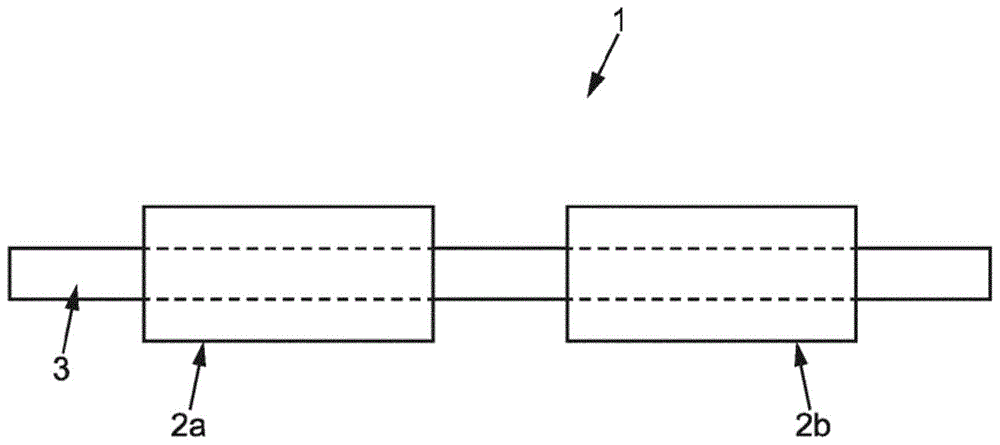
本公开涉及剃刀,并且更具体地说,涉及剃刀刀片,其中剃刀刀片的切削区为异形的。
背景技术:
:剃刀刀片边缘的形状在剃须质量中起重要作用。剃刀刀片典型地具有朝向最终尖端会聚的连续锥形形状。剃刀刀片的最接近最终尖端的部分称为边缘尖端。如果边缘尖端较厚,那么这将能够减少磨损并且延长使用寿命,但是会产生较大的切削力,从而对剃须舒适性产生不利影响。薄边缘尖端轮廓产生了较小的切削力,但是也使破损或损坏的风险增加,并且缩短了使用寿命。因此,期望剃刀刀片的切削边缘在切削力、剃须舒适性和使用寿命之间实现最佳折衷。为了实现上述目的,剃刀刀片的切削边缘进行成形。剃刀刀片的形状可为研磨过程的结果。许多文献主要涉及涂覆刀片的形状而没有详述下面的基底的形状,或仅仅通过限定夹角。虽然可认为刀片的较薄边缘尖端可呈现某些优点,但是此几何形状本身的定义为不充分的,因为如上所述,这类边缘可较弱。申请人已经执行大量的工作以便确定刀片的特性,总体上,这在寻找更薄的边缘几何形状时可为有益的。增强剃刀刀片属性为极其困难的过程。首先,剃刀刀片使用具有非常高产量(每月数百万件产品)的工业过程来制造。其次,为了知道新的剃刀刀片是否提供增强的性能,必须执行模拟剃须的测试,其结果必须与剃刀刀片属性相关。此外,在评估测量结果时还要考虑测量方法的分散性。本公开的目的为提供适用于剃须装置的剃刀头的剃刀刀片,其中与现有技术相比,在维持耐久性的同时改善流动性。技术实现要素:因此,在实施例中,公开具有终止于刀片尖端的对称锥形刀片边缘的剃刀刀片基底,剃刀刀片包含基底和覆盖基底的涂层,涂层包含软涂层和硬涂层,硬涂层至少包含主层,软涂层覆盖硬涂层,其中基底具有基底尖端,其中厚度在距基底尖端5微米的距离处测量为介于1.30微米和2.00微米之间,厚度在距基底尖端20微米的距离处测量为介于4.00微米和6.00微米之间,厚度在距基底尖端40微米的距离处测量为介于8.00微米和11.50微米之间,并且厚度在距基底尖端250微米的距离处测量为介于41.70微米和47.00微米之间。除非另外明确说明,否则权利要求中提供的所有刀片边缘测量数据都是通过共焦显微镜测量获得的。通常,距基底尖端的前40微米(μm)内的较厚边缘轮廓提供增加的耐久性。预计这将对流动性产生负面影响。然而,考虑到在剃须期间剃刀刀片在整个研磨区保持与毛发接触的事实,已经发现将厚度减小超过40μm可对流动性产生积极影响,同时维持耐久性。一种用于测量刀片边缘几何形状的已知方法为使用扫描电子显微镜(sem)。sem在刀片横截面上执行。使用刀片尖端横截面的sem照片。基于距需要测量边缘厚度的尖端的距离来选择放大率。举例来说,对于距尖端测量高达20μm的边缘厚度,可使用3,500倍的放大率。必须将试样插入腔室中,使得电子束垂直地撞击刀片横截面表面。然后使用特殊的图像处理软件分析产生的图像。