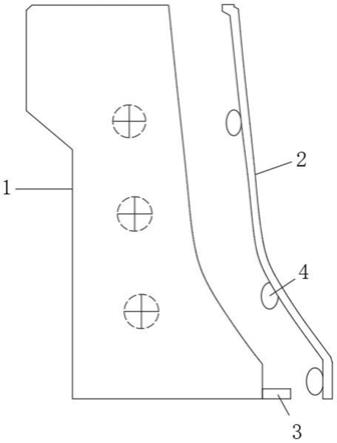
1.本发明涉及混凝土防撞墩修复领域,尤其涉及一种混凝土防撞墩修复方法。
背景技术:2.防撞墩也称防撞护栏,是一种安装于公路两侧或中央,防止车辆穿越以及冲出路面区域的路面设施,很多防撞墩都由混凝土浇筑而成,为了增加防撞等级都设有配筋,调查发现,北方地区混凝土防撞墩在使用几年后,在防撞墩根部20cm以内高度常发生剥落破坏,严重时钢筋外露,使其防撞等级降低,且美观性严重下降,究其原因发现,冬季雪天喷洒的除冰盐和融雪剂中含有大量腐蚀性离子和氯离子,车辆驶过会将其溅射到防撞墩上,由于混凝土表面及内部存在大量毛细孔,腐蚀性的离子及氯离子会慢慢渗入到混凝土内部,氯离子作为一种催化剂会破坏钢筋钝化膜引起锈蚀,锈蚀的钢筋从内部将混凝土保护层胀坏,另一方面,防撞墩也承受着冻融循环破坏作用,当环境温度降低到冰点以下时,混凝土防撞墩毛细孔中的吸附的游离状态水会结冰,而水在转化成冰的过程体积变大11%,是膨胀过程,若解冻后再结冰,膨胀继续增大,最终可能导致混凝土剥落破坏。
3.针对防撞墩所遭受的上述破坏问题,目前采取的解决方式是大量路政工人进行现场修补,这种方式存在的问题包括如下:一,施工现场需要设置交通管制,造成交通拥堵,降低行车效率,由此带来的隐性成本支出很高;二,现场需要工人携带大量建筑材料施工效率低成本高且养护条件难保证,修补效果不理想;三,修补位置与未修补位置外观差别明显,整体颜色斑驳,美观性很差;四,修补位置未能从根本上解决问题,同样存在钢筋锈蚀、冻融破坏和尾气侵蚀问题,往往远未达到使用年限又需要继续修补。
4.为了解决这一问题,有技术工作者提出采用3厘米厚uhpc作为防撞墩现场浇筑的模板,随着防撞墩的凝结硬化,该uhpc模板与防撞墩形成一个整体,这种方案能够解决现浇混凝土防撞墩劣化的问题,但是存在如下问题:一,模板过于厚重,成本高,搬运不便且容易断裂;二,未提出非现场浇筑混凝土防护的解决方案;三,对于已发生破损混凝土防撞墩,未提出修复方案。
5.市场调研发现,有人采用外贴3-5cm厚的防护板对防撞墩进行加强防护,具体方案为:防护板为分体结构,由上平面板和下弧面板两部分组成,上平面板与防撞墩之间涂抹一层砂浆找平层,然后通过金属长螺栓穿过防护板进而拧入防撞墩中的螺纹套进行固定;下弧面板与防撞墩底部的弧面采用抹灰砂浆进行粘结。该种方案存在的问题有两点:第一,采用螺栓固定上平面板,外露的螺栓头会因为锈蚀逐渐变小,最终无法发挥将上平面板与防撞墩固定作用,进而上平面板脱落而给路面行车造成巨大安全威胁;第二,下弧面板与防撞墩之间采用砂浆黏结方式不可靠,随着使用时间延长,砂浆粘接力因为各种原因而丧失,下弧面板同样会脱落给路面行车造成巨大威胁。
技术实现要素:6.本发明的目的是为了解决现有技术中存在的缺点,而提出的一种混凝土防撞墩修
复方法。
7.为了实现上述目的,本发明采用了如下技术方案:
8.一种混凝土防撞墩修复方法,包括防撞墩、防护板、封浆料以及聚合物砂浆,具体修复过程包括以下步骤:
9.s1、防撞墩的预处理;
10.s2、预处理完成后,采用快硬型的封浆料对防撞墩待修补面与路面交界处进行均匀铺设;
11.s3、采用快硬型的聚合物砂浆堆积于防护板粘贴面中部偏下位置,厚度大于防护板与防撞墩之间缝隙设计宽度;
12.s4、将防护板平行贴合于防撞墩上,防护板底部采用座浆形式落在均匀铺设的快硬型的封浆料中,调节防护板与防撞墩之间缝隙均匀,满足灌浆条件;
13.s5、将防护板与防撞墩之间的缝隙边缘用快硬型的封浆料封住,保证缝隙外侧没有露出快硬型的封浆料,不影响下一块防护板的安装;
14.s6、快硬型的聚合物砂浆对防护板与防撞墩进行强力粘结,防止在后续灌浆过程中防护板向外胀开;
15.s7、采用大流动度快硬型灌浆料对防护板与防撞墩之间缝隙进行快速灌浆,灌浆方式为人工倾倒或者机械压力灌浆方式,灌浆过程需保证灌浆位置固定,将大流动度快硬型灌浆料从一侧往另一侧灌入,方便内部气体的排出,可以采用一次灌浆或者多次灌浆方式;
