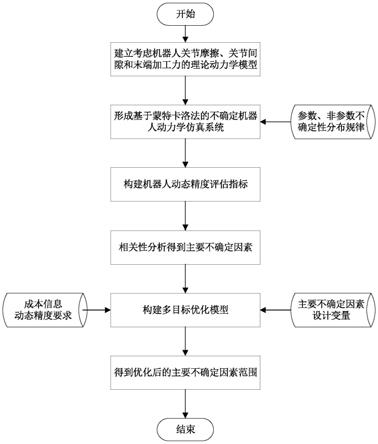
1.本发明属于工业机器人精度设计领域,具体涉及一种工业机器人动态精度设计方法和系统。
背景技术:2.工业机器人由于加工效率高、工作范围广、柔性化程度高等特点在汽车制造、机械加工等领域备受青睐,并逐渐被引入航空制造业,但是传统基于运动学的精度设计方法已经无法满足新一代航空产品对机器人加工动态精度提出的要求。其原因在于每台制造出来的机器人的实际运动学、动力学参数与设计阶段的理论值均有较大误差,且这类误差往往具有不确定性。另外,机器人的关节间隙、关节摩擦、末端加工力等均是随机变化的。这些不确定误差因素严重影响机器人定位精度、轨迹精度与动态性能的一致性,因此必须从机器人动力学角度出发,考虑机器人加工过程中更加全面的不确定因素,在设计阶段展开研究从而提升动态精度。
3.目前机器人的精度设计包括精度分析与精度优化分配两个互逆的过程。已公开的发明专利申请“一种机器人精度设计方法,cn106777422a”基于运动学模型分析制造精度、运动控制精度与机器人概率精度值的对应关系,根据允许的精度剩余量分配公差项目。国外有s.s.rao在期刊《reliability engineering&system safety》上发表的“uncertainty analysis and allocation of joint tolerances in robot manipulators based on interval analysis”考虑了机器人末端执行器的位置、方向误差以及制造成本,基于运动学研究了关节公差的优化分配问题。现有文献中存在的技术问题:1)忽略实际机器人在制造安装以及加工运动过程的误差源所导致的不确定性,将所有影响因素确定性分析;2)机器人精度设计依赖经验法则,缺少一种机器人动态精度评估指标,形成一套系统的机器人动态精度优化设计方法。
技术实现要素:4.本发明针对现有技术中的不足,提供一种工业机器人动态精度设计方法和系统。
5.为实现上述目的,本发明采用以下技术方案:
6.一种工业机器人动态精度设计方法,其特征在于,包括如下步骤:
7.步骤s1:建立考虑关节摩擦、关节间隙和末端加工力的机器人动力学模型;
8.步骤s2:形成基于蒙特卡洛法的不确定机器人动力学仿真系统;
9.步骤s3:基于步骤s1的机器人动力学模型和步骤s2的不确定机器人动力学仿真系统,计算机器人动态精度评估指标,并利用相关性分析得出影响机器人动态精度的主要不确定因素,忽略次要不确定因素;
10.步骤s4:结合机器人加工的零件精度要求,建立机器人主要不确定因素的约束模型,构建融合动态精度评估指标与成本的多目标函数;
11.步骤s5:基于遗传算法进行多目标优化,求解多目标函数得到优化后影响机器人
动态精度的主要不确定因素的参考范围,从而指导动态精度设计。
12.为优化上述技术方案,采取的具体措施还包括:
13.进一步地,所述步骤s1中,对于n个连杆的机器人,将机器人末端加工力考虑为连杆n+1作用在连杆n上的力和力矩,分别建立机器人的关节摩擦模型和关节间隙模型
[0014][0015][0016]
式中,表示n
×
1关节角速度矢量;fs表示静摩擦力;fc表示库伦摩擦力;σ表示粘性摩擦系数;vs表示stribeck系数;δ表示轴径和衬套撞击引起的贯入深度;表示相对冲击速度;k表示广义刚度参数;d表示阻尼参数;
[0017]
最终得到机器人动力学模型为:
[0018][0019]
式中,τ表示n
×
1关节力矩矢量;θ表示n
×
1关节转角矢量;指n
×
1关节角加速度矢量;m(θ)表示n
×
n惯性矩阵;表示n
×
n科式力和离心力矩阵;g(θ)表示n
×
1重力矩矢量。
[0020]
进一步地,所述步骤s3具体包括如下步骤:
[0021]
步骤s3.1:设置样本数n,每个样本里包括机器人的t个不确定因素,不确定因素包括机器人的运动学参数、动力学参数、关节摩擦、关节间隙和末端加工力;