在一些实施例中,本领域的普通技术人员还可使用以下特征中的一个或多个:基底具有带有一个、两个或三个小面的轮廓,每个小面具有连续锥形几何形状;基底的厚度在距基底尖端30微米的距离处测量为介于6.00微米和8.70微米之间;基底的厚度在距基底尖端50微米的距离处测量为介于10.00微米和14.00微米之间;基底的厚度在距基底尖端100微米的距离处测量为介于19.00微米和24.00微米之间;基底的厚度在距基底尖端150微米的距离处测量为介于27.70微米和32.00微米之间;基底的厚度在距基底尖端200微米的距离处测量为介于34.70微米和40.00微米之间;基底的厚度在距基底尖端300微米的距离处测量为介于48.70微米和54.00微米之间;基底的厚度在距基底尖端350微米的距离处测量为介于55.70微米和61.00微米之间;基底具有基底尖端和朝向基底尖端的锥形几何形状;硬涂层至少包含主层;主层为强化涂层;施用硬涂层或强化涂层作为主层提高剃须性能和耐久性。主层包含铬(cr)、铬-铂(cr-pt)混合物、碳化铬(cr-c)混合物、金刚石、类金刚石碳(dlc)、氮化物、碳化物、氧化物和/或硼化物;主层为剃刀刀片提供耐腐蚀性和边缘强化;硬涂层可另外包含中间层,中间层位于基底和主层之间;中间层用于促进主层与基底的粘接;中间层包含铬(cr)、钛(ti)、铌(nb)、钼(mo)、铝(al)、镍(ni)、铜(cu)、锆(zr)、钨(w)、钒(v)、硅(si)和/或钴(co)和/或其任何合金和/或任何组合;硬涂层可另外包含外涂层,外涂层位于主层和软涂层之间;主层可被外涂层覆盖;外涂层用于促进润滑涂层与主层的粘接;外涂层包含铬(cr)、钛(ti)、铌(nb)和/或钼(mo)和/或其任何合金和/或任何化合物。在另一个实施例中,二硼化钛可用作主层。外涂层可被作为润滑层的软涂层覆盖;润滑剂可为疏水的或亲水的,如多氟烃,例如聚四氟乙烯(ptfe);此涂层减少剃刀头和皮肤之间的摩擦;层的沉积可用各种物理气相沉积技术进行,如溅射、rf-dc磁控溅射、反应磁控溅射、不平衡磁控溅射、电子束蒸发、脉冲激光沉积或阴极电弧沉积;刀片的基底由原材料制成,所述原材料为例如不锈钢,其先前已经历冶金处理。例如,刀片基底主要包含铁,和以重量计,c:0.40-0.80%;si:0.10-1.5%;mn:0.1-1.5%;cr:11.0-15.0%;和mo:0.0-5.0%。在本公开内可使用其它不锈钢。可考虑被称为剃刀刀片基底材料的其它材料。本公开的另一个目的为提供剃须装置,其包含剃刀手柄和剃刀头,其中所述剃刀头包含至少一个根据本公开的剃刀刀片。本公开的又一个目的为提供剃刀头,其具有包含至少一个根据本公开的剃刀刀片的壳体。本公开的另一个目的为提供剃须装置,其包含剃刀手柄和这类剃刀头。根据一些具体实施例,满足距硬涂层尖端在40μm和350μm之间距离的厚度范围为重要的,以便实现剃须舒适性和刀片耐久性的期望几何形状。附图说明根据以下对提供为非限制性实例的一些实施例以及附图的描述,将易于看出其它特性和优点。