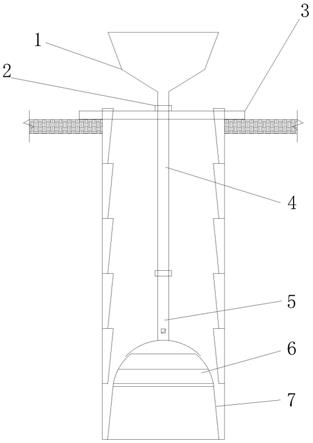
1.本发明涉及人工挖孔桩施工技术领域,更具体地说,涉及一种人工挖孔桩混凝土护壁浇筑施工体系及其施工方法。
背景技术:2.近年来,随着人们生活水平越来越高,我国建筑市场飞速发展,高层民用建筑特别是三、四线城市开发越来越普及。目前,我国人工挖孔桩采用传统的混凝土人工浇筑方式,该浇筑做法缺点明显。
3.一是人工挖孔桩井下作业条件差,环境恶劣;二是劳动强度大,安全隐患较高;三是人工挖孔桩混凝土护壁混凝土浇筑工序繁琐,需不断地吊运混凝土至孔桩底部,浇筑周期长。
技术实现要素:4.1.发明要解决的技术问题
5.针对现有技术存在的缺陷与不足,本发明提供了一种人工挖孔桩混凝土护壁浇筑施工体系及其施工方法,本发明较传统的人工挖孔桩混凝土护壁浇筑技术安全系数高,无需人工全程在人工挖孔桩井下进行混凝土护壁浇筑作业,大大的减小了施工安全隐患;施工节奏快,混凝土浇筑过程连续性,简化施工步骤,大大减少了混凝土浇筑周期,提高混凝土浇筑成型质量,工具安装和拆除方便快捷,周转材料可重复使用,提高使用率,钢护筒及混凝土分流器均为定制出厂,轻量化操作,大大提高了施工效率,同时减少施工安全风险。
6.2.技术方案
7.为达到上述目的,本发明提供的技术方案为:
8.本发明的一种人工挖孔桩混凝土护壁浇筑施工体系,包括料斗,所述的料斗的底部设置有连接扣和导管,料斗与导管连通,导管的外圈设置有钢质搁板,料斗与导管的连接处通过连接扣固定,连接扣支撑在钢质搁板上,所述的导管的底部设置有定制导管,定制导管的外圈开设有洞口,定制导管的底部设置有混凝土分流器及定型钢护筒,所述的混凝土分流器由第一圆台形钢护壁、第二圆台形钢护壁和球面形定制钢板组成,混凝土分流器底部设置有定型钢护筒。
9.进一步地,所述的连接扣由锁定螺栓、半圆型钢板和链接杆组成,半圆型钢板与链接杆链接,并通过锁定螺栓固定。
10.进一步地,所述的料斗为上口直径2000mm,下口200mm定型化漏斗,漏斗采用壁厚8mm钢板现场焊制而成,料斗底部与导管焊接连接。
11.进一步地,所述的导管一端为直径200mm,长度2000mm,壁厚8mm,导管的另一端满焊定制导管,定制导管直径180mm,长度50mm。
12.进一步地,所述的定制导管一端直径200mm,另一端为封闭端口,距封闭端口50mm处开80mm*80mm的洞口,导管与定制导管的连接处通过连接扣固定。
13.进一步地,所述的钢质搁板设有两组,钢质搁板的板面开设有半圆孔,钢质搁板相互之间通过固定扣固定,半圆孔直径为200mm。
14.进一步地,所述的球面形定制钢板与定制导管焊接,第一圆台形钢护壁、第二圆台形钢护壁的外沿均开设有u型卡槽,第一圆台形钢护壁通过其外沿的u型卡槽与定型钢护筒卡合连接,第二圆台形钢护壁通过其外沿的u型卡槽与第一圆台形钢护壁卡合连接。
15.进一步地,所述的定型钢护筒为底部直径1100mm
‑
2100mm,上部直径1000mm
‑
2000mm高度1000mm,厚度8mm的圆台形钢护筒,第二圆台形钢护壁为下部直径1300mm
‑
1600mm,上部直径900mm
‑
1200mm的圆台形护筒,护筒厚度8mm,第一圆台形钢护壁为下部直径1300mm
‑
2000mm,上部直径900mm
‑
1600mm的圆台形护筒,护筒厚度8mm。
16.进一步地,所述的钢质搁板由左搁板和右搁板组成,左搁板和右搁板的板面上均开设有半圆孔,左搁板的板面上开设有齿形槽,右搁板的底面设置有齿形连接件,右搁板通过齿形连接件与左搁板板面上的齿形槽咬合,左搁板和右搁板咬合后通过固定螺栓装配。