[0022]
步骤s3.2:根据t个不确定因素的分布规律生成n组随机样本值xj=[x
j1
,
…
,x
jt
],j=1,..,n;
[0023]
步骤s3.3:将步骤s3.2生成的样本值输入步骤s1中的机器人动力学模型,得出末端动态精度f(xj),评判是否满足机器人动态精度fa的要求,最终得到满足动态精度要求的个数m;
[0024]
步骤s3.4:n组样本仿真完毕后,得出所提出的机器人动态精度评估指标pf=m/n;将t个不确定因素与动态精度评估指标进行相关性分析,判断各个不确定因素与动态精度评估指标之间的相关程度,从而确定影响机器人动态精度的主要不确定因素;
[0025]
步骤s3.5:输出k个影响机器人动态精度的主要不确定因素。
[0026]
进一步地,所述步骤s3.4中,确定影响机器人动态精度的主要不确定因素的方式具体如下:
[0027]
若相关性系数的绝对值及其相关性检验统计量的绝对值较大,则为主要不确定因素,反之为次要不确定因素;假设一共进行s组仿真,每组生成n组样本值,得到第i组仿真的动态精度评估指标pf(e)i;xi为某一个不确定因素的观测值,每一组相关性系数与检验统计量r的公式为:
[0028]
[0029][0030]
式中,为该不确定因素的均值,为动态精度评估指标的均值。
[0031]
进一步地,所述步骤s4具体包括如下步骤:
[0032]
步骤s4.1:根据步骤s3.5输出的k个主要不确定因素作为设计变量,结合机器人加工的零件精度要求,建立机器人主要不确定因素的约束模型:
[0033][0034]
式中,x1,x2,...,xk为k个主要不确定因素,e
1a
,e
2a
,...,e
ka
为k个主要不确定因素的下限值,e
1b
,e
2b
,...,e
kb
为k个主要不确定因素的上限值;
[0035]
步骤s4.2:建立工业机器人本体制造成本cost(y)与主要不确定因素之间的关系:
[0036]
cost(y)=at-b
[0037]
式中,t表示公差,a、b为成本系数,y=[e
1a
,e
2a
,...,e
ka
,e
1b
,e
2b
,...,e
kb
]为主要不确定因素的设计变量;
[0038]
结合机器人动态精度评估指标,构建精度优化设计的多目标函数w(y)为:
[0039]
w(y)=ω1cost(y)+ω2/pf(y)
[0040]
式中,ω1和ω2为权重系数;pf(y)表示根据主要不确定因素的动态精度评估指标。
[0041]
本发明还提出了一种工业机器人动态精度设计系统,其特征在于,包括:
[0042]
机器人动力学模型建立单元,用于建立考虑关节摩擦、关节间隙和末端加工力的机器人动力学模型;
[0043]
基于蒙特卡洛法的不确定机器人动力学仿真系统,用于基于机器人动力学模型计算机器人动态精度评估指标,并利用相关性分析得出影响机器人动态精度的主要不确定因素,忽略次要不确定因素;
[0044]
多目标函数构建单元,用于结合机器人加工的零件精度要求,建立机器人主要不确定因素的约束模型,构建融合动态精度评估指标与成本的多目标函数;
[0045]
多目标优化单元,用于基于遗传算法进行多目标优化,求解多目标函数得到优化后影响机器人动态精度的主要不确定因素的参考范围,从而指导动态精度设计。
[0046]
进一步地,所述机器人动力学模型建立单元中,对于n个连杆的机器人,将机器人末端加工力考虑为连杆n+1作用在连杆n上的力和力矩,分别建立机器人的关节摩擦模型和关节间隙模型
[0047][0048][0049]
式中,指n
×
1关节角速度矢量;fs表示静摩擦力;fc表示库伦摩擦力;σ表示粘性摩擦系数;vs表示stribeck系数;δ表示轴径和衬套撞击引起的贯入深度;表示相对冲击速度;k表示广义刚度参数;d表示阻尼参数;
[0050]
最终得到机器人动力学模型为:
[0051][0052]
式中,τ表示n
×
1关节力矩矢量;θ表示n
×