在图式中:-图1和2为研磨机的示意图,-图3a为根据本公开的实施例的基底的刀片边缘的示意性轮廓图;-图3b为根据本公开的另一个实施例的基底的刀片边缘的示意性轮廓图;-图3c为根据本公开的另一个实施例的基底的刀片边缘的示意性轮廓图;-图4a为图3a的剃刀刀片的刀片边缘的基底尖端的示意性轮廓图;-图4b为图3b的剃刀刀片的刀片边缘的基底尖端的示意性轮廓图;-图4c为图3c的剃刀刀片的刀片边缘的基底尖端的示意性轮廓图;-图5a和5b为共焦测量装置的示意图;-图6为具有示意性涂层的本公开的剃刀刀片的刀片边缘的示意性轮廓图;-图7为被本公开的涂层覆盖的剃刀刀片的刀片边缘的示意性轮廓图;和-图8a为根据本公开的实施例的被硬涂层覆盖的基底的刀片边缘的示意性轮廓图;-图8b为根据本公开的另一个实施例的被硬涂层覆盖的基底的刀片边缘的示意性轮廓图;-图8c为根据本公开的另一个实施例的被硬涂层覆盖的基底的刀片边缘的示意性轮廓图;-图9a为被图8a的硬涂层覆盖的基底的刀片边缘的基底尖端的示意性轮廓图;-图9b为被图8b的硬涂层覆盖的基底的刀片边缘的基底尖端的示意性轮廓图;-图9c为被图8c的硬涂层覆盖的基底的刀片边缘的基底尖端的示意性轮廓图;-图10a和10b为根据本公开的剃刀刀片的两个实施例的透视图;和-图11为根据本公开的包含至少一个剃刀刀片的剃须装置的示意图。在不同的图中,相同附图标记表示相同或相似的元件。具体实施方式根据本说明书的剃刀刀片的期望刀片轮廓可通过涉及一个、两个、三个或四个研磨工位的研磨过程来实现。图1和2示意性地示出具有两个工位2a和2b的研磨设备1。基础材料为连续条带3。连续条带3由用于剃刀刀片基底的原材料制成,所述原材料先前已经进行合适的冶金处理。此原材料例如为不锈钢。本公开还被认为适用于具有碳钢基底的剃刀刀片。另一种可能的材料为陶瓷。这些材料被认为是在适用于剃刀刀片材料的范围内。金属条带比多个剃刀刀片长,例如它对应于1000或更多个将来的剃刀刀片。在研磨之前,一般来说,金属条带3具有矩形横截面。如果要在两个边缘上执行研磨,那么金属条带的高度可略微高于一个精加工的剃刀刀片的高度,或略微高于两个精加工的剃刀刀片的高度。金属条带的厚度为未来剃刀刀片的最大厚度。连续条带3具有例如可介于74μm和100μm之间的厚度。条带可通过冲头,其使得能够在研磨过程期间沿设备1运载条带,和/或可用于促进单个剃刀刀片与条带的未来分离。当金属条带3沿研磨工位2a、2b移动时,其依次经历粗磨、半精加工和精加工研磨操作。根据所涉及的工位数量,粗磨和半精加工操作可单独执行或在同一工位执行。此后,可需要精加工研磨操作。研磨步骤连续执行,因为条带连续移动通过工位而不停止。当单独执行粗磨时,需要一个或两个研磨工位。每个研磨工位可利用相对于移动条带平行定位的一个或两个磨轮。当单独执行粗磨时,需要一个或两个研磨工位。每个研磨工位可利用相对于移动条带平行定位的一个或两个磨轮。磨轮沿其长度具有均匀的砂砾尺寸。所述磨轮也可为完整的主体、螺旋槽或沿其长度的连续盘形图案。磨轮的材料可包含立方氮化硼(cbn)、碳化硅和氧化铝或金刚石。当同时执行粗磨和半精加工操作时,需要单个研磨工位。在此情况下,工位包括形成为螺旋形螺旋或具有特殊轮廓的连续盘形图案的两个磨轮。这些轮的旋转轴可相对于移动条带平行或定位成一定角度。下倾角范围在0.5°和5°之间。轮的砂砾尺寸也可为均匀的或沿其长度朝向条带的出口逐渐减小。轮的磨料可为立方氮化硼(cbn)、碳化硅和氧化铝或金刚石。精加工操作需要单个研磨工位,其中2个磨轮相对于移动条带定位成一定角度。下倾角范围在1°和5.5°之间。轮形成螺旋形螺旋,并且也为特殊异形的。