16.s8、待防护板与防撞墩之间的大流动度快硬型灌浆料初凝后,进行下一块防护板的安装操作;
17.s9、灌浆完成后,防撞墩与防护板中部的大流动度快硬型灌浆料凝结硬化后产生桥接作用,大流动度快硬型灌浆料的一侧与防撞墩紧密结合,另一侧与防护板内部粗糙表面结合,从而使防护板牢牢防护于防撞墩外侧,起到保护作用;
18.s10、从灌浆开始1-2个小时后,防护板即可完全固定于防撞墩外侧,形成一个整体。
19.优选的,所述步骤s2中铺设厚度以防护板贴合后底部不漏水为准。
20.通过采用上述技术方案:在铺设过程中,以不漏水为标准,能够确保灌浆过程不漏浆且不漏水,保证凝结硬化后的粘结强度。
21.优选的,所述步骤s3中在防护板平行贴合于防撞墩上时,快硬型的聚合物砂浆可以粘贴于防撞墩底部,保证防撞墩与防护板之间形成足够强度的粘结力。
22.优选的,所述步骤s5中安装过程中,如果只有一边侧边露出来,则这个露出的侧边用快硬型的封浆料封闭,另一个侧边与上一块防护板的侧边之间的缝隙用快硬型的聚合物砂浆填补缝隙。
23.通过采用上述技术方案:使防护板与防撞墩之间形成空腔,且除顶面的缝隙外,其他侧面和底面均不漏水和漏浆。
24.优选的,所述步骤s3中快硬型的聚合物砂浆形成强度的时间不晚于快硬型的封浆料的终凝时间。
25.优选的,所述步骤s8中在进行下一块防护板施工前,首先清理防护板底部露在外
侧快硬型的封浆料。
26.优选的,所述步骤s1中预处理的步骤具体为:
27.s1.1、防撞墩由于冻融循环破坏或钢筋锈蚀问题导致面向行车道一侧发生混凝土保护层破损,首先,剔除表面已破损的混凝土基层,露出新鲜混凝土基面;
28.s1.2、然后,对于未露出钢筋的防撞墩表面,涂刷高渗透型的钢筋阻锈剂,待钢筋阻锈剂渗透至钢筋表面进行后续操作;
29.s1.3、对于已露出钢筋的混凝土防撞墩,首先清除破损混凝土基层,并采用物理打磨或化学试剂清洗方式清除钢筋表面的锈蚀,待钢筋表面干燥后,使用高阻锈型砂浆对钢筋附近和防撞墩表面进行修补,等到修补中的高阻锈型砂浆硬化再进行后续工作。
30.通过采用上述技术方案:由于采用阻锈剂对钢筋附近进行处理,混凝土防撞墩内部的钢筋的锈蚀情况大大改善,防锈效果大大提高。外层防护板可选超高性能混凝土材料制成,厚度尺寸控制在10mm-20mm之间,即可具有非常高抗氯离子渗透、抗冻融性能,且重量轻,弯曲韧性大,搬运方便。以上两方面相互作用,可使混凝土防撞墩的免维护周期提高10-15年,大幅降低维修成本,降低维护过程交通管制带来的社会经济成本。
31.本发明的有益效果为:
32.1、采用超高性能混凝土制作的防护板,具有非常高的密实程度,进而抵抗除冰盐、融雪剂和腐蚀气体能力大大提高,免维护周期大大延长,对维护所需的交通管制时间大大缩短,社会效益非常显著。
33.2、采用超高性能混凝土制作的防护板,使用期间无需修补,因而解决了修补位置与未修补位置颜色不一致的问题,美观性得到了保证。
34.3、对锈蚀部位进行清理,提高防锈能力,同时外部采用超高性能混凝土防护板进行隔绝,两方面操作使得防撞墩对钢筋锈蚀、冻融循环破坏和尾气侵蚀的抵抗能力得到了极大提高,从根本上解决了破坏问题。
35.4、防护板在预制构件厂生产,现场安装采用快硬型的封浆料和大流动度快硬型灌浆料,从施工开始至完全固化只需要1-2个小时,无需洒水养护,效率快速,且通过安装防护板后,防撞墩的免维护周期提高至10-15年,与现场修补相比,防撞墩整个生命周期内的维护次数大大降低,效果好且总体成本低。
36.5、超高性能混凝土制作的防护板具有极高的弯曲强度和抗压强度,由于不需要考虑对现浇混凝土的变形约束作用,厚度可控制在10mm-20mm范围内即可,不仅降低了材料成本,同时减轻了搬运重量。
37.6、防护板既可用于已破损混凝土防撞墩的修复,也可用于新混凝土防撞墩的防护,应用场景更宽。
附图说明
38.图1为本发明具体实施方式中防撞墩与防护板分体结构图;
39.图2为本发明具体实施方式中防撞墩与防护板整体结构图。