1关节转角矢量;指n
×
1关节角加速度矢量;m(θ)表示n
×
n惯性矩阵;表示n
×
n科式力和离心力矩阵;g(θ)表示n
×
1重力矩矢量。
[0053]
进一步地,所述不确定机器人动力学仿真系统包括总控模块、随机数模块、机器人动力学模型模块、相关性分析模块和结果输出模块;
[0054]
所述总控模块设置样本数n,每个样本里包括机器人的t个不确定因素,所述不确定因素包括机器人的运动学参数、动力学参数、关节摩擦、关节间隙和末端加工力;
[0055]
所述随机数模块根据t个不确定因素的分布规律生成n组随机样本值xj=[x
j1
,...,x
jt
],j=1,...,n;
[0056]
所述机器人动力学模型模块将随机数模块生成的样本值输入机器人动力学模型,得出末端动态精度f(xj),评判是否满足机器人动态精度fa的要求,最终得到满足动态精度要求的个数m;
[0057]
所述相关性分析模块在n组样本仿真完毕后,得出所提出的机器人动态精度评估指标pf=m/n;将t个不确定因素与动态精度评估指标进行相关性分析,判断各个不确定因素与动态精度评估指标之间的相关程度,从而确定影响机器人动态精度的主要不确定因素;
[0058]
所述结果输出模块输出k个影响机器人动态精度的主要不确定因素。
[0059]
进一步地,所述相关性分析模块确定影响机器人动态精度的主要不确定因素的方式具体如下:
[0060]
若相关性系数的绝对值及其相关性检验统计量的绝对值较大,则为主要不确定因素,反之为次要不确定因素;假设一共进行s组仿真,每组生成n组样本值,得到第i组仿真的动态精度评估指标pf(e)i;xi为某一个不确定因素的观测值,每一组相关性系数与检验统计量r的公式为:
[0061][0062][0063]
式中,为该不确定因素的均值,为动态精度评估指标的均值。
[0064]
进一步地,所述多目标函数构建单元根据结果输出模块输出的k个主要不确定因素作为设计变量,结合机器人加工的零件精度要求,建立机器人主要不确定因素的约束模型:
[0065][0066]
式中,x1,x2,...,xk为k个主要不确定因素,e
1a
,e
2a
,...,exa为k个主要不确定因素
的下限值,e
1b
,e
2b
,...,e
kb
为k个主要不确定因素的上限值;
[0067]
然后建立工业机器人本体制造成本cost(y)与主要不确定因素之间的关系:
[0068]
cost(y)=at-b
[0069]
式中,t表示公差,a、b为成本系数,y=[e
1a
,e
2a
,...,e
ka
,e
1b
,e
2b
,...,e
kb
]为主要不确定因素的设计变量;
[0070]
结合机器人动态精度评估指标,构建精度优化设计的多目标函数w(y)为:
[0071]
w(y)=ω1cost(y)+ω2/pf(y)
[0072]
式中,ω1和ω2为权重系数;pf(y)表示根据主要不确定因素的动态精度评估指标。
[0073]
本发明的有益效果是:本发明通过建立机器人加工运动过程中的动力学模型,形成基于蒙特卡洛法的机器人不确定动力学仿真系统,在此基础上进行动态精度分析与优化设计。本发明考虑了机器人的实际加工动态过程中的不确定因素,形成了一个完善的不确定仿真系统,可以在设计阶段就对机器人进行仿真研究与优化设计,相比较于经验法则更具有指导意义。
附图说明
[0074]
图1是本发明的工作流程图。
[0075]
图2是本发明形成的机器人不确定动力学仿真系统的组成模块示意图。
[0076]
图3是本发明的仿真流程图。
具体实施方式
[0077]
现在结合附图对本发明作进一步详细的说明。
[0078]
如图1所示,本发明提出了一种工业机器人动态精度设计方法,其中:包括如下步骤:
[0079]
1、建立考虑机器人关节摩擦、关节间隙、末端加工力的动力学模型,具体为:
[0080]
(1)建立机器人的运动学模型,由机器人连杆i的关节转角θi、连杆偏置di、连杆长度ai和关节扭角αi这4个参数建立连杆i+1相对于连杆i的位姿变换矩阵it