磨料可为立方氮化硼(cbn)、碳化硅和氧化铝或金刚石。轮的长度也可在3到8英寸(7.62cm到20.32cm)之间的范围内。调谐所述过程以便获得具有朝向基底尖端14的锥形几何形状的对称剃刀刀片基底10,如图3a-3c所示。锥形几何形状沿轮廓为连续的,并且可提供有一个、两个或三个相邻小面,分别如图3a、3b和3c所描绘。为了测量刀片几何形状、表面粗糙度和研磨角度,已使用共焦显微镜。图5a和5b示出典型的实例。共焦显微镜包含led光源21、针孔板22、具有压电驱动器24的物镜23和ccd相机25。led源21通过针孔板22和物镜23聚焦到反射光的样品表面上。通过针孔板22的针孔将反射光减少到聚焦的那部分,并且这落在ccd相机上。这里示出的样品示意性地表示剃刀刀片9。使用剃刀刀片的一侧相对于穿过装置内的透镜23的透镜聚焦轴成一定角度。如图5b示意性所描绘,刀片9相对于共焦显微镜定向,其中角度a介于25°和35°之间,优选为30°。刀片9可维持在磁性板支架9'上的适当位置。共焦显微镜具有例如200μm×200μm的给定测量范围。在本实例中,在针孔板22和透镜23之间使用半透明镜28以将反射光导向ccd25。在此情况下,另一个针孔板27用于过滤。然而,在变型中,半透明镜28可用在光源和针孔板22之间,这将使得能够仅使用一个针孔板用于发射的光信号和反射的光信号两者。压电驱动器24适于沿光传播轴移动透镜23,以改变焦点的深度位置。可在保持此测量范围的尺寸的同时改变焦平面。为了扩展测量范围(特别是为了测量远离尖端的刀片边缘),可在另一个位置处执行另一个测量,并且可拼接由所有测量产生的数据。然后可仅仅通过将刀片翻转到其另一侧来测量刀片的另一侧。根据一个实例,可使用基于共焦多针孔(cmp)技术的共焦显微镜。然后,针孔板22具有以特殊图案排列的大量孔。针孔板22的移动使得能够在图像范围内无缝扫描样品的整个表面,并且仅来自焦平面的光到达ccd相机,其中强度遵循共焦曲线。因此,共焦显微镜能够在纳米范围内具有高分辨率。如图3a-3c、4a-4c和8a-8b所描绘,根据本说明书的剃刀刀片包含锋利的刀片基底10。刀片基底10具有平面部分8,其中刀片的两个相对侧彼此平行。此外,刀片基底还包含在图3a-3c和4a-4c上以横截面示出的连接到平面部分8的刀片边缘11,其侧面12和13为锥形的并且会聚到刀片的刀片边缘11的基底尖端14。基底10的形状为异形的,这意味着基底10的横截面沿剃刀刀片的每个小面的长度大致相同。更确切地说,当刀片基底10具有唯一小面,更确切地说一侧上的单个小面12和另一侧上的单个小面13(参见图3a和4a)时,基底10的横截面沿剃刀刀片的长度大致相同。当刀片基底10具有两个小面,更确切地说一侧上的两个小面12和12'以及另一侧上的两个小面13和13'(参见图3b和4b)时,基底10的横截面沿第一小面剃刀刀片的长度大致相同,并且基底10的横截面沿第二小面剃刀刀片的长度大致相同。当刀片基底10具有三个小面,更确切地说一侧上的三个小面12、12'和12″以及另一侧上的三个小面13、13'和13″(参见图3c和4c)时,基底10的横截面沿第一小面剃刀刀片的长度大致相同,刀片的横截面沿第二小面剃刀刀片的长度大致相同,并且基底10的横截面沿第三小面剃刀刀片的长度大致相同。