17.一种人工挖孔桩混凝土护壁浇筑施工体系的施工方法,其步骤为:
18.步骤一:在人工挖孔桩混凝土护壁浇筑施工前,根据不同桩径按方案中选定定型钢护筒,并对好桩心进行放置;
19.步骤二:在人工挖孔桩混凝土护壁浇筑施工前,根据步骤一中相关参数,选择与定型钢护筒相对应的混凝土分流器并卡合连接;
20.步骤三:在人工挖孔桩混凝土护壁浇筑施工前,将定制导管与导管采用链接扣连接固定,并根据人工挖孔桩的桩身长度选择数量;
21.步骤四:在人工挖孔桩混凝土护壁浇筑施工前,采用挖机将已固定连接定制导管与导管吊装与混凝土分流器固定,后用钢质搁板进行支撑,支撑后导管高出钢质搁板100mm;
22.步骤五:在人工挖孔桩混凝土护壁浇筑施工前,将料斗与导管进行连接固定,固定后,先计算所需人工挖孔桩混凝土护壁的浇筑量,后采用细石混凝土进行浇筑。浇筑过程中,将料斗采用挖机悬吊固定;
23.步骤六:浇筑完成后,依次拆除料斗、钢质搁板、导管、定制导管连接扣;
24.步骤七:检查桩底人工挖孔桩混凝土护壁浇筑情况,如果混凝土量缺失,采用人工浇筑进行混凝土浇筑,浇筑完成后将混凝土分流器的第一圆台形钢护壁、第二圆台形钢护壁拆除,并清洗干净;
25.步骤八:人工挖孔桩混凝土护壁混凝土强度满足后,将定型钢护筒拆除,进行下一步工序人工挖土施工;
26.步骤九:重复进行步骤一至步骤八施工工序,直至人工挖孔桩达到设计桩身要求。
27.3.有益效果
28.采用本发明提供的技术方案,与现有技术相比,具有如下有益效果:
29.本发明较传统的人工挖孔桩混凝土护壁浇筑技术安全系数高,无需人工全程在人工挖孔桩井下进行混凝土护壁浇筑作业,大大的减小了施工安全隐患;施工节奏快,混凝土浇筑过程连续性,简化施工步骤,大大减少了混凝土浇筑周期,提高混凝土浇筑成型质量,工具安装和拆除方便快捷,周转材料可重复使用,提高使用率,钢护筒及混凝土分流器均为定制出厂,轻量化操作,大大提高了施工效率,同时减少施工安全风险。
附图说明
30.图1为本发明的整体结构图;
31.图2为本发明的料斗结构图;
32.图3为本发明的连接扣结构图;
33.图4为本发明的钢质搁板俯视图;
34.图5为本发明的导管结构图;
35.图6为本发明的定制导管结构图;
36.图7为本发明的混凝土分流器结构图;
37.图8为本发明的定型钢护筒结构图;
38.图9为本发明的钢质搁板分解图。
39.图中:1、料斗;2、连接扣;21、锁定螺栓;22、半圆型钢板;23、链接杆;3、钢质搁板;31、半圆孔;32、左搁板;321、齿形槽;33、右搁板;331、齿形连接件;4、导管;5、定制导管;51、洞口;6、混凝土分流器;61、第一圆台形钢护壁;62、第二圆台形钢护壁;63、球面形定制钢板;64、u型卡槽;7、定型钢护筒。
具体实施方式
40.下面结合附图和实施例对本发明作进一步的描述:
41.实施例1
42.从图1
‑
8可以看出,本实施例的一种人工挖孔桩混凝土护壁浇筑施工体系,包括料斗1,料斗1的底部设置有连接扣2和导管4,料斗1与导管4连通,导管4的外圈设置有钢质搁板3,料斗1与导管4的连接处通过连接扣2固定,连接扣2支撑在钢质搁板3上,导管4的底部设置有定制导管5,定制导管5的外圈开设有洞口51,定制导管5的底部设置有混凝土分流器6及定型钢护筒7,混凝土分流器6由第一圆台形钢护壁61、第二圆台形钢护壁62和球面形定制钢板63组成,混凝土分流器6底部设置有定型钢护筒7。
43.连接扣2由锁定螺栓21、半圆型钢板22和链接杆23组成,半圆型钢板22与链接杆23链接,并通过锁定螺栓21固定。