i+1
为:
[0081][0082]
式中,rot()表示旋转矩阵变换,trans()表示平移矩阵变换。
[0083]
利用式(1),通过依次连乘连杆i+1相对于连杆i的位姿变换矩阵即可获取机器人末端执行器n相对于基坐标系0的位姿变换矩阵:
[0084][0085]
式中,0rn为机器人末端执行器的姿态旋转矩阵;0pn为机器人末端执行器的位置矢量;01×3为1行3列全零矩阵。
[0086]
(2)建立机器人的动力学模型,具体的递推公式如下:
[0087][0088][0089]
式中,分别表示关节i的角速度、角加速度;iεi、iωi、
iai
、
iaci
分别表示连杆i的角加速度、角速度、原点加速度、质心加速度在连杆坐标系i下的投影;
i-1
ε
i-1
、
i-1
ω
i-1
、
i-1ai-1
分别表示连杆i-1的角加速度、角速度、原点加速度在连杆坐标系i-1下的投影;
i-1zi-1
=[0,0,1]
t
;
iri-1
表示连杆坐标系i-1相对于连杆坐标系i的旋转矩阵;
iri+1
表示连杆坐标系i+1相对于连杆坐标系i的旋转矩阵;
i+1
pi表示连杆坐标系i-1原点与连杆坐标系i的原点的距离在连杆坐标系i-1中的投影;
irci
表示连杆i质心在连杆坐标系i中的投影;
ifi
、ini分别表示作用于连杆i的外力、外力矩在连杆坐标系i中的投影;
ifi
、ini分别表示连杆i-1作用在连杆i的力和力矩在连杆坐标系i中的投影;
i+1fi+1
、
i+1ni+1
分别表示连杆i+1作用在连杆i的力和力矩在连杆坐标系i+1中的投影;mi表示连杆i的质量;g表示重力加速度矢量;ii
ci
表示连杆i相对于质心的惯性张量矩阵;τi表示连杆i关节轴上的驱动力矩。
[0090]
(3)对于n个连杆的机器人,将机器人末端加工力考虑为连杆n+1作用在连杆n上的力和力矩并分别建立机器人的关节摩擦模型和关节间隙模型
[0091][0092][0093]
式中,表示n
×
1关节角速度矢量;fs表示静摩擦力;fc表示库伦摩擦力;σ表示粘性摩擦系数;vs表示stribeck系数;δ表示轴径和衬套撞击引起的贯入深度;表示相对冲击速度;k表示广义刚度参数;d表示阻尼参数。
[0094]
最终可以将机器人动力学模型写为:
[0095][0096]
式中,τ表示n
×
1关节力矩矢量;θ表示n
×
1关节转角矢量;表示n
×
1的关节角加速度矢量;m(θ)表示n
×
n惯性矩阵;表示n
×
n科式力和离心力矩阵;g(θ)表示n
×
1重力矩矢量。
[0097]
2、形成基于蒙特卡洛法的不确定机器人动力学仿真系统,在此基础上进行相关性分析,如图2、图3所示,仿真系统包括总控模块、随机数模块、机器人动力学模型模块、相关性分析模块、结果输出模块。具体为:
[0098]
(1)总控模块:设置样本数n,每个样本里包括机器人的运动学参数(连杆长度、关节扭角、关节转角、连杆偏置)、动力学参数(转动惯量、质心位置、质量)、关节摩擦、关节间隙、末端加工力等t个不确定因素。其中,运动学参数、动力学参数、关节间隙矢量、关节摩擦
系数服从正态分布规律,设置初始值m=0,j=0。
[0099]
(2)随机数模块:设e=[e
1a
,e
2a
,...,e
ta
,e
1b
,e
2b
,...,e
tb
],e
1a
,e
2a
,...,e
ta
为t个不确定因素的分布区间下限值,e
1b
,e
2b
,...,e
tb
为上限值。根据t个不确定因素在区间内的分布规律,即生成n组随机样本值xj=[x
j1
...,x
jt
],j=1,...,n。
[0100]
(3)机器人动力学模型模块:将随机数模块中的样本值输入步骤1中机器人动力学模型,得出末端动态精度f(xj),评判是否满足机器人动态精度fa的要求,若满足,则ij=1,反之,ij=0,最终满足动态精度要求的个数m=m+ij。