已经制造、测量和测试具有各种几何形状的剃刀刀片的剃须性能。制造不仅包括通过研磨的基底锐化,而且包括如下文将描述的涂层。对于剃须测试,仅修改研磨步骤以便生成各种基底几何形状,其它过程步骤保持相同。测试确定边缘尖端的薄度可通过检查距基底尖端14位于5微米和20微米的控制点的厚度来限定。此外,边缘尖端的强度可通过检查距基底尖端14位于20微米和250微米的控制点的厚度来限定。在强度测试之后,确定对于具有带有表1的以下特征的基底10的剃刀刀片获得合适的剃须效果。*************表1-总刀片边缘轮廓上述尺寸可通过使用相同制造过程制造的产品的分散来获得。刀片在这些控制点之间和之外(从尖端开始和远离尖端)具有平滑的轮廓。从尖端至多到过渡点的刀片厚度增加率(斜率)应该连续减小,使得刀片边缘更容易穿透毛发,从而产生更好的舒适性。过渡点(从40μm到350μm)之后的刀片轮廓应位于特定的值范围内,以便支持从刀片的前40μm到未研磨部分的几何平滑过渡。在该区域中,厚度增加率小于或等于40μm处的增加率。由粗磨阶段生成的刀片边缘轮廓典型地覆盖距基底尖端14在50μm-350μm之间的区,从而确定精加工操作的材料去除速率。通常,精加工研磨阶段主要是为了平滑由粗磨以及刀片边缘轮廓的最终成形而产生的多余表面粗糙度。为了获得最佳处理效率,精加工砂轮的材料去除速率应保持最小,但使得诱导表面粗糙度范围在0.005μm-0.040μm之间。举例来说,上述基底轮廓的厚度可用以下等式y=a×xn+c来描述。一个或多个公式可一个接一个地施加到从基底尖端14延伸到过渡点的刀片部分,基底距所述过渡点具有未研磨部分。在一个实施例中,轮廓可符合等式y=a×xn,其中常数取自下面的表2:x(μm)an[0,20]0.470.85(20,350]0.550.80表2在另一个实施例中,轮廓可符合等式y=a×xn+c,其中常数取自下面的表3:x(μm)anc[0,20]0.470.850(20,70]0.2511(70,480]0.1418.70表3在另一个实施例中,轮廓可符合等式y=a×xn+c,其中常数取自下面的表4:x(μm)anc[0,20]0.470.850(20,70]0.2111.8(70,480]0.1416.70表4包含刀片边缘11的剃刀刀片基底10可由不锈钢制成。合适的不锈钢可主要包含铁,和以重量计,c:0.40-0.80%;si:0.10-1.5%;mn:0.1-1.5%;cr:11.0-15.0%;和mo:0.0-5.0%。在本公开内可使用其它不锈钢。可考虑被称为剃刀刀片基底材料的其它材料。下面描述剃刀刀片的另外的制造步骤。在根据上述技术并且利用表5-12的不同值制造基底之后,在第二步骤中,将基底10(或研磨的刀片)引入沉积腔室中以便进行涂覆。在施加此涂层之前执行上述几何形状测量。涂层配置可包括一层或多层,其改善保护涂层的属性,因此可分别区分中间层、主层和软涂层。中间层和主层限定硬涂层。硬涂层被软涂层覆盖。涂层使得能够减少刀片边缘的磨损、改善整体切削属性并且延长剃刀刀片的可用性。被这几层覆盖的剃刀刀片9仍具有异形几何形状和锥形几何形状,其中两个涂层侧面朝向刀片尖端14″会聚(参见图6和7)。