44.料斗1为上口直径2000mm,下口200mm定型化漏斗,漏斗采用壁厚8mm钢板现场焊制而成,料斗1底部与导管4焊接连接。
45.导管4一端为直径200mm,长度2000mm,壁厚8mm,导管4的另一端满焊定制导管5,定制导管5直径180mm,长度50mm。
46.定制导管5一端直径200mm,另一端为封闭端口,距封闭端口50mm处开80mm*80mm的洞口51,导管4与定制导管5的连接处通过连接扣2固定。
47.钢质搁板3设有两组,钢质搁板3的板面开设有半圆孔31,钢质搁板3相互之间通过固定扣固定,半圆孔31直径为200mm。
48.钢质搁板3采用5*5方钢制作的长1.5m宽1m的2块板。
49.球面形定制钢板63与定制导管5焊接,第一圆台形钢护壁61、第二圆台形钢护壁62的外沿均开设有u型卡槽64,第一圆台形钢护壁61通过其外沿的u型卡槽64与定型钢护筒7卡合连接,第二圆台形钢护壁62通过其外沿的u型卡槽64与第一圆台形钢护壁61卡合连接。
50.球面形定制钢板63可选用为直径900mm、1000mm、1100mm三种规格的球面型,厚度
8mm的钢板。
51.第二圆台形钢护壁62共计5种规格,分别为下部直径1600mm,上部直径1200mm圆台形护筒,护筒厚度8mm;
52.下部直径1400mm,上部直径1000mm圆台形护筒,护筒厚度8mm;
53.下部直径1200mm,上部直径800mm圆台形护筒,护筒厚度8mm;
54.下部直径1500mm,上部直径1100mm护筒,护筒厚度8mm;
55.下部直径1300mm,上部直径900mm护筒,护筒厚度8mm;
56.护筒上部四周设有4个直径20mm孔口,下部均设深度10mm,宽度9mm倒“u”型卡槽,与与第一圆台形钢护壁61镶嵌连接;
57.第一圆台形钢护壁61共计9种规格,分别为下部直径为2000mm,上部直径1600mm圆台形护筒,护筒厚度8mm;
58.下部直径1800mm,上部直径1400mm圆台形护筒,护筒厚度8mm;
59.下部直径1600mm,上部直径1200mm圆台形护筒,护筒厚度8mm;
60.下部直径1400mm,上部直径1000mm圆台形护筒,护筒厚度8mm;
61.下部直径1200mm,上部直径800mm圆台形护筒,护筒厚度8mm;
62.下部直径1900mm,上部直径1500mm圆台形护筒,护筒厚度8mm;
63.下部直径1700mm,上部直径1300mm圆台形护筒,护筒厚度8mm;
64.下部直径1500mm,上部直径1100mm圆台形护筒,护筒厚度8mm;
65.下部直径1300mm,上部直径900mm圆台形护筒,护筒厚度8mm;上部四周设有4个直径20mm孔口,护筒下部均设深度10mm,宽度9mm倒“u”型卡槽,与定型钢护筒7镶嵌连接。
66.定型钢护筒7共计11种规格,分别为底部直径2100mm,上部直径2000mm,高度1000mm,厚度8mm的圆台形钢护筒;
67.底部直径2000mm,上部直径1900mm,高度1000mm,厚度8mm的圆台形钢护筒;
68.底部直径1900mm,上部直径1800mm,高度1000mm,厚度8mm的圆台形钢护筒;
69.底部直径1800mm,上部直径1700mm,高度1000mm,厚度8mm的圆台形钢护筒;
70.底部直径1700mm,上部直径1600mm,高度1000mm,厚度8mm的圆台形钢护筒;
71.底部直径1600mm,上部直径1500mm,高度1000mm,厚度8mm的圆台形钢护筒;
72.底部直径1500mm,上部直径1400mm,高度1000mm,厚度8mm的圆台形钢护筒;