[0101]
(4)相关性分析模块:n组样本仿真完毕后,可以得出所提出的机器人动态精度评估指标pf(e)=m/n。此处的pf(e)是指考虑了所有不确定因素的动态精度评估指标,e是所有不确定因素的上下限。将t个不确定设计变量与动态精度评估指标进行相关性分析,判断各个随机不确定因素与最终动态精度评估指标之间的相关程度,从而确定动态精度的主要影响因素。若相关性系数的绝对值及其相关性检验统计量的绝对值较大,则为主要因素。假设一共进行s组仿真,每组生成n组样本值,得到第i组仿真的动态精度评估指标pf(e)i=m/n。xi为某一个不确定因素的观测值,每一组相关性系数与检验统计量r的公式为:
[0102][0103][0104]
式中,为该不确定因素的均值,为动态精度评估指标的均值。
[0105]
(5)结果输出模块:根据步骤(1)~(4)输出最终影响机器人动态精度的主要不确定因素k个。
[0106]
3、确定主要不确定因素设计变量的约束条件,构建融合动态精度指标与成本的多目标函数,具体为:
[0107]
(1)约束条件:根据步骤2中确定的k个主要不确定因素作为设计变量,结合机器人加工零件要求、本体制造精度等,形成机器人主要参数、非参数不确定因素的约束模型。主要参数和非参数包括机器人的运动学参数不确定性、动力学参数不确定性以及诸如关节摩擦、关节间隙与末端加工力等非参数的不确定性。
[0108][0109]
式中,x1,x2,..,xk为k个主要不确定因素,e
1a
,e
2a
,...,e
ka
为k个不确定因素的下限值,e
1b
,e
2b
,...,e
kb
为k个不确定因素的上限值。
[0110]
(2)多目标函数:通过下式建立工业机器人本体制造成本与不确定因素之间的关系:
[0111]
cost(y)=at-b
ꢀꢀ
(11)
[0112]
式中,t表示公差,a、b为成本系数,y=[e
1a
,e
2a
,...,e
ka
,e
1b
,e
2b
,...,e
kb
]为主要不
确定因素的设计变量。
[0113]
结合本发明提出的机器人动态精度评估指标要求,最终精度优化设计目标函数为
[0114]
w(y)=ω1cost(y)+ω2/pf(y)
ꢀꢀ
(12)
[0115]
式中,ω1和ω2为权重系数;pf(y)指根据主要不确定因素的动态精度评估指标。
[0116]
4、基于遗传算法进行多目标优化,具体为:把待优化的主要不确定因素经编程转成特定进制的染色体,利用不同的染色体构成一个初始种群,进而随机产生初始种群,并将初始种群作为问题的初始解,经复制、交叉和变异这3种算子的重复操作,迭代进化,可以得到最优解,最终求解得到优化后影响机器人动态精度的主要因素参考范围,从而指导动态精度设计。
[0117]
此外,本发明还提出了一种工业机器人动态精度设计系统,包括以下组成部分:
[0118]
机器人动力学模型建立单元,用于建立考虑关节摩擦、关节间隙和末端加工力的机器人动力学模型;
[0119]
基于蒙特卡洛法的不确定机器人动力学仿真系统,用于基于机器人动力学模型计算机器人动态精度评估指标,并利用相关性分析得出影响机器人动态精度的主要不确定因素,忽略次要不确定因素;
[0120]
多目标函数构建单元,用于结合机器人加工的零件精度要求,建立机器人主要不确定因素的约束模型,构建融合动态精度评估指标与成本的多目标函数;
[0121]
多目标优化单元,用于基于遗传算法进行多目标优化,求解多目标函数得到优化后影响机器人动态精度的主要不确定因素的参考范围,从而指导动态精度设计。
[0122]
其中,工业机器人动态精度设计系统的各组成部分的工作方式与前述方法相对应。
[0123]
以上仅是本发明的优选实施方式,本发明的保护范围并不仅局限于上述实施例,凡属于本发明思路下的技术方案均属于本发明的保护范围。应当指出,对于本技术领域的普通技术人员来说,在不脱离本发明原理前提下的若干改进和润饰,应视为本发明的保护范围。