参考图8a-8c和9a-9c,考虑到尖端为被硬涂层覆盖的基底10的硬涂层尖端14',而它为基底10的基底尖端14,根据本说明书的剃刀刀片9将具有与如图3a-3c和4a-4c所描绘的刀片基底10类似的异形几何形状和锥形几何形状。由于基底10具有异形几何形状和锥形几何形状,其中两侧朝向基底尖端14会聚,所以被主层16覆盖的基底10具有异形几何形状和锥形几何形状,其中两个涂层侧面朝向硬涂层尖端14'会聚。另外,当提供有多于一个小面12、13,例如两个小面12、12'和13、13'或三个小面12、12'、12″和13、13'、13″时,被主层16覆盖的基底14仍然具有相同数量的小面(一个、两个或三个)的轮廓。如图3a-3c和4a-4c所描绘,包含刀片边缘11(其具有异形几何形状并且具有锥形几何形状,其中两个基底侧面12、13朝向基底尖端14会聚)的刀片基底10至少在刀片边缘处被沉积在剃刀刀片基底10上的主层16覆盖,如图6所描绘。主层16优选为强化涂层。这种层改善耐腐蚀性、边缘强化以及剃须性能。涂层使得能够减少刀片边缘的磨损、改善整体切削属性并且延长剃刀刀片的可用性。覆盖基底尖端14的强化涂层16具有异形几何形状并且具有锥形几何形状,其中两个涂层侧面朝向硬涂层尖端14'会聚。基底10和硬涂层的组装由表述“涂覆基底19”表示。在图6所描绘的实施例中,刀片边缘基底10涂覆有强化涂层16和作为润滑层的软涂层17。在这种情况下,硬涂层减少到唯一主层16。软涂层17可为疏水的或亲水的,如多氟烃,例如含氟聚合物。润滑层通常用于剃刀刀片领域,用于减少在剃须期间的摩擦。强化涂层16因其机械属性而使用;这为剃刀刀片提供耐腐蚀性和边缘强化。强化涂层16可包含铬(cr)、铬-铂(cr-pt)混合物、碳化铬(cr-c)混合物、金刚石、类金刚石碳(dlc)、氮化物、碳化物、氧化物和/或硼化物。此外,硬涂层可另外包含中间层(15)。在这种情况下,刀片的刀片边缘11被中间层15覆盖,如图7所描绘。举例来说,中间层15可包含铬(cr)、钛(ti)、铌(nb)、钼(mo)、铝(al)、镍(ni)、铜(cu)、锆(zr)、钨(w)、钒(v)、二氧化硅(si)、钴(co)或其任何合金或任何组合。中间层15在强化涂层16之前实施。因此,刀片的刀片边缘11的涂层配置包含覆盖刀片的刀片边缘11的中间层15和覆盖中间层15的强化涂层16。这类覆盖的刀片仍然具有锥形几何形状,其中两个涂层侧面朝向硬涂层尖端14'会聚。此外,强化涂层16可被外涂层20覆盖。外涂层20位于主层16和软涂层17之间。因此,外涂层20也被软涂层覆盖,所述软涂层为可为疏水的或亲水的润滑层17,如多氟烃,例如含氟聚合物,如图7所示。如图7所描绘,涂层因此包含软涂层17以及包含中间层15、主层16和外涂层20的硬涂层。在不存在中间层15的情况下,涂层包含软涂层17以及包含主层16和外涂层20的硬涂层。在沉积润滑层17之前执行基底的上述几何形状测量。外涂层20用于改善聚合物膜与主层的粘合性。可用于促进润滑涂层与主层粘接的对应材料为铬(cr)、钛(ti)、铌(nb)、钼(mo)或其任何合金或任何化合物。在另一个实施例中,二硼化钛可用作外涂层。