73.底部直径1400mm,上部直径1300mm,高度1000mm,厚度8mm的圆台形钢护筒;
74.底部直径1300mm,上部直径1200mm,高度1000mm,厚度8mm的圆台形钢护筒;
75.底部直径1200mm,上部直径1100mm,高度1000mm,厚度8mm的圆台形钢护筒;
76.底部直径1100mm,上部直径1000mm,高度1000mm,厚度8mm的圆台形钢护筒;
77.定型钢护筒7为底部直径1100mm
‑
2100mm,上部直径1000mm
‑
2000mm高度1000mm,厚度8mm的圆台形钢护筒,第二圆台形钢护壁62为下部直径1300mm
‑
1600mm,上部直径900mm
‑
1200mm的圆台形护筒,护筒厚度8mm,第一圆台形钢护壁61为下部直径1300mm
‑
2000mm,上部直径900mm
‑
1600mm的圆台形护筒,护筒厚度8mm。
78.从图9可以看出,钢质搁板3由左搁板32和右搁板33组成,左搁板32和右搁板33的板面上均开设有半圆孔31,左搁板32的板面上开设有齿形槽321,右搁板33的底面设置有齿形连接件331,右搁板33通过齿形连接件331与左搁板32板面上的齿形槽321咬合,左搁板32
和右搁板33咬合后通过固定螺栓装配。
79.一种人工挖孔桩混凝土护壁浇筑施工体系的施工方法,其步骤为:
80.步骤一:在人工挖孔桩混凝土护壁浇筑施工前,根据不同桩径按方案中选定定型钢护筒7,并对好桩心进行放置;
81.步骤二:在人工挖孔桩混凝土护壁浇筑施工前,根据步骤一中相关参数,选择与定型钢护筒7相对应的混凝土分流器6并卡合连接;
82.步骤三:在人工挖孔桩混凝土护壁浇筑施工前,将定制导管5与导管4采用链接扣2连接固定,并根据人工挖孔桩的桩身长度选择数量;
83.步骤四:在人工挖孔桩混凝土护壁浇筑施工前,采用挖机将已固定连接定制导管5与导管4吊装与混凝土分流器6固定,后用钢质搁板3进行支撑,支撑后导管4高出钢质搁板3有100mm;
84.步骤五:在人工挖孔桩混凝土护壁浇筑施工前,将料斗1与导管4进行连接固定,固定后,先计算所需人工挖孔桩混凝土护壁的浇筑量,后采用细石混凝土进行浇筑。浇筑过程中,将料斗1采用挖机悬吊固定;
85.步骤六:浇筑完成后,依次拆除料斗1、钢质搁板3、导管4、定制导管5连接扣2;
86.步骤七:检查桩底人工挖孔桩混凝土护壁浇筑情况,如果混凝土量缺失,采用人工浇筑进行混凝土浇筑,浇筑完成后将混凝土分流器6的第一圆台形钢护壁61、第二圆台形钢护壁62拆除,并清洗干净;
87.步骤八:人工挖孔桩混凝土护壁混凝土强度满足后,将定型钢护筒7拆除,进行下一步工序人工挖土施工;
88.步骤九:重复进行步骤一至步骤八施工工序,直至人工挖孔桩达到设计桩身要求。
89.本发明较传统的人工挖孔桩混凝土护壁浇筑技术安全系数高,无需人工全程在人工挖孔桩井下进行混凝土护壁浇筑作业,大大的减小了施工安全隐患;施工节奏快,混凝土浇筑过程连续性,简化施工步骤,大大减少了混凝土浇筑周期,提高混凝土浇筑成型质量,工具安装和拆除方便快捷,周转材料可重复使用,提高使用率,钢护筒及混凝土分流器均为定制出厂,轻量化操作,大大提高了施工效率,同时减少施工安全风险。
90.以上示意性的对本发明及其实施方式进行了描述,该描述没有限制性,附图中所示的也只是本发明的实施方式之一,实际的结构并不局限于此。所以,如果本领域的普通技术人员受其启示,在不脱离本发明创造宗旨的情况下,不经创造性的设计出与该技术方案相似的结构方式及实施例,均应属于本发明的保护范围。