50-80℃,时间为3-5min。
14.优选的,所述步骤(3)中,干燥的温度为100-120℃,时间为1-2min。
15.优选的,所述羟基硅油为α,ω-二羟基聚硅氧烷,粘度为5000-20000mpa
·
s。
16.优选的,所述水性聚氨酯为聚酯型水性聚氨酯或聚醚型水性聚氨酯,固含量为20-40wt%;水性聚氨酯的引入不仅致孔,还可提升有机硅发泡涂层的极性和力学性能,进而提高其与合成革极性基材间的粘接力,为高物性有机硅合成革的制造奠定物质基础。
17.优选的,所述固化剂为正硅酸甲酯、正硅酸乙酯和正硅酸丁酯中的一种或多种。
18.优选的,所述催化剂为异辛酸铋和/或新葵酸铋。
19.本发明还提供一种上述制备方法制备得到的有机硅合成革发泡涂层。
20.本发明借助油包水体系前驱体原位构建有机硅合成革发泡涂层,可实现硫化、发泡分步进行,克服了传统工艺发泡与硫化速率难以协调的问题。
21.本发明的技术方案相比现有技术具有以下优点:
22.(1)首次提出油包水型有机硅发泡涂层原位制备方法,该方法无需使用任何乳化剂和发泡剂,利用双组分室温/低温固化硅橡胶体系中水分的挥发致孔,为有机硅合成革发泡涂层的构建提供了新思路。
23.(2)水性聚氨酯(wpu)的引入不仅致孔,还可与有机硅组分形成互穿网络,进而有效提升有机硅发泡涂层的极性、力学性能以及与极性基材间的粘接力,为高物性有机硅合成革的制造奠定了物质基础。
24.(3)基于油包水体系的发泡涂层原位构建方法可实现硫化与发泡分步进行,有效克服了传统发泡工艺存在的发泡与硫化速率难以协调的问题,泡孔结构与涂层物性更具可调控性。
附图说明
25.图1为有机硅合成革发泡涂层原位制备流程图。
具体实施方式
26.下面结合附图和具体实施例对本发明作进一步说明,以使本领域的技术人员可以更好地理解本发明并能予以实施,但所举实施例不作为对本发明的限定。
27.实施例1
28.(1)羟基硅油-水性聚氨酯油包水乳液的制备:
29.将5000mpa
·
s的α,ω-二羟基聚硅氧烷70份加入配料罐中并置于分散机下,于100r/min转速下对其进行充分搅拌。在持续搅拌条件下,采用蠕动泵以10ml/h的速度将30份固含量为20wt%的脂肪族聚酯型水性聚氨酯缓慢加入至α,ω-二羟基聚硅氧烷中,加入完毕后即可得到羟基硅油-水性聚氨酯油包水乳液;
30.(2)有机硅-聚氨酯互穿网络发泡涂层的原位制备:
31.向步骤(1)中制备的油包水乳液中加入正硅酸甲酯,控制羟基硅油与正硅酸甲酯的质量比为100:2,随后加入新葵酸铋0.3份,混合均匀后迅速涂敷于离型纸表面,涂膜厚度控制在0.8mm,然后置于50℃烘箱中固化3min,待有机硅组分固化完全后,将烘箱温度升至100℃继续干燥2min以除去内部水分,即得到有机硅-聚氨酯互穿网络发泡涂层。
32.该涂层在制备和使用过程中不使用任何有机溶剂,经对比测试,与单一组分有机硅发泡涂层相比,涂层力学强度从1.8mpa提升至2.8mpa,涂层与基布的剥离强度从35n/3cm提升至45n/3cm。
33.实施例2:
34.(1)羟基硅油-水性聚氨酯油包水乳液的制备:
35.将10000mpa
·
s的α,ω-二羟基聚硅氧烷60份加入配料罐中并置于分散机下,于200r/min转速下对其进行充分搅拌。在持续搅拌条件下,采用蠕动泵以20ml/h的速度将40份固含量为30wt%的脂肪族聚醚型水性聚氨酯缓慢加入至α,ω-二羟基聚硅氧烷中,加入完毕后即可得到羟基硅油-水性聚氨酯油包水乳液;
36.(2)有机硅-聚氨酯互穿网络发泡涂层的原位制备:
37.向步骤(1)中制备的油包水乳液中加入正硅酸乙酯,控制羟基硅油与正硅酸乙酯的质量比为100:2,随后加入新葵酸铋0.2份,混合均匀后迅速涂敷于离型纸表面,涂膜厚度控制在0.8mm,然后置于60℃烘箱中固化3min,待有机硅组分固化完全后,将烘箱温度升至110℃继续干燥1min以除去内部水分,即得到有机硅-聚氨酯互穿网络发泡涂层。
38.该涂层在制备和使用过程中不使用任何有机溶剂,经对比测试,与单一组分有机硅发泡涂层相比,涂层力学强度从1.8mpa提升至3.2mpa,涂层与基布的剥离强度从35n/3cm提升至48n/3cm。
39.实施例3:
40.(1)羟基硅油-水性聚氨酯油包水乳液的制备:
41.将20000mpa
·
s的α,ω-二羟基聚硅氧烷50份加入配料罐中并置于分散机下,于500r/min转速下对其进行充分搅拌。在持续搅拌条件下,采用蠕动泵以50ml/h的速度将50份固含量为40wt%的芳香族聚醚型水性聚氨酯缓慢加入至α,ω-二羟基聚硅氧烷中,加入完毕后即可得到羟基硅油-水性聚氨酯油包水乳液;
42.(2)有机硅-聚氨酯互穿网络发泡涂层的原位制备:
43.向步骤(1)中制备的油包水乳液中加入正硅酸丁酯,控制羟基硅油与正硅酸丁酯
的质量比为100:2,随后加入异辛酸铋0.1份,混合均匀后迅速涂敷于离型纸表面,涂膜厚度控制在1.0mm,然后置于80℃烘箱中固化5min,待有机硅组分固化完全后,将烘箱温度升至120℃继续干燥1min以除去内部水分,即得到有机硅-聚氨酯互穿网络发泡涂层。
44.该涂层在制备和使用过程中不使用任何有机溶剂,经对比测试,与单一组分有机硅发泡涂层相比,涂层力学强度从1.8mpa提升至3.9mpa,涂层与基布的剥离强度从35n/3cm提升至50n/3cm。
45.显然,上述实施例仅仅是为清楚地说明所作的举例,并非对实施方式的限定。对于所属领域的普通技术人员来说,在上述说明的基础上还可以做出其它不同形式变化或变动。这里无需也无法对所有的实施方式予以穷举。而由此所引申出的显而易见的变化或变动仍处于本发明创造的保护范围之中。