最后,沉积上述层,可实施各种物理气相沉积技术,如溅射、rf-dc磁控溅射、反应磁控溅射或不平衡磁控溅射、电子束蒸发、脉冲激光沉积、阴极电弧沉积。以下公开三层系统的涂覆程序的实例,这允许根据本说明书制造剃刀刀片。在这种情况下,硬涂层包含中间层15、主层16和外涂层20。在将带有刀片基底的刀片卡口装载到旋转夹具上之后,将腔室置于10-5托的基础压力下。然后将氩(ar)气插入腔室中,压力高达8毫托(8.10-3托)。刀片卡口的旋转以6rpm的恒定速度开始,并且目标在0.2安培(a)的dc电流控制下操作。将200伏特(v)-600v的dc电压施加在不锈钢刀片上4分钟,以便执行溅射蚀刻步骤。在另一个实施例中,将100伏特(v)-600v的脉冲dc电压施加在不锈钢刀片上4分钟,以便执行溅射蚀刻步骤。在溅射蚀刻步骤结束后进行中间层的沉积,将腔室压力调节至3毫托。中间层目标在3安培(a)-10a的dc电流控制下操作,同时将0伏特(v)-100v的dc电压施加在旋转刀片上。调节沉积时间,在主层之前沉积5nm-50nm的中间层。在一个实施例中,ti可为中间层,而在另一个实施例中,cr可为中间层。在沉积中间层之后,中间层目标的电流降低到0.2安培(a)并且(一个或多个)主层目标的电流增加到3a-6a。特定实施例包括在粘接中间层的顶部上10nm-400nm的tib2化合物膜。将0v-600v的dc偏置电压施加在旋转刀片上。此外,在主层的顶部上,以3a的电流和0v-450v的偏置电压在(一个或多个)cr目标上沉积cr软涂层。特定的cr层厚度为5nm-50nm。最后,在每个刀片边缘小面上,总涂层厚度可从10至500nm变化,并且优选从10nm至250nm变化。根据本说明书的剃刀刀片的厚度根据较低和较高的涂层厚度总结在表13中。根据本公开的剃刀刀片9的厚度在距硬涂层尖端14'的距离x(以微米为单位)处测量。当硬涂层包含中间层15、主层16和外涂层20时,然后在距外涂层20的距离x处测量厚度。剃刀刀片9的边缘轮廓的厚度为未涂覆刀片(意味着基底)的边缘轮廓的厚度加上涂层的厚度的总和。最后,在每个刀片边缘小面上,总涂层厚度可从10至500nm变化,并且优选从100nm至400nm变化。表5刀片可固定或机械组装到剃刀头上,并且剃刀头本身可为剃刀的一部分。刀片可以可移动地安装在剃刀头中,并且因此安装在弹性指状物上,所述弹性指状物将所述刀片推向静止位置。刀片可固定,特别是焊接到支撑件29,特别是具有l形横截面的金属支撑件,如图10a所示。另选地,刀片可为整体弯曲的刀片,如图10b所示,其中上述公开的几何形状适用于刀片尖端14″和弯曲部分30之间。此外,图11示出剃须刀架105,其具有包含至少一个如上所述的剃刀刀片的壳体110。剃刀刀片的数量可多于一个,例如五个或更多或更少。这类剃须刀架105可连接到剃刀手柄201,以形成用于剃须目的的剃须装置200。剃须刀架105可以可拆卸地连接到剃刀手柄201。剃须刀架105可枢转地连接到剃刀手柄201。尽管本文已经参考特定装置、材料和实施例对前述描述加以描述,但是并不旨在限于本文公开的细节;相反,其扩展到如在所附权利要求书的范围内的所有功能上等效的结构、方法和用途。当前第1页12