40.图例说明:1、防撞墩;2、防护板;3、封浆料;4、聚合物砂浆。
具体实施方式
41.下面将结合本发明实施例中的附图,对本发明实施例中的技术方案进行清楚、完整地描述。
42.如图1-2所示,一种混凝土防撞墩修复方法,包括防撞墩1、防护板2、封浆料3以及聚合物砂浆4,具体修复过程包括以下步骤:
43.步骤一、防撞墩1由于冻融循环破坏或钢筋锈蚀问题导致面向行车道一侧发生混凝土保护层破损,首先,剔除表面已破损的混凝土基层,露出新鲜混凝土基面;
44.然后,对于未露出钢筋的防撞墩1表面,涂刷高渗透型的钢筋阻锈剂,待钢筋阻锈剂渗透至钢筋表面进行后续操作;
45.对于已露出钢筋的混凝土防撞墩1,首先清除破损混凝土基层,并采用物理打磨或化学试剂清洗方式清除钢筋表面的锈蚀,待钢筋表面干燥后,使用高阻锈型砂浆对钢筋附近和防撞墩1表面进行修补,待修补中的高阻锈型砂浆硬化再进行后续工作。
46.步骤二、采用快硬型的封浆料3对防撞墩1待修补面与路面交界处进行均匀铺设,厚度以防护板2贴合后底部不漏水为准,其中,防护板2采用超高性能混凝土材料制成,具有非常高抗氯离子渗透、抗冻融性能;
47.步骤三、使用快硬型的聚合物砂浆4堆积于防护板2粘贴面中部偏下位置,其中,可将快硬型的聚合物砂浆4以有机树脂材料进行替代,使用厚度大于防护板2与防撞墩1之间缝隙设计宽度,快硬型的聚合物砂浆4形成强度的时间不晚于快硬型的封浆料3的终凝时间,在防护板2平行贴合于防撞墩1上时,快硬型的聚合物砂浆4可以粘贴于防撞墩1底部,保证防撞墩1与防护板2之间形成足够强度的粘结力。
48.步骤四、将防护板2平行贴合于防撞墩1上,防护板2底部采用座浆形式落在均匀铺设的快硬型的封浆料3中,调节防护板2与防撞墩1之间缝隙均匀,满足灌浆条件。
49.步骤五、参照图2,将防护板2与防撞墩1之间侧面缝隙用快硬型的封浆料3封住,保证外侧没有露出快硬型的封浆料3,不影响下一块防护板2的安装,如果安装过程中,只有一边侧面露出来,则这个露出的侧面用快硬型的封浆料3封闭,其中,快硬型的封浆料3可用聚合物砂浆4进行替代,另一个侧面与上一块防护板2的侧面之间的缝隙用聚合物砂浆4填补缝隙,通过上述操作,可以使防护板2与防撞墩1之间形成空腔,且除顶面的缝隙外,其他侧面和底面均不漏水和漏浆;
50.步骤六、在快硬型的聚合物砂浆4对防护板2与防撞墩1的强力粘结下,使防护板2牢牢固定在防撞墩1上,既不会上下移动,也不会前后左右移动,防止在后续灌浆过程中向外胀开。
51.步骤七、采用大流动度快硬型灌浆料对防护板2与防撞墩1之间缝隙进行快速灌浆,灌浆方式为人工倾倒或者机械压力灌浆方式,灌浆过程需保证灌浆位置固定,将大流动度快硬型灌浆料从一侧往另一侧灌入,方便内部气体的排出,可以采用一次灌浆或者多次灌浆方式,采用大流动度快硬型灌浆料一次灌浆,这样操作可以大幅度加快设备的周转,提高工作效率。
52.步骤八、待防护板2与防撞墩1之间的灌浆料初凝后,清理防护板2底部露在外侧的封浆料3,进行下一块防护板2的安装操作。
53.步骤九、灌浆完成后,防撞墩1与防护板2中部的灌浆料凝结硬化后产生桥接作用,
一侧与防撞墩1紧密结合,另一侧与防护板2内部粗糙表面黏合,从而使防护板2牢牢防护于防撞墩1外侧,起到保护作用。
54.步骤十、从灌浆开始1-2个小时后,防护板2即可完全固定于防撞墩1面向行车道的侧面,形成一个整体。
55.通过上述操作后,可对已破损混凝土防撞墩1进行内部修复和外层防护,由于采用阻锈剂对钢筋附近进行处理,混凝土防撞墩1内部的钢筋的锈蚀情况大大改善,防锈效果大大提高,外层防护板2采用超高性能混凝土材料制成,具有非常高抗氯离子渗透、抗冻融性能。两方面相互作用,可使混凝土防撞墩1的免维护周期提高10-15年,大幅降低维修成本,降低维护过程交通管制带来的社会经济成本。
56.以上所述,仅为本发明较佳的具体实施方式,但本发明的保护范围并不局限于此,任何熟悉本技术领域的技术人员在本发明揭露的技术范围内,根据本发明的技术方案及其发明构思加以等同替换或改变,都应涵盖在本发明的